万立罐焊接方案DOC.docx
《万立罐焊接方案DOC.docx》由会员分享,可在线阅读,更多相关《万立罐焊接方案DOC.docx(31页珍藏版)》请在冰豆网上搜索。
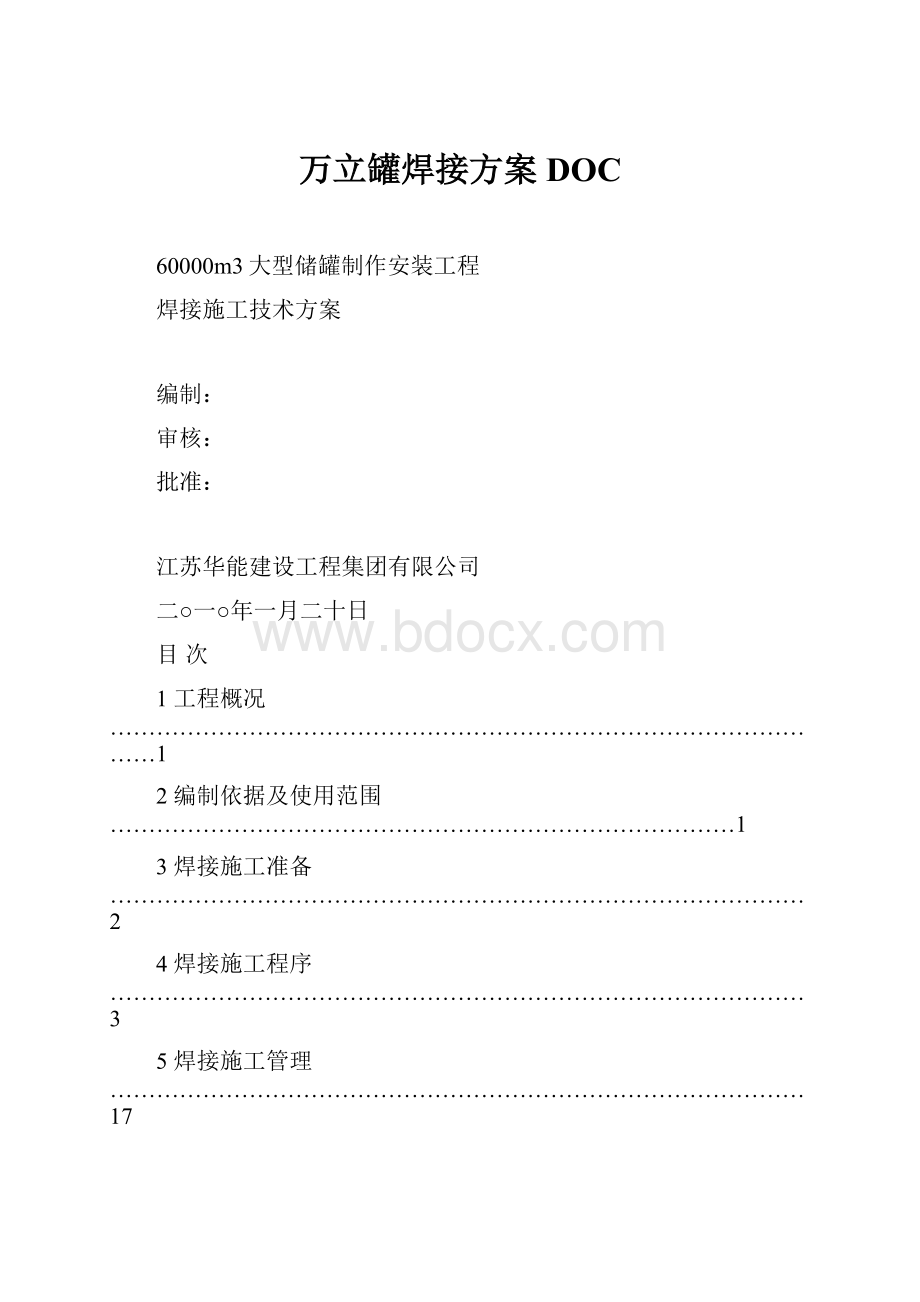
万立罐焊接方案DOC
60000m3大型储罐制作安装工程
焊接施工技术方案
编制:
审核:
批准:
江苏华能建设工程集团有限公司
二○一○年一月二十日
目次
1工程概况……………………………………………………………………………………1
2编制依据及使用范围………………………………………………………………………1
3焊接施工准备………………………………………………………………………………2
4焊接施工程序………………………………………………………………………………3
5焊接施工管理………………………………………………………………………………17
6焊接安全管理………………………………………………………………………………18
7焊接防护措施………………………………………………………………………………19
1工程概况
********大型储罐制作安装工程共计*台60000m3罐,。
罐体内径为60000mm,罐壁高度为22000mm,罐主体壁板材质为****。
储罐的主要焊缝总长度约为***m,其中立缝****m,环缝*****m(参见下表),罐底*****m,罐底与罐壁之间的角焊缝*****m,浮顶及其他焊缝约*****m。
表1.1罐壁焊接工程量(单台罐)
名称
规格(mm)
材质
数量
总重(t)
预制焊缝长度(m)
第一圈壁板
第二圈壁板
第三圈壁板
第四圈壁板
第五圈壁板
第六圈壁板
第七圈壁板
第八圈壁板
第九圈壁板
包边角钢
合计
2编制依据及使用范围
2.1编制依据
2.1.160000m3原油罐施工图。
2.1.2施工及验收规范、标准
a)《立式圆筒形钢制焊接储罐施工及验收规范》GB50128-2005
b)《60000m3浮顶原油储罐施工技术条件》
c)《钢结构工程施工质量验收规范》GB50205-2001
d)《石油化工立式圆筒形钢制储罐施工工艺标准》SH3530-2001
e)《承压设备无损检测》JB/T4730.1-2005~JB4730.6-2005
f)《现场设备、工业管道焊接工程施工及验收规范》GB50236-2001
2.2适用范围
本方案仅适用于我公司承建的********项目60000m3原油罐的焊接施工。
3焊接施工准备
3.1油罐施工前,应组织好焊工培训及考试取证工作,具有足够数量的合格焊工。
有成熟
的焊接工艺及合格的焊接工艺评定。
3.2焊接材料准备充足,质量要得到保证,并应有项目齐全的质量证明文件。
焊接材料应
设专人负责保管,使用前按规定烘干,烘干后的焊条保存在恒温箱中。
现场使用时,
置于保温桶内,超过4小时后须重新烘干,焊后所有的焊条头都必须回收到指定地点。
3.3焊接设备施焊前均应调试好。
3.4备有一定数量的焊机易损件、消耗件。
3.5施工现场焊机的电源配电箱摆放处应垫高300mm,并保证表面平稳。
