ZF20704成品与出货检验程序.docx
《ZF20704成品与出货检验程序.docx》由会员分享,可在线阅读,更多相关《ZF20704成品与出货检验程序.docx(13页珍藏版)》请在冰豆网上搜索。
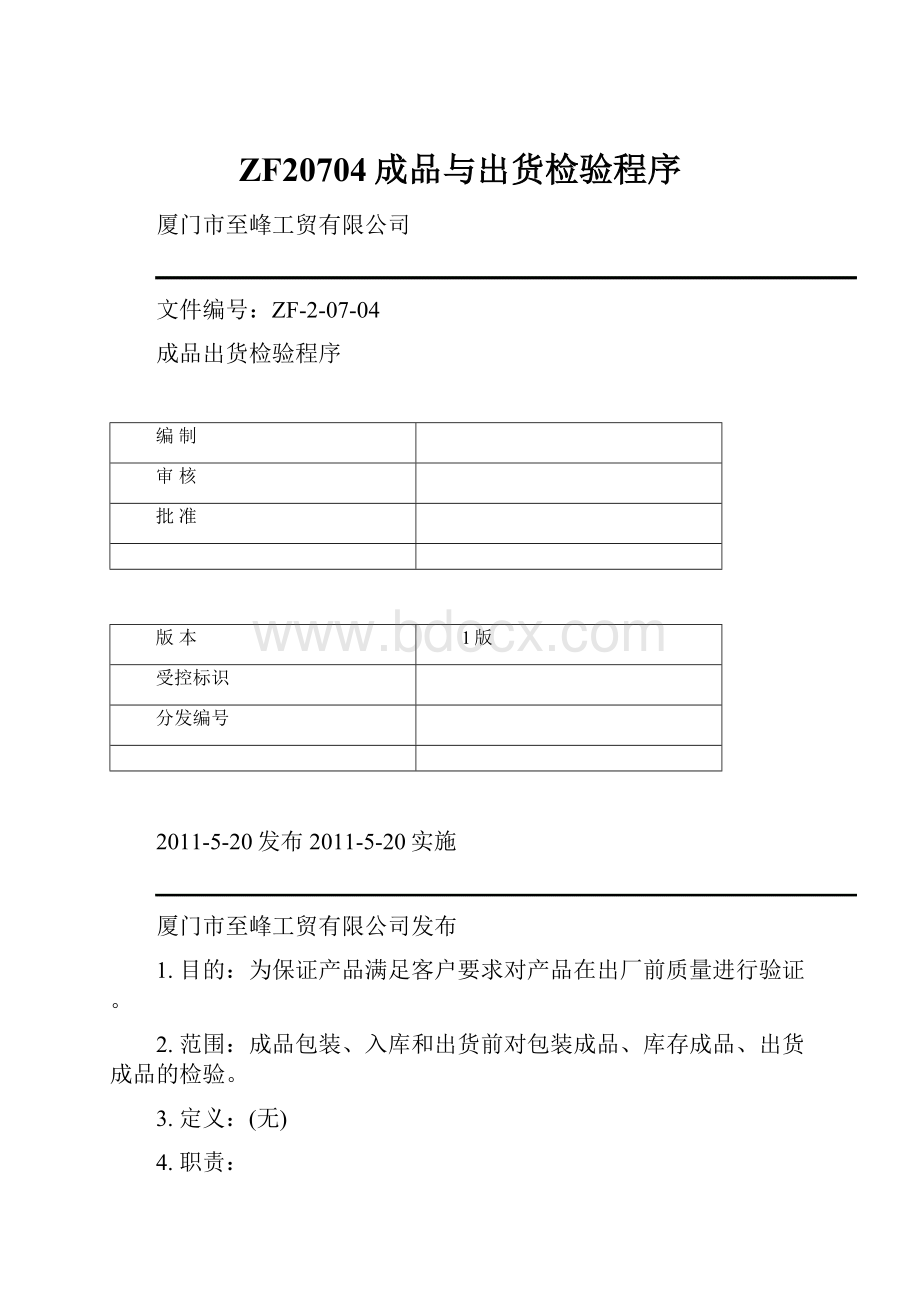
ZF20704成品与出货检验程序
厦门市至峰工贸有限公司
文件编号:
ZF-2-07-04
成品出货检验程序
编制
审核
批准
版本
1版
受控标识
分发编号
2011-5-20发布2011-5-20实施
厦门市至峰工贸有限公司发布
1.目的:
为保证产品满足客户要求对产品在出厂前质量进行验证。
2.范围:
成品包装、入库和出货前对包装成品、库存成品、出货成品的检验。
3.定义:
(无)
4.职责:
4.1.品管部:
4.1.1.品管部QE:
A.成品检验标准、原始订单、检验等依据的收集、建立和提供;
B.质量异常的稽核和提报、追踪;
C.质量记录的整理存档,统计分析;
D.客户验货准备、陪同及记录,验货结果、客户要求事项等的整理发布,处理结果追踪。
4.1.2.品检PQC:
A.包装成品(含首件检验)、库存成品的检验和判定。
B.成品检验记录的填写、质量记录的收集、汇总给品管部QE统计;
C.质量问题的反馈、处理、追踪及纠正预防措施的落实及跟踪;
D.不良品的管制、标识。
4.1.3.品管部OQC:
A.整理准备检验依据,并依照进行检验。
B.库存成品\出货成品检验的执行及异常的反馈、监督处理。
C.出货检验报告的填写、汇总。
4.2.资材仓库:
成品包装、成品储存、成品装货。
4.3.制造单位:
产品的自检、质量异常的纠正预防措施的提出和处理。
4.4.技术部:
技术资料、包装方式、装柜方式的确定和辅导。
5.作业内容:
5.1.包装成品首件确认:
5.1.1.批量成品包装前,由包装组依据《制造命令单》、《包装作业指导书》、有效的产品图纸,《产品检验规范》等文件,详细了解客户的包装要求(如唛头、标签、条形码等),使用对应的包装材料和包装方法进行包装,必要时通知技术部进行辅导。
5.1.2.首件制作完成由品检人员进行首件确认,首件确认必须完成如下的检验项目:
A.确认包装的正确性:
包装材料的材质、规格、尺寸和包装方式、产品及所需零配件数量。
B.确认包装的符合性:
客户要求的唛头、标签、条形码、包装方式等。
C.确认包装的安全性:
技术部包装设计员和品管部QE应在品质策划阶段,对包装的合理性和安全性进行验证。
品检人员首件确认时应再次检查各部件间是否保护、固定良好,必要时进行跌落和颠簸实验。
D.验证包装材积和重量。
5.2.包装成品过程检验:
依据《制程检验办法》执行包装成品的过程检验.
5.3.包装成品入库检验:
5.3.1.所有包装成品在入库时均应得到有效的检验,合格后方可入库。
5.3.2.检验依据:
《制造命令单》、《产品检验规范》、《抽样计划表》、产品图纸及相关《包装作业指导书》等资料
5.3.3.产品外观检验:
