完整版150T转炉毕业课程设计说明书.docx
《完整版150T转炉毕业课程设计说明书.docx》由会员分享,可在线阅读,更多相关《完整版150T转炉毕业课程设计说明书.docx(32页珍藏版)》请在冰豆网上搜索。
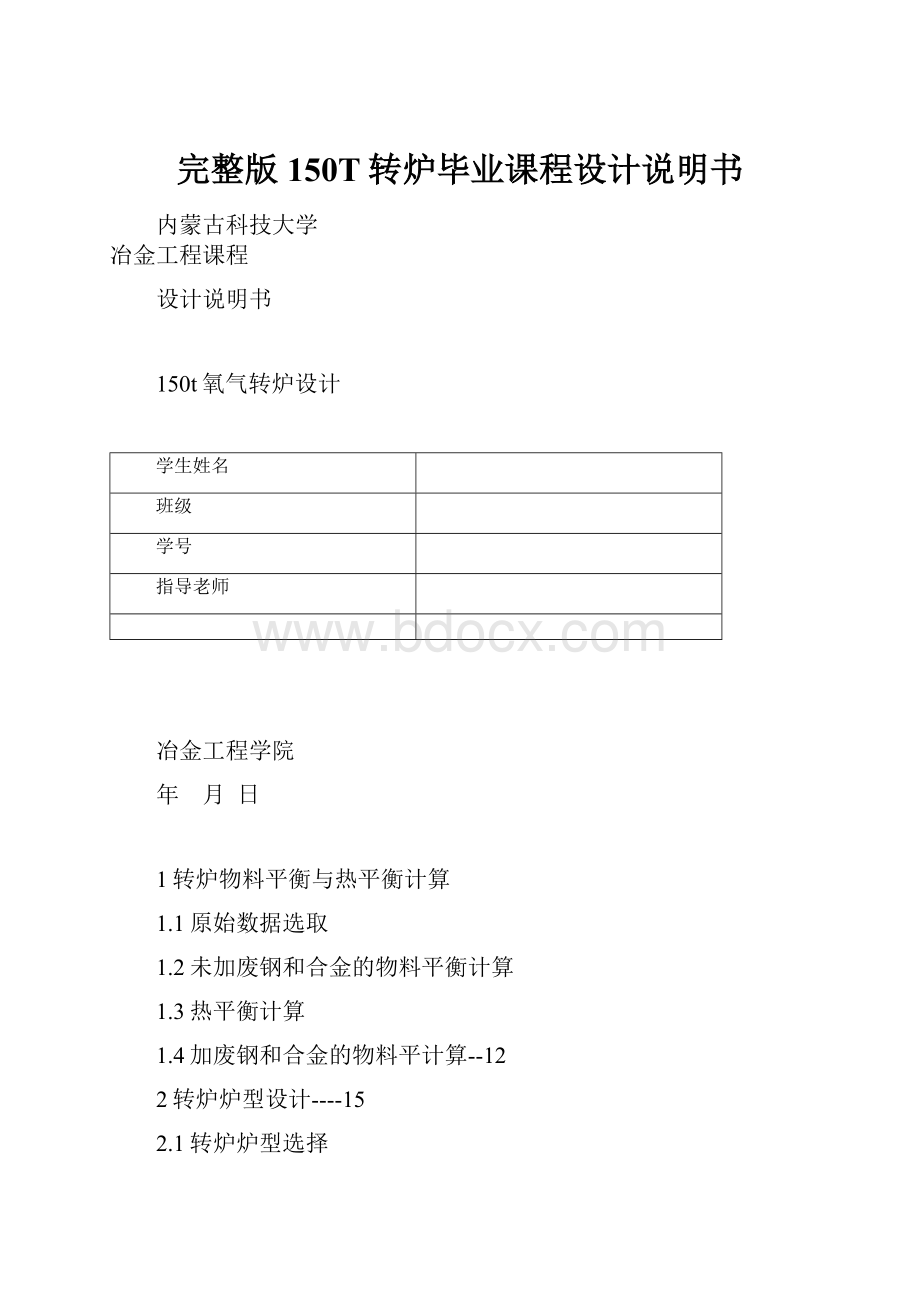
完整版150T转炉毕业课程设计说明书
内蒙古科技大学
冶金工程课程
设计说明书
150t氧气转炉设计
学生姓名
班级
学号
指导老师
冶金工程学院
年月日
1转炉物料平衡与热平衡计算
1.1原始数据选取
1.2未加废钢和合金的物料平衡计算
1.3热平衡计算
1.4加废钢和合金的物料平计算--12
2转炉炉型设计----15
2.1转炉炉型选择
2.2转炉炉容比与高宽比5
2.3转炉主要尺寸确定--15
2.4转炉炉体结构图
参考文献-21
转炉物料平衡与热平衡计算
物料平衡是计算转炉炼钢过程中加入炉内与参与炼钢的全部物料(如铁水、废钢、氧气、冷却剂、渣料、合金添加剂、被侵蚀的炉衬等)和炼钢过程的产物(如钢水、炉渣、炉气、烟尘等)之间的平衡关系。
热平衡是计算转炉炼钢过程的热量收入(如铁水物理热、化学热)和热量支出(如钢水、炉渣、炉气的物理热、冷却剂溶化和分解热)之间的平衡关系。
下面我以Q235钢为例,其规格成分为(%):
C0.14~0.22,Si0.12~0.30,Mn0.40~0.65,P≤0.045,S≤0.050
1.1原始数据的选取
1.1.1原材料成分(表1-1~表1-5)
表1-1铁水、废钢成分(%)
成分含量
C
Si
Mn
P
S
钢种Q235设定值
0.17
0.22
0.40
P≤0.045,
S≤0.050
铁水
3.92
0.6
0.4
0.075
0.04
废钢
0.18
0.22
0.50
0.030
0.030
终点钢水
0.10
痕迹
0.12
0.0075
0.024
注:
《C》和《Si》按实际上生产选取;《Mn》《P》《S》分别按铁水中相应成分的30%,10%,60%留在钢水中设定
表1-2渣料和炉衬(原材料)材料成分(%)
种类
CaO
SiO2
MgO
Al2O3
S
P
CaF2
FeO
Fe2O3
烧减
H2O
C
石灰
90
2.3
1.6
1.24
0.08
4.78
矿石
1.0
5.0
0.47
1.0
0.03
28.5
63.7
0.3
萤石
5.49
0.63
3.54
0.04
0.58
87.3
2.42
白云石
53.1
0.45
28.6
2.05
0.01
0.12
15.67
炉衬
1.40
2.00
78.80
0.50
0.50
1.8
15
表1-3铁合金成分(分子)及其回收率(分母)
项目
C
Si
Mn
Al
P
S
Fe
硅铁
---
73.0075
0.5080
2.500
0.05100
0.03100
23.92100
锰铁
6.6090
0.5075
67.880
---
0.23100
0.13100
24.74100
