第四篇 第二章 天然气深冷处理.docx
《第四篇 第二章 天然气深冷处理.docx》由会员分享,可在线阅读,更多相关《第四篇 第二章 天然气深冷处理.docx(37页珍藏版)》请在冰豆网上搜索。
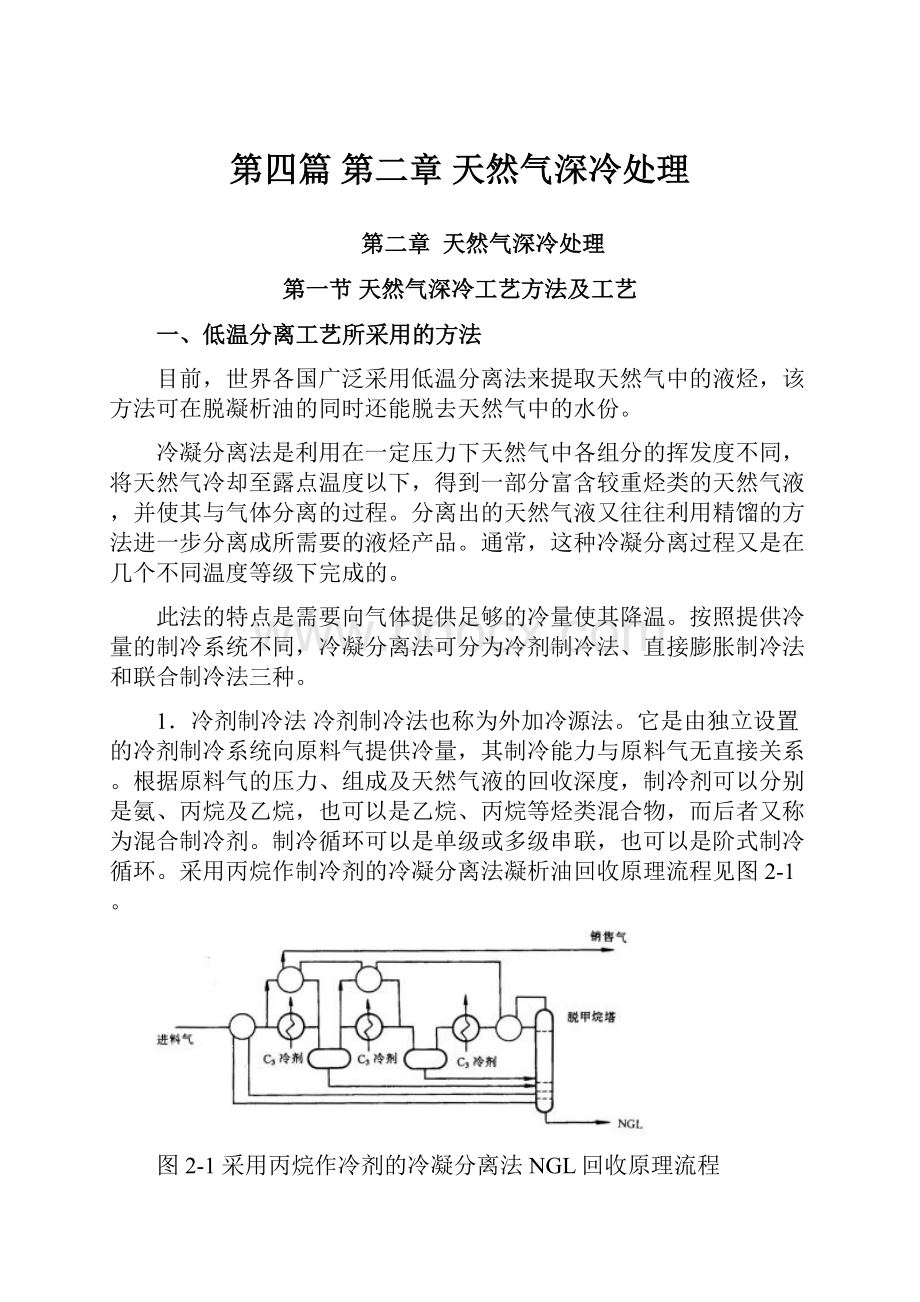
第四篇第二章天然气深冷处理
第二章天然气深冷处理
第一节天然气深冷工艺方法及工艺
一、低温分离工艺所采用的方法
目前,世界各国广泛采用低温分离法来提取天然气中的液烃,该方法可在脱凝析油的同时还能脱去天然气中的水份。
冷凝分离法是利用在一定压力下天然气中各组分的挥发度不同,将天然气冷却至露点温度以下,得到一部分富含较重烃类的天然气液,并使其与气体分离的过程。
分离出的天然气液又往往利用精馏的方法进一步分离成所需要的液烃产品。
通常,这种冷凝分离过程又是在几个不同温度等级下完成的。
此法的特点是需要向气体提供足够的冷量使其降温。
按照提供冷量的制冷系统不同,冷凝分离法可分为冷剂制冷法、直接膨胀制冷法和联合制冷法三种。
1.冷剂制冷法冷剂制冷法也称为外加冷源法。
它是由独立设置的冷剂制冷系统向原料气提供冷量,其制冷能力与原料气无直接关系。
根据原料气的压力、组成及天然气液的回收深度,制冷剂可以分别是氨、丙烷及乙烷,也可以是乙烷、丙烷等烃类混合物,而后者又称为混合制冷剂。
制冷循环可以是单级或多级串联,也可以是阶式制冷循环。
采用丙烷作制冷剂的冷凝分离法凝析油回收原理流程见图2-1。
图2-1采用丙烷作冷剂的冷凝分离法NGL回收原理流程
(1)适用范围。
在下列情况下可采用冷剂制冷法:
以控制外输气露点为主,并同时回收部分凝液的装置。
通常,原料气的冷冻温度应低于外输气所要求的露点温度5℃以上。
原料气较富,但其压力和外输气压力之间没有足够压差可供利用,或为回收凝液必须将原料气适当增压,所增压力和外输气压力之间没有压差可供利用,而且采用制冷剂制冷又可经济地达到所要求的凝液收率。
(2)制冷剂选用的依据。
制冷剂选用的主要依据是原料气的冷冻温度和制冷系统单位制冷量所耗的功率,并应考虑以下因素:
氨适用于原料气冷冻温度高于-25℃~-30℃时的工况。
丙烷适用于原料气冷冻温度高于-35℃~-40℃时的工况。
以乙烷、丙烷为主的混合冷剂适用于原料气冷冻温度低于-35~-40℃时的工况。
能使用凝液作制冷剂的场合应优先使用凝液。
天然气采用制冷剂法回收液烃时在相图上的轨迹见图2-2中的ABC线所示。
图2-2天然气液回收在相图上的轨迹线
2.直接膨胀制冷法直接膨胀制冷法也称膨胀制冷法。
此法不另设独立的制冷系统,原料气降温所需的冷量由气体直接经过串接在该系统中的各种类型膨胀制冷设备来提供。
因此,制冷能力直接取决于气体的压力、组成、膨胀比及膨胀制冷设备的热力学效率等。
常用的膨胀制冷设备有节流阀、透平膨胀机及热分离机等。
(1)节流阀制冷。
在下述情况下可考虑采用节流阀制冷:
