4烧结车间生产过程中职业有害因素分析.docx
《4烧结车间生产过程中职业有害因素分析.docx》由会员分享,可在线阅读,更多相关《4烧结车间生产过程中职业有害因素分析.docx(40页珍藏版)》请在冰豆网上搜索。
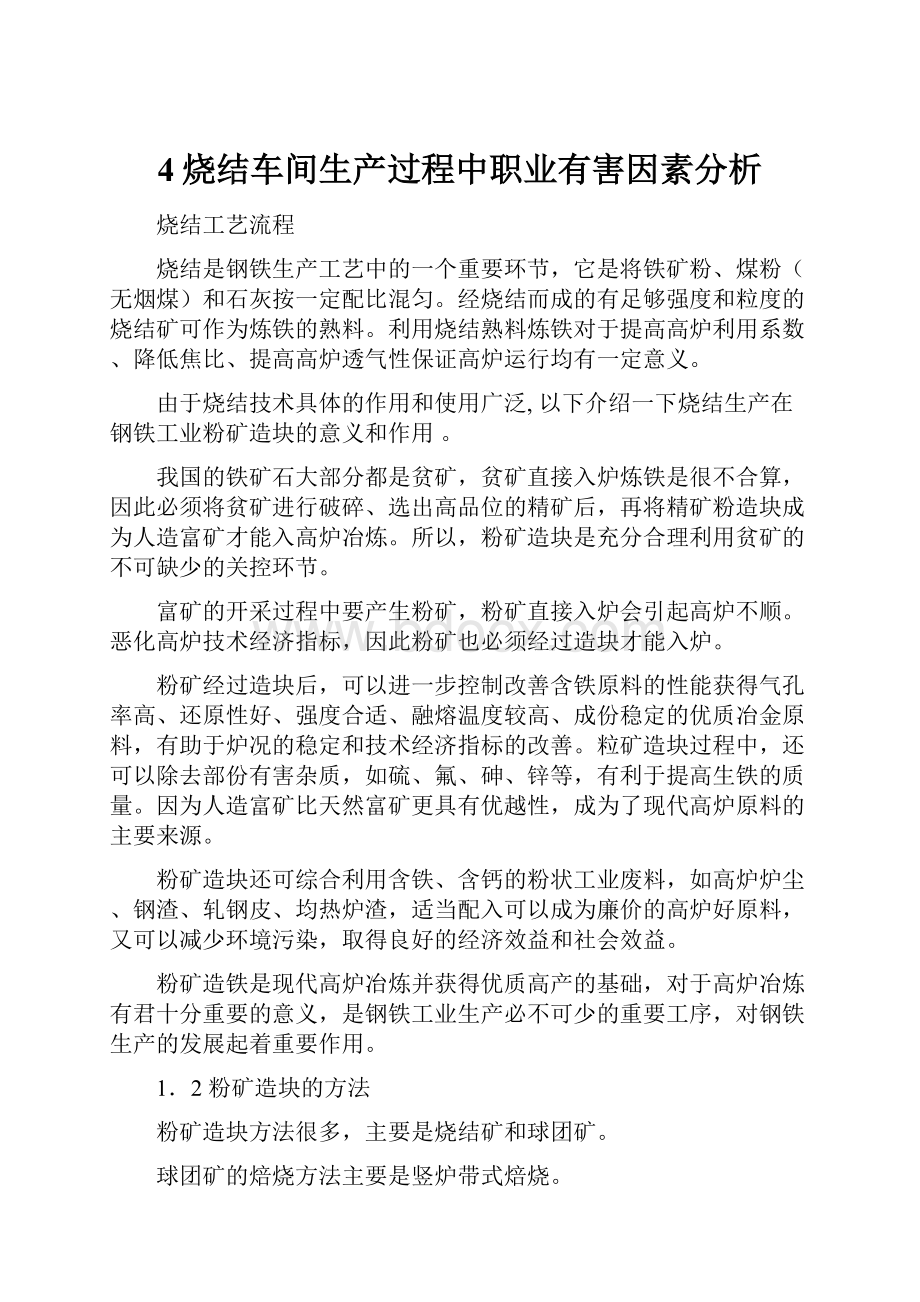
4烧结车间生产过程中职业有害因素分析
烧结工艺流程
烧结是钢铁生产工艺中的一个重要环节,它是将铁矿粉、煤粉(无烟煤)和石灰按一定配比混匀。
经烧结而成的有足够强度和粒度的烧结矿可作为炼铁的熟料。
利用烧结熟料炼铁对于提高高炉利用系数、降低焦比、提高高炉透气性保证高炉运行均有一定意义。
由于烧结技术具体的作用和使用广泛,以下介绍一下烧结生产在钢铁工业粉矿造块的意义和作用。
我国的铁矿石大部分都是贫矿,贫矿直接入炉炼铁是很不合算,因此必须将贫矿进行破碎、选出高品位的精矿后,再将精矿粉造块成为人造富矿才能入高炉冶炼。
所以,粉矿造块是充分合理利用贫矿的不可缺少的关控环节。
富矿的开采过程中要产生粉矿,粉矿直接入炉会引起高炉不顺。
恶化高炉技术经济指标,因此粉矿也必须经过造块才能入炉。
粉矿经过造块后,可以进一步控制改善含铁原料的性能获得气孔率高、还原性好、强度合适、融熔温度较高、成份稳定的优质冶金原料,有助于炉况的稳定和技术经济指标的改善。
粒矿造块过程中,还可以除去部份有害杂质,如硫、氟、砷、锌等,有利于提高生铁的质量。
因为人造富矿比天然富矿更具有优越性,成为了现代高炉原料的主要来源。
粉矿造块还可综合利用含铁、含钙的粉状工业废料,如高炉炉尘、钢渣、轧钢皮、均热炉渣,适当配入可以成为廉价的高炉好原料,又可以减少环境污染,取得良好的经济效益和社会效益。
粉矿造铁是现代高炉冶炼并获得优质高产的基础,对于高炉冶炼有君十分重要的意义,是钢铁工业生产必不可少的重要工序,对钢铁生产的发展起着重要作用。
1.2粉矿造块的方法
粉矿造块方法很多,主要是烧结矿和球团矿。
球团矿的焙烧方法主要是竖炉带式焙烧。
烧结方法主要有吹风烧结法和抽风烧结法两大类。
国内外普遍采用的是常式抽风烧结机。
所谓“烧结”就是指粉状物料加热到熔点以下而粘结成固体的现象.
烧结过程简单来说,就是把品位满足要求,但粒度却不满足的精矿和其他辅助原料混合后在烧结机上点火燃烧,重新造块,以满足高炉的要求。
点火器就是使混合料在烧结机上燃烧的关键设备,控制好点火器的温度、负压等,混合料才能成为合格的烧结成品矿。
烧结的主要工序是:
配料,混料,看火等。
看火的经验:
看火主要控制的三点温度是;点火温度,终点温度,和总管废气温度。
铁矿粉造块
铁矿粉造块目前主要有两种方法:
烧结法和球团法。
两种方法所获得的块矿分别为烧结矿和球团矿。
铁矿粉造块的目的:
◆综合利用资源,扩大炼铁用的原料种类。
◆去除有害杂质,回收有益元素,保护环境。
◆改善矿石的冶金性能,适应高炉冶炼对铁矿石的质量要求。