A.颜色是否与《制造命令单》要求色号一致,各部件之间是否存在色差。
B.喷粉的产品表面不能有超过限度的色差、混色、麻点、针孔、桔皮、流挂、积粉、露底、污染、起泡、爆粉及油污、管内生锈等现象。
C.电镀产品表面应均匀、不能有超过限度的变色、烧伤、脱皮、发黄、水渍、水印、水锈、麻点、毛刺、管内生锈等现象。
D.零配件颜色是否符合相关资料要求。
E.产品不得有超过限度的研磨砂痕,毛刺、飞溅物、焊渣是否打磨干净,产品是否划伤,产品是否变形。
5.3.4.产品尺寸、装配和性能检验:
A.检查各零部件尺寸是否符合要求。
B.组装产品并互换装配,检查产品是否可组装,伸缩部分是否自如、转动部分是否灵活、与其他产品配合是否符合要求。
C.必要时根据产品的特性需要进行承重测试,根据产品功能进行产品的试使用。
D.组装性产品必须按照技术文件和《产品检验规范》的要求并按抽样计划进行组装检验。
5.3.5.包装项目检验:
A.外箱是否良好,捆扎包装是否规范。
B.产品外箱唛头、标签、条码的检验。
C.包装方式和装箱数的检验。
D.对新产品的包装成品进行净、毛重和材积抽验,核对是否与出货资料、唛头标示相符。
E.必要时进行跌落和颠簸实验。
5.3.6.包装成品经检验合格后,包装PQC于“标识卡”上签认后,包装组方能办理《成品入库单》入库。
包装PQC同时将检验结果记录于《成品检验记录表》。
5.3.7.判定为不合格时,包装PQC应进行标识并要求包装人员予以隔离,同时反馈QC组长进行处理,不合格品的处理按《不合格品管理办法》进行。
5.3.8.成品检验发现的质量异常,其处理方式参照《制程检验办法》中5.9的规定进行。
5.4.库存成品检验:
5.4.1.资材仓库仓管员定期对库存成品进行核查,具体按《仓储管理办法》的要求执行。
5.4.2.对于成品库存每超过一个月,需重新启用出货时资材仓库应通知品检人员安排检验。
5.5.出货检验:
5.5.1.检验依据:
品管部应协调确保OQC充分掌握以下检验依据以执行出货检验:
A.《制造命令单》:
品管部资料员应提供《制造命令单》,以作为OQC出货检验依据。
B.客户图纸/客户确认图:
业务部业务部须在出货检验执行前提供客户图纸/客户确认图的最新版本至品管部。
品管部QE应对图纸中英文描述进行中文备注,客户前期沟通中的重要强调信息等备注于图纸上,OQC依照检验。
C.色板及其他必要的限度样:
品检人员提供经客户确认并正式发行的色板;品管部QE(限度样室等)应提供压克力、塑料件等其他经确认的需比对颜色及外观的限度样。
D.客户投诉及品质履历。
品检人员应确保OQC掌握相关客户投诉和品质履历。
E.其他重点品质控制项目:
其他客户原始信息、前期试制工作中的重点内容,品检人员、品管部QE应适时提供给OQC。
5.5.2.出货检验通知及检验时间安排:
A.出货检验通知:
每批产品入库产品达到当柜出货量50%时,资材仓库必须通知OQC执行出货检验。
B.未经过OQC检验的产品禁止装柜出货。
5.5.3.出货检验内容包括:
A.OQC依据《出货明细》的出货数量结合《抽样计划》进行抽检。
B.产品包装检验:
装箱数量,外箱的唛头、标签、条码是否与客户要求一致。
对包装方式的合理性,应作综合评估,对认为不合理的包装方式,应及时向品管部QE提出反馈,由品管部QE进行追踪再作评估及追踪处理。
C.产品外观检验:
表面处理是否与客户的要求一致,产品的整体外观。
D.产品重要尺寸的确认:
依据客户图纸或确认图对产品重要尺寸进行核对确认。
E.有组装配合要求的产品,OQC须依抽样计划进行组装。
5.5.4.检验结果:
A.出货检验合格时OQC在每一个栈板上原物料标识卡上盖QC合格章或签名,以进行标识合格状态。
B.出货检验不合格时标识黄色《不合格品》,注明件号、数量、检验人员和日期等信息。
标识《不合格品》的产品不得装柜。
C.在检验成品不能满足客户要求时,产品不得装柜,OQC作成《成品出货检验报告》并经品管部品管部QE主管签核后反馈给制造部门相应主管,由品管部对不合格品进行追踪处理,接到信息品管部应立即协调相关部门进行处理。
必要时品管部可向业务部提出向客户沟通确认相关事项。
D.对于检验不合格的产品经处理后需再次经OQC检验合格后方可装柜。
5.5.5.出货检验经确认为不合格品时,品管部依《不合格品管理办法》进行处理。
5.5.6.品管部OQC在每批出货成品检验完成后提出《成品出货检验报告》,经品管部主管签核后存档备案。
若有不合格品时可将信息同时传递至相关涉及的部门。
5.5.7.对于严重不良的缺陷必要时用数码相机拍照留底作为改善的依据,在每周的管理例会上报告上一周的出货检验品质的情况。
5.5.8.如客户有提出《成品出货检验报告》的要求时,品管部应及时按要求提供至业务部。
5.5.9.品管部OQC须依据成品出货检验记录、报告整理成周、月的出货成品质量统计分析,经品管部经理核准后抄送涉及部门,作为产品改善的参考依据之一。
5.5.10.成品异常状况的分析与改善措施情况,品管部QE应记入质量履历并作为相关质量会议议题之一。
5.5.11.每批次的抽样数量依MIL-STD-105E一般检验Ⅰ水平,尺寸及组装特性的抽样数量按S-1。
5.6.客户验货
5.6.1.客户验货前业务部业务部应明确客户完整的需求,含客户名称、件号、要求验货数量、验货具体时间、客户要求验货产品的状态、客户来访人员信息及侧重点以及其他强调事项,并提前书面传递品管部、生管部、制造部及必要的配合部门。
5.6.2.业务部应与生管部确认验货的时间,生管部并确保在此确认时间前,可以完整的提供客户要求验货的所有准备工作。
5.6.3.生管部应负责管控要求制造单位在客户来访前完成客户要求状态的所有产品,并协调转运至指定位置。
产品完成的时间,应充分考虑组装、布置等所需的时间。
5.6.4.品管部应准备验货要求的检验资料、检验工具,同时协调资源按客户要求的状态进行组装等准备工作,确保以客人要求的状态准备好客户验货的产品。
生管部门和制造单位应全力配合协调人力、产品准备和场地布置等工作。
