中小企业ERP基本原理及系统架构.docx
《中小企业ERP基本原理及系统架构.docx》由会员分享,可在线阅读,更多相关《中小企业ERP基本原理及系统架构.docx(62页珍藏版)》请在冰豆网上搜索。
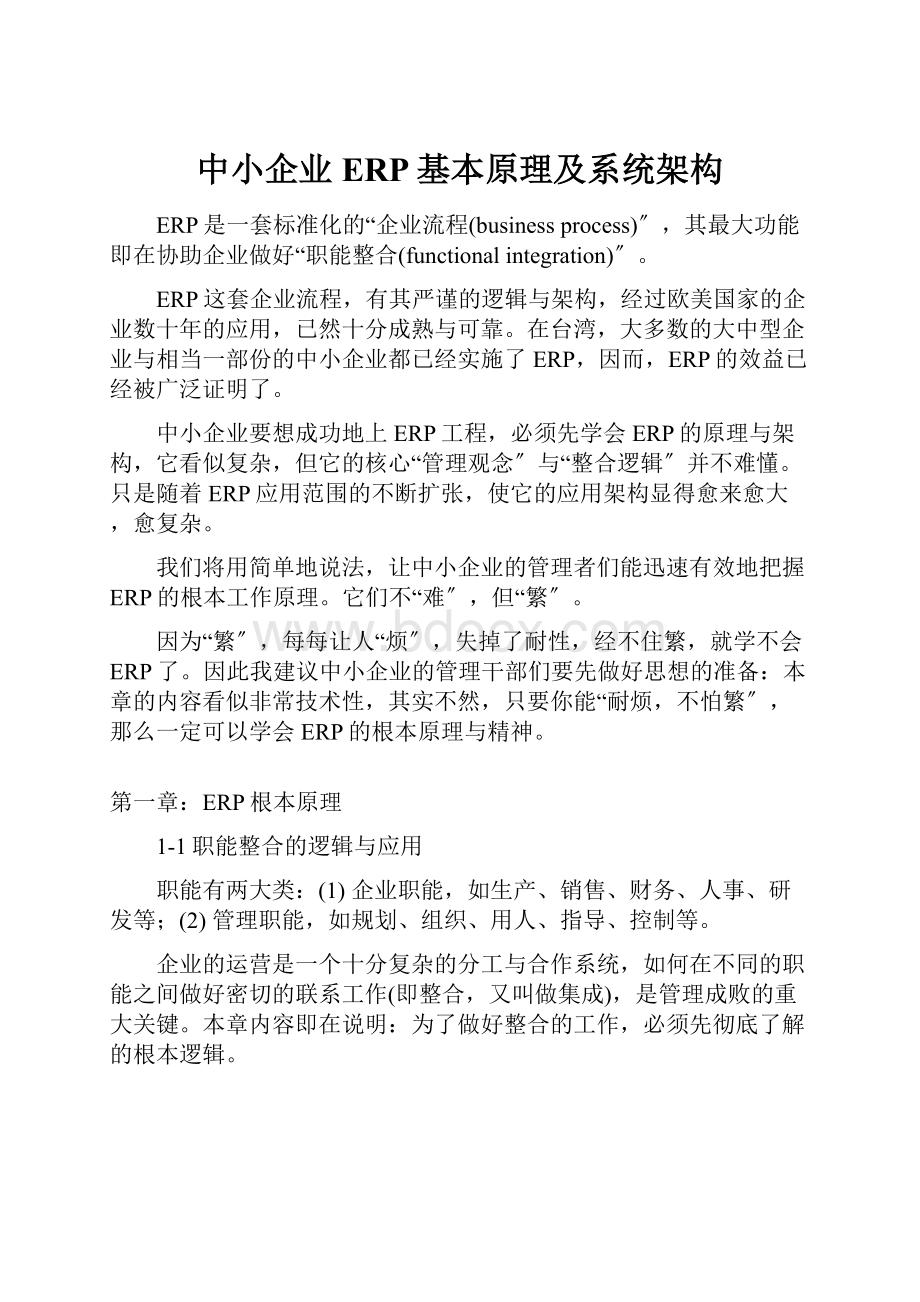
中小企业ERP基本原理及系统架构
ERP是一套标准化的“企业流程(businessprocess)〞,其最大功能即在协助企业做好“职能整合(functionalintegration)〞。
ERP这套企业流程,有其严谨的逻辑与架构,经过欧美国家的企业数十年的应用,已然十分成熟与可靠。
在台湾,大多数的大中型企业与相当一部份的中小企业都已经实施了ERP,因而,ERP的效益已经被广泛证明了。
中小企业要想成功地上ERP工程,必须先学会ERP的原理与架构,它看似复杂,但它的核心“管理观念〞与“整合逻辑〞并不难懂。
只是随着ERP应用范围的不断扩张,使它的应用架构显得愈来愈大,愈复杂。
我们将用简单地说法,让中小企业的管理者们能迅速有效地把握ERP的根本工作原理。
它们不“难〞,但“繁〞。
因为“繁〞,每每让人“烦〞,失掉了耐性,经不住繁,就学不会ERP了。
因此我建议中小企业的管理干部们要先做好思想的准备:
本章的内容看似非常技术性,其实不然,只要你能“耐烦,不怕繁〞,那么一定可以学会ERP的根本原理与精神。
第一章:
ERP根本原理
1-1职能整合的逻辑与应用
职能有两大类:
(1)企业职能,如生产、销售、财务、人事、研发等;
(2)管理职能,如规划、组织、用人、指导、控制等。
企业的运营是一个十分复杂的分工与合作系统,如何在不同的职能之间做好密切的联系工作(即整合,又叫做集成),是管理成败的重大关键。
本章内容即在说明:
为了做好整合的工作,必须先彻底了解的根本逻辑。
根本整合用名词的介绍
本节要说明一些在人工操作下没有,但在进行“职能整合〞时又非用不可的名词。
换言之,要了解整合的逻辑,就必须先彻底弄清楚这些名词的真正含义与功能。
所谓整合,是有效地处理「连动的关系」。
连动关系的内容有两个:
一个是「数量」的连动关系,另一个那么是「时间」的连动关系。
ERP中处理数量连动的逻辑是靠三个数量来做到的,这三个数量分别是在手量、在单量、预约量。
一般在商业里说的“进销存〞,或制造业里说的“产供销〞,都要靠这三个数量来做职能间的整合。
因此,这三个数量可以说是ERP根本逻辑的基石。
