尿素的工艺和职业危害教材.docx
《尿素的工艺和职业危害教材.docx》由会员分享,可在线阅读,更多相关《尿素的工艺和职业危害教材.docx(23页珍藏版)》请在冰豆网上搜索。
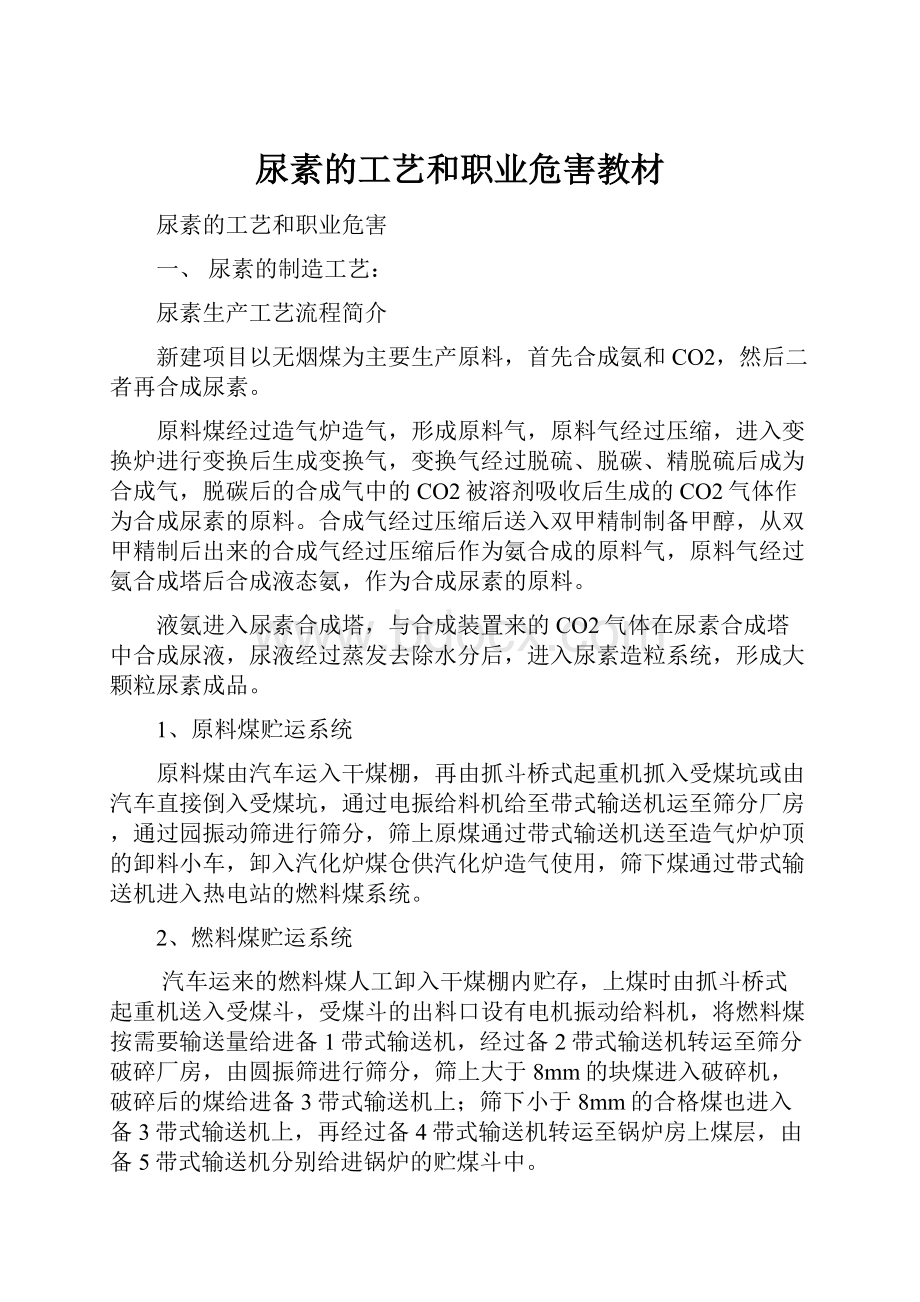
尿素的工艺和职业危害教材
尿素的工艺和职业危害
一、尿素的制造工艺:
尿素生产工艺流程简介
新建项目以无烟煤为主要生产原料,首先合成氨和CO2,然后二者再合成尿素。
原料煤经过造气炉造气,形成原料气,原料气经过压缩,进入变换炉进行变换后生成变换气,变换气经过脱硫、脱碳、精脱硫后成为合成气,脱碳后的合成气中的CO2被溶剂吸收后生成的CO2气体作为合成尿素的原料。
合成气经过压缩后送入双甲精制制备甲醇,从双甲精制后出来的合成气经过压缩后作为氨合成的原料气,原料气经过氨合成塔后合成液态氨,作为合成尿素的原料。
液氨进入尿素合成塔,与合成装置来的CO2气体在尿素合成塔中合成尿液,尿液经过蒸发去除水分后,进入尿素造粒系统,形成大颗粒尿素成品。
1、原料煤贮运系统
原料煤由汽车运入干煤棚,再由抓斗桥式起重机抓入受煤坑或由汽车直接倒入受煤坑,通过电振给料机给至带式输送机运至筛分厂房,通过园振动筛进行筛分,筛上原煤通过带式输送机送至造气炉炉顶的卸料小车,卸入汽化炉煤仓供汽化炉造气使用,筛下煤通过带式输送机进入热电站的燃料煤系统。
2、燃料煤贮运系统
汽车运来的燃料煤人工卸入干煤棚内贮存,上煤时由抓斗桥式起重机送入受煤斗,受煤斗的出料口设有电机振动给料机,将燃料煤按需要输送量给进备1带式输送机,经过备2带式输送机转运至筛分破碎厂房,由圆振筛进行筛分,筛上大于8mm的块煤进入破碎机,破碎后的煤给进备3带式输送机上;筛下小于8mm的合格煤也进入备3带式输送机上,再经过备4带式输送机转运至锅炉房上煤层,由备5带式输送机分别给进锅炉的贮煤斗中。
造气系统生产工艺流程及其职业病危害因素的分布
3、造气系统生产工艺
(1)造气
造气过程由吹风、上吹制气、下吹制气、空气吹净五个阶段组成。
粒度合格的原料块煤,经皮带运至各造气炉料仓,由自动加煤装置将煤连续均匀地加入造气炉内,与鼓风机鼓入的空气混合进行燃烧,同时将混有少量空气的过热蒸汽分别从炉底和炉上部通入炉内,与炽热的炭层发生反应,在造气炉内发生的主要化学反应有:
以上反应产生的混合气分别称为上行煤气和下行煤气,上、下行煤气进入造气余热回收器回收热量后,进入煤气冷却器,洗涤冷却至常温后送气柜。
造气炉产生的吹风气经炉上部进入旋风除尘器除尘后去吹风气回收系统。
(2)原料气压缩工艺
原料气压缩系统压缩机分为四级压缩系统
来自加压炉气柜的0.004Mpa(g)、40℃半水煤气经原料气压缩机的三个一级进气缓冲器后分别进入三个一级气缸进行压缩,从三个一级气缸排出的0.25Mpa(g)、153℃气体通过三个一级排气缓冲器后依次进入一级冷却器和一级分离器,温度降到40℃并分离冷凝液后经二级进气缓冲器分别进入二级气缸进行压缩。
