材料成型过程数值模拟南京农业大学.docx
《材料成型过程数值模拟南京农业大学.docx》由会员分享,可在线阅读,更多相关《材料成型过程数值模拟南京农业大学.docx(41页珍藏版)》请在冰豆网上搜索。
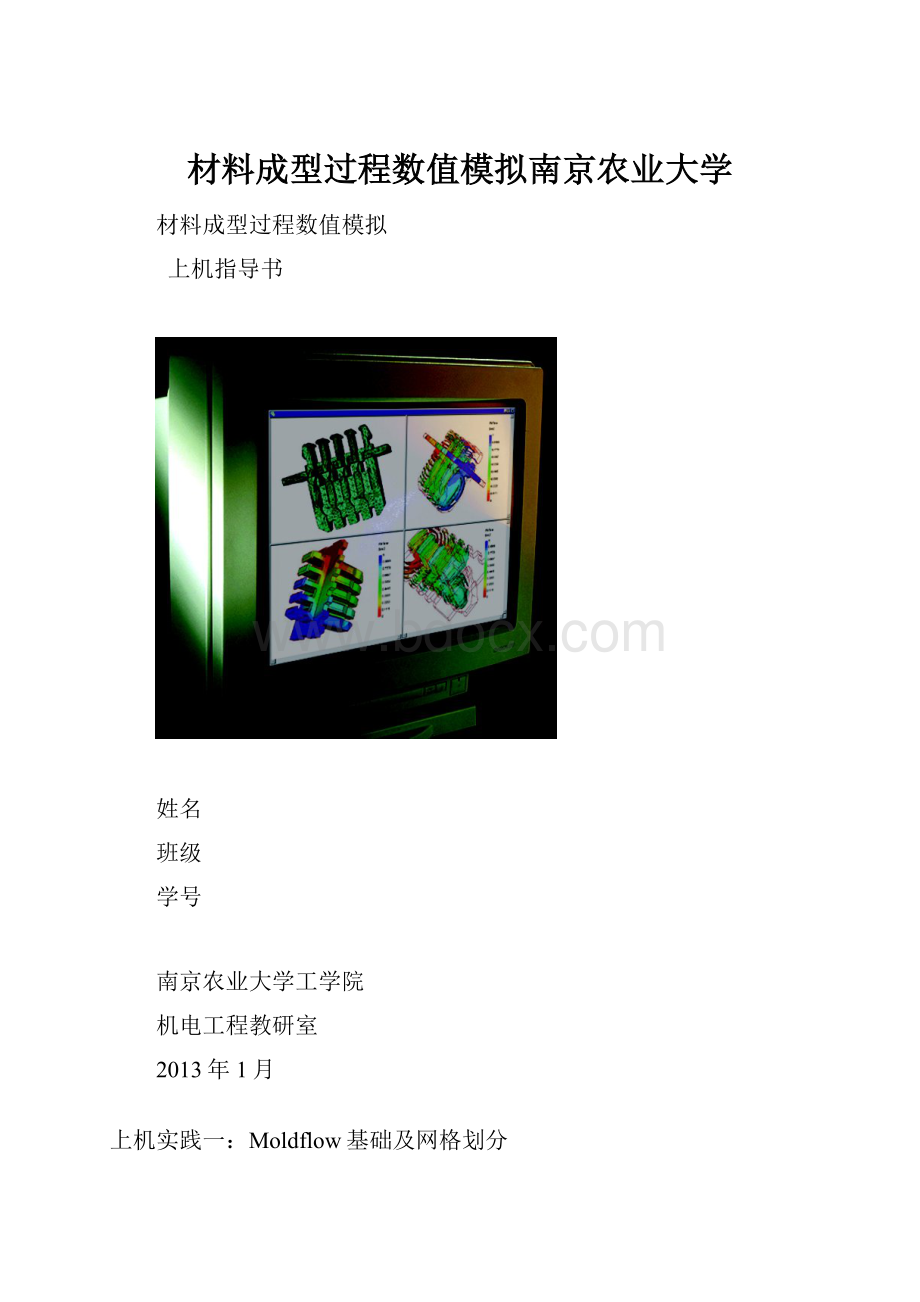
材料成型过程数值模拟南京农业大学
材料成型过程数值模拟
上机指导书
姓名
班级
学号
南京农业大学工学院
机电工程教研室
2013年1月
上机实践一:
Moldflow基础及网格划分
一、目的
1.熟练Moldflow软件的界面。
2.掌握三维绘图软件生成实体模型导入Moldflow方法。
3.掌握Moldflow模流分析的基本步骤及详细的操作方法。
4.熟练掌握Moldflow中网格的类型、各种网格类型的应用条件、网格的划分、网格结果检查、修改等。
5.熟练掌握Moldflow进行最佳浇口分析及填充分析。
6.熟练掌握Moldflow最佳浇口和流动分析结果导出。
二、内容
1.采用pro/E三维绘图软件建立三维模型,并以STL格式导出。
2.对模型划分网格、检查网格、修改网格等。
3.利用Moldflow对该模型进行最佳浇口、填充和流动分析。
4.导出Moldflow模流分析的结果。
三、上机实践
1.采用三维软件建立实体模型,并以STL格式导出。
2.模型导入
2.1打开软件
双击桌面上
打开Moldflow软件,会出现如图1所示界面
图1Moldflow初始界面图2输入对话框
2.2导入产品模型
(1)执行【文件】→【导入】命令(如图2所示),会弹出如图所示的对话框。
(2)在对话框中找到*.stl文件所在的路径,选择该文件,然后单击【打开】按钮打开文件,会弹出模型“输入”选项设置对话框(图3),选择网格类型和单位尺寸,单击【确定】完成导入模型。
图3“输入”选项设置对话框
3.网格划分
执行【网格】→【生成网格】命令(图4)后,工程管理视窗中的“工具”页面显示“生成网格”定义信息(图5),设定参数并单击【立即划分网格】按钮,系统将自动对模型进行网格划分和匹配。
网格划分信息可以在模型显示区域下方的“网格日志”中查看。
图4图5
4.网格检验与修补
4.1执行【网格】→【网格诊断】命令(图4),系统自动弹出【网格诊断】对话框,如图5所示,上面显示了网格的信息。
网格统计提供了网格不同特性快速评价,针对具体的分析内容对网格进行修补。
图5网格统计
4.2执行【网格】→【网格修补向导】命令(图4),系统自动弹出【网格修补向导】对话框,如图6所示,根据向导可以完成一定网格修补。
不能修补的网格则要通过手动的方法完成。
图6-1图6-2
图6-3图6-4
图6-5图6-6
图6-7图6-8
图6-9
图6网格修补向导
5.选择分析类型
执行【分析】→【设定分析顺序】命令(图7所示),系统自动弹出【选择分析顺序】对话框,如图8所示。
选择“浇口位置”,单击【确定】按钮。
完成分析类型选择。
图7图8
6.定义成型材料
执行【分析】→【选择材料】命令,系统自动弹出【选择材料】对话框,如图9所示。
选择制品的材料,单击【确定】按钮。
图9图10
7.浇口位置分析
双击方案任务视图(图10)中的“立即分析”。
系统弹出信息提示对话框,单击【确定】按钮开始分析。
(注:
浇口优化分析时不需要事先设定浇口位置。
成型工艺条件采用默认)分析完成后,在分析日志窗口中的Gate可以看到最佳浇口位置信息;也可以选中方案任务中的【最佳浇口位置】复选框,显示最佳浇口信息。
8.复制模型
在完成最佳浇口位置分析基础上,进行产品翘曲和流动分析。
对上述模型进行复制。
9.选择分析类型
执行【分析】→【设定分析序列】命令,系统自动弹出【选择分析顺序】对话框,如图8所示。