(1)在单量(OnOrderQuantity)
当某电器经销商(代号为甲)针对某一产品(例如某型号的电视机而其代号为A)发出了一张采购单(P/O#123)要买500台时,我们就说电视机A的“在单量〞为500台。
在单量代表“已方案好了要有,但目前尚未真正拥有的〞数量,可将它的含义想成是一个“在单据上的〞数量。
在管理上,在单量也代表一种“已经承诺了〞的数量。
上述A的在单量为500台,表示我们已经对供货商发出了采购单,即已经承诺了要买500台。
(2)在手量(OnHandQuantity)
如果供货商交来电视机A共300台,此时成品仓库内办理验收而多了300台,我们称此300台为“在手量〞。
在手量代表一个已经拥有(实现)的数量。
此时,原先电视机A的在单500台应该变成500台-300台=200台,因为未实现(即未验收)的数量只剩下200台,而非原先的500台。
(3)预约量(AllocatedQuantity)
如果某客户向经销商甲订货80台,预定一周后交货。
此时我们称电视机A的预约量为80台,表示在手量300台中已经接到客户订单的“预约〞数量为80台。
当然,成品仓库内还没有出货,在手量仍然是300台,而“预约量〞是代表一种未来将会发生的出货需求。
为什么接到客户的订单时要对成品库存量做预约呢?
因为预约量代表一种“预留〞或“待发〞的数量,可以让我们预先估算在手量是否会缺乏,而对可能发生的缺货状况预先做准备。
依据以上这三种数量,ERP衍生出其它两个有用的数量,如下述。
(4)在手可用量(OnHandAvailableQuantity)
电视机A的在手量为300台,预约量为80台,我们称300台-80台=220台为“在手可用量〞。
换言之,在我们手上而“可〞以供新的订单来“用〞的数量有220台。
销售人员看到在手可用量,就知道他“能再接单而可立即出货〞的数量。
(5)可用量(AvailableQuantity)
对销售人员而言,公司到目前为止总共还可再接多少台电视机A的订单呢?
答案是420台,即在手可用量220台与在单量200台的合计。
因此:
在手可用量=在手量-预约量
可用量=在手可用量+在单量
=〔在手量-预约量〕+在单量
手工作业下,我们的数据只有在手量〔即库存量或称在库量等〕,库存数据并未登录在单量与预约量,也未计算出可用量。
因此,无法提供管理者要应用的信息。
例如,目前库存里有多少台电视机A?