经二级气缸压缩至0.73Mpa(g)、122℃的气体依次经二级排气缓冲器、二级冷却器和二级分离器后通过三级进气缓冲器进入三级气缸进行压缩。
经三级气缸压缩1.8Mpa(g)、131℃的气体依次经三级排气缓冲器、三级冷却器和三级分离器后通过四级进气缓冲器进入四级气缸进行压缩。
经四级气缸压缩的3.55Mpa(g)、131℃的气体依次经四级排气缓冲器、四级冷却器和四级分离器温度降到40℃并分离冷凝液后送至变换工序。
(3)吹风气回收
吹风气回收是合成氨达到蒸汽自给必须实施的一项节能措施。
吹风气主要收集自造气炉,由造气炉来的吹风气以及氢氨回收等回收来的吹风气与热空气充分混合后,于燃烧炉中燃烧,产生高温(800~950℃)烟气,烟气从燃烧炉下部出口经高温空气余热器、高压蒸汽过热器吸收部分余热后到余热锅炉加热汽包内的软水产生饱和蒸汽,最后由引风机引至主烟囱排出。
余热锅炉产生的饱和蒸汽,经高压蒸汽过热器加热升温后,送至高压蒸汽管网共发电使用。
4、变换系统生产工艺
(1)变换
来自原料气压缩的压力3.55Mpa(g),温度40℃的半水煤气进入气气换热器换热后进入第一混合器,与中压蒸汽混合升温至反应温度,进入第一变换炉进行变换反应,主要化学方程式为:
出第一变换炉的变换气经中压废热锅炉回收热量产生中压蒸汽,然后再经气气换热器进一步降低温度,进入第二混合器配入一定量的蒸汽后进入第二变换炉。
出第二变换炉的变换气中CO降至2%,温度265℃,变换气再经过中压废热锅炉、气气换热器、混合器回收热量,经水冷器将温度降至40℃,经分离器分离冷凝液后进入变换气脱硫工序。
(2)变换气脱硫
来自变换工段的变换气,进入脱硫塔的下部,与塔顶喷淋而下的脱硫贫液逆流接触,变换气中的H2S被吸收。
出塔变脱气中的H2S含量约20mg/Nm3,温度40℃,经变脱气分离器分离掉夹带的栲胶溶液后,进干法脱硫塔进一步脱硫后,变脱气中的H2S≤2ppm后,送往脱碳装置。
从脱硫塔顶进入的脱硫贫液吸收了变换气中的H2S后,富液从塔底排出,首先经过涡轮机回收静压能后进入喷射氧化再生槽顶的喷射器口,与自吸的空气在喷射器混合,形成一股射流,进行强化氧化反应,然后进入喷射氧化再生槽,这时硫泡沫及溶液从喷射再生槽底迅速返上。
在喷射氧化再生槽内,氧化浮选出的硫泡沫自流入硫泡沫槽,由硫泡沫泵加压送入熔硫釜连续熔硫,熔硫釜排出的清液进入溶液
缓冲槽降温后返回贫液槽,经贫液泵加压到4.0Mpa后分别送入脱硫塔循环喷淋脱硫。
熔硫釜底部排出物为硫磺,凝固后即为硫膏,硫膏外卖销售。
各排出点排出的溶液均收集于低位槽。
(3)NHD脱碳
来自变换气脱硫工段的变脱气首先进入气体换热器使其温度降至17℃,经原料气分离器进入脱碳塔底部。
变脱气由下而上与从塔顶下来的NHD溶液逆流接触,气体中的CO2被溶剂吸收。
从塔顶出来的脱碳气含CO2<0.38%,温度-2℃。
经脱碳气分离器除去少量夹带的NHD雾沫后,脱碳气进入气体换热器换热,温度升至30℃,送入精脱硫工段。
