5PU球场施工方案篮球场解析.docx
《5PU球场施工方案篮球场解析.docx》由会员分享,可在线阅读,更多相关《5PU球场施工方案篮球场解析.docx(45页珍藏版)》请在冰豆网上搜索。
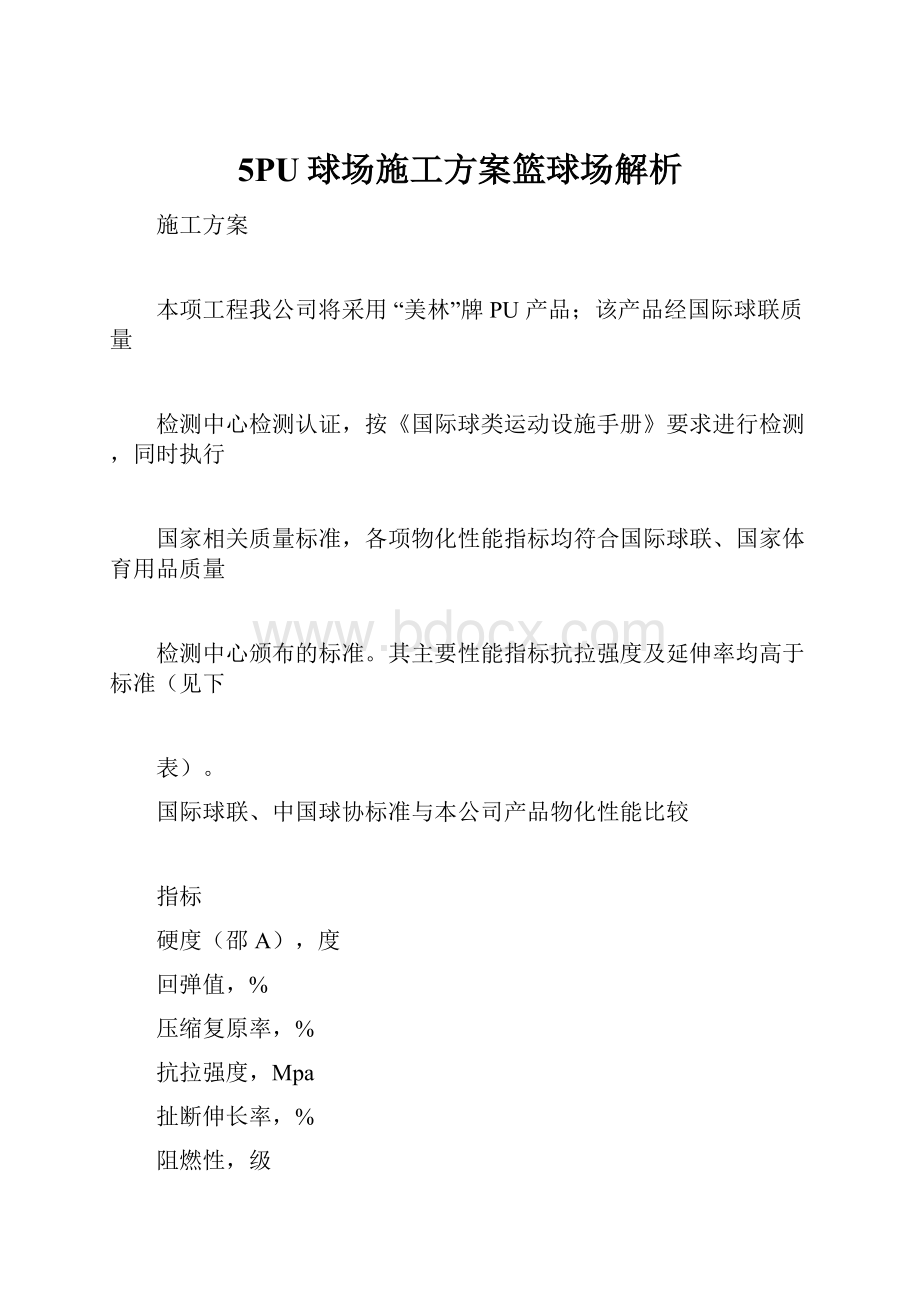
5PU球场施工方案篮球场解析
施工方案
本项工程我公司将采用 “美林”牌 PU 产品;该产品经国际球联质量
检测中心检测认证,按《国际球类运动设施手册》要求进行检测,同时执行
国家相关质量标准,各项物化性能指标均符合国际球联、国家体育用品质量
检测中心颁布的标准。
其主要性能指标抗拉强度及延伸率均高于标准(见下
表)。
国际球联、中国球协标准与本公司产品物化性能比较
指标
硬度(邵 A),度
回弹值,%
压缩复原率,%
抗拉强度,Mpa
扯断伸长率,%
阻燃性,级
抗滑值,EPDM
国际
45-60
≥20
0.65
≥70
1
50
国家
45-60
≥20
85-90
0.7
≥90
1
50-60
“美林”牌
45-60
≥30
≥98
1.3
≥95
1
55-60
实测值
45-60
≥25
≥95
≥0.75
≥90
1
55-60
该材料在抗老化、抗磨损和环保方面有出色的表现,并且在全自动的生
产条件下进行各成分配比,组分精确,性能稳定。
能够提供 10 年以上的寿
命。
保证了该场地的质量。
弹性 PU 球场施工是一个比较专业的施工工序,它的主导工序为:
施工
准备→碎石垫层施工→压实成型→水泥石粉施工→压实→养护→沥青混凝
土铺设→养护→塑胶面层铺设→验收。
一、碎石垫层的施工方法:
1
碎石底基层施工工艺流程:
施工放样→准备下承层→运输和摊铺未筛分
碎石→洒水使碎石湿润→运输和撒布石屑→拌和并补充洒水→整形→碾压
1、 准备工作
(1)准备下承层
① 基层的下承层是原夯实基土。
下承层表面应平整、坚实 ,没有任何松
散的材料和软弱地点。
② 下承层的平整度和压实度应符合规范的规定。
③ 用 12~15T 三轮压路机进行碾压检验(压 3-4 遍).在碾压过程中,如发
现土过干、表层松散,应适当洒水;如发生“弹簧”现象,应采取挖开
晾晒、换土、掺石灰或粒料等措施进行处理。
④ 对于底基层,根据压实度检查(或碾压检验)和弯沉测定的结果,凡
不符合设计要求的路段,必须根据具体情况,分别采用补充碾压、加厚
底基层、换填好的材料、挖开晾晒等措施,使达到标准。
⑤ 底基层上的低洼和坑洞,应仔细填补及压实。
底基层上的搓板和辙槽,
应刮除,松散处应耙松、洒水并重新碾压。
⑥ 逐一断面检查下承层标高是否符合设计要求。
下承层标高的误差应符
合规范要求。
(2)材料用量
① 计算材料用量,根据各段基层的宽度、厚度及预定的干压实密度,计
算各段需要的干集料数量。
再根据现场碎石的含水量以及所用运料车辆
的吨位,计算每车料的堆放距离。
② 在料场洒水加湿碎石,使其含水量较最佳含水量大 1%左右,以减少运