选择“流动+翘曲”,单击【确定】按钮。
完成分析类型选择。
10.设定注射位置
双击方案任务视窗中的“设定注射位置”图标,根据浇口优化结果,选择最佳浇口位置节点,完成浇口位置设定。
11.工艺参数设定
双击方案任务视窗中的“工艺设置”图标,系统弹出【工艺设置向导】对话框,如图11所示,完成第1页设置后,单击下一步进入【工艺设置向导】对话框的第2页,选中【分离翘曲原因】复选框,单击【完成】按钮,结束工艺过程参数的设置。
图11-1图11-2
图11工艺设置向导对话框
12.分析计算
双击方案任务视图中的“立即分析”。
系统弹出信息提示对话框,单击【确定】按钮开始分析。
13.结果查看
在方案任务视图中,选择要查看的结果进行显示。
四、出现的问题及解决方法记录
上机实践二:
浇道系统、冷却系统设计
一、目的
1.熟练掌握Moldflow软件浇道系统设计和冷却系统设计的过程。
2.熟练掌握利用浇道系统向导建立浇道系统以及手动建立浇道系统的方法。
3.熟练掌握利用冷却系统向导建立冷却系统以及手动建立冷却系统的方法。
4.熟练掌握Moldflow模流分析结果的导出。
二、内容
1.采用pro/E三维绘图软件建立三维模型,并以STL格式导出。
2.建立浇道系统。
3.建立冷却系统。
4.导出Moldflow模流分析的结果。
三、上机实践
1.采用三维软件建立实体模型,并以STL格式导出。
2.模型导入
双击桌面上
打开Moldflow软件,执行【文件】→【导入】,找到*.stl文件并选择该文件,然后单击【打开】按钮打开文件,在“输入”选项设置对话框中选择相应的网格类型和单位尺寸,单击【确定】完成导入模型。
3.网格划分
执行【网格】→【生成网格】,设定参数并单击【立即划分网格】按钮,完成网格划分。
4.网格检验与修补
执行【网格】→【网格诊断】,弹出“网格诊断”对话框,显示网格的信息。
检查网格是否需要修补,如果要修补,则执行【网格】→【网格修补向导】自动修补,或通过手动的方法完成。
5.选择分析类型
执行【分析】→【设定分析顺序】,选择分析类型,单击【确定】按钮。
6.定义材料
执行【分析】→【选择材料】,在“选择材料”对话框中选择制品的材料,单击【确定】按钮。
7.设定注射位置
执行【分析】→【设置浇口位置】,在网络模型上欲设浇口的节点位置处单击鼠标设置出浇口位置。
8.浇注系统
执行【建模】→【流道系统向导】命令,会弹出“流道系统向导”对话框,如图1所示。
在对话框中的X、Y值确定入料点位置(默认位置模具中心),如果使用热流道系统,可以勾选“使用热流道系统”选项。
单击“下一步”完成对话框里的选项和参数设置。
单击“完成”,系统会自动创建出浇注系统。
图1-1图1-2
图1-3
图1流道系统向导
9.浇注系统
执行【建模】→【冷却回路向导】命令,会弹出“冷却回路向导”对话框,如图2所示。
指定水路的直径、水路距产品模型上表面和下表面间的距离、水路的方向、水路数目、两水路的中心距离、超出产品的距离等。
如果有水路存在,勾选“首先删除现有水路”。
如果水路采用软管连接,勾选“使用软管连接官路”。
图2-1图2-2
图2冷却回路向导
10.工艺参数设定
双击方案任务视窗中的“工艺设置”图标,系统弹出【工艺设置向导】对话框,如图3所示,完成第1页设置后,单击下一步进入【工艺设置向导】对话框的第2页,完成对话框里的选项和参数设置,单击【完成】按钮,结束工艺过程参数的设置。
图3-1图3-2
图3工艺设置向导对话框
11.分析计算
双击方案任务视图中的“立即分析”。
系统弹出信息提示对话框,单击【确定】按钮开始分析。
12.结果查看
在方案任务视图中,选择要查看的结果进行显示。
