1500m3高炉煤气净化系统设计.docx
《1500m3高炉煤气净化系统设计.docx》由会员分享,可在线阅读,更多相关《1500m3高炉煤气净化系统设计.docx(19页珍藏版)》请在冰豆网上搜索。
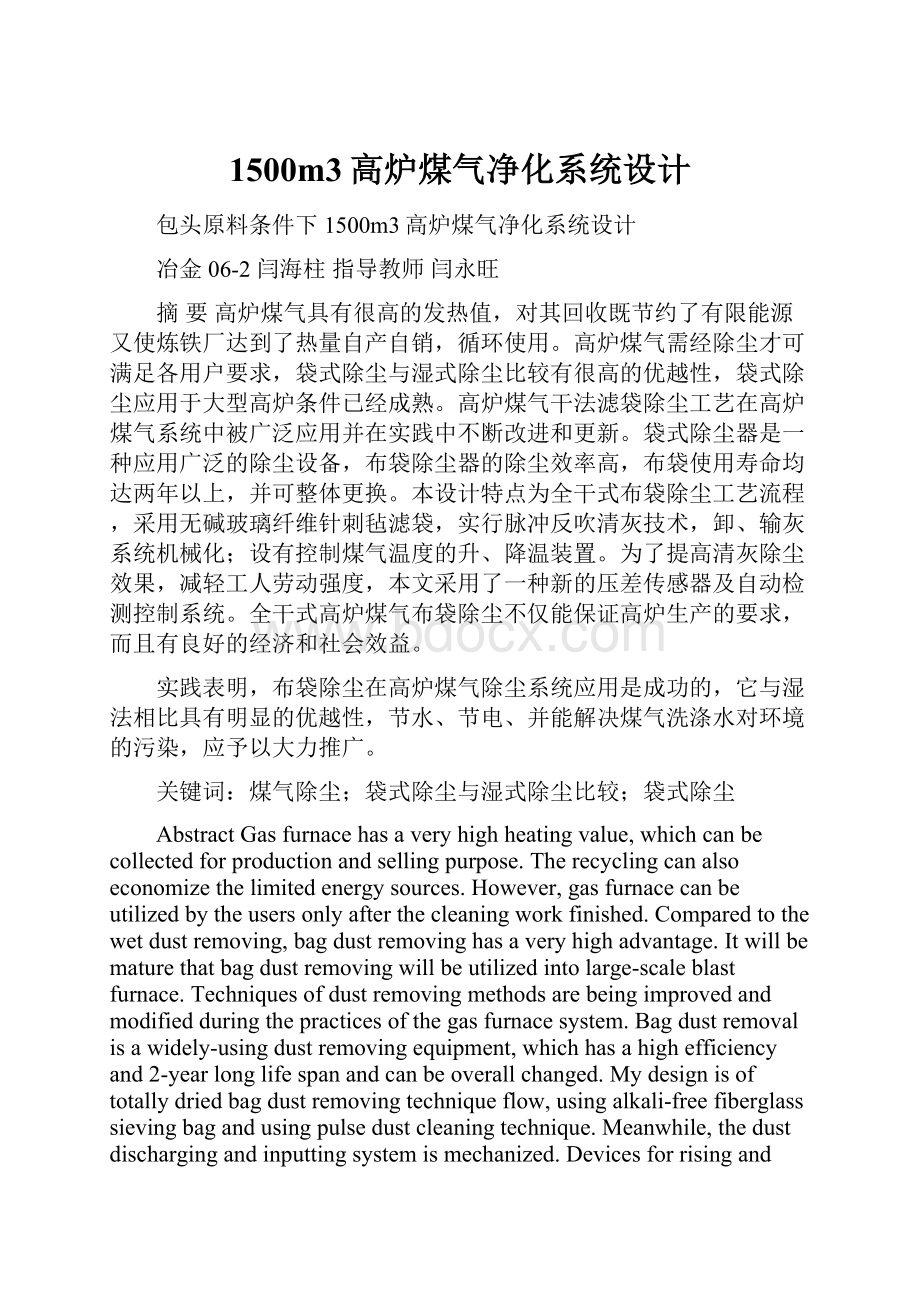
1500m3高炉煤气净化系统设计
包头原料条件下1500m3高炉煤气净化系统设计
冶金06-2闫海柱指导教师闫永旺
摘要高炉煤气具有很高的发热值,对其回收既节约了有限能源又使炼铁厂达到了热量自产自销,循环使用。
高炉煤气需经除尘才可满足各用户要求,袋式除尘与湿式除尘比较有很高的优越性,袋式除尘应用于大型高炉条件已经成熟。
高炉煤气干法滤袋除尘工艺在高炉煤气系统中被广泛应用并在实践中不断改进和更新。
袋式除尘器是一种应用广泛的除尘设备,布袋除尘器的除尘效率高,布袋使用寿命均达两年以上,并可整体更换。
本设计特点为全干式布袋除尘工艺流程,采用无碱玻璃纤维针刺毡滤袋,实行脉冲反吹清灰技术,卸、输灰系统机械化;设有控制煤气温度的升、降温装置。
为了提高清灰除尘效果,减轻工人劳动强度,本文采用了一种新的压差传感器及自动检测控制系统。
全干式高炉煤气布袋除尘不仅能保证高炉生产的要求,而且有良好的经济和社会效益。
实践表明,布袋除尘在高炉煤气除尘系统应用是成功的,它与湿法相比具有明显的优越性,节水、节电、并能解决煤气洗涤水对环境的污染,应予以大力推广。
关键词:
煤气除尘;袋式除尘与湿式除尘比较;袋式除尘
AbstractGasfurnacehasaveryhighheatingvalue,whichcanbecollectedforproductionandsellingpurpose.Therecyclingcanalsoeconomizethelimitedenergysources.However,gasfurnacecanbeutilizedbytheusersonlyafterthecleaningworkfinished.Comparedtothewetdustremoving,bagdustremovinghasaveryhighadvantage.Itwillbematurethatbagdustremovingwillbeutilizedintolarge-scaleblastfurnace.Techniquesofdustremovingmethodsarebeingimprovedandmodifiedduringthepracticesofthegasfurnacesystem.Bagdustremovalisawidely-usingdustremovingequipment,whichhasahighefficiencyand2-yearlonglifespanandcanbeoverallchanged.Mydesignisoftotallydriedbagdustremovingtechniqueflow,usingalkali-freefiberglasssievingbagandusingpulsedustcleaningtechnique.Meanwhile,thedustdischargingandinputtingsystemismechanized.Devicesforrisinganddroppingarealsoavailable.Toimprovethedustremovingefficiencyandalleviatethelaborintensity,thispaperadoptsasenseorganofpressdifferenceandautomaticcheckingcontrolmanagingsystem.Total-driedbagdustremovingcannotonlymeettherequirementsofblastfurnaceproductionbutalsobringafavorableeconomyandpublicbenefits.
Ithasbeenprovedthatbagdustremovingissuccessfullyappliedingasfurnacedustcleaningsystem.Thereisanobviousadvantagecomparingtothewetone.Duetoitswatersaving,electronicsavingandasolutiontotheenvironmentpollutedbythegasabstersion,itcanbewidelyusedcommonly.
