广安脱硫运行说明.docx
《广安脱硫运行说明.docx》由会员分享,可在线阅读,更多相关《广安脱硫运行说明.docx(35页珍藏版)》请在冰豆网上搜索。
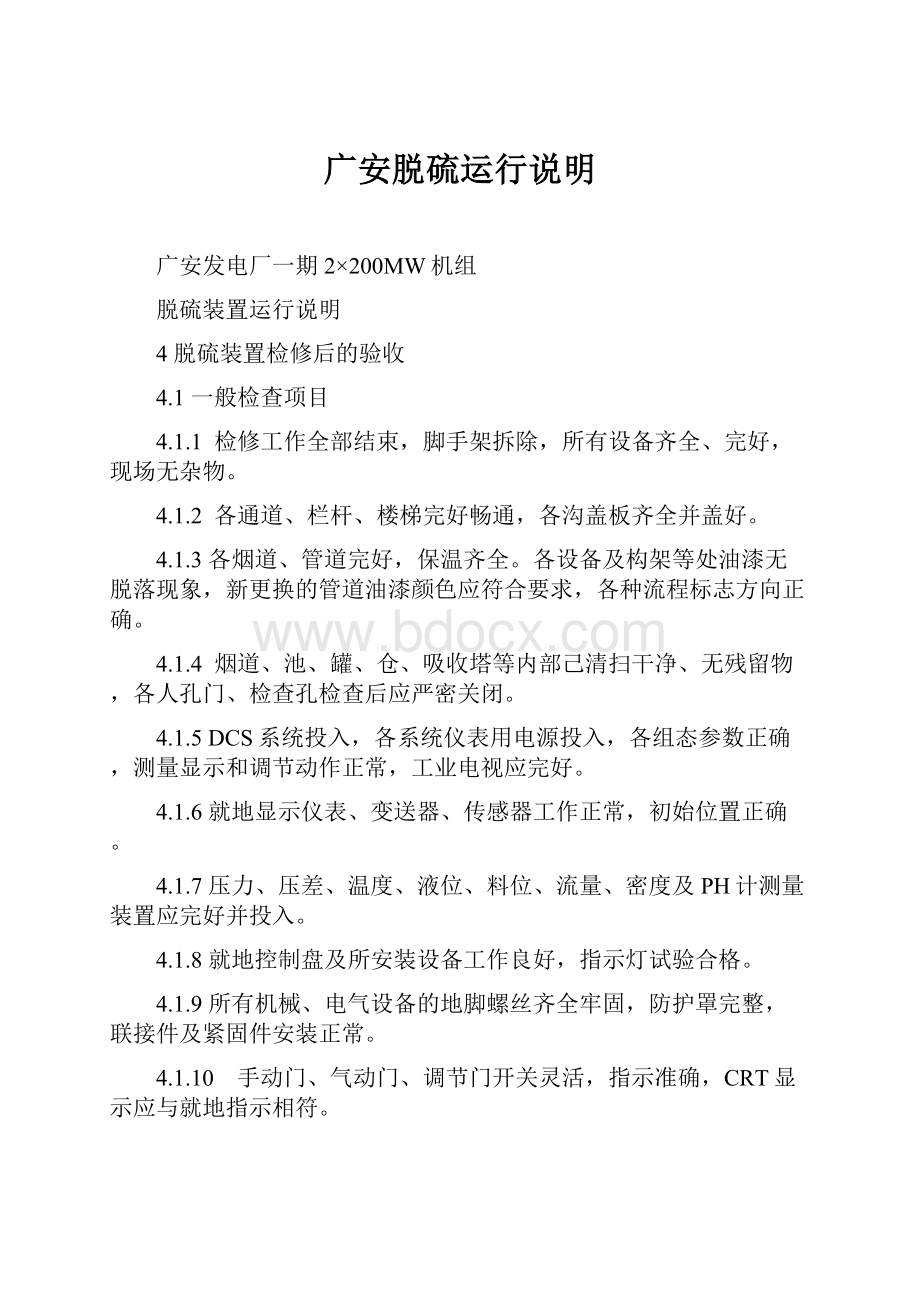
广安脱硫运行说明
广安发电厂一期2×200MW机组
脱硫装置运行说明
4脱硫装置检修后的验收
4.1一般检查项目
4.1.1检修工作全部结束,脚手架拆除,所有设备齐全、完好,现场无杂物。
4.1.2各通道、栏杆、楼梯完好畅通,各沟盖板齐全并盖好。
4.1.3各烟道、管道完好,保温齐全。
各设备及构架等处油漆无脱落现象,新更换的管道油漆颜色应符合要求,各种流程标志方向正确。
4.1.4烟道、池、罐、仓、吸收塔等内部己清扫干净、无残留物,各人孔门、检查孔检查后应严密关闭。
4.1.5DCS系统投入,各系统仪表用电源投入,各组态参数正确,测量显示和调节动作正常,工业电视应完好。
4.1.6就地显示仪表、变送器、传感器工作正常,初始位置正确。
4.1.7压力、压差、温度、液位、料位、流量、密度及PH计测量装置应完好并投入。
4.1.8就地控制盘及所安装设备工作良好,指示灯试验合格。
4.1.9所有机械、电气设备的地脚螺丝齐全牢固,防护罩完整,联接件及紧固件安装正常。
4.1.10 手动门、气动门、调节门开关灵活,指示准确,CRT显示应与就地指示相符。
4.1.11 电气系统表计齐全完好,开关柜内照明充足,端子排、插接头等无异常松动和发热现象。
4.1.12开关、接触器及各种保险管齐全完好,保险的规格与设计值相符,马达加热器连接正确、完好。
4.1.13各种开关的分合闸指示明显、正确,分合闸试验合格。
4.2分系统检查
4.2.2烟气系统及密封系统的检查
4.2.2.1检查脱硫装置进、出口烟气挡板和旁路挡板安装完好,其旁路挡板应开启,净烟气挡板及原烟气挡板应严密关闭。
4.2.2.2 各挡板电动执行装置应完好,连杆、拐臂连接牢固,在就地用手摇各挡板应开关灵活,无卡涩现象,挡板开关位置指示正确,并处于自动位置。
4.2.2.3 挡板的密封风机外形完好,靠背轮连接牢固,旋转灵活,无卡涩现象,地脚螺丝牢固,保护罩完整牢固。
4.2.2.4 密封风机的进、出口管道应安装牢固,密封风机进气门应关闭,其电加热装置完好并处于停运状态。
4.2.2.5 各挡板密封装置完好,密封管道畅通。
4.2.2.6 各膨胀节应完好,安装牢固,膨胀自由。
4.2.2.7 烟道内防腐层应完好无脱落。
4.2.2.8 GGH系统安装完好。
4.2.3箱、罐、池及吸收塔的检查
4.2.3.1各箱、罐、池及吸收塔的外形完整无变形,各焊接处焊接牢固,各管道膨胀自由。
