机 械 制 造 技 术 基 础 期 未 作 业.docx
《机 械 制 造 技 术 基 础 期 未 作 业.docx》由会员分享,可在线阅读,更多相关《机 械 制 造 技 术 基 础 期 未 作 业.docx(21页珍藏版)》请在冰豆网上搜索。
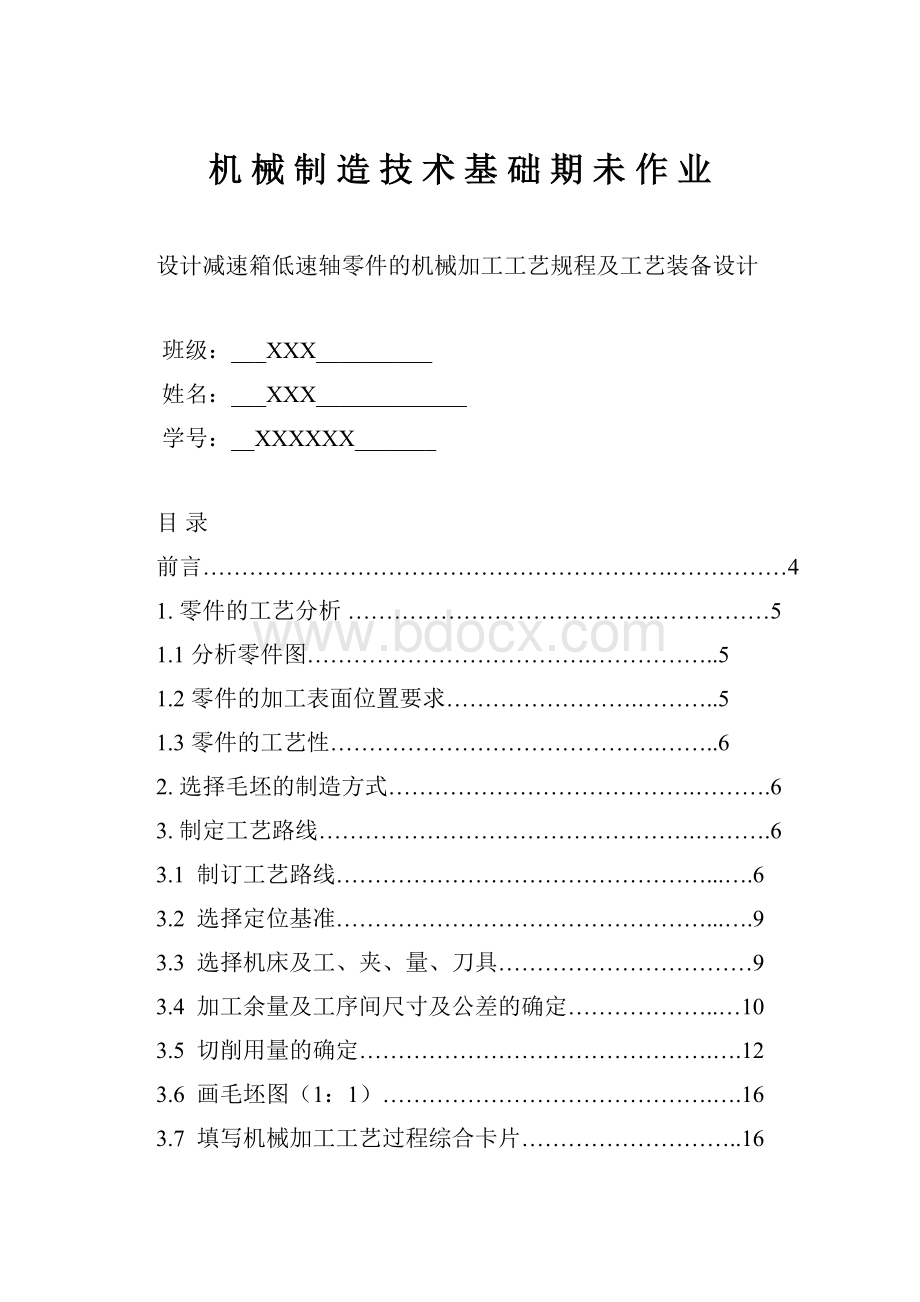
机械制造技术基础期未作业
设计减速箱低速轴零件的机械加工工艺规程及工艺装备设计
班级:
___XXX__________
姓名:
___XXX_____________
学号:
__XXXXXX_______
目录
前言…………………………………………………….……………4
1.零件的工艺分析………………………………….……………5
1.1分析零件图……………………………….……………..5
1.2零件的加工表面位置要求…………………….………..5
1.3零件的工艺性…………………………………….……..6
2.选择毛坯的制造方式………………………………….……….6
3.制定工艺路线………………………………………….……….6
3.1制订工艺路线…………………………………………...….6
3.2选择定位基准…………………………………………...….9
3.3选择机床及工、夹、量、刀具……………………………9
3.4加工余量及工序间尺寸及公差的确定………………..…10
3.5切削用量的确定……………………………………….….12
3.6画毛坯图(1:
1)…………………………………….….16
3.7填写机械加工工艺过程综合卡片………………………..16
4.工艺装备设计…………………………………………………..16
4.1确定设计方案,绘制结构原理示意图…………………....16
4.2选择定位元件,计算定位误差…………………………....17
4.3计算所需夹紧力,设计夹紧机构…………………………18
4.4画出夹具装配图……………………………………………19
附件………………………………………………………………..20
机械制造技术基础任务书
设计减速箱低速轴零件的机械加工工艺规程及工艺装备设计
(1,2组为低速轴,3、4组为中速轴,5、6组为高速轴)
内容:
1、生产纲领为中批或大量生产(1、3、5为中批,2、4、6为大量)
2、零件图1张
3、毛坯图1张
4、机械加工工艺过程综合卡片1张
5、工艺装备设计(铣键槽的夹具)图1套
班级:
_______xx__________
姓名:
_______xx____________
学号:
_______xxx______
前言
机械制造工艺规程的编制要求学生通过工艺设计获得综合运用所学过的全部课程进行工艺及结构设计的基本能力,也为以后的毕业设计进行一次综合训练和准备,并能得到下列各方面的锻炼:
1、运用机械制造技术基础课程中的基本理论正确地解决一个零件在加工过程中的定位、夹紧以及工艺路线的安排、工艺尺寸的确定、加工定位误差的计算等问题,保证加工质量,
2、提高结构设计能力。
学生通过设计夹具的训练,获得根据被加工零件的加工要求,设计高率,省力、经济合理而保证加工质量的夹具能力。
3、学会使用手册及图表的资料。
掌握与本设计有关的各种资料的名称、出处,能够做到熟练运用
一、零件的工艺分析
1、分析零件图
零件图是表达零件的形状、大小和特征,在生产中直接指导制造和检验零件,它是制造零件时的技术文件和依据。