KeyWords:
gasdustremoving;comparisionbetweenbagdustremovingandwetdustremoving;bagdusting
前言
高压脉冲喷吹类袋式除尘器(LNQM),此除尘器其清灰方式为高压氮气脉冲喷吹;过滤方式为外滤式,滤袋形状为圆筒形,滤料为无碱玻璃纤维针刺毡,进气方式为下进气;并有先进的箱体自动检漏、温度自动控制、灰位自动控制装置;并对炉尘进行综合的回收利用,以变废为宝、化害为利。
1炼铁工艺计算
吨铁煤气量:
1847.09m3/t;吨铁炉尘量:
76.99kg/t;炉顶煤气温度:
253。
72℃。
2重力除尘器及管道设计计算
2.1计算高炉煤气发生量与煤气含尘量
由前边工艺计算得,鼓风含氮量为76%,煤气含氮量55.90%,煤气正常温度250℃左右,炉顶正常压力0.2MPa(包钢),高炉利用系数为2.0t/m3·d,煤气含尘量为76.99kg/t-p,吨铁煤气量Vg=1847.09m3。
则高炉日产铁量:
高炉煤气发生量:
高炉煤气含尘量:
依照包钢1号1513m3高炉喉口直径6600mm,本设计选用喉口直径6600mm。
则炉喉的截面积S1=3.14×(6.6/2)2=34.19m2。
2.2煤气管道设计
2.2.1导出管设计计算
为了减少炉尘吹损,煤气导出管的煤气流速不宜太大,常为3~4m/s。
煤气导出口处的总截面积不应小于炉喉截面积的40%。
煤气导出管中心水平倾角一般为50°~53°,以使灰尘不致沉积堵塞而返回炉内。
设计的煤气导出管为四根,取煤气在煤气导出管内的流速ν导=3.5m/s,已知除尘器每小时过滤煤气总流量Q=230886.25m³/h。
则煤气导出管总截面积S导=Q/﹙ν导×3600﹚=18.32m2,取19m2。
则一根煤气导出管截面积=19/4=4.75m2
根据圆形面积公式可知煤气导出管直径D导=2460mm。
S导/S=19/34.19×100%=55.57%,满足设计要求。
煤气导出管中心水平倾角为53°
参考1513m3高炉重力除尘器的设计,导出管高度取h1=15300mm
2.2.2上升管设计计算
煤气上升管内的流速为6~8m/s,上升管总截面积为炉喉面积的25%~35%,上升管的高度应保证煤气下降管有足够大的坡度。
设计的煤气上升管为两根,取煤气上升管内的煤气流速ν上=7m/s。
则煤气上升管总截面积S上=230886.25/﹙7×3600﹚=9.16m2,取10m2。
则有S上/S1=10/52.78=29.25%,符合设计要求。
即有一根煤气上升管的截面积=10/2=5m2。
因此可知煤气上升管的直径D上为:
则
mm
上升管高度取h2=8900mm
下降管上管口中心线到上升管管顶距离取h3=2400mm
2.2.3下降管设计计算
为了防止煤气灰尘在煤气下降管道内沉积堵塞管道,煤气下降管内的煤气流速应大于煤气上升管内的煤气流速。
煤气下降管内的流速为6~9m/s,煤气下降管的中心线倾角应大于45°,以使灰尘能流入重力除尘器。
设计的煤气下降管为两根,取煤气下降管总截面积为煤气上升管总截面积的80%,煤气下降管的中心线倾角取45°。
煤气下降管总截面积S下=S上×80%=10×80%=8m2。
则下降管中的煤气流速ν下=Q/﹙S下×3600﹚=8.02m/s,满足设计要求。
则一根煤气下降管的直径D下为
2×
则
2256.89mm
2.3高炉炉顶管道设计参数
表2.1煤气流速表
煤气管道
煤气流速(标态)m/s