4.2.3.2各箱、罐、池及吸收塔的衬胶完整无老化、无腐蚀,且衬胶与塔壁粘接牢固无起泡处。
4.2.3.3吸收塔原烟气入口处不锈钢雨棚无磨损、腐蚀和变形。
4.2.3.4吸收塔内氧化空气供气管连接牢固,且其出口无结垢和异物堵塞。
4.2.3.5吸收塔各层喷嘴排列整齐,连接牢固。
各喷嘴完好无磨损、无堵塞。
各喷嘴连接管道无破裂、无老化、无腐蚀。
4.2.3.6除雾器连接牢固,完好,无老化、无腐蚀、无积浆或积灰。
4.2.3.7除雾器冲洗喷嘴安装牢固、齐全,各喷嘴喷射方向正确,无堵塞。
4.2.3.8石灰石浆液箱和石膏浆液箱内的折流板安装牢固、无磨损、无腐蚀。
4.2.4转动机械的检查
4.2.4.1通则
4.2.4.1.1 减速器、轴承油室油位正常,油镜清晰,油质良好,有高、低、正常油位标志,轴承带油良好,用润滑油脂润滑的轴承,应有足够的油脂。
4.2.4.1.2 各设备的油质良好,油位计及油镜清晰完好。
各油箱油位应在正常范围以内,电加热器应完好,油过滤器安装正确,切换灵活。
4.2.4.1.3 联轴器连接牢固,旋转灵活无卡涩,地脚螺丝紧固,保护罩安装完整、牢固。
4.2.4.1.4 转动机械周围应清洁,无积油、积水及其它杂物。
4.2.4.1.5 电动机绝缘合格,电源线、接地线连接良好,旋转方向正确。
电流表、启、停开关指示灯应完好,电流表应标有额定电流红线。
4.2.4.1.6 轴承及电动机线圈温度测量装置完好,可靠。
4.2.4.1.7 各冷油器冷却风机进、出口管路畅通,连接牢固。
4.2.4.1.8 各传动皮带轮连接牢固,皮带无跑偏现象。
4.2.4.1.9 各处事故按钮完好。
4.2.4.1.10各转机的速度测量装置应完好。
4.2.4.2搅拌器的检查
4.2.4.2.1 各箱、罐、池及吸收塔搅拌器叶片安装牢固、无磨损、无腐蚀。
4.2.4.2.2 吸收塔各侧入式搅拌器安装下倾角及切圆角度应正确。
4.2.4.2.3 各箱、罐、池顶入式搅拌器应垂直安装,双叶轮搅拌器的连接轴连接牢固且同心。
4.2.4.2.4 各搅拌器轴封安装完好,冲洗水管道畅通无杂物堵塞。
4.2.4.3增压风机的检查
4.2.4.3.1 风机的入口集气箱和出口扩压管的膨胀节联接牢固,膨胀自由。
4.2.4.3.2 润滑油系统无异常,并启动油泵试转正常。
4.2.4.3.3 润滑油系统冷油器完好,且其冷却风机试转正常。
4.2.4.3.4 轮毂加热器完好无异常。
4.2.4.3.5 密封风机及加热器完好无异常。
4.2.4.3.6 就地手摇增压风机前导叶,检查其实际开度与指示相符后,将手动切换为自动。
4.2.4.3.8 用DCS远方操作增压风机前导叶,检查其实际开度与指示值是否相符,动作是否灵活。