答:
300台。
够用吗?
会缺货吗?
有多少台可以紧急调拨给同行或应付紧急性的客户订单?
在手工作业下我们很难立即获得完整而且正确的答案。
如果自“供需〞的观点来思考,那么在单量代表「供给」,而预约量代表「需求」。
供需之间是否平衡,有两个检查的方式:
目前是否平衡?
眼前的供给是在手量,需求量是预约量,假设在手可用量大于零,那么代表目前手上可立即供给的数量足以应付需求。
未来是否平衡?
总共的供给是可用量,假设可用量大于预约量那么代表供给不缺。
当然“不缺〞还不够,我们还要力求“不多〞。
因为多出来的数量可能代表呆滞品,会积压资金。
数量负责单位性质
在单量———→采购单位————→供给
在手量———→库存单位————→现况
预约量———→销售单位————→需求
可用量———→〔计算〕————→方案
〔图1整合用名词例示──采购件〕
图1列出上述各项整合用的名词,请思考各名词的负责单位。
在图1中是以采购件来举例的,如果换成一个自制的半成品,各负责单位就应该对应的改变了。
请参阅本章第三节「根本整合用名词与连动关系的演变」中的说明。
1-2连动关系的处理
前面说过,整合在处理连动的关系,而连动关系的内容有两个:
数量与时间。
(1)数量连动
了解上述整合用的名词后,可用下面的例子来说明连动关系(整合关系)的处理方式。
例:
某公司对其产品甲有以下一连串的活动
1.在1月10日发出采购单(P/O)编号112,要进货500台。
2.供给厂商于1月15日交来第一批货300台,仓库当天予以验收入库。
3.1月18日销售部门接到客户订单(C/0)编号123,数量100台。
4.1月19日销售部门接到客户订单(C/0)编号124,数量50台。
5.1月20日出货(C/0)编号124,数量50台。
6.1月22日接到某客户大订单(C/O)编号125,数量300台。
那么产品甲库存数据逐日变动的状况如表所示。
01/10
01/15
01/18
01/19
01/20
01/22
产品甲
的库存
资料
采购
#112
500台
验收
#112
300台
接单
#123
100台
接单
#124
50台
出货
#124
50台
接单
#125
300台
A
在单量
500
200
200
200
200
200
B
在手量
0
300
300
300
250
250
C
预约量
0
0
100
150
100
400
01/10
01/15
01/18
01/19
01/20
D
在手
可用量
0
300
200
150
150
-150
E
可用量
500
500
400
350
350
50
〔注:
计算公式:
D=B-C,E=A+D〕
〔表1:
数量连动的举例〕
1月22日时,公司自数据上可知:
在手可用量为-150台,即手上所有的数量缺乏以应付订单C/O#125的需要。
但这是否表示公司无法准时交货给客户了呢?
不一定。
由于可用量是正值50,因此我们知道总供给量是足够的。
问题在:
在单量200台交货时间和订单出货时间的比拟。
因此,在「数量」连动关系的处理之外,我们还必须再考虑「时间」连动关系的处理。
(2)时间连动
状况:
C/O#123,数量100台,将于1月25日交货。
P/O#112,余量200台,将于1月23日入库。
C/O#125,数量300台,将于1月24日交货。
那么产品甲库存数据逐日变动的状况应如表2所示:
产品甲
1月22日
1月23日
1月24日
1月25日
在单量
200
0
0
0
在手量
250
450
150
50
预约量
400
400
100
0
可用量
50
50
50
50
〔表2时间连动的举例〕
我们发现:
供给状况完全可以满足订单所需,因为可用量一直是正值,即在手量一直是正值。
反之,假设P/O#112余量200台的交货入库时间改为1月25日,那么1月24日的在手量为250台,预约量为300台,可用量将成为-50台,表示将无法如C/O#125之要求交货给客户。
承办人假设不能延期交货(例如客户不容许),采购单位就必须催促供货商把P/O#112之交货时间提前。
1-3连动关系的应用:
自动规划
了解ERP中整合的逻辑,以及连动关系的处理方法后,我们可以进一步理解为什么ERP能够替我们做自动的规划,并告诉我们应如何最好地做好供给工作:
刚好足够的数量,在及时的时间,供给业务所需。
例:
销售部门接到客户订单#126,数量150台,预定2月5日交货,又预期于2月10日会另接到订单,数量有200台,而3月份方案再卖出400台,应如何来备货(采购)?