零件图上的技术要求一般包括表面光洁度、尺寸偏差、表面形状偏差、表面相对位置偏差、某些特殊加工要求及装配要求,热处理和表面处理等要求。
2、零件的加工表面位置要求
低速轴需要加工的部分主要是回转面,长度为262mm。
轴的各个轴肩相邻处需要加工退刀槽,轴肩两端要进行倒角加工。
在轴径为Φ42和Φ58要加工键槽。
该低速轴需要加工的表面及加工表面之间的位置要求如下:
(1)Φ42表面粗糙度为1.6,外圆表面的圆跳动为0.012。
该段上面开有键槽,粗糙度为3.2,相对外圆的对称度为0.02。
(2)Φ48表面粗糙度为6.3,轴肩的粗糙度为3.2。
(3)Φ50表面粗糙度为0.8,同轴圆柱面之间的公差值为0.005,外圆表面的圆跳动为0.015。
(4)Φ58表面粗糙度为1.6,外圆表面的圆跳动为0.015,轴肩粗糙度为3.2。
该段上面开有键槽,槽底粗糙度为6.3,槽面粗糙度为3.2,相对外圆的对称度为0.02。
(5)Φ50,表面粗糙度为0.8,轴肩粗糙度为3.2,相对于Φ42外圆表面的圆跳动为0.015。
(6)其余表面粗糙度均为12.5。
3、零件的工艺
零件的材料选用45钢,其切削性能好,具有较高的强度和韧性等综合机械性能,适用于传递扭矩和承受载荷。
可切削性好。
为了保证技术要求,增加耐磨性,对零件进行调质处理。
二、选择毛坯的制造方式
考虑到轴在工作的时候经常要承受不稳定的冲击载荷,需要有较高的强度和冲击韧性,选用锻件。
因其采用中批生产,且零件的尺寸不大,故可用模锻成型。
可大量减少切削加工的劳动量,从而提高材料的利用率,降低机械加工的成本。
三、制定工艺路线
1、制订工艺路线
本零件的加工面有外圆,端面,槽等。
其加工方法如下:
端面尺寸要求不高,车削即可。
键槽加工键槽,铣键槽。
外圆公差等级和粗糙度要求不同,选择粗车,半精车,精车等加工方法。
各个轴径的选择要求如下:
(1)Φ48,Φ58,Φ64三个外圆面未标注公差尺寸,根据GB1800-79规定其公差等级按IT12,表面粗糙度为Ra6.3,需要进行粗车。
(2)Φ50有公差要求,公差等级为IT7,表面粗糙度为Ra0.8,可采用粗车→半精车→精车→磨削。
(3)Φ42,Φ58有公差要求,公差等级为IT7,表面粗糙度为Ra1.6,可采用粗车→半精车→精车。
(4)槽的槽深公差等级分别为IT13,IT14。
其表面粗糙度分别为Ra3.2和Ra6.3。
采用粗铣,半精铣。
该零件的加工质量要求比较高,因此加工阶段划分为:
粗加工、半精加工、精加工、磨削加工四个阶段。
由以上的分析可得到如下的方案:
方案一
序号
工序内容
设备
工序1
车两端面,钻中心孔
车床
工序2
车外圆,切槽,倒角
车床
工序3
铣键槽
磨床
工序4
去毛刺
钳工
工序5
磨外圆
磨床
工序6
终检
方案二
序号
工序内容
工序1
两边同时车铣端面,钻中心孔
工序2
粗车轴上的各外圆表面,半精车Φ64
工序3
以Φ64和左端面孔定位,半精车轴左部的所有外表面
工序4
以Φ64和右端面孔定位,半精车轴右部的所有外表面
工序5
以两端面孔定位切退刀槽,倒角
工序6
铣键槽
工序7
磨削各外圆
工序8
终检
方案分析:
对于方案一,工序比较集中,这样能减少工件安装的次数,有利于保证位置公差要求,减少辅助时间,提高劳动生产率。
对于小批量而言确实能降低生产成本;但本题要求中批生产,反而会使生产成本增加。
