PE管焊接操作方法》.docx
《PE管焊接操作方法》.docx》由会员分享,可在线阅读,更多相关《PE管焊接操作方法》.docx(10页珍藏版)》请在冰豆网上搜索。
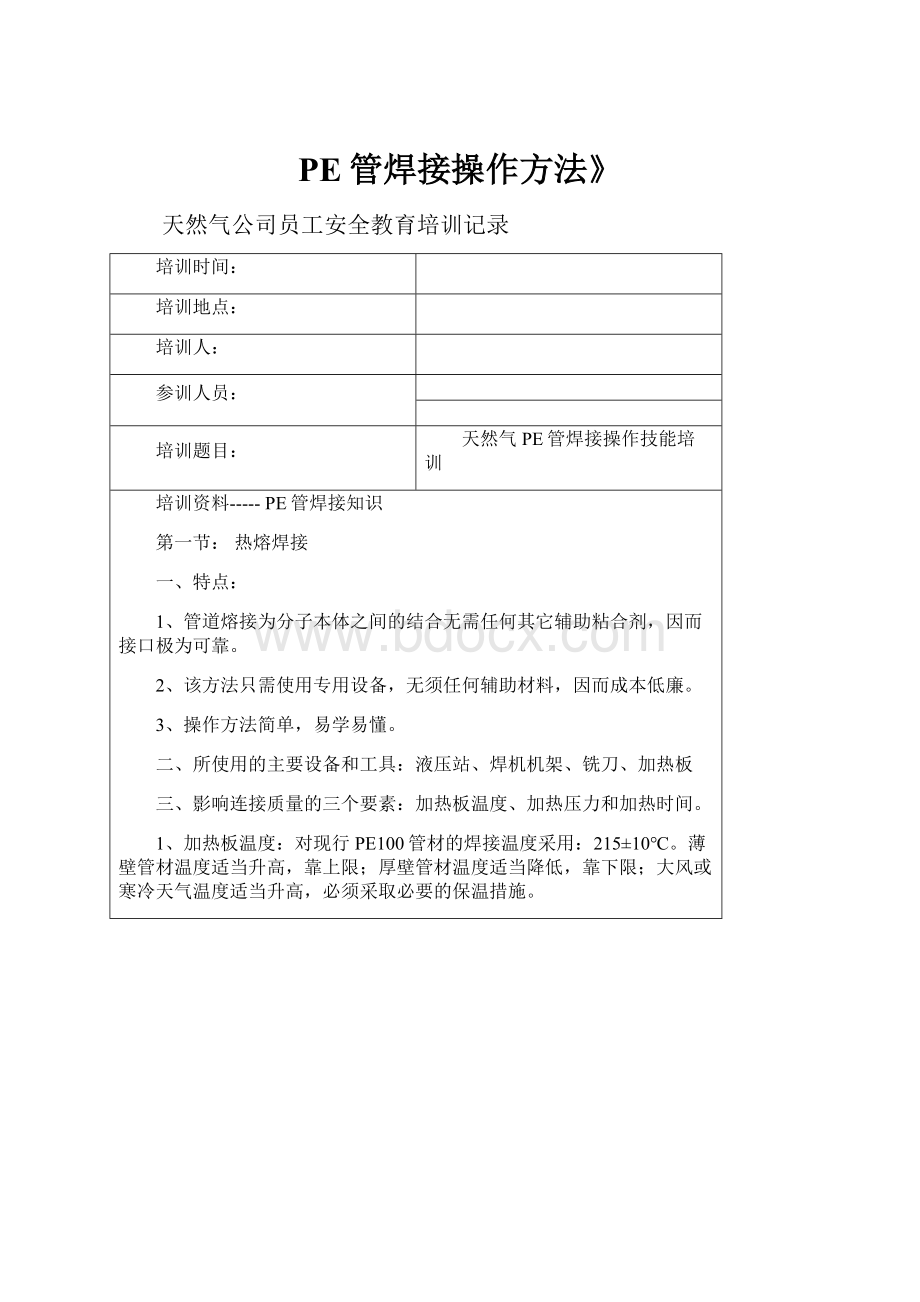
PE管焊接操作方法》
天然气公司员工安全教育培训记录
培训时间:
培训地点:
培训人:
参训人员:
培训题目:
天然气PE管焊接操作技能培训
培训资料-----PE管焊接知识
第一节:
热熔焊接
一、特点:
1、管道熔接为分子本体之间的结合无需任何其它辅助粘合剂,因而接口极为可靠。
2、该方法只需使用专用设备,无须任何辅助材料,因而成本低廉。
3、操作方法简单,易学易懂。
二、所使用的主要设备和工具:
液压站、焊机机架、铣刀、加热板
三、影响连接质量的三个要素:
加热板温度、加热压力和加热时间。
1、加热板温度:
对现行PE100管材的焊接温度采用:
215±10℃。
薄壁管材温度适当升高,靠上限;厚壁管材温度适当降低,靠下限;大风或寒冷天气温度适当升高,必须采取必要的保温措施。
2、加热时间和加热压力:
P(MPa)
0.15
0.01
0.00t(S)
图:
热熔焊接过程曲线示意图
2.1初始加热阶段(t1,P1)
将加热板放入两管端之间,加压到P1,加热时间为t1,其目的使初始熔融的物料在压力的作用下全部挤出,直到管材两端面每一点均和加热板紧密接触为止,保证下一步加热时,两管端能均匀吸热。
加热时间t1按卷边高度确定。
卷边高度emin=0.1×壁厚+0.5(mm)
2.2吸热阶段(t2,P2)
当卷边高度达到emin时,将压力由P1降至P2,继续加热t2时间,目的是保持微小压力,以保证管端与加热板表面接触,继续加热,使焊接管端产生足够的熔融物料。
吸热时间t2=壁厚×参数(PE80为10,PE100为12)
2.3切换时间(t2)
