9顾正桂萃取精馏技术在资源综合利用过程中的应用.docx
《9顾正桂萃取精馏技术在资源综合利用过程中的应用.docx》由会员分享,可在线阅读,更多相关《9顾正桂萃取精馏技术在资源综合利用过程中的应用.docx(21页珍藏版)》请在冰豆网上搜索。
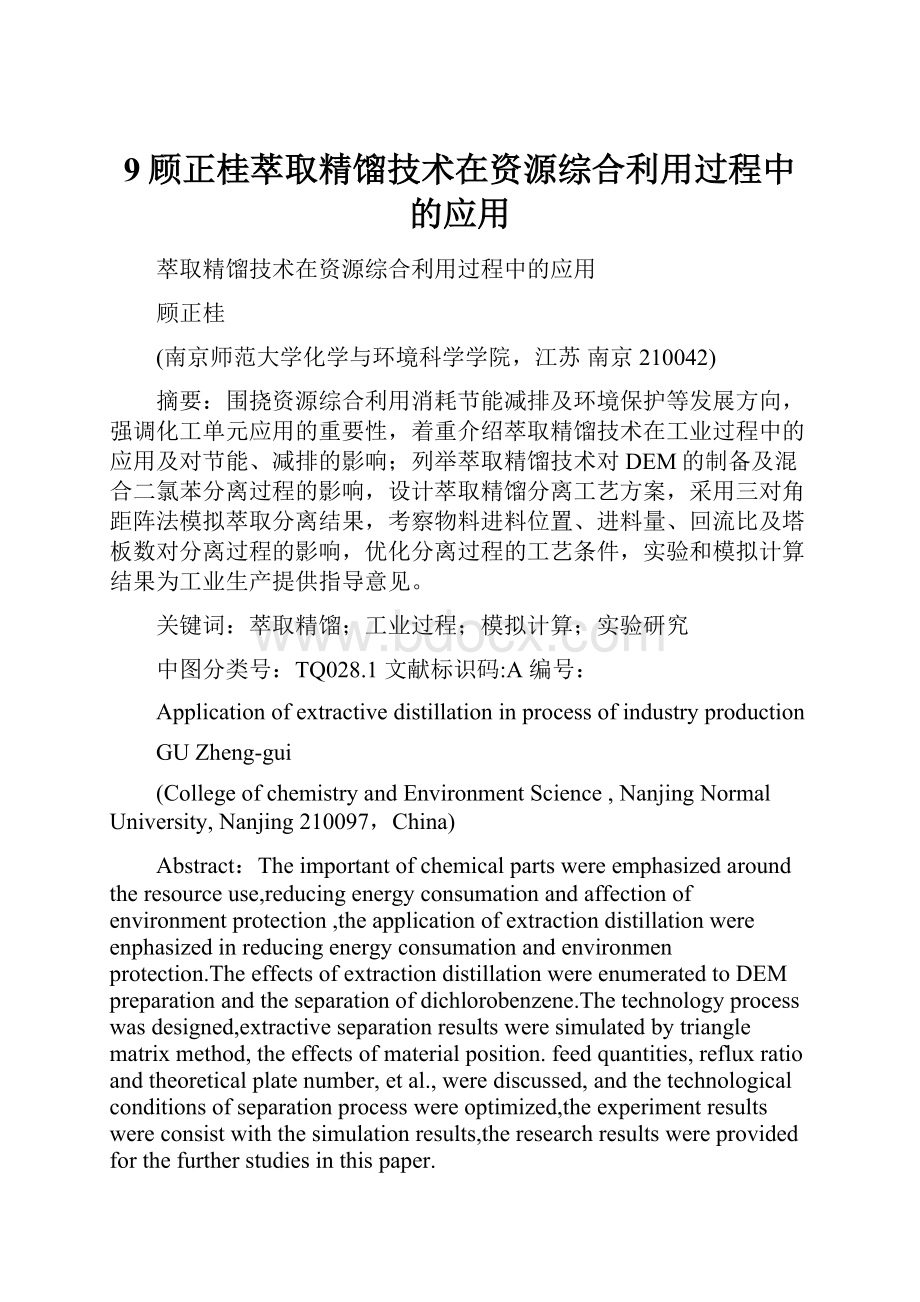
9顾正桂萃取精馏技术在资源综合利用过程中的应用
萃取精馏技术在资源综合利用过程中的应用
顾正桂
(南京师范大学化学与环境科学学院,江苏南京210042)
摘要:
围挠资源综合利用消耗节能减排及环境保护等发展方向,强调化工单元应用的重要性,着重介绍萃取精馏技术在工业过程中的应用及对节能、减排的影响;列举萃取精馏技术对DEM的制备及混合二氯苯分离过程的影响,设计萃取精馏分离工艺方案,采用三对角距阵法模拟萃取分离结果,考察物料进料位置、进料量、回流比及塔板数对分离过程的影响,优化分离过程的工艺条件,实验和模拟计算结果为工业生产提供指导意见。
关键词:
萃取精馏;工业过程;模拟计算;实验研究
中图分类号:
TQ028.1文献标识码:
A编号:
Applicationofextractivedistillationinprocessofindustryproduction
GUZheng-gui
(CollegeofchemistryandEnvironmentScience,NanjingNormalUniversity,Nanjing210097,China)
Abstract:
Theimportantofchemicalpartswereemphasizedaroundtheresourceuse,reducingenergyconsumationandaffectionofenvironmentprotection,theapplicationofextractiondistillationwereenphasizedinreducingenergyconsumationandenvironmenprotection.TheeffectsofextractiondistillationwereenumeratedtoDEMpreparationandtheseparationofdichlorobenzene.Thetechnologyprocesswasdesigned,extractiveseparationresultsweresimulatedbytrianglematrixmethod,theeffectsofmaterialposition.feedquantities,refluxratioandtheoreticalplatenumber,etal.,werediscussed,andthetechnologicalconditionsofseparationprocesswereoptimized,theexperimentresultswereconsistwiththesimulationresults,theresearchresultswereprovidedforthefurtherstudiesinthispaper.
