机械原理课程设计说明书.docx
《机械原理课程设计说明书.docx》由会员分享,可在线阅读,更多相关《机械原理课程设计说明书.docx(35页珍藏版)》请在冰豆网上搜索。
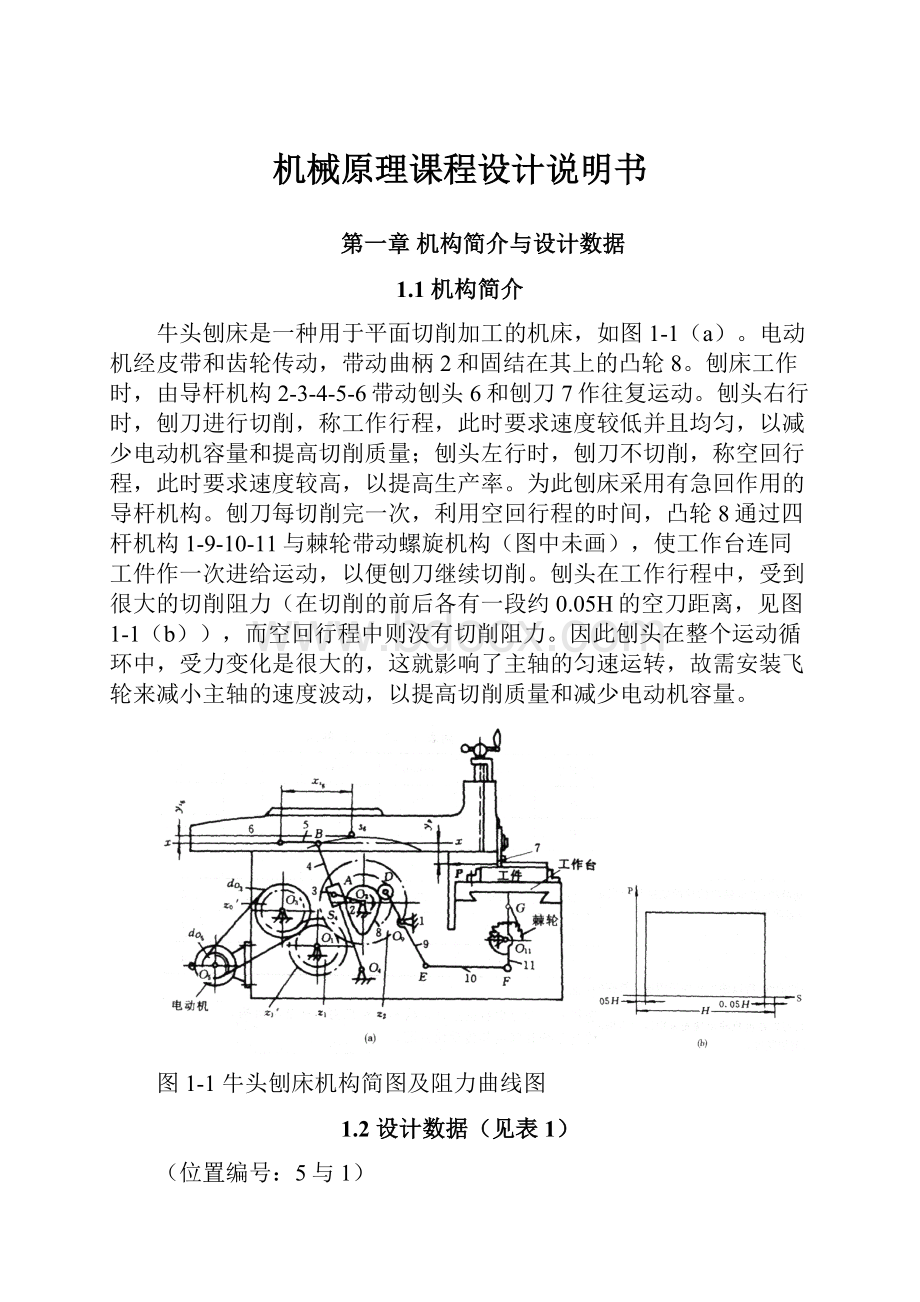
机械原理课程设计说明书
第一章机构简介与设计数据
1.1机构简介
牛头刨床是一种用于平面切削加工的机床,如图1-1(a)。
电动机经皮带和齿轮传动,带动曲柄2和固结在其上的凸轮8。
刨床工作时,由导杆机构2-3-4-5-6带动刨头6和刨刀7作往复运动。
刨头右行时,刨刀进行切削,称工作行程,此时要求速度较低并且均匀,以减少电动机容量和提高切削质量;刨头左行时,刨刀不切削,称空回行程,此时要求速度较高,以提高生产率。
为此刨床采用有急回作用的导杆机构。
刨刀每切削完一次,利用空回行程的时间,凸轮8通过四杆机构1-9-10-11与棘轮带动螺旋机构(图中未画),使工作台连同工件作一次进给运动,以便刨刀继续切削。
刨头在工作行程中,受到很大的切削阻力(在切削的前后各有一段约0.05H的空刀距离,见图1-1(b)),而空回行程中则没有切削阻力。
因此刨头在整个运动循环中,受力变化是很大的,这就影响了主轴的匀速运转,故需安装飞轮来减小主轴的速度波动,以提高切削质量和减少电动机容量。
图1-1牛头刨床机构简图及阻力曲线图
1.2设计数据(见表1)
(位置编号:
5与1)
表1设计数据
案
方
位
单
号
符
容
内
计
设
导杆机械的运动分析
导杆机构的动态静力分析
n2
lO2O4
lO2A
lO4B
lBC
lO4S4
xS6
yS6
G4
G6
P
yP
JS4
r/min
mm
N
mm
kgm2
Ⅰ
60
380
110
540
0.25
0.5
240
50
200
700
7000
80
1.1
案
方
位
单
号
符
容
内
计
设
飞轮转动惯量的确定
凸轮机构的设计
齿轮机构的设计