2
输过程中的集料离析现象。
(3)运输和摊铺集料运输:
① 集料装车时,应控制每车料的数量基本相等。
② 在同一料场供料的路段 ,由远到近将料按要求的间距卸置于下承层上 ,
卸料间距应严格掌握 ,避免料不够或过多 ,并且要求料堆每隔一不定期
距离留一缺口,以便施工。
在粗集料处于潮湿状态时,再摊铺细集料。
③ 集料在下承层上的堆置时间不宜过长。
运送集料较摊铺集料工序只宜
提前 1-2D。
(3)摊铺
① 摊铺前要事先通过试验确定集料的松铺系数 (或压实系数 ,它是混合
料的干松密度与干压实密度的比值).人工摊铺混合料时,其松铺系数约
为 1.4-1.5。
② 将集料均匀地摊铺在预定的宽度上,要求表面应平整。
③ 检验松铺材料的厚度 ,看其是否符合预计要求。
必要时应进行减料或
补料工作。
(4)碾压
摊铺整形后的基层,当碎石的含水量等于或略大于最佳含水量时,立
即用 12t 以上三轮压路机进行碾压。
碾压时,后轮应重叠1/2 轮宽;后轮必
须超过两段的接缝处。
后轮压完全宽时,即为一遍。
碾压一直进行到要求的
密实度为止。
一般需碾压6-8 遍。
压路机的碾压速度,头两遍以采用
1.5-1.7KM/H 为宜,以后用 2.0-2.5KM/H 为宜。
还应注意下列各点:
①两侧应多压 2-3 遍。
3
②碾压全过程均应随碾压随洒水,使其保持最佳含水量。
洒水量可参考
表 7-6 中数量并结合季节洒水,待表面晾干后碾压,但薄于 10CM 时不宜摊
铺后洒水,可在料堆上泼水,摊铺后立即碾压。
碾压直到要求的密实度。
③开始时,应用相对较轻的压路机稳压,稳压两遍后,即时检测、找补。
④碾压中局部有“软弹药”、“翻浆”现象,应立即停止碾压,待翻松晒
干,或换含水量合适的材料后再行碾压。
⑤两作业段的衔接处,应搭接拌和。
第一段拌和后,留 5-8M 不进行碾
压,第二段施工时,将前段留下未完成部分,重新拌和,并与第二段一起碾
压。
⑥严禁压路机在已完成的或正在碾压的路段上调头和急刹车。
二、石粉稳定层的施工方法:
水泥石粉稳定层施工工艺流程:
施工放样→准备下承层→运输未筛分石
粉→参入比例的水泥→洒水使石粉湿润→搅拌→运输和撒布现场→补充洒
水→整形→碾压
2、 准备工作
(1)准备下承层
⑦ 基层的下承层是原夯实基土。
下承层表面应平整、坚实 ,没有任何松
散的材料和软弱地点。
⑧ 下承层的平整度和压实度应符合规范的规定。
⑨ 用 12~15T 三轮压路机进行碾压检验(压 3-4 遍).在碾压过程中,如发
现土过干、表层松散,应适当洒水;如发生“弹簧”现象,应采取挖开晾晒、
换土、掺石灰或粒料等措施进行处理。
4
⑩ 对于底基层,根据压实度检查(或碾压检验)和弯沉测定的结果,凡
不符合设计要求的路段,必须根据具体情况,分别采用补充碾压、加厚底基
层、换填好的材料、挖开晾晒等措施,使达到标准。
⑪ 底基层上的低洼和坑洞,应仔细填补及压实。
底基层上的搓板和辙槽,
