多晶硅工艺生产技术葸国隆.docx
《多晶硅工艺生产技术葸国隆.docx》由会员分享,可在线阅读,更多相关《多晶硅工艺生产技术葸国隆.docx(48页珍藏版)》请在冰豆网上搜索。
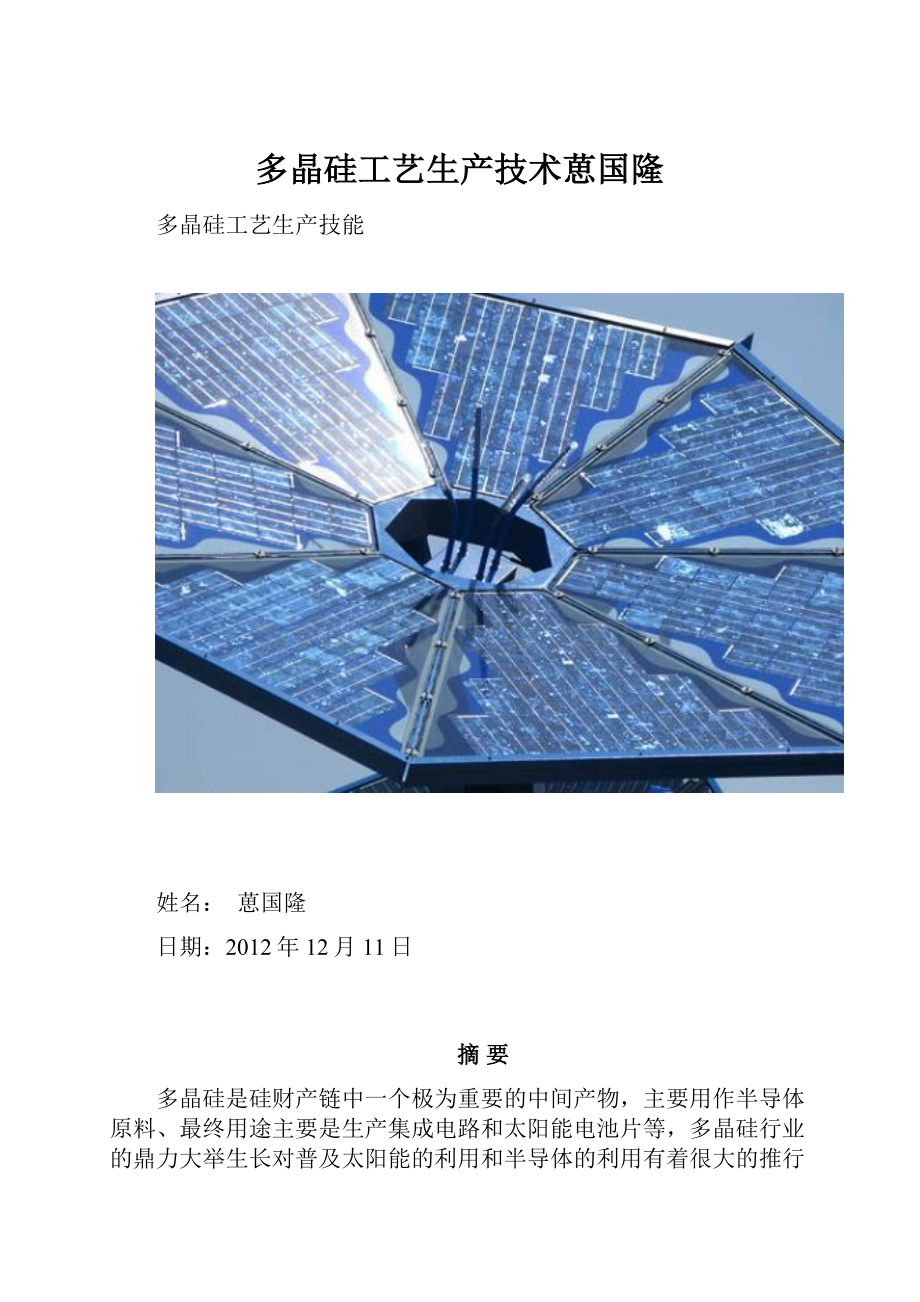
多晶硅工艺生产技术葸国隆
多晶硅工艺生产技能
姓名:
葸国隆
日期:
2012年12月11日
摘要
多晶硅是硅财产链中一个极为重要的中间产物,主要用作半导体原料、最终用途主要是生产集成电路和太阳能电池片等,多晶硅行业的鼎力大举生长对普及太阳能的利用和半导体的利用有着很大的推行动用。
本文主要是对多晶硅的工艺生产介绍,首先通过对多晶硅产物的认识和用途进行了开端的了解,再通过对多晶硅的生长历程和当前多晶硅生产的主流工艺进行介绍,进而通过对多晶硅生产历程各个工段的工艺和重点控制介绍的要领,详尽的论述了多晶硅的生产工艺之生产的闭环性和控制的庞大和稳定性。
通过这样的说明,使得各人最终了解多晶硅,认识多晶硅和多晶硅的生产工艺,从而了解多晶硅生产历程。
要害字:
多晶硅、改进西门子法、还原炉
第一章多晶硅的认识和产物的用途
一、什么是多晶硅
我们所说的多晶硅是半导体级多晶硅,或太阳能级多晶硅,它主要是用产业硅或称冶金硅(纯度98-99%)经氯化合成生产硅氯化物,将硅氯化物精制提纯后得到纯三氯氢硅,再将三氯氢硅用氢进行还原生成有金属光芒的、银灰色的、具有半导体特性产物,称为半导体级多晶硅。
二、什么是半导体
所谓半导体是界于导体与绝缘体性质之间的一类物质,导体、半导体与绝缘体的大概分别是以电阻率来分别的,见表1。
表1导体、半导体与绝缘体的分别
名称
电阻率(Ω.Cm)
备注
导体
<10-4
<0.0001
Cu,Ag,AL等
半导体
10-4~109
0.0001~1000000000
Si,Ge,GaAs等
绝缘体
>109
>1000000000
塑料,石英,玻璃,橡胶等
三、纯度表现法
半导体的纯度表现与一般产物的纯度表现是不一样的,一般产物的纯度是以主体物质的含量几多来表现,半导体的纯度是以杂质含量与主体物质含量之比来表现的。
见表2。
表2纯度表现法
1%
1/100
10-2
2N
百分之一(减量法,扣除主要杂质的量后)
1PPm
1/1000000
10-6
6N
百万分之一
1PPb
1/1000000000
10-9
9N
十亿分之一
1PPt
1/1000000000000
10-12
12N
万亿分之一
四、多晶硅产物的用途
半导体多晶硅自己用途并不大,必须要将多晶硅培育成单晶硅,经切、磨、抛制成硅片(又称硅圆片),在硅片上制成电子元件(分立元件、太阳能能基片、集成电路或超大范围集成电路),才气有用。
