机器视觉大作业范本模板.docx
《机器视觉大作业范本模板.docx》由会员分享,可在线阅读,更多相关《机器视觉大作业范本模板.docx(10页珍藏版)》请在冰豆网上搜索。
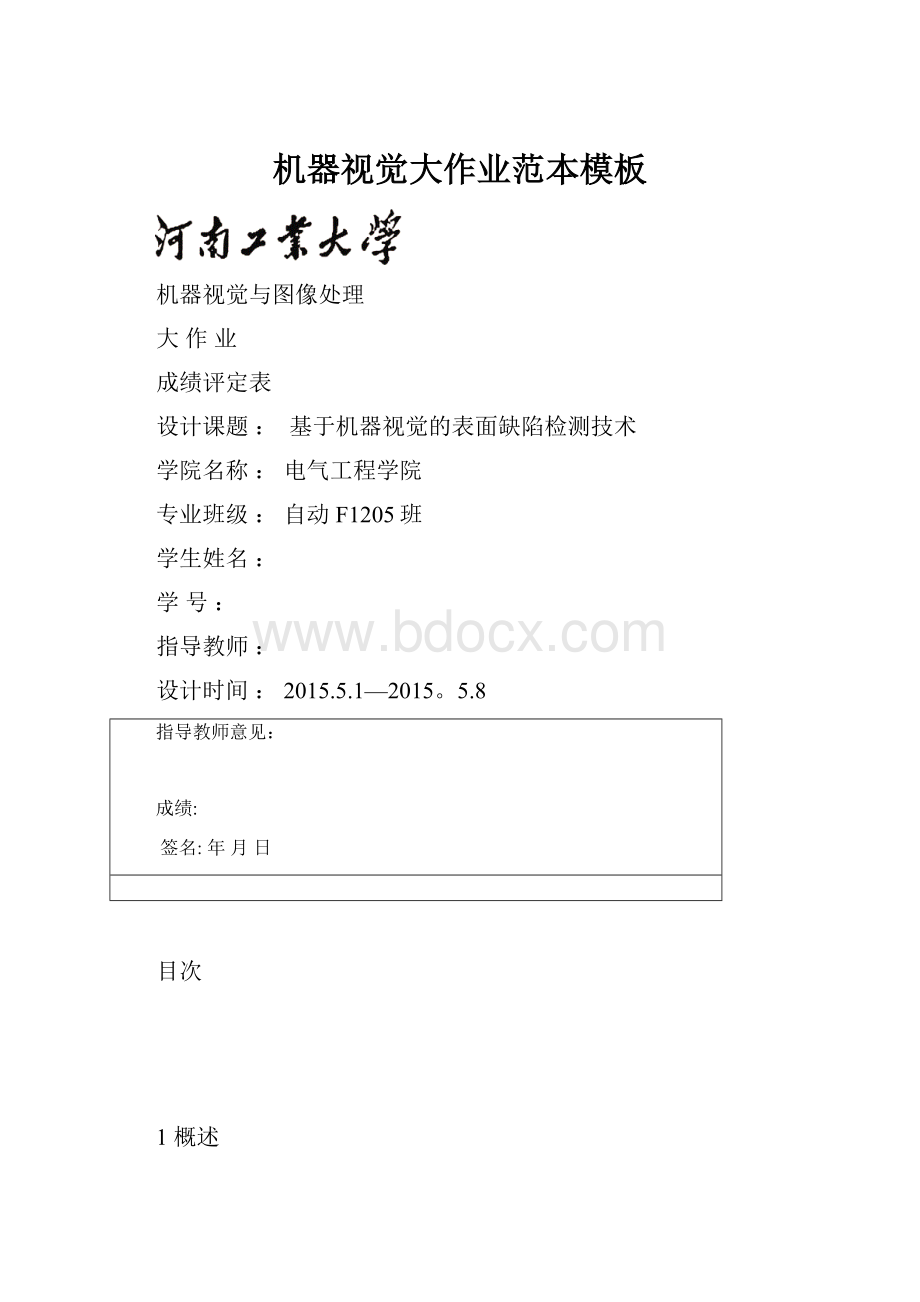
机器视觉大作业范本模板
机器视觉与图像处理
大作业
成绩评定表
设计课题:
基于机器视觉的表面缺陷检测技术
学院名称:
电气工程学院
专业班级:
自动F1205班
学生姓名:
学号:
指导教师:
设计时间:
2015.5.1—2015。
5.8
指导教师意见:
成绩:
签名:
年月日
目次
1概述
1。
1设计意义
传统的人工检测产品表面质量的方法不仅工作量大,而且易受检测人员主观因素的影响,容易对产品表面缺陷造成漏检,尤其是变形较小、畸变不大的夹杂缺陷漏检,极大降低了产品的表面质量,从而不能够保证检测的效率与精度。
而发展迅速的基于机器视觉的表面缺陷检测技术可以很好的解决这一问题。
机器视觉主要是采用计算机来模拟人的视觉功能,从客观事物的图像中提取信息,进行处理并加以理解,最终用于实际检测、测量和控制。
基于机器视觉技术的缺陷检测系统,由于其非接触检测测量,具有较高的准确度、较宽的光谱响应范围,可长时间稳定工作,节省大量劳动力资源,极大地提高了工作效率。
可对工件表面的斑点、凹坑、划痕、色差、缺损等缺陷进行检测。
所以,人工检测难以达到降低消耗、提高产品质量的目的,采用基于机器视觉的表面缺陷检测技术成为必需。
这也就是设计该基于机器视觉的表面检测控制系统的意义。
1。
2机器视觉与图像处理技术简介
图像处理技术简介:
在机器视觉系统中,视觉信息的处理技术主要依赖于图像处理方法,它包括图像增强、数据编码和传输、平滑、边缘锐化、分割、特征抽取、图像灰度处理、小波处理、图像识别与理解等内容。
经过这些处理后,输出图像的质量得到相当程度的改善,既改善了图像的视觉效果,又便于计算机对图像进行分析、处理和识别。