4.2.4.3.9 风机出口管道滑动装置安装正确,滑轨上应无障碍物。
4.2.4.4氧化风机的检查
4.2.4.4.1 氧化风机本体和电机外形正常,空气管道消音器、过滤器清洁无杂物。
4.2.4.4.2 氧化风机隔音罩完好,排风扇启停正常。
4.2.4.4.3 风机出口启动气动门排气口无障碍物。
4.2.4.4.4 润滑油系统无异常,启动辅助油泵试转正常。
4.2.4.4.5 润滑油系统冷油器完好。
4.2.4.5泵的检查
4.2.4.5.1 检查各泵机械密封装置完好,无漏泄。
4.2.4.5.2各机械密封冷却水管道安装完整,无泄漏。
4.2.4.5.3 各泵吸入口滤网清洁无杂物堵塞。
4.2.4.5.4 各泵轴承油杯应有足够润滑油。
4.2.4.5.5 各电源线、接地线应连接良好。
4.2.4.6球磨机的检查
4.2.4.6.1 冷却水管应畅通,各冷油器外形正常,冷却水适量,无漏油和漏水现象。
4.2.4.6.2 减速器、传动装置、筒体螺栓及大齿轮连接螺栓牢固,进、出口导管法兰等螺栓应紧固、完整。
4.2.4.6.3 球磨机周围应无积浆、杂物,人孔门应严密关闭。
4.2.4.6.4 球磨机检修完毕,筒体内应按规定补充一定量的、规定大小的钢球。
4.2.4.6.5 大齿轮润滑油系统各油、气管道、支吊架完好,油管、气管无堵塞、无漏气、漏油现象。
喷雾板应固定牢固、完好,润滑油箱油位正常。
4.2.4.6.6 大小齿轮内已加入了足够的润滑油。
4.2.4.6.7 就地操作盘上各表计、指示灯应完好齐全。
4.2.4.6.8 就地盘内各设备应整洁。
空压机皮带完好,松紧适当,空压机出口门应开启,启动前应开启储气罐的放水门疏水,空气入口滤网应完好无堵塞。
4.2.4.6.9 球磨机盘车装置的推杆进退自如,爪形离合器完好并处于断开位置。
4.2.4.6.10 液力偶合器外形完好,充油适量,易熔塞完好无漏油现象。
4.2.4.6.11 球磨机出口格筛完好、清洁无杂物堵塞,其杂物斗内应无杂物和积浆。
4.2.4.7称重皮带给料机的检查
4.2.4.7.1 称重皮带给料机进、出料口应畅通,石灰石厚度调节装置调整适当。
4.2.4.7.2 就地盘称重测量装置应完好准确,并已校核。
4.2.4.7.3 皮带主轮、尾轮应安装良好,托辊齐全。
4.2.4.7.4 皮带无破裂、无损伤,接头完好,皮带上应无杂物。
4.2.4.7.5 受料槽安装正确,无破损。
4.2.4.8石灰石仓及刮刀式卸料机的检查
4.2.4.8.1缓冲锥体和刮刀卸料机的刮刀安装牢固,无磨损。
4.2.4.8.2齿轮转动机构应完好,并有足够的润滑油脂。
4.2.4.8.3齿轮转动机构的电机冷却风机完好,其进、出口应畅通。
4.2.4.8.4齿轮油箱油位正常,油泵完好,其供油管路畅通。
