车刀的选择和使用.docx
《车刀的选择和使用.docx》由会员分享,可在线阅读,更多相关《车刀的选择和使用.docx(11页珍藏版)》请在冰豆网上搜索。
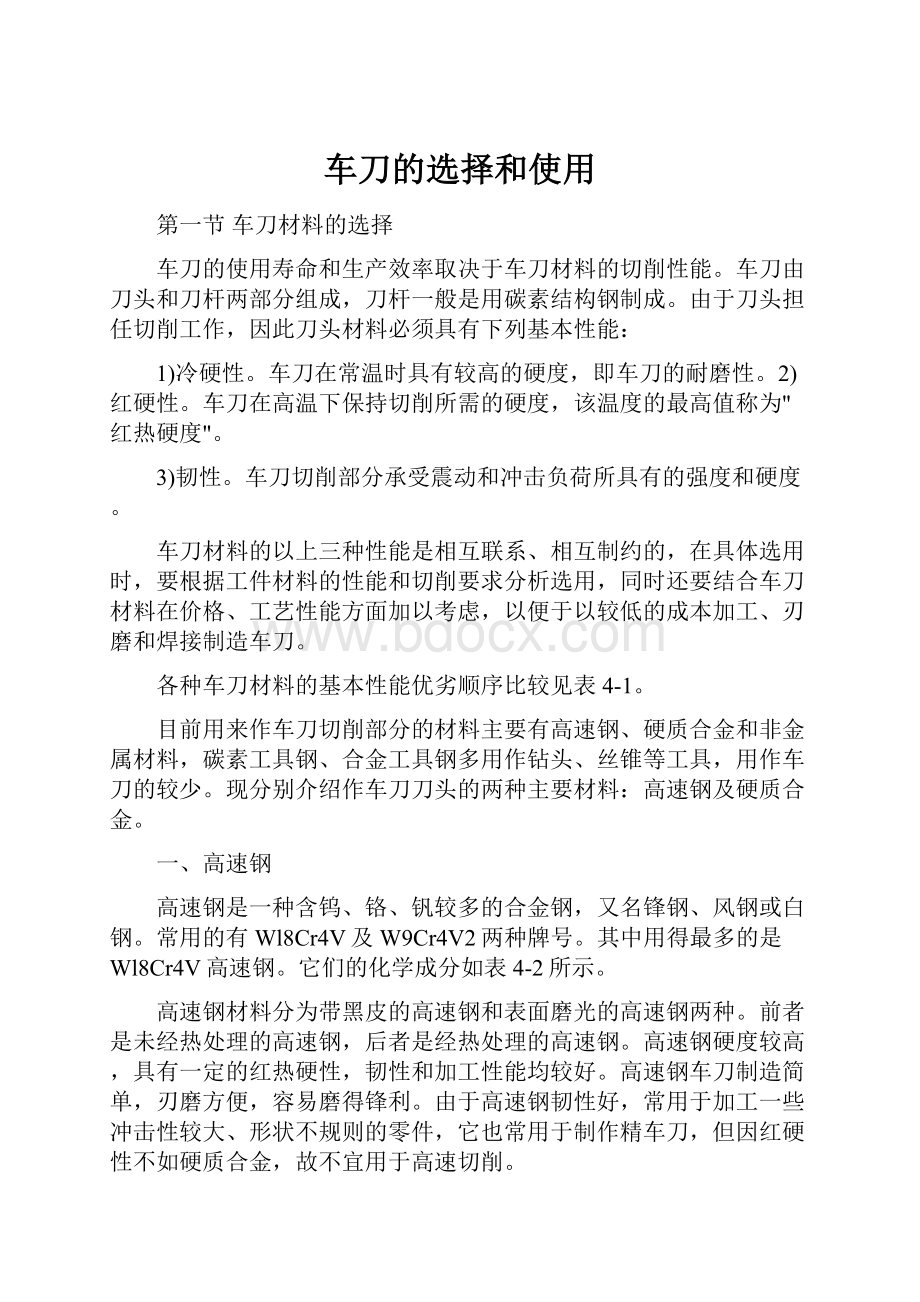
车刀的选择和使用
第一节车刀材料的选择
车刀的使用寿命和生产效率取决于车刀材料的切削性能。
车刀由刀头和刀杆两部分组成,刀杆一般是用碳素结构钢制成。
由于刀头担任切削工作,因此刀头材料必须具有下列基本性能:
1)冷硬性。
车刀在常温时具有较高的硬度,即车刀的耐磨性。
2)红硬性。
车刀在高温下保持切削所需的硬度,该温度的最高值称为"红热硬度"。
3)韧性。
车刀切削部分承受震动和冲击负荷所具有的强度和硬度。
车刀材料的以上三种性能是相互联系、相互制约的,在具体选用时,要根据工件材料的性能和切削要求分析选用,同时还要结合车刀材料在价格、工艺性能方面加以考虑,以便于以较低的成本加工、刃磨和焊接制造车刀。
各种车刀材料的基本性能优劣顺序比较见表4-1。
目前用来作车刀切削部分的材料主要有高速钢、硬质合金和非金属材料,碳素工具钢、合金工具钢多用作钻头、丝锥等工具,用作车刀的较少。
现分别介绍作车刀刀头的两种主要材料:
高速钢及硬质合金。
一、高速钢
高速钢是一种含钨、铬、钒较多的合金钢,又名锋钢、风钢或白钢。
常用的有Wl8Cr4V及W9Cr4V2两种牌号。
其中用得最多的是Wl8Cr4V高速钢。
它们的化学成分如表4-2所示。
高速钢材料分为带黑皮的高速钢和表面磨光的高速钢两种。
前者是未经热处理的高速钢,后者是经热处理的高速钢。
高速钢硬度较高,具有一定的红热硬性,韧性和加工性能均较好。
高速钢车刀制造简单,刃磨方便,容易磨得锋利。
由于高速钢韧性好,常用于加工一些冲击性较大、形状不规则的零件,它也常用于制作精车刀,但因红硬性不如硬质合金,故不宜用于高速切削。
二、硬质合金
硬质合金是由难熔材料的碳化钨、碳化铁和钴的粉末在高压下成形,经l350~1560"(2高温烧结而成的材料,具有极高的硬度,仅次于陶瓷和金刚石。
硬质合金的红硬性很好,在1000℃左右仍能保持良好切削性能;具有较高的使用强度,其抗弯强度可高达1000--1700MPa,但脆性大、韧性差、怕震,以上这些缺点可通过刃磨合理的角度加以克服,因此,硬质合金现已被广泛应用。
常用的硬质合金可根据其制造的合金元素不同,分为以下四类:
1.钨钴合金
由碳化钨和钴组成,常温时的硬度为HRA87~92,红硬性为800--900,代号为YG,常用牌号为YG3、YG3X、YG6、YG6X、YG8、YGll等。
其中YG3X及YG6X属于细颗粒碳化钨合金。
YA6则是我国试制成功的一种含有少量碳化钴的细颗粒硬质合金。
钨钴合金冷硬性很高,韧性也较好,宜用于加工脆性材料,如金属蚀口铸铁,也可车削冲击性较大的工件。
由于它的红硬度较差,在600℃时,钨钴合金容易和切屑粘结,使刀头前面磨损,故不宜用于车削软钢等韧性金属。
YG6X细颗粒碳化钴合金耐磨性较好,其强度近似YG6,因此车削冷硬合金铸铁、耐热合金钢及普通铸铁等都有良好效果。
2.钨钛钻合金
由碳化钨、碳化钛及元素钻组成,代号用YT表示,常用的有YT5、YTl4、YTl5、YT30等牌号。
钨钴钛合金的冷硬性能和红硬性能比硬质合金高。
在高温条件下比钨钴合金耐热耐磨、抗粘性大,宜于加工钢料及其他韧性金属材料,但由于性脆,不耐冲击,故不宜加工脆性金属。
3.钨钴钛铌合金
它是钨钴钛合金中的新产品,由碳化钨、碳化钛、钴、少量碳化铌组成,代号为YW,常用牌号为YWl、YW2。
它的耐磨性和热硬性都比较好,适用于切削各种铸铁和特殊合金钢材,如不锈钢、耐热钢、高锰钢等较难加工的材料。
4.钨钴铌类合金
这是一种含有少量碳化铌的细颗粒钨钻类硬质合金,代号为YA,常用牌号为YA6。
它的耐磨性能更高,适合于不锈钢、耐热钢、特硬铸铁、铁合金、硬塑料、玻璃和陶瓷等的加工。
在选用硬质合金时,应根据硬质合金本身性能特点、加工工件材料和切削条件等因素综合考虑。
表4-3为常用硬质合金使用性能及使用范围,可作为选用的参考。
除高速钢和硬质合金两种常用车刀切削材料外,还有碳素工具钢、合金工具钢、金刚石、陶瓷等。
碳素工具钢、合金工具钢的切削性能差,而金刚石价格高,以上三者都较少采用。
由于陶瓷材料比硬质合金的红硬性更高,耐磨性好,价格低,正成为一种应用广泛的刀具材料,但由于该种材料性脆、怕冲击、刃磨困难,所以在使用时仍受到一定的限制。
表4-4是常用车刀材料的特性及其切削成本对比情况。
第二节车刀刀具几何角度的选择及变化分析
为了顺利地进行切削,必须了解车刀切削部分的几何角度及其几何角度在切削过程中变化。
一、车刀切削部分的几何角度
1.车刀的组成部分
车刀的刀头是车刀的切削部分。
它由以下部分组成:
(1)前刀面:
切屑流出时,刀头与切屑相接触的表面,又称前面,用符号八表示。
(2)主后刀面:
刀头上与切削表面相对的表面,又称主后面,用符号A表示。
(3)副后刀面:
刀头上与工件已加工表面相对的表面,又称副后面,用符号"表示。
车刀组成部分见图4-3。
(4)主切削刃:
前面与主后刃面的交线,它担负主要的切削工作。
(5)副切削刃:
前面与副后刃面的交线,它也起切削作用。
(6)刀尖:
主切削刃与副切削刃的交点。
任何车刀都由以上部分组成,只是数目不完全相同,如普通外圆车刀的刀头部分一般由三面、两刃和一尖组成,但切断刀则由两个副切削刃和两个刀尖组成。
刀头部分的切削刃可以是直线,也可以是曲线,如样板车刀的切削刃就是曲线。
2.辅助基准面
为了确定和测量车刀的几何角度,需要选择几个辅助平面作为基准面.见图4-4。
(1)切削平面:
通过切削平面并与该点切削速度方向相垂直的平面,用符号P,表示。
(2)基面:
通过切削刃选定点并与工件过渡表面相切,且垂直于切削平面的平面,用符号P。
表示。
(3)正交平面:
通过主切削刃选定点且垂直于主切削平面和基面的平面。
用符号Pn表示。
当主切削刃与水平面平行时,切屑流出的方向正接近于这一平面所处的位置,因此车刀上主要切削角度都在正交平面上进行测量,如前角、后角的测量。
3.车刀的切削角度
车刀的切削角度共有7项,用于表示切削部分的几何形状,并可在主截面与上述3个基准面内度量,如图4-5所示。
(1)前角7。
它是车刀前刀面与基面之间在正交平面投影的角度,用符号7。
表示。
它是车刀切削部分的一个主要工作角度,直接影响车刀主切削刃的锋利度和刃口强度。
加大前角7。
,可以减小切屑变形和摩擦,从而降低切削力和切削热,切削起来较快,但另一方面前角过大,会削弱刀尖强度,减少散热能力,加剧刀具磨损。
(2)后角。
它是车刀副后刀面与基面之间在正交平面的投影角度,用符号a。
表示。
它影响主后面与过渡表面之间的摩擦情况。
(3)主偏角k,
它是主切削刃与进给方向在基面上投影的夹角,用符号k,表示。
它影响主刀刃参加工作的长度,并影响切削力的大小。
(4)副偏角k:
它是副切削刃与进给方向在基面上投影的夹角,用符号k:
表示。
它影响已加工表面的粗糙度及副刀刃参加工作的长度。
(5)刀尖角e
刀尖角为主、副切削刃在基面上投影的夹角,用符号e表示。
刀尖角的大小影响刀尖的强度及传热性能。
它与前角、后角之间的羊乏喃.