从脱碳塔顶进入的贫液在塔内吸收CO2后,富液由脱碳塔底部引出,进入水力透平回收静压能。
回收能量后的富液进入高压闪蒸槽,部分溶解的CO2和大部分H2在此解吸出来,即高压闪蒸气,送回原料气压缩机三段入口,作原料气。
从高压闪蒸槽底部出来的溶液减压进入低压闪蒸槽。
此时,大部分溶解的CO2气被解吸出来,经气体换热器回收冷量后大部分送往尿素工段作为尿素原料,其余就地放空。
从低压闪蒸槽底部出来的溶液经富液泵提压后,其中一少部分溶液流经溶液过滤器滤除固体杂质。
大部分溶液送入气提塔。
溶液自上而下与塔底送入的气提空气逆流接触进行传质传热,此时溶液中所吸收的CO2被空气气提出来。
解吸气从塔顶引出,经空气换热器换热后,引至塔顶约50m高度放空。
气提空气由空气鼓风机经空气过滤器从大气吸入。
先通过空气冷却器冷却并在空气水分离器中将冷凝下来的水分离掉,进入气提塔底部去气提含CO2的富液。
最后从气提塔顶部由空气鼓风机引出。
NHD溶液具有吸水性,它将原料气和气提空气中的水份吸收而使溶液中水含量积累增高,当NHD溶液含水超过3%(wt)就会降低其吸收CO2性能。
因此需要抽出部分溶液进行脱水。
从富液泵出口
引出部分溶液,经过溶液换热器换热后进入脱水塔。
出脱水塔顶部气相经脱水塔水冷器冷凝,进入冷凝液贮槽后,不凝气放空,冷凝液用泵打至水处理系统。
从脱水塔底部引出的溶液已脱水,经过溶液换热器换热降低温度后送至地下槽。
脱水所需热源由脱水搭内的蒸汽盘管提供。
系统中各排液导淋回收的NHD溶液经过排液总管流入地下槽,存入溶液贮槽,并通过补液泵补入气提塔,保持系统各处的正常液位。
脱碳工艺流程见图3-9。
(4)精脱硫
来自脱碳装置的脱碳气,首先进入气液分离器,分离掉夹带的液滴后,进入精脱硫塔,在该塔脱除H2S。
然后气体进入合成气压缩工段。
(5)合成气压缩
来自精脱硫工序的温度40℃、压力3.0Mpa的精脱气与来自氢氨回收工序的氢气一起进入本工序,经一段进气分离器分离出夹带的液滴后进入合成气压缩机低压缸。
精脱气经一段压缩后,送往双甲精制工序。
来自双甲工序的温度6℃、压力7.7Mpa的精制气,进入合成气压缩机的高压缸,经七级压缩后在缸内与氨合成工序来的循环气混合加压至14.3Mpa,75℃后,送至氨合成工序。
5、甲醇合成系统
(1)双甲精制
来自精脱硫装置的精脱气,其总硫小于0.1ppm,补入氢回收装置来的氢回收气,与分子筛再生气一并进入合成气压缩机低压缸,压缩至7.9MPa,出口温度约为168℃,进入双甲精制装置。
新鲜合成气首先进入第一进出口换气器预热至230℃,再进入等温列管式第一甲醇塔.合成塔壳侧副产2.7MPa的中压饱和蒸汽,并入中压蒸汽管网。
出第一甲醇塔的合成气进入第一进出口换热器,
再进入脱盐水预热器回收热量后,进入第一水冷器进一步冷却至40℃,进甲醇分离器分离出液体粗甲醇。
甲醇分离器出口的合成气进入第二进出口换热器壳侧,预热后进入第一蒸汽加热器加热至220℃后,进入绝热式固定床第二甲醇塔。