硅由于它的一些良好的半导体性能和富厚的原料,自1953年硅作为整流二极管元件问世以来,随着工艺技能的革新,硅的纯度不停的提高,目前已生长成为电子产业中应用最遍及的一种半导体质料。
在最初由于制造硅质料的技能问题,半导体多晶硅纯度不高,只能作晶体检波器(矿石收音机,相当于二极管).随着质料制造工艺技能的不停革新与完善,质料纯度不停提高,制造乐成种种半导体器件,从晶体管、整流元件、太阳能电池片到集成电路到大范围集成电路和超大范围集成电路,才使硅质料得到遍及的用途。
半导体多晶硅是单晶硅的要害原质料,制成单晶硅后通过切、磨、抛工序制成硅片,在硅片上进行半导体器件的制造,(通过扩散、光刻、掺杂、离子注入------等许多工序)即集成电路(管芯或称为芯片、基片)。
由于大范围集成电路和超大范围集成电路技能的突破,半导体器件得到飞速生长,在各行各业得到遍及的应用如军事、航天、航空、帆海和信息技能上等等。
第二章多晶硅的生产要领
半导体多晶硅的生产的起步在20世纪40-50年代,但发明硅的一些半导体特性是比力早的(1930年),多晶硅生产工艺的发明与完善经历了慢长时间的探索。
一、锌还原法(杜邦法)
美国杜邦公司于1865年发明
SiCL4+2Zn====Si+2ZnCL2900-1000℃
经过7-8年的探索,制得30-100Ω.cm电阻率的多晶硅样品。
二、四氯化硅氢还原法(贝尔法)
贝尔实验室于1930-1955年发明
SiCL4+H2====Si+4HCL1100-1200℃
在钼丝上沉积,然后将多晶硅剥下来拉制单晶硅,或在石英管内反响制得针状硅收集后拉制单晶硅,制得P型电阻率100-3000Ω.cm的单晶硅。
三、三氯氢硅热剖析法(倍西内法)
法国于1956年发明,
4SiHCL3====Si+3SiCL4+2H2900-1000℃
在钽管上沉积,然后将多晶硅剥下来拉制单晶硅,或在石英管内反响制得针状硅收集后拉制单晶硅,制得P型电阻率400-600Ω.cm的单晶硅。
四、三氯氢硅氢还原法(西门子法)
德国于1955-1957年发明
SiHCL3+H2====Si+3HCL1000-1100℃
在硅芯发热体上沉积多晶硅,纯度提高,多晶硅经区熔后基硼含量0.05PPB,P型电阻率数千到30000Ω.cm,寿命到达1000μS
五、硅烷热剖析法
SiH4====Si+2H2900-1000℃
六、改进西门子法
各国于1960年-1975年间不停革新与完善,是目前普遍接纳的工艺技能。
SiHCL3+H2====Si+3HCL1000-1100℃
在硅芯发热体上沉积多晶硅,纯度提高,硅、氯原料消耗大幅度地低落。
目前世界上生产半导体级多晶硅主要接纳此法。
第三章改进西门子法工艺
一、生长历程
所谓改进西门子法,即以原料(三氯氢硅)闭路循环为主。