1月25日
2月5日
2月10日
3月
在单量
0
0
0
0
在手量
50
50
0
0
预约量
0
150
200
400
可用量
50
-100
-200
-400
〔表3.自动规划的举例〕
经过表3中的演算过程,我们知道2月5日以前必须进货100台,2月10日前须进货200台,而3月需再进货400台。
如果供货商所容许的交货提前期为10天,那么我们的备货方案应该是:
1月26日发出P/O,数量100台,2月5日交货;
1月31日发出P/O,数量200台,2月10日交货。
另外,因3月份的方案销售量400台未指定日期,此时我们还无法计算出详细的采购方案,应将此400台需求先做「需求均化(demandsmoothing)」作业后,再细化计算采购方案。
需求均化是“将需求依时间单位平均化〞的意思,如将3月份的方案销售量400台依「周」作均化,视一个月有四周,那么3月份每周的需求量为100台,并称此作业为「均化到周」;同理,如果「均化到日」而3月份有25个工作天,那么可计算出每日的需求量为16台。
为什么要作需求均化呢?
是为了要把采购的批量(lotsize)减小,如将每个月交货一次的作业改为每周交货一次,以减少库存的积压。
当然,对制造或委外工作的规划,也同样可以先作需求均化,以减小批量、缩短工作的周期时间(cycletime)、降低库存的积压。
又,所谓预期在2月10日会另外接到订单200台,这是一种「销售预测」的行为,此时这200台还不是客户订单(C/O)量,因此在库存管理的实务上,并不将此200台列出为预约量,上表的内容只是为了要说明需求「净算(netting)」的逻辑,请读者们不要误会,以为对销售预测值也要做预约工作。
根本整合用名词与连动关系的演变
上述的说明是针对一个成品(电视机)来举例,而且该成品是采购来的。
如果该成品是企业自己生产的,或是针对某一项生产要用的零件而言,上述整合用名词的定义和用法还一样吗?
现将各情况下的定义列出在下面:
A.针对生产要用的采购料件而言,各名词的定义为
(1)在手量:
现有该采购件的库存量。
(2)在单量:
已下采购单而供给厂商尚未交货的数量(应交而未交,或尚未到期故未交货的数量)。
(3)预约量:
已发制令,要领用,而车间尚未领料的数量。
可用量:
可供新的制令来使用的数量。
可用量=在单量+在手量-预约量-平安存量。
在手可用量:
在手量中可供新的制令使用的数量。
在手可用量=在手量-预约量-平安存量。
B.针对自行生产的成品而言,各名词的定义为
(1)在手量:
现有该成品的库存量。
(2)在单量:
已下制令而制造车间尚未完工缴库的数量。
(3)预约量:
已接到客户订单但尚未出货的数量。
C.针对生产用的半成品而言,各名词的定义为
(1)在手量:
现有该半成品的库存量。
(2)在单量:
已下制令而制造车间尚未完工缴库的数量。
(3)预约量:
已发制令,要领用,而车间尚未领料的数量。
您也许已注意到了:
不管定义如何变化,「在单量」总是代表一个成品、半成品、零件的「供给数量」;而「预约量」总是代表着它的「需求数量」,记住这个根本的原那么,就很容易掌握各个名词在不同场合下所代表的真正意义了。
应用整合逻辑的前提
在前面的说明里,我们了解:
在单量代表“供给〞,预约量代表“需求〞,而在手量那么是供需平衡后的“现况〞;经过计算得到的可用量那么是方案作业的主要依据。
借助这样一套整合的逻辑,可以将销售、供给、生产三方面的职能密切地结合在一起,一方面协助我们做好执行和控制的工作,同时也可利用其自动规划的功能协助我们做好规划的工作。
当然,这样一套整合逻辑要使用大量的数据,更需要有快速的运算工具,因此,它是必须使用电脑来处理的一套作业与管理方法,同时对企业的数据管理(datamanagement)也有着相当的要求。
如果用户的数据不全、数据的精确度不够,或是数据的及时性很差,那么这套整合逻辑的成效就要大打折扣了,在讨论整合逻辑进一步的应用前,特别先提出来请读者们注意。
1-4
MRP/DRP/ERP的产生
现代的分销业(或称为商业)可以利用上述的“自动规划的逻辑〞,由电脑自动做出采购方案,这就是西方先进企业常用的「配销需求规划系统」,英文是DistributionRequirementPlanning,简称作DRP系统。
制造业计算采购需求的工作就更复杂了,因为它卖出的产品不是直接买来的,必须买材料来进一步制造。
一个产品往往要用到许多件的材料,而其中有相当的比率(如超过50%)是共用性的材料,故上述这种自动规划的逻辑还不够用,必须再加以扩充,而形成了「材料需求规划」系统,英文是ManufacturingRequirementPlanning,简称作MRP系统。
西方制造业在大量应用MRP(材料需求规划系统)而取得管理效益后,又试着把“产能面〞的需求计算也纳入系统之中,因而产生了「产能需求规划系统(CRP:
CapacityRequirementPlanning)」,并逐渐把车间的「车间控制(SFC:
ShopFloorControl)」、销售单位的DRP功能、应收帐款和应付帐款的管理、会计总帐自动更新….等功能都加以集合,形成了管理整个制造企业资源的管理系统,因而称作「制造资源规划(ManufacturingResourcePlanning)」系统,其英文简称也是MRP。
因此,MRP系统有了狭义与广义之分,狭义的MRP系统是指「物料需求规划系统」;广义的MRP那么是指「制造资源规划系统」。
由于二者的英文缩写都是MRP,通常为了防止混淆而称前者为MRP,称后者为MRPⅡ。
近年来随着信息科技(IT:
InformationTechnology)的迅速开展,企业对IT的应用也逐步增加。
借助IT中C/S(Client/Server)的技术,企业可以将分散在各地机构的信息处理,用网络联系起来,而形成一个协调而统一的信息处理系统。
MRPⅡ对“数量与时间〞的整合功能,因为C/S技术而得以进一步扩增了对“空间〞的整合,并有了新的名称叫「企业资源规划系统(ERP:
EnterpriseResourcesPlanning)系统」。
其实,DRP、MRP、MRPⅡ、ERP.…不管是哪个P,其根本精神都是“整合、整合、再整合〞。
第二章:
制造企业ERP的BOM
对商业企业来说,我们上一章中所介绍的整合逻辑已能满足许多中小企业上ERP工程的大部份需求。
但对制造企业或系统集成商来说,仅靠整合逻辑的功能是不够的,还必须知道用料结构(BOM)与需求规划(MRP)的功能。
商业企业假设要由销售方案来自动计算采购方案,也需要应用MRP的功能。
因而,我们在本章中介绍BOM,而在下一章说明MRP。
2-1用料结构表的定义
假设有一个产品甲是经过以下的生产活动制造出来的:
(1)将2个原料b1和3个零件b2以制程1做成一个半成品B,
(2)将1个原料c1和2个零件c2以制程2做成一个半成品C,(3)将2个半成品B、1个半成品C、以及2个包装料a以制程3做成一个成品甲。
那么,我们可以用以下的图标法来表达甲的用料关系,其中括号内的数字是代表所用的数量:
阶码(LevelCode)
甲-------------0
a
(2)B
(2)C
(1)-------------1
b1b2c1c2-------------2
(2)(3)
(1)
(2)
这样的一个结构关系称作「用料结构(BillOfMaterial)」,一般均简称作BOM,中文也可称作「零件构成表」或「产品结构表」。
上例中的BOM不只有一个阶层,因此我们称它为多阶层的BOM。
阶层(level)的指定在惯例上是由上而下,从0开始计算的,在第二局部第3章中我们会再详细地说明。
我们把各料件间的附属关系定义为母子关系(也有人称之为父子关系)。
例如甲为母件,而a、B、C即为甲的子件。
又如假设B为母件,那么b1、b2就是B的子件。
2-2料品供给类型
采购来的原料或零件,一定是子件,它们不可能是母件。
自制或委外加工的产成品(半成品或成品)那么一定是其制造所需料件的母件。
假设以供给的类型来区分,我们可以将工厂所有的料件(Item)区分为三大类:
[1]自制件(ManufacturedItem),或简称作M/O件(M/O是制令的代称);
[2]委外件(SubcontractedItem),或简称作S/O件(S/O是委外加工单的代称);
[3]采购件(PurchasedItem),或简称作P/O件(P/O是采购单的代称)。
这三种料件,今后统称作「料品」,它泛指原料(rawmaterial)、零件(component)、半成品(semi-finishedgood)或是成品(finishedgood),换言之,即「料」及「品」的统称。
2-3手工作业无法准确计算采购量
在手工作业下,也有一个类似BOM的概念,叫做「标准用量表」,「零件构成表」,或称作「用料清单」,它的形态如表1所示。
XYZ
用料标准
毛需求量
库存量
净需求量
产品甲
1
100
0
100
包装料a
原料b1
零件b2
原料c1
原料c2
2
4
6
1
2
200
400
600
100
200
100
200
300
200
100
100
200
300
100
(用料清单)〔采购需求计算过程〕
〔表1手工作业下计算净需求量的方法〕
甲产品如果接到客户订单共计100个,那么各料件的「毛需求量(GrossRequirement,简称GR)」如X栏内数字所示。
计算采购需求的人员会找出各料件的库存量,如Y栏内数字所示,然后计算X-Y=Z,就得到Z栏内的数字,为应采购的数量,称作「净需求量(NetRequirement,简称NR)」。
我们要问:
这样的计算过程正确吗?