13.结果输出
执行【报告】→【报告生成向导】命令,系统弹出“报告生成向导”对话框,如图4所示,选择方案,要导出的数据类型以及报告的形式。
图4-1图4-2
图4-3
图4报告生成向导
在实际模拟过程中,很多情况需要手动的方法创建浇注系统,下面将演示浇注系统手动创建方法和操作步骤。
手动创建流道的方法有两种:
一种是使用直线创建,另一种是使用柱单元创建命令。
本此上机实践浇注系统采用直线创建方法。
8.浇注系统
执行【建模】→【移动/复制】→【平移】命令,系统弹出如图5所示对话框,在输入参数下面,“选择”输入欲设浇口的节点,在“矢量”内输入节点要移动的距离,勾选“复制”,根据实际情况选择复制的“数量”。
图5图6
执行【建模】→【创建曲线】→【直线】命令,系统弹出如图6所示对话框,在输入参数下面,“坐标”内输入刚创建的两个节点,在选择选项下面,“创建为”内冷浇口,设计冷浇口的属性,如图7所示,
图7冷浇口属性
执行【建模】→【创建节点】→【按偏移】命令,系统弹出如图8所示对话框,在输入参数下面,“基准”输入节点,在“偏移”内输入节点要偏动的距离,在“节点数”内输入要偏动节点数量。
执行【建模】→【创建曲线】→【直线】命令,系统弹出如图6所示对话框,在输入参数下面,“坐标”内输入创建的两个节点,在选择选项下面,“创建为”内冷流道,设计冷流道的属性。
执行【建模】→【创建节点】→【按偏移】命令,系统弹出如图8所示对话框,在输入参数下面,“基准”输入节点,在“偏移”内输入节点要偏动的距离,在“节点数”内输入要偏动节点数量。
执行【建模】→【创建曲线】→【直线】命令,系统弹出如图6所示对话框,在输入参数下面,“坐标”内输入创建的两个节点,在选择选项下面,“创建为”内冷主流道,设计冷主流道的属性。
完成上述操作后出现如图9所示的流道系统。
执行【网格】→【网格生成】命令,得到如图10所示的流道系统。
图8图9图10
四、出现的问题及解决方法记录
上机实践三:
单动拉伸模拟
一、目的
1.熟练DYNAFORM软件能进行板材哪些成型类型模拟。
2.熟练掌握利用自动设置进行单动拉伸成型操作方法。
3.熟练掌握利用手动设置进行单动拉伸成型操作方法。
4.熟练掌握单动拉伸成型过程仿真结果的后处理操作方法。
二、内容
1.采用pro/E三维绘图软件建立三维模型,并导出。
2.利用DYNAFORM软件中提供的自动设置进行单动拉伸成型仿真。
3.利用手动设置进行单动拉伸成型仿真。
4.对单动拉伸成型进行后处理并将结果导出。
三、上机实践
启动eta/DYNAFORM
一)选择菜单File-Open…打开文件对话框
图1打开文件对话框图2打开的模型
打开文件路径,选择数据库文件single_action.df,单击打开按钮。
这时在屏幕上显示了如图2所示的模型。
二)设定单位
选择菜单【Tools】→【AnalysisSetup】。
选择缺省的单位作为单位系统。
缺省的单位系统是MM(毫米),TON(吨),SEC(秒)和N(牛顿)
三)自动设置
在进入自动设置界面之前,只需要对工具进行网格划分。
用户可以单击【Setup】→【AutoSetup】进入自动设置。
如图3所示。
图3AutoSetup菜单
单击AutoSetup菜单后,系统会弹出自动设置对话框,提示用户定义基本的设置参数。
如图4所示。
1.选择模拟类型:
Sheetforming;2.输入板料的厚度:
1.0(mm);3.选择工艺类型:
Singleaction;4.以凹模作为接触偏置的参考面,选择Die,如图5a所示;5.单击【OK】确认并进入到自动设置的主对话框中。
图4新建模拟对话框如图5a以凹模作为接触偏置的参考面
1)基本参数设置
