毕业论文年产100万吨连铸坯的全连铸转炉炼钢车间工艺设计.docx
《毕业论文年产100万吨连铸坯的全连铸转炉炼钢车间工艺设计.docx》由会员分享,可在线阅读,更多相关《毕业论文年产100万吨连铸坯的全连铸转炉炼钢车间工艺设计.docx(56页珍藏版)》请在冰豆网上搜索。
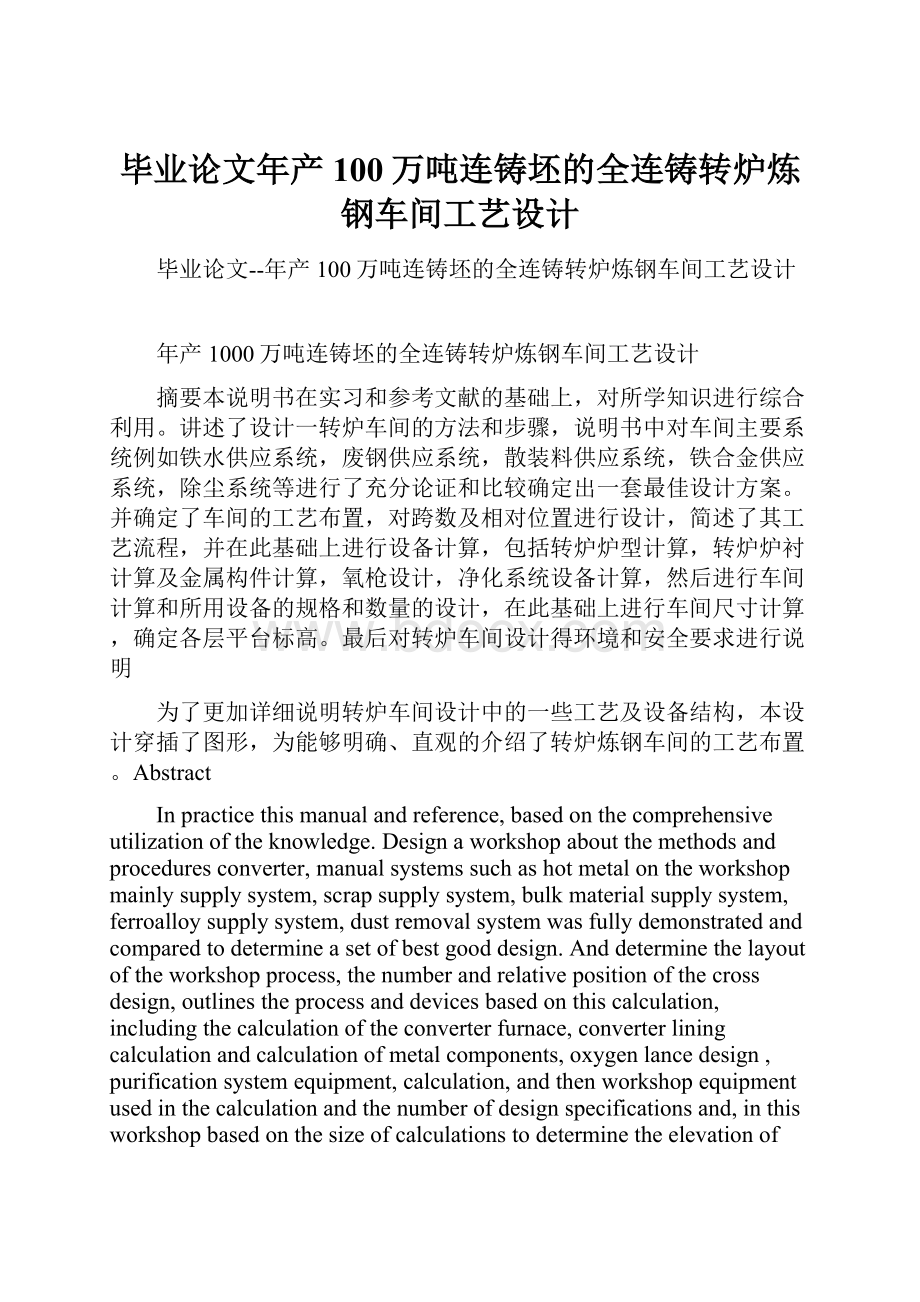
毕业论文年产100万吨连铸坯的全连铸转炉炼钢车间工艺设计
毕业论文--年产100万吨连铸坯的全连铸转炉炼钢车间工艺设计
年产1000万吨连铸坯的全连铸转炉炼钢车间工艺设计
摘要本说明书在实习和参考文献的基础上,对所学知识进行综合利用。
讲述了设计一转炉车间的方法和步骤,说明书中对车间主要系统例如铁水供应系统,废钢供应系统,散装料供应系统,铁合金供应系统,除尘系统等进行了充分论证和比较确定出一套最佳设计方案。
并确定了车间的工艺布置,对跨数及相对位置进行设计,简述了其工艺流程,并在此基础上进行设备计算,包括转炉炉型计算,转炉炉衬计算及金属构件计算,氧枪设计,净化系统设备计算,然后进行车间计算和所用设备的规格和数量的设计,在此基础上进行车间尺寸计算,确定各层平台标高。
最后对转炉车间设计得环境和安全要求进行说明
为了更加详细说明转炉车间设计中的一些工艺及设备结构,本设计穿插了图形,为能够明确、直观的介绍了转炉炼钢车间的工艺布置。
Abstract
Inpracticethismanualandreference,basedonthecomprehensiveutilizationoftheknowledge.Designaworkshopaboutthemethodsandproceduresconverter,manualsystemssuchashotmetalontheworkshopmainlysupplysystem,scrapsupplysystem,bulkmaterialsupplysystem,ferroalloysupplysystem,dustremovalsystemwasfullydemonstratedandcomparedtodetermineasetofbestgooddesign.Anddeterminethelayoutoftheworkshopprocess,thenumberandrelativepositionofthecrossdesign,outlinestheprocessanddevicesbasedonthiscalculation,includingthecalculationoftheconverterfurnace,converterliningcalculationandcalculationofmetalcomponents,oxygenlancedesign,purificationsystemequipment,calculation,andthenworkshopequipmentusedinthecalculationandthenumberofdesignspecificationsand,inthisworkshopbasedonthesizeofcalculationstodeterminetheelevationofeachfloorplatform.Finally,theconverterworkshopdesignedtoexplainenvironmentalandsafetyrequirements.
Foramoredetaileddescriptionofsomeoftheconverterprocessplantdesignandequipmentinthestructure,thedesigninterspersedwithgraphics,tobeabletoclear,intuitiveintroductiontotheprocessofconvertersteelmakingplantlayout.