机器视觉技术简介:
机器视觉是将图像处理、计算机图形学、模式识别、计算机技术、人工智能等众多学科高度集成和有机结合,而形成的一门综合性的技术.一般地说,机器视觉是研究计算机或其他处理器模拟生物宏观视觉功能的科学和技术,也就是用机器代替人眼来做测量和判断.机器视觉系统如图
图1—1机器视觉系统构成
机器视觉系统的特点是提高生产的柔性和自动化程度.在一些不适合于人工作业的危险工作环境或人工视觉难以满足要求的场合,常用机器视觉来替代人工视觉;同时在大批量工业生产过程中,用人工视觉检查产品质量效率低且精度不高,用机器视觉检测方法可以大大提高生产效率和生产的自动化程度。
而且机器视易于实现信息集成,是实现计算机集成制造的基础技术。
因此,在现代自动化生产过程中,人们将机器视觉系统广泛地用于工况监视、成品检验和质量控制等领域.
2基于机器视觉的表面检测控制系统的总体设计
该系统是由CCD摄像头、照明系统、图像采集卡、机械装置、主控计算机等部件组成,图3-1为系统结构图。
其工作过程是:
首先将工件送到CCD摄像头视场内;然后由成像系统和图像采集卡将图像采集到计算机内部;运用图像处理技术对采集到的原始图像进行预处理以改善图像质量,从中提取感兴趣的特征量;最后运用模式识别技术对取到得特征量进行分类整理以完成系统的检测。
下面分别介绍系统的各部分的组成及工作原理。
1234
5
61、CCD摄像头及照明系统2、图像采集卡3、主控计算
机4、分类机构5、工件6、传送装置
图2—1机器视觉系统结构图
2。
1CCD摄像头
CCD是一种半导体成像器件,具有灵敏度高、抗强光、畸变小、体积小、寿命长,抗震动等优点。
本系统采用的是国产MTV-1881EX型号的黑白摄像头,它的工作方式是将被摄物体的图像经过镜头聚焦到CCD芯片上,CCD根据光的强弱积累相应比例的电荷,各个像素积累的电荷在视频时序的控制下,逐点外移,经视频捕捉卡滤波、放大处理,A/D转换后形成视频信号输出.