进入【General】页面后,用户只需要将标题“Title”改成便于识别的名称即可,如single_action。
其他参数可以不作修改,采用软件推荐使用的缺省值。
如图6所示。
图6General页面
1.1板料定义
1.将页面切换到【Blank】页面。
单击自动设置页面上面红色的Blank标签,系统会进入到板料定义页面。
2.在Blank页面单击“Geometry”组中的Definegeometry…按钮。
如图7所示
图7板坯部件
3.系统弹出“Definegeometry”对话框,如图8所示。
4.单击【AddPart…】按钮,在弹出的对话框中选择BLANK零件层,如图9所示。
图8定义板坯图9选择零件层
5.选择零件层后单击【OK】按钮返回“Definegeometry”对话框。
在对话框中我们可以看到零件层BLANK已经添加在板料的零件列表中,如图10所示。
图10定义板坯零件列表图11板料材料及其属性定义
6.单击【EXIT】按钮退出Definegeometry对话框,系统返回Blank页面。
这时关于板料的基本参数都已经定义好,板料页面的标签由红色变为黑色,如图11所示。
定义板料后,系统自动为板料选择一种缺省的材料及相应的属性,如图11所示。
我们可以单击【BLANKMAT】按钮对材料进行重新定义。
单击【BLANKMAT】按钮弹出如图12所示的材料对话框。
单击“MaterialLibrary…”按钮,这时系统弹出如图13所示的材料库,选择美国材料数据库,我们可以根据需要选择与零件匹配的材料模型及材料。
选择完成后,单击【OK】返回AutoSetup主界面。
图12板料材料定义图13材料库对话框
1.2工具定义
1.将页面切换到Tools页面。
单击自动设置页面上面红色的【Tools】标签,系统会进入到工具定义页面。
2.为了方便工具单元的选择和定义,我们最好将板料零件层关闭。
单击工具栏中按钮,然后单击零件层的BLANK,将板料零件层关闭。
3.单击【OK】按钮退出零件层开/关对话框。
在工具页面的左边,系统默认定义了三个工具,die、punch和binder。
用户可以分别为三个工具定义零件。
4.将当前工具切换到die。
在左边的工具列表中选择die,然后在界面上选择几何定义下面的红色“Definegeometry…”按钮,对工具die进行定义。
如图14所示。
图14die工具定义
5.系统弹出Definegeometry对话框。
在Definegeometry对话框中单击【AddPart…】按钮,如图15所示。
6.在弹出的SelectPart对话框中选择DIE,如图16所示。
7.单击【OK】按钮返回Definegeometry对话框,DIE零件层已经加入到die的零件列表中,如图17所示。
8.单击【EXIT】按钮返回Tools页面。
这时有关die的工具几何已经定义完成,die的标签由红色变为黑色,如图18所示。
9.在左边的工具列表中单击punch,将当前工具切换到punch,下面进行工具punch的几何定义。
10.仅显示DIE零件层,并设置为当前零件层。
单击punch页面中红色的Definegeometry…按钮。
系统弹出Definegeometry对话框,如图19所示。
图15定义工具几何图16选择零件层图17定义几何零件列表
图18die工具定义
11.单击Definegeometry对话框中的【CopyElem…】按钮。
系统弹出如图20所示的对话框。
12.在CopyElement对话框中单击【Select…】按钮,选择需要复制的单元。
图19定义几何对话框图20复制单元对话框图21选择单元