由于西门子法生产多晶硅时,进入还原炉的三氯氢硅和氢气的混淆物是在流动状态下进行的,反响速度不快,一次硅的转化率只有15-25%,其余75-85%的高纯原料从还原炉尾气排出,已往没有接纳,而用水洗法处置惩罚后排入大气和河流。
称为原始的西门子法。
这是第一阶段。
厥后(1966年)接纳80℃的深冷接纳(干冰+酒精,后用-80℃的复叠式氟压机取代),把未反响的硅氯化物接纳下来,继而将氢(含有HCL)用碱洗法接纳其中的氢气,称为“湿法接纳”。
称为开端革新的西门子法,这是第二阶段。
这样原质料的利用率大幅度地提高,单耗低落,从1Kg多晶硅需用产业硅10Kg以上,变为需用5-6Kg产业硅,原料消耗淘汰了一半。
再厥后,接纳低温变压吸收、脱吸与吸附的工艺装置称为“干法接纳”,分别接纳氢气、硅氯化物和HCL,返回流程中循环使用,原质料进一步大幅度地低落。
1Kg多晶硅需用产业硅粉低落到1.5Kg,这是改进西门子法,称为第三阶段。
二、改进西门子法归纳起来有三大特点
1)接纳多对棒大型还原炉(硅棒对数从9对、12对到50对,硅芯长度从1.5米、2米到2.5米或2.8米);
2)还原炉尾气接纳“干法接纳”,接纳H2、HCL与硅氯化物;
3)四氯化硅氢化转化为三氯氢硅,再循环接纳利用。
三、工艺生产化学反响方程式
H2+CL2=2HCL
3HCL+Si=SiHCl3+H2
SiHCl3+H2=Si+3HCL
SiCl4+H2=SiHCl3+HCL
第四章多晶硅生产的工艺历程
一、合成部门
1、液氯汽化
1)工艺说明
液氯受热会迅速汽化,其蒸汽压随温度升高而增大,通过控制液氯的温度就可得到需要的汽化压力:
20℃
25℃
30℃
65℃
20℃左右。
2)流程简图
图1液氯汽化工艺流程简图
图2汽化器流程图
3)控制要点
A、为了满足后续工艺需要氯气的压力,控制液氯钢瓶汽化的热水温度是一个重点;
B、控制缓冲罐氯气出口压力,需要一个恒压。
2、HCL合成
1)工艺说明
从氢气制备与净化工序来的氢气和从合成气干法分散工序返回的循环氢气分别进入本工序氢气缓冲罐并在罐内混淆。
出氢气缓冲罐的氢气引入氯化氢合成炉底部的燃烧枪。
从液氯汽化工序来的氯气经氯气缓冲罐,也引入氯化氢合成炉的底部的燃烧枪。
氢气与氯气的混淆气体在燃烧枪出口被点燃,经燃烧反响生成氯化氢气体。
出合成炉的氯化氢气体流经空气冷却器、水冷却器、深冷却器、雾沫分散器后,被送往三氯氢硅合成工序。
为包管宁静,本工序设置一套主要由废气处置惩罚塔、碱液循环槽、碱液循环泵和碱液循环冷却器组成的含氯废气处置惩罚系统。
须要时,氯气缓冲罐及管道内的氯气可以送入废气处置惩罚塔内,用氢氧化钠水溶液洗涤撤除。
该废气处置惩罚系统保持连续运转,以包管可以随时吸收并处置惩罚含氯气体。
其反响可简写成下面的方程式:
H2+CL2=2HCL
2)流程简图
图3HCL合成工艺流程简图
图4HCL合成炉流程图
3)控制要点
A、氢气和氯气的配比。