出第二甲醇塔的气体经过第二进出口换热器冷却至75℃后,进入第二水冷器进一步冷却至40℃后,在甲醇水洗塔塔底分离出粗甲醇。
从甲醇精馏装置常压塔底来的废水或界外来的脱盐水经废水加压泵加压后送入甲醇水洗塔。
出甲醇水洗塔的合成气进入甲烷化进出口换热器,预热至280℃,进入第二蒸汽加热器加热至310℃,入绝热式固定床甲烷化塔。
出甲烷化塔的合成气进入甲烷化进出口换热器壳侧冷却至88℃,再进入最终水冷器进一步冷却至40℃后,经氨冷器冷至8℃,进入气液分离器分离出液相水。
出气液分离器的气体进入分子筛干燥净化系统。
甲醇分离器和甲醇水洗塔来的粗甲醇合并后减压送入粗甲醇闪蒸槽,闪蒸后粗甲醇送精馏装置制得产品精甲醇。
闪蒸气并入可燃料气管网送吹风回收装置。
(2)分子筛干燥
来自双甲合成含有H2、N2、CH4、Ar及微量H2O、CO、CO2,温度为8℃得新鲜合成气进入分子筛干燥净化系统。
用于分子筛干燥系统再生的气体取自净化后的新鲜合成气,其量为总新鲜气的4%。
再生气经调节阀减压后并由再生气加热器加热至250℃后,进入分子筛干燥器,对其进行再生。
再生后的气体经再生气水冷器冷至40℃后返回合成气压缩机低压缸入口加以回收利用。
(3)甲醇精馏
从甲醇合成工段来的粗甲醇,与闪蒸槽来的蒸汽冷凝液在粗甲醇换热器中换热,达到70℃左右进入预精馏塔(简称预塔)中上部进行蒸馏反应。
而冷凝液温度降至84℃,与加压塔预热器来的蒸汽冷凝液汇合,一起进入冷凝液冷却器冷却至60℃后,进入冷凝液槽,经冷凝液泵加压返回脱盐水站。
从预塔塔顶出来的馏分经预塔冷凝器Ⅰ冷凝后,用预塔回流泵加压后送至预塔塔顶回流。
未冷凝的轻组分及不凝气体经气液分离器分离后至吹分气回收系统或高空排放,气液分离器回收的甲醇液自流入地下槽。
从预塔塔底出来即为脱除轻组分后的预后甲醇,温度为85℃,用预后甲醇泵抽出,送至加压塔预热器加热至110℃后送入加压塔中下部,塔底有再沸器加热。
加压塔上部侧线采出精甲醇,经加压塔冷却器冷却后送至精甲醇中间槽。
从加压塔塔顶出口的甲醇蒸汽进入常压塔,在常压塔冷凝再沸器中冷凝,释放的热用来加热常压塔中的物料。
常压塔顶部出来的甲醇蒸汽经常压塔冷凝器冷却后,进入回流槽;塔底液相由常压塔回流泵引至塔底回流;未冷凝的轻组分经常压塔液封槽后排入大气。
常压塔的回流液中采出精甲醇,经常压塔精甲醇冷却器冷却后送精甲醇中间槽。
常压塔的中下部有温度为83℃杂醇采出,主要成分为异丁基油,经异丁基油冷却器冷却后送异丁基油槽,经异丁基油泵打入甲醇罐区的杂醇罐贮存。
需装车外运时,开启杂醇装车泵,杂醇通过汽车鹤管输送至汽车槽车外运。
精甲醇中间槽的精甲醇经分析合格后,通过精甲醇泵送入到甲醇成品罐区贮存;不合格的甲醇通过精甲醇泵送到粗甲醇贮槽。
需装汽车外运时,开启甲醇装车泵,甲醇通过汽车鹤管输送至汽车槽车外运。
来自各个排放点的污甲醇排入到地下槽,经地下槽液下泵送入甲醇缓冲槽。