压力很高的气井气(一般在10MPa或更高),特别是其压力会随开采过程逐渐递减时,应首先考虑采用节流阀制冷。
节流后的压力应满足外输气要求,不再另设增压压缩机。
如气源压力不够高或已递减到不足以获得所要求低温时,可采用制冷剂预冷。
气源压力较高,或适宜的冷凝分离压力高于干气外输压力,仅靠节流阀制冷也能获得所需的低温,或气量较小不适合用膨胀机制冷时,可采用节流阀制冷。
如气体中重烃较多,靠节流阀制冷不能满足冷量要求时,可采用制冷剂预冷。
原料气与外输气有压差可供利用,但因原料气较贫故回收凝液的价值不大时,可采用节流阀制冷,仅控制其水露点及烃露点以满足管输要求。
若节流后的温度不够低,可采用制冷剂预冷。
采用节流阀制冷的低温分离法工艺流程示意图见图1-11所示。
天然气采用节流阀制冷回收液烃时在相图上的轨迹线见图2-2中ABC`线所示。
(2)热分离机制冷。
热分离机是70年代由法国ELF-Bertin公司研制的一种简易有效的气体膨胀制冷设备,由喷嘴及接受管组成,按结构可分为静止式和转动式两种。
自80年代末期以来,热分离机已在我国一些轻烃回收装置中得到应用。
在下述情况下可考虑采用热分离机制冷:
原料气量不大且其压力高于外输气压力,有压差可供利用,但靠节流阀制冷达不到所需要的温度时,可采用热分离机制冷。
热分离机的气体出口压力应能满足外输要求,不应再设增压压缩机。
热分离机的最佳膨胀比约为5,且不宜超过7。
如果气体中重烃较多,可采用制冷剂预冷。
适用于气量较小或气量不稳定的场合,而简单可靠的静止式热分离机特别适用于单井或边远井气井气的凝析油的回收。
(3)膨胀机制冷。
当节流阀或热分离机制冷不能达到所要求的凝液收率时,可考虑采用膨胀机制冷。
其适用情况如下:
原料气量及压力比较稳定。
原料气压力高于外输气压力,有足够的压差可供利用。
气体较贫及凝液收率要求较高。
1964年美国首先将透平膨胀机制冷技术用于天然气液回收过程中。
由于此法具有流程简单、操作方便、对原料气组成的变化适应性大、投资低及效率高等优点,因此近二三十年来发展很快,美国新建或改建的天然气液回收装置有90%以上采用了透平膨胀机制冷法。
天然气采用膨胀机制冷回收液烃时的原理流程见图2-3所示。
其在相图上的轨迹见图2-2中ARC``线所示。
图2-3采用膨胀机制冷法的NGL回收原理流程
3.联合制冷法联合制冷法又称为制冷剂与直接膨胀联合制冷法。
顾名思义,此法是冷剂制冷法与直接膨胀制冷法二者的联合,即冷量来自两部分:
一部分由膨胀制冷法提供;一部分则由制冷剂制冷法提供。
当原料气组成较富,或其压力低于适宜的冷凝分离压力,为了充分、经济地回收天然气液而设置原料气压缩机时,应采用有冷剂预冷的联合制冷法。
由于我国的伴生气大多具有组成较富、压力较低的特点,所以自80年代以来新建或改建的轻烃回收装置普遍采用膨胀制冷法及有冷剂预冷的联合制冷法,而其中的膨胀制冷设备又以透平膨胀机为主。