keywords:
extractivedistillation;industryprocess;simulationcalculation;experimentresearch
1萃取精馏在工业生产过程中的应用
随着经济的发展,我国资源结构发生了根本性的变化,20世纪60~70年代以煤炭资源为主要原材料,80年代转变为以石油为主要原材料,随着资源需求量的增加,现有石油、煤炭供应量远满足不了需求。
近年,国家发展改革委员会、财政部发出生物质能综合利用通知,为加速农林废弃生物质能综合利用,国家近期将重点支持三大领域,包括生物质成型燃料、畜禽养殖场沼气发电和生物质气化(碳化)发电。
无论是石油、煤炭工业的发展,还是生物质资源的利用,加快资源的综合利用,是解决资源、能源紧张的有效途径,也是减排的有效手段。
资源综合利用的有效途径是多种多样,按照过程控制和实现目标产物,围挠提高产品品质和减排,应将资源利用分为2种类型,一是针对原材料,对处理的方法和工艺进行优化,二是对过程典型设备结构进行设计和优化,达到最大限度的利用原材料,实现过程中能源的循环利用,减少生产过程中残余物的排放排。
1.1煤炭综合利用及有待开发的前景[1]
煤炭不仅是一种能源资源,同时还是一种宝贵的碳氢资源和化工原料。
煤化工的产品主要有洁净的高温值燃料、化学品和炭素材料。
煤化学工程和煤基—碳化学工程可以用煤为原料生产塑料、合成纤维、
合成橡胶、碳纤维、医药、农药、染料、香料等人们现实生产和生活中已不可缺少的物资和用品。
目前煤化工加工体系如图1所示。
图1煤化工加工体系
随着清洁能源和可再生能源的开发,21世纪的能源结构将逐渐改变,到21世纪中叶有可能发生重大变化,但煤炭的绝对消费量有增无减。
洁净煤技术和煤炭转化将起重大作用。
煤的洁净转化和定向转化将在本世纪得到蓬勃发展,煤炭的综合利用前景广阔。
据估计,到2010年,煤炭在一次能源中仍将占60%以上。
到本世纪中叶,煤炭有可能降到50%左右,但是由于国民经济发展的需要,煤炭消费的绝对量仍很大。
与此同时,由于石油供给骤减,煤化工将取代石油化工。
为了我国的可持续发展,解决好能源与环境问题至关重要。
在21世纪上半叶,要大力推广洁净煤技术,发展煤化工。
大力发展煤气化、液化及热解技术,无论液化过程,还是热解过程,分离技术的应用将起到重要的作用,尤其萃取分离技术对产品的品质提升和原材料充分利用均会起到明显的效果。
1.2石油综合利用及有待开发的前景
石油化工产品多种多样,不同的产品有不同的生产过程,但完整的化工生产过程主要由原材料供应、反应过程、分离过程、传热过程、环保装置及公用工程所构成。
随着石油工业的发展,石油化工产品生产所用原料路线发生了根本性的变化,20世纪60年代至70年代,石油化工基础原料生产主要以煤炭为原料,从70年代末,我国相继从国外引进大型炼油装置,许多化工产品,如烯烃、芳烃、乙炔、各种单体以及合成氨等相继转为利用石油、天然气生产。
目前除10%左右石油化工产品来自煤炭及生物质外,约有90%以上的有机化工产品来源于石油、天然气,因此石油化学工业已形成重要的基础工业部门。