1--4假设条件(工艺参数设定值)
名称
参数
名称
参数
终渣碱度
萤石加入量
白云石加入量
喷溅铁损
炉衬蚀损量
矿石加入量
炉气中自由氧含量
气化去硫量
金属中《C》氧化产物
%CaO%SiO2=3.8
为铁水量的0.25%
为铁水量的2.5%
铁水量的1%
铁水的0.3%,炉龄>2000
铁水量的0.5%
0.5%(体积比)
占总的三分之一
90%氧化为CO,10%氧化为CO2
渣中铁损
烟尘量
氧气纯度
废钢量
终渣∑w(FeO)按w(Fe2O3)=1.35w(FeO)折算
为渣量的6%
为铁水量的1.5%。
其中(FeO75%,Fe2O320%)
99.6%,N2为0.4%
又热平衡计算确定,结果为铁水量的13.35%,即废钢比为11.78%
15%,而。
。
。
。
。
。
。
。
。
1.2冶炼钢种及规格成分
要求冶炼低碳钢,以Q235钢为例,其规格成分为(%):
C0.14~0.22,Si0.12~0.30,Mn0.40~0.65,P≤0.045,S≤0.050
1.2未加废钢和合金的物料平衡计算
物料平衡基本项目:
(1)收入项:
铁水、废钢、溶剂(石灰、萤石、白云石)、氧气、炉衬蚀损、铁合金。
(2)支出项:
钢水、炉渣、烟尘、渣中铁珠、炉气、喷溅。
1.2.1渣量及其成分计算
根据铁水、渣料质量及其冶炼钢种的要求,采用单渣法操作。
为了简化运算,以100kg铁水为计算基础。
(1)铁水中元素氧化量(表1-6)
氧化量=元素在铁水中的含量–元素在钢水中的含量
表1-6铁水中的元素氧化量
元素%
项目
C
Si
Mn
P
S
铁水
3.92
0.6
0.4
0.075
0.04
钢水
0.14
0
0.136
0.0075
0.0256
氧化量
3.78
0.6
0.264
0.0675
0.0144
由表1-6知:
脱磷率=0.06750.075×100%=90%;
脱硫率=0.01440.04×100%=36%;
钢中残锰量=0.1360.4×100%=34%.
(2)各元素耗氧量及氧化产物量(表1-7)
表1-7铁水中元素氧化量、氧化产物量
元素
反应
元素氧化量
kg
耗氧量kg
产物量kg
C
[C]+12O2=CO
3.78×90%=3.402
3.402×1612=4.536
3.402×2812=7.938
C
[C]+O2=CO2
3.78×10%=0.378
0.378×3212=1.008
0.378×4412=1.386
Si
[Si]+O2=SiO2
0.6
0.6×3228=0.686
0.6×6028=1.286
Mn
[Mn]+12O2=MnO
0.264
0.264×1655=0.0768
0.264×7155=0.341
P
2[P]+52O2=P2O5
0.0675
0.0675×8062=0.087
0.0675×14262=0.154
S
[S]+O2=SO2
0.0144×13=0.0043
0.0043×3232=0.0043