对于方案二,工序比较分散,采用端面孔定位加工各轴的表面,会使各表面产生加工误差。
综合以上两个方案的优点,制定一个最优方案如下:
序号
工序内容
设备
工序1
车两端面,钻中心孔
组合机床
工序2
粗车外圆
车床
工序3
精车外圆,Φ42Φ50Φ58切退刀槽,倒角
车床
工序4
铣键槽
铣床
工序5
去毛刺
钳工
工序6
磨外圆面H,M,G,P,N
磨床
工序7
终检
2、选择定位基准
粗基准的选择:
根据粗基准的选择原则,为了使加工表面有足够而均匀的加工余量,应该选择毛坯上面加工余量小而均匀的重要表面为粗基准。
对于轴类而言,一般以外圆为粗基准。
对该轴来说,Φ64mm的外圆表面精度较小,故其加工余量也会小,从而可以作为粗基准加工其两边的表面。
加工两端面时,两个表面相互位置精度要求较高时,两个表面互为基准反复加工,可以不断提高定位基准的精度。
精基准的选择:
根据基准不变的原则,轴类零件在整个加工过程中大部分工序都以两个顶尖孔为定位基准。
可以保证其相互位置精度,使各表面之间达到很高的位置精度。
同时,各工序所用的夹具统一,从而减少了设计和制造夹具的时间和费用,有利于提高生产率。
3、选择机床及工、夹、量、刀具
机床的选择:
为了保证加工质量,又要经济合理,机床选用CA6140卧式车床,831005,M131W。
夹具的选择:
车床专用夹具,铣床专用夹具,三爪自定心卡盘,V型块。
量具的选择:
本零件属于中批量生产,一般情况下尽量使用通用量具,根据零件表面的精度要求和形状特点。
外圆表面的公差等级为7级,在粗车、半精车中使用读书值0.02测量范围0-500游标卡尺,在精车中因为批量较大,为提高测量效率,故采用专用卡规测量。
百分尺。
刀具的选择:
查表1.1,YT类硬质合金刀,粗加工YT5,半精加工YT15,精加工YT30。
镗刀,切槽刀采用低速钢。
端面用直柄立铣车刀;磨削外圆用PZA400x50x203A80M4V35。
4、加工余量及工序间尺寸及公差的确定
已知机械加工后轴的重量为0.8kg,由此初步估计机械加工前铸件的毛坯重量为1kg。
由于该轴材料为45钢,是碳的质量分数大于0.65%的碳素钢,该铸件的采制系数属M1级。
轴经锻造后应安排退火,正火,以消除残留的锻造应力,并使不均匀的金相组织通过重新结晶而得到细化,均匀的组织,从而改善加工性能。
确定加工余量时,只需将零件的尺寸加上余量值即可。
若只需粗加工时,可取所查数据中的较小值,反而取较大值。
则其毛坯尺寸如下:
零件尺寸
单面加工尺寸
毛坯尺寸
Φ42
3
Φ48
Φ48
1.5
Φ51
Φ50
2
Φ54
Φ58
3
Φ64
Φ64
1.5
Φ67
Φ58
1.5
Φ61
Φ50
2
Φ54
由零件图,低速轴毛坯尺寸的允许偏差为:
尺寸
尺寸偏差
Φ42
+0.050
+0.034
Φ50
+0.021
+0.002
Φ50
+0.021
+0.002
Φ58
+0.060
+0.041
加工表面加工余量偏差的确定:
加工表面
工序双边余量
工序尺寸及公差
表面粗糙度
粗
半精
精
粗
半精
精
粗
半精
精
Φ42
3.4
2.2
0.2
Φ42±0.01
Ra6.3
Ra3.2
Ra0.8
Φ48
3
Φ48±0.01
Ra6.3
Φ50
2.4
2.2
0.2
Φ52.4±0.01
Φ52.2±0.01
Φ50.2±0.01
Ra6.3
Ra3.2
Ra0.8
Φ58
3.4
