U型管换热器毕业设计说明书u型管换热器毕业设计.docx
《U型管换热器毕业设计说明书u型管换热器毕业设计.docx》由会员分享,可在线阅读,更多相关《U型管换热器毕业设计说明书u型管换热器毕业设计.docx(12页珍藏版)》请在冰豆网上搜索。
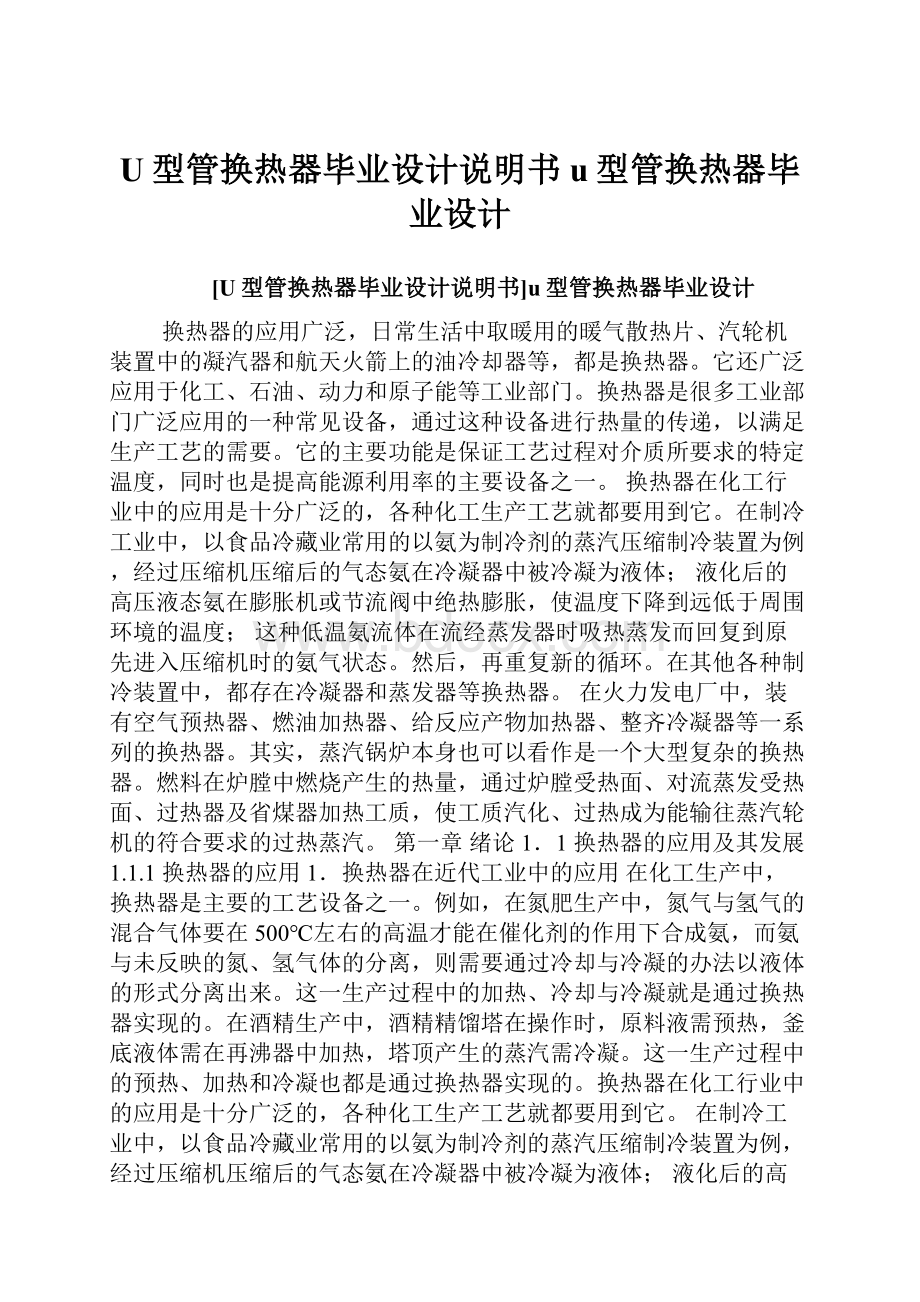
U型管换热器毕业设计说明书u型管换热器毕业设计
[U型管换热器毕业设计说明书]u型管换热器毕业设计
换热器的应用广泛,日常生活中取暖用的暖气散热片、汽轮机装置中的凝汽器和航天火箭上的油冷却器等,都是换热器。
它还广泛应用于化工、石油、动力和原子能等工业部门。
换热器是很多工业部门广泛应用的一种常见设备,通过这种设备进行热量的传递,以满足生产工艺的需要。
它的主要功能是保证工艺过程对介质所要求的特定温度,同时也是提高能源利用率的主要设备之一。
换热器在化工行业中的应用是十分广泛的,各种化工生产工艺就都要用到它。
在制冷工业中,以食品冷藏业常用的以氨为制冷剂的蒸汽压缩制冷装置为例,经过压缩机压缩后的气态氨在冷凝器中被冷凝为液体;液化后的高压液态氨在膨胀机或节流阀中绝热膨胀,使温度下降到远低于周围环境的温度;这种低温氨流体在流经蒸发器时吸热蒸发而回复到原先进入压缩机时的氨气状态。
然后,再重复新的循环。
在其他各种制冷装置中,都存在冷凝器和蒸发器等换热器。
在火力发电厂中,装有空气预热器、燃油加热器、给反应产物加热器、整齐冷凝器等一系列的换热器。
其实,蒸汽锅炉本身也可以看作是一个大型复杂的换热器。
燃料在炉膛中燃烧产生的热量,通过炉膛受热面、对流蒸发受热面、过热器及省煤器加热工质,使工质汽化、过热成为能输往蒸汽轮机的符合要求的过热蒸汽。
第一章绪论1.1换热器的应用及其发展1.1.1换热器的应用1.换热器在近代工业中的应用在化工生产中,换热器是主要的工艺设备之一。
例如,在氮肥生产中,氮气与氢气的混合气体要在500℃左右的高温才能在催化剂的作用下合成氨,而氨与未反映的氮、氢气体的分离,则需要通过冷却与冷凝的办法以液体的形式分离出来。
这一生产过程中的加热、冷却与冷凝就是通过换热器实现的。
在酒精生产中,酒精精馏塔在操作时,原料液需预热,釜底液体需在再沸器中加热,塔顶产生的蒸汽需冷凝。
这一生产过程中的预热、加热和冷凝也都是通过换热器实现的。
换热器在化工行业中的应用是十分广泛的,各种化工生产工艺就都要用到它。
在制冷工业中,以食品冷藏业常用的以氨为制冷剂的蒸汽压缩制冷装置为例,经过压缩机压缩后的气态氨在冷凝器中被冷凝为液体;液化后的高压液态氨在膨胀机或节流阀中绝热膨胀,使温度下降到远低于周围环境的温度;这种低温氨流体在流经蒸发器时吸热蒸发而回复到原先进入压缩机时的氨气状态。
然后,再重复新的循环。
在其他各种制冷装置中,都存在冷凝器和蒸发器等换热器。
在火力发电厂中,装有空气预热器、燃油加热器、给反应产物加热器、整齐冷凝器等一系列的换热器。
其实,蒸汽锅炉本身也可以看作是一个大型复杂的换热器。
燃料在炉膛中燃烧产生的热量,通过炉膛受热面、对流蒸发受热面、过热器及省煤器加热工质,使工质汽化、过热成为能输往蒸汽轮机的符合要求的过热蒸汽。
在核电长中,蒸汽发生器是一项很重要的工艺设备。