0.0043×6432=0.0086
S
[S]+(CaO)=(CaS)+[O]
0.0144×23=0.0096
0.0096×(-1632)=-0.0048
(2)
0.0096×7232=0.0216
Fe
[Fe]+12O2=FeO
0.701×5672=0.545
0.701×1672=0.156
0.701
Fe
[Fe]+32O2=Fe2O3
0.186×11216=1.302
0.186×48160=0.056
0.186
总计
6.572
6.605
注意*:
1.假定炉内气化脱硫13;铁的氧化由表1-13得出。
(2).由CaO还原出的氧量;消耗的CaO量=0.0096×5632=0.0168kg
(3)渣料的加入量
1)萤石加入量:
在本设计中,取萤石加入量为:
100×0.25%=0.25kg,其成分质量计算见表1-9.(质量计算中各成分质量百分数见表1-2)
表1-9萤石加入量及成分
成分
质量kg
成分
质量kg
CaF2
0.25×87.3%=0.218
MgO
0.25×0.63%=0.002
SiO2
0.25×5.49%=0.014
0.25×0.58%=0.001
Al2O3
0.25×3.54%=0.009
S
0.25×0.04%≈0.000(忽略)
H2O
0.25×2.42%=0.011
其中:
2[P]+52O2=P2O5
(P2O5)生成量=0.001×14262=0.002kg
3)白云石加入量:
为了提高转炉寿命,采用白云石造渣,根据已投产转炉的经验,在本设计中为:
100×2.5%=2.5kg,其成分质量计算见表1-10。
(质量计算中各成分质量百分数见表1-2)
表1-10生白云石加入量及成分
成分
质量kg
成分
质量kg
CaO
2.5×53.1%=1.328
MgO
2.5×28.6%=0.715
SiO2
2.5×0.45%=0.011
烧减
2.5×15.67%=0.392
Al2O3
2.5×2.05%=0.051
P
2.5×0.12%=0.003
S
2.5×0.01%=≈0.000(忽略)
其中:
烧减是白云石中分解产生的气体。
4)炉衬侵蚀量:
转炉炉衬在炉渣作用下,将被侵蚀和冲刷进入渣中,本设计中取铁水量的0.3%,即100×0.3%=0.3kg,其成分质量计算见表1-11.(质量计算中各成分质量百分数见表1-2)
表1-11炉衬侵蚀量及成分
成分
质量kg
成分
质量kg
CaO
0.3×1.4%=0.0042
SiO2
0.3×2.0%=0.006
MgO
0.3×78.8%=0.2364
C
0.3×15%=0.045
Al2O3
0.3×0.5%=0.002
Fe2O3
0.3×0.5%=0.002
其中:
炉衬中碳的氧化与金属中氧化生成的CO和CO2比例相同。
即:
[C]+12O2=CO:
氧化产物CO量为:
0.045×90%×2812=0.0945kg
耗氧量为:
0.045×90%×1612=0.054kg
[C]+O2=CO2:
氧化产物CO2量为:
0.045×10%×4412=0.0165kg
耗氧量为:
0.0165×3244=0.012kg
共消耗氧量=0.054+0.012=0.066kg
矿石侵蚀量及成分
成分
质量kg
成分
质量kg
CaO
0.5×1.0%=0.005
SiO2
0.5×5.0%=0.025
MgO
0.5×0.47%=0.002
S
0.03×15%=0.005
Al2O3
0.5×1.0%=0.005
Fe2O3
0.5×63.7%=0.319
FeO
0.5×28.5=0.143
H2O
0.5×0.3=0.002
5)石灰加入量:
根据铁水成分,取终渣碱度R=3.8,石灰加入量计算如下:
∑(SiO2)=铁水[Si]生成(SiO2)+炉衬、白云石、萤石、矿石带入的(SiO2)
=1.286+0.006+0.011+0.014+0.025=1.342kg
∑(CaO)=白云石、炉衬、矿石带入(CaO)—铁水、矿石中S消耗CaO量
=1.328+0.0042+0.005—0.0168-0.005×5632=1.312kg
石灰加入量={∑w(SiO2)×R-∑w(CaO)}wCaO有效×100%
=(1.342×3.8–1.312)(90%–3.8×2.3%)×100%=4.66kg
注意:
wCaO有效=w(CaO石灰)-R×w(SiO2石灰)
其成分质量计算见表1-12.(质量计算中各成分质量百分数见表1-2)
表1-12石灰加入量及成分
成分
质量kg
成分
质量kg
CaO
4.66×90%=4.194
SiO2
4.66×2.3%=0.107
MgO
4.66×1.6%=0.075
S
4.66×0.08%=0.0037
Al2O3
4.66×1.24%=0.058
烧减
4.66×4.78%=0.223
其中:
[S]+(CaO)=(CaS)+[O]
生成的(CaS)=0.0037×7232=0.008kg
6)渣中的铁氧化物:
对于冶炼Q235钢,根据已投产转炉渣中含∑(FeO)量,取(FeO)=8.25%,(Fe2O3)=5%。
7)终渣总量及成分:
根据表1-7~表1-12中的数据,确定终渣总量及成分,见表1-13,若不计(FeO)、(Fe2O3),由表1-13中可得:
CaO+MgO+SiO2+P2O5+MnO+Al2O3+CaF2+CaS
=5.531+1.03+1.449+0.156+0.341+0.125+0.218+0.023=8.873kg
已知(FeO)=8.25%,(Fe2O3)=5%,则其余渣应占渣量总数的86.75%。
故总渣量为8.87386.75%=10.228kg
由此可知:
(FeO)=10.228×8.25%=0.844kg,
(Fe2O3)=10.228×5%=0.511kg。
由于矿石和炉衬中带入部分(FeO)和(Fe2O3),其含量参见表1-2和1-10,实际铁氧化物为:
(FeO)=0.844—0.143=0.701kg;其值列入表1-7.