常压塔底部排除的废水经残液冷却器冷却至40℃,由残液泵升压后送往双甲精制工序。
6、氨合成系统
(1)氨合成
来自双甲精制的合成气,进入合成气压缩机高压缸加压后,与来自高压氨分离器的循环气在高压缸加压后循环段内混合,经循环段压缩至14.2MPa温度74.3℃,然后进入气气换热器被加热到208℃,进入氨合成塔。
从合成塔出来的气体,氨含量约为16.92%,温度为424℃,经废热锅炉和锅炉给水预热器回收热量后,气体被冷却到243.5℃。
锅炉补给水首先进入锅炉给水预热器,加热至204℃后进入废热锅炉,在此吸收出塔气热量,所产蒸汽并入中压蒸汽管网。
出锅炉给水预热器的气体进入气气换热器、水冷器进一步冷却,然后通过冷交换器与来自高压氨分离器的循环气进行热交换后,气体被冷却至28.6℃,依次再进入第一氨蒸发器,第二氨蒸发器使气体温度降至-10℃,产品氨被冷凝下来。
合成气与液氨的混合物进入高压氨分离器,在这里液氨大部分被分离出来,一小部分气体离开高压氨分离器进入冷交换器,被加热至35.5℃,部分作为驰放气送回氢氨回收装置,部分进入循环气压缩机即合成气压缩机高压缸最后一段。
高压氨分离器送出的液氨进入中压氨分离器并被减压至2.2MPa,溶解在液氨中的大部分气体被闪蒸出来,闪蒸气送往氢氨回收。
-10℃的液氨自中压氨分离器分离出来后,进入液氨换热器,与来自冷冻站的液氨换热,温度升至约30℃,送往氨库。
来自冷冻站40℃的液氨经液氨换热器降至0℃,送往第一氨蒸发器,第一氨
蒸发器底部液氨送往第二氨蒸发器,两台氨蒸发器顶部气氨分别送往氨压缩机。
第一氨蒸发器。
第二氨蒸发器、高压氨分离器、中压氨分离器的底部排污送至排污罐,直接加入低压蒸发,进行高点排放。
(2)氢氨回收
两台高压水泵将脱盐水输送至高压水洗塔顶部,洗涤原料气中的氨。
来自氨合成的驰放气,进入高压水洗塔,与脱盐水逆流接触洗涤,以使出塔的气体中氨浓度小于10ppm。
驰放气从高压塔塔顶出来后称原料气(即水洗后的驰放气),原料气进入气液分离器,将雾除去后进入原料气加热器,加热后进入膜分离器。
原料气分为渗透气和非渗透气,渗透气送入两套合成氨系统回收;非渗透气送至吹风气回收系统回收。
氢氨回收工艺流程见图3-14。
7、尿素合成系统
尿素合成的原料为CO2和液氨,采用改进型二氧化碳汽提法工艺,主要工艺流程为在合成压力下,用二氧化碳气对甲铵液进行气提,分解的氨和二氧化碳在合成压力下冷凝成尿液,尿液蒸发后进行大颗粒造粒工艺(采用海德鲁流化床大颗粒造粒技术)生成尿素颗粒。
主要工艺过程包括包括CO2压缩、CO2脱硫、CO2脱氢、尿素合成及蒸发、大颗粒造粒系统、成品包装贮运系统。
(1)原料液氨的供应
来自氨合成系统的原料液氨,进入高压液氨泵,升压至16.0Mpa(A)后送至高压喷射器作为动力原料,将高压洗涤器来的甲铵液增压后带进高压甲铵冷凝器后输入尿素合成塔。
(2)CO2压缩、脱硫和脱氢