设计取值m/s
炉顶煤气导出管
3~4
V1=3.5
炉顶煤气上升管
6~8
V2=7
炉顶煤气下降管
6~9
V3=8.02
表2.2炉顶管道参数表
内径D(mm)
根数
夹角
煤气导出管
2460
4
煤气上升管
2524
2
煤气下降管
2256.892
2
煤气放散管
644.444
2
2.4重力除尘器的设计
2.4.1重力除尘器的设计要求
①除尘器直径必须保证煤气在标准状况下的流速不超过0.6~1.0m/s。
②除尘器直筒部分的高度,要求能保证煤气停留时间不小于12~15s。
③除尘器下部圆锥面与水平面的夹角应做成
。
④除尘器内喇叭口以下的积灰体积应能具有足够的富余量(一般应满足三天的积灰量)。
⑤除尘器下降管直径按煤气流速10m/s左右设计,一般为7~11m/s。
⑥除尘器阻力一般为150~390Pa
2.4.2重力除尘器部分设计参数选择
①所设计的重力除尘器要求除尘效率为80%。
②重力除尘器直筒直径必须保证煤气流速为0.8m/s。
③煤气能在沉降室停留时间为15s。
2.4.3重力除尘器设备尺寸计算
(1)每秒煤气量
:
(2)选择重力除尘器煤气入口管道直径为
,且煤气入口流速v0=10m/s,则由此可得:
mm
(3)由煤气在沉降室的停留时间为45s,煤气流速v1=0.5m/s,则重力除尘器直筒段的截面积:
S重=Q/v1=128.27m2
根据圆形面积公式可知重力除尘器内径:
=
mm
(4)除尘器直筒部分高度取H直筒=12000mm
(5)直筒部分体积V直=qt=64.135×15=962.025m3
(6)经参考潍坊1080m³高炉重力除尘器,知重力除尘器内径D重=11280mm,煤气出口管直径D出=2520mm,中心管直径D中=3500mm。
因此,设计的重力除尘器的煤气出管口
D出=﹙2520/11280﹚×10502=2346.19mm,也就是说半净煤气管道的直径为2346.19mm。
中心管直径D中=﹙3500/11280﹚×10502=3258.60mm,取3400mm。
中心管长度L中=13500mm
上锥体高度H上锥=﹙10502-3400﹚×0.5×tan50°=4231.92mm
下锥体高度H下锥=﹙10502-900﹚×0.5×tan50°=5721.61mm
除尘器的容积V=Q×t=230886.25÷3600×45=2886.075m³
式中:
V——除尘器容积,m³;
Q——处理气体量,m³/s;
t——气体在除尘器内停留时间,s,一般取30~60s,本次取45s。
除尘器的长度L=V/S=2886.075/128.27=22.5m
式中:
L——除尘器长度,m;
V——除尘器容积,m³;
S——除尘器截面积,m³。
(7)除尘器出口煤气流速V2,且煤气密度为
,则
24.4积灰量及灰斗设计
由前面工艺设计得知,吨铁产生的炉尘量76.99kg,高炉日产量30000t,则高炉每天产生炉尘量为76.99×3000=230.97t,设计重力除尘器除尘效率为80%,则重力除尘器除去的灰量为230.97×80%=184.776t。
炉尘的堆密度约为1.5t/m³,则炉尘体积V体积=184.776/01.5=123.184m³。
根据要求,设计灰斗满足容纳三天的积灰量,故灰斗容积应大于3×123.184=369.552m³。
最小灰斗高度满足4π·(D/2)2·h/3=3202mm
取排灰口直径径D排=900mm
2.4.5压力损失
由重力除尘器压力损失计算公式得:
Pa