3.6在施工现场的平台上设置横、立焊机机架各一个,以便焊机到达现场后重新调试。
3.7气电立焊所使用的CO2保护气体,使用前应经预热和干燥,其纯度不得低于99.5%,水
份含量不应超过0.005%。
3.8在下列任何环境中,如不采取有效的防护措施,不得进行焊接:
a)雨天、雪天和雾天;
b)手工焊时,风速超过8m/s;气电立焊或气体保护焊时,风速超过2m/s;
c)焊接环境气温:
普通碳素钢焊接时低于-20℃、16MnR焊接时低于-10℃、高强度钢焊接时低于0℃;
d)大气相对湿度超过85%,不宜进行现场焊接。
<以上防护措施见本方案7.0条>
3.9产品焊接试板
3.9.1产品焊接试板应在焊接工艺评定试验结果合格后进行,且应与现场焊接同步完成;
3.9.2产品焊接试板的数量除气电立焊外按各种焊接位置、焊接方法至少各一块,气电立焊产品试板至少应包括32mm、21.5mm及12mm三种规格的焊接接头,所有试板应在现场焊接产品前,由施焊油罐罐体的一般水平的焊工(或焊接操作工)采用与实际焊接相同的条件和相同的焊接工艺施焊。
3.9.3产品焊接试板的尺寸、式样、截取、试验方法应按JB4744-2000《钢制压力容器产品焊接试板的力学性能检验》的规定进行;
3.9.4产品焊接试板的焊缝应进行100%射线检测和100%超声检测,射线检测按JB/T4730.2-2005《承压设备无损检测第2部分:
射线检测》中的II级为合格,超声检测按JB/T4730.3-2005《承压设备无损检测第3部分:
射线检测》中的I级为合格。
4焊接施工程序
4.1总的焊接施工工序
施工准备
罐底中幅板焊接、试漏
\
罐底边缘板组焊
浮顶底板组焊、试漏
桁架、隔板组焊、试漏
第一节壁板立缝组焊
浮顶顶板组焊、试漏
第二节壁板立缝组焊
船舱气密试验
第一圈环缝组焊
第三节壁板立缝组焊
边缘板收缩缝组焊
大角缝组焊
第二圈环缝组焊
龟甲缝组焊
第四到六节壁板组焊
第一、二圈加强圈组焊
剩余焊缝真空试漏
第七节壁板组焊
第三圈加强圈组焊
第八节壁板组焊
第一、二圈抗风圈组焊
第九节壁板组焊
包边角钢组焊
4.2罐底边缘板的焊接
4.2.1焊接程序
对接缝外端300mm部位根部焊道焊接
PT检查
外端300mm焊缝
填平、盖面焊接
固定点焊
表面MT
待罐壁与罐底之间角焊缝焊完之后焊接剩余焊缝
RT检查
4.2.2坡口形式
4.2.3选用焊接工艺参数
a)边缘板焊接工艺参数如下表:
焊接
方法
焊接层次
焊条(丝/剂)
牌号
规格
电流(A)
电压(V)
焊接速度(cm/min)
手工焊
1
LB-62UL
φ4.0
130~180
25~30
5~10
手工焊
2~3
LB-62UL
φ4.0
130~180
25~30
5~10
手工焊
4~5
LB-62UL
φ4.0
130~180
25~30
5~10
b)外端300mm外的边缘板对接缝焊接工艺参数如下表:
焊接
方法
焊接层次
焊条(丝/剂)
牌号
规格
电流
(A)
电压
(V)
焊接速度(cm/min)
手工焊
1
LB-62UL
φ4.0