13.在SelecteElements对话框中选择DISPLAYED按钮选择所有的单元,接着选中Exclude选项,使用Spread工具选择压料面,这时程序提示有15089个单元已经被选中,如图21和图22所示。
系统会将这些单元copy到一个默认的零件层中,并自动将这个层加入到punch的几何列表中。
14.单击【OK】按钮退出SelecteElements对话框。
图22加亮显示选中的单元图23复制单元对话框
15.单击【Apply】按钮,这时所选择的单元将复制到一个新的零件层中,如图23和图24所示。
图24复制到新层的单元图25定义几何零件列表
16.单击CopyElement对话框中的【Exit】按钮退出。
这时在工具几何列表中一个自动生成的名为OFFSET00的零件层被添加进来,如图25所示。
17.单击【Exit】退出工具几何定义对话框并返回Tools页面。
这时punch工具标签由原来的红色变为黑色,表示punch工具已经定义完成,如图26所示。
图26punch工具定义图27选择单元
18.仅显示DIE零件层,并设置为当前零件层。
在Tools页面左边将当前工具切换到binder。
然后单击工具几何下面的红色Definegeometry…按钮。
19.同样单击【CopyElem…】按钮,在CopyElements对话框中选择【Select…】按钮来选择需要复制到binder中的单元。
如图20所示。
20.将单元选择方式切换到Spread工具方式。
然后选择工具的法兰面。
系统提示有2716个单元已经被选中,如图27所示。
21.单击【OK】按钮退出单元选择对话框。
在单元复制对话框中单击【Apply】按钮进行单元复制。
所有选中的单元将自动复制到一个新的零件层,如图28所示。
系统并且将这个零件层加入到binder几何列表中,单击【Exit】退出单元复制对话框。
22.单击【Exit】返回Tools页面。
所有的工具名称标签已经由红色变成黑色。
表示整个工具都已经定义完成,如图29所示。
图28加亮显示选中的单元图29binder工具定义
1.3工具定位
在所有的工具都定义完成之后,用户需要定位各个工具在的相对位置。
这一步是工具定义完成后必须进行的步骤,否则用户就可能得不到正确的结果。
此外,工具的定位跟每一个工具的工作方向都有很大的关系,因此我们在定位之前需要仔细检查每一个工具的工作方向。
默认情况下,如果用户使用程序设置的工序模板,那么默认的工作方向就不需要修改。
对于特殊的方向,用户需要自己来调整。
1.单击【Tools】页面右下角的【Positioning…】按钮进入工具定位对话框,或者在菜单栏单击【Tools】-Positioning…。
2.这时由于还没有对工具进行定位操作,所以所有的工具在原始位置。
工具后面的输入框中显示都是0,如图30a所示。
3.选择Blank选项中on后面的punch作为自动定位的参考工具。
也就是说在自动定位操作中,此工具是固定不动的,然后激活Tools中,die和binder后的复选框,所有的工具和板料进行自动定位。
4.这时所有的工具和板料都会自动定位到一个合适的位置。
并且在自动定位对话框中,每一个工具和板料后面显示自动定位后该工具或板料相对于原始位置沿工作方向移动了多少距离,如图30b所示。
图30a工具定位前图30b工具自动定位后
5.在屏幕右下角的显示选项(DisplayOptions)中,关闭线(Lines)和曲面(Surfaces)的显示。
如图31所示。
图31显示选项
6.单击工具栏中的按钮。
屏幕上会显示工具和板料定位后的相对位置。
如图32所示。
图32定位后的工具和板料的相对位置
7.用户单击工具定位对话框中的【OK】按钮保存当前对工具的定位设置并返回AutoSetup主界面。