目前,轻烃回收装置采用的几种主要工艺方法的烃类收率见表2-1。
当以回收C2+为目的时,可选用的制冷方法是表2-1中的下面四种。
其中,马拉法的实质是用物理溶剂(例如N一甲基吡咯烷酮)代替吸收油,将原料气中的C2+吸收后,采用抽提蒸馏的工艺获得所需的C2+。
乙烷、丙烷的回收率依市场需求情况而定,分别为2%~90%和2%~100%。
这种灵活性是透平膨胀机制冷法所不能比拟的。
表2-1一些NGL回收方法的烃类回收率,%
方法
乙烷
丙烷
丁烷
天然汽油(C5+)
吸收法
5
40
75
87
低温油吸收法
15
75
90
95
冷剂制冷法
25
55
93
97
阶式制冷法
70
85
95
100
节流阀制冷法
70
90
97
100
透平膨胀机制冷法
85
97
100
100
马拉法
2~90
2~100
100
100
需要指出的是,由于天然气的压力、组成及要求的液烃收率不同,因此,轻烃回收中的冷凝分离温度也有不同。
根据天然气在冷冻分离系统中的最低冷冻温度,通常又将冷凝分离法分为浅冷分离与深冷分离两种。
浅冷分离的冷冻温度一般在-20℃~-35℃,而深冷分离的冷冻温度一般均低于-45℃,最低达-100℃以下。
二、天然气凝液回收的工艺方法及设备
通常,天然气液回收工艺方法主要由原料气预处理、压缩、冷凝分离、凝液分馏、干气再压缩以及制冷等部分组成。
1.原料气预处理
原料气预处理的目的是脱除原料气中携带的油、游离水和泥砂等杂质,以及脱除原料气中的水蒸汽和酸性组分等。
当采用浅冷分离工艺时,只要原料气中二氧化碳含量不影响商品天然气的质量要求,就可不必脱除原料气中的二氧化碳。
但当采用深冷分离工艺时,由于二氧化碳会在低温下形成固体,堵塞管线或设备,故应将其含量脱除到允许范围之内。
脱水设施应设置在气体可能产生水合物的部位之前。
流程中有原料气压缩机时,可根据具体情况经过比较后,将脱水设施设置在压缩机的级间或末级之后。
当需要脱除原料气中的酸性组分时,一般是先脱酸性组分再脱水。
2.原料气压缩
原料气压缩目的是为了高压原料气进入装置后即可直接进行预处理和冷凝分离。
但当原料气为低压伴生气时,由于压力通常仅为0.1MPa~0.3MPa,为了提高天然气的冷凝率以及干气要求在较高的压力下外输时,通常都要将原料气增压至适宜的冷凝分离压力后再进行冷凝分离。
当采用膨胀机制冷时,为了达到所要求的冷冻温度,膨胀机进、出口压力必须有一定的膨胀比,因而也应保证膨胀机入口气流的压力。
原料气压缩通常都将压缩后的原料气冷却至常温后将会析出一部分游离水与液烃,分离出游离水与液烃后的气体再进一步进行脱水与冷冻,从而减少脱水与制冷系统的负荷。
3.冷凝分离
(1)多级冷凝与分离经过预处理和增压后的原料气,在某一压力下经过一系列的冷却与冷冻设备,不断降温与部分冷凝,并在气液分离器中进行气、液分离。
由平衡冷凝原理可知,凝液中含有较多的重组分,而气体中则含有较多的轻组分。
