催化分馏塔等现场制作设备施工方案.docx
《催化分馏塔等现场制作设备施工方案.docx》由会员分享,可在线阅读,更多相关《催化分馏塔等现场制作设备施工方案.docx(43页珍藏版)》请在冰豆网上搜索。
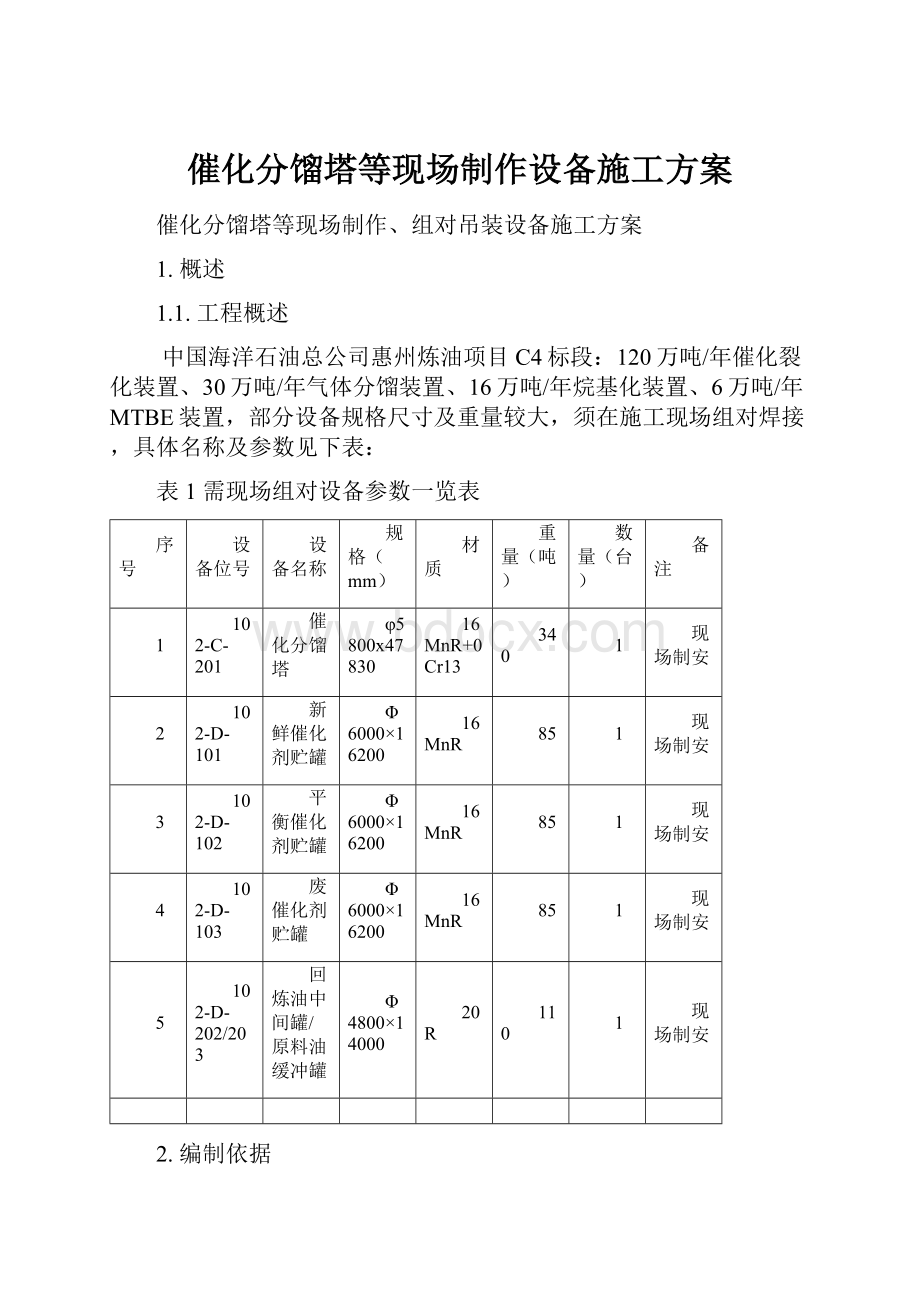
催化分馏塔等现场制作设备施工方案
催化分馏塔等现场制作、组对吊装设备施工方案
1.概述
1.1.工程概述
中国海洋石油总公司惠州炼油项目C4标段:
120万吨/年催化裂化装置、30万吨/年气体分馏装置、16万吨/年烷基化装置、6万吨/年MTBE装置,部分设备规格尺寸及重量较大,须在施工现场组对焊接,具体名称及参数见下表:
表1需现场组对设备参数一览表
序号
设备位号
设备名称
规格(mm)
材质
重量(吨)
数量(台)
备注
1
102-C-201
催化分馏塔
φ5800x47830
16MnR+0Cr13
340
1
现场制安
2
102-D-101
新鲜催化剂贮罐
Φ6000×16200
16MnR
85
1
现场制安
3
102-D-102
平衡催化剂贮罐
Φ6000×16200
16MnR
85
1
现场制安
4
102-D-103
废催化剂贮罐
Φ6000×16200
16MnR
85
1
现场制安
5
102-D-202/203
回炼油中间罐/原料油缓冲罐
Φ4800×14000
20R
110
1
现场制安
2.编制依据
2.1.《压力容器安全技术监察规程》(质技监局锅发[1999]154号)
2.2.《钢制压力容器》GB150-1998
2.3.《钢制塔式容器》JB4710-1992
2.4.《石油化工钢制塔、容器现场组焊施工工艺标准》SH3524-1999
2.5.《钢制压力容器焊接规程》 JB/T4709-2000
2.6.《现场设备、工业管道焊接工程施工及验收规范》GB50236-98
2.7.《压力容器无损检测》 JB4730-94
2.8.《化工塔类设备施工及验收规范》 HGJ211-85
2.9.《石油化工设备安装工程质量检验评定标准》 SHJ514-90
2.10.《石油化工施工安全技术规程》 SH3505-1999