一、铁矿粉烧结生产
1.烧结的概念
将各种粉状含铁原料,配入适量的燃料和熔剂,加入适量的水,经混合和造球后在烧结设备上使物料发生一系列物理化学变化,将矿粉颗粒黏结成块的过程。
2.烧结生产的工艺流程
目前生产上广泛采用带式抽风烧结机生产烧结矿。
主要包括烧结料的准备,配料和混合,烧结和产品处理等工序。
图2-4 抽风烧结工艺流程
◆烧结原料的准备
①含铁原料
含铁量较高、粒度<5mm的矿粉,铁精矿,高炉炉尘,轧钢皮,钢渣等。
一般要求含铁原料品位高,成分稳定,杂质少。
②熔剂
要求熔剂中有效CaO含量高,杂质少,成分稳定,含水3%左右,粒度小于3mm的占90%以上。
在烧结料中加入一定量的白云石,使烧结矿含有适当的MgO,对烧结过程有良好的作用,可以提高烧结矿的质量。
③燃料
主要为焦粉和无烟煤。
对燃料的要求是固定碳含量高,灰分低,挥发分低,含硫低,成分稳定,含水小于10%,粒度小于3mm的占95%以上。
对入厂烧结原料的一般要求见表2—2。
表2-2 入厂烧结原料一般要求
◆配料和混合
①配料
配料目的:
获得化学成分和物理性质稳定的烧结矿,满足高炉冶炼的要求。
常用的配料方法:
容积配料法和质量配料法。
容积配料法是基于物料堆积密度不变,原料的质量和体积成比例这一条件进行的。
准确性较差。
质量配料法是按原料的质量配料。
比容积法准确,便于实现自动化。
②混合
混合目的:
使烧结料的成分均匀,水分合适,易于造球,从而获得粒度组成良好的烧结混合料,以保证烧结矿的质量和提高产量。
混合作业:
加水润湿、混匀和造球。
根据原料性质不同,可采用一次混合或二次混合两种流程。
一次混合的目的:
润湿和混匀,当加热返矿时还可使物料预热。
二次混合的目的:
继续混匀,造球,以改善烧结料层透气性。
用粒度10~Omm的富矿粉烧结时,因其粒度已经达到造球需要,采用一次混合,混合时间约50s。
使用细磨精矿粉烧结时,因粒度过细,料层透气性差,为改善透气性,必须在混合过程中造球,所以采用二次混合,混合时间一般不少于2.5~3min。
我国烧结厂大多采用二次混合。
◆烧结生产
烧结作业是烧结生产的中心环节,它包括布料、点火、烧结等主要工序。
①布料
将铺底料、混合料铺在烧结机台车上的作业。
当采用铺底料工艺时,在布混合料之前,先铺一层粒度为10~25mm,厚度为20~25mm的小块烧结矿作为铺底料,其目的是保护炉箅,降低除尘负荷,延长风机转子寿命,减少或消除炉箅粘料。
铺完底料后,随之进行布料。
布料时要求混合料的粒度和化学成分等沿台车纵横方向均匀分布,并且有一定的松散性,表面平整。
目前采用较多的是圆辊布料机布料。
②点火
点火操作是对台车上的料层表面进行点燃,并使之燃烧。
点火要求有足够的点火温度,适宜的高温保持时间,沿台车宽度点火均匀。
点火温度取决于烧结生成物的熔化温度。
常控制在1250±50℃。