目前我国石油加工体系如图2所示,石化化工加工体系已基本形成,但产品的品质、过程能源的综合利用及深加工有待进一步开发。
如石油炼制中生产大量的90#、120#、200#溶剂油及裂解和重整中形成的重芳油深加工领域需要加强开发,实现资源的最大化利用。
在这些领域国外许多技术有待消化、吸收和提高,更需要创新性的方法、工艺及先进的设备。
图2石油加工体系图
1.3天然气综合利用及发展前景
以天然气为原料经过裂解、分离和合成等加工过程,可生产基础原料、精细有机化工原料、精细化学品及高分子材料。
目前天然气加工情况如图3所示,从天然气到材料的合成已形成较为完整的体系,但裂解及分离过程所形成馏分的加工过程有待改进,产品品质有待进一步提高,需要引进和采用新的分离和加工技术,实现现有资源的最大化利用,如合成气的利用、二烯烃的提取及碳五的开发均有待提高。
1.4生物质综合利用及有待开发前景[2]
随着经济的快速发展,煤炭和石油的供应满足不了需求,加强第三大资源-生物质的利用已成为化工、能源及环境行业急需要解决的课题。
为了加强生物质的利用,国家近期将重点支持生物质利用的一些领域,包括生物质成型燃料、畜禽养殖场沼气发电、生物质气化(碳化)发电及深加工成清洁产品。
图3天然气加工体系图
(1)生物质成型燃料。
以农作物秸秆、林木枝桠材、农林产品加工剩余物等生物质为原料,生产颗粒状、棒状和块状等致密成型燃料,主要用于为农村和小城镇居民提供炊事、取暖等生活燃料,多余产品可向市场出售。
通过示范项目建设,完善生物质成型技术,建立生物质成型燃料的商业化经营模式。
(2)畜禽养殖场沼气发电。
以大型畜禽养殖场的沼气为燃料进行发电利用,完善畜禽养殖场环境治理工程,增加清洁能源供应,提高畜禽养殖的经济效益,促进畜禽养殖废弃物资源的综合利用。
养殖场沼气发电站并入电网运行,所发电力首先满足自身用电需要,多余电力向电网企业出售。
生物质能利用提上日程国家重点支持三大领域。
(3)生物质气化(碳化)发电。
结合农林生物质气化(碳化)集中供气,利用多余生物质燃气进行发电,充分利用农林废弃生物质资源,提高生物质气化(碳化)项目的经济效益。
示范项目要采用高效清洁的生物质气化技术,燃气发电机组并入电网运行,所发电力由电网企业收购。
(4)农副产品清洁化深加工成生化产品。
目前部分资源已在利用,通过不同的方式实现了生物、医药及化工产品的生产,但生产的规模、能源的综合利用及清洁化生产未能得到一定水准。
按照现有状况,生产的方法、工艺及设备有待改进,需要采用节能型的生产工艺和环保性的设备。
对于这一领域的开发,先进的分离技术需要大胆采用。
1.5萃取精馏技术对资源综合利用的影响
资源充分利用需要不断地对加工方法、加工过程及设备进行改进和提高,完整的化工生产过程主要由原材料供应、反应过程、分离过程、传热过程、环保及公用工程所构成,如图4所示。
对于原料的深
加工、产品的品质提高及节能减排,控制加工过程每1个环节尤为重要,采取新方法、新工艺和新型设备是关键,分离技术技术在这一领域显得十分重要。
近年来,特种分离过程在资源综合利用领域中越来
越多受到欢迎,如萃取精馏,液液萃取及膜分离技术受到生产的重视,按照分离介质,分离过程大计可分为图5所示方向。