2.11.《压力容器现场组焊(安装)质量保证手册》 Q/HSS01.03
2.12.《起重机械安全规程》 GB6067-85
2.13.《150吨以上履带起重机技术条件》 GB/T14560-93
2.14.《起重机试验规范和程序》 GB5905-86
2.15.招标文件及资料、图纸
3.施工工艺程序、施工方法
3.1.施工方法概述
根据本工程设备的特点,催化分馏塔(C-201)等设备,拟在场外分片制作,采用拖车运输到现场临设区,在临设区组对钢平台上,将分片到货的设备筒体组焊成节,再组对成段,然后二次运输到基础附近,将其吊装到基础上组对焊接,采用正装法施工。
催化分馏塔(C-201)吊装拟采用一台250吨履带吊(SCX2500)进行,其它设备吊装拟采用一台150吨履带吊(QUY150型)进行。
3.2.施工程序:
施工准备(编制焊接工艺卡、焊工考试、吊车进场道路、敷设平台等)→设备场外分片制作→吊车进场→基础验收→设备组对、焊接→无损探伤检测→吊装组对、脚手架搭设→安装内件→水压试验→设备外表面喷砂除锈、防腐、设备内表面酸洗钝化→脚手架拆除→设备封闭
3.3.施工准备:
3.3.1.熟悉设计图纸、文件及相应的技术规程规范,准备焊接工艺评定、编制焊接工艺卡。
3.3.2.组对钢平台应铺设在临设区内,平台规格:
16*40m,铺设方法见图1,钢平台上准备防风、防雨棚,配备必须的消防、照明装置。
3.3.3.计量器具准备:
所有的计量器具,如钢卷尺、水平仪、电流表、电压表、氩气表等必须在检验合格周期内;机具准备:
电焊机、烘箱、砂轮磨光机、起重机具等性能必须良好,数量应满足施工需要。
3.3.4.准备和制作施工中所需的样板、胎具及工卡具、设备吊耳等。
3.3.5.敷设必要的水电设施
3.4.材料管理
3.4.1.材料订购:
供应部门应根据材料计划进行采购,并应符合相应的材料标准;
3.4.2.材料的到货及验收
✧材料到货后应按规格、材质不同分别堆放,材料检验员应对其质保书及到货材料进行核查,无误后方可办理入库。
✧材料标记:
对到货的每一种材料表面作出标记,标记应根据材料情况选择钢印标记、记号笔及挂标签。
3.5.下料、坡口
3.5.1.