(Fe2O3)=0.507—0.319—0.002=0.186kg.其值列入表1-7
表1-13终渣总量及成分
成分
氧化产物kg
石灰kg
矿石kg
白云石kg
炉衬kg
萤石kg
总计kg
CaO
4.194
0.005
1.328
0.004
5.531
MgO
0.075
0.002
0.715
0.236
0.002
1.03
SiO2
1.286
0.107
0.025
0.011
0.006
0.014
1.449
P2O5
0.154
0.002
0.156
MnO
0.341
0.341
Al2O3
0.058
0.005
0.051
0.002
0.009
0.125
CaF2
0.218
0.218
CaS
0.0135
0.008
0.001
0.023
FeO
0.837
0.143
0.980
Fe2O3
0.507
0.319
0.002
0.828
总计
10.681
冶炼中的吹损计算
根据假设条件,渣中铁珠量为渣量的6%,喷溅损失为铁水量的1%,烟尘损失为铁水量的1.5%。
故可得到:
渣中铁珠量=10.681×6%=0.64kg
喷溅损失量=100×1%=1.0kg
烟尘铁损失量=100×1.5%×(75%×5672+20%×112160)=1.085kg
元素氧化损失=6.572kg(见表1-7)
吹损总量=0.64+1.0+1.085+6.572=9.297kg
钢水量=100—9.297=90.703kg.
1.2.3氧气消耗量计算
1)元素氧化耗氧=6.605kg(见表1-7);
2)烟尘铁氧化耗氧=100×1.5%(75%×1672+20%×48160)=0.341kg;
3)炉衬中碳氧化耗氧=0.066kg(见表1-10下)。
4)炉气自由氧含量=0.054kg
故总耗氧量=6.605+0.341+0.066+0.054=7.066kg.
换算为标准体积为:
7.066×22.432=4.946m3
即冶炼100kg铁水需要4.901氧气。
取氧气利用率为80%,则冶炼1t铁水的实际供氧量为:
4.94680%×10=61.83m3t
由于氧气不纯,含有0.4%的氮气,故供氧时带入的氮气为:
7.066×0.4%=0.028kg
其体积量为:
0.028×22.428=0.023m3,则冶炼1t铁水将会带入0.23m3的氮气。
1.2.4炉气量及成分计算
炉内产生的炉气由CO、CO2、SO2、H2O、N2和自由O2组成。
其中:
CO来源于铁水和炉衬中的碳氧化;CO2来源于铁水、炉衬中碳氧化,以及白云石和石灰石中的烧减量;SO2来源于铁水中硫氧化;H2O来源于矿石和萤石中;N2来源于供氧时被带入。
自由O2约占炉气总量的0.5%,即以上气体占炉气总量的99.5%,则炉气总体积V∑为:
V∑=Vg+0.5%V∑+199.6(22.432Gs+0.5%V∑-Vx)
V∑=99.6Vg+0.7Gs-Vx99.1=7.559m3
式中Vg----CO、CO2、SO2和H2O各组分总体积,m3。
本计算中,其值为
8.033×22.428+2.018×22.444+0.009×22.464+0.013×22.418=7.472m3
Gs----不计自由O2的消耗量,kg。
本计算中,其值为7.012kg(如上)
Vx----铁水与石灰中的S与CaO反应还原出的氧量,其质量为0.007kg。
0.5%----炉气中的自由氧含量。
99.6----由氧气纯度为99.6%转换得来。
自由O2量为7.559×0.5%=0.038m3,其质量为0.038×3222.4=0.054kg
表1-14炉气量及成分7.439
成分
质量kg
体积m3
体积%
CO
7.938+0.095=8.033
8.033×22.428=6.426
85.43
CO2
1.386+0.0165+0.392+0.223=2.018
2.018×22.444=1.027
13.51
SO2
0.009
0.009×22.464=0.00315
0.04
H2O
0.002+0.011=0.013
0.013×22.418=0.0162
0.22
N2
0.028
0.023
0.31
O2
0.054
0.038
0.49
总计
10.021
7.439
100
1.2.5未加废钢和合金时的物料平衡表
把以上各种物质的总收入和总支出汇总起来,得到未加合金时的物料平衡表1-15.