核燃料裂变所产生的大量的热量首先传给冷却剂,冷却剂在蒸汽发生器中再将热量传给反应产物、使反应产物汽化成蒸汽,由蒸汽来转动汽轮发电机发电。
此外,在核电厂系统中还装有各种加热器、蒸汽冷凝器等换热器。
在动力、化工、制冷等工业中,换热器不仅是不可缺少的工艺设备,而且在金属消耗和投资方面也占有较大的比例。
在火力发电厂中,如果将锅炉也作为换热设备,则换热器的投资约占电厂总投资的70%左右。
在一般石油化工企业中,换热器的投资约占总投资的30%~40%。
2.换热器在节能降耗中的应用换热器在节能技术改造中具有很重要的作用,表现在两个方面:
一是在生产工艺流程中使用着大量的换热器,提高这些换热器的效率,显然可以减少能源的消耗;另一方面,用换热器来回收工业余热,可以显著地提高设备的热效率。
工业预热数量大,分布广,各国均已把余热回收列为节能工作的一个重要方面。
研究表明,换热器是最有效的余热回收设备。
以锻造加热炉为例,普通加热炉每公斤锻件的能耗为0.7公斤标准燃料,而装有换热器的加热炉每公斤锻件的能耗只有0.15公斤左右标准燃料。
烧燃料的工业炉,约有60%~70%的热量由烟气带走,被浪费掉了。
有段时期国内偏重于用余热锅炉来回收烟气余热,而较少采用换热器。
余热锅炉的热回收率虽较高,但它无助于工业炉本身热效率的提高,因而无助于炉用高质燃料的节省。
装设换热器利用烟气余热来预热工业炉的进风,可使工业炉本身的热效率得到提高,因而可以节省炉用高质燃料。
用普通换热器将空气预热至300~400℃,一般可节约燃料15%~25%,用高温换热器时可以取得更好的效果,节约燃料可达40%以上。
烧低热值染了的加热炉,将空气和煤气预热至300℃,可使升温速度提高1~2倍,可使产量提高20%~30%。
对于烧油的炉子,预热工期有助于染有雾化质量的改善,使燃料得到充分的燃烧。
换热气的后面再装预热锅炉,可使燃料热量的利用率达到80%~90%。
由此可见,工业炉烟气的余热回收,应首先满足炉内需要以节省炉用高质燃料;然后早考虑外部需要,争取得到更大的经济效益。
对于其他余热的回收,也应遵守以节约燃料为中心进行综合利用的原则。
由于工业余热分布广、形式各种各样,故节能方案也各不相同,但在各种节能方案中,换热器几乎是不可缺少的。
1.1.2换热器的发展1.换热设备的发展概况换热器在工业中的应用,至少已有200余年的历史。
200余年的换热器发展史,可大致划分为三个时期:
20世纪以前为原始时期;20时间的前50年为初步发展时期;近30余年为迅速发展时期。
(1)原始时期这个时期的换热器大都是由铸铁管组装而成的管式换热器,主要用于动力、化工、钢铁等工业部门。
19实际50年代,考贝尔和西门子分别发明了炼铁炉和炼钢炉用的蓄热室。
由于用蓄热室预热空气比用当时的金属换热器所能达到的温度高,因而逐渐取代了原始的铸铁管换热器,成为19世纪后50年中工业炉的主要换热设备。
(2)初步发展时期20世纪初,换热器开始进入了一个新的发展时期─在科学理论指导下的初步发展时期。
在20世纪的前50年中,换热器的发展发生了如下变化:
①管式换热器发展迅速50年代初,U型管式、套管式、绕管式、蛇管式等各种管式换热器,其结构已近于比较完善的程度,许多国家都制订了系列标准。
随着冶金工业的发展,钢、合金钢、铝、钢等均已成为管式换热器广泛采用的材料。