下料、坡口可用机械法或火焰法进行切割。
复合钢板用机械法时,基层放在下面,复层放在上面,以避免损伤复层。
用火焰法时,复层放在下面,基层放在上面,切割从基层进行。
切割时应预热和缓冷,以避免发生裂纹和切割面硬化,切割之后应表面探伤检测,不得存在裂纹、划痕、垢皮之类防碍下道工序的缺陷,若有此类缺陷应用砂轮磨掉。
下料前应确认板材的规格尺寸,下料用10米卷尺必须有检验合格证,采用半自动火焰切割机切割,并按图纸要求打好坡口,壁板下料尺寸误差应满足以下要求:
(测量位置见图2)
壁板长度AE、CF尺寸公差:
±2mm;
壁板对角线长度AF、AE公差:
±5mm
壁板宽度AC、EF尺寸公差:
±2mm;
3.5.2.壁板卷制
壁板卷制前应制作好弧形样板和直线样板,样板采用1mm厚白铁皮制作,弧形样板弦长为2m,直线样板长度为1m,为了防止运输过程中发生曲率变化,还须按塔壁板的曲率制作壁板运输胎具,胎具具体形式见右图3。
3.5.3.筒体临时加固方法
筒体组对,首先按照图纸及规范要求对各节筒体组对段进行圆周找圆,找圆方法,用弧形胎具、千斤顶和锤子冷找圆法,找圆合格后用临时支撑加固,见图4所示。
坡口按技术要求打磨好钝边,组对坡口处理完后,将筒体放到准备好的胎具上进行对口,胎具要放置在同一条中心线上。
3.6.半成品、零部件验收
3.6.1.进入现场的半成品、零部件必须具有下列出厂技术文件:
✧装箱单
✧压力容器产品安全质量监督检验证书
✧产品质量证明文件
✧其他技术文件
3.6.2.半成品出厂应按规定附带符合要求的试板
3.6.3.半成品应有明显标记并与排版图一致。
3.6.4.坡口表面应符合下列要求:
✧坡口尺寸符合图样规定,表面应平滑
✧熔渣、氧化皮应清除干净
✧坡口表面不得有裂纹、分层、夹渣等缺陷
3.6.5.球形封头、椭圆形封头瓣片的曲率偏差见下图5:
3.6.6.球形封头、椭圆形封头瓣片的几何尺寸允许偏差见下图6:
3.6.7.分片的筒体板应立放在钢平台上,用弦长等于设计内直径的1/4且不小于1000mm的样板检查板片的弧度,间隙不得大于3mm。
3.6.8.内件及附件的验收
✧内件及附件的交附应有装箱清单,装箱清单应写内件、附件的型号、规格、材质、数量及产品合格证。
✧内件及附件的外形尺寸,加工精度应符合设计文件及标准要求,无运输变形及局部损坏。
✧清点、验收后的塔内件、附件应按材质型式分类堆放,并用铭牌作标志;堆放场地应平整、清洁,无泥砂、油污、腐蚀性气体等;设备内件、附件严禁露天堆放,以防腐蚀。
3.7.设备的现场组装
3.7.1.封头的组装:
3.7.2.
筒节组装
3.7.3.
筒体的组对:
3.7.4.