2。
2图像采集卡
本系统采用的是大恒PCI—XR视频捕捉卡,具有高品质的视频采集性能,具备高速PCI总线,采集频率为3D帧/秒,显示画面流畅不间断;显示分辨率640X480。
动态捕捉影像以静态图像方式存盘,提供BMP,JPG,TIP,TGA等多种存盘格式。
其工作原理如图3-2所示:
图3—2VIDEO—PCI—XR图像采集片工作原理
四路复合视频输入经多路开关,软件选择其中一路作为当前输入,输出到A/D进行模/数变换,数字化的图像信号经各种图像处理后,利用PCI总线,传到VAG卡显示或计算机内存存储.由于要检测工件的两个表面,所以需要在硬件上使用两路视频输入,每路采集不同表面的图像。
采样频率在一定范围内可调,满足不同场合的需求。
2。
2.1视频输入信号及采样频率
凡符合PAL制式(625行,50场/秒)和NTSC制式(525行,60场/秒)的视频设备输出的图像信号均可作为该视频捕捉卡的输入源。
在一般情况下,摄像机、
录像机等视频设备均满足上述标准。
采样频率在一定范围内可调,满足不同场合的需求。
2。
2.2视频输入窗口和显示窗口
视频输入窗口是指数字化后的输入图像尺寸.在PAL制式,输入窗口最大尺寸为768X576。
在NTCS制式为64X480。
图像显示窗口是指在VAG显示器上显示的图像尺寸,其最大值不能超过输入图像窗口。
当图像显示窗口小于视频输入窗口时,有两种方法可以采用。
一种方法是减少视频输入窗口的大小,即重新设置起始行、终止行、起始列、终止列。
使视频输入窗口与图像显示窗口相匹配.处理后的结果显示的仅是全部输入图像的一个局部,这种方法称为裁剪。
另一种方法是采用对视频输入窗口采用抽点和抽行的方法减少其大小,即根据视频输入窗口和图像显示窗口的相对大小设置缩小比例系数,处理后的结果显示的是缩小的全部输入图像,这种方法称为比例缩小。
也可以将两种方法结合起来,达到所需要的结果.
2。
3软件设计
本课题中的图像处理算法均采用Matlab程序语言实现模拟,Matlab提供一个高度集成的、集科学计算、程序设计和可视化归于一身的.
为了设计出实用有效的软件,必须按照软件工程的理论,进行充分的分阶段的分析和设计。
采用模块化结构设计,其特点为:
1)可修改性。
对模块内部的修改,对模块外部没有影响;增加或删除几个模块,不影响整个程序;
2)可读性。
每个模块意义和职责明确,模块间的接口关系清楚,便于用户和设计人员进行系统代码的维护;
3)验证性.独立于其它模块,可单独验证一个模块的正确性,便于进行调试。
采用模块化原理使软件结构清晰,容易阅读理解和维护。
本系统中,按照算法要求设计了各子程序.
3表面缺陷检测软件设计
由于本系统是一个完整、实时的缺陷检测系统,需要系统从原始图像采集到图像预处理、阈值选取、分割,再到模式识别,最后到缺陷种类分选整套过程有一个全面、整体的设计。
系统主要有以下几个模块:
图像实时采集模块、图像预处理模块、阈值选取模块、图像测量模块、缺陷检测模块、缺陷识别模块,其过程如图4—1所示。
图3—1缺陷检测过程
3。
1图像实时采集模块
为了准确、及时获得图像的当前状态,需要不断地通过图像采集卡将CCD摄像系统的图像信息直接读取到计算机内存,在计算机内存中进行其他的后续处理,如:
图像滤波、图像测量、缺陷检测等等。
3.2图像预处理模块
为去掉噪声对图像的于扰,要将刚采集的图像数据进行预处理,如:
去除孤立点、平滑、滤波等;同时,还要对图像进行灰度调整,增加对比度,为后续的图像处理工作做准备,如图4-2所示。
图3—2原始图像及灰度调整后图像
经过预处理后,图像的对比度增加,拉伸了图像灰度,表现在灰度直方图上就是峰与峰之间的距离加大,便于选取分割阈值及后续图像分割,如图4—3所示。
图3-3灰度调整前及灰度调整后图像直方图
3.3阈值选取模块
阈值的选取对于分割图像、提取缺陷信息至关重要,其方法也很多,本系统采取利用图像的灰度直方图来选取阈值,如图4—4所示。
图3-4滤波前及滤波后的灰度直方图
3.4图像测量模块与缺陷检测模块
用于实际实验获得实验数据,进而对图像处理。
3。
5缺陷识别模块
经过以上处理,从原始图像中提取出了含有缺陷的图像信息,得到了目标缺陷。
为了把各种不同类型的目标缺陷分类,需要识别出它们之间的不同。
根据缺陷的形状信息,可以用一组描述特征来表示其特性。
选择区域描述特征,不但可以减少在区域中原始数据的数量,而且也有利于区别带有不同特性的区域。
同时,这些描述特征对于目标缺陷大小的变化、旋转、平移是不变的.