由下面的说明可以知道这种计算过程是错误的:
[1]所谓「库存量」到底是什么量?
是在手量?
在手可用量?
还是可用量?
由第二局部第1章中的说明,可以看出这里的库存量应该是可用量,但手工作业时往往没有可用量的数据,使采购人员不敢轻易扣除他所看到、当时的库存帐数据,因其中有许多是制造车间应领而尚未领的数量。
这是手工作业下无法准确计算净需求量的重大原因之一。
[2]半成品B与C有库存吗?
许多企业受制于工程技术水平及管理观念的误导,很少以批对批法〔Lot-For-Lot〕来生产,而往往有半成品库存的留置。
假设B有库存50个,那么上述的计算过程就完全错了。
如何计算才对呢?
请看下节的说明。
2-4BOM逐层式的展开
依照下表所示的计算步序,由上而下逐层地计算。
步序
料品
毛需求量
X
库存量
Y
净需求量
Z=X-Y
读BOM带出各
子件毛需求量
1
甲
100
0
100
a
B
C
200
200
100
2-1
2-2
2-3
a
B
C
200
200
100
100
50
0
100
150
100
b1
b2
c1
c2
300
450
100
200
3-1
3-2
3-3
3-4
b1
b2
c1
c2
300
450
100
200
200
300
200
100
100
150
100
〔表2BOM展开〕
将表1与表2相比拟可发现:
b1及b2原先在手工作业下计算出的采购量太多了,c1及c2那么未多采购,如表3所示。
原计算之采购量
BOM展开之采购量
多采购之数量
b1
200
100
100
b2
300
150
150
c1
0
c2
100
100
0
〔表3BOM展开与手工计算净需求量的比拟〕
原因是:
半成品B有库存而C没有。
b1及b2多采购的数量刚好是B已在手上的库存量。
50个B刚好等于100个b1再加上150个b2,此即多采购的数量。
由这些说明,得到如下的结论:
[1]手工作业下,库存量的数据往往只有在手量,而无预约量和可用量,这就造成了计算采购、委外、自制数量的重大困扰。
因此,手工作业下的计算只是“近似值〞而非“精确值〞。
负责计算的人员往往宁可多买、多做,而绝不会少算、少买、少做。
这是造成呆滞库存量的重大原因之一。
[2]BOM的展开(explosion)是一个优良的计算工具,在有半成品库存的情况下,仍可正确地计算出应该生产、委外和采购的数量。
虽然其计算比拟繁杂,但我们可把它完全交给电脑来执行,不必由人员来费心。
[3]用BOM展开来计算是否就一定正确呢?
不然,当有某些料品是共用件(commonparts),即供给数个母件生产之用时,BOM的展开方式会有重大的错误,必须改以MRP的方式来计算,我们在下一章中会做详细地说明。
2-5独立需求与相依需求
在上例中,甲是成品,即卖给客户的产品,它的需求量是由客户(市场)来决定的,公司本身只能预测,而不能自行决定,因此称作「独立需求(IndependentRequirement)」。
独立,就是不相关的意思,它强调了公司对此需求在某种程度上的“不可控制性〞。
反之,当甲的数量决定后(如客户订单量为100个),其下的各项料品需求数量依BOM的内容均可一一详细计算出来。
换言之,B、C、a、b1、b2、c1、c2之数量均是由甲的数量来决定的,因而这些需求被称作「相依需求(DependentRequirement)」。
指出料品不同的需求特性,是美国奥立奇(JosephOrlicky)教授的重大奉献。
为什么重要呢?
因为它提供了一个“以简驭繁〞的观念和工具。
如果客户不再订购甲产品,那么所有甲的子件中,凡有平安存量的都已成