应刮除,松散处应耙松、洒水并重新碾压。
⑫ 逐一断面检查下承层标高是否符合设计要求。
下承层标高的误差应符
合规范要求。
(2)材料用量
③ 计算材料用量,根据各段基层的宽度、厚度及预定的干压实密度,计算
各段需要的干集料数量。
再根据现场碎石的含水量以及所用运料车辆的吨
位,计算每车料的堆放距离。
④ 在料场洒水加湿石粉,使其含水量较最佳含水量 11%左右,以减少运
输过程中的集料离析现象。
(3)运输和摊铺集料运输:
④ 集料装车时,应控制每车料的数量基本相等。
⑤在同一料场供料的路段 ,由远到近将料按要求的间距卸置于下承层
上,卸料间距应严格掌握 ,避免料不够或过多 ,并且要求料堆每隔一不定期距
离留一缺口,以便施工。
在粗集料处于潮湿状态时,再摊铺细集料。
⑥集料在下承层上的堆置时间不宜过长。
运送集料较摊铺集料工序只
宜提前 1-2D。
(3)摊铺
④摊铺前要事先通过试验确定集料的松铺系数(或压实系数,它是混合
5
料的干松密度与干压实密度的比值 ).人工摊铺混合料时 ,其松铺系数约为
1.4-1.5。
⑤ 将集料均匀地摊铺在预定的宽度上,要求表面应平整。
⑥检验松铺材料的厚度,看其是否符合预计要求。
必要时应进行减料或
补料工作。
(4)碾压
摊铺整形后的基层,当碎石的含水量等于或略大于最佳含水量时,立即
用 12t 以上三轮压路机进行碾压。
碾压时,后轮应重叠1/2 轮宽;后轮必须
超过两段的接缝处。
后轮压完全宽时,即为一遍。
碾压一直进行到要求的密
实度为止。
一般需碾压6-8 遍。
压路机的碾压速度,头两遍以采用
1.5-1.7KM/H 为宜,以后用 2.0-2.5KM/H 为宜。
还应注意下列各点:
①两侧应多压 2-3 遍。
②碾压全过程均应随碾压随洒水,使其保持最佳含水量。
洒水量可参考
表 7-6 中数量并结合季节洒水,待表面晾干后碾压,但薄于 10CM 时不宜摊
铺后洒水,可在料堆上泼水,摊铺后立即碾压。
碾压直到要求的密实度。
③开始时,应用相对较轻的压路机稳压,稳压两遍后,即时检测、找补。
④碾压中局部有“软弹药”、“翻浆”现象,应立即停止碾压,待翻松晒
干,或换含水量合适的材料后再行碾压。
⑤两作业段的衔接处,应搭接拌和。
第一段拌和后,留 5-8M 不进行碾压,
第二段施工时,将前段留下未完成部分,重新拌和,并与第二段一起碾压。
严禁压路机在已完成的或正在碾压的路段上调头和急刹车。
三、沥青砼施工方法:
6
(一)拌和设备
我公司采用市政公司沥青搅拌站供料,工作能力是 120M3/H 以上,能够
根据现场施工的进度,来组织调料及运输材料。
(二)摊铺设备
我公司购买了进口大型沥青摊铺机,摊铺宽度 3.5 米到 7 米,根据场地
的宽度可以自动伸缩,性能达到国家有关标准,保证场地的平整度。
(三)运输设备
车辆数量根据沥青砼搅拌场地与运动场的距离确定,车辆数量必须满足
拌和设备连续生产的要求,不因车辆少而临时停工。
车量数量可按下式计算。