δ
nO5
z1
zO’
z1’
JO2
JO1
JO3
JO5
φmax
lO9D
[α]
δ0
δ01
δ0’
dO5
dO3
m12
mO31’
α
r/min
kgm2
°
mm
°
mm
°
Ⅰ
0.15
1440
10
20
40
0.5
0.3
0.2
0.2
15
125
40
75
10
75
100
300
6
3.5
20
第二章设计内容
2.1导杆机构的运动分析
已知:
曲柄每分钟转数
,各构件尺寸及重心位置,且刨头导路
位于导杆端点B所作圆弧高的平分线上(如图2-1)。
图2-1曲柄位置图图2-2摆杆加速度线图
2.1.1机构的运动简图
以O4为原点定出坐标系,根据两固定端之间的尺寸定出O2点,并以110mm(实际尺寸,下同)为半径做圆。
过O4引两条长为540mm的线段,与以O2为圆心所做的圆相切与1点、8点,线段左端点即为B点。
线段O4B在左右极限位置所能扫过的轨迹即为B点的运动轨迹,B点运动弦的中间位置变为点C的运动轨迹。
过B点作半径为135mm的圆弧与运动轨迹相交于C点,此时即为机构运动时的左极限位置。
曲柄位置图的作法:
1和8’为工作行程起点(左极限位置)和行程终点(右极限位置)所对应的曲柄位置,1’和7’为切削起点和终点所对应的曲柄位置,其余2、3…12等,是由位置1起,顺ω2方向将曲柄圆作12等分的位置(如图2-3)。
图2-3机构的运动简图
2.1.2曲柄位置“1”、“5”两点运动分析
图解法:
曲柄在位置“1”的速度分析
取曲柄在位置“1”进行速度分析。
因曲柄2和构件3在A处用转动副相连,故V2A=V3A,其大小等于ω2lO2A,方向垂直于OO2A,指向与ω2一致。
ω2=2πn2/60rad/s=2πrad/s
υ3A=υ2A=2π*110mm/s=691.15*10-3m/s(⊥O2A)
取构件3和4的重合点A进行分析,列速度矢量方程:
υ4A=υ3A+ υ4A3A
大小?
√?