当加热时间t2达到后,迅速退开两管端,取出加热板,并立即合拢两管端。
这段时间尽可能缩短,最大不能超过t3(约6秒)
t3=3+0.01D(秒)D为管材公称外径
2.4保压冷却时间(P3、t4)
特别注意:
过大的压力将会使熔融物料全部挤出而形成夹焊。
四、热熔对焊焊口的目视检查标准:
1、翻边对称:
焊口具有沿管材圆周平滑对称的翻边,翻边最低处的深度不应低于管材表面。
2、对中整平:
管材管件连接时应尽可能的同轴,错位量不应超过管材壁厚的10%,沿相邻两组件翻边的外圆周的任何一处都不应超过该值。
3、翻边宽度:
环缝高度h=0.1~0.2s(s为壁厚道)
4、切除翻边:
两边存在均匀的卷边,卷边尺寸相近,表面饱满光洁,不能有气泡。
五、焊接:
1、检查核对焊接的管材规格、压力等级是否正确,表面是否有磕、碰、划伤,如伤痕深度超过管材的10%,应予以局部切除后方可使用。
2、用干净的布清除两管端的油污或异物。
3、将欲焊接的管材置于机架卡瓦内,使两端伸出的长度相当(在不影响铣销和加热的情况下应可能短),管材机架以外的部分用支撑物托起,使管材轴线与机架中心线处于同一高度,然后用卡瓦坚固好。
4、置入铣刀,先打开铣刀电源开关,然后在合拢管材两端,并加以适当的压力,直到两端均有连续的切屑出现后,撤掉压力,略等片刻,再退开活动架,关掉铣刀电源。
切屑厚度应为0.5mm左右,通过调节铣刀片的高度可调节切屑厚度。
5、取出铣刀,合拢两管端,检查两端对齐情况。
管材两端的错位量不应超过壁厚的10%,通过调整管材直线度各松紧卡瓦可予以改善;管材两端面间的间隙也不应超过壁厚的10%,否则应再次铣削,直到满足上述要求。
6、将加热板表面的灰尘和残留物清除干净(应特别注意不能划伤加热板表面的不粘层),检查加热板温度是否达到设定值。
7、加热板温度达到设定值,放入机架,施加规定的压力,直到两边最小卷边达到规定值(0.1×管材壁厚+0.5mm).