N=α(t1+t2+t3)/T
(四)沥青砼拌和
1、一般要求
(1)试拌
沥青砼宜在拌和厂制备。
在拌制一种新配合比的砼前,或生产中断定了
一段时间后,应根据室内配合比进行试拌。
通过试拌及抽样试验确定施工质
量控制指标。
对间歇式拌和设备,应确定每盘热料仓的配合比。
对连续式拌和设备(对
不能保证均匀进料和连续计量或矿粉损失较多的连续式拌和设备,不得用于
沥青混凝土的拌制),应确定各种矿料送料口的大小及沥青和矿料的进料速
度。
沥青砼应按设计沥青用量进行试拌,试拌后取样进行马歇尔试验,并将
其试验值与室内配合比试验结果进行比较,检验设计沥青用量的合理性,必
7
要时可作适当调整。
要求沥青的马歇尔指标软化点在 45 摄氏度以上,延度
大于 100cm。
沥青碎石砼可按规定的沥青用量范围(见下表 -沥青混合料配比、含油
量,每次变动范围不超过±0.5%)进行试拌。
试拌后抽样检查其级配和沥青
用量,确定适宜的沥青用量。
A、粗料:
碎石:
石屑:
粗砂:
粉料=45:
20:
28:
7
筛径37.5 31.5 26.5 19.0 16.0 13.29.54.75 2.36 1.180.6
级配%10097.5 83.0 66.5 62.0 57.5 43.0 24.5 19.0 15.5 12.0
B、细料:
石屑:
粗砂:
粉料=54:
35:
11
筛径
级配%
13.2
100
9.5
97.5
4.75
65
2.36
43
1.18
30.5
0.6
27
0.3
16.5
0.15 0.075
11.5 5.5
C、沥青用量:
粗粒式的用油量 4.80-5.30%
细粒式的用油量 6.50-7.20%
确定适宜的拌和时间。
间歇式拌和设备每盘拌和时间宜为 30-60S,以沥
青混合料拌和均匀为准。
(2)沥青砼的拌制
根据配料单进行,严格控制各种材料用量及其加热温度。
拌和后的沥青
砼应均匀一致,无花白、无离析和结团成块等现象。
每班抽样做沥青砼性能、
矿料级配组成和沥青用量检验。
每班拌和结束时,清洁拌和设备,放空管道
中的沥青。
做好各项检查记录,不符合技术要求的沥青砼禁止出厂。
2、拌和
(1)材料供给
8
所用矿料符合质量要求,贮存量应为平均日用量的 5 倍,堆料场应加遮
盖,以防雨水。
研究表明:
矿料含水量的多少对设备生产能力的影响很大,
矿料的含水量大则意味着烘干与加热费时,生产能力降低,燃料消耗率增加。
例如干燥滚筒生产能力为 50-80T/H 时,含水量为 5%-8%的矿料,含水量每增
加 1%,干燥能力下降约 10%,每吨产品的燃油消耗率将增加 105。
矿粉和沥
青贮量应为平均日用量的 2 倍。
(2)拌和设备运行
起动前要拉动信号,使各岗位人员相互联系,确认准备就绪时才能合上
电闸。
对各组成分的起动,应按料流方向顺序进行。
待各部分空运转片刻,
确认工作良好时,才可开始上料,进行负荷运转。