(6)刃倾角A
它是主切削刃与基面间的夹角,用符号A表示。
主要影响排屑情况和刀尖承受冲击的能力。
当刀尖是主切削刃最低点时A为正值;当刀尖是主切削刃最高点时A为负值。
当刀刃与基面平行时A为零度。
(7)副后角口,
它是副切削平面在副截面内的夹角,用符号a,表示。
其作用与后角a。
相似。
车刀静止状态下的几何角度如图4-6所示。
二、车刀几何角度选择
合理选择车刀的几何参数,可保证零件的加工精度、粗糙度,增大切削用量,减少车刀磨损,提高刀具耐用度,降低成本,提高生产效率。
1.前角70
前角70大小主要与需切削的工件材料及刀具材料性能有关,选择前角70时可从以下一些影响因素进行考虑:
(1)工件材料对前角选择的影响
车削塑性材料工件时,切屑呈带状,切削力集中在离主切削刃较远的前刀面上,刀尖不易受损。
为减少变形,应取较大的前角。
而车削脆性材料工件,其切屑呈碎粒状,加上工件表面硬度高,通常含有杂质及有砂眼缩孔等缺陷,使刀尖附近集中了很大的冲击力。
为保护刀尖,加工时一般情况下前角应取小些。
但在加工较硬材料工件时,因切削阻力大,应取较小前角,以保证车刀刀刃强度。
如在加工铬锰钢、淬硬钢工件时,车刀前角通常磨成负前角,以增加车刀耐用度。
(2)刀具材料对前角选择的影响
采用硬质合金、高速钢等不同刀具材料,切削时其车刀前角大小选择有所不同,高速钢车刀前角一般比硬质合金车刀的前角大。
表4-4是硬质合金车刀和高速钢车刀切削不同材料时前角的选择。
(3)加工特点对前角选择的影响
加工阶段不同,前角的选择不同。
粗加工时,切削深度大、切削时的冲击力大,为提高车削效率,应采用较小的前角;精加工时,切削深度小、进给量小、切削时的冲击力小,为减少变形,提高精度,则前角可选择大些,其值可较表4-4中的前角的选取增大5。
左右。
2.后角a
后角的选择原则是在保证刀具有足够的散热性能和强度的基础上,保证刀具锋利和减少与工件摩擦,一般不宜过大。
否则会加速刀具磨损,降低刀具强度而造成崩刃。
在加工塑性材料时,由于工件表面弹性复原会与刀具后面发生摩擦,为了减少摩擦应取大些后角口。
,加工脆性材料时,应取小些后角。
高速钢刀具后角a。
一般可在6。
~l2。
之间选取。
硬质合金刀具可在2。
~l2。
之间选取,粗车时3。
~6。
,精车时6。
~l2。
3.主偏角k,
主偏角k,主要是改变刀具散热情况,并适应机床一刀具一夹具系统的刚度需要。
为了改善刀具的散热情况,常采用较小的主偏角k,。
因此选择主偏角k,的原则是:
在机床一刀具一夹具刚度允许的范围内,主偏角尼r应尽量小些,一般可在45。
~75。
之间选取,但在车细长轴时为了减少工件弯曲和振动采用较大主偏角k,,一般可在75。
~90。
之间选取,车阶台轴时则取90。
。
4.副偏角k:
副偏角k:
的主要作用是减少副刀刃与工件之间的摩擦。
此外,还可以改善工件表面光洁度及刀具散热情况。
副偏角k:
一般可在10。
~l5。
之间选取。
5.刃倾角A
刃倾角A的作用是改变切屑流动方向,以增加刀尖强度。
当刃倾角A是负值时,切屑向待加工面方向流出,刀尖强度差些。
刃倾角A是正值时,切屑向已加工方向流出,刀尖强度高。
当刃倾角.零度时,切削则垂直于刀刃方向流出。
所以在选取角度时,粗加工取正值,精加工取负值。
一般刃倾角A可在一4。