方向⊥O4B⊥O2A∥O4B
取速度极点p,速度比例尺uv=0.01(m/s)/mm,作速度多边形(如图2-4)
图2-4位置1的速度多边形
得:
υ4A=0m/s
υ4A3A=691.15*10-3m/s
w4=0rad/s
所以:
υB=0m/s
υC=0m/s
曲柄在位置“1”的加速度分析
取曲柄在位置“1”进行加速度分析。
因构件2和3在A点处的转动副相连,故a2An=a3An,其大小等于ω22lO2A,方向由A指向O2。
ω2=2πn2/60rad/s=2rad/s
a2An=a3An=ω22*lO2A=(2π)2*110mm/s2=4342.63*10-3m/s2
a4An=ω42lO4A=0m/s2
a4A3AK=2ω4υ4A3A=0m/s2
取3、4构件重合点A为研究对象,列加速度矢量方程:
a4A=a4An+a4Aτ= a3An+a4A3AK+a4A3A
大小:
?
ω42lO4A ?
√0?
方向:
?
B→A⊥ABA→O2⊥O4B∥O4B
取加速度极点为p',加速度比例尺µa=0.1(m/s2)/mm,作加速度多边形(如图2-5)
图2-5位置1的加速度多边形
得:
a4Aτ=4342.63*10-3m/s2
所以:
4=a4Aτ/lO4A=4342.63*10-3/363.73=11.94
aBτ=
4*lAB=11.94*540*10-3m/s2=6447.06*10-3m/s2
取5、6构件的重合点C为研究对象,列加速度矢量方程:
ac=aBτ+aBn+aBC
大小?
α*lAB0?
方向x-x⊥O4B0⊥BC
取加速度极点为p',加速度比例尺µa=0.1(m/s2)/mm,作加速度多边形,(如图2-5)。
得:
ac=6.01m/s2
曲柄在位置“5”的速度分析
取曲柄在位置“5”进行速度分析。
因曲柄2和构件3在A’处用转动副相连,故V2A=V3A,其大小等于ω2lO2A,方向垂直于OO2A’,指向与ω2一致。
ω2=2πn2/60rad/s=2πrad/s
υ3A’=υ2A=2π*110mm/s=691.15*10-3m/s(⊥O2A)
取构件3和4的重合点A’进行分析,列速度矢量方程:
υ4A‘=υ3A‘+ υ4A3A‘
大小?
√?
方向⊥O4B’⊥O2A’∥O4B’
取速度极点p,速度比例尺uv=0.01(m/s)/mm,作速度多边形(如图2-6)
图2-6位置5的速度多边形
得:
υ4A‘=680.17*10-3m/s
υ4A3A‘=122.72*10-3m/s
w4‘=1.39rad/s
所以:
υB‘=753.03*10-3m/s
取5、6构件的重合点C为研究对象,列速度矢量方程:
υc‘=υb‘+ υbc‘
大小?
√?
方向x-x⊥O2A’⊥B’C’
得:
υC‘=748.91*10-3m/s
υbc‘=38.83*10-3m/s
曲柄在位置“5”的加速度分析
取曲柄在位置“5”进行加速度分析。
因构件2和3在A‘点处的转动副相连,故a2An‘=a3An‘,其大小等于ω22lO2A,方向由A‘指向O2。
ω2=2πn2/60rad/s=2rad/s
a2An‘=a3An‘=ω22*lO2A=(2π)2*110mm/s2=4342.63*10-3m/s2
a4An‘=ω42lO4A=948.49*10-3m/s2
a4A3AK‘=2ω4υ4A3A=342.26*10-3m/s2
取3、4构件重合点A为研究对象,列加速度矢量方程:
a4A‘=a4An‘+a4Aτ‘= a3An‘+a4A3AK‘+a4A3A‘
大小:
?
ω42lO4A ?
√2ω4υ4A3A‘?
方向:
?
B‘→A‘⊥A‘B‘A‘→O2⊥O4B‘∥O4B‘
取加速度极点为p',加速度比例尺µa=0.05(m/s2)/mm,作加速度多边形(如图2-7)
图2-7位置5的加速度多边形
得:
a4A3AK‘=2ω4υ4A3A‘=2*1.40*122.72m/s2=342.26m/s2
a4Aτ‘=428.81*10-3m/s2
所以:
4‘=a4Aτ‘/lO4A=0.88rad/s2
aB‘=aBn‘+aBτ‘=1.06m/s2
取5、6构件的重合点C‘为研究对象,列加速度矢量方程:
ac=aBτ+aBn+aBC
大小?