当原料气采用压缩机增压,或者采用透平膨胀机制冷时,这种冷凝分离过程通常是在不同压力与温度等级下分几次进行的。
由各级分离器分出的凝液,通常是按其组成、温度、压力和流量等,分别送至凝液分馏系统的不同部位进行分馏,也可直接作为产品出装置。
采用多级分离的原因是:
可以合理利用制冷系统不同温度等级的冷量。
当原料气中含有较多的丙烷、丁烷、戊烷及更重烃类时,增压后采用较高温度等级的冷量即可将相当一部分丙烷、丁烷及几乎全部戊烷及更重烃类冷凝,但所需冷量一般较多。
如果要使原料气中的一部分乙烷及大部分丙烷冷凝,则需要较低温度等级的冷量。
而且,通常是先将前面冷凝下来的凝液分出,故进一步冷冻降温时所需的冷量也往往较少。
采用制冷剂压缩制冷时制冷温度越低,获得单位制冷量所需能耗及运行费用越高。
当原料气为低压伴生气时,采用透平膨胀机制冷也是如此。
如果采用冷剂与膨胀机联合制冷,制冷剂压缩制冷可以经济地提供较多的冷量,但其温度等级较高,而膨胀机制冷仅在制冷温度等级较低时能耗相对较少,但提供的冷量也较少,正好与上述要求相适应。
因此,可以先采用制冷剂预冷,在较高的温度等级(例如,低于-25℃~-35℃)下将较重烃类冷凝与分离出来,再用膨胀机制冷,在较低的温度等级(例如,低于-80℃~-90℃)下使一部分乙烷及大部分丙烷冷凝与分离。
由于已将预冷时析出的凝液分出,使膨胀机入口的气流变贫,不仅减少了膨胀机出口物流的带液量,而且有利于降低膨胀机的制冷温度,使乙烷、丙烷的冷凝率增加。
可以使原料气初步分离。
多级冷凝分离实质上可近似看成是原料气的多次平衡冷凝过程。
因此,原料气经过多级冷凝分离后已获得了初步分离,分出的各级凝液在组成也有一定差别。
前几级冷凝分离分出的凝液中含重组分较多,后几级冷凝分离分出的凝液中含轻组分较多。
这样,就可根据凝液的组成、温度、压力、流量等,分别将它们送至凝液分馏系统的不同部位。
工艺流程组织的需要。
当原料气为低压伴生气并采用多级压缩机增压时,级间及末级出口的气体必须按照压力高低、是否经过干燥器脱水等分别冷却与分离。
如果采用透平膨胀机制冷,经过预冷后的物流在进入膨胀机前也必须先进行气液分离,将预冷中析出的凝液分出。
气体在膨胀机中膨胀降温时,又会析出一部分凝液。
有的装置是将膨胀机出口物流进行气液分离后,再将分出的低温凝液送至脱甲烷塔(如装置以回收C3+为目的,则为脱乙烷塔)塔顶,但更多的装置则是将膨胀机出口的气液混合物流直接送至脱甲烷塔(或脱乙烷塔)直径较大的塔顶空间进行气液分离。
然而,多级冷凝分离的级数越多,设备及配套设施就越多,因而投资就会越高,故应根据原料气组成、装置规模、投资及能耗等进行综合比较后,确定合适的分离级数与塔的进料股数。
分离级数一般以2~5为宜。
当装置中有脱甲烷塔时,该塔的进料股数多为2~4股;当装置中只有脱乙烷塔和其后的分馏塔时,脱乙烷塔的进料股数多为1~3股。