KeyWords:
Steel,blowingconverter,continuouscasting,billet,slab,materialbalance,heatbalance,furnacedesign
1文献综述1
1.1国外炼钢技术的发展1
1.2钢铁工业在国民经济中的地位和作用1
1.3现代转炉炼钢工艺流程2
1.4我国氧气转炉炼钢技术展望2
0>.转炉大型化和流程优化2
.转炉高效化3
.钢水洁净化3
.控制模型化3
.资源综合利用化3
1.5现代转炉炼钢技术存在的问题4
2转炉炼钢厂设计方案5
2.1转炉车间组成5
2.2转炉座数、容量和车间生产能力的确定5
.转炉座数5
.车间生产能力的确定5
2.3主要钢种的选择6
2.4工艺流程6
2.5原料方案7
.铁水的供应7
.废钢的供应7
.散装料的供应7
.铁合金的供应8
2.6主厂房工艺布置8
.原料跨的布置8
.炉子跨的布置9
.精炼跨的布置9
3物料平衡与热平衡计算10
3.1物料平衡10
.需原始数据10
.衡基本项目11
.骤11
3.2热平衡计算18
.需原始数据18
.骤19
4顶底复吹转炉炉型设计23
4.1炉型选择23
4.2原始条件23
4.3主要参数的确定23
4.4炉衬各层填充材料选择27
5生产工艺设计28
5.1炼钢原料28
.28
.28
.28
.28
.28
.石29
.29
5.2装料制度29
5.3供氧制度29
.膛内氧气射流的特性29
.流对转炉熔池的作用30
.气转炉的氧枪操作30
5.4造渣制度30
.度的控制与石灰加入量的确定30
.灰熔解速度的因素31
.度的控制31
.化性的控制31
.及其控制32
.留渣操作32
5.5温度制度33
.度的确定33
.及其加入量的确定33
5.6终点控制和出钢34
5.7脱氧制度和合金化35
.气转炉炼钢的脱氧方法35
.的一般原理35
6转炉炉体金属构件设计37
6.1炉壳设计37
6.2支撑装置设计37
6.3倾动机构的设计38
7氧气转炉供氧系统设计39
7.1氧气的供应39
.钢车间需氧量计算39
.能力的选择39
7.2氧枪设计39
.型与选择40
.计40
7.3氧枪枪身设计41
.层尺寸的确定41
.度的确定42
7.4转炉底部供气构件设计42
.类42
.量43
.件43
.件布置43
8转炉车间烟气净化与回收44
8.1转炉烟气与烟尘44
.特征44
.特征44
8.2烟气净化方案选择44
.近烟气处理方法44
.气净化方法45
8.3烟气净化系统45
8.4烟气净化回收系统主要设备45
.45
.尘器46
.46
车间主要设备的选择47
9.1原料跨47
.的设计47
.斗的计算48
9.2转炉跨48
.48
.量的确定49
9.3精炼跨49
9.4连铸跨50
.生产:
尺寸为170mm×1500mm50
.生产:
尺寸为150mm×150mm53
.艺参数的确定54
.主要工艺参数的确定54
.的有关参数54
.重机的选择55
10主厂房工艺布置56
10.1原料跨间的布置56
10.2转炉跨间的布置58
.的布置58
.各平台的确定59
10.3连铸设备的布置62
11总劳动定员表65
1炼钢工序65
2连铸工序66
3燃气67
4给排水67
5热力68
6通风68
7电气68
8精炼工序68
9机修69
10检化室69
12主要技术经济指标70
致谢71
1文献综述10-6。
除了对钢水杂质元素控制外,还要对钢水的夹杂物进行控制,特别是氧化物夹杂。
复吹转炉可以明显降低转炉终点游离氧含量,减少氧化物夹杂的生产。
因此,转炉复吹技术的开发和应用,对于从源头上减少夹杂物有着重要作用。
.控制模型化