4.2.4.8.5刮刀卸料机的下料管应畅通,无磨损。
4.2.4.8.6各仓的进料管应畅通无堵塞。
4.2.4.8.7石灰石仓除尘器的振打装置及除尘风机应完好,滤袋无破损和积灰。
4.2.4.8.8石灰石缓冲仓外形正常,进、出口管道应畅通,且无磨损。
4.2.4.8.9石灰石仓内应无水源进入。
4.2.4.8.10料位测量显示应准确,并已校核。
4.2.4.9螺旋输送机的检查
4.2.4.9.1螺旋输送机内应无杂物和积块,外形正常,地脚螺栓牢固,并严密关闭检查孔。
4.2.4.9.2试转电动机正常,旋转方向正确,电机绝缘合格,电源线、接地线连接良好。
4.2.4.9.3靠背轮连接牢固,旋转灵活、无卡涩现象;地脚螺栓紧固,保护罩完整、牢固。
4.2.4.9.4轴承润滑油脂充足。
4.2.4.10斗式提升机的检查
4.2.4.10.1检查提升机竖井内应无障碍物,底部无石灰石堆积。
4.2.4.10.2斗与皮带连接应完好、牢固。
各料斗外形正常,无磨损和变形。
4.2.4.10.3调紧装置应灵活,试转提升机应正常(无卡涩),皮带无跑偏现象,且接头联接牢固。
4.2.4.10.4斗式提升机驱动装置安装牢固。
4.2.4.10.5皮带无破裂、无损伤,不打滑。
4.2.4.12振动给料机及金属分离器的检查
4.2.4.12.1卸料斗格栅应完好,格栅上应无杂物。
4.2.4.12.2振动给料机的机座及减振弹簧应完好、牢固,各支架、螺栓连接应无裂纹和松动。
4.2.4.12.3振动给料机的进、出口应畅通,无严重磨损。
4.2.4.12.4振动装置应完好,试转振动给料机应正常,给料方向正确。
4.2.4.12.5检查金属分离器弃铁皮带应无跑偏,皮带无破损现象。
4.2.4.12.6应保持金属分离器吸铁距离在250mm以内。
4.2.4.12.7电磁铁接线应正确,试转时应正常。
4.2.4.12.8弃铁箱应清理干净。
4.2.4.13除尘器的检查
4.2.4.13.1检查除尘风机冷却风道畅通,各部件连接牢固,消音器外形正常,入口应无破损,滤网上无积灰和杂物。
4.2.4.12.2除尘器滤袋应完好、清洁,无积灰,各空气管道应畅通、无堵塞。
4.2.4.12.3试转螺旋输送机及旋转锁气器应正常,旋转方向正确,且速度测试正确可靠。
4.2.4.12.4检查反吹压缩机的进口滤网清洁无杂物堵塞。
4.2.4.12.5反吹压缩机贮气罐外形完好,开启贮气罐疏水门,疏水3—5min后关闭。
贮气罐安全门排气口应畅通。
4.2.4.12.6检查就地盘的开关,指示灯,标志应齐全、准确。
4.2.4.12.7试投除尘器工作正常后,停止其运行。
4.2.5石膏(石灰石)旋流浓缩站及脱水机的检查
4.2.5.1旋流器的检查