2.2
0.2
Φ61.4±0.01
Φ60.2±0.01
Φ58.2±0.01
Ra6.3
Ra3.2
Ra0.8
Φ64
3
Φ67±0.01
Ra6.3
Φ58
3
Φ61±0.01
Ra6.3
Φ50
2.4
2.2
0.2
Φ52.4±0.01
Φ52.2±0.01
Φ50.2±0.01
Ra6.3
Ra3.2
Ra0.8
5、切削用量的确定
(1)车两端面,打中心孔,粗车Φ48,Φ58,Φ64,表面粗糙度值为Ra6.3。
加工条件:
45钢,模锻,正火
机床:
CA6140
刀具:
刀片材料为YT15,刀杆尺寸16×25。
Kr=90°,r0=15°,a0=12°,rR=0.5mm。
粗车Φ64
确定端面的最大加工余量:
已知毛坯长度方向的余量为2(-0.7~1.5)。
考虑7°的锻模拔模斜度,则毛坯的最大加工余量为8mm。
分两次加工,切削深度为2mm,公差为IT13。
计算切削速度
按《切削手册》表1.27,切削速度公式为(刀具寿命选T=60min)
式中Cv=242xv=0.15yv=0.35m=0.2
修正系数km=1.44Ks=0.8Kk=1.04kr=0.81Kbv=0.97
所以V=108.6m/min
主轴转速n=1000×V/π×d=1000×108.6/(3.14×64)=500r/min
切削时T=l/(n×f)=10/(0.52×500)=0.038min
粗车50
切削深度:
单边余量为2mm可一次切削
进给量:
f=0.50
切削速度
得V=116m/min
主轴速度:
n=1000×V/π×d=1000×116/(3.14×64)=577r/min
按照机床说明书,则去n=560r/min
切削工时T=l/(n×f)=0.136min
验证机床功率:
主切削力F计算公式
F=cf×apxv×fyv×km
式中cf=2880xv=1.0yv=0.75km=0.94kr=0.89
所以F=2780N
P=f×v/(6×1000)=6.43kw
由《切削手册》机床说明书可知CA6140卧式车床主电动机的功率为7.5kw。
所以机床的功率足够,能够保证正常加工。
验证机床进位系统强度
已知主切削力F=2780N,径向切削力Fp按《切削手册》有计算公式Fp=279N
轴向切削力Ff按《切削手册》有Ff=1292N
取机床导轨与床鞍之间的摩擦系数μ=0.1则切削力在纵向进给方向上对进给机构的作用力
F=Ff+μ(Fp+F)=1597.9N
小于机床纵向方向可以承受的最大纵向力。
所以系统可以正常工作。
粗车时各轴径的切削用量和基本时间
工步
切削深度
进给量
切削速度
车床速度
基本时间
Φ42
3
0.5
118.7
900
0.182
Φ48
3
0.5
107
710
0.101
Φ50
2
0.5
116
560
0.136
Φ58
3
0.5
138
760
0.179
Φ64
4
0.5
108.6
500
0.038
Φ58
3
0.5
138
760
0.021
Φ50
2
0.5
116
560
0.071
精车时各轴径的切削用量和基本时间
工步
切削深度
进给量
切削速度
车床转速
基本时间
Φ42
1.2
0.3
150
1200
0.228
Φ50
1.2
0.3
150
1200
0.106
Φ58
1.2
0.3
150
1200
0.189
Φ50
1.2
0.3
150
1200
0.056
