单壳程双管程管壳式换热器设计.docx
《单壳程双管程管壳式换热器设计.docx》由会员分享,可在线阅读,更多相关《单壳程双管程管壳式换热器设计.docx(15页珍藏版)》请在冰豆网上搜索。
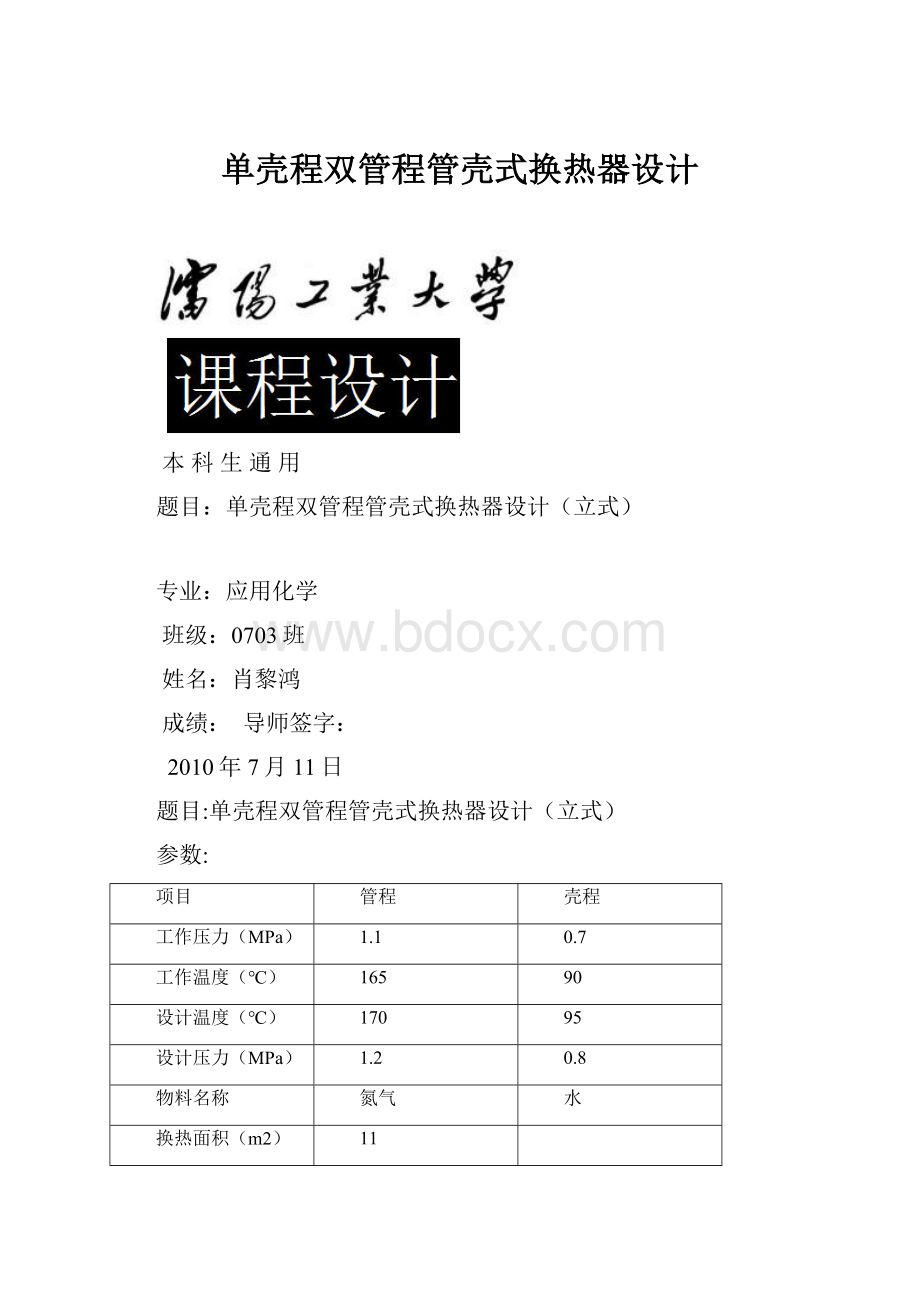
单壳程双管程管壳式换热器设计
本科生通用
题目:
单壳程双管程管壳式换热器设计(立式)
专业:
应用化学
班级:
0703班
姓名:
肖黎鸿
成绩:
导师签字:
2010年7月11日
题目:
单壳程双管程管壳式换热器设计(立式)
参数:
项目
管程
壳程
工作压力(MPa)
1.1
0.7
工作温度(℃)
165
90
设计温度(℃)
170
95
设计压力(MPa)
1.2
0.8
物料名称
氮气
水
换热面积(m2)
11
焊缝系数
0.85
0.85
腐蚀余量(mm)
1
1
要求:
要求每位学生在设计的过程中,充分发挥自己的独立工作能力及创造能力,在设计过程中必须做到:
(1)及时了解有关资料,做好准备工作,充分发挥自己的主观能动性和创造性。
(2)认真计算和制图,保证计算正确和图纸质量。
(3)按预定计划循序完成任务。
日程安排:
1.准备阶段(1天)
2.设计计算阶段(3天)
3.绘图阶段(4天)
4.编写设计说明书(2天)
1.绪论
热交换器,通常又称作换热器,是化工﹑炼油和食品及其他工业部门的通用设备,在生产中占有重要作用。
化工生产中,换热器可作为加热器、冷却器、冷凝器、蒸发器和再沸器等,应用甚为广泛。
换热器种类很多,但根据冷、热流体热量交换的原理和方式基本上可以分为三大类,及间壁式、混合式和蓄热式。
三类换热器中,间壁式换热器应用最多。
本次设计的管壳式换热器就属于间壁式换热器的一种。
立式固定管板式换热器示意图
2.设计计算
2.1管子数n的计算
选25×2.5的无缝钢管,材质20号钢,管长1.5m。
因为F=πd均Ln,所以
2.2管子排列方式,管间距的确定
本设计物料:
管程氮气,壳程水,循环水工作温度90℃较高,不易结垢。
可暂不考虑机械清洗水垢的问题,故排列方式采用结构紧凑、传热系数较高的正三角形排列。
由《化工设备与仪表自动化》中表6-4得六角形层数为6,对角线上的管数为13,管子根数为127其中因安排拉杆需减少6根(参见2.12拉杆设计),实际管数121根。
查表6-5,由管子外径25mm,可得管间距α=32mm。
管子排列方式如右图:
2.3壳体直径的确定
Di=a(b-1)+2l
式中Di—换热器内径,mm
b—正六角形对角线上的管子数,查表6-4,取b=13
l—最外层管子的中心到壳壁边缘的距离,取l=2d.
查《仪表设备及仪器自动化》P58表2-5,并结合壳体直径的计算,确定Di=500mm
2.4壳体厚度的计算
pc—计算压力,取pc=0.8MPa;Di=500mm;焊接系数φ=0.85;
材料选用Q235-B钢,[σ]95℃=113Mpa。