在炼油、精细化学品、医药及环保应用领域中,常遇到难分离的共沸物、小沸点差的混合溶液,对于这类介质采取萃取分离技术是行之有效的。
2设计萃取精馏模型及模拟框图
计算的目的是在不同的设计参数下分析从不同组份及含量的原料中目标产物,观察塔内、塔顶和塔底各组份、温度及流量的变化情况,考验汽液平衡模型,并为进一步小塔试验提供必要的数据。
萃取精馏塔的模型见图6,计算框图见图7[3]。
本程序作如下说明:
①在计算中,汽液两相假设为恒分子流,原料为饱和蒸汽进料;②本程序计入逐极压力变化,每层实际压降近似值取3mmHg;③子程序TRIDA用于求解各极的液相组成xij时,求出的xij为负值时均置为零。
输入各独立变量值Zfi、ZSi、V1、L1、N、Pj、Fj、Sj、Gj
给定Vj、Lj
给定初值Tij,由物料恒算方程计算xij初值
Tk=1.01Tk-1
Tk=0.99Tk-1
正割法调整T
据以Wilson方程求rij
NO
NO
A
YES
B
由Antoine常数求饱和蒸汽压Pij
由关系式Kij=rijPij/Pj
求平衡常数Kij
C
YES
NO
调用TRIDIA求解xij
圆整xij=xij/Σxij.yij=Kij.xij
xijo=xijo+(xij-xijo)•Sx
NO
输出计算结果
Tj、Pj、Xij、Yij
YES
图7萃取精馏计算框图
决定萃取分离效果的主要因素是溶剂,除此以外,还与溶剂与进料的比例、回流比及进料位置等因素有关。
采用有效的溶剂与进料的比例、回流比及进料位置等能取得较好的结果。
3萃取精馏在综合利用过程的应用
3.1在混合氯化苯分离过程中的应用
3.1.1混合二氯苯分离现状
二氯苯生产方法主要有定向合成法和氯化苯副产品加工法,目前国外在定向连续合成生产领域取得了一些进展。
连续法生产工艺又分为两步连续氯化工艺和一步连续氯化工艺。
无论是联产法,还是苯的定向催化氯化法,在苯或氯苯的氯化过程中,由于第2个氯取代基占据的位置不同形成了邻、间、对3种二氯苯异构体,他们的沸点很接近,邻二氯苯和对二氯苯的相对挥发度仅为1.059,用常规的精馏方法很难对它们进行有效分离,间二氯苯和对二氯苯的分离难度更大,虽然它们的熔点相差较大,但由于存在两元和三元晶相共熔,单纯用结晶法也难以将它们彻底分离。
目前国外提出各种方法分离二氯苯混合物,归纳有如下分离方法:
①萃取蒸馏法;②分子筛吸附法;③冷冻结晶与共熔结晶分离法;④氯化分离法;⑤采用前4种方法相结合分离二氯苯混合物的方法。
由于各种原因,目前工业生产中采用多次精馏和结晶结合的方法分离混合二氯苯。
3.1.2多次精馏工艺存在的问题
目前工业生产中,普遍采用先精馏,分离氯化苯和混合二氯苯,然后采用多次精馏方法先将间、对二氯苯与邻二氯苯分开,然后采用结晶方法将间二氯苯与对二氯苯分开,再采用精馏法提取邻二氯苯,分离工艺如图8所示,工艺流程主要由三个塔(T-1、T-2、T-3)和结晶装置(T-4)构成,该过程的物料及组成情况见表1,从表1可知每生产一吨对二氯苯,所消耗总能量为8.12×106kJ/t,生产1t邻二氯苯需要能量为18.91×106kJ/t。