(2)适宜的冷凝分离压力与温度如前所述,当原料气为低压伴生气时,为了提高凝析油的冷凝率及满足干气外输的要求,需将原料气进行增压与冷冻。
这里所说的适宜冷凝分离压力与温度,对于只采用冷剂制冷的装置来讲,一般是指气体在蒸发器中冷冻后的适宜压力与温度;对于采用膨胀机制冷或冷剂与膨胀机联合制冷的装置来讲,一般是指气体在进入膨胀机之前的最后一级气液分离器的适宜压力与温度。
(3)低温换热设备冷凝分离系统中一般都有很多换热设备,这些换热设备除了采用管壳式、螺旋板式换热器外,在低温下运行时大多采用板翅式换热器。
板翅式换热器可作为气/气、气/液、液/液换热器,也可用作冷凝器或蒸发器,可用于逆流、并流和错流的情况,而且在同一设备内可允许2~9股物流之间的换热。
蒸发器是冷剂进行蒸发制冷的主要换热设备。
板翅式蒸发器的冷端温差一般应在3℃~5℃,管壳式蒸发器的冷端温差一般应在5℃~7℃。
蒸发器中冷、热流的对数平均温差宜小于10℃~15℃。
当对数平均温差偏大时,应考虑采用分级制冷的方法。
换热器中冷、热流的对数平均温差也宜小于15℃~20℃。
4.凝液分馏
由冷凝分离系统获得的天然气液有些装置直接作为产品销售,有些装置则送至凝液分馏系统进一步加工成乙烷、丙烷、丁烷(或丙、丁烷混合物)、天然汽油等产品。
凝液分馏系统的作用就是按照上述各种产品的质量要求,利用精馏方法对天然气液进行分离。
因此,凝液分馏系统的主要设备就是分馏塔,以及相应的冷凝器、重沸器和其它配套设施等。
(1)凝液分馏流程由于凝液分馏系统实质上就是对天然气液进行分离的过程,因此,合理组织分离流程,对于节约投资、降低能耗和提高经济效益都是十分重要的。
通常,轻烃回收装置的凝液分馏系统大多采用按烃类相对分子质量从小到大逐塔分离的顺序流程,依次分出乙烷、丙烷、丁烷(或丙、丁烷混合物)、天然汽油等,见图2-4所示。
或者说,对于回收C2+的装置,应先从凝液中脱出甲烷;需要生产乙烷时,再从剩余凝液中分出乙烷。
对于回收C3+的装置,应先从凝液中脱除甲烷和乙烷。
剩余的凝液需要进一步分离时,可根据产品要求、凝液组成进行技术经济比较后确定分离流程。
采用顺序流程的原因是:
图2-4凝液分馏的顺序流程
可以合理利用低温凝液冷量。
凝液分馏系统中的脱甲烷塔全塔通常均在低温下运行,是各分馏塔中温度最低、投资最多和能耗最大的一个塔。
此外,脱乙烷塔的塔顶部位一般也在低温下运行。
当装置以回收C2+为目的时,脱甲烷塔对保证乙烷的收率起着决定性作用,而且它的冷量消耗在凝液分馏系统中占绝大多数比例。
当装置以回收C3+为目的时,脱乙烷塔对保证丙烷的收率也起着决定性作用。
因此,采用图2-4所示的顺序流程,将冷凝分离系统来的各级低温凝液以多股进料形式直接进入脱甲烷(或脱乙烷塔),如前所述,既可合理利用低温凝液的冷量,减少脱甲烷塔(或脱乙烷塔)的冷量消耗,又可降低塔的负荷。
可以减少分馏塔的负荷及热量消耗。