为了提高换热器的效率,30年代已出现了肋片管式换热器。
这一时期,管式换热器在所有的换热设备中占据着绝对优势。
②出现了多种板式结构换热器由于“板式”传热表面的传热性能比“管式”优越,相继出现了板式、螺旋板式、板肋式、板壳式等以板片为基本构件的换热器。
与管式换热器相比,这些板式结构换热器的突出优点是传热效率高、结构紧凑、质量小、,因此受到各工业部门的重视。
(3)迅速发展时期进入50年代以后,科学技术和工业生产有了飞速发展,使换热器也进入了一个飞速发展时期。
①管式换热器的发展随着强化传热技术的发展,各种型式的强化传热管相继出现。
在U型管式换热器中,强化传热管已被广泛采用,在提高传热效率、提高紧凑性和降低材料消耗等方面均取得了显著效果。
通过选用新型材料和对关键受力部件的改进,操作温度和压力都有了明显的提高,目前U型管式换热器的最高操作温度可达1500℃(压力为8MPa)。
②板式结构换热器得到广泛应用随着工艺和传热学的发展,板式结构换热器在设计和生产上遇到的问题逐步得到解决,近20年来发展很快,已在许多工业部门中得到广泛应用。
在压力较低、温度不高、流量不很大的若干场合,各种板式结构换热器已逐步取代管式换热器。
其中的螺旋板式换热器作为一种高效换热设备,发展尤为迅速。
2.换热器的发展趋势当前换热器发展的基本趋势将是:
继续提高设备的传热效率,促进设备结构的紧凑性,加强生产制造的标准系列化和专业化,并在广泛的范围内继续向大型化的方向发展。
U型管式换热器:
由于它具有结构坚固、弹性大和使用材料范围广等独特的优点,今后仍将在广泛的领域内得到继续发展。
尤其在高温、高压和大型化的场合下,更有其广阔的发展前途。
但为了加强其传热效率,在高温和高压的条件下,采用电焊焊接式的翅片管的结构将会得到重视和发展。
制造工艺上进一步机械化和自动以及起采用各种新技术,在发展U型管式换热器方面仍将占有重要的地位。
板式换热器:
该种形式的换热器进一步发展的趋势,将是提高操作温度和操作压力,设计大型板片以增大它的处理量,扩大它的使用范围,并采用新的结构材料和新的制造工艺。
其中尤以研制新的垫片材料,改进密封结构,增强板片的刚度,以便提高操作温度和操作压力,扩大使用范围等,将是今后发展的重点。
螺旋板换热器的近期发展,将对其各种结构形式的换热器扩大其应用场合,同时,如何进一步提高其承压能力,增大处理量,并改进焊接工艺,以适应石油及化学工业的要求。
1.2换热器的分类及其特点换热器的类型随工业发展而增多,早期的换热设备由于制造工艺和科学反应产物平的限制,多有结构简单、换热面积小和体积较大等特征。
在化工生产中,由于用途、工作条件和热载体的特性等的不同,对换热器提出了不同的要求,所以出现了各种不同形式和结构的换热器。
为了便于区分和分析研究,可将换热器按下列方式进行分类。
1.2.1换热器的分类1.按作用原理或传热方式分类
(1)混合式换热器它是利用两种换热流体的直接接触与混合的作用来进行热量交换的。
混合式换热器操作的一个主要因素,就是要使两种流体的接触面积尽可能大,以促进它们之间的热量交换。
为了获得更大的接触面积,可在设备中防止隔栅填料,有时也可把液体喷成细滴。
此类设备通常做成塔状。
