TPM优秀奖审查表.docx
《TPM优秀奖审查表.docx》由会员分享,可在线阅读,更多相关《TPM优秀奖审查表.docx(24页珍藏版)》请在冰豆网上搜索。
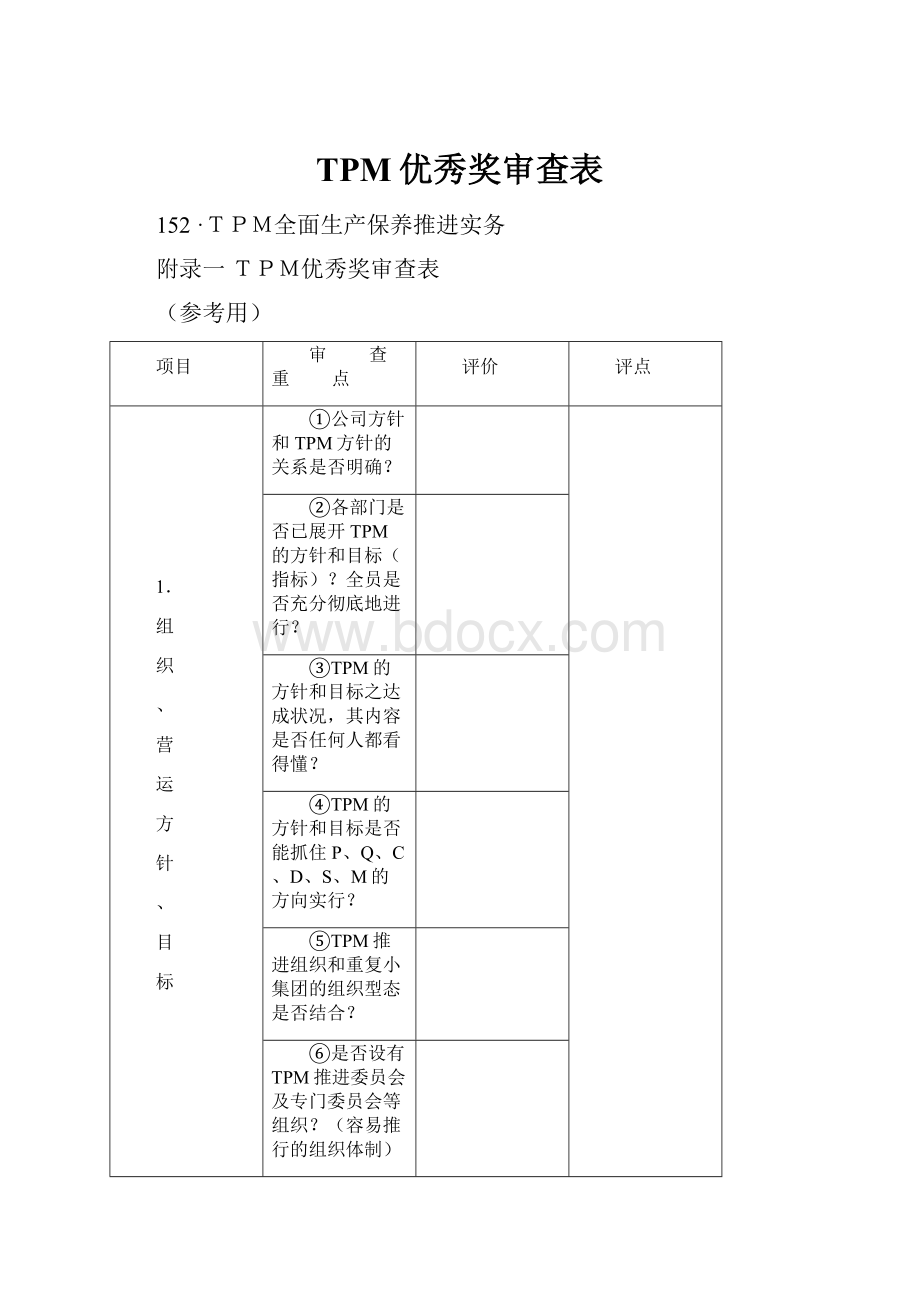
TPM优秀奖审查表
152·TPM全面生产保养推进实务
附录一TPM优秀奖审查表
(参考用)
项目
审 查 重 点
评价
评点
1.