5.6.5.品管部(或项目制人员)应全程掌握进度,如所需产品及各种准备条件不能按时间达成要求的,应及时向业务和公司进行反馈,必要时动用公司资源以达成客户需求。
5.6.6.客户要求来厂验货的产品,原则上品管部应确保出货检验已提前完成。
以保证以合格产品提供给客户检验,提高一次交验合格率,维护客户信心。
5.6.7.验货过程由业务部业务部主责陪同,对验货人员提出的疑问负责解答和全程记录,品管部应安排品管部QE参与验货过程,掌握客户验货的质量反馈并作记录。
5.6.8.验货过程制造部负责产品准备、拆箱、包装作业以及协助品管装配。
5.6.9.验货结束后,品管部品管部QE应和业务员共同确认验货结果,并整理验货结果报告通知品管部、生管部及制造部。
验货出现异常的,由品管部追踪责任单位进行不合格品处理,品管部品管部QE应追踪验货异常的处理结果。
OQC再次检验合格的成品方可出货。
5.6.10.客户验货可视同出货检验,但客户验货结果不能免除公司的质量责任。
6.相关文件:
6.1.《抽样计划表》
6.2.《包装作业指导书》
6.3.《不合格品管理办法》
7.使用表单:
7.1.《质量异常通知单》
7.2.《成品出货检验报告》
1.
目的:
为有效控制产品制造过程的质量,确保产品质量满足客户的要求。
2.范围:
所有产品包装前制造过程各个阶段的质量检验。
3.定义:
3.1.自检:
生产过程中作业员按规定的要求对产品进行自主检验。
3.2.巡检:
PQC按规定的要求巡回检验在制的产品。
3.3.首件检验:
PQC对每道工序制作的第一个产品经自检合格后的质量再确认。
3.4.终检:
PQC在零部件或产品完成加工的移转前,按规定要求对其进行的检验。
4.职责:
4.1.品管部:
4.1.1.品管部QE:
A.《产品检验标准》、抽样计划、限度样的建立和提供。
B.质量异常的稽核和提报,提出纠正预防措施,并追踪改善成效。
C.进行统计分析及追踪改善,以及质量记录的整理存档;
D.质量教育需求的提出和进行;
E.检具的设计及测量器具的管理。
4.1.2.品检人员:
A.首件检验、巡检、终检的检验进行。
B.制程检验记录的填写;质量记录整理存档。
C.质量问题的反馈、处理;跟踪纠正预防措施的落实。
D.不合格品的管制、标识。
4.2.制造部各工序:
4.2.1.负责首件品、在制品、成品的自检、互检。
4.2.2.提出制程不合格品的纠正预防措施;
4.2.3.质量异常的处理。
4.3.技术部:
4.3.1.技术文件/图纸的提供。
4.3.2.制作过程的技术辅导。
4.3.3.工艺执行状况的检查。
4.4.各部门:
本部门造成的质量异常的纠正预防措施的提出和执行;其它部门提出的纠正预防措施的执行。
5.作业内容:
5.1.检验依据:
品管部根据制程质量控制需要,在各制造单位设立相应的QC组,执行质量检验。
制程检验依据首件品、限度样、技术文件、抽样计划结合等进行。
5.2.品管部QE须对进行受控管理,对限度样要建立专门的贮存室并形成《限度样一览表》,指定品保员进行管理.