2.4.6出口含尘浓度
2.4.7重力除尘器参数列
表2.3重力除尘器参数表
除尘器直径D
10502mm
直径部分高度h5
12000mm
除尘器入口管径d
2858.33mm
除尘器出口管径g
2346.19mm
灰斗下口口径f
900mm
灰斗倾角
灰斗容积V灰斗
>369.552m3
储灰能力
3天
出口含尘浓度C
8.3g/m3
除尘器压力损失
P
82.89Pa
除尘器除尘效率
80%
灰斗高度h4
5721.61mm
除尘器上截锥体高度h6
4231.92mm
3布袋除尘器的设计
3.1除尘器的选择设计
本设计中除尘器决定选择正压外滤式脉冲清灰除尘器,具体采用高压、外滤式、脉冲喷吹、下进气、圆袋形式。
在本设计中,要求对除尘器箱体采取各方面措施,如采用焊缝渗漏检验,严密性好的阀门和检修门,本体密封性检验等,以保证除尘器的漏风率控制在<2%的国际先进水平。
结合高炉炉尘的主要组成成分,根据实际情况选择脉冲清灰方式的过滤风速为u=35m/h。
本设计所选用的滤料为:
无碱玻璃纤维针刺毡,这种针刺毡的单纤维呈三维空间自由分布,具有多孔性,孔隙率高达80%,透气性极好,最大透气量约为800L/m2.s。
玻璃纤维针刺毡的外表面经常起绒,凸凹不平,各单纤维向外突出,形成了疏松多孔的表面,每根单纤维都是一个过滤单元,这样的表面面积较平面面积大得多,所以其透气性好,过滤负荷较高。
它的强度虽然比Nomex稍差,但耐热温度高,可达280℃,而且价格适中。
本设计选择滤袋尺寸大小为:
(d×L)=
(300×10000)mm
3.2过滤面积
过滤面积可以根据处理煤气量与煤气过滤风速来求得,即:
(3-1)
式中A——除尘器总的布带面积,m2;
qv——除尘器过滤煤气总流量,m3/h
——布袋允许的过滤负荷,高炉煤气除尘,过滤负荷一般为30~35m3/(m2
h)。
本次设计煤气量大,取过滤负荷35m3/(m2
h)。
m2
3.3滤袋及箱体个数
滤袋数量可由除尘器总过滤面积与单个滤袋的过滤面积求得
(条)
选择每个箱体布置滤袋条数为10×10=100条,则需箱体个数n为:
n=N/144=700.29/100=7.003(个),取8个。
由于布袋属于易损件,寿命一般为1.5年到2年,所以当某一布袋箱体内滤袋破损出现故障需要检修时,为了保证一个箱体的检修不至于过大地影响其它箱体正常工作,需要在布袋箱体进出口管上增设切断阀;并且在设备投资允许的条件下,应留两个布袋除尘器作备用,一个清灰,另一个检修。
现选择箱体个数n=10个,然后验算布袋总条数N为:
N=100×n=100×10=1000(条)
这样,除尘器就有足够的能力保证在箱体检修时仍然能正常工作。
3.4除尘器平面布置
(1)除尘器的边长计算
袋式除尘器有几个矩形箱体构成,当每个布袋箱体的布袋较多时,应分成几组布置,个组之间流出400mm的通道以便检修,边缘的空间为300mm。
采用正方形布置。
本设计的除尘器箱体为正方形,每个箱体分为4组,每组的布袋个数为25个,横纵各为5个,则箱体边长L为:
(3-2)
式中:
n——每组每列滤袋个数(条)
a——滤袋间的中心距a=d+
mm
N——沿各方向滤袋的组数(组)
S——每相邻两组滤袋最边上滤袋的中心距S=d+400mm
m——靠箱边滤袋中心至箱体内壁距离m=d/2+300mm
根据以上公式,具体布置参数为:
n=5条
N=2组
a=d+
=300+120=420mm
S=d+400=300+400=700mm