组
织
、
营
运
方
针
、
目
标
①公司方针和TPM方针的关系是否明确?
②各部门是否已展开TPM的方针和目标(指标)?
全员是否充分彻底地进行?
③TPM的方针和目标之达成状况,其内容是否任何人都看得懂?
④TPM的方针和目标是否能抓住P、Q、C、D、S、M的方向实行?
⑤TPM推进组织和重复小集团的组织型态是否结合?
⑥是否设有TPM推进委员会及专门委员会等组织?
(容易推行的组织体制)
⑦部、课内TPM会议在进度管理上是否活用?
⑧专门委员会的机能有无发挥?
(活动内容和委员会间的整合)
⑨第一线的小集团活动是否活泼化?
⑩是否设有设备保养的专门担当者,并能发挥其机能?
2.
个
别
改
善
①对生产部门损失的用词和定义及其目标、方针是否具体明确?
②生产部门现状的损失是把握住?
③部门别模范设备的个别改善是否有横向发展?
④个别改善的专案小组是否由管理者领导?
幕傣人员、专门人员是否参与?
有无成果?
⑤各改善主题是否都设有目标,且其对成果指标的贡献程度是否明确?
⑥改善的成果是否以P、Q、C、D、S、M定量的表现出来?
⑦改善活动是否很活泼地进行?
(从质与量两方面来评估)
⑧改善活动中的必要手法,如PM分析等,是否有效地应用?
⑨是否决定出重点的个别改善主题?
⑩为落实改善结果,必要时是否标准化?
153· 肆、TPM活动推动的程序
项目
审查重点
评价
评点
3.
自
主
保
养
①自主保养的展开是否遵照七大步骤来实施?
而且管理者是否实际实施诊断?
②职场、现场的活动状况、目标达成状况、及今后课题是否均揭示在活动看板上?
③为了养成察觉异常的能力,是否指出异常点,予以复原,并实施更多的小改善?
④自己的设备能否自己维护、改善?
⑤垃圾、污垢、原材料飞散、漏油等是否消除?
对其发生源的对策是否了解?
⑥清洁、加油、锁紧、点检是否确实实施?
维持的工作是否落实?
困难部位是否拟订对策?
⑦吻合记号、加油标示等目视管理是否彻底实施?
⑧工具等的整理、整顿、清扫是否确实实施?
⑨重点教育是否整理成教育用讲议?
是否充分活用?
⑩管理者是否将已作成之模范设备进行水平式展开?
4.
计
划
保
养
①自主保护和计划保养的责任范围及共同协力的体制是否明确?
②依据时间的TPM(定期保养)及依据状态的CBM(条件保养)等保养方式是否合理选择?
③修护技术、点检技术、润滑管理技术、故障解析技术等专门保养技术水平是否充分?
④设备的信赖性、保养性、时间移动率是否定量把握?
⑤改良保养是否积极进行,并有效提升效果?
是否反应到MP设计上?
⑥预备品、模具、冶工具、量具、图画等的管理是否良好?
⑦设备的恶化状态、故障、设备停止、保养工数等保养数据之取得和活用方法是否适切实际?
⑧保养情报的管理是否已系统化?
⑨设备诊断技术是否适切活用,并使其效果提升?
⑩保养费用的瞀编列和管理是否适切?
*TBM:
TimeBaseMainterance
CBM:
ConditionBaseMainterance
154·TPM全面生产保养推进实务
项目
审查重点
评价
评点
5.
品
质
保
养
①为了确定品质和设备的关系,是否适切地实施设备的条件设定及维持管理,以防止设备产生不良品?
②对于品质不良的发生原因是否采取再发生防止的措施?
(有关人、设备)
③因设备而发生的不良率是否有降低?
④品质特性和加工条件、设备精度等,其关联性是否予以追究?
⑤与品质有关的设备零组件,有无下工夫使其容易点检?
⑥各种分析手法是否以阶层别有效应用?
⑦是否有很多不良再发生的状况?
(是否拟订杜绝不良之对策?
)
⑧有无采取事前点检的办法,使其不会因设备故障而造成不良?
⑨为降低因设备引起的不良率,是否进行必要的品质管理教育以及研究?