160~180
26~28
8~15
手工焊
2
LB-62UL
φ4.0
160~180
26~28
8~15
埋弧焊
3
US-40/MF300
φ2.4
350~500
28~40
25~40
埋弧焊
4
US-40/MF300
φ2.4
350~500
28~40
25~40
埋弧焊
5~6
US-40/MF300
φ2.4
350~500
28~40
25~40
埋弧焊
7~8
US-40/MF300
φ2.4
350~500
28~40
25~40
4.2.4质量要求
a)边缘板对接缝外端300mm焊接时全部采用焊条电弧焊,焊条为LB-62UL/φ4.0;除外端300mm外的边缘板对接缝焊接首先采用焊条电弧焊打底,焊条为LB-62UL/φ4.0,然后采用埋弧自动焊进行焊接,焊丝为US-40/φ2.4,焊剂为MF300;
b)焊缝应在充分干燥的条件下进行焊接,并应进行外观检查,检查前应将溶渣、飞溅清理干净;
c)焊缝的表面及热影响区不得有裂纹、气孔、夹渣和弧坑等缺陷;
d)焊缝的咬边深度不得大于0.5mm,咬边的连续长度不得大于100mm,焊缝两侧咬边的总长度,不得超过该焊缝长度的10%;
e)焊缝与母材之间应平滑过渡,咬边应打磨圆滑;
f)焊缝宽度应按坡口宽度两侧各增加1mm~2mm确定,焊缝余高不超过3.0mm;
g)每条边缘板对接缝外端300mm焊缝,应进行射线探伤,标准按照JB/T4730-2005中规定的Ⅱ级为合格。
h)边缘板的对接焊缝,在根部焊道焊接完毕后,应进行渗透检测,在最后一层焊道焊接完毕后,应进行渗透或磁粉检测。
i)罐底边缘板之间的对接焊缝坡口表面应进行磁粉检测或渗透检测,结果为Ⅰ级合格。
坡口检查合格后,应在坡口表面涂刷一道不影响焊接质量的防锈漆。
4.2.5注意事项及质量保证措施
a)垫板铺设完毕,边缘板铺设以前,将垫板从中心向两侧各30mm范围内用磨光机将铁锈等清除干净;
b)焊前坡口表面应进行磁粉探伤,坡口边缘100mm范围内进行超声波探伤;
c)先将第一块板与垫板整条点焊,另一张板外侧600mm与垫板点焊,以后依次类推;
d)组装定位焊应使垫板和边缘板严密结合,其间隙不得大于1mm;
e)定位焊长度50mm、间隔300mm;
f)定位焊应使用和正式焊接相同的焊条;
g)焊接时焊工应按圆周方向均布对称隔一焊道跳焊向同一个方向进行施焊。
焊前用液化气焰预热100℃以上;
h)采用多层焊,注意层间接头必须错开50mm以上;
i)先焊外端300mm范围内的焊缝,焊后将罐壁板落位处的焊道磨平,在大角缝焊后并在龟甲缝焊前将剩余焊缝焊完;
j)第一层焊道必须在边缘板外端垫板上停弧,后续焊道停弧处错开,最后一层焊道将边缘板外端焊满。
4.3罐底中幅板的焊接
4.3.1焊接程序
自动焊盖面(两端留200mm不焊)
根部焊道PT检查
)
短缝打底焊
焊短缝两端预留焊缝并检验
长缝打底焊并PT
长缝自动焊盖面
真空试漏
MT检查
焊长缝两端预留焊缝
4.3.2中幅板焊接顺序示意图:
4.3.3接头型式
4.3.4选用焊接工艺参数
选用焊接工艺参数如下表:
焊接
方法
焊接层次
焊条(丝/剂)
牌号
规格
电流
(A)
电压
(V)
焊接速度(cm/min)
气体保护焊
1
TWE-711
φ1.2
150~210
18~20
20~30
埋弧焊
2
HO8A/HJ431
+ER70S-6(碎焊丝)
φ4.0
550~650
35~40
30~40
4.3.5质量要求
a)焊缝应进行外观检查,检查前应将熔渣、飞溅清理干净;
b)焊缝的表面不得有裂纹、气孔、夹渣和弧坑等缺陷;
c)焊道两侧熔合良好,焊缝表面过渡圆滑均匀,不应有凸起现象;
d)按设计要求对打底焊焊道进行磁粉或渗透探伤,自动焊后,表面应进行渗透探伤或磁粉探伤。
4.3.6注意事项及质量保证措施
a)垫板铺设完毕,中幅板铺设以前,将垫板从中心向两侧各30mm范围内用磨光机将铁锈清除干净;
b)组装定位焊时应使垫板与中幅板严密结合,其间隙不得大于1mm;
c)定位焊时应使用和正式焊接相同的焊条,即采用J427φ3.2焊条,定位焊长度50mm,间隔300mm;
d)焊前应将坡口内的泥沙、铁锈、水及油污等杂物清理干净,并应在充分干燥的条件下进行焊接,坡口内若有水分,用氧炔焰烘烤干净;
e)焊接全部采用CO2气体保护焊打底,然后添加碎焊丝进行埋弧自动焊盖面;埋弧焊两端预留的200mm焊缝待根部焊道探伤合格后,用手工焊接完成;
f)焊接时焊工沿罐底中心线对称分布施焊,先焊短缝后焊长缝,由里向外,分段退步焊,长缝分5~7段,短缝视具体情况分2~3段;
g)打底焊时坡口根部与垫板熔合良好,打底厚度要均匀一致,一般为4mm~5mm为宜,不能将上坡口边缘熔化,层间清渣干净后才能进行盖面焊,且应和打底焊接头错开50mm以上,层间清理干净,不得有未焊透、咬边、烧穿等缺陷;
h)为防止起弧处产生气孔,应采用退弧引弧法;
i)不要在焊道以外的地方引弧;
j)长焊缝焊接前应在焊缝一侧离焊缝边缘100mm处打上与焊缝平行的型钢进行刚性固定,以减少焊接变形,型钢规格为Ⅰ16;
k)中幅板边缘焊缝150mm~200mm先不焊,待罐底边缘板收缩缝焊完之后再焊接;
l)焊前铺放焊机用的轨道时,要求轨道长度方向与焊缝平行,机长在焊接过程中密切注意焊丝落点,所有分段退步的接头处要求用磨光机修出一个缓坡。
焊接过程中不得随意调节电流和电压大小;
m)电焊把线,自动焊机电缆不得有破损,以免电弧烧伤罐底板;
n)中幅板对接焊缝在充水前后均用真空箱法进行气密性试验,试验负压值不得低于53kPa,无渗漏为合格;同时在充水前后要进行磁粉检测;
o)局部焊道外观成型不良及焊肉高度不够时,用J427φ4.0的焊条进行手工补焊,对MT及真空试漏不合格处要求由合格焊工进行返修,返修采用焊条电弧焊,焊条采用J427。
4.4罐底边缘板与中幅板之间的龟甲缝焊接
4.4.1焊接程序
真空试漏
4.4.2焊接坡口
4.4.3选用焊接工艺参数
选用焊接工艺参数如下表:
焊接
方法
焊接层次
焊条(丝/剂)
牌号
规格
电流
(A)
电压
(V)
焊接速度(cm/min)
气体保护焊
1
TWE-711
φ1.2
150~210
18~20