来自界区的二氧化碳气体,其中CO2≥98.5%(V),通过二氧化碳液滴分离器后进入二氧化碳压缩机。
其中在二氧化碳压缩机三段出口设置脱硫工序脱除CO2气体中的硫化物,然后去脱氢工序。
二氧化碳气体在进入二氧化碳液滴分离器之前,加入空气用于脱氢反应器和设备的防腐,保证进入二氧化碳汽提塔之前的氧含量达到0.75%(V)。
二氧化碳压缩机的五段出口气体,先进入高压CO2加热器,加热到150℃以上,进入装有催化剂的脱氢反应器,以燃烧二氧化碳气体中的可燃气体组份,使CO2气体中的H2≤50ppm,气体再经高压CO2冷却器冷却到120℃,送入汽提塔。
(3)尿液合成和气提
尿素合成塔、汽提塔、高压甲铵令凝器和高压洗涤器四台设备组成高压圈。
从高压甲铵冷凝器底部导出的液体甲铵和少量未冷凝的氨和二氧化碳气体,分别用两条管线送入尿素合成塔底部。
合成塔内生产的尿素合成反应液经溢流管从塔下部排出,经液位控制阀进入汽提塔的上部管箱,经塔内的液体分配器均匀地分配到每根汽提管中,沿管壁形成液膜均匀下降;由汽提塔下部导入的二氧化碳气体在汽提管内与合成反应液逆流相遇。
汽提管间以2.0MPa左右的蒸汽加热。
汽提管内合成反应液中过剩的氨和未转化的甲铵被气提气提出和分解,从塔顶排出;合成的尿液和少量未分解的甲铵从塔底排出。
从气体塔顶部排出的气体与新鲜氨及高压洗涤器来的甲铵液一起进入高压甲铵冷凝器的顶部,在该冷凝器内氨和二氧化碳反应生成甲铵,并释放大量的反应热。
甲铵液从冷凝器底部通过管道导出;各管间设冷却水(脱盐水)带走反应热,并利用反应热副产蒸汽;未反应的气体从下部导出。
在高压甲铵冷凝器中生成的甲铵、甲铵液、已冷凝的氨和未冷凝的氨及二氧化碳一起导入尿素合成塔的底部。
转化和加热尿素合成塔的所需的热量由附加的氨和二氧化碳的冷凝反应提供。
从合成塔顶部排出的气体,进入高压洗涤器内,这时气体中的氨和二氧化碳用加压后的低压吸收段来的甲铵液冷凝吸收,生成甲铵液,从溢流管流到高压喷射器,再经高压甲铵冷凝器返回尿素合成塔;不凝气体和一定数量的氨自高压洗涤塔的顶部排出高压系统,进入低压吸收塔经洗涤吸收后,尾气通过放空筒排入大气,氨水溶液去氨水槽。
来自汽提塔底部的尿素-甲铵溶液,经过汽提塔的液位控制阀减压,溶液中的二氧化碳和氨得到闪蒸,气-液混合物喷到精馏塔顶部,在此甲铵进一步分解,而后进入精馏塔下部的分离器分离。
液体经液位控制阀流入闪蒸槽,气体上升到精馏塔填料段,精馏后的气体由顶部导出精馏塔,与来自低压洗涤器液位槽的液体和来自第一解吸塔的回流冷凝器的部分冷凝液,从下部一并进入浸没式低压冷凝器,两相并流上升进行吸收,吸收时产生的热量由低压甲铵冷凝器中的冷却水带走,此冷却水经低压甲铵冷凝器循环水泵送至低压甲铵冷凝器循环冷却期冷却后循环使用。
浸没式低压冷凝器中的气液混合物从冷凝器的上部溢流到低压洗涤器液位槽,进行气液分离,液体从液位槽底部导出,经高压甲铵泵升压后送高压洗涤器顶部;液位槽分离出的气体,经常压吸收塔吸收后放空。
(4)尿液的蒸发