中国钢铁产品的质量稳定性不够,其原因有很多,但转炉靠工人操作引起波动大是其主要原因。
随着计算机技术的迅猛发展,炼钢模型的开发和利用不断进步。
目前,中国大部分转炉实现了模型控制。
转炉模型主要有转炉静态和动态模型、转炉自动吹炼模型、转炉合金模型等。
模型的应用对生产操作的稳定、提高劳动生产率、减少质量波动等起着促进作用。
因此,有必要继续优化、完善冶金模型,进一步提高模型控制精度,全面推进大、中型转炉的全自动不倒炉炼钢技术,进行智能型转炉炼钢。
.资源综合利用化
改变原有炼钢过程产生大量废弃物的概念,将炼钢过程产生的液态、固态和气态的物质定义为炼钢过程副产品加以利用。
1.5现代转炉炼钢技术存在的问题
现代转炉炼钢技术普遍存在的问题主要是随着社会对洁净钢的生产需求日益提高,迫切需要建立起一种全新的、能大规模廉价生产纯净钢的生产体系。
因此,如何降低生产成本、能耗,生产出大量的纯净钢以达到社会的需求是当前必须解决的问题。
2转炉炼钢厂设计方案
2.1转炉车间组成
现代氧气转炉炼钢车间一般由以下几个部分组成:
主厂房(包括炉子跨、原料跨、炉外精炼及钢包转运跨、浇铸系统各跨间);铁水预处理站及铁水倒罐间;废钢堆场与配料间;铁合金仓库及散装源料储存运输设施;中间渣场;耐火材料仓库;一、二次烟气净化设施及煤气回收设施;水处理设施;分析检测及计算机监控设施;备品备件库、机修间;生产必须的生活福利设施;水、电、气(氧气、氩气、氮气、压缩空气)等的供应设施。
车间的主要生产操作都集中在主厂房内进行,主厂房也包括原料跨、炉子跨和浇铸跨。
2.2转炉座数、容量和车间生产能力的确定
.转炉座数
转炉座数的确定与采用的吹炼制度有关,也与转炉的寿命有关。
由于现代的转炉炼钢都采用“溅渣护炉”操作,从而大大的提高了转炉的寿命,现代转炉寿命已经可以达到10.000~20.000炉,因此,本设计采用“三吹三”制度(即三个转炉都同时进行吹炼工作)完全能够保持生产的顺利进行。
.车间生产能力的确定
计算年出钢炉数
每一座转炉的年出钢次数N为:
式中T1――每炉钢的平均冶炼时间,min,参照表2-1,本设计中取每炉钢平均冶炼时间为42min;1440――一天的时间换算为分钟,min/d;
365――一年的日历天数,d/a;
――转炉作业率,本设计取87%。
则每一座转炉的年出钢次数N为:
(炉)
表2-1氧气转炉平均冶炼时间
公称容积/t153050100~120150200250300平均供氧时间/min12~1414~1515~1616~1818~1919~2020~2121~22平均冶炼时间/min25~2828~3030~3333~3636~3838~4040~4242~45计算转炉公称容量
转炉车间年产钢水量:
WnNQη
式中:
W――转炉车间年产钢水量;
n――车间经常吹炼炉子座数;
Q――转炉公称容量,t;
N――每一座转炉年出钢炉数;
η――连铸坯收得率,本设计取98%。
因此,转炉公称容量为:
(吨)
参照表2-2,本设计中取转炉公称容量为300吨。
采用“三吹三”制度。
不考虑转炉精炼收得率,验算连铸钢坯年产量:
所以,本设计所选转炉符合产量要求。
表2-2氧气转炉公称容量系列
转炉公称容量/t20153050100120150200250300最大出钢量/t30203660120150180220275320钢包容量/t30204060120150180220275320浇铸吊车起重量/t63/1680/20100/32180/63/20225/63/20280/80/20360/100/20400/100/20450/100/202.3主要钢种的选择
钢种:
普碳钢,低合金钢
产品规格:
方坯,板坯
2.4工艺流程