m=d/2+300=300/2+300=450mm
则除尘室每个箱体边长
L=(5-1)×4200×2+(2-1)×700+2×450=4960mm
(2)除尘器的总高度
H=L1+H1+H2+H3(3-3)
式中L1——滤袋层高度mm
H1——气体分配层高度mm
H2——灰斗高度mm
H3——灰斗排尘孔距地坪高度mm
参考包钢5号高炉(1500m3)箱体高度18000mm,取本设计的箱体高度为H=19000mm。
(3)箱体布置
由于本设计共有10个箱体,箱体单排布置采用单排一列式(实际中应更多的考虑现场的实际情况,若现场有一方形地带,则尽可能布置为并列式。
)为了适应今后高炉扩容和提高冶炼强度的需要,还应留有今后增加箱体的空间。
3.5总除尘效率
3.6反吹清灰设计
3.6.1清灰方式的选择
脉冲喷吹清灰方式的主要特点在于它是短期性的喷吹过程以及它年产生施加于滤袋内侧的相对较高的剩余压力。
脉冲喷吹的持续时间极短,一般只有0.02~0.3s,低压脉冲喷吹的喷吹压力一般为0.1~0.3MPa;而高压脉冲喷吹的喷吹压力一般为0.5~0.7MPa。
所以脉冲喷吹清灰可以在极短的时间内喷入大量的清灰气体。
脉冲反吹清灰属于高能清灰,由于反吹时间极短,压力大,以及气流的高速运动,使布袋充分的抖动,将网眼内粉尘迅速、有效地清落,从而恢复了布袋的透气性,因此,清灰效果好。
3.6.2压力损失
在本设计中,选择除尘器平均阻力为1200Pa左右。
清灰压差是干法滤袋除尘阻力的标志。
干法滤袋除尘器阻力主要取决于瓦斯灰在滤袋表面的厚度。
高炉煤气干法布袋除尘器在系统工作一段时间后,由于滤袋内侧的瓦斯灰膜增厚,除尘器阻力增加,当荒煤气入口压力与净煤气出口压力之差达到一定压力值时,就应对除尘器进行清灰操作。
本设计选择定压反吹即开始进行除尘器清灰操作的最大压力差为5000Pa,即当除尘器的箱体内外压力差超过5000Pa时,便对除尘器进行清灰,但是也应注意:
如果压力差始终达不到5000Pa,那么也要每两小时反吹一次。
3.6.3喷吹气体及参数的选择
1)喷吹气体
脉冲喷吹常用的气体有空气和高压氮气,但由于除尘器内煤气温度较高(约为200℃)而且钢铁厂中均有制氧设备这样在得到氧气的同时也分离出了大量的氮气,所以脉冲喷吹气体最好不采用空气喷吹而应采用喷吹高压氮气,以防随空气喷入的氧在高温下与煤气反应而发生爆炸。
因此本设计所使用的喷吹气体为:
高压
。
2)喷吹压力
喷吹压力既不能过高,也不能过低,过高易吹烂布袋,过低则吹不掉灰尘。
低压脉冲喷吹的喷吹压力一般为0.1~0.3MPa;而高压脉冲喷吹的喷吹压力一般为0.5~0.7MPa。
喷吹气流自上而下作快速运动,其冲击强度也迅速衰减,所以滤袋的长度受到一定的限制。
由于本设计选择的滤袋较长(10m),所以为保证喷吹气体与有足够的喷吹动量,并节省喷吹气体,设计采用高压喷吹方式。
因此本设计高压喷吹的压力选择为:
0.65Mpa。
3)清灰周期
本设计要设计的除尘器已知过滤风速为35m/h,入口含尘浓度为8.3g/m3,故可选择喷吹清灰周期T=120s,由于设计采用了定压差电控仪,使喷吹周期变为可调的,所以,实际的喷吹周期会在120s附近波动
4)喷吹时间
由于本设计采用高压氮气脉冲清灰方式,滤袋长度为10m,故选择喷吹持续时间为0.3s较为合适。
实际操作中可以在0.1~0.3s调整。
5)脉冲阀
一般来说,在大型外滤式脉冲布袋除尘器中,除尘器在进行脉冲反吹操作时,采取分排脉冲反吹,由一个脉冲阀控制10~12个滤袋。