B、HCL合成炉熄火连锁
C、HCL的点火装置
3、三氯氢硅合成
1)工艺说明
原料硅粉经吊运,通过硅粉下料斗而被卸入硅粉吸收料斗。
硅粉从吸收料斗放入下方的中间料斗,经用热氯化氢气置换料斗内的气体并升压至与下方料斗压力平衡后,硅粉被放入下方的硅粉供给料斗。
供给料斗内的硅粉用安装于料斗底部的星型供料机送入三氯氢硅合成炉进料管。
从氯化氢合成工序来的氯化氢气,与从循环氯化氢缓冲罐送来的循环氯化氢气混淆后,引入三氯氢硅合成炉进料管,将从硅粉供给料斗供入管内的硅粉挟带并输送,从底部进入三氯氢硅合成炉。
在三氯氢硅合成炉内,硅粉与氯化氢气体形成沸腾床并产生反响,生成三氯氢硅,同时生成四氯化硅、二氯二氢硅、金属氯化物、聚氯硅烷、氢气等产物,此混淆气体被称作三氯氢硅合成气。
反响大量放热。
合成炉外壁设置有水夹套,通过夹套内水带走热量维持炉壁的温度。
出合成炉顶部挟带有硅粉的合成气,经三级旋风除尘器组成的干法除尘系统撤除部门硅粉后,送入湿法除尘系统,被四氯化硅液体洗涤,气体中的部门细小硅尘被洗下;洗涤同时,通入湿氢气与气体打仗,气体所含部门金属氧化物产生水解而被撤除。
撤除了硅粉而被净化的混淆气体送往合成气干法分散工序化学方程式如下:
3HCL+Si=SiHCl3+H2
2)流程简图
图5三氯氢硅合成工艺流程简图
图6三氯氢硅合成炉流程图
图7除尘流程图
3)控制要点
A、自动加料控制;
B、集沉器自动吹扫和切换控制;
C、带滤器自动吹扫和切换控制;
D、合成塔的炉温控制;
E、洗涤塔塔温控制;
二、提纯部门
1、工艺说明
凭据进入精馏车间的物料来源的差别,精馏工艺也大抵分为以下几个功效块:
合成料提纯;还原接纳料提纯;氢化接纳料提纯;SiCl4综合利用;还可能有崎岖沸物的分散提纯。
合成料是含有多种杂质身分的混淆液,特别是其中的硼化合物、磷化合物、有机硅化合物和低分子有机物等较难分散,它们与SiHCl3的相对挥发度比力靠近,分散系数靠近1。
因此,这部门物料需用较多级的精馏塔进行连续精馏才气得到及格的产物。
历程主要包罗:
组分SiHCl3和SiCl4分散,硼磷和金属杂质的分散,精提纯SiHCl3或SiCl4。
还原接纳料是由未反响的高纯SiHCl3、反响副产物SiCl4等氯硅烷冷凝液组成的混淆物,其种种金属、非金属杂质含量较低。
因此,还原接纳料的提纯历程主要是分散SiHCl3中的SiCl4、SiH2Cl2、硼磷和金属杂质,其提纯工艺比合成料提纯要简朴。
氢化料的提纯与还原接纳料提纯相似,其提纯工艺比合成料提纯要简朴
2、流程简图
图8粗馏提纯工艺流程简图
图9合成精馏提纯工艺流程简图
图10还原精馏提纯工艺流程简图
图11氢化精馏提纯工艺流程简图
图12合成氯硅烷粗馏1级流程图
图13合成氯硅烷精馏1级流程图
3、控制要点
A、控制塔内压差恒定。