Q=W×(λ+C×Δt)1-1
表1的物料衡算表
流分
组成(质量分数)/%
流量/kg·h-1
间二氯苯
对二氯苯
邻二氯苯
1
0.0300
0.5500
0.4200
29.40
2
0.0345
0.6831
0.2824
21.43
3
0.0495
0.8978
0.0526
11.57
4
0.0168
0.4311
0.5521
9.86
5
0.2424
0.5048
0.2527
2.30
6
0.0016
0.9953
0.0031
9.27
7
0.0173
0.1921
0.7900
7.97
8
0.0344
0.3808
0.5848
3.98
9
0.0034
0.0015
0.9951
3.98
3.1.3萃取精馏和结晶结合分离混合二氯苯[4]
萃取精馏和结晶结合工艺如图9所示,萃取精馏塔(T-1)、溶剂回收塔(T-2)、结晶装置(T-3)及精馏塔(T-4)所需条件见表2所示,分离结果见表3所示。
萃取精馏结果表明,以二苯胺为萃取剂,采用萃取精馏法分离间二氯苯、对二氯苯和邻二氯苯溶液,当溶剂比为1:
1,回流比R=4时,原料液经萃取后,一次萃取可得到96.8%以上的邻二氯苯,再经精馏邻二氯苯含量可达到99.5%以上,得率可达到72%以上,同时得到99.8%以上的对二氯苯,对二氯苯得率达到83.5%,上述条件适宜工业化操作。
表2分离过程工艺条件
工艺参数
萃取装置(T-1)
再生塔(T-2)
精馏塔(T-4)
塔顶温度/℃
173.3~173.8
179.0~179.5
178.3~178.6
塔底温度/℃
203.1~205.6
226.2~207.9
180.6~181.2
回流比(R)
4
1~2
3
塔板数(N)
115
36
42
原料进料位置(NF)
103
17
21
萃取剂进料位置(NS)
5
-
-
表3萃取过程分离结果
流股
流速/g·h-1
含量(质量分数)/%
对二氯苯
间二氯苯
邻二氯苯
二苯胺
①
29.1
0.5500
0.0300
0.4200
-
②
18.2
0.8672
0.0411
0.0916
-
③
40.0
0.0056
0.0031
0.2638
0.7275
④
28.7
0.0010
0.0003
0.0014
0.9973
⑤
10.8
0.0205
0.0114
0.9681
-
⑦
4.8
0.5017
0.1529
0.3453
-
⑧
13.4
0.9980
0.0013
0.0007
-
⑨
2.1
0.0946
0.0532
0.8521
-
⑩
8.7
0.0023
0.0013
0.9961
-
3.1.42种方法对比
采用2种工艺分离二氯苯,分离过程能耗及得率见表4所示。
结果表明采用萃取精馏和结晶结合的方法与精馏和结晶结合方法相比,纯度较高,对二氯苯含量达到99.8%以上,对二氯苯和邻二氯苯的得率分别达到86%和80%以上。
采用萃取精馏和结晶结合方法生产1t邻二氯苯能耗低于精馏和结晶结合方法的71.3%。
表4萃取精馏和结晶结合的方法与精馏和结晶结合方法对比
萃取精馏和结晶结合
精馏和结晶结合方法
对二氯苯
邻二氯苯
对二氯苯
邻二氯苯