铣键槽
背吃刀量确定i=h/ap通常i=1即一次铣削到规定深度ap=h=3.5mm
进给量确定按机床功率为1.5kw,工件-夹具系统刚度为中等条件选取,该工序的每齿进给量为0.04
铣削速度的计算按镶齿铣刀d/z=80/10的条件选取,铣削速度v可取44.9m/min。
有公式5-1n=1000v/πd可求得该工序铣刀转速,n=178.65r/min,参照831005型立式铣床的主轴转速,去主轴转速n=188r/min,即求得铣削速度v=47.22m/min
基本时间Tj=【(l+l1+l2)*i】/fmz
L1=0.5d+(1~2)l2=l-3
可得Tj=62.5s
磨削
选择砂轮,WA46kv6P350×40
切削用量砂轮转速为n=1500r/min
砂轮切削速度V=27.3m/s
f=0.5轴向方向的进给量B=20mm
工件速度V=10m/min
径向方向的进给量f=0.015/20
切削加工时T=(2×L×b×Z×b×k)/(1000×v×Fa×Fv)
L加工长度8236386810820
b加工宽度42485058645850
Z单边加工余量0.1
k系数1.10
v工作台移动速度
Fa工作台往返一次砂轮轴向进给量
Fv工作台往返一次砂轮轴向进给量
T=2×(8+10+20+36+38+68+82)×(42+48+50+50+58+58+64)×0.1×1.10/(1000×10×20×0.015)
=7.11min
6、画毛坯图(1:
1)
附图1
7、填写机械加工工艺过程综合卡片
附图2
四、工艺装备设计
1)确定设计方案,绘制结构原理示意图。
本工序加工键槽,保证轴肩与键槽右端的长度为11,和外圆到键槽底部的距离为360-0.2及键宽140-0.043,为了提高劳动生产率,保证加工质量,降低劳动强度,需要设计专用夹具。
该工序在立式铣床X5012上加工,零件属于中批量生产。
根据工件的加工要求,该工件必须限制工件的五个自由度,即X移动,X转动,Z移动,Y移动,Y转动,用V型块接触限制X移动,X转动,Y移动,Y转动,挡住Z移动。
为了保证定位的精度需要在外圆面上加一个压板。
2)选择定位元件,计算定位误差。
由零件图可知,Φ42+0.050+0.034二孔端对孔中心线有平行度和对称度要求,设计基准以孔中心线。
为了使误差为零,应选选择自动定心夹具,同时为了提高加工效率,两个孔端面同时加工,为了缩短辅助时间,准备采用气动夹紧。
由于此工序工件的定位是外圆,夹具上相应的定位元件选为V型块和压板。
(1)计算Φ42+0.050+0.034二孔外端面铣加工后与键孔中心线的最大平行度误差
键孔与定位轴外径的最大间隙为
△max=0.050-0.034=0.016
由于孔外端面还有进行磨削加工,故上述下平行度误差值是可以允许。
(2)工序基准为左端面,定位基准是外圆中心线,其联系尺寸为11定位尺寸,引起工序基准相对定位基准在加工尺寸方向上产生的最大变化量为0,所以
△jb=0
工件以中心孔定位,定位基准是中心孔
△db=0
因此,△dw=△jb+△db=0<1/3T即满足要求。
3)计算所需夹紧力,设计夹紧机构。
刀具:
低速钢镶齿三面刃铣刀,Φ225mm,Z=20
其中:
CF=650αp=3.1mmXF=1.0fz=0.08mmyF=0.72
Αe=40mmμF=0.86dD=225mmqF=0.86ωF=0z=20
∴F=1456N