α‘*lABω42lAB?
方向x-x⊥O4B‘∥B‘C‘⊥B‘C‘
取加速度极点为p',加速度比例尺µa=0.1(m/s2)/mm,作加速度多边形,(如图2-7)。
得:
ac=0.597m/s2
解析法:
如图2-8,建立直角坐标系,并标出各杆矢量及方位角。
利用两个封闭图形ABCA及CDEGC。
投影方程式为:
(1)
(2)
(3)
(4)
1求
图
由公式
(1)和
(2)得:
图2-8
(5)
(6)
上式等价于
(7)
对
求导得:
(8)
同理得:
(9)
2求滑块E的
由(3)、(4)式得:
(10)
(11)
求导得:
(12)
(13)
再求导得:
(14)
(15)
程序编写过程(计算机C语言程序)
程序说明:
在程序中,各个字母与图4中的对应关系为:
a=AB,b=CD,c=DE,d=AC,e=H(H为水平导轨到底座的距离),f=ω2。
表1与图2-8中各数据的对应关系为:
ω2=2πn=2×3.14×60÷60=6.28
AB=lo2a=0.11AC=lo2o4=0.38
CD=lo4b=0.54DE=lbc=0.135
由几何关系可得:
其中θ为极位夹角。
由机构运动简图可得:
解得:
θ=14.82°≈15°
代入上式:
H=0.538
#include
#include
#definePI3.1415926
voidmain()
{doublea=0.110,b=0.54,c=0.135,d=0.38,e=0.538,f=6.28;
/*a=AB,b=CD,c=DE,d=AC,e=H,f=ω1*/doubleB,C,E,F,G,I,L,M,O;
/*B=θ3,C=θ4,E=Se,F=ω3,G=ω4,I=Ve,L=а3,M=а4,O=аe*/
doublex=0;printf("θ1θ3θ4SeW3W4VeA3A4Ae\n");
while(x<6.3)
{
B=atan((d+a*sin(x))/(a*cos(x)));/*求θ3*/
if(B<0)B=PI+B;
C=PI-asin((e-b*sin(B))/c);/*求θ4*/
if(C<0)C=PI+C;
E=b*cos(B)+c*cos(C);/*求Se*/
F=(a*f*(a+d*sin(x)))/(d*d+a*a+2*d*a*sin(x));/*求ω3*/
G=-(F*b*cos(B))/(c*cos(C));/*求ω4*/
I=-(F*b*sin(B-C))/cos(C);/*求Ve*/
L=((d*d-a*a)*d*a*f*f*cos(x))/((d*d+a*a+2*d*a*sin(x))*(d*d+a*a+2*d*a*sin(x)));/*求а3*/
M=(F*F*b*sin(B)+G*G*c*sin(C)-L*b*cos(B))/(c*cos(C));/*求а4*/
O=-(L*b*sin(B-C)+F*F*b*cos(B-C)-G*G*c)/cos(C);/*求аe*/
printf("%3.0f%3.3f%3.3f%3.3f%3.3f%3.3f%3.3f%3.3f%3.3f%3.3f\n",x*180/PI,(B*180)/PI,(C*180)/PI,E,F,G,I,L,M,O);
x=x+PI*15/180;
}
}
输出说明:
工作形成终点8'与8之间的夹角
8O28'=(90-14.85)×2-30×5=0.3°故忽略不计,认为其重合,因为7位置与X轴之间的夹角为15°,所以在程序中,以15°为累加值,依次输出,便可得到相应的结果。
各构件的位置、速度和加速度
运行结果截图:
筛选出1、5位置的基本数据:
位置1:
位置5:
表2
位置
项目
ω2
θ2
Sc
ω4
ω5
Vc
A4
A5
Ac
1
6.28
195
-0.290
0.060
-0.070
-0.029
-11.583
13.557
5.701
5
6.28
75
-0.103
1.389
0.325
-0.748
1.003
-7.469
-0.624
单位
rad/s
rad
m
rad/s
rad/s
m/s
rad/s2
rad/s2
m/s2
2.1.3刨头的运动线图