点火时间通常40~60s。
点火真空度4~6kPa。
点火深度为10~20mm。
③烧结
准确控制烧结的风量、真空度、料层厚度、机速和烧结终点。
烧结风量:
平均每吨烧结矿需风量为3200m3,按烧结面积计算为(70~90)m3/(cm2.min)。
真空度:
决定于风机能力、抽风系统阻力、料层透气性和漏风损失情况。
料层厚度:
合适的料层厚度应将高产和优质结合起来考虑。
国内一般采用料层厚度为250~500mm。
机速:
合适的机速应保证烧结料在预定的烧结终点烧透烧好。
实际生产中,机速一般控制在1.5~4m/min为宜。
烧结终点的判断和控制:
控制烧结终点,即控制烧结过程全部完成时台车所处的位置。
中小型烧结机终点一般控制在倒数第二个风箱处,大型烧结机控制在倒数第三个风箱处。
带式烧结机抽风烧结过程是自上而下进行的,沿其料层高度温度变化的情况一般可分为5层,各层中的反应变化情况如图2—5所示。
点火开始以后,依次出现烧结矿层,燃烧层,预热层,干燥层和过湿层。
然后后四层又相继消失,最终只剩烧结矿层。
图2-5烧结过程各层反应示意图
①烧结矿层
经高温点火后,烧结料中燃料燃烧放出大量热量,使料层中矿物产生熔融,随着燃烧层下移和冷空气的通过,生成的熔融液相被冷却而再结晶(1000—1100℃)凝固成网孔结构的烧结矿。
这层的主要变化是熔融物的凝固,伴随着结晶和析出新矿物,还有吸入的冷空气被预热,同时烧结矿被冷却,和空气接触时低价氧化物可能被再氧化。
②燃烧层
燃料在该层燃烧,温度高达1350~1600℃,使矿物软化熔融黏结成块。
该层除燃烧反应外,还发生固体物料的熔化、还原、氧化以及石灰石和硫化物的分解等反应。
③预热层
由燃烧层下来的高温废气,把下部混合料很快预热到着火温度,一般为400~800℃。
此层内开始进行固相反应,结晶水及部分碳酸盐、硫酸盐分解,磁铁矿局部被氧化。
④干燥层
干燥层受预热层下来的废气加热,温度很快上升到100℃以上,混合料中的游离水大量蒸发,此层厚度一般为l0~30mm。
实际上干燥层和预热层难以截然分开,可以统称为干燥预热层。
该层中料球被急剧加热,迅速干燥,易被破坏,恶化料层透气性。
⑤过湿层
从干燥层下来的热废气含有大量水分,料温低于水蒸气的露点温度时,废气中的水蒸气会重新凝结,使混合料中水分大量增加而形成过湿层。
此层水分过多,使料层透气性变坏,降低烧结速度。
烧结过程中的基本化学反应
①固体碳的燃烧反应
固体碳燃烧反应为:
反应后生成C0和C02,还有部分剩余氧气,为其他反应提供了氧化还原气体和热量。
燃烧产生的废气成分取决于烧结的原料条件、燃料用量、还原和氧化反应的发展程度、以及抽过燃烧层的气体成分等因素。
②碳酸盐的分解和矿化作用
烧结料中的碳酸盐有CaC03、MgC03、FeC03、MnC03等,其中以CaC03为主。
在烧结条件下,CaC03在720℃左右开始分解,880℃时开始化学沸腾,其他碳酸盐相应的分解温度较低些。