B、控制塔顶压力恒定。
C、控制回流比。
D、控制精馏塔釜、塔中和塔顶的温度。
三、氢化还原部门
1、还原工序
1)工艺说明
经氯硅烷分散提纯工序精制的三氯氢硅,送入本工序的三氯氢硅汽化器,被热水加热汽化;从还原尾气干法分散工序返回的循环氢气流经氢气缓冲罐后,也通入汽化器内,与三氯氢硅蒸汽形成一定比例的混淆气体。
从三氯氢硅汽化器来的三氯氢硅与氢气的混淆气体,送入还原炉内。
在还原炉内通电的炽热硅芯/硅棒的外貌,三氯氢硅产生氢还原反响,生成硅沉积下来,使硅芯/硅棒的直径逐渐变大,直至到达划定的尺寸。
氢还原反响同时生成二氯二氢硅、四氯化硅、氯化氢和氢气,与未反响的三氯氢硅和氢气一起送出还原炉,经还原尾气冷却器用循环冷却水冷却后,直接送往还原尾气干法分散工序。
还原炉炉筒夹套通入热水,以移除炉内炽热硅芯向炉筒内壁辐射的热量,维持炉筒内壁的温度。
出炉筒夹套的高温热水送往热能接纳工序,经废热锅炉生产水蒸汽而降温后,循环回本工序各还原炉夹套使用。
还原炉在装好硅芯后,开车前先用水力射流式真空泵抽真空,再用氮气置换炉内空气,再用氢气置换炉内氮气(氮气排空),然后加热运行,因此开车阶段要向情况空气中排放氮气,和少量的真空泵用水(可作为清洁下水排放);在停炉开炉阶段(约5-7天1次),先用氢气将还原炉内含有氯硅烷、氯化氢、氢气的混淆气体压入还原尾气干法接纳系统进行接纳,然后用氮气置换后排空,取出多晶硅产物、移出废石墨电极、视情况进行炉内超纯水洗涤,因此停炉阶段将产生氮气、废石墨和清洗废水。
氮气是无害气体,因此正常情况下还原炉开、停车阶段无有害气体排放。
废石墨由原生产厂接纳,清洗废水送项目含氯化物酸碱废水处置惩罚系统处置惩罚。
化学反响方程式如下:
SiHCl3+H2―→Si+SiCl4+HCl
2)流程简图
图14还原炉生产多晶硅工艺流程简图
图15806号炉调控柜控制画面
图16806号炉进料流程画面
3)控制要点
A、还原炉进料自动控制;
B、还原炉尾气压力自动控制;
C、还原炉电气控制(由PLC独立完成)
D、还原炉进料配比控制;
E、还原炉电流控制;
F、还原炉内温度和炉壁温度控制。
2、四氯化硅氢化
1)工艺说明
经氯硅烷分散提纯工序精制的四氯化硅,送入本工序的四氯化硅汽化器,被热水加热汽化。
从氢气制备与净化工序送来的氢气和从还原尾气干法分散工序来的多余氢气在氢气缓冲罐混淆后,也通入汽化器内,与四氯化硅蒸汽形成一定比例的混淆气体。
从四氯化硅汽化器来的四氯化硅与氢气的混淆气体,送入氢化炉内。
在氢化炉内通电的炽热电极外貌四周,产生四氯化硅的氢化反响,生成三氯氢硅,同时生成氯化氢。
出氢化炉的含有三氯氢硅、氯化氢和未反响的四氯化硅、氢气的混淆气体,送往氢化气干法分散工序。
氢化炉的炉筒夹套通入热水,以移除炉内炽热电极向炉筒内壁辐射的热量,维持炉筒内壁的温度。