结合本设计的实际情况,选择每10个滤袋共用一个脉冲阀,则脉冲阀总数量K=N/10=1000/10=100(个)。
6)压缩氮气消耗量
压缩氮气的消耗量与上述参数的选择有关,其计算公式为:
(3-4)
式中
——每台袋式除尘器每分钟压缩氮气消耗量m3
K——脉冲阀总数量(个)
T——脉冲周期min
——附加系数
=1.2
q——每个脉冲阀每次压缩氮气消耗量m3/阀次
各种参数选择为:
K=100
T=2min
q=0.02m3
=1.2
则压缩氮气的总消耗量为:
Q=1.2×100×0.02/2=1.2m3/min
3.7卸灰系统及操作步骤
1)卸灰系统的工艺流程为:
除尘器下灰斗→气动卸灰球阀→电动钟形卸灰阀→气动卸灰球阀→输灰管道→大灰仓→气动卸灰球阀→电动叶轮给料机→加湿装置→运灰罐车
2)操作步骤:
卸输灰系统的操作:
输灰时首先打开的煤气球阀(或氮气球阀)向输灰管道中输入输灰介质,然后依次打开气动球阀X、钟形卸灰阀、气动球阀Y、仓壁振动器,当下锥体下部热电偶检测温度开始升高并接近上部热电偶检测的温度时,可断定本箱体的灰已卸完,依次关闭仓壁振动器、气动球阀Y、钟形卸灰阀、气动球阀X,本箱体的卸输灰已完成。
按同样的操作顺序对每个箱体进行卸灰。
大灰仓中的灰位由安装在大灰仓上的三个射频导纳料位计测定,灰位(时间)到一定值时,通过气动卸灰球阀、电动叶轮给料机、加湿装置,由专用运灰罐车运出厂区。
气动卸输灰在布袋反吹后进行。
正常输灰采用高压净煤气,事故情况采用氮气输送。
用净煤气输灰时经过滤后的煤气送至低压净煤气管网,回收利用。
用氮气输灰时过滤后的气体也送至低压净煤气管网,因为在每个箱休卸灰后期氮气中也会含一部分煤气。
4除尘中的自动控制系统
4.1煤气温度自动控制
在不同的煤气温度条件下,煤气换热系统采取不同的工作状态:
①当高炉炉况正常,炉顶上升管荒煤气温度低于300℃时,荒煤气走旁
通管道而不经过换热器,布袋亦可正常工作。
②当炉顶上升管荒煤气温度高于350℃,出现高炉炉况不稳时,就必须采用管式换热器通以冷却水冷却,以保证将布袋除尘器的煤气温度控制在300℃以下。
4.2定压差电控仪
为了使布袋除尘器的实际压力值能很好地与设计值相符合,本设计采用了冶金部安全技术研究所研制的AL-3型电控仪采用定工作点的自动控制方式,使喷吹周期变为可调的,从而保证阻力损失为固定值。
该控制方式称为定压控制方式。
图4.1为AL-3型电控仪的工作方框图。
图4.1AL-3型电控仪的工作方框图
4.3脉冲控制仪
根据实际情况,本设计采用鞍山耐焦设计院研制的WHK型无触点脉冲电控仪。
这种电控仪由晶体管分离元件和集成组件组成,其主要技术性能如下:
①脉冲宽度可调范围为0.03~0.3s
②脉冲间隔可调范围为1~180s
③控制仪可在-20℃~50℃和相对湿度85%(28℃时)以下时正常工作
④允许交流电源电压波动范围为20V
10%
⑤总能耗约为40W
4.4箱体自动检漏
除尘检漏仪工作原理:
在流动粉体中,颗粒与颗粒,颗粒与布袋之间因摩擦碰撞产生静电荷,其电荷量的大小即反映粉尘含量的变化,检漏仪就是测量电荷量的大小变化,来判断布袋除尘系统是否有损漏的。
当出现下列情况之一时,就可判断该箱体布袋有破损:
(1)该箱体出口的自动检漏仪发出布袋破损声光报警信号;
(2)该箱体出口的流量显示值明显超出正常值。
操作人员必须认真详细记录检漏情况和时间,如果发现布袋有破损,应立即通知有关人员,停止该箱体运行。
5余压发电系统设计