~十4。
之间选取。
以上角度一般均指静态下测量的角度。
三、车刀安装和切削运动对角度的影响车刀安装得是否正确,对切削是否顺利,车出来的工件表面是
否光洁等都有很大关系。
有了合理角度的车刀,如果没有正确安装,它就不能发挥应有的作用。
此外,由于切削时走刀运动的影响,也会使车刀角度改变。
1.车刀安装高低对角度的影响
车刀刀尖应装得与工件中心线一样高,如图4-7所示,这时车刀角度没有变化。
要做到这一点,我们可以用床尾顶针尖作为标准,或者先在工件端面车一印痕就可知道中心,也可以记住自己车床中拖板滑块平面与工件中心线的距离,用钢尺量其高低。
如果刀尖高于工件中心,如图4-7(a)所示,这时切削平面位置改变,基面也随着改变,结果造成前角增大,后角减小,造成车刀切人工件的困难。
相反,如果刀尖低于工件中心,如图4-7(c)所示,则前角减小,后角增大。
2.车刀安装偏斜对角度的影响
车削时,一般车刀安装总是与工件中心线垂直,这样主偏角和副偏角不会改变。
如果车刀刀头向左倾斜,主偏角将增大,副偏角则减小,如图4-8(a)所示。
相反,如果车刀刀头向右倾斜,如图4-8(C)所示。
主偏角将减小,副偏角则增大。
此外,在安装车刀时,还应避
免车刀伸出太长,造成成车削振动,影响表面光洁度,甚至会折断。
一般伸出长度不超过刀杆高度的一倍半,如图4-9所示。
(a)车刀安装伸出量正确;(b)车刀安装伸出量过长
车刀下面垫片要平整,如图4-10,同时要尽可能用厚垫片代替薄垫片,刀架上的螺丝要拧紧。
四、走刀运动对切削运动的影车平面时,车刀按一定的走刀量在平面上车出一条螺旋线,愈近中心愈倾斜,这样由于切削平面和基面位置改变,使车刀的后角减小,前角增大。
走刀量增大,后角减小愈多,如果用很小的后角车刀以大走刀量进行车削,就无法实现车削了。
车外圆时,在工件上车出来的也是一条螺旋线,走刀量愈大,倾斜愈厉害,结果使车刀后角减小,前角增大,如图4-11所示。
因此,在磨刀时要注意这个角度的变化。
第三节刀具的刃磨
为了顺利地进行切削,必须把车刀磨成一定的几何形状,刃磨是形成正确合理的刀头几何角度的必要手段。
车刀刃磨可分为机械刃磨和手工刃磨两种。
机械刃磨的效率高,但对设备有一定的要求,一些有条件的单位可以采用。
手工刃磨灵活,对设备要求低,一般工厂仍普遍的采用。
车刀刃磨质量的好坏,直接影响着车削加工的质量。
因此,刃磨车刀是车工必须掌握的主要基本技能之一,车刀刃磨的要点如下。
一、砂轮的正确选择
常用的砂轮有氧化铝系砂轮(刚玉砂轮)和碳化硅砂轮两种。
氧化铝系砂轮的主要成分是Al2Q,适于刃磨碳素工具钢及高速钢车刀;碳化硅砂轮磨料的主要成分是SiC,硬度很高,适于刃磨硬质合金刀头。
砂轮有粗细之分。
砂轮的粗细是以其磨料颗粒的大小进行区分的。
粗细以粒度表示,当磨料的平均直径大于63,am时,用恰好可以通过的筛网号来表示,粒度号越大,磨粒的尺寸越小,砂轮愈细。
当磨粒平均直径为0.5~63,am时,磨粒也称为微粉,用W表示。
粗磨车刀应选用较粗的软砂轮,可选用40~60号较粗磨粒砂轮。
精磨车刀可选用80~120号较细磨粒硬砂轮。
砂轮同时具有软硬之分。
其硬度是指砂轮表面的磨粒在外力作用下使其脱落的难易程度。
磨粒越易脱落,则砂轮的硬度越低,反之则高。
砂轮的硬度取决于砂轮结合剂的性能。