纯度/%
99.80
99.81
99.51
99.50
得率/%
86.8
80.6
57.07
32.12
能耗/106kJ·t-1
7.67
5.44
8.12
18.91
3.2在甲缩醛和乙醛酯合成与分离过程中的应用
3.2.1生产现状[5-6]
目前,国产的二甲氧基甲烷的浓度一般都在85%左右,少数几家厂家具备生产高纯度的二甲氧基甲烷(99%以上)。
国内的二甲氧基甲烷生产厂家较少(有供应者,多为转销),由于技术限制,生产的规模也较小(最大的产量为6万t/a)。
可以说国内市场上的二甲氧基甲烷产量,远远达不到化工市场的需求量,高浓度的二甲氧基甲烷还依赖于进口。
3.2.2连续反应精馏与精馏结合制备甲缩醛[7~11]
该工艺是将2个或多个且每个都充填固态酸性催化剂的反应器连接到单个蒸馏塔上[17],含有甲醇、甲醛和水的溶液在反应器中与固态酸性催化剂进行固、液接触,催化产生二甲氧基甲烷。
采用连续反应精馏法,DMM的转化率明显提高,固体酸催化剂可循环使用,但生产的混合物含DMM仅为45%~49%,需要采用其他方法进一步提高。
1—甲醇进料口;2—蒸馏塔;3—蒸发器;4—冷凝器;5—贮槽;6—甲醛进料口;7,8,9—固体酸催化剂
图10连续反应制备DMM流程图
3.2.3反应萃取精馏制备甲缩醛[12]
把原料①(甲醇和甲醛溶液)经过1计量泵经进料口进入萃取反应精馏塔,原料的进料口设在精馏塔的第27块塔板处;精馏塔经控温加热套加热控温,萃取剂和催化剂(合称试剂②)从精馏段以上加入,其进料口设在精馏塔的第5块塔板处。
精馏塔中低沸点的甲醇和甲醛气化成气体,在压力作用下向塔顶运动,与催化剂逆流充分接触生成产物DMM。
产物DMM和过量的反应物甲醇、微量的甲醛及水,经萃取剂萃取分离,产物DMM由于相对易挥发,从塔顶出料口排出。
塔顶气体经冷凝器冷凝,冷凝收集器收集得到③。
催化剂、萃取剂与少量的反应物甲醇、甲醛及水组成了④一同从塔底出料口出料,经提升泵,到达溶剂回收塔。
溶剂回收塔是1座精馏塔。
回收塔经控温加热套加热,低沸点物质⑤从塔顶出料口排出,经冷凝器冷凝后由冷凝收集器收集;萃取剂和催化剂塔底出料得到⑥,经循环泵送到催化剂与萃取剂进料口,循环利用。
配制原料甲醇、甲醛溶液(含甲醛37%~40%)质量比为0.9∶1;萃取剂甘油和原料的质量比为1.2∶1;催化剂对甲苯磺酸质量为原料的5%。
把原料(甲醇、甲醛)和试剂(甘油和对甲苯磺酸)均按流速质量流量15mL/min进入塔内,塔底以相同的流速出料,进入溶剂回收塔。
得到的产品中DMM含量达到99.5%以上,收率达到85%以上。
具体操作条件如表5,分离结果见表6所示。
表5反应萃取精馏工艺的操作条件
进料参数
反应萃取精馏塔
溶剂回收塔
塔底温度/℃
95~105
98~110
塔顶温度/℃
42~45
75~83
回流比R
3~4
3~4
塔板数N
35
29
反应物进料口(Nf)
5
16
萃取剂和催化剂进料口(NS)
27
-
表6反应萃取精馏分离结果
物
料
组成(质量分数)/%
二甲氧基甲烷
甲醇
甲醛
水
甘油
催化剂
①
-
45.0
25.0
30.0
-
-
②
-
-
-
-