⑩工程内制品的直行率是否已大幅提升?
6.
制
品
、
设
备
初
期
管
理
①是否实施制品、设备的初期管理,并提高成果?
②制品、设备初期管理的进行方法是否适切?
(含DR、自动机械的除错程式)
③制品、设备初期管理的管理项目和基准是否适切?
④制品、制和之开发和设备计划的关系是否适切?
⑤制品、设备的计划、开发、设计等其是否充分考虑,安全性、信赖性、保全性、操作性、经济性,而设计审查效果是否提高?
⑥有关设备、模具、治工具等是否依照MP设计的构想进行,其方法是否系统化?
⑦为了达成MP设计的效果,是否建立情报回馈体制?
⑧进行设备计划时,是否检讨其不确实要因?
⑨设备投资案的经济性比较法与风险是否适切?
(有无实施LCC及LCP之评价?
)
⑩设备预算的编列是否适切?
*LCC:
LifeCicleCost(寿命周期成本)
LCP:
LifecycleProfit(寿命周期利益)
155.肆、TPM活动推动的程序
项目
审查重点
评价
评点
7.
教
育
训
练
①管理者、幕傣人员、作业者、保养人员须具备的知识、技能是否明确?
②是否掌握每位作业人员对哪些设备操作能力较佳?
哪些设备操作能力较差?
③教育的重要主题是否与公司将来计划有所关连、结合?
④对管理者、幕傺人员、作业者、保养人员是否建立效果效果良好的教育体系?
⑤是否有提升技能的教育课程(作业者、保全人员),且实际实施及改善?
⑥是否设有保养技能研修场所,并活用这个场所?
⑦教育的传达是否活泼,全员的技能是否提升且加以活用?
⑧是否掌握住教育训练的效果?
⑨有资格的机械保养技能士是否不够多?
⑩在参加公司外的演讲会、研修会后是否能积极地收集相关资料
8.
管
理
间
接
部
门
①P、Q、C、D、S、M和TPM的关连性是否良好,损失的用词和定义、目标和实绩是否明确?
②对生产部门的效率化是否有支援的活动?
③制品及半成品的在库量是否减少?
④生产系统是否做到必要的物品只在需要的时候生产所需要的量?
⑤资料共通化、检索速度是否提升?
⑥是否谋求业务效率化及精度提升?
⑦事务用品的在库量是否减少,且环境是否改善?
⑧是否建立体制,使情报传达迅速确实,且需要的情报能马上得到?
⑨重要的情报是否有防止遗失的管理?
资料内容是否易看且易取出?
⑩所管理的设备是否有效率活用?
156.TPM全面生产保养推进实务
项目
审查重点
评价
评点
9.
安
全
卫
生
和
环
境
管
理
①是否有确立安全卫生和环境管理的方针及具资格之指导者
②健康管理、卫生设备是否良好?
③对过去所发生的劳动灾害及工场灾害,是否做科学的分析,并采取防止再发生的对策?
④安全点检手册是否完整,且按内容确实实施安全巡回检查?
⑤是否发觉无意中事故,并针对物和人原因分析?
⑥[指差呼称]等所规定的事是否确实实行?
且有严格的规律?
⑦安全盖、安全栅栏、安全标示、愚巧法及防止灾害扩大对策等的安全设施是否良好?
⑧新技术、新设备导入时有无实施安全教育?
⑨废水处理、空气污染防治、噪音防止、振动防止等的公害对策管理是否良好?
⑩紧急应变手册是否完整?
是否依其内容实施防灾训练?
保护用具、急救器具是否准备妥当?
10.
效
果
与
评
价
①设备的总合效率、突发故障、小停止等之指标是否达成其设定目标?
②工程不良、顾客抱怨件数是否愿意减低?
③制品、半成品在库存是否比实施TPM前大幅度减少?
④休业灾害件数、公害是否继续保持[O]的状态?
⑤改善提案的件数是否达到所设定的目标?
⑥是否进行省资源、省能源、降低成本的活动?
⑦表示企业全体业绩之经常利益及总资本经常利益率和附加价值的生产性是否提升?
⑧TPM费用对应效果的测定是否适切实行?
⑨依据TPM活动的无形效果,是否已使企业的体制获得改善,建立明朗舒适的工作场所?