4.2.5.1.1浆液分配箱外形完好,各个旋流器安装正确,漏斗无堵塞。
4.2.5.1.2各旋流器底流流出口应无磨损。
4.2.5.1.3石膏旋流器浆液分配箱溢流应畅通无堵塞。
4.2.6.2脱水机及石膏皮带输送机的检查
4.2.5.2.1脱水机滤布、槽形皮带、滑道安装正确,各支架安装牢固,皮带上无剩余物,皮带张紧适当。
4.2.5.2.2皮带和滤布托辊转动自如无卡涩现象。
4.2.5.2.3皮带主轮和尾轮安装完好,轮与带之间应无异物。
皮带和滤布应完好,无划伤或抽丝现象。
4.2.5.2.4皮带下料处石膏清理器安装位置适当,下料口清理干净。
4.2.5.2.5皮带进浆分配管畅通均匀,无堵塞。
4.2.5.2.6滤布冲洗水、滑道冷却水、真空盒密封水管路畅通,无堵塞。
4.2.5.2.7真空盒与皮带之间间隙适当,其管路畅通,密封严密。
4.2.5.2.8真空泵、滤液水泵、冲洗水泵、滤饼冲洗水泵安装完好,管路畅通。
4.2.5.2.9开启真空泵冷却水门和真空泵密封水进口门,开启真空泵的排水阀向冲洗水箱注水至溢流。
4.2.5.2.10开启调偏装置仪用空气阀,检查滤布位置偏移传感器是否准确、灵敏;托辊的位移方向正确。
检查完毕,停止其运行。
4.2.5.2.11启动石膏皮带输送机,检查其前进、停止是否可靠,试转正常后停止其运行。
4.2.5.2.12控制方式置远方,确认DCS石膏厚度输出值为零。
4.2.5.2.13调整真空盒高度适当,其调整装置应灵活。
密封条密封良好,滑道密封水应适当。
4.2.5.2.14试转脱水机,检查其走带正常,滤布重锤位置正常,张紧度适当,将走带速度逐渐增加至100%,检查运转声音正常,确认皮带及滤布位置正常后,停止其运行。
4.2.6转动机械的试运转
转动机械新安装或大修后应进行试运转,试转时间不少于2h,以验证其可靠性。
转动机械试运行时,应遵守《电力安全工作规程》的有关规定。
试转完毕后,将负荷减至最小,然后分别用事故按钮逐个停止转机运行。
转机试运合格应符合下列要求:
转动方向正确.。
转动机械应无摩擦、撞击等异声。
轴承温度与振动应符合有关规定。
轴承油室油镜清晰,油位线标志清楚,油位正常,油质良好,轴承无漏油、甩油现象。
检查转机各处无油垢、积灰、积浆、漏风、漏水等现象。
各风门应关闭严密,以防止停用时风机反转。
皮带应无跑偏、打滑现象。
转机试转后,将试转情况及检查中所发现的问题,做好详细记录,汇报班长、值长及有关部门。
4.2.7脱硫装置的联锁保护试验
脱硫装置在启动前,必须作各种联锁和保护试验,试验由有关单位参加,同时向值长联系该项工作。
此项工作应在各设备检修工作全部结束后,并经验收合格方可进行。
4.2.7.1 脱硫装置的保护动作条件