96.2
3.8
③
99.57
0.41
微量
0.02
-
-
④
微量
5.9
1.7
22.3
67.4
2.7
⑤
16.0
7.7
微量
76.3
-
-
⑥
-
-
-
少量
96.2
3.8
表7分离过程工艺条件
条件
萃取精馏塔
再生塔
回收塔
塔顶/℃
88.5~89.5
78~101
78.3~78.6
塔底温度/℃
98~112
~183
99~101
回流比(R)
3~4
1~3
3~4
塔板数(N)
35
27
31
原料进料位置(Nf)
29
13
16
溶剂1进料位置(Ns1)
4
/
/
溶剂2进料位置(Ns2)
18
/
/
3.2.4复合萃取精馏制备乙醛酯[13、14]
经过反应精馏生产乙醛酯的含量见表2所示。
通过对回流比、溶剂进料比及进料位置的研究,当R=4、容积比例为1:
1:
1、进料位置为NF=29、NS1=4、NS2=18的条件下,塔顶DEM的含量可以达到99.6%以上。
经正交试验优化,分离过程中各塔温度、回流比、进料位置及塔板数取表7所示数值,可得到表8所示结果。
表8萃取过程分离结果
流速/kg·h-1
组成/%
DEM
乙醇
水
乙二醇
①
2.500
45.03
49.83
5.14
0.00
②
1.119
99.61
0.27
0.12
0.00
③
3.000
0.00
0.00
0.00
100.00
④
3.000
0.00
0.00
100.00
0.00
⑤
7.370
0.15
16.86
42.28
40.71
⑥
4.370
0.25
28.43
71.32
0.00
⑦
1.287
0.85
95.05
4.10
0.00
以Wilson方程为模型能较好地模拟DEM、乙醇和水复合萃取精馏分离结果;以水和乙二醇为萃取剂,采用复合萃取法分离DEM、乙醇和水溶液,当溶剂比为1:
1:
1,回流比R=4时,原料液经复合萃取后,一次萃取可得到99.6%以上的DEM,得率可达到99%以上,同时得到95%以上乙醇,模拟和实验结果最大相对误差≤1.1%。
工艺过程简单,适宜进一步放大试验研究。
4结论
本文系统阐明资源综合利用的途径,强调萃取精馏技术对工业生产及节能、减排的影响;列举萃取精馏技术在DEM的制备及混合二氯苯分离过程的应用,设计萃取精馏分离工艺方案,采用三对角距阵法模拟萃取分离结果,考察物料进料位置、进料量、回流比及塔板数对分离过程的影响,优化分离过程的工艺条件,实验和模拟计算结果为工业生产提供指导意见。
参考文献
[1]李光斌.浅述煤炭综合利用的应用前景[J].陕西煤炭,2008
(1):
76-78.
[2]官巧燕,廖福霖,罗栋.国内外生物质能发展综述[J].农机化研究,2007,(11):
20-24.
[3]顾正桂,章高健.乙醇浓缩和回收的萃取精馏工艺[J].化学工程.1995,23(5):
66-69.
[4]顾正桂,王琼.混合二氯苯的萃取结晶分离方法:
中国,200410065090.9[P].2006-05-31.
[5]赵鸣玉.甲缩醛和缩醛法[J].中国化工,1998(7):
45-48.
[6]顾正桂,管小伟,李伟敏.反应精馏和液液萃取结合制备高纯度