砂轮的硬度分为软、中软、中、中硬、硬等级别。
粗磨车刀时可选用较软的砂轮,以提高生产率,精磨时则应用较硬的砂轮,以提高加工精度。
二、刃磨程序
高速钢和硬质合金刀头的刃磨有所不同,硬质合金刀片性硬而脆,刃磨时切削刃易产生锯齿形缺口。
以下分别介绍它们的刃磨过程的一般步骤。
至于刃磨时的操作方法应在实践中训练,这里不作文字的描述。
1.高速钢车刀刃磨一般步骤
(1)磨主后刀面
磨出车刀的主偏角k,和主后角口。
如图4-12所示
(2)磨副后刀面
磨出车刀的副偏角k:
和主后角口,如图4-13所示。
(3)磨前刀面
磨出车刀的前角y。
和刃偏角A,如图4一l4所示。
(4)磨刀尖圆弧
磨出主、副刀刃之间的过渡刃,如图4-15所示。
(5)精磨
在较细硬的砂轮上仔细修磨刀头各面,使车刀的几何形状和角度符合要求,并提高车刀的表面粗糙度。
(6)研磨
有精确角度的车刀,在刃磨时,还要考虑研磨,要求用平整的氧化铝油石,轻研车刀后面和过渡刃,研去刀刃上留下的毛刺,或研磨棱面和断屑槽,进一步减小各切削刃及各面的粗糙度。
2.硬质合金车刀刃磨一般步骤
(1)粗磨刀杆非硬质合金部位各面的几何形状
应在氧化铝砂轮上进行,以便减少在刃磨刀片部位时的刃磨量。
因此在刃磨主、副后角时可比刀片部位的主、副后角大。
左右o
(2)粗磨刀头
粗磨刀头硬质合金部位各面,可在较粗的绿色碳化硅砂轮上进仃。
其步骤是:
1)磨主后刀面,磨出车刀主偏角忌,;
2)磨副后刀面,磨出车刀副偏角志:
和副后角口:
;
3)磨车刀前面,磨出车刀前角托,刃倾角A及排屑槽形状。
以上磨削过程与高速钢车刀磨削过程类似。
(3)精磨刀头
在较细粒度的绿色碳化硅砂轮上精磨各面,准确的磨出各角度的大小,将各刃磨面磨平磨光。
其步骤是:
1)精磨前面:
2)磨主后面,同时调整斜棱面的宽度:
3)磨副后面,最后修磨过渡刃或修光刃。
(4)研磨刀头
用平整的400粒度的绿色碳化硅油石仔细研磨车刀各面,将刀刃上的锯齿形缺口磨平,并使各面粗糙度在0.10以上。
三、刃磨车刀注意事项
1)握刀姿势要正确,手指不能抖动,用力不能过大,以免手滑时触及砂轮而受伤。
2)磨刀时,人站在砂轮的侧面,防止砂轮粉屑或碎裂时飞出
3)砂轮必须有防护罩,砂轮未转稳时不能磨刀,磨刀用砂轮不准磨其他物件。
4)磨碳素钢、合金钢及高速钢刀具时,要经常冷却,不能使刀头烧红。
磨硬质合金刀头时不要进行冷却。
5)在盘形砂轮上磨刀时,应避免使用砂轮侧面,在碗形砂轮上磨刀时,不准使用砂轮内、外圆。
6)刃磨时应将车刀左右移动,不能固定在砂轮一处,以免砂轮表面磨成凹槽。
托架与砂轮之间的空隙不可超过3mm,以免不慎将车刀嵌入空隙,发生事故危险。
7)禁止两人同时使用一个砂轮。
四、车刀角度的检查
车刀磨好后,必须检查刃磨质量和角度是否合乎要求。
检查刃磨质量时,主要是观察刀刃是否锋利、表面是否有裂纹等缺陷。
对于要求高的车刀,可用l0~20倍放大镜观察。
检查角度时,先用样板检查车刀主后角,然后检查楔角。
如果这两个角度合格,前角也就合乎要求了。
其检验方法如图4-16所示。
车刀角度也可以用专用量角台或万能游标量角器测量。
其测量方法如图4-17~图4-20所示。
其中图4-17为车刀前角测量,图4-18为车刀后角测量,图4-19为车刀刃倾角测量,图4-20为车刀主偏角和副偏角测量。