8、将压力减小到接触压力,继续加热规定的时间。
9、时间达到后,退开活动架,迅速取出加热板,然后合拢两管端,其时间间隔应尽可能短,最长不应超过切换时间。
10、将压力上升至规定值熔接压力,保压自然冷却。
冷却规定的时间后,卸压,松开卡瓦,取出连接完成的管材。
六、注意事项:
1、操作人员必须经专业培训并取得上岗资格证书才可以进行焊接操作。
2、操作人员应遵循该工艺规程和焊接工艺参数。
3、焊口的冷却时间可适应缩短,但应保证其充分冷却。
4、焊口冷却期间,严禁对其施加任何外力。
5、每次焊接完成后,应对其进行外观检验,不符合要求的必须切断返工。
第二节:
电熔承插连接
一、特点:
一)、优点:
1、使用设备少,操作简单;
2、极大地消除了人为因素影响,因而更为可靠;
3、熔接区域较对接更大,故而更为安全。
二)、缺点:
每个焊口都必须使用一个电熔管件,因而焊口成本较高。
二、所使用的主要设备和工具:
电熔焊机,刮削工具,夹持工具,切断工具,辅助工具(记号笔、直角尺、清洗剂、干净的抹布等),鞍型加紧定位工具,开孔工具。
三、电熔焊接的三要素:
1、输入电压:
一般是39.5V
2、加热时间:
一般在管件上都在标注:
以“秒(sec)”为单位。
3、冷却时间:
一般在管件上也有标注,以“分钟(min)”为单位。
四、电熔承插焊接的目视检查标准
1、对中:
按规范的连接程序检查管材和管件是否已经正确对正。
2、刮皮:
是否按规范的连接程序要求在管材的整个外圆周进行了刮皮,尤其要检查管材插入深度。
3、应检查插入的标记,确认插入到位。
4、熔融材料:
检查焊接时的熔融物料或电熔丝有没有从管件内挤出。
5、观察孔:
焊接完成后,观察孔应观察到有熔融柱挤出。
6、冷却时间:
达到规定的冷却时间前,不应移走夹具,不应对接头处施加任何外力。
五、电熔承插焊接工艺规程:
1、检查电熔管件有无断丝、绕丝不均匀等异常现象。
不合格的管件禁止使用。
2、核对欲焊接的管材规格、压力等级是否正确,检查其表面是否有磕、碰、划伤,如伤痕深度超过管材壁厚的10%,应予以局部切除后方可使用。
3、消除管材、管件焊接区域的灰尘或污物。
4、在管材端按照需插入管件长度用记号笔进行标注,刮除管材表皮(厚度约0.2mm)并修整光滑;刮削段长度应大于插入长度。
刮削后的管材表面不应被再次污染。
5、再次按插入长度对管材进行标注。
6、将刮削后的管材插入清洁后的管件到标注尺寸,必要时应予以夹持固定。
管材与管件之间一般以略微用劲即可插入为宜。
7、根据电熔管件的不同,选择合适的插头,进行正确的程序或参数设置。
8、将焊机输出插头插入管件插孔内并锁紧,确认设定程序或参数无误后,启动电熔焊机进行焊接。
9、在熔接过程中,操作者必须注意观察管件观察孔内熔体的流出情况,及时中断异常熔接状态。
10、焊接完成,待接头自然冷却后,取下电极插头。
六:
注意事项
1、操作人员必须经专业培训并取得上岗资格证书才可以进行焊接操作。
2、操作人员必须遵循该工艺规程和电熔管件所规定的焊接对数。
3、电熔管件必须在管材焊接端处理完毕后,才可打开包装进行安装。
4、无环境温度自动补偿功能的焊机,在设置加热时间时,应予以必要时间补偿,具体参照管件使用说明书。
5、启动电熔焊机前,应再次检查管材插入长度是否非达到标注尺寸,否则,可能因插装不当造成不良熔接。
6、接头冷却期间,严禁对其施加任何外力。
第三节:
电熔鞍型连接
一、电熔鞍型和鞍型三通的目视检查标准
1、刮皮:
是否整个鞍型焊接区域都进行了刮削。
2、外型检查:
鞍型或鞍型三通的出口应置于管材中心线,管壁不能有塌陷。
3、熔融材料:
在任何位置焊接过程中的熔融物料都不应从管件内部流出。
4、观察孔:
焊接完成后,观察孔应达到规定的要求(即在加热过程中,观察孔中圆柱状突起应逐步增高,但不能有熔融物溢出)。
5、冷却时间:
使用专用夹具,直到规定的冷却时间结束,并且不应对接头外施加任何外力。
6、辅助工具:
使用辅助工具时不应对管材周面造成损伤。
二、电熔鞍型焊接操作工艺规程
1、检查电熔管件有无断丝、绕丝不均匀等异常现象。
不合格的管件禁止使用。
2、核对欲焊接的管材规格、压力等级是否正确,检查其表面是否有磕、碰、划伤,如伤痕深度超过管材壁厚的10%,应予以局部切除后方可使用。
3、清除管材、管件焊接区域的灰尘或污物。
4、从包装袋内取出鞍型管件,将其置于管材上待焊接的位置,使用记号笔在管材上画了出管件外形。