在图2-4所示的顺序流程中,除脱甲烷塔进料为冷凝分离系统来的各级低温凝液外,脱乙烷塔、脱丙烷塔和脱丁烷塔的进料均为前一个分馏塔塔底来的剩余凝液。
由于按照凝液中烃类相对分子质量从小到大逐塔分离,故各塔的负荷及相应的冷凝器和重沸器的热负荷都较小。
而且,除脱甲烷塔塔底温度通常为低温外,其它各塔塔底温度均高于常温,因而重沸器所需的热量也较小。
(2)塔侧换热器一般的精馏,只在分馏塔两端(塔顶和塔底)对塔内物流进行冷却和加热,属于常规精馏,而在塔中间对塔内物流进行冷却和加热的,则属于非常规精馏或复杂精馏。
通常,分馏塔的温度自下而上逐渐降低。
对于塔顶温度低于常温、塔底温度高于常温,而且塔顶、塔底温差较大的分馏塔,如在精馏段设置塔侧冷凝器,就可利用比塔顶冷凝器温度等级较高的冷剂作为冷源,以代替一部分塔顶原来用的温度等级较低冷剂提供的冷量,故可降低能耗。
同理,在提馏段设置塔侧重沸器(中间重沸器),就可利用比塔底重沸器温度等级较低的物流作为热源,也可降低能耗。
对于脱甲烷塔,由于其塔底温度低于常温,因此塔底重沸器本身就是回收冷量的设备。
此时如在提馏段适当位置设置塔侧重沸器,就可回收温度等级比塔底更低的冷量。
必须强调的是,利用复杂精馏塔来提高塔内分离过程的热力学效率,不是靠降低塔的总热负荷,而是借助所用冷量和热量温度等级不同而实现的。
(3)分馏塔的运行压力脱甲烷塔是将凝液中甲烷和乙烷进行分离的精馏设备。
由塔顶馏出的气体中主要组分是甲烷,此外还有少量乙烷。
如果凝液中溶有氮气和二氧化碳,则大多数氮气和相当一部分二氧化碳也将从脱甲烷塔塔顶馏出。
选择脱甲烷塔的压力是一个十分关键的问题。
它会影响到原料气压缩机、膨胀机和干气再压缩机的投资及操作费用、塔顶乙烷损失、塔顶冷凝器所用冷剂的温度等级和负荷、塔侧及塔底重沸器所能回收冷量的温度等级和负荷,以及凝液分馏系统的操作费用等。
当脱甲烷塔进料组成和乙烷收率一定时,塔顶温度随塔的压力降低而降低。
如果要求塔顶的乙烷损失更少,则在相同塔压下所需的塔顶温度更低。
因此,从避免采用过低温度等级的冷量考虑,应尽量采用较高的运行压力。
而且,运行温度过低,对塔的材质要求也更高。
但是,随着塔压增加,甲烷对乙烷的相对挥发度降低,当塔板数一定时,要保证一定的分离要求,就必须增加回流比,或者保持回流比恒定而增加塔板数。
而且,塔压增加后无论是保持回流比恒定还是增加回流比,都会使塔的热力学效率降低,能耗增加。
在对上述因素综合考虑之后,脱甲烷塔不宜采用较高的压力。
此外,由于塔压较低,低压下塔内物流的冷量也可通过塔侧重沸器和塔底重沸器回收,降低整个装置的能耗。
如果是以低压伴生气为原料气,采用压缩机增压且干气外输压力要求不高时,脱甲烷塔就更应采用较低压力。
通常,脱甲烷塔压力为0.7MPa~3.2MPa。
当脱甲烷塔运行压力高于3.0MPa时,称之为高压脱甲烷塔;当脱甲烷塔运行压力低于0.8MPa时,称之为低压脱甲烷塔;脱甲烷塔运行压力介于高压与低压之间时,称之为中压脱甲烷塔。