由计算得刨头C在各个位置对应位移、速度、加速度,将其依次连接,构成圆滑的曲线,即得刨头C的运动线图。
刨头C在各个位置的Sc、Vc、ac。
表3
参数数
位置
1
2
3
4
5
6
7
8
9
10
11
12
Sc
(mm)
0
29.34
69.25
123.9
184.0
254.4
288.6
248.6
179.2
130.7
83.7
24.40
Vc
(m/s)
0
0.427
0.64
0.748
0.749
0.66
0.438
0.016
-0.552
-1.221
-1.179
-0.619
Ac
(m/s2)
6.01
3.739
2.071
0.617
-0.654
-1.401
-3.292
-5.594
-8.663
-5.840
4.876
9.059
刨头的运动线图如图2-9、2-10、2-11。
图2-9位置-位移图
图2-10位置-速度图
图2-11位置-加速度图
2.2导杆机构的动态静力分析
已知:
各构件的重量G(曲柄2、滑块3和连杆5的重量都可忽略不计),导杆4绕重心的转动惯量
及切削力
的变化规律(图1-1(
))。
结合图1-1(b)及机构的运动分析,取滑块C(位置1)进行受力分析可得:
滑块C共受4个力,分别为G6、FⅠ6、R16、R56。
其中G6、FⅠ6为已知力,滑块6的重力G6=700N(竖直向下)、惯性力FⅠ6=mc*ac=429.33N(与ac的方向相反);R16、R56方向已知,大小未知,地面对构件6的支持力方向竖直向上,构件5对滑块6的作用力方向有C指向B。
受力如图2-12所示。
图2-12C处的受力图
选取比例尺为u2=10N/mm,由ΣF=G6+FⅠ6+R16+R56=0可作力多边形如图2-13所示。
图2-13C处力多边形
得:
R16=736.90N
R56=430.91N
取摇杆4进行受力分析得:
摇杆4共受7个力,分别为G4、FⅠ4、R23、R54、F14x、F14y、Js4
。
其中G4、FⅠ4、R54为已知力,摇杆4的重力G4=200N(竖直向下)、惯性力FⅠ4=m4*a4=65.79N(与a4的方向相反)、R54=R56=430.91N(由B指向C)、Js4
=13.13KN·m;R23、F14x、F14y均为方向已知,大小未知。
受力如图2-14所示。
图2-14摇杆4的受力图
对点O4进行力矩平衡得:
ΣM=G4*HG+FⅠ4*H4+R23*H+R54*H5+F14x*0+F14y*0+Js4
其中HG=78.16*10-3m、H4=270.00*10-3m、H5=501.75*10-3m、H=363.73*10-3m。
得:
R34=722.34N
F14x=194.00N
F14y=43.11N
选取比例尺为u3=5N/mm,由ΣF=G4+FⅠ4+R23+R54+F14x+F14y=0可作力多边形如图2-15所示。
图2-15摇杆4的力多边形
取曲柄2进行受力分析得:
曲柄2共受2个力,分别为R23’、R12,曲柄在力R23’、R12作用下处于二力平衡。
受力如图2-16所示。
图2-16曲柄2的受力图
得:
M=0,即在此时所需施加的平衡力矩为零。
2.3飞轮设计
已知:
机器运转的速度不均匀系数
,由动态静力分析所得的平衡力矩
,具有定传动比的各构件的转动惯量J,电动机、曲柄的转速
、
及某些齿轮的齿数(参见表1)。
驱动力矩为常数。
2.3.1设计过程:
1、在完成导杆机构的动态静力分析后,将同一方案中每一个小组成员计算所得的平衡力矩My进行统计汇总(共12个点),并按照一定的比例作M—Ψ图,并计算出其与x轴之间所夹的面积,将该计算所得面积除以横坐标跨度,即可得Ma。
如图2-17所示。
图2-17
2、根据惯性力法作出相应的A—Ψ图,并计算出各个位置对应的功的差,即A’值。
如图2-18所示。
图2-18
3、根据过程2中所得的各个位置的A’值,作出相应的A’—Ψ图,从图中可得到最大盈亏功[A’]。
如图2-19所示。
图2-19
4、根据过程3中所得的最大盈亏功[A’],带入公式:
JF>=900·[A’]/(π2·n2·[δ])
可得:
JF>=58.24(kg·m2)
2.4凸轮机构设计
已知:
摆杆9为等加速等减速运动规律,其推程运动角δ0,远休止角δ01,回程运动角δ0’(见图3),摆杆长度
,最大摆角
,许用压力角
(参见表1);凸轮与曲柄共轴。
2.4.1凸轮基本尺寸的确定
根据从动件运动规律,按公式分别计算推程和回程的(
)
,然后用几何作图法直接绘出
(φ)及φ(ψ)线图。
求基圆半径r0及凸轮回转中心O2至从动件摆动中心O
的距离lO2Oo4按φ(ψ)线图划分ψ
角时,可将其所对的弧近视看成直线,然后根据三角形相似原理,用图解法按预定比例分割ψ
角所对应的弧,自从动件摆动中心O4作辐射线与各分割点想连,则ψ
角便按预定比例分割。
由摆杆9做等加速等减速运动,及角角加速度ε与角度δ的关系可得:
设:
δ在0—37.5度时:
ε=a;
δ在37.5—75度时:
ε=-a;
δ在75—85度时:
ε=0;
δ在85—122.5度时:
ε=-a;
δ在122.5—160度时:
ε=a;
那么:
δ在0—37.5度时:
dψ=aδ;
δ在37.5—75度时:
dψ=75a-aδ;
δ在75—85度时:
dψ=0;
δ在85—122.5度时:
dψ=-aδ+85a;
δ在122.5—160度时:
dψ=aδ-160a;
得:
δ在0—37.5度时:
ψ=
δ在37.5—75度时:
ψ=-
+75aδ-1406.25a
δ在75—85度时:
ψ=1406.25a
δ在85—160度时:
δ—ψ图像与δ在0—75度时的图像关于δ=80对称。
由以上计算可得
=1406.25a=
a=0.01067
由公式得出如下数据关系:
表4
δ
dψ
ψ
δ
dψ
ψ
0
0
0
85
0
15.00469
5
0.05335
0.133375
90
-0.05335
14.87131
10
0.1067
0.5335
95
-0.1067
14.47119
15
0.16005
1.200375
100
-0.16005
13.80431
20
0.2134
2.134
105
-0.2134
12.87069
25
0.26675
3.334375
110
-0.26675
11.67031
30
0.3201
4.8015
115
-0.3201
10.20319
35
0.37345
6.535375
120
-0.37345
8.469313
40
0.37345
8.469313
125
-0.37345
6.535375
45
0.3201
10.20319
130
-0.3201
4.8015
50
0.26675
11.67031
135
-0.26675
3.334375
55
0.2134
12.87069
140
-0.2134
2.134
60
0.16005
13.80431
145
-0.16005
1.200375
65
0.1067
14.47119
150
-0.1067
0.5335
70
0.05335
14.87131
155
-0.05335
0.133375
75
0
15.00469
160
0
0
由以上数据画出从动杆运动线图:
图2-20
图2-21
图2-22
根据凸轮转向,摆杆长lO4D,角位移线图ψ=ψ(φ)图和以上求得的r
=80mm,lO
O
,画出凸轮理论廓线,并找出其外凸轮曲线最小曲率半径P
。
然后,再选取滚子半径r
,画出凸轮的实际廓线。
2.4.2凸轮实际廓线
1、设计原理
设计凸轮轮廓依据反转法原理。
即在整个机构加上公共角速度(-ω)(ω为原凸轮旋转角速度)后,将凸轮固定不动,而从动件连同机架将以(-ω)绕凸轮轴心逆时针方向反转,与此同时,从动件将按给定的运动规律绕其轴心相对机架摆动,则从动件的尖顶在复合运动中的轨迹就是要设计的凸轮轮廓。
2、设计凸轮轮廓:
A、绘制凸轮的理论轮廓线[既滚子轴心实际轮廓]
将ψ-φ曲线图(如图2-23、2-24、2-25)的推程运动角和回程运动角个分成4等份,按式求个等分点对应的角位移值:
ψ1=μψ1*11'',ψ1=μψ2*22'',……,的数值。
选取适当的长度比例尺μl定出O2和O9的位置(选取μl=0.002m/mm)。
以O2为圆心,以r0/μl为半径,作圆,再以以O2为圆心,以rb/μl为半径作基圆。
以O9为圆心,以lOo9D/μl为半