通常用装载机将不同规格的矿料投入相应的料仓,在拌和设备运行中要
经常检查矿石料仓贮料情况。
如果发现各斗内的贮料不平衡时,应及时停机,
以防满仓或贮料串仓。
检查振动筛的橡皮减振块,发现有裂纹时,要及时更
换,贮料仓的存料要过半才可开始称量。
矿粉要根据用料情况上料,防止上
料过多或卡住机器。
防止沥青从保温箱中溢出,必要时可用工具在箱内搅动,
以免沥青溢出。
拌和设备在停机之前应先停止供给砂石料并少上矿粉,使滚筒空转
3-5min,待筒内出完余料再停止筒的转动。
在筒空转时还应加喷燃器的风门,
尽快驱除筒内的废气,并使筒冷却,然后关闭喷燃器的油门和燃油泵的总油
门。
停机后矿粉仓和矿粉升运机内不得有余料。
停机后矿粉仓和矿粉升运机
内不得有余料,在停止搅拌前应先停止喷沥青。
将进入搅拌器内的余料干搅
几分钟后放净,以便刷净搅拌器内的残余沥青。
9
3、 拌和质量检测:
(1)搅拌质量的直观检查
质检人员必须在料车装料过程中和开离拌和厂前往摊铺工地途中经常
进行目测。
仔细的目测有可能发现混合料中存在的某些严重问题。
沥青混合料生产的每个环节都应特别强调温度控制。
这是质量控制的首
要因素。
目测经常可以发现沥青混合料的温度是否符合规定。
料车装载的混
合料中有黄烟往往表明混合料过热,若混合料温度过低,沥青裹覆不够。
装
车将比较困难。
此外,如运料车上的沥青混合料能够堆积很高,则说明混合
料欠火,或混合料中沥青含量过低。
反之,如果热拌混合料在料车中容易坍
平(不易堆积),则可能是因为沥青过量或矿料湿度过大所致。
(2)拌和质量测试
2.1 温度测试
直观检验固然很重要,但检验人员必须进行测定。
沥青混合料的温度还
常在料车上测出。
较理想的方法是使用有度盘和铠装枢轴的温度计,将枢轴
从车箱一侧的预留孔中插入混合料中,使之达到足够的深度(至少 15CM),
混合料直接与枢轴接触,可测出料温。
2.2 沥青混合料的取样和测试
沥青混合料的取样与测试是拌和厂进行质量控制最重要的两项工作,取
样和测试所得到的数据,可以证明成品是否合格。
因此,必须严格遵循取样
和测试程序,确保试验结果能够真实反映混合料的质量和特性。
作为称职的
检验人员必须能采集有代表性的样品,进行现场试验室试验,并解释试验数
据。
10
2.3 检测记录
检测人员必须保留详细的检验记录。
这些记录是确定沥青混合料是否符
合规范要求。
因此,记录必须清楚、完整和准确。
这些记录还将成为施工和
工程用量的历史记录。
所以,检测记录也就成为日后研究和评价该项工程的
依据。
为了能够反映实际情况,这些记录和报告必须在进行所规定的试验或测
量的当时抓紧时间填写。
每项工程必须记日记。
应记录:
工程编号、拌和厂
位置、拌和设备的类型和型号、原材料来源、主要工作人员姓名以及其它数
据。
还应记录日期和当天的气象情况及拌和厂的主要活动和日常工作。
对异
常情况,特别是对沥青混合料可能产生不利影响的情况必须进行说明。
4、施工放样