4.2.7.1.1根据锅炉运行情况,进行烟气系统(挡板)热态或冷态联锁保护试验。
(试验方法在调试时确定)
4.2.7.2 联锁试验方法
4.2.7.2.1断开各试验转机的工作电源送上试验电源。
4.2.7.2.2联系热工,送上有关气动执行器、仪表、信号、DCS等装置的操作电源、保护电源。
4.2.7.2.3制浆系统、石灰石预处理系统、增压风机、氧化风机等装置的联锁或联动投入。
合上各转机开关,分别用事故按钮,逐个停止金属分离器、振动给料机、预破碎机、螺旋输送机、斗式提升机、石灰石刮刀卸料机、称重皮带机、球磨机、吸收塔再循环泵、增压风机、氧化风机、搅拌器、脱水机、真空泵、石膏皮带输送机、石灰石浆液泵、石膏浆液泵等应动作正常。
4.2.7.2.4重新合上上述开关,依次进行各设备的联动或联锁试验。
4.2.7.2.5电(气)动阀门试验:
a)电(气)动门试验应由热工人员、机务检修人员、运行人员三者参加。
b)试验前联系送电并检查电(气)动门控制装置良好。
c)全开全关电(气)动门,要求开关灵活,无卡涩现象。
d)电(气)动门关完时要求无漏流并且可靠。
e)电(气)动门试验应做好如下记录:
全开、全关的行程时间。
4.2.7.2.6调节门、调节挡板试验:
新安装或检修后的调节门,调节挡板应进行开关试验,由热工人员、检修人员和运行人员共同进行。
电动远操全开、全关一次,观察传动装置及阀门、挡板动作应符合试验要求。
试验要求:
传动装置无卡涩,轻便灵活,风门、挡板、调节门开关方向应与指示方向一致,开、关应到位,漏流应符合要求。
4.2.7.2.7声光信号试验:
联系热工、电气进行事故音响、报警和光字牌试验。
4.2.7.2.8球磨机低油量保护试验:
(见厂家说明书)
4.2.7.2.9氧化风机低油压保护试验:
当氧化风机润滑油压低至Ⅱ()值,油压低Ⅱ值发出跳闸信号,相应氧化风机跳闸。
4.2.7.2.10试验注意事项:
a)球磨机、增压风机及氧化风机做总联锁或低油压试验时,均做操作电源试验,严禁做动力电源试验(联锁控制部分检修时除外)。
b)做各联锁、球磨机低流量及保护试验时,发现的问题应报告值长,由电气、热工人员消除后再做,直至合格。
c)各联锁在大修或联锁回路检修后必须做动态试验。
d)转动设备试验前按转机启动前检查要求进行。
e)各联锁、保护试验合格后,将各联锁保护开关置于‘投入’位置,做好记录,汇报值长。
5 脱硫装置的启动
5.1公用系统的启动
5.1.1压缩空气系统的启动
5.1.3.1开启压缩风机进口阀。
5.1.3.2开启压缩风机冷却水阀。
(首次启动用临时水源或新加装水源)
5.1.3.2启动压缩风机。
5.1.3.3检查压缩空气罐压力达到bar,压缩风机自动停止.