⑩对TPM活动中所残留的问题是否有明确的认识,并作成具体的实行计划?
表12.3TPM的效果与效果项目
分类
NO.
项目
计算式
内容
生
产
1
生产性
生产费(生产金额)
劳动人员数(总劳动时间)
平均单位劳动量的产出量
2
设备总合率
时间运转率×性能运转率×良品率
现状设备从时间、速度品质各方面,对产品制造的贡献
3
时间运转率
负荷时间—停机时间
负荷时间
相对于负荷时间,扣除设备停止时间(故障、制程准备、调整等)之运转时间之比率
4
性能运转率
产量×实际周期时间基准时期
━━━━━━━━×━━━━
负荷时间—停机时间实际周期
计算进度损失的指标,求出在时间运转率中看不出来的速度损失
5
良品率
投入率—不良数
投入数
相对投入数量的良品数之比率
6
故障件数
实际数值
突发故障件数
7
故障强度数
总故障停机时间
━━━━━━━×100
总动作时间
因故障而造成设备停机的时间之比率
8
故障频度率
性总停机次数
━━━━━━×100
总动作时间
平均负荷时间的故障发生比率
9
MTBF
总动作时间
━━━━━━━
总故障停止次数
平均两次故障的间隔时间
10
BTTR
总修护时间
━━━━━
总修护次数
平均每次修护时间
11
制程准备时间
实际数值
12
短暂性停机次数
实际数值
13
机械器具装备率
机械设备+工具器具+车辆搬运设备
从业人员数
14
设备投资率
加工产出金额
━━━━━━×100
设备资产
加工产出金额占设备资产的比率,从此可以看出资本的生产化
15
计划达成率
实旋件数
━━━━×100
计划件数
16
预防保养率
PM费+CM费
━━━━━━━━×100
PM费+CM费+BM费
17
自动化率
自动化要素作业数
━━━━━━━━×100
总要素作业数
设备生产线的要素作业中,自动化的比率。
所谓要互作业是指产品的夹装、加工、品质检验、拆御、搬运等五项
512新TPM加工组立篇
分类
NO.
项目
计算式
内容
生
产
18
无人化
夜间、白天时间的残存率
19
人工修整
20
产生
品
质
1
制程内不良
实际数值
2
诉程内不良
实际数值
3
诉赔件数
已交货之退货个数
—━━━━━━━ ×106(PPM)
交货数
4
已交货之退货率
1制品单位的检查费用
品质损益分歧点 ━ ━━━━━━━━━━
1个不良品所造成的损失
5
市场诉赔金额
实际数值
成
本
1
合理化金额
实际数值
2
保养费
实际数值
3
资本回转率
净营业额
固定资产
表示固定资产的利用度,数值愈大表示设备资产充分活用
4
固定资产报废额
5
折旧率
折旧费
━━━━ ×100
固定资产
交
期
1
延误日期
实际交货日—约定交货日
2
产品滞留日数
产品平均库存额
月平均营业额
安
全
卫
生
1
灾害频度率
停机灾害件数
━━━━━━ ×106
劳动时间
表示灾害的发生比率,平均每1百万小时发生的件数
2
强度率
劳动损失日数
━━━━━━ ×1000h
总劳动时间
表示灾害的程度,相对1000小时的总劳动时间与灾害所引起的损失天数之比
教
育
、
士
气
1
小集团活动时间
实际数值
2
小集团活动次数
实际数值
3
提案改善件数
实际数值
4
公司外发表次数
实际数值
5
国家资格
实际数值
6
操作失误件数
实际数值
7
参加教育训练人数
实际数值
8
必要文件找出时间
实际数值
9
自主保养率
操作人员处理件数
━━━━━━━━×100
总故障件数
159·伍、TPM活动的要角
图表五~1自主保养扩展的步骤
(自主保养圈活动的推行方法)
步骤
名称
活动内容
设备方面的目标
(现场诊断的要点)
人员方面的目标
(圈活动的诊断要点)
管理者、幕僚
的指导、协助
重点
1
初 期
清 扫
除去设备附近的垃圾、灰尘(拿来走不要的物品)
·排队因环境所造成的不利因素,防止强制劣化。