催化分馏塔(C-201)第二段下封头的组对:
3.7.5.催化分馏塔(C-201)第段上封头的组对:
3.8.裙座的制作、安装
3.8.1.裙座上地脚螺栓通孔应跨中均布,中心圆直径允差、相邻两孔弦长允差和任意两孔弦长允差均不大于2mm。
3.8.2.裙座的中心线应与塔体中心线相重合,其允许误差为±5mm。
3.8.3.裙座与塔体封头相接处,如遇到封头拼接焊缝时,应在裙座上开出豁口。
3.8.4.裙座的底座应垂直于底座圈和塔体中心线。
3.8.5.设备垫铁的选用
根据公式A≥C·100(G1+G2)/nR和G2=πd02[σ]n′/4
式中:
A—一组垫铁的面积mm2
C—系数C=2.3
G1—设备附件及物料等的重量
G2—全部地脚螺栓紧固后,作用在垫铁上的总压力Kgf
d0—地脚螺栓根径mm
n′—地脚螺栓数量
[σ]—地脚螺栓材料的许用应力
n—垫铁组数量
R—基础混凝土的抗压强度
✧每个地脚螺栓近旁一组垫铁,尽量靠近地脚螺栓。
✧垫铁组宜使用成对斜垫铁,两垫铁的斜面要相向使用,搭接长度应不小于全长的3/4,偏斜角度不超过3°;斜垫铁下面应有平垫铁。
✧应尽量减少每一组垫铁的块数,一般不超过4块,并应少用薄垫铁;放置平垫铁时,最厚的放在下面,最薄的放在中间,调整完毕后应将每块垫铁互相焊牢。
✧每一组垫铁均应放置整齐平稳,接触良好;垫铁表面的油污等应清除干净;设备找平后,每组垫铁均应压紧,可以采用手锤逐组敲击听音检查。
✧垫铁应露出设备底座板外缘10mm,垫铁组伸入长度应超过地脚螺栓。
3.9.组对允许偏差项目值:
3.9.1.对口错边量的允许值见表-2、图-12:
表-2:
对口处钢板厚度δn
按焊接接头类别划分的对口错边量b
A
B
12<δn≤20
≤3
≤1/4δn,
20<δn≤40
≤3
≤5
3.9.2.棱角对口后棱角E值:
不得大于设备壳体名义厚度δn的1/10,且不大于3mm,见图-13
E
Di
Di
δn
δn
3.9.3.圆度e的允许值不大于该断面设计内径Di的1%,且不大于25mm,见图-14:
组对成型后,在塔体上0°、90°、180°、270°纵向组装线方位拉φ0.5mm钢丝检查,塔体不直度ΔL应≤1.5mm/m,且不大于3mm。
3.10.接管的制作、安装
3.10.1.接管安装中心方位及标高允许偏差为±5mm。
补强圈的弧度与壳体相吻合,贴紧。
3.10.2.接管、补强圈与壳体间的焊接形式按照图纸要求进行,其中径向接管与壳体之间采用全熔透焊。
3.10.3.接管与壳体连接的内外壁应圆滑过渡,并对此焊缝进行100%磁粉检测,符合JB4730-94规定中的Ⅰ级为合格。
3.10.4.DN≥600的管口接管(含水包)采用现场钢板卷焊时,接管自身的焊接接头应进行100%射线探伤检查,符合JB4730-94规定中的Ⅱ级为合格。
3.10.5.设备上凡被补强圈、支座、垫板等覆盖的焊缝均应打磨至于母材齐平,以使设备与其间紧密贴合。
3.10.6.设备补强圈应在设备压力试验前通以0.4MPa~0.5MPa的压缩空气检查焊缝质量。
3.11.法兰安装
法兰面应垂直于接管法兰,应保证法兰面的水平或垂直,其偏差均不得超过法兰外径的1%(法兰外径小于100mm时接管按100mm计)且不大于3mm。
法兰螺栓通孔应于设备主轴或铅垂线跨中布置。
3.12.加强圈、保温支承圈的制作、焊接
3.12.1.加强圈采用弯制,其内侧圆弧度不得大于3mm(1.5m长圆弧样板检查)。
3.12.2.保温支承圈采用半自动氧乙炔焰切割机下料,其内侧圆弧度不得大于3mm(1.5m长圆弧样板检查)。
3.12.3.安装前,先对筒体进行找平,然后采用塑料管水位计在筒体内壁划出组装基准线,依照基准线进行安装。