表1-15未加废钢和合金时的物料平衡表
收入
支出
项目
质量kg
%
项目
质量kg
%
铁水
100
86.67
钢水
90.703
79.11
石灰
4.66
2.54
炉渣
10.681
8.82
白云石
2.5
2.60
炉气
10.021
9.11
萤石
0.25
0.35
烟尘
1.50
1.39
炉衬
0.3
0.43
喷溅
1.0
0.87
氧气
7.066
6.44
铁珠
0.64
0.70
总计
114.776
100
总计
114.545
100
计算误差=(收入项—支出项)收入项×100%
=(114..545)114.776×100%=0.2%
1.3热平衡计算
计算所需原始数据有:
各种入炉料及产物的温度(表1-16);物料平均热熔(表1-17);反应热效应(1-18),熔入铁水中的元素对铁熔点的降低值(1-19)
入炉料及产物的温度设定值(表1-16)
名称
入炉物料
产物
铁水
废钢
其他原料
炉渣
炉气
烟尘
温度C
1250
25
25
与铁水相同
1450
1450
注意:
纯铁熔点1536℃
表1-17各材料的热容(kJkg.K)
项目
固态平均热容
熔化潜热
液(气)态平均热容
生铁
0.745
218
0.837
钢
0.699
272
0.837
炉渣
209
1.248
炉气
1.137
烟尘
0.996
209
矿石
1.047
209
表1-18反应热效应(25℃)
元素
反应
反应热kJ·kg-1元素
C
[C]+12O2=CO
-11639
C
[C]+O2=CO2
-34834
Si
[Si]+O2=SiO2
-29202
P
2[P]+52O2=P2O5
-18980
Mn
[Mn]+12O2=MnO
-6594
Fe
[Fe]+12O2=FeO
-4250
Fe
[Fe]+32O2=Fe2O3
-6460
SiO2
SiO2+2CaO=2CaOSiO2
-1620
P205
P2O5+4CaO=4CaOP2O5
-4880
熔入铁水中的元素对铁熔点的降低值(1-19)
元素
C
Si
Mn
P
S
Al
Cr
N’H’O
在铁水中极限溶解度%
5.41
18.5
无限
2.8
0.18
35
无限
溶入1%元素使铁熔点降低值℃
65
70
75
80
85
90
100
8
5
30
25
3
1.5
N,H,O溶入使铁熔点的降低值
适用含量范围%
<1
1.0
2.0
2.5
3.0
3.5
4.0
≤
3
≤15
≤0.7
≤0.08
≤1
≤18
1.3.1热收入
热收入主要是铁水的物理热和元素氧化的化学热。
(1)铁水物理热
铁水凝固温度Tf可用表达式Tf=(1539—∑[%i]△Ti—4)计算,,即
Tf=1536—(100×3.92+8×0.6+5×0.4+30×0.075+25×0.04)—6
=1140℃
铁水物理热Q物=CsTf+Qf+Cl(T—Tf)
=100×[0.745×(1140—25)+218+0.837×(1250—1140)]
=114074.5kJ
注:
式中[%i]---铁水中元素含量;
△Ti-----1%的元素使纯铁凝固温度的降低值,参考高泽平《炼钢工艺学》表8-20
Cs、Cl----分别为液态、固态的热容量,kJkgK,参考表1-3;
Tf、T---分别为冷却剂(生铁)的熔点和熔池温度,K,Tf见表1-3.
(2)铁水中元素氧化放热和成渣热
根据表1-18、表1-7、表1-12数据计算如下:
[C]+12O2=CO3.402×11639=39595.88kJ
[C]+O2=CO20.378×34834=13167.25kJ
[Si]+O2=SiO20.6×29202=17521.2kJ