计算壁厚为
取c2=1mm,由书中表4-7得c1=0.3mm
圆整后实取Sn=4mm。
DN500,δ=4每米钢板质量为50kg。
2.5壳体液压试验应力校核
试验压力
故:
Q235-B在常温时
故液压试验应力校核合格。
2.6分程隔板的选择
分程隔板应采用与封头、管箱短节相同材料,故材料选用Q235-B。
要求隔板的密封面与壳体法兰密封面,管板密封面与分程槽面须处于同一基面。
分程隔板槽深度为4mm,槽宽12mm。
其结构相见装配图。
查《化工单元过程及设备课程设计》表4-1得分程隔板的最小厚度为8mm
2.7封头的选择
上下封头均选用EHA椭圆封头,其厚度与壳体厚度相同,材料选用Q235-B钢。
上封头的主要尺寸如下表:
公称直径DN(mm)
曲面高度h1(mm)
直边高度h2(mm)
碳钢厚度δ(mm)
500
125
40
4
下封头的主要尺寸如下表:
公称直径DN(mm)
曲面高度h1(mm)
直边高度h2(mm)
碳钢厚度δ(mm)
500
125
50
4
查《过程设备机械设计》P106标2JB/T4746-2002得:
公称直径
DN(mm)
总深度
H(mm)
内表面积
A(m2)
容积
V(m3)
质量
M(kg)
500
150
0.3103
0.0213
9.6
如下图所示:
2.8法兰,管板的选择
容器法兰材料选16MnR。
根据JB4701—2000标准,选用DN500,PN1.6(MPa)的甲型平密封面法兰。
DN25(100)PN<4MPa管法兰的接管伸出长度为150mm。
容器法兰的主要尺寸如下表:
公称直径DN,mm
法兰,mm
螺柱
D
D1
D2
D3
D4
δ
d
规格
数量
500
630
590
555
545
542
44
23
M20
28
其密封面结构如下图所示:
选用固定式换热器管板,不兼做法兰,换热管与管板的连接采用先焊后强度胀的连接形式,考虑到胀接结构要求,此次管板的厚度取30mm。
实际上,管板的厚度应按GB151-1991进行强度计算,但由于计算复杂,在此不进行具体的校核。
2.9垫片尺寸的确定
由于与壳体接触的介质仅为冷却水,对密封的要求一般,因此密封垫片选用价格相对较低的石棉橡胶片。
根据JB/T4704—1992及所选的DN500,PN1.6(MPa)甲型平焊法兰。
垫片尺寸如下表:
(单位:
mm)
公称直径DN
垫片内径di
垫片外径D0
垫片厚度t
500
504
544
3
2.10管子拉脱力的计算
计算数据如下表
项目部件
管子
壳体
材质
20号钢
Q235-B钢
(α/℃)
11.8×10-6
11.8×10-6
E(MPa)
0.21×106
0.21×106
尺寸
φ25×2.5×1500
φ500×4
管子数
127根
管间距
32mm
管壳壁温差/℃
T=75
管子与管板连接方式
开槽胀接
胀接长度
L=40mm