出精馏塔底部尿液,经液位槽控制阀减压后,送到闪蒸槽,这时有相当一部分水、氨和二氧化碳闪蒸出来。
离开闪蒸槽的尿液(浓度约为73%(wt))流入尿液槽,通过尿液泵经流量控制阀后进入一段蒸发器,使用低压蒸汽对其进行加热,尿液进一步被浓缩,从73%浓缩到95-96%,此时称为熔融尿素,经过一段蒸发分离器分离后。
通过熔融尿液泵送往大颗粒造粒系统进行造粒。
闪蒸尾气和一段蒸发分离器分离出的气体汇合后送入一段蒸发冷凝器中进行冷凝,冷凝液流到氨水槽的第一小间隔;不凝气体由一段蒸发喷射器抽到放空管放空。
(5)回收液的解析和水解
蒸发和闪蒸的冷凝液中含有一定量的氨、少量二氧化碳和少量尿素,经真空液分管流入氨水槽。
氨水槽内用隔板分为三个间隔。
各间隔之间在下部有孔连通。
一段蒸发冷凝器中的冷凝液流入第一小间隔。
氨水槽第一小间隔的冷凝液一部分经低压吸收塔给料泵送往低压吸收塔作为吸收液,一部分送往一段蒸发器气相管线作冲洗用水,另一部分进入一段蒸发冷凝器作冲洗用水。
由常压吸收塔来的液体经排气筒流入氨水槽的第二小间隔,由解析塔给料泵经解析塔换热器加热后送到第一解析塔上部。
解吸出氨和二氧化碳。
出第一解吸塔的液体,经水解塔给料泵加压,经水解塔换热器换热后,进入水解塔的上部。
水解塔的下部通入蒸汽。
使该液体中所含的少量尿素水解成氨和二氧化碳。
解吸出来的氨和二氧化碳及水蒸汽(气相),直接导入第一解吸塔的下部,与第一解吸塔的液体进行质热换热交换;解吸出的液相经水解塔换热器换热后进入第二解析塔的上部,塔下部通入蒸气进行解析,从液相中解析出来的氨和二氧化碳及水蒸汽,导入第一解吸塔的下部,与第一解吸塔的液体进行质热换热交换。
出第一解吸塔的气体,含水小于40%,在回流冷凝器中冷凝。
冷凝液一部分作为回流液回流到第一解吸塔的顶部,进行质热交换,以减少出塔气相的水含量,另一部分冷凝液,送到低压甲铵冷凝器。
未被冷凝的气体进入吸收塔,进一步回收氨和二氧化碳后放空。
第二解吸塔解吸后的液体含氨小于5ppm;尿素小于5ppm。
经解吸塔换热器换热和废水冷却器冷却,送至水处理工序处理后循环使用。
(6)尿素大颗粒造粒
原料尿液来自尿液蒸发系统,闪蒸后的73%尿液和大颗粒尿素造粒时返回的稀尿液一起浓缩为熔融尿素(95-96%的尿液),通过静态混合器与添加剂甲醛混合后,经熔融尿素泵送到造粒机进行造粒。
甲醛贮罐内的甲醛由甲醛计量泵按一定的比例加到静态混合器中与原料尿液混合,混合后的尿液经进入造粒器的喷嘴进行雾化,雾化后的尿液在造粒器中与返料接触进行造粒。
造粒器雾化喷嘴内尿液在一定压力下喷射,被一定压力的雾化空气喷雾成细小液滴,喷洒到返料晶种表面,悬浮于流化床层中,细粒晶种包裹涂布逐步成长为多层质密结构的尿素粒子。
造粒后,尿素颗粒在冷却室冷却至95℃,经造粒机出料液位调节阀控制,并通过安全筛到第一流化床冷却器,该冷却用的流化空气由第一冷却器流化空气鼓风机提供。
在流化空气的作用下,尿素颗粒向出口方向流动。