然后将鞍型管件放入包装袋内,以免其内表面电容丝受到污染。
5、均匀的刮削焊接区域内所有管材表面,刮削厚度不应太厚,刮削范围应覆盖所有标记。
6、使用合适的溶解清洗剂和清洁、干燥、无油脂、无毛绒的棉布清洁刮削的荡然无存及鞍型管件(取出前一直放在包装袋内)的内表面。
7、对于不同的鞍型管件,应根据具体管件的使用方法说明进行紧固。
8、根据电熔管件的不同,选择合适的插头,进行正确的程序或参数设置。
9、将焊机输出插头插入管件插孔内并锁紧,确认设定程序或参数无误后,启动电熔焊机进行焊接。
10、在熔接过程中,操作者必须注意观察管件观察孔内熔体的流出情况,及时中断异常熔接状态。
11、焊接完成,待接头自然冷却后,取下电极插头。
12、达到管件标注规定的冷却时间后,参照使用说明,使用管件自带的刀具或专用刀具进行开孔。
三:
注意事项
1、操作人员必须遵循该工艺规程和电熔管件所标注的焊接参数。
2、无环境温度自动补偿功能的焊机,在设置加热时间时,应予以必要时间补偿,具体参照管件使用说明书。
3、焊接管件时,必须按照管件要求的固定方式或固定工具的说明书进行操作。
管件必须达到规定的冷却时间后方可进行开孔操作。
4、焊接区域冷却期间,严禁对其施加任何外力。
四、管道带压开孔操作工艺规程
1、在管材上选定焊接适当部位,清洁管材焊接区域。
2、以鞍型管件为样本,在管材上标好熔接区域,刮削此区域,要求刮削区域要稍大于标号区域。
3、清洁鞍型管件内表面,用专用夹具把鞍型管件在主管道上适当位置固定好。
用适当的压力压紧管件,做好焊接准备。
4、将电熔焊机和管件连接,进行焊接(注:
焊接过程严格遵守电熔焊接工艺规程)
5、在鞍型管件焊接冷却到规定时间后,用电熔套筒连接鞍型管件支线端和法兰头(记住套法兰片),冷却足够的时间。
6、连接法兰头球阀,注意放好密封圈。
注:
1)、待连接球阀在使用前,必须作压力试验。
2)、进行此操作时,用支撑物垫好阀门,以避免电熔焊接部位承受不必要的应力。
3)、注意阀门是否全部打开。
4)、注意阀门是否全部打开。
7、在主管道上系好控制架,以确保管件在固定架中心位置(注:
必须使用固体控制架,如果没有则必须在主管道上系环型夹具)。
8、把开孔工具固定在控制架上,调整机具在固定架上的位置,拧紧活结,把开孔器用螺栓固定在球阀上。
9、当所有螺栓坚固好后,确认开孔工具和球阀已连接好。
10、通过开孔器的进气孔,对此分支系统进行气密性试验,如测试成功,再进行下一步操作,关闭气孔活栓。
11、把开孔器钻头,从阀穿过直至接触管材表面,逆向旋转机械驱动装置,使其退到钻杆末端,将自动扳手套到钻杆上,缓慢转动钻杆,直到驱动装置头上的自锁杆能转动180度。
12、顺时针旋转自动扳手开孔。
开始时会遇到小小阻力,等钻头进入管壁时,阻力会迅速增加,当即将钻通时,阻力将缩小,继续旋转自动扳手直到全部穿透,驱动装置达到其最大行程,以免钻孔不彻底。
一旦主管被钻穿,此时打开气孔将有
五、电熔鞍型连接操作容易出现以下几个问题:
1、主管道刮削区域外表面与鞍型管件内表面不相吻合。
2、鞍型件在主管道上固定时两端机械固定夹持强度不统一。
3、刮削区域表面或鞍型件内表面受到污染。
地下燃气管道与建筑物构筑物或相邻管道之间的水平净距(米)
项目
地下燃气管道压力(MPa)
低压<0.01
中压
B≤0.2
A≤0.4
建筑物
基础
0.7
1.0
1.5
外墙面
—
—
—
给水管
0.5
0.5
0.5
污水、雨水排水管
1.0
1.2
1.2
电力电缆
直埋
0.5
0.5
0.5
在导管内
1.0
1.0
1.0
通信电缆
直埋
0.5
0.5
0.5
在导管内
1.0
1.0
1.0
其他燃气管道
DN≤300
0.4
0.4
0.4
其他燃气管道
DN≥300
0.5
0.5
0.5
热力管
直埋
1.0
1.0
1.0
在管沟内
1.0
1.5
1.5
电杆(塔)基础
≤35KW
1.0
1.0
1.0
>35KW
2.0
2.0
2.0
通信照明电杆(至电杆中心)
1.0
1.0
1.0
铁路路堤坡脚
5.0
5.0
5.0
街树(至树中心)
0.75
0.75
0.75
地下燃气管道与构筑物或相邻管道之间垂直净距(米)
项目
地下燃气管道(不有套管时,以套管计)
给水管、排水管或其他燃气管道
0.15
热力管、热水管的管沟(或顶)
0.15
电缆
直埋
0.50
在导管内
0.15
铁路(轨底)
1.20
有轨电车(轨底)
1.00