对于回收乙烷的装置,脱乙烷塔及其后各塔的运行压力应根据塔顶产品的要求、状态(气相或液相)及塔顶冷凝器或分凝器冷却介质的温度来确定。
对于脱丙烷塔、脱丁烷塔(或脱丙、丁烷塔),塔顶温度宜比冷却介质温度高10℃~20℃,产品的冷凝温度最高不应超过50℃。
(4)分馏塔的选型塔型的选择应考虑处理量、操作范围、塔板效率、投资和压力降等因素,一般可选用填料塔;直径较大(大于1.5m)的分馏塔,也可选用浮阀塔,填料宜选用规整填料,如金属板波纹填料。
这种填料效率高、压降小、通量大,具有良好的传质性能,是一种高效填料。
它在较大直径的塔内等板高度仍为0.2m~0.3m,其缺点是价格较高。
采用金属板波纹填料时,喷淋密度一般不小于5m3/(m2•h),气相动能因子宜为0.7kg0.5/(m0.5•S)~2kg0.5/(m0.5•S)。
当选用浮阀塔时,由于凝液在塔内不易起泡,塔内降液管中液体停留时间取3s~3.5s即可。
凝液分馏系统中各塔的典型工艺参数见表2-2。
表中数据并非设计值,只是以往采用的典型数据。
实际选用时取决于很多因素,诸如进料组成、能耗及投资等。
表2-2典型的分馏塔工艺参数
塔名
操作压力,MPa
实际塔板数,块
回流比
回流比
塔效率,%
脱甲烷塔
1.38~2.76
18~26
顶部进料
顶部进料
45~60
脱乙烷塔
2.59~3.10
25~35
0.9~2.0
0.6~1.0
50~70
脱丙烷塔
1.65~1.86
30~40
1.8~3.5
0.9~1.1
80~90
脱丁烷塔
0.48~0.62
25~35
1.2~1.5
0.8~0.9
85~95
丁烷分离塔
0.55~0.69
60~80
6.0~14.0
3.0~3.5
90~110
凝液稳定塔
0.69~2.76
16~24
顶部进料
顶部进料
40~60
回流量与塔顶产品量之比,mol/mol。
回流量与进料量之比,m3/m3。
5.干气再压缩
当采用透平膨胀机制冷时,由膨胀机出口物流分离出来的干气或由脱甲烷塔(或脱乙烷塔)塔顶馏出的干气压力一般可满足管输要求。
但是,有时即使经过膨胀机驱动的压缩机增压后,其压力仍不能满足外输要求时,则还要设置再压缩机,将干气增压至所需之值。
干气再压缩机的选择原则与原料气压缩机相同。
6.制冷
制冷系统的作用是向需要冷冻至低温的原料气及分馏塔塔顶冷凝器提供冷量。
当装置采用冷剂制冷法时,由单独的制冷系统提供冷量。
当采用膨胀制冷法时,所需冷量是由原料气或分离出凝液后的气体直接经过工艺过程中各种膨胀设备来提供。
此时,制冷系统与冷凝分离系统在工艺过程中结合为一体。
如果原料中C3+烃类含量较多,装置以回收C3+烃类为目的,且对丙烷的收率要求不高(例如丙烷收率低于65%~70%)时,通常大多采用浅冷分离工艺。
此时,一般仅用冷剂制冷法(冷剂为丙烷、氨等)即可。