碳酸钙分解产物Ca0能和烧结料中的其他矿物发生反应,生成新的化合物,这就是矿化作用。
反应式为:
CaCO3+SiO2=CaSiO3+CO2
CaCO3+Fe2O3=CaO·Fe2O3+CO2
如果矿化作用不完全,将有残留的自由Ca0存在,在存放过程中,它将同大气中的水分进行消化作用:
CaO+H2O=Ca(OH)2
使烧结矿的体积膨胀而粉化。
③铁和锰氧化物的分解、还原和氧化
铁的氧化物在烧结条件下,温度高于l300℃时,Fe203可以分解:
Fe304在烧结条件下分解压很小,但在有Si02存在、温度大于1300℃时,也可能分解:
二、球团矿生产
1.球团矿的概念
把细磨铁精矿粉或其他含铁粉料添加少量添加剂混合后,在加水润湿的条件下,通过造球机滚动成球,再经过干燥焙烧,固结成为具有一定强度和冶金性能的球型含铁原料。
2.球团矿生产迅速发展的原因:
◆天然富矿日趋减少,大量贫矿被采用。
铁矿石经细磨、选矿后的精矿粉,品位易于提高。
过细精矿粉用于烧结生产会影响透气性,降低产量和质量。
细磨精矿粉易于造球,粒度越细,成球率越高,球团矿强度也越高。
◆球团法生产工艺的成熟。
从单一处理铁精矿粉扩展到多种含铁原料。
生产规模和操作也向大型化、机械化、自动化方向发展。
技术经济指标显著提高。
球团产品也已用于炼钢和直接还原炼铁等。
◆球团矿具有良好的冶金性能:
粒度均匀、微气孔多、还原性好、强度高,有利于强化高炉冶炼。
3.球团矿生产的工艺流程
一般包括原料准备、配料、混合、造球、干燥和焙烧、冷却、成品和返矿处理等工序,如图2-6所示。
图2-6 球团矿生产的工艺流程
烧结车间生产过程中职业有害因素分析
1粉尘
烧结过程中机头产生含尘烟气,其中含有一定数量的SO2等有害气体;另外在生产过程中物料破碎、混合等工序以及转运过程中、机尾、整粒系统产生粉尘,成分复杂的颗粒物;烟气温度高、颗粒物黏度大,含有硫、铝、锌、氟、一氧化碳、二氧化硅等有害成分,如果各工序段扬尘点密封罩密封不严,除尘器故障,或者卸灰阀故障堵塞,不及时清理,也可能烧结机本体、风机等受烟气长期腐蚀密封性不好,粉尘可能散发到车间,车间如果通风不良,对工作人员可能造成职业病伤害。
2噪声和振动
烧结厂的噪声主要来源于高速运转的设备。
这些设备主要有主风机、冷风机、通风除尘机、振动筛、四辊破碎机、抽风机、环冷机冷却风机、除尘系统的风机和助燃风机,以及成品和燃料的筛分设备、水泵。
如果不选用低噪声设备又不安装消声器、消音隔声设施,则可能导致工作岗位的噪声超标,长期在这种环境中工作,可能引发员工职业病伤害。
3中毒
工业点火炉点火燃料为煤气,煤气含有氢气、一氧化碳等可燃成分,如果和空气配比不恰当,未充分燃烧的煤气停留在炉内,检修时吹扫不彻底,或者煤气管道由于缺陷或者腐蚀导致泄露,未及时发现,通风不畅,可能引发工作人员中毒。