出炉筒夹套的高温热水送往热能接纳工序,经废热锅炉生产水蒸汽而降温后,循环回本工序各氢化炉夹套使用。
化学反响方程式如下:
SiCl4+H2=SiHCl3+HCL
2)流程简图
图17四氯化硅氢化工艺流程简图
图18四氯化硅氢化流程画面
图19四氯化硅氢化炉调控柜控制画面
3)控制要点
A、氢化炉进料自动控制;
B、氢化炉尾气压力自动控制;
C、氢化炉电气控制(由PLC独立完成)
D、氢化炉进料配比控制;
E、氢化炉功率控制;
F、氢化炉炉内温度和炉壁温度控制。
四、接纳部门
1、工艺说明
1)还原炉尾气接纳装置(CDI-1)
从三氯氢硅氢还原工序来的还原尾气经此工序被分散成氯硅烷液体、氢气和氯化氢气体,分别循环回装置使用。
还原尾气干法分散的原理,从变温变压吸附器出口得到的高纯度的氢气,流经氢气缓冲罐后,大部门返回三氯氢硅氢还原工序到场制取多晶硅的反响,多余的氢气送往四氯化硅氢化工序到场四氯化硅的氢化反响;吸附器再生废气送往废气处置惩罚工序进行处置惩罚;从氯化氢解析塔顶部得到提纯的氯化氢气体,送往安排于三氯氢硅合成工序的循环氯化氢缓冲罐;从氯化氢解析塔底部引出的多余的氯硅烷液体(即从三氯氢硅氢还原尾气中分散出的氯硅烷),送入氯硅烷贮存工序的还原氯硅烷贮槽。
2)氢化炉尾气接纳装置(CDI-2)
从四氯化硅氢化工序来的氢化气经此工序被分散成氯硅烷液体、氢气和氯化氢气体,分别循环回装置使用
氢化气干法分散的原理和流程与三氯氢硅合成气干法分散工序十分类似。
从变温变压吸附器出口得到的高纯度氢气,流经氢气缓冲罐后,返回四氯化硅氢化工序到场四氯化硅的氢化反响;吸附再生的废气送往废气处置惩罚工序进行处置惩罚;从氯化氢解析塔顶部得到提纯的氯化氢气体,送往安排于三氯氢硅合成工序的循环氯化氢缓冲罐;从氯化氢解析塔底部引出的多余的氯硅烷液体(即从氢化气中分散出的氯硅烷),送入氯硅烷贮存工序的氢化氯硅烷贮槽。
3)合成尾气接纳装置(CDI-3)
从三氯氢硅氢合成工序来的合成气在此工序被分散成氯硅烷液体、氢气和氯化氢气体,分别循环回装置使用。
三氯氢硅合成气流经混淆气缓冲罐,然后进入喷淋洗涤塔,被塔顶流下的低温氯硅烷液体洗涤。
气体中的大部份氯硅烷被冷凝并混入洗涤液中。
出塔底的氯硅烷用泵增压,大部门经冷冻降温后循环回塔中用于气体的洗涤,多余部份的氯硅烷送入氯化氢解析塔。
出喷淋洗涤塔塔顶撤除了大部门氯硅烷的气体,用混淆气压缩机压缩并经冷冻降温后,送入氯化氢吸收塔,被从氯化氢解析塔底部送来的经冷冻降温的氯硅烷液体洗涤,气体中绝大部门的氯化氢被氯硅烷吸收,气体中残留的大部门氯硅烷也被洗涤冷凝下来。
出塔顶的气体为含有微量氯化氢和氯硅烷的氢气,经一组变温变压吸附器进一步撤除氯化氢和氯硅烷后,得到高纯度的氢气。
氢气流经氢气缓冲罐,然后返回氯化氢合成工序到场合成氯化氢的反响。