A.在操作压力下,每平方米胀接周边所产生的力qp
式中
p=1.1(MPa);l=40mm
B.温差应力导致的每平方米胀接周边上的拉脱力
式中
则
由已知条件可知,qp与qt的作用方向相同,都使管子受压,则合拉脱力为
q<[q]=4.0(MPa)
因此,拉脱力在许用范围内。
2.11是否安装膨胀节的计算
管,壳壁所产生的轴向力:
压力作用于壳体上的轴向力:
其中
则
压力作用于管子上的轴向力:
根据《钢制管壳式换热器设计规定》:
q<[q]=4.0(MPa)条件成立,故本换热器不必设置膨胀节。
2.12折流板设计
折流板为单弓形,切缺率(切掉圆弧的高度与壳体内径百分比)为20%~49%,通常为20%~25%,最佳大小一般为20%,此时单位压降下的传热膜系数最高。
切掉圆弧的高度
实际应用中,单弓形折流板间距B=(0.2-1.0)Di,以0.4~0.5最优。
取B=0.5Di=250mm。
折流板数
折流板最小厚度与壳体直径、换管无支承板有关,由书中表6—6查得为3mm。
由表6—8查得折流板外径496.5mm,材料为Q235—B钢。
按GB151规定,I级换热器由于d<32mm,l=1500>900mm,故折流板管孔直径与允许偏差分别为25.4mm和0.3mm。
弓形缺口为上下布置,以造成流体剧烈扰动,增大传热系数。
2.13拉杆设计
由于换热管外径大于19mm,故拉杆采用拉杆定距管的形式。
根据《过程设备机械设计》中表5-6,拉杆选用Φ10,共6根,材料为Q235—B钢,如图所示:
由GB151-1999表45查得,拉杆的主要尺寸如下表:
拉杆螺纹公称直径
dn/mm
数量
基本尺寸
拉杆直径d/mm
La/mm
Lb/mm
/mm
10
6
10
13
≥40
1.5
选用定距管规格为φ25×2.5(碳钢20),共6根。
拉杆孔见上图:
dn=10mm,L2=1.5×dn=15mm
2.14开孔补强
换热器壳体和封头的接管处开孔需要补强,常用的结构是在开孔外面焊上一块与容器的材料和厚度相同,即4mm厚的Q235—B钢板。
开孔补强如下图。
2.15支座
采用裙座,裙座厚度取Sc=8mm,基础环厚度取10mm。
设计结果,见所绘的换热器装配图。
3.设计评述
本次设计的单壳程双管程管壳式换热器,其两端与壳体连为一体,管子则固定于管板上,其结构简单;在相同的壳体直径内,排管最多,比较紧凑。
考虑到清洗和整体结构的要求,由于壳程介质清洁,故采用结构紧凑,传热系数较高的正三角形排列。
在壳体设计时增加了液压试验应力校核,以确保在运行中的安全。
但并未对封头、法兰、管板、换热管等受力元件进行强度计算。
封头,容器法兰、管板,垫片,拉杆的选择均参照国家标准GB151-1999,但封头直边高度的选择并未依据其厚度而选择。
由于压力不高、气密性要求较高,故封头与壳体的连接结构采用平垫密封结构。
管板不兼做法兰,采用焊接的方式与壳体连接。