4高温
生产过程中,烧结机、工业炉、高炉返矿缓冲槽等设备均不同程度放散出大量辐射热和对流热,车间内气温较高,尤其在夏季,当室外环境温度较高和空气相对湿度较大时,岗位人员、检修人员机体可出现热蓄积,即机体产热和受热和散热平衡的破坏,体温升高,易发生中暑。
高温主要影响人体的体温调节和水盐代谢及循环系统,还可以抑制中枢神经系统,使工人在作业中注意力分散,准确性下降,易疲劳,而引发工伤事故。
烧结生产主要危险源及主要事故类别和原因
危险源:
高温、粉尘、高速机械转动、有毒有害气体、高处作业等危害;
事故类别:
机械伤害、高处坠落、物体打击、起重伤害、灼烫、触电、中毒以及尘肺等8类;
事故原因:
设备缺陷、技术和工艺缺陷、防护装置缺陷、作业环境差,规章制度不完善和违章作业等。
插入案例:
1、炼铁分厂烧结车间“2.25”险肇事故通报
炼铁分厂烧结车间2月25日发生一起险肇事故,现将事故情况通报如下;
一、事故经过:
2月25日下午14:
20分左右,烧结车间维修二段钳二班在检修更换烧结机2#大烟道灰斗时,班长柳昌岐负责在上面对一个灰斗进行切割作业;副班长张晓平带领赵可江等人负责旁边另一个灰斗的拆除任务,张晓平负责现场外围监护工作,当他确认现场安全后,通知上面检修人员割除灰斗,灰斗被割除后在下落途中,检修人员赵可江突然从旁边穿出,头部碰在下落的灰斗边沿上,头部被安全帽边沿擦伤。
二、事故原因:
1、检修人员赵可江本人安全意识淡薄,对现场的危险因素未进行确认就穿越检修现场。
2、检修人员拆除灰斗时,未对灰斗作任何捆绑、牵引,作业过程安全措施不到位。
3、烧结车间在检修现场安全管理措施没有落实到位,现场无安全警示牌和安全警戒线。
4、现场监护确认不到位。
5、现场备件放置杂乱,阻挡了监护人的视线。
2、关于对炼铁分厂烧结车间“5.3”工亡事故的处理报告
2009年5月3日炼铁分厂4#烧结机在停产检修过程中发生一起安全事故,具体情况汇报如下:
一、事故经过
炼铁分厂烧结车间75㎡烧结机工程属新建项目,2009年4月16日到4月22日经试生产结束后,75㎡烧结机全线停产,炼铁分厂对75㎡烧结机工程存在的安全、环保、生产、设备、防汛等方面存在的问题,并结合75㎡烧结机在试生产过程中反映出的安全隐患进行了充分的自查,共查出各类问题和隐患52项。
从2009年4月26日开始,炼铁分厂烧结车间按照公司、分厂安排,对查出的以上诸多方面的安全隐患和存在的问题进行逐项整改。
2009年5月3日,炼铁分厂烧结车间2烧工段负责处理烧结机尾部撒矿及单辊大轴加防护套;作业人员:
副段长宁海成、看火工董强、焊工朱卫东;作业地点:
75㎡烧结机台车平台(+16.7m)。
烧结车间75㎡烧结机维修班负责处理双层卸灰阀下卸灰口焊管;作业人员:
李文宽、吴斌;作业地点:
75㎡烧结机主厂房吊装孔下(±0m)平台。
2009年5月3日下午14:
00左右上班后,炼铁分厂烧结车间2烧工段段长付淼电话通知副段长宁海成,要求安排人员到75㎡烧结机台车平台(+16.7m)回收焊接、切割工具,副段长宁海成安排看火工董强到吊装孔下(±0m)平台处进行吊运监护,焊工朱卫东负责对工具进行捆绑、吊挂,副段长宁海成本人负责行车操作。
2009年5月3日下午14:
00左右,烧结车间75㎡烧结机维修班上班后,李文宽、吴斌到主厂房吊装孔下(±0m)平台处倒运焊接用管头。
宁海成、朱卫东先将电焊机、乙炔瓶分别从台车平台(+16.7m)吊运至吊装孔下(±0m)平台后,宁海成将行车小钩升至台车平台(+16.7m)准备吊运两个氧气瓶(第三次吊运),朱卫东将两个氧气瓶用吊运麻绳交叉捆绑好,将麻绳另一端挂至行车小钩上,同时用手拉住绳头掌握平衡,行车将两个氧气瓶吊至吊装孔前落地又重新进行捆绑确认后,开始将氧气瓶从台车平台(+16.7m)往吊装孔下(±0m)平台下放,当时大约是14:
50分左右,当氧气瓶吊运下放到单辊平台(+12.5m)处时绳索突然脱落,这时吊装孔下(±0m)平台上李文宽正在搬运焊接用接管,脱落的氧气瓶正好砸中李文宽头部,李文宽随即俯卧倒地。
宁海成、朱卫东当发现氧气瓶脱落将人砸伤后,迅速到75㎡烧结机主控室打电话通知略钢医院120:
说“75㎡烧结机处将人砸伤请求立即前来抢救。
”大约15:
10分左右,略钢120救护人员赶到,开始对李文宽进行现场紧急救护,经过抢救后诊断,确定人已死亡。
二、事故原因分析:
1、焊工朱卫东、副工段长宁海成在吊运氧气、乙炔瓶过程中,违反“十不吊”规定,①“行车吊挂重物吊绳和附件捆绑不牢,不符合安全要求的不吊”,②“氧气瓶、乙炔瓶等有爆炸性重物的不吊”,且副工段长宁海成没有经过专业培训,没有取得行车操作证,属严重违章,是造成事故的直接原因。
2、吊运监护人董强监护不力,严重失职,没有及时有效的阻止李文宽在吊装孔下(±0m)作业,是造成这起事故的另一主要原因。
3、烧结车间领导对存在高空吊运作业,且有交叉作业的工作场所的危险性认识不足,不同单位、不同维修班组在同一场所且有高空吊运作业的交叉作业,没有设立安全协调监护人员,致使两班组在作业过程中得不到相互协调,是造成这起事故的又一重要原因。
4、李文宽本人安全意识不足,在有交叉作业的工作场所内对周边的作业环境没有进行安全确认,二烧工段已将第二批工具吊下,李文宽本人应该引起足够的注意,知道有人在使用行车从台车平面(+16.7m)往下吊运工具,安全确认不够,是造成这起事故的另一原因。
3、关于对烧结分厂“10.18”工伤事故处理的报告
2010年10月18日,烧结分厂维修作业区钳工一班发生一起工伤事故,现通报如下:
一、事故经过:
2010年10月18日凌晨2时35分,烧结分厂一作业区小夜班班长给调度室反映,1#烧结机单辊小格拉链机头轮轴承散架需钳工进行处理,随即调度联系维修作业区安排处理,于3时15分钳工一班和可新、汪成勇、吴雷3人前来处理,因小格拉链头轮设在烧结机设备下方,空间十分狭窄,里面只能进去一人,因此,汪成勇在里面拆卸损坏的轴承,和可新在外递送工具并做监护,吴雷负责搬运氧气、乙炔和领轴承。