·排除灰尘、污秽物提高点检、修理的品质以求缩短时间。
·找出潜在的缺陷并处理
·根据人手与设备的接触,产生对设备的爱惜心与好奇心。
·由于圈的活动,而学习圈长的教导。
·教导垃圾、灰尘与设备劣化、保养性关系。
·教导清扫重点部位与加油、锁紧松动螺栓、螺帽的重要性(使用螺栓、螺帽、加油手册)。
·教导[清扫即点检]的意义。
基
本
条
件
的
整
备
2
问题点
改善
消耗垃圾、污秽物的发生源,防止飞散,改善加油不易之部位,以缩短清扫、加油的时间。
·消除垃圾、污秽物的发生、附著,提高设备的固有信赖性。
·由清扫、加油的改善,提高保养性。
·从身边的改善中学习设备的改善技术。
·培养由圈活动提出改善案。
·体会改善的乐趣。
·有效利用改善的理念,给予具体化的提示。
·马上处理,申请工令。
·使用对准线条、记号、加油视窗,可以一目了然。
3
制订清
扫、给
油基准
制订在短时间内可以完成清扫、加油、锁紧动螺栓、螺帽之行动基准(必须标示日常、定期所需时间)
·维持设备保养的3要素:
即清扫、加油、锁紧松动的螺栓、螺帽。
·自己制订基准、遵守基准,并了解遵守基准的重要性。
·每个人都有知道自己的任务。
4
总检点
根据点检手册实施点检技能教育,从总点检的实行,找出设备的小缺陷,使点检容易实行。
·设备的主要部份。
·在外观上做总点检,使劣化复原,以提高信赖性。
·使零件编号铭板、温度标、标示器等点检容易。
·由点检教育的实施,以学习设备功能,判定基准和点检技能。
·实地学习简单的不良对策方法。
·由圈长的教导学习领导统御,从被教导中知道自己的责任。
·整理总点检资料,民工资料的重要性。
·制订总点检手册、事故例,对圈长实施教育训练。
·制订点检预定表。
·发现不良之处,迅速请求改善。
·实地教导简单的不良对策方法。
·使点检容易实行。
·教导如何惧资料及解析。
·参与圈长的保养计划报备。
彻底实施点检及维持
160· TPM全面生产保养推进实务
5
自主
点检
制订自主点检
项目表(合乎
清扫基准、加
油基准、点检
基准,并提高
效率),提高
操作信赖性。
·由总点检使设备的劣化恢复。
·由以目视管理,谋求清扫、点检加油的效率化。
·重新认定设备的角色、人员的任务及明确判断如何才是异常。
·使设备的操作性良好。
·根据总点检手岫、自行制订日常定期点检项目表,还是自主管理的开始。
·了解时系列性资料记录的重要性。
·学习何谓正确操作?
何谓异常?
异常应如何处理?
·对于点检的重点位置点检周期资料的看法,给予提示。
·给予点检检查项目表、表格制作、填写方法之提示。
·对操作标准、故障排除、手册的制订,以教育方式给予技术上的支援。
6
整理、
整顿
实行现场各种管理项目的标准化,作业效率化和品质。
·确保安全。
·改善制程与减少库存。
·资料记录的标准化。
·备品及材料、在制品、成品、模具、夹具、工具的管理基准
·改善设备及其他配置。
·在制品、不良品、模具、夹具、工具、量具、搬运工具、通路之管理基准化,及现场用目视管理。
·由各种管理项目的标准化,以扩大自主管理的范围。
·从基准化与资料的掌握,了解基准提升之重要性。
·具备管理、监督者原有的任务。
·支援圈或部门对基准化之请求。
·教导使用IE、QC之分析方法、改善方法,及用目视管理方法。
周
边
设
备
问
题
点
的
改
善
7
自主管
理的彻
底执行
(个别
对策)
·分析各种资料及改善,以提高设备的信赖、保养性和操作性。
·根据资料,找出设备的弱点,并作重点改善,以求延长设备寿命及点检周期。
·提升目标意义,并加强包括保养成本在内的成本观念。
·由修理技能的教育训练,学会简单的修理能力。
·学习资料的记录、解析和改善技术。
·支援设备改善技术。
·修理技能的教育训练
·参与设备改善检讨,与圈共同推展设备改善。
·改善内容的标准化。