3.12.4.保温圈若与筒体环焊缝、接管或吊耳相碰,可适当调整标高或局部截断。
3.12.5.加强圈若与筒体环焊缝、接管或吊耳相碰,可适当调整间距,调整后,相邻加强圈间距不得大于3500mm,加强圈不能截断。
3.13.塔内件安装
3.13.1.塔内件安装的一般规定
(1)内件安装前,应清除表面油污、焊渣、铁锈、泥沙及毛刺等杂物,对塔盘零部件还应编注序号以便安装。
(2)安装塔盘人员应遵守下列规定:
✧一层塔盘的承载人数不得超过塔盘的承载能力。
✧塔内施工人员须穿干净的胶底鞋,且不得将体重加在塔板上,应站在梁上面或木板上;
✧人孔及人孔盖的密封面及塔底管口应采取保护措施,避免砸坏或堵塞;搬运和安装塔盘零部件时,要轻拿轻放,防止碰撞弄脏,避免变形损坏;
✧施工人员除携带该层紧固件和必需工具外,严禁携带多余的部件,每层塔盘安装完毕后,必须进行检查,不得将工具等遗忘在塔内。
(3)内件安装应在塔体压力试验合格并清扫干净后进行;内件安装时,应严格按图样规定施工,以确保传质、传热时气液分布均匀。
3.13.2.塔盘构件安装
(1)塔盘构件安装宜按下列顺序进行:
支撑点测量-→降液板安装-→横梁安装-→受液盘安装-→塔盘板安装-→溢流堰安装-→气液分布元件安装-→通道板拆装-→清理杂物-→检查人员最终检查-→通道板安装-→人孔封闭-→填写封闭记录
(2)塔盘支持圈水平度、间距的复测方法、部位及标准应符合下列规定:
✧塔体安装合格后,将水平仪的储罐固定在一层支持圈上或特设的支架上,刻度尺下端放在支持圈测点上,各测点玻璃管液面计读数的差值即为水平度偏差值(见图15)
图15用水平仪测量支持圈水平度
✧支持圈与塔壁焊接后,其上表面在300毫米弦长上的局部水平度偏差不得超过1毫米,整个支持圈上表面水平度允许偏差按下表的规定:
表3:
整个支持圈上表面水平度允许偏差(毫米)
塔体内径
允许偏差
1600<D≤4000
≤5
4000<D≤6000
≤6
✧
相邻两层支持圈的间距允许偏差不得超过±3毫米,每20层内任意两层支持圈间距允许偏差不得超过±10毫米。
(3)降液板的支持板安装偏差应符合下列规定(见图16):
✧螺栓孔水平面间距A允许偏差不得超过3毫米;
✧
支持板安装部位B允许偏差为±2B/100;
✧支持板倾斜度Q允许偏差为±2G/100;
✧支持板安装位置R1允许偏差为±5R1/1000,但不大于6毫米;
✧支持板安装位置R2允许偏差为±5R2/1000,但不大于12毫米。
(4)降液板安装应符合下列规定:
✧降液板的长度允许偏差+0~-4毫米,宽度尺寸允许偏差+0~-2毫米,降液板的螺孔距离允许偏差为±1毫米。
✧降液板安装位置要求:
①液板底端与受液盘上表面的垂直距离K允许偏差为±3毫米(见图17);
②液板与受液盘立边或进口堰边的水平距离D允许偏差为+5~-3毫米(见图五);
③液板至塔内壁通过设备中心的垂直距离A允许偏差为±6毫米(见图18);
④降液板间距B允许偏差为±6毫米(见图18)
✧固定在降液板上的塔板支承件,其上表面与支持圈上表面应在同一水平线上,允许偏差为+1~-0.5毫米。
图17降液板安装允许偏差
图18降液板、塔板支承板安装允许偏差
(5)梁安装应符合下列规定:
✧梁上表面的水平度在300毫米长度不得超过1毫米,总长度弯曲度允许偏差为梁长度的1/1000,但不得超过5毫米;
✧梁安装的中心位置与图示尺寸的偏差不得超过2毫米;
✧梁安装后,其上表面与支持圈上表面应在同一水平度上,梁的水平度偏差:
D≤1600,水平度≤3毫米;1600<D≤4000,水平度≤5毫米。
(6)受液盘安装应符合下列规定:
✧受液盘板的长度允许偏差为+0~-4毫米,宽度尺寸允许偏差为+0~-2毫米;