约4时许,汪成勇用手捂着左眼睛从里面钻出来说:
“轴承内套取不下来,他眼睛里进去渣子了(汪成勇在敲打轴承内套时眼睛里崩进渣子)”。
调度值班长张翠兰便叫赶紧送往医院就诊,经医院检查后被诊断为:
左眼球被异物深度击伤。
二、事故原因:
事故发生后,公司安环部、烧结分厂对事故现场和事故相关人员进行调查了解,并于10月19日下午14时30分在维修作业区钳工一班组织召开了事故分析会,经过调查分析认为:
1、事故者个人安全防护意识不到位,对作业现场潜在的危险源因素没有充分认识,盲目操作,是造成这起事故的主要原因。
2、1#烧结机现场环境差,检修现场狭窄,夜间光线不好是造成这起事故的另一原因。
高炉炼铁生产工艺流程简介
高炉炼铁生产是冶金(钢铁)工业最主要的环节。
高炉冶炼是把铁矿石还原成生铁的连续生产过程。
铁矿石、焦炭和熔剂等固体原料按规定配料比由炉顶装料装置分批送入高炉,并使炉喉料面保持一定的高度。
焦炭和矿石在炉内形成交替分层结构。
矿石料在下降过程中逐步被还原、熔化成铁和渣,聚集在炉缸中,定期从铁口、渣口放出。
高炉生产是连续进行的。
一代高炉(从开炉到大修停炉为一代)能连续生产几年到十几年。
高炉冶炼目的:
将矿石中的铁元素提取出来,生产出来的主要产品为铁水。
付产品有:
水渣、矿渣棉和高炉煤气等。
高炉冶炼原理简介:
高炉生产是连续进行的。
一代高炉(从开炉到大修停炉为一代)能连续生产几年到十几年。
生产时,从炉顶(一般炉顶是由料种和料斗组成,现代化高炉是钟阀炉顶和无料钟炉顶)不断地装入铁矿石、焦炭、熔剂,从高炉下部的风口吹进热风(1000~1300摄氏度),喷入油、煤或天然气等燃料。
装入高炉中的铁矿石,主要是铁和氧的化合物。
在高温下,焦炭中和喷吹物中的碳及碳燃烧生成的一氧化碳将铁矿石中的氧夺取出来,得到铁,这个过程叫做还原。
铁矿石通过还原反应炼出生铁,铁水从出铁口放出。
铁矿石中的脉石、焦炭及喷吹物中的灰分和加入炉内的石灰石等熔剂结合生成炉渣,从出铁口和出渣口分别排出。
煤气从炉顶导出,经除尘后,作为工业用煤气。
现代化高炉还可以利用炉顶的高压,用导出的部分煤气发电。
高炉冶炼工艺流程简图:
[高炉工艺]高炉冶炼过程:
高炉冶炼是把铁矿石还原成生铁的连续生产过程。
铁矿石、焦炭和熔剂等固体原料按规定配料比由炉顶装料装置分批送入高炉,并使炉喉料面保持一定的高度。
焦炭和矿石在炉内形成交替分层结构。
矿石料在下降过程中逐步被还原、熔化成铁和渣,聚集在炉缸中,定期从铁口、渣口放出。
高炉冶炼工艺--炉前操作:
一、炉前操作的任务
1、利用开口机、泥炮、堵渣机等专用设备和各种工具,按规定的时间分别打开渣、铁口,放出渣、铁,并经渣铁沟分