5.1.3.4开启压缩空气出口总阀。
5.1.2工艺水系统的启动
5.1.2.1检查工艺水箱外形正常,滤网无堵塞,并有水位指示,溢水管畅通,放水门应严密关闭。
5.1.2.2检查工艺水箱供水管道应畅通,节流孔板应无堵塞。
5.1.2.3工艺水系统的冲洗和投入
联系化学,脱硫投工艺水。
开启工艺水箱底部放水总门。
开启工艺水箱进水气动阀。
对工艺水箱进行冲洗。
冲洗3—5min,确认冲洗合格后,关闭工艺水箱底部放水手动门,向工艺水箱进水。
当工艺水箱液位达到m时,启动其中一台工艺水泵SGC运行。
5.1.3低压挡板密封系统的启动
5.1.3.1开启低压密封风机进口挡板。
5.1.3.2开启低压密封空气出口挡板。
5.1.3.3逐个开启烟气挡板的密封气进气手动门和电动门(处于关闭状态的烟气挡板)。
5.1.3.4确认烟道内无人检修,投入电加热器,将空气加热至约℃左右。
(此启动过程同样适用于高压挡板密封系统,高压挡板密封系统的启动在增压风机后原烟气挡板关闭前完成)
5.2箱、罐、池及吸收塔的上水和冲洗
5.2.1制浆系统的冲洗及上水
5.2.1.1球磨机循环箱的冲洗及上水
5.2.1.1.1开启工艺水至球磨机循环箱进水气动门,上水至溢流。
5.2.1.1.2开启球磨机循环箱底部排浆手动门,对循环箱进行冲洗。
5.2.1.1.3冲洗3-5min,确认冲洗合格后,关闭球磨机循环箱底部排浆手动门。
5.2.1.1.4开启球磨机循环泵入口气动门、排浆手动门,对该泵吸入管进行冲洗,冲洗3-5min,确认冲洗合格后,关闭该泵入口管排浆手动门及入口气动门。
5.2.1.1.5循环箱液位达到40%以上时,启动该浆液箱搅拌器运行。
5.2.1.2球磨机旋流器的冲洗及上水
5.2.1.2.1开启制浆系统冲洗工艺水手动总门及#1球磨机循环泵冲洗气动门。
5.2.1.2.2开启#1循环泵出口气动门,逐个开启各旋流子进浆分门,对旋流器进行冲洗,同时向石灰石浆液箱上水。
5.2.1.2.3冲洗3-5min,确认冲洗合格后,关闭#1循环泵出口气动门,#1循环泵冲洗气动门。
5.2.1.2.4打开#2循环泵出口气动门,#2循环泵冲洗气动门,对#2冲洗管进行冲洗至合格。
5.2.1.2.3关闭#2循环泵出口气动门,#2循环泵冲洗气动门及各旋流子进浆分门。
5.2.2石灰石浆液箱上水及冲洗
5.2.2.1开启石灰石浆液箱工艺水进水手动门、气动门。
5.2.2.2石灰石浆液箱上水至溢流时,关闭石灰石浆液箱工艺水进水气动门,开启石灰石浆液箱底部排浆手动门。
5.2.2.3冲洗3-5min,确认冲洗合格后,关闭石灰石浆液箱底部排浆手动门。
5.2.2.4依次开启石灰石浆液泵进口气动门及排浆门,对石灰石浆液泵吸入管进行冲洗。
5.2.2.5冲洗3-5min,确认冲洗合格后,关闭石灰石浆液泵进口气动门及该泵吸入管排浆手动门。
5.2.2.6石灰石浆液箱水位放至m时,关闭石灰石浆液箱排浆门,启动石灰石浆液箱搅拌器运行。
5.2.3石膏旋流浓缩站冲洗及石膏浆液箱上水
5.2.3.1开启石膏排出泵进、出口气动门,石膏排出泵冲洗水手动门和气动门。