✧受液盘的局部水平度在300毫米长度内不得超过2毫米。
整个受液盘的弯曲度,当受液盘长度小于或等于4米时不得超过3毫米;
✧受液盘其他安装要求与塔盘相同。
(7)分块式塔盘板安装应符合下列要求:
✧塔盘板两端支承板间距E允许偏差为±3毫米;
✧塔盘板长度允许偏差为+0~-4毫米,宽度尺寸允许偏差为+0~-2毫米;
✧塔盘板局部不平度在300毫米长度内不得超过2毫米,塔盘板在整个板面内的弯曲度按下表的规定:
表4:
整块塔盘板允许弯曲度(毫米)
塔盘板长度
弯曲度
筛板、浮阀
<1000
2
1000~1500
2.5
>1500
3
✧塔盘板的安装应在降液板、横梁的螺栓紧固后进行,先组装两侧弓形板,再由塔壁两侧向塔中心循序组装塔盘板;
✧塔盘板安装时,先临时固定,待各部位尺寸与间隙调整符合要求后,再用卡子,螺栓予以紧固;
✧每组装一层塔盘板,即用水平仪校准塔盘水平度,水平度合格后,拆除通道板放在塔盘上。
(8)塔盘板水平度测量方法及合格标准应符合下列规定:
✧塔盘板安装后,塔盘面水平度允许偏差按下表的规定:
表5:
塔盘面上水平度允许偏差(毫米)
塔体内径
水平度允许偏差
1600<D≤4000
6
4000<D≤6000
9
✧安装在塔盘板上的卡子、螺栓的规格、位置、紧固度应符合图样规定;
✧样板的排列、板孔与梁距离、板与梁或支持圈搭接尺寸及密封填料等应符合图样规定。
(9)溢流堰安装应符合下列规定:
✧溢流堰(出口堰与进口堰)安装后,堰顶端水平度允许偏差应按下表6的规定;堰高允许偏差应按下表7的规定:
表6:
溢流堰顶端水平度允许偏差(毫米)
塔盘直径
允许偏差
1500<D≤2500
4.5
D>2500
6
表7:
溢流堰高度允许偏差(毫米)
塔盘直径
允许偏差
D≤3000
±1.5
D>3000
±3
✧组装可调进口堰时,进口堰与降压板的间隙用进口堰进行调整,进口堰固定后,在其两端安装调整板并用螺栓固定,进口堰与塔壁应无间隙。
3.13.3.塔盘气液分布元件的安装
(10)浮阀安装应符合下列规定:
✧浮阀质量应符合规范的规定。
安装时,宜检查浮阀的重量,并且测浮阀腿的高度、弯曲度、伤痕、表面毛刺等情况;
✧浮阀安装后应检查浮阀腿在塔板内的挂连情况、浮阀腿煨弯长度及角度(或铆固)情况(宜用专用工具)应符合设计要求;手从下边托浮阀时,应能上下活动,开度一致,没有卡涩现象。
3.13.4.塔盘全部安装完成后,检查人员应会同有关人员按要求进行检查;
在最终检查之前,应清除塔盘上及塔底的杂物;最终检查之后安装塔盘通道板、人孔盖,并进行封闭,同时填写“塔盘安装检查记录”。
4.吊装
4.1.催化分馏塔(C-201)的吊装
4.1.1.吊车选用:
设备分段吊装拟采用一台250吨履带吊(SCX2500)进行。
4.1.2.场地要求:
250t履带吊车行走道路及站位基础下挖600mm,并机械夯实,上铺400mm毛石;毛石上铺200mm碎石,并机械夯实。
履带下铺40mm钢板,并保证基础不积水。
4.1.3.设备分段
4.1.3.1.催化分馏塔(C-201)分段情况见表2(含梯子平台等重量)。
均按板宽1.8m考虑,现场施工时应按实际板宽调整。
基础高按3m考虑
表8:
催化分馏塔(C-201)分段表
序
号
分段
名称
规格
(mm)
设备重量(t估)
安装顶
标高
吊车型号
吊车性能
回转半径
(m)
臂杆
长度
(m)
额定起重量(t)
1
第一段(裙座下封头)
φ5800×3960
29
6.96m
250吨履带吊(SCX2500)
30
91
249
2
第二段
(筒体)
φ5800×5400×(26+3)
27
12.36m
250吨履带吊(SCX2500)
30
91
249
3