吸附器再生废气含有氢气、氯化氢和氯硅烷,送往废气处置惩罚工序进行处置惩罚。
出氯化氢吸收塔底溶解有氯化氢气体的氯硅烷经加热后,与从喷淋洗涤塔底来的多余的氯硅烷会合,然后送入氯化氢解析塔中部,通过减压蒸馏操纵,在塔顶得到提纯的氯化氢气体。
出塔氯化氢气体流经氯化氢缓冲罐,然后送至设置于三氯氢硅合成工序的循环氯化氢缓冲罐;塔底撤除了氯化氢而得到再生的氯硅烷液体,大部门经冷却、冷冻降温后,送回氯化氢吸收塔用作吸收剂,多余的氯硅烷液体(即从三氯氢硅合成气中分散出的氯硅烷),经冷却后送往氯硅烷贮存工序的原料氯硅烷贮槽。
2、流程简图
CDI-1,CDI-2,CDI-3三套系统处置惩罚的流程根本一样,在此只列出一副简图。
图20接纳工艺流程简图
图21还原尾气干法分散控制画面
图22还原尾气压缩机控制画面
图23还原尾气解析塔控制画面
3、控制要点
A、氢气压缩机连锁控制(由氢压机自带PLC独立控制);
B、解析塔温度、液位、压力自动控制;
C、吸附塔自动切换控制;
D、吸附塔出口尾气压力和吹扫压力自动控制;
E、吸附塔冷热水的温度控制。
五、公用帮助部门
各个分站都有自己的独立DCS控制系统或PLC控制系统,此处不做论述。
1、电解水制氢与氢气净化提纯;
2、空分制氮(生产中的掩护气体);
3、压缩空气制备(自控与工艺使用);
4、锅炉生产蒸汽(供精馏塔加热与制备蒸馏水);
5、冷冻站(供冷却水);
6、供配电站;
7、供水站(供自来水、脱盐水、循环水、冷冻盐水与超纯水);
8、三废处置惩罚:
建有尾气和废液处置惩罚装置和综合利用,可制备产业级的产物——氯化钙与硝酸钙。
第五章多晶硅工艺的主要控制
由于多晶硅工艺控制主要由单回路、串级回路和分程控制回路组成,庞大的联锁控制主要体现在还原氢化部门和尾气接纳吸附塔部门。
现将这两个庞大的联锁控制介绍如下:
一、还原炉的自动和联锁控制
还原炉流程图和调控柜控制画面:
图24还原炉流程画面
图25还原炉调控柜流程图
1)还原炉自动升电流、降电流
由于还原炉生产一炉多晶硅产物需要的周期是5~7天,电流需要从起步的20A升到最终的3000A,并且每个操纵员需要存眷8台还原炉,因此靠手动升电流和降电流是不可能完成,只能自动。
步伐如下:
图26还原炉升降电流步伐逻辑图
图27硅棒生长电流电压曲线图
2)还原炉停炉联锁
为了包管还原炉在生产历程中的稳定运行,其连锁掩护主要包罗有:
A、电气调控柜停止调功联锁
当还原炉生产硅棒产物历程中,若有硅棒裂纹、熔断器熔断大概电源妨碍,则连锁调控柜自动断电,还原炉停炉。
B、进料切断联锁
当还原炉调控柜一旦断电,就要切除进料切断阀,具体为切断氯硅烷和氢气的进口切断阀。
二、尾气接纳吸附塔的顺序控制
1)尾气接纳吸附塔流程和控制画面
图28吸附塔工艺流程图
图29吸附塔程控监督流程图
2)顺序控制时序图介绍