当用两把刀铣削时,F’=2F=2912N
水平分力:
F1=1.1F’=3230N
垂直分力:
F2=0.3F’=873N
在计算切削力时,必须把安全系数考虑在内,安全系数K
基本安全系数1.5
加工性质系数1.1
刀具钝化系数1.1
断续切削系数1.1
∴Q=F1K=6395N
选用气缸一斜锲夹紧机构,锲角α=10°其结构形式选用Ⅳ型
则扩大比i=3.42为克服水平切削力,夹具定位面及夹紧面上的摩擦系数为0.25,实际夹紧力N为
N=12790N
气缸选用Φ100mm。
当压缩空气单位压力P=0.5Mpa时,气缸推力为3900N,故实际夹紧力为:
Q=3900i=13338N
此时Q大于所需的夹紧力,故夹具可安全工作。
4)画出夹具装配图。
附件:
毛坯图
机械加工工艺过程卡片
机械加工工艺过程卡片
产品型号
零件图号
产品名称
零件名称
低速轴
共1页
第1页
材料牌号
45钢
毛坯种类
锻件
毛坯外形尺寸
Φ67
长266
每毛坯可制件数
1
每台件数
1
备注
工序号
工序
工序内容
车间
工段
设备
工艺装备
工时
准终
单件
5
下料
锯棒料Φ67长266
锯床
锯尺卡尺
15
车
车两端面,钻中心孔
车床CA6140
车刀、卡尺、三爪自定心卡盘
25
车
粗车外圆
车床CA6140
车刀、卡尺、三爪自定心卡盘
35
车
精车外圆,Φ42Φ50Φ58切退刀槽,倒角
车床CA6140
车刀、卡尺、三爪自定心卡盘
45
铣
铣键槽
铣床
专用夹具、卡尺、铣刀
55
磨
去毛刺
磨床
顶装、砂轮、卡尺
65
磨
磨外圆面H,M,G,P,N
磨床
顶装、砂轮、卡尺
75
检验
终检
塞规、百分表、卡尺
设计(日期)
审核(日期)
标准(日期)
会签(日期)
标记
处数
更改文件号
签字
日期
标记
处数
更改文件号
签字
粗车
机械加工工序卡片
产品型号
零件图号
产品名称
零件名称
低速轴
共1页
第1页
车间
工序号
工序名称
材料牌号
25
粗车
45钢
毛坯种类
毛坯外形尺寸
每毛坯可制件数
每台件数
锻件
1
1
设备名称
设备型号
设备编号
同时加工件数
车床
CA6140
1
夹具编号
夹具名称
切削液
三爪自定心卡盘
工位器具编号
工位器具名称
工序工时
准终
单件
工步号
工步内容
工艺设备
主轴转速r/min
切削速度mm/min
进给量mm/r
背吃刀量mm
进给次数
工步工时
机动
辅助
1
装夹工件
三爪自定心卡盘、车刀
0.5
2
2
2
粗车外圆
3
500
108.6
4
560
116
5
710
107
6
760
138
7
900
118.7
设计(日期)
审核(日期)
标准(日期)
会签(日期)
标记
处数
更改文件号
签字
日期
标记
处数
更改文件号
签字
日期
精车
机械加工工序卡片
产品型号
零件图号
产品名称
零件名称
低速轴
共1页
第1页
车间
工序号
工序名称
材料牌号
35
精车
45钢
毛坯种类
毛坯外形尺寸
每毛坯可制件数
每台件数
锻件
1
1
设备名称
设备型号
设备编号
同时加工件数
车床
CA6140
1
夹具编号
夹具名称
切削液
三爪自定心卡盘
工位器具编号
工位器具名称
工序工时
准终
单件
工步号
工步内容
工艺设备
主轴转速r/min
切削速度mm/min
进给量mm/r
背吃刀量mm
进给次数
工步工时
机动
辅助
1
精车外圆
三爪自定心卡盘、车刀
1200
150
0.15
2
2