第三段
(筒体)
φ5800×5400×(26+3)
27
17.76m
250吨履带吊(SCX2500)
30
91
249
4
第四段
(过渡段)
φ5800×5400×(26+3)/(24+3)
26.5
23.16m
250吨履带吊(SCX2500)
30
91
249
5
第五段
φ5800×5400×(24+3)
25
28.56m
250吨履带吊(SCX2500)
30
91
249
6
第六段
φ5800×5400×(24+3)
25
33.96m
250吨履带吊(SCX2500)
30
91
249
7
第七段
φ5800×5400×(24+3)/(22+3)
25
39.36m
250吨履带吊(SCX2500)
30
91
249
8
第八段
φ5800×5400×(22+3)
23.5
44.76m
250吨履带吊(SCX2500)
30
91
249
9
第九段
φ5800×5400×(22+3)
23.5
50.16m
250吨履带吊(SCX2500)
30
91
249
15
第十段
上封头段φ5800*4830
20.5
54.99m
250吨履带吊(SCX2500)
38
91+65
70
4.1.3.2.新鲜催化剂贮罐、平衡催化剂贮罐、废催化剂贮罐、回炼油中间罐/原料油缓冲罐由于招标阶段没有提供设备图纸,不再详细列出分段明细;其中新鲜催化剂贮罐、平衡催化剂贮罐、废催化剂贮罐拟分四段选用150t履带吊(QUY150型)吊装,回炼油中间罐/原料油缓冲罐拟分五~六段选用150t履带吊(QUY150型)吊装。
4.1.4.设备吊装受力计算
催化分馏塔(C-201)吊装计算以最具代表性的第一段、第九段、第十段为例对主吊吊车选用性能加以确认,并核算吊车的起吊能力。
4.1.4.1.催化分馏塔(C-201)第一段吊装计算:
(1)设备的吊装参数
设备直径:
φ5800×3960
设备长度度:
3.96m
设备重量:
29T
(2)主吊车吊装计算
① 主吊车性能预选用为:
250吨履带吊(SCX2500),
回转半径:
20m臂杆长度:
70.1m
起吊能力:
40.6t
② 臂杆倾角计算:
α=arccos(S-F)/L
=arccos(20-1.4)/70.1
=74.6°
式中:
S—吊车回转半径:
选S=20m
F—臂杆底铰至回转中心的距离,F=1.4m
L—吊车臂杆长度,选L=70m
③ 净空距离A的计算:
A=Lcosα-(H-E)ctgα-D/2
=70.1cos74.6°-(6.96-2.5)ctg74.6°-5.8/2=14.6m
式中:
H—设备吊装时距臂杆最近的最高点至地面的高度,选H=6.96m
E—臂杆底铰至地面的高度,E=2.5m
D—设备直径:
D=5.8m
④ 设备吊装总荷重:
P=K(PQ+PF)=1.1*(29+3)=35.2t
式中:
PQ—设备吊装自重PQ=29t
PF—设备吊装吊索及平衡梁等的附加重量,取PF=3t
K—动载系数,K取1.1
⑤ 主吊车吊装能力选用校核:
吊装总荷重/起吊能力=P/Q=35.2/40.6=86.7%,能满足吊装要求。
(4)吊装钢丝绳的较核计算
钢丝绳规格:
φ43mm,6*37+1-155;
拴挂方式:
1弯2股;
①受力计算
T=P/K*C
T=1080/6*0.82=147.6KN
式中:
T—钢丝绳的容许拉力
P—钢丝绳的钢丝破断拉力总和,P=1080kN
K—安全系数,K=6
C—6*37+1-155钢丝绳的换算系数,c=0.82
②受力分析
图20:
受力分析图
S=G/2n*(1/sinβ)
=352/4*(1/sin60°)=102KN
式中:
G—设备及吊索平衡梁的重量,G=352