(看时序图请,前后两张并起来看)
图30程控时序图1
图30程控时序图2
3)吸附塔切换历程条件梯形图
图31梯形图——1
图32梯形图——2
图33梯形图——3
图34梯形图——4
图35梯形图——5
图36梯形图——6
4)步伐(部门)
(*此段步伐为步伐运行时,需要加载的阀门状态和设定参数变量,以及自界说的变量*)
SEQUENCECDI1SEQ(HPM;POINTCDI1SEQ)
LOCALCMD:
LOGICALATFL(001)--DCPOINTCONTROLFLAG
LOCALMSGA:
STRINGATSTR16
(1)--DCORRCPOINTERRORMSG
LOCALSPVALUE:
NUMBERATNN(01)--RCSPVALUE
LOCALOPVALUE:
NUMBERATNN(02)--RCOPVALUE
EXTERNALCDI1TS1,CDI1TS2,CDI1TS3,CDI1TS4,CDI1TS5,CDI1TS6,CDI1TS7,CDI1TS8
EXTERNALCDI1TS12,CDI1TS13,CDI1TS14,CDI1TS15,CDI1P1505SP,CDI1TS10,CDI1TS11
EXTERNALHS_1510,HS_1511,HS_1514,HS_1515,HS_1516,HS_1517,HS_1518,HS_1519
EXTERNALHS_1521,HS_1524,HS_1525,HS_1526,HS_1527,HS_1528,HS_1529,HS_1530
EXTERNALHS_1531,HS_1534,HS_1535,HS_1536,HS_1537,HS_1538,HS_1539,PIC_1505
EXTERNALTI_1512,ZSC_1510,ZSC_1511,TI_1522,TI_1532,TI_1509_1507,ZSC_1530
EXTERNALZSC_1520,ZSC_1521,ZSO_1511,ZSO_1524,ZSO_1531,TI_1641,FI_1504,TI_1651
EXTERNALPI_1510,PI_1520,PI_1530
EXTERNALPDISL_1530,PDISL_1531,PDISL_1520,PDISL_1521,PDISL_1511
EXTERNALCDI1A1,CDI1A2,CDI1A3,CDI1A4,CDI1A5,CDI1A6,CDI1A7,CDI1A8,CDI1A9,CDI1A10
EXTERNALCDI1A12,CDI1A13,CDI1A14,CDI1A15,CDI1A16,CDI1A17,CDI1A18,CDI1A19
EXTERNALCDI1A22,CDI1MA,CDI1CR,CDI1TR,CDI1TR1,CDI1TSA1,CDI1A20,C