管子与管板的连接形式采用胀焊、焊接和胀接并用,兼顾胀接的密封性好和焊接强度高的特点。
以上结构均详见装配图。
管壳式换热器的特点是壳层清洗困难,管壳程间有温差应力存在,当热冷流体温差较大时,需在壳体设置膨胀节。
经计算,本次设计的换热器不需设计膨胀节。
在折流板设计时,选用弓形折流板。
由于物料为无相变流体,兼顾传热与压降两个因素,切缺率(h/Di)选为0.2,此时单位压降下的传热膜系数最高;单弓形折流板间距B取为0.5Di。
由于计算复杂,本次设计并未对开孔补强及群座进行设计计算。
4.参考文献
1.《机械设计基础》.刘泽深.中国建筑工业出版社
2.《化工设备机械基础》.赵军.化学工业出版社
3.《机械设计基础课程设计》.刘泽深.中国建筑工业出版社
4.《简明机械零件设计手册》.朱龙根.机械工业出版社
5.《机械设计课程设计手册》.龚桂义.高等教育出版社
6.《化工制图》.熊洁羽.化学工业出版社
7.《化工设备与仪表自动化》.唐洪波,马冰洁.沈阳工业大学
8.《化工原理课程设计》.贾绍义,柴诚敬.天津大学出版社
9.《过程设备机械设计》.潘红良,郝俊文.华东理工大学出版社
10.《换热器设计手册》.T.Kuppan.化学工业出版社
11.《化工装置实用工艺设计》.E.E.路德维德.化学工业出版社
12.《化工单元过程及设备课程设计》.匡国柱,史启才.化学工业出版社
附:
设计结果一览表
换热管数
121
管子规格
φ25×2.5×1500
排列方式
正三角形
管间距/mm
32
壳体直径/mm
500
壳体壁厚/mm
4.0
分程隔板厚度/mm
8
分程槽宽/mm
12
封头规格
DN500×4,PN1.6曲面高度125mm
上封头直边高度/mm
40
下封头直边高度/mm
50
容器法兰:
甲型平焊平密封面DN500,PN1.6
法兰内径/mm
510
法兰外径/mm
630
螺栓孔中心圆直径/mm
590
螺栓孔直径/mm
23
法兰厚度/mm
44
密封面厚度/mm
3
法兰质量/kg
36.8
螺柱规格
M20
螺柱数量
28
接管伸出长度/mm
150
管板不兼做法兰
管板厚度/mm
30
石棉橡胶垫片
垫片公称直径/mm
500
垫片内径/mm
504
垫片外径/mm
544
垫片厚度/mm
3
温差应力
管壳壁轴向力/N
9.06×105
管子轴向力/N
1.065×105
壳体轴向力/N
0.315×105
拉脱力/Mpa
2.05
单弓形折流板
切缺率/%
20
折流板间距/mm
250
折流板外径/mm
496.5
管孔孔直径/mm
25.4
折流板最小厚度/mm
3
折流板形式
上下
拉杆:
拉杆定距管结构
拉杆数
6
螺纹公称直径/mm
10
拉杆孔L2/mm
15
拉杆直径/mm
10
定距管数
6
定距管规格
φ25×2.5
M10螺母厚度/mm
17.77
M10最大直径/mm
8.4
裙座厚度/mm
8
裙座基础环厚/mm
10