20~30
埋弧焊
2
HO8A/HJ431
+ER70S-6(碎焊丝)
φ4.0
550~650
35~40
30~40
4.4.4质量要求
a)焊缝应进行外观检查,检查前应将熔渣、飞溅清理干净;
b)焊缝的表面不得有裂纹、气孔、夹渣和弧坑等缺陷;
c)焊道两侧熔合良好,焊缝表面过渡圆滑均匀,不应有凸起现象;
d)龟甲缝焊接在边缘板收缩缝和中幅板预留焊缝焊完之后进行。
4.4.5注意事项及质量保证措施
a)中幅板根据组焊后位置进行修整开坡口,再组对点焊收缩缝;
b)定位焊采用LB-62UL焊条,定位焊长度50mm,间隔300mm,点焊应使垫板与边缘板、中幅板贴紧,其间隙不得大于1mm;
c)焊接分两次成型,打底用焊条电弧焊,第二层用填充碎焊丝的埋弧自动焊;
d)收缩缝和龟甲缝应在充水前后用真空箱法进行气密性试验,试验负压值不得低于53kPa,无渗漏为合格;
e)中幅板与边缘板之间的对接焊缝在全部焊完后,应进行渗透或磁粉检测,检测标准按照JB4730-2005,Ⅰ级合格。
f)罐底板所有焊缝的根部焊道焊完后,应进行渗透检测;全部焊完后,丁字焊缝在沿三个方向各200mm范围内及中幅板与边缘板的对接焊缝,应进行渗透或磁粉检测。
g)罐底所有焊缝应采用真空箱进行严密性试验,试验负压值不得低于53kPa,无渗漏为合格。
4.5罐底边缘板与罐壁之间的大角缝焊接
PT检查
自动焊盖面
4.5.1焊接程序
打磨焊道表面
内侧手工焊打底打底
外侧定位焊
打磨焊道表面
外侧手工焊打底打底
MT检查
打磨焊道表面
充水试验后MT复检
MT检查
打磨焊道表面
自动焊盖面
PT检查
4.5.2焊缝坡口及焊缝尺寸
4.5.3选用焊接工艺参数
选用焊接工艺参数如下表:
焊接
方法
焊接层次
焊条(丝/剂)
牌号
规格
电流(A)
电压(V)
焊接速度(cm/min)
手工焊
1
LB-62UL
φ4.0
130~190
25~30
8~15
手工焊
2
LB-62UL
φ4.0
130~190
25~30
8~15
埋弧焊
3~5
US-40\MF300
φ2.4
350~500
28~40
25~40
埋弧焊
6~8
US-40\MF300
φ2.4
350~500
28~40
25~40
4.5.4质量要求
a)焊缝应进行外观检查,检查前应将熔渣、飞溅等清理干净;
b)焊缝的表面不得有裂纹、气孔、夹渣和弧坑等缺陷;
c)内角缝靠罐底一侧的边缘应平滑过渡;
d)底层罐壁与罐壁边缘板之间的大角焊缝,在初层焊道焊完后,应进行渗透检测;在罐内及罐外角焊缝焊后进行磁粉探伤检查,油罐充水试验后应采用同样的方法进行复检;达到Ⅰ级合格;
e)保证焊脚尺寸。
4.5.5注意事项及质量保证措施
a)在第二条环缝组对完后进行角焊缝的组对焊接;
b)定位焊前先将坡口内的水分、铁锈、泥沙、油污等杂物清理干净;
c)定位焊在罐外侧进行,定位焊长度50mm,间隔300mm;
d)定位焊前要进行100℃预热;
e)使用和正式焊接相同的焊条,保证定位焊质量;
f)正式焊接前,先检查定位焊质量,有缺陷的部位打磨掉;