5.3.首件检验:
5.3.1.制程过程中各生产组别应执行首件检验,首件检验的时机包括:
A.制程在每班次生产开始;交接班产品未切换的仍须重新执行首件检验。
B.材料、工序变更;
C.作业员变更;
D.产品更换;
E.换模;异常处理后(如:
模夹具维修、机器维修、质量异常等)等情况。
5.3.2.首件检验应当全面,应当对本加工工序所涉及的品质项目进行全面检验并记录。
5.3.3.首件生产前准备:
生产单位应准备用于生产的技术文件,质量依据文件及必要的外观限度样和量具。
生产单位应当对作业员进行必要的产品培训,以确保作业人员熟悉操作手法,明确品质标准,掌握重点注意事项。
5.3.4.首件生产的自检:
作业员或调模工对首件产品进行自检,首件检验应含产品的加工尺寸和外观、加工方法、工模夹具及所使用物料等方面。
5.3.5.首件检验合格后,PQC在《首件标识卡》合格栏上判定并签名,产品方可开始批量生产。
5.3.6.首件产品确认时,PQC对首件产品确认无把握时,应及时逐级上报解决。
5.4.自检、互检:
5.4.1.作业员在生产过程中应依据首件产品或检验依据文件、限度样对所生产的零件进行自检。
自检发现不合格品时,作业员应立即暂停作业并向组长报告,即时反馈PQC对已制品进行质量确认,由品检人员判定后作业员依要求处理。
生产组长须确保作业员执行一小时一次的自检,防止出现批量不良。
5.4.2.自检发现不合格品时按《不合格品管理办法》处理。
5.5.巡检:
5.5.1.PQC应巡查作业员的作业方法,对标准的掌握、使用容器、工件的摆放及防护是否正确,同时监督作业员自检动作是否执行。
5.5.2.首件合格批量生产时,PQC依据首件品、限度样、技术文件进行巡检,检验内容包括首件检验项目(本工序加工项目)、组合件整体性能检验,同时进行产品试组装、特殊性能测试。
检验结果记录于《制程检验记录表》上。
5.5.3.PQC巡检时发现异常状况时,应立即要求作业员暂停生产,并立即反馈QC组长和制造单位主管,经QC组长判定为不合格品时,要求责任单位进行纠正和纠正措施。
异常排除后,经重新首件检验确认方可继续生产。
5.5.4.巡检发现且判定为不合格品时按《不合格品管理办法》处理。
5.6.移出判定:
5.6.1.制造单位生产的半成品、成品由物料组人员进行标识。
要跨课移转到下一工序时,由物料组通知PQC做移出判定。
5.6.2.品检人员对巡检合格的产品,物料移转时,PQC须判定产品是否合格,《标识卡》上签认,判定为不合格品时,物料不得移转。
5.7.库存物料的检验:
5.7.1.资材课依《仓储管理办法》进行仓库管理,定期对库存物料进行核查。
对于超过保存期限、需移出的物料或呆滞物料的转用等由资材课报品检人员检验。
5.7.2.品检人员依相应的检验标准或规范对物料进行检验,物料经检验合格,由品检人员于相应的标识卡上签认以示负责。
5.7.3.当判定不合格时必须立即通知仓管员进行物料的隔离,并依《不合格品管理办法》相应的处理。
5.8.不合格品的处理:
品检人员执行不合格品的判定。
对于不合格品须挑选、返工、返修的,品管部应明确其标准并追踪至重新判定合格。
具体不合格品的管理依《不合格品管理办法》进行。
5.9.制程质量异常管理:
5.9.1.出现质量异常,PQC应立即通知生产组长停止生产不合格品,并要求采取纠正预防措施。
并对产生的不合格品进行追溯、标识、隔离等措施。
5.9.2.制程出现以下质量异常时,PQC应开具《质量异常通知单》,经品管主管确认后和制造单位主管一起组织进行异常处理。
A、工艺图纸异常;
B、工模夹具异常不能即时现场调整须停产送修;
C、加工时发生连续异常时。
5.9.3.质量异常责任单位应及时回复《质量异常通知单》,品管部应追踪纠正预防措施的完整落实。
包括追踪重新首件检验合格、不合格品处理完成,模夹具的改善、技术资料和、限度样的标准化。
5.10.品管部QE依据制程检验的各类检验记录表整理成周、月的制程质量统计分析,经品管部经理核准后分发制造部、管理部、技术部,作为制程质量改善的参考依据。
5.11.制程异常状况的分析与改善措施情况,品管部QE应记入质量履历。
5.12.其他单位对于品检人员的判定存在争议时,品管部经理应主导在满足客户要求的前提下会同相关部门评估解决。
品管部对质量判定结果进行最终裁决。
特殊情况,总经理可从经营的角度对成品是否放行进行决定。
6.相关文件:
6.1.《不合格品管理办法》
6.2.《纠正和预防管理办法》
6.3.《抽样计划表》
7.使用表单:
7.1.《首件标识卡》
《质量异常通知单》