1.4工序定义
工序定义的目的是方便用户设置当前模拟需要的工序个数、每一个工序所需的时间以及工具在每一个工序中的状态等等。
用户可以单击设置主界面上Process标签进入工序设置界面。
用户只需要在新建一个设置时选择了程序内置的设置模板之后,程序会自动添加一些必要的工序。
对应典型的程序,这些工序基本上不需要做修改或者修改很少就可以计算。
这样大大减少了用户设置的时间。
由于在前面选择的模板是单动(SingleAction)成形,因此成形默认产生了两个工序,一个压边工序,另外一个是拉延工序。
这两个工序都已经定义好,用户不需要做任何修改就可以进入下一步。
只需要检查自己设置的结果是否与图33一致。
1.在界面的左边工序列表中选择closing工序作为当前工序,检查默认的closing设置是否与图33a一致。
默认情况下应该是一致的。
2.在界面的左边工序列表中选择drawing工序作为当前工序,检查默认的drawing设置是否与图33b一致。
默认情况下应该是一致的。
图33a合模工序定义图33b拉延工序定义
1.5动画显示
现在所有的设置都已经完成,用户可以进行提交计算。
但是在提交计算之前,用户最好对设置的模型进行动画显示,以便检查各个工具所定义的运动情况。
1.选择菜单栏的【Preview】→【Animation…】。
如图34所示。
2.这时工具将以动画的形式显示其运动状态。
3.用户可以选中IndividualFrames,然后单击中的按
钮来显示一步一步的状态。
如图35所示。
图34显示动画菜单图35动画控制对话框
4.在屏幕上,系统会显示所有工具当前相对其初始状态的位置,如图36所示。
5.单击【Exit】按钮返回AutoSetup主界面。
图36工具运动到第3帧的模型图37任务菜单
1.6任务提交
在验证了工具运动的正确性后,我们可以对当前设置进行任务提交计算。
1.单击菜单栏的【Job】→【Options…】。
如图37所示。
2.系统弹出任务提交对话框,如图38所示。
单击【Ok】按钮完成选项设定。
图38任务选项对话框图39任务菜单
3.单击菜单栏的【Job】→【JobSubmitter…】,如图39所示。
弹出图40所示的另存为对话框,输入文件名并保存,默认情况下,文件位于工作目录下。
图40另存为对话框图41任务提交管理器
4.这时系统将当前的任务已经提交给Jobsubmitter进行统一管理了,如果在Jobsubmitter任务列表中,已经有其它的任务在计算,那么当前任务需要等待。
如果没有其它任务,那么系统就会弹出LS-DYNA的计算窗口,如图42所示。
图42求解器计算窗口
四)应用eta/POST进行后处理
eta/POST能够读取和处理d3plot文件中所有可用的数据。
除了包含没有变形的模型数据,d3plot文件还包含有所有的由LS-DYNA生成的结果文件(应力,应变,时间历史曲线,变形过程等)。
详细的使用方法请参考eta/POST在线帮助。
1)读入结果文件d3plot到eta/Post
单击eta/DYNAFORM主菜单上的【PostProcess】菜单启动eta/POST。
eta/POST缺省的安装路径是C:
\ProgramFiles\Dynaform5.6。
在这个目录下,双击执行文件EtaPostProcessor.exe也可以启动,或者从操作系统的开始菜单的DYNAFORM5.6程序组启动。
如图43所示。
后处理界面如图44所示。
图43后处理菜单
图44后处理界面图45打开对话框
1.在eta/Post中,选择菜单【File】→【Open】,打开如图45所示的对话框。
2.从文件列表中选择LS-DYNA的结果文件,包含d3p