图4—26工件表面缺陷分类表示
鉴于工件表面缺陷图像不同特征之间有一定的相关性,为降低识别算法的复杂性,特征识别时采用阶层识别的方法.利用二叉树线性分类器,如图4—26所示,逐层选用不同的描述特征,选择描述特征的准则是同种特征值相差最明显的,保证描述特征具有较大相互独立性.描述特征的分类阈值由实验分析和特征分析结果得到,具体过程如下所述。
图4-27圆度判断
(1)圆度判断
圆度判断主要是针对掉角的缺陷,根据工件的特性,如图4-27所示,我们采取的方法:
首先遍历圆周,因为背景的灰度值是很低的,可以比较容易将工件和背景分割开,提取出工件的外形;然后计算圆周上各点到圆心的距离,并和半径比较,如果比半径小于某一个设定值时,认为该点不在圆周上,如果这样的点连续而它们个数超过掉角缺陷的设定值时,可以认为这个工件是不圆的。
如图4—28所示,半径的值并不是一条直线,而是一条曲线,甚至有些地方有凹沟,这
表明工件本身不圆。
我们可以利用这个数据曲线可以计算最小半径、掉角方向和掉角角度.
图4—28扫描工件外圆所得的数据
经过运算,可以得到如表4-1数据,根据圆度技术要求,设定合适缺陷阈值,可以把圆度上有缺陷的工件在识别其他种类缺陷之前剔出来.
(2)识别麻坑和掉角
麻坑和掉角区别就是麻坑在工件表面的内部,而掉角在工件表面的边缘。
利用不变矩,就可以计算出缺陷区域的形心坐标,判断缺陷区域是否在工件图像的边缘,如果在边缘,则可以确定是掉角;否则,是麻坑。
(3)识别刀纹、裂纹和划痕
刀纹一般宽度和长度较大,而且面积也大,不变矩长短径之比要比裂纹和划痕小,同时,缺陷区域的分散度和复杂度较大,综合利用这几点就可以确定刀纹.至于裂纹和划痕,在缺陷区域本身的形状上很难区分。
4总结
通过本次课程设计,对本课程应用于实际生产需求的作用有了更深的了解,同时,对机器视觉的图像处理技术更加熟练.在该课程设计的系统中具有非接触、不干扰生产过程的特点,具有很好的实用推广价值。
该系统采用黑白面阵CCD和多通道图像采集卡采集图像数据,提高了检测系统的速度并降低了对CCD性能要求,使系统在现有的条件下比较容易实现实时在线检测;采用自动选取图像分割阈值,降低了对实时环境的要求,提高了系统的可推广性;根据实际应用的阈值把工件信息从图像中提取出来并扫描工件在图像中的位置、尺寸信息,实现了系统的自动测量;利用自动选取的阈值对金属工件表面的图像进行二值化分割,再根据扫描得到的工件信息去除掉工件边缘的光圈,从而实现各种缺陷的自动提取,为缺陷类型的识别打下基础。
虽然图像测量与缺陷检测没有实际操作,可是,对整个产品表面缺陷检测系统运行流程有了简单的了解。
对课程实际的运用有了初步的认识。
5参考文献
[1]郑芳庭,利用图像处理技术测量板形零件参数的研究[D],上海,上海交通大学,2001
[2]郎锐,数字图像处理学[M],北京希望电子出版社,2008年12月第1版
[3]夏正良,数字图像处理[M],东南大学出版社,2007年6月第2版
[4]胡小峰,赵辉,VisualC++/Matlab图像处理与识别实用案例精选[M],人民邮电出版社,2004年9月第1版
[5]文库基于机器视觉的表面缺陷检测系统设计