(2)蓄热式换热器它是让两种温度不同的流体先后通过同一种固体填料的表面,首先让热流体通过,把热量蓄积在填料中,然后,当冷流体再通过时,将热量带走,这样在填料被加热和被冷却的过程中,进行着热流体和冷流体之间的热量传递。
在使用这种换热器时,不可避免地会使两种流体有少量混合,且必然是成对的使用,即当一个通入热流体时,另一个则通入冷流体,并靠自动阀进行交替切换,使生产得以连续进行。
(3)间壁式换热器它是利用一种固体壁面将进行热交换的两种流体隔开,使它们通过壁面进行传热。
这种形式的换热器使用最广泛。
2.按生产中使用目的分类即分为冷却器、加热器、冷凝器、汽化器(或再沸器)和换热器等。
3.按换热器所用材料分类一般可把换热器分成金属材料和非金属材料两类。
4.按换热器传热面的形状和结构分类它用于区分各种形式的间壁式换热器。
其分类有:
(1)通过管壁传热的换热器(即“管式”)①蛇管式换热器②套管式换热器③U型管式换热器:
这类换热器又可分为U型管式、U形管式和浮头式。
(2)通过板面传热的换热器(即“板面式”)①螺旋板式换热器②板式换热器③伞板式换热器④板翅式换热器⑤板壳式换热器(3)其它形式的换热器这类换热器一般都是为了满足某些特殊要求而出现的,有些还处于发展阶段,其中比较成熟的,如回转式换热器和热管等。
1.3U型管式换热器的设计U型管式换热器的设计资料较完善,已有系列化标准。
目前我国U型管式换热器的设计、制造、检验、验收按“钢制U型管式换热器”(GB151)标准执行。
U型管式换热器的设计和分析包括热力设计、流动设计、结构设计以及强度设计。
其中以热力设计最为重要。
不仅在设计一台新的换热器时需要进行热力设计,而且对于已生产出来的,甚至已投入使用的换热器在检验它是否满足使用要求时,均需进行这方面的工作。
热力设计指的是根据使用单位提出的基本要求,合理地选择运行参数,并根据传热学的知识进行传热计算。
流动设计主要是计算压降,其目的就是为换热器的辅助设备—例如泵的选择做准备。
当然,热力设计和流动设计两者是密切关联的,特别是进行热力计算时常需从流动设计中获取某些参数。
结构设计指的是根据传热面积的大小计算其主要零部件的尺寸,例如管子的直径、长度、根数、壳体的直径、折流板的长度和数目、隔板的数目及布置以及连接管的尺寸等等。
在某些情况下还需对换热器的主要零部件—特别是受压不均做应力计算,并校核其强度。
对于在高温高压下工作的换热器,更不能忽视这方面的工作。
这是保证安全生产的前提。
在做强度计算时,应尽量采用国产的标准材料和部件,根据我国压力容器安全技术规定进行计算或校核。
第二章换热器的工艺计算U型管式换热器的工艺设计只要包括以下内容:
1.根据换热任务和有关要求确定设计方案;2.初步确定换热器的结构和尺寸;3.核算换热器的传热面积和流体阻力;4.确定换热器的工艺结构。
2.1设计条件表2-1设计条件壳程管程流体名称混氢油反应产物总流量(t/h)25-----工作温度/进/出(℃)134/316370/210压力/(MPa)17.115.62.2确定物性数据在以上条件下,查得其基本物性数据为:
表2-2物性数据介质密度(kg/m3)比热容(KJ/kg×℃)黏度(Pa×s)导热系数(W/(m×℃))反应产物9944.1740.735×10-30.626混氢油7892.390.0115×10-30.0582.3符号说明0——热流体的密度,kg/m3;0——热流体的黏度,Pa×s;0——热联体的导热系数,W/(m×℃);——热流体的比热容,KJ/kg×℃;——冷流体的比热容,KJ/kg×℃;i——冷流体的密度,kg/m3i——冷流体的黏度,i——冷流体的导热系数,——换热管数目。
2.4流体走向的确定两流体为均不发生相变的传热过程,因反应产物的对流传热系数一般较大,且易结垢,故选择冷却反应产物走换热器的管程,混氢油走壳程。
2.5估算传热面积,初选换热器的规格2.5.1计算热负荷和冷却反应产物的用量=(2-1)=(2-2)式中——热流体的质量流量kg/s;——冷流体的质量流量kg/s;——热流体的比热容,KJ/kg×℃;——冷流体的比热容,KJ/kg×℃;——热流体始末的温度,℃;,——冷流体的始末温度,℃。
2.5.2计算两流体的平均温度差=230°C(2-3)而(2-4)查得:
。
所以(2-5)2.5.3初选换热器的规格根据两流体的情况,假设,故(2-6)式中——估算传热面积,;——实际传热面积,。
初步选用U型管式式换热器。
据此,由换热器系列标准初选换热器为下表所示:
表2-3初选换热器参数壳径/mm600管子尺寸/mm2025中心排管数16管长/m4.5管程流通面积/m20.0364管子总数241管程数2管子排列方法正三角形实际传热面积(2-7)若选择该型号的换热器,则要求过程的总传热系数为290w。
2.6换热管的排列和管心距—般说来,正三角形排列在相同的管板面积上可排较多的管子,而且管外表面传热系数较大,但正三角形排列时管外机械清洗较为困难,而认管外流体的流动阻力也较大。
在本设计中壳程中介质混氢油是非腐蚀性介质利于清洗,但由于是多管程结构,采用组合排列方法。
每一程内都采用正三角形排列,而在各程之间为了便于安装隔板,采用矩形排列方法。
所以本设计采用常规的正三角形排列。
管心距(mm)(2-9)按常用管心距表中查得管外径为25mm的管心距为t=32mm。
2.7折流板采用弓形折流板,取弓形折流板圆缺高度为壳体内径的25%,则切去的圆缺高度为取折流板间距B=0.3D=180mm。
则(块)(2-10)折流板圆缺面反应产物平装配。
2.8接管根据流体的操作情况及结构尺寸要求,取管程接管内流体流速为1.5m/s,则管程接管内径为(2-11)式中——管程接管内径,mm;——冷却反应产物的体积流量,m3/s;——冷却反应产物的流速,m/s。
取壳程接管内流体流速为0.5m/s,则壳程接管内径为(2-12)式中——壳程接管内径,mm;——混氢油的体积流量,m3/s;——混氢油的流速,m/s。
综合考虑无缝钢管标准尺寸、接管直径与筒体内径关系以及补强需要,取管程接管为,壳程接管为。
考虑经济性及焊接要求,接管材料选用20号钢。
2.9压强降的核算2.9.1管程压强降(2-13)式中——单程直管阻力,Pa;——局部阻力,Pa;——壳程数:
——管程数;——管程总阻力;——管程结构校正因数,量纲为1,对内径20mm外径25mm的管子,取1.4。
其中,=1,=2,=1.4。
管程流通面积(2-14)(2-15)(2-16)蛇管壁粗糙度,由关系图查得:
,所以(2-17)(2-18)则所以管程流体阻力在允许的范围内。