施工放样包括标高测定与平面控制两项内容。
标高测定的目的是确定下
承层表面高程与原设计高程相差的确切数值,以便在挂线时纠正到设计值或
保证施工层厚度。
根据标高值设置挂线标准桩,藉以控制摊铺厚度和标高。
对无自控装置的摊铺机,不存在挂线问题,但应根据所测标高值和本层应铺
厚度综合考虑确定实铺厚度,用适当垫块或定位螺旋调整铺机就位,为便于
掌握铺筑宽度和方向,还应放出摊铺的平面轮廓线或设置导向线。
标高放样应考虑下承层标高差值(设计值与实际标高值之差)、厚度和本
层应铺厚度。
综合考虑后定出挂线桩顶的标高,再打桩挂线。
当下承层厚度
不够时应在本层内加入厚度差并兼顾设计标高。
如果下承层厚度够而标高低
时,应根据设计标高放样。
如果下承层的厚度与标高都超过设计值时,应按
本层厚度放样。
若厚度和标高都不够时,应以差值大的为标准放样。
总之,
11
不但要保证沥青砼面总厚度,而且要考虑标高不超出容许范围。
当两者矛盾
时,应以满足厚度为主考虑放样,放样时计入实测的松铺系数。
(五)摊铺作业
摊铺时应先检查摊铺机的熨平板宽度和高度时否适当,并调整好自动找
平装置。
摊铺时,石油沥青混合料温度不应低于 1000C,煤油沥青混合料不
应低于 700C。
摊铺厚度应为设计厚度乘以松铺系数,沥青混合料的松铺系数
通过试铺碾压确定,也可按沥青混凝土混合料:
1.15-1.35 取值,细料式沥
青混合料取上限。
摊铺后应检查平整度,发现问题及时修整。
雨季施工时,应注意气象预报,现场应缩短施工路段,各工序要紧密衔
接。
运料车和工地应备有防雨设施,并做好基层的排水工作。
下承层潮湿时,
不得摊铺沥青混合料,对未经压实而遭雨淋的沥青混合料,要全部清除,更
换新料。
(六)摊铺过程的质量检验及控制措施
1、质量检验
(1)沥青含量的直观检查。
如果混合料又黑又亮,料车上的混合料呈
圆锥状或混合料在摊铺机受料斗中蠕动时,则表明沥青含量正常;如果混合
料特别黑亮,料车上的混合料呈平坦状或沥青结合料从骨料中分离出来则表
明沥青含量过大(或骨料没有充分烘干,表面上看起来沥青太多);如果混
合料呈褐色,暗而脆,粗骨料没有被完全裹覆,受料斗中的混合料不蠕动,
则表明含量太少(或过热,拌和不充分)。
(2)混合料温度。
沥青混合料在正常摊铺和碾压温度范围内,往往冒出
淡蓝色蒸气,沥青混合料产生黄色蒸气或缺少蒸气说明温度过高或过低。
通
12
常在料车到达工地时测定混合料的温度,有时也在摊铺后测定。
每天早晨要
特别注意做这项检查,因此时下承层表层温度和气温都比较低。
平时只要混
料有温度较低现象或初次碾压,而压路机跟不上时,则应测定温度,测量铺
层的温度时,应将温度计的触头插进未压实的面层中部,然后把触点周围轻
轻用足踏实。
(3)厚度检测。
摊铺机在摊铺过程中,应经常检测虚铺厚度。
(4)表观检查。
未压实混合料的表面结构无论是纵向或横向都应均匀、
密实、平整、无撒裂,无波浪、局部粗糙、拉沟等现象,否则,应查明原因,