雾化空气经造粒器雾化空气加热器预热至135℃后进入喷嘴外围环隙区,保护喷嘴并将尿液雾化。
流化空气由造粒器流化空气风机提供,经造粒器流化空气加热器预热至40~45℃后,送至造粒器下箱体,通过多孔板分布器进入上箱体,形成流化床并调节床温在110℃。
雾化空气和流化床空气夹带尿素粉尘,从造粒器上箱体顶部由造粒冷却洗涤器抽风机抽出,送至造粒器洗涤器进行洗涤。
出第一流化床冷却器的尿素颗粒经斗式提升机提升并借助振动筛给料器进入振动筛,振动筛将尿素颗粒分成三种规格:
超大颗粒尿素、成品尿素和细小颗粒尿素。
超大颗粒尿素经过破碎机给料斗由破碎机给料器送至破碎机,经破碎后的粒子与振动筛分出的细小颗粒一并送回造粒器作返料晶种;筛出的合格成品尿素进行最终产品冷却器内进行冷却,使产品温度降至50℃以下经产品输送机送至包装仓库。
产品冷却器抽出的含有尿素粉尘的空气送至冷却器洗涤器进行洗涤再利用。
从造粒器排出的空气中的尿素粉尘数量占总数的3/4左右。
该气体与从第一流化床冷却器、除尘风机、烟气风机等出来的尿素粉尘空气一起进入造粒冷却洗涤器,由洗涤器循环泵用稀尿液循环洗涤,以除去尿素粉尘。
洗涤后的空气由洗涤器抽风机排至放空筒后进入大气。
洗涤液流至洗涤器循环贮槽中循环使用。
洗涤器循环贮槽液体的浓度随洗涤的进行不断增大,当尿素浓度达到45%后,由洗涤器循环泵送至稀尿液回收贮槽。
稀尿液回收槽除收集造粒器洗涤器循环槽的洗涤尿液外,还接受并溶解造粒器出料中的少量块状尿素和破碎机、安全筛等设备的溢流尿素颗粒。
在稀尿液回收槽内设置有蒸汽喷射器,用低压蒸汽喷射加热搅拌,以利于尿素溶解,最后尿素回收泵将浓度为45%的稀尿液送至尿素蒸发系统的尿液贮槽,提浓后重新造粒。
成品尿素由NO.1至NO.3带式输送机输出,经电子皮带秤计量后输送至包装楼内,由四通分料阀分配,将尿素分别分至NO.4带式输送机、NO.5带式输送机和指定的贮斗内,再分别由三通分料阀分配送入指定的贮斗内,供包装用。
四个贮斗下方对应于包装机组进行称重、灌袋、封口、包装后由倒袋输送机放平,经NO.8带式输送机输送至NO.9带式输送机上,再由尿素袋装仓库B的桥式堆包机码垛堆存,也可由倒袋输送机上的挡包器将袋装尿素挡向NO.6带式输送机输送至NO.7带式输送机上送往尿素袋装仓库A的桥式堆包机码垛堆存。
装车时,由人工拆垛,用手推车转运至装车站台外运。
若需大袋包装颗粒尿素时,则由贮斗下方对应的1吨定量包装机进行称重,大袋尿素由叉车转运至装车站台外运。
二、危害种类
1、粉尘类:
有煤尘、矽尘、电焊烟尘、其它粉尘等。
2、毒物类:
有一氧化碳、二氧化碳、二氧化硫、氮氧化物(一氧化氮、二氧化氮)、硫化氢、二硫化碳、3,4苯丙芘、菲、蒽、呋喃、茚、萘、联苯、吡啶、苯酚、二甲酚、辛烷、五氧化二钒、碳酸钠、氰化物、苯、甲苯、二甲苯、氢氧化钠、硫酸、盐酸、肼(联氨)、六氟化硫、甲醇、甲醛、氨、尿素等。
3有害物理因素类:
有噪声、高温、热辐射、全身振动、γ射线、工频电场等职业病危害
4、危害