g)焊前去除坡口内的锈蚀、水分及其他污物,并用液化气火焰预热至100℃以上;
h)焊接方法采用焊条电弧焊内外角焊缝各封底一层,埋弧自动焊盖面;
i)焊接时焊工沿圆周方向均匀分布;
j)罐内外第一层焊道焊接时,沿同一方向退步焊,退步长度1500mm~2000mm;
k)埋弧焊接时沿同一方向进行焊接,每两名焊工(焊机)之间焊接焊缝长度差不大于2000mm;
l)埋弧自动焊起弧和收弧处应用砂轮机进行打磨修理;
m)埋弧焊接时调整好焊枪角度及层间焊道成型,使焊缝外观呈微凹形为宜;
n)层间接头错开50mm以上;
o)外侧手弧焊时,若风速过大,应采取有效的防风措施;
p)内角焊缝下部与边缘板母材连接处应用砂轮修磨平整;
r)内、外侧第一层手弧焊后应进行100%的PT;
s)充水前后均应进行100%MT;
t)PT、MT探伤结果均应不低于JB/T4730-2005的Ⅰ级合格标准。
4.6壁板立缝的焊接
4.6.1焊接程序
第一节壁板纵缝下部300mm焊缝手工焊接
气电立焊
RT检查
坡口间隙检查修整
组装定位焊
4.6.2坡口形式(见附图)
4.6.3选用焊接工艺参数
焊接工艺参数如下表:
立缝编号
焊接部位
焊接层次
焊接
方法
焊条(丝/剂)牌号
规格
电流
(A)
电压
(V)
焊接速度(cm/min)
第一圈
外侧
1
EGW
DWS-60G
φ1.6
300~400
34~40
10~14
内侧
1
EGW
DWS-60G
φ1.6
300~400
34~40
12~16
第二圈
外侧
1
EGW
DWS-60G
φ1.6
300~400
34~40
8~15
内侧
1
EGW
DWS-60G
φ1.6
300~400
34~40
8~15
第三圈
内侧
1
EGW
DWS-60G
φ1.6
300~400
34~40
6~12
第四圈
内侧
1
EGW
DWS-60G
φ1.6
300~400
34~40
8~15
第五圈
内侧
1
EGW
DWS-60G
φ1.6
300~400
34~40
10~15
第六圈
内侧
1
EGW
DWS-60G
φ1.6
300~400
34~40
10~15
第七圈
内侧
1
EGW
DWS-43G
φ1.6
340~360
35~37
13~14
第八圈
内侧
1
EGW
DWS-43G
φ1.6
340~360
35~37
13~14
第九圈
内侧
1
EGW
DWS-43G
φ1.6
340~360
35~37
13~14
4.6.4焊接方法
a)立缝组对从内侧进行,组对间隙为5mm,组对好后焊上E型板;
b)立缝错边量要求不大于1/10的板厚且不大于1.5mm;
c)所有立缝均采用手工电弧焊和气电立焊相结合的焊接方法;
d)第一节壁板纵缝下部约300mm采用手工焊接,其余各节壁板纵缝下部约50mm采用手工焊;
e)焊前彻底清除焊缝坡口表面及坡口两侧20mm范围内的油、锈、泥等污物;
f)第一圈纵缝焊接时,起弧时,在起弧处±50mm高度和焊缝中心线两侧各100mm范围内,采用氧气乙炔焰进行预热,其预热温度为100℃~150℃。