5.2.3.2开启石膏排出泵后母管至吸收塔再循环调节门,调节门前后气动门及旁路气动门,冲洗3-5min,确认冲洗合格后关闭,关闭石膏排出泵进口气动门。
5.2.3.3打开石膏排出泵后母管至石膏石膏旋流站气动门。
5.2.3.4依次开启石膏旋流站各旋流子进浆气动门对各旋流子进行冲洗,冲洗3—5min,确认冲洗合格后,依次关闭上述进浆气动门。
5.2.3.5关闭石膏排出泵后母管至石膏石膏旋流站气动门,石膏排出泵冲洗水气动门。
5.2.3.6依次打开石膏浆液泵各冲洗水门和泵进口放浆门冲洗至合格后关闭泵进口放浆门。
5.2.3.6打开石膏浆液泵进口门,冲洗石膏浆液泵进口管线至合格,同时向石膏浆液箱上水。
5.2.3.7石膏浆液箱上水至溢流,关闭石膏浆液泵冲洗水门,开启石膏浆液箱底部排浆手动门,冲洗至合格后关闭。
5.2.3.8通过石膏排出泵冲洗水和石膏浆液泵冲洗水向石膏浆液箱上水。
5.2.3.9石膏浆液箱液位m以上,启动石膏浆液箱搅拌器运行。
5.2.4吸收塔冲洗及上水
5.2.4.1开启除雾器冲洗水管线各手动门,启动除雾器冲洗水泵SGC,并投入除雾器冲洗程序向吸收塔上水。
5.2.4.2吸收塔内液位约m时,开启吸收塔底部排浆手动门。
5.2.4.3确认吸收塔放水水质清洁无杂物后,关闭吸收塔底部排浆手动门,若吸收塔内杂物较多,应将吸收塔内水放尽后,再重新向吸收塔上水,直至冲洗合格。
5.2.4.4确认吸收塔冲洗干净,液位m时,启动搅拌器运行。
5.2.5吸收塔充浆
5.2.5.1开启吸收塔底部排浆手动门,向吸收塔区域集水坑上水。
5.2.5.2吸收塔区域集水坑内液位达到m时,启动该集水坑搅拌器运行。
5.2.5.3启动吸收塔区域集水坑泵,开启该泵出口气动门及至吸收塔气动门,关闭该泵至缓冲箱手动门。
调整吸收塔底部排浆手动门,保持集水坑水位稳定。
5.2.5.4确认系统倒换正常后,向吸收塔区域排水沟内人工加入事先准备好的石膏晶种约100t。
5.2.5.5配浆完毕,关闭吸收塔底部排浆手动门.
5.2.5.6视吸收塔区域集水坑液位情况,停止集水坑泵运行,并对管线进行冲洗。
5.3 石灰石输送系统的启动
5.3.1除尘器的启动
启动石灰石仓振打式除尘器。
分别开启卸料斗及预破碎机至除尘器吸入管手动门,开启反吹压缩机储气罐疏水门,放水3—5min后,关闭该门。
启动除尘器风机及反吹压缩机,维持储气罐压力正常。
启动除尘器旋转锁气器及其螺旋输送机。
开启除尘器反吹系统各门。
当除尘器进出口压差至Pa时,对滤袋进行自动反吹。
5.3.2 预破碎系统的启动
确认卸料斗内有石灰石,启动石灰石仓进料螺旋输送机。
启动斗式提升机。
启动金属分离器。
启动振动给料机。
启动完毕,检查各处下料均匀。
5.4制浆系统的启动
5.4.1 启动声光信号报警。
5.4.2 开启球磨机油系统各冷却水门。
5.4.2开启球磨机进、出口大瓦油泵及高压顶轴油泵入口手动门、减速器油泵进、出口各手动门。
启动球磨机进出口大瓦、减速器油泵及高压顶轴油泵运行,确认各处供油量正常。
5.4.3 开启球磨机大齿轮喷淋系统各门,对喷淋系统就地盘送电,然后启动喷淋系统空压机,并投入喷淋系统。
5.4.4 开启工艺水至球磨机和循环箱各手动门、气动门。