及时处理。
2、摊铺中的质量缺陷及防治措施
,
摊铺中常见的质量缺陷主要有:
厚度不准、平整度差(小波浪、台阶)
混合料离析,裂纹、拉沟等。
与这些质量缺陷相关的因素有:
机械本身的调
整、摊铺机的操作和混合料的质量等,见下表,为了防止和消除在施工中可
能发生的各种质量缺陷,应注意下列各点:
沥青路面施工缺陷的产生原因
铺面缺陷裂纹
拉沟 小波浪 混合料离析
原因
200号 以 下 石 料 过 多
混(0.074MM)
O
合温度不当O
料沥青含量过多或过少
矿粉含量不足
骨料的尺寸与摊铺厚度不协
调
O
O
O
砂未完全烘干
O
13
摊
铺
受料斗翼板上积料过多
受料斗两面三刀翼板翻动过
速
O
O
机
的
操
作
供料系统速度忽快忽慢
机械猛烈起步和紧急制动
摊铺速度快慢不匀
行走装置打滑
熨平板的工作仰角调整过量
O
O
O
O
O
O
摊
铺
机
的
振捣梁与熨平板的相互位置
调整不当
振捣梁、熨平板底面磨损
刮料护板安装不当
O
O
O
O
调各部分的驱动链条松紧未调
整好
发动机调速未调好
O
O
注 O 表示缺陷
(七)压实作业
1、压实程序
沥青混合料的压实应按初压、复压、终压(包括成形)三个阶段进行。
压路
机应以慢而均匀的速度碾压,其碾压速度应符合下表要求。
压路机碾压速度
压路机类型
适宜
初压
最大
适宜
复压
最大
适宜
终压
最大
钢筒式压路
机
轮胎压路机
1.5-2
-
3
-
2.5-3.5
3.5-4.5
5
8
2.5-3.5
4-6
5
8
14
54-54-52-35
(静压)(静压)(振动)(振动)(静压)(静压)
注:
静压是指关闭振动装置的无振动碾压
(1)初压
1.1 初压应在混合料摊铺后较高温度下进行,并不得产生推移、开裂,压
实温度可根据沥青稠度、压路机类型、气温、铺筑层厚度、混合料类型经试
铺试压确定,一般为 1100C-1300C(煤沥青混合料不高于 900C)。
1.2 压路机应从外侧向中心碾压。
相邻碾压带应重叠 1/3-1/2;轮宽,
最后碾压路中心部分,压完全幅为一遍,当边缘有挡板、路缘石、路肩等支
挡时,应紧靠支挡碾压。
当边缘无支挡时,可用耙子将边缘的混合料稍稍耙
高,然后将压路机的外侧轮伸出边缘 10CM 以上碾压。
也可在边缘先空出宽
30-40CM,待压完第一遍后,将压路机大部分重力位于已压实过的混合料面
上再压边缘,以减少向外摊移。
1.3 应采用轻型钢筒式压路机或关闭振动装置的振动压路机碾压 2 遍,
其线压力不宜小于 350N/CM。
初压的目的是整平和稳定混合料,为复压创造
有利条件,是压实的基础,所以,初压时应特别注意检查平整、路拱,必要
时予以适当调整。
1.4 碾压时应将驱动轮面向摊铺机,碾压路线及碾压方向不应突然改变
而导致混合料移位。
压路机起动、停止必须减速缓慢进行。
(2)复压
2.1 复压的目的是使混合料密实、稳定、成形,混合料的密实程度取决
于这一