一侧焊完后用砂轮机打磨干净,必须将缺陷全部清除干净,个别熔透不好的部位,采用气刨清根后补焊,其余各圈立缝均要求去湿;
g)立缝焊接过程中因正常或非正常原因停止而重新起弧,会在接头处产生缺陷,此接头要用炭弧气刨将缺陷清除干净,然后用手弧焊焊接填满;
h)焊接中应保证焊道始端和终端的质量。
始端应采用后退引弧法,每条立缝起弧处宜从环缝坡口起弧,焊后将环缝内的焊肉割掉。
焊前先在壁板顶上点焊两块熄弧板。
熄弧板要求焊牢,焊后用氧—乙炔焰切割掉并打磨平整,焊条的使用同打底焊时手弧焊焊条的使用方法。
终端应将弧坑填满;
i)安装铜垫板时应注意:
1)对准缝将玻璃带粘在坡口面上,注意要使玻璃带处在坡口面的中心,禁止使用被水淋湿的玻璃带;
2)从底部起顺序将铜垫板固定到焊缝上,注意使铜垫板上的进出水口朝向分水管;
3)连接水管时,注意不要有水泄漏;
4)若不小心坡口内进水时,用氧气—乙炔焰使其充分干燥或更换玻璃带;
5)对于第一圈立缝,若铜垫板在内侧过于伸出时,会使铜垫板焊损以及根部熔合不良,应采用两层玻璃带等办法;
6)铜垫板之间的连接处要求紧密结合,且不得对偏。
j)第一、二圈立缝焊接分两次成型,先焊外侧,后焊内侧,内侧焊接前先用磨光机将焊渣清理干净;第三至九圈立缝从外侧进行焊接且一次成型;
k)两台焊机对称分布,朝同一方向自下而上进行焊接;
l)第一、二圈立缝双面焊的对接接头在背面焊接前用磨光机打磨,对于12MnNiVR还应作MT检测;
m)对板厚大于25mm的钢板,当采用碳弧气刨清根时,应进行预热,预热温度为100~150℃;
n)多层焊的层间接头应错开50mm。
4.6.5质量要求及注意事项
a)焊后应进行外观检查,检查前应将熔渣、飞溅等清理干净;
b)焊缝表面及热影响区不得有裂纹、气孔、夹渣和弧坑等缺陷;
c)焊缝的咬边深度不得大于0.4mm,咬边的连续长度不得大于100mm,焊缝两侧咬边的总长度不得超过该焊缝总长度的10%;
d)第一节及第二节壁板立缝的咬边均应打磨圆滑;
e)焊缝不得有低于母材表面的缺陷,内侧焊缝余高不得大于1mm,外侧焊缝余高为板厚δ>25mm时为≤3.0mm;12mm<δ≤25mm时为2.5mm;δ≤12mm时为1.5mm;
f)焊缝宽度应按坡口宽度两侧各增加1mm~2mm确定;
g)12MnNiVR钢板之间及12MnNiVR与16MnR之间的焊缝在焊接完成后应至少36小时才能进行无损检测;
h)厚度大于27mm的各层壁板的纵缝应100%进行射线检测。
4.7壁板环焊缝焊接
4.7.1焊接程序
RT检查
4.7.2坡口型式
4.7.3选用焊接工艺参数
焊接工艺参数如下表:
环缝
编号
焊接
部位
焊接层次
焊接
方法
焊条(丝/剂)牌号
规格
电流
(A)
电压
(V)
焊接速度(cm/min)
第一圈
外侧
1~8
SAW
US-49/MF-33H
φ3.2
450~500
27~28
45~60
内侧
9~14
SAW
US-49/MF-33H
φ3.2
450~500
27~28
47~69
第二圈
外侧
1~3
SAW
US-49/MF-33H
φ3.2
300~500
24