2.9.2壳程压强降(2-19)式中——流体横国管束的压强降,Pa;——流体通过折流板缺口的压强降,Pa;——壳程压强降的结垢校正因数,量纲为1,液体可取1.15。
=(2-20)(2-21)式中——管子排列方法对压强降的校正系数,对正三角形排列=0.5;——壳程流体的摩擦系数,当Re0>500时,;——横过管束中心线的管子数;——折流挡板数;h——折流挡板间距;——按壳程流通面积S0计算的流速,m/s。
其中=1.15,=1,16。
。
壳程流通面积(2-22)(2-23)(2-24)(2-25)所以=所以壳程流体阻力也在允许的范围内。
2.10总传热系数的核算2.10.1管程对流传热系数(2-26)(2-27)=0.023=2211.92.10.2壳程对流传热系数(2-28)取换热器列管之中心距t=32mm。
则流体通过管间最大截面积为(2-29)三角形排列时(2-30)(2-31)(2-32)壳程中混氢油被冷却,取。
所以==2.10.3总传热系数(2-33)====由前面的计算可知,选用该型号换热器时要求过程的总传热系数为,在规定的流动条件下,计算出的为,安全系数为%=20.3%此安全系数在15%~25%之内,所以符合要求。
第三章换热器的结构设计管程设计压力为17MPa,壳程设计压力为18MPa,取管程设计温度为454,壳程设计温度为400。
3.1筒体3.1.1材料的选取选取筒体材料为,钢板标准为,热轧钢板,=510,=345,在设计温度下,,,。
3.1.2结构尺寸由工艺计算并经圆整的内径为,所求出的面积裕量为20.3%,符合工艺要求,所以取是合适的。
工艺计算得到的相关参数不必更改。
筒体壁厚按GB151-1999,圆筒的最小厚度不得低于6mm。
3.1.3结构形式按标准GB151-1999,选择壳体型式可以选择代号为“E”的单壳程壳体,其结构型式如(图3-1):
图3-1壳体型式3.2管箱材料3.2.1材料的选取选取选管箱材料与筒体材料相同为,选用钢板标准为,热轧钢板,=510MPa,=345MPa,在设计温度下,。
3.2.2结构尺寸由于该换热器为单壳程、双管程,故选用B型封头管箱型。
管箱所要确定的尺寸主要是管箱长度。
管箱直径是由壳程直径决定。
管箱长度尺寸的确定是以保证流体分布均匀、流体合理以及强度因素来确定最小长度,而以制造安装方便来限制最大长度的。
因为右边管箱有接管,选取管箱总长为;选取左边管箱总长为200mm。
管箱壁厚按GB151-1999,管箱壁厚不得低于圆筒的最小厚度6mm。
3.3管箱法兰3.3.1材料的选取考虑焊接问题及经济性问题,选取法兰材料为Q345R,即用板材加工,选用标准为GB713-2008,=510MPa,=345MPa,在设计温度下,。
根据操作情况,又考虑螺栓材料的硬度一般要比螺母材料的硬度大一些以及经济性问题,螺栓材料选用CrMoA钢,螺母材料选用30CrMoA钢,选用标准均为,正火处理,工作适应温度为。
3.3.2结构尺寸根据换热器的设计压力仅为0.5MPa,工作介质对密封要求不高,选用甲型平焊法兰,采用凸面密封,选用标准为。
根据管箱公称直径选取管箱法兰参数如表3-1:
表3-1管箱法兰参数DN/mmD/mmD1/mmD2/mmb/mmd/mm螺栓规格螺栓数量6007156806373218M16243.3.3结构型式如(图3-2)所示:
图3-2管箱法兰3.4接管材料3.4.1材料的选取接管材料选用20号钢的无缝钢管,选用标准为GB/T8163-1999,,。
3.4.2结构尺寸壳程接管:
由壳体中走混氢油,其密度为ρ=789kg/m3,qm,s=*****kg/h,并由第二章求得的混氢油流速uo=0.14m/s。
考虑流阻影响接管直径应大于以上结果,再考虑原整取(接管外径),壁厚参考GB8163标准选择为5mm。
管程接管:
同以上方法,由工艺计算取为。
接管高度参照HG*****,按设计压力PN≤4.0MPa,查壳程接管伸出长度l=180mm;管程接管伸出长度l=180mm。
3.4.3结构型式图3-3接管图3-3接管3.5接管法兰3.5.1材料的选取根据设计压力,选用带颈平焊钢制法兰(SO型),采用突面形式密封,材料选用20Ⅱ,选用标准为。
3.5.2结构尺寸管箱接管公称直径为所选管箱接管法兰参数如表3-2:
表3-2管箱接管法兰参数DN/mmD/mmK/mmL/mmTh/mmn/mmC/mmB1/mm15026522518M16820161筒体接管公称直径为,所选筒体接管法兰参数如表3-3:
表3-3筒体接管法兰参数DN/mmD/mmK/mmL/mmTh/mmn/mmC/mmB1/mm15026522518M168201613.6垫片因换热器管程、壳程设计压力均为17及法兰密封形式,且两侧介质均不属于腐蚀性介质,故选用非金属软垫片即可。
综合考虑选择橡胶垫XB350,参数见表3-4:
表3-4垫片参数内径/mm垫片宽度/mm垫片系数/m比压力y硬度材料垫片厚度/mm600141.001.475橡胶板33.7管板3.7.1材料的选取考虑法兰和筒体材料以及实际工作情况,选取管板材料为Q345R。
查相关参考资料得:
。
3.7.2结构尺寸选择管板兼做法兰的结构,依据所选管箱法兰尺寸,如下表3-5:
3-5管板参数(mm)DNDD1D2D3D4D5cd2螺栓bfb60071568065059763760012.518M162430403.7.3结构型式图3-5带法兰管板3.8材料3.8.1材料的选取分程隔板应采用与封头、管箱同等材料,选用,选用钢板标准为,热轧钢板,=510MPa,=345MPa,在设计温度下,。
3.8.2结构尺寸壳体的公称直径为600mm,根据GB151-1999选取隔板最小厚度不得小于8mm.3.9换热管3.9.1材料的选取管子材料为无缝碳钢管,选用标准为,,,。
3.9.2结构尺寸由工艺计算选用无缝碳钢管型号,外径偏差为,厚度偏差为2.5。
3.9.3排列型式换热管按正三角形排列,间距t=32mm,排管总数为241,有两个管程,每程116根。
分程隔板槽两侧相邻的管中心距,即,取。
布管限定圆的直径,而,最小取8mm。
则。
具体排管如下:
图3-6排管图3.10拉杆3.10.1材料的选取拉杆材料为20号钢,,。
3.10.2结构尺寸由工艺计算得到尺寸如表3-6:
表3-6拉杆尺寸参数(mm)直径数量拉杆螺纹DNLaLb孔深164162060203.10.3结构型式图3-7拉杆3.11折流板的选取及布置3.11.1材料的选取由工艺计算得所需折流板24块,选取折流板材料为。
=375MPa,=235MPa,在设计温度下。
折流