别流人渣、铁罐内,渣铁出完后封堵渣、铁口,以保证高炉生产的连续进行。
2.完成渣、铁口和各种炉前专用设备的维护工作。
3、制作和修补撇渣器、出铁主沟及渣、铁沟。
4、更换风、渣口等冷却设备及清理渣铁运输线等一系列和出渣出铁相关的工作。
高炉冶炼工艺--高炉基本操作:
高炉基本操作制度:
高炉炉况稳定顺行:
一般是指炉内的炉料下降和煤气流上升均匀,炉温稳定充沛,生铁合格,高产低耗。
操作制度:
根据高炉具体条件(如高炉炉型、设备水平、原料条件、生产计划及品种指标要求)制定的高炉操作准则。
高炉基本操作制度:
装料制度、送风制度、炉缸热制度和造渣制度。
高炉冶炼主要工艺设备简介:
[高炉设备]高炉:
横断面为圆形的炼铁竖炉。
用钢板作炉壳,壳内砌耐火砖内衬。
高炉本体自上而下分为炉喉、炉身、炉腰、炉腹、炉缸5部分。
由于高炉炼铁技术经济指标良好,工艺简单,生产量大,劳动生产效率高,能耗低等优点,故这种方法生产的铁占世界铁总产量的绝大部分。
高炉生产时从炉顶装入铁矿石、焦炭、造渣用熔剂(石灰石),从位于炉子下部沿炉周的风口吹入经预热的空气。
在高温下焦炭(有的高炉也喷吹煤粉、重油、天然气等辅助燃料)中的碳同鼓入空气中的氧燃烧生成的一氧化碳和氢气,在炉内上升过程中除去铁矿石中的氧,从而还原得到铁。
炼出的铁水从铁口放出。
铁矿石中未还原的杂质和石灰石等熔剂结合生成炉渣,从渣口排出。
产生的煤气从炉顶排出,经除尘后,作为热风炉、加热炉、焦炉、锅炉等的燃料。
高炉冶炼的主要产品是生铁,还有副产高炉渣和高炉煤气。
[高炉设备]高炉热风炉介绍:
热风炉是为高炉加热鼓风的设备,是现代高炉不可缺少的重要组成部分。
提高风温可以通过提高煤气热值、优化热风炉及送风管道结构、预热煤气和助燃空气、改善热风炉操作等技术措施来实现。
理论研究和生产实践表明,采用优化的热风炉结构、提高热风炉热效率、延长热风炉寿命是提高风温的有效途径。
[高炉设备]铁水罐车:
铁水罐车用于运送铁水,实现铁水在脱硫跨和加料跨之间的转移或放置在混铁炉下,用于高炉或混铁炉等出铁。
炼铁生产中的主要安全技术
炼铁安全生产的主要特点
炼铁是将铁矿石或烧结球团矿、锰矿石、石灰石和焦炭按一定比例予以混匀送至料仓,然后再送至高炉,从高炉下部吹入1000℃左右的热风,使焦炭燃烧产生大量的高温还原气体煤气,从而加热炉料并使其发生化学反应。
在1100℃左右铁矿石开始软化,1400℃熔化形成铁水和液体渣,分层存于炉缸。
之后,进行出铁、出渣作业。
炼铁生产所需的原料、燃料,生产的产品和副产品的性质,以及生产的环境条件,给炼铁人员带来了一系列潜在的职业危害。
例如,在矿石和焦炭运输、装卸,破碎和筛分,烧结矿整粒和筛分过程中,都会产生大量的粉尘;在高炉炉前出铁场,设备、设施、管道布置密集,作业种类多,人员较集中,危险有害因素最为集中,如炉前作业的高温辐射,出铁、出渣会产生大量的烟尘,铁水