如果对丙烷的收率要求较高(例如,丙烷收率高于75%~80%),或以回收C2+烃类为目的时,此时就要采用深冷分离工艺,选用透平膨胀机制冷法、冷剂与膨胀联合制冷法或混合冷剂制冷法。
第二节天然气深冷工艺原理
一、相变制冷
1.相变制冷原理及过程
相变是指物质聚集态的变化。
物质在发生集态变化时,必然伴随着一定数量的能量交换。
相变制冷就是利用某些物质相变时的吸热效应:
固体物质的融解或升华;液体的汽化等都是吸热的相变过程。
通过这些过程吸收大量热量(潜热),从而可获得低温。
由于升华或融解不能连续提供冷量,不适用于气体分离。
在天然气分离工业中最常见的是利用物质由液态转化为蒸汽的吸热效应制冷,称之为汽化制冷,相变介质称为制冷剂。
为了实现汽化制冷,普遍采用的制冷系统有蒸汽压缩式、吸收式和蒸汽喷射式三类。
以蒸汽压缩式应用最广泛,该制冷系统包括四个主要设备:
压缩机、冷凝器、膨胀机或节流阀、蒸发器。
设备之间用管道连接成为一个完全封闭循环。
在如图2-5所示的系统中,按以下过程进行制冷循环操作。
(1)蒸发过程制冷剂液体(如液氨)在状态4的低温、低压下送入蒸发器管间,与管内的被冷流体(如原料气)换热,在蒸发器内制冷剂吸热而气化(状态1),被冷流体放热而得以降温。
(2)压缩过程为了循环使用制冷剂,可将离开蒸发器的低压低温气态制冷剂通过压缩机,压缩成为高压、高温的制冷剂蒸气(状态,2)。
图2-5蒸汽压缩制冷循环
(3)冷凝过程把处于状态2的制冷剂饱和蒸气引入冷凝器中,与低温的水或空气接触,使制冷剂蒸气变为同温、同压的饱和液体。
(4)膨胀过程从冷凝器流出的液态制冷剂处于状态3(高温、高压),经节流降压(或膨胀机作外功)而降温,使制冷剂的温度远低于被冷流体的温度再导入蒸发器中。
2.制冷剂
制冷剂,也称制冷工质,它是制冷系统中完成制冷循环的工作介质。
如前所述,制冷剂在蒸发器内吸收被冷却物体的热量而蒸发,在冷凝器内将热量传递给周围空气或水而被冷凝成液体。
因此制冷剂是实现人工制冷不可缺少的物质,它与制冷装置的特性及一定条件下的操作压力密切相关。
我们可以通过选择不同的制冷剂或改变制冷剂的蒸发压力来获得不同的低温。
表2-3无机化合物制冷剂
制冷剂代号
制冷剂名称
化学分子式
标准大气压力下沸点(℃)
凝固点(℃)
临界温度(℃)
R717
R718
R729
R744
R764
氨
水
空气
二氧化碳
二氧化硫
NH3
H2O
CO2
SO2
-33.4
100.00
-194.4
-78.52
-10
-77.7
0
-56.6
-75.2
132.4
374.15
-140.56
31
157.2
表2-4氟利昂制冷剂
制冷剂代号
制冷剂名称
化学分子式
标准大气压力下沸点(℃)
凝固点(℃)
临界温度(℃)
R10
R11
R12
R13
R13B1
四氯化碳
一氟三氯二甲烷
二氟二氯甲烷
三氟一氯代甲烷
三氟一溴甲烷
CCl4
CCl3F
CCl2F2
CCl