根据设计任务书的要求以及现代连铸技术的发展趋势,确定本设计方案的基本工艺流程如图2-1所示。
图2-1炼钢车间工艺流程图
2.5原料方案
.铁水的供应
铁水是转炉炼钢主要原料,高炉铁水采用混铁车运输,经预处理后转运兑入转炉。
.废钢的供应
废钢主要靠外购,部分本厂返分废钢。
生铁本厂供给,作冷却剂加入。
废钢要求:
表面清洁少锈、无油污、无泥沙
废钢中不得有铅、锡、砷等有色金属
废钢中硫、磷含量要低
外形尺寸要合格,不能过大
废钢中不得有密封容器、易燃易爆物品和毒品
废钢管理要求:
入场后,分类存放
清除处理,清除油污、泥沙等杂质和有色金属、毒品
使外形尺寸合格
炼钢车间,在原料跨一端单独设废钢间,按每炉需用量装入废钢,料斗送到炉前。
废钢一次一斗装入。
.散装料的供应
散装料包括:
石灰、白云石、萤石、铁矿石、焦炭等。
供应系统包括散装堆场,地下料仓,由地下料仓送往主厂房的运料设施,转炉上方高位料仓,称量和向转炉加料的设施。
为了保证转炉正常生产,应设散装料堆场,尽可能靠近转炉。
各种料储量按20天考虑。
在靠近主厂房附近设置地下料仓,它兼有部分储存和转运作用。
地下料仓为地下式,便于火车或汽车或运输带自动卸料。
地下料仓量按3天考虑。
从地下料仓向高位仓供料采用全胶带运输。
往各高位料仓布料采用可逆活动胶带运输机。
运输能力按每日工作一个班(约7h)考虑。
设置高位料仓起临时储料的作用,并利用重力方式向转炉及时可靠的供料,保证转炉正常生产。
高位料仓沿炉子跨纵向布置,三座转炉共用一套高位料仓,这样可以相互支持供料,并避免由于转炉停炉后料仓内剩余石灰的粉化。
散装料的用途如下:
石灰:
主要是造渣材料。
石灰极易潮湿,故在入炉前须烘烤,以提高石灰的活性,有利于冶炼。
萤石:
用于稀释炉渣,提高炉渣的活性。
白云石:
用于提高炉渣的碱度,减小对炉衬的侵蚀。
铁矿石:
用作冷却剂。
.铁合金的供应
铁合金的供应一般由炼钢厂的铁合金车间,铁合金料仓及称量和输送设施等几部分组成。
铁合金主要用来调整钢液的成分、温度并进行合金化处理。
其主要作用如下:
硅铁:
用于合金化,也作脱氧剂。
锰铁:
用于合金化,也作脱氧剂。
根据碳含量可分为中碳、低碳、高碳锰铁,锰铁中碳含量越低,磷含量越低,价格越昂贵。
铝铁:
合金化材料,也作脱氧剂。
在铁合金车间内储存、烘烤及加工合格块度,按铁合金的品种和牌号分类存放,并相应保存好出厂化验单。
铁合金由铁合金车间运入转炉车间的方式为全胶带供料系统,这种系统工作可靠,运输量大,机械化程度高。
2.6主厂房工艺布置
.原料跨的布置
主要完成对铁水,加废钢和转炉炉前的工艺操作,在原料跨的两端分别布置铁水和废钢工段。
铁水供应方式采用300t混铁车,并进行铁水预处理。
该方案包括铁水预处理车间,倒渣站,铁水倒灌站。
铁水预处理车间和倒渣站位于炼铁车间与铁水罐站之间,且彼此平行布置。
经处理后的混铁车,每隔三次送到倒渣站倒渣。
铁水倒灌站设有两条运输线和与其垂直布置的受铁坑,受铁坑位于铁水线下面。
一个铁水坑由两个铁水转注位置。
铁水预处理的方式是混铁车喷吹法,同时脱硫脱磷。
废钢供应方式是在原料跨的一端外侧另建废钢间,废钢装入料斗并称重,然后料斗送进原料跨待用。
转炉渣罐的转运方式为将渣罐车横穿过原料跨,在主厂房之外的中间渣场处理。
.炉子跨的布置
炉子跨是车间中厂房最高、建筑结构最复杂和单位投资最多的跨间。
很多重要的生产设备与辅助设备都布置在这里,其中包括转炉、转炉倾动机构系统、散料供应系统和加料、供氧系统、底吹气系统、烟气净化系统,出渣、出钢设施、拆修炉设备。
炉子跨采用横向布置。
烟道和烟罩皆沿跨间朝炉后弯曲,一是便于氧枪和副枪穿过烟罩插入转炉内,二是有一个连续的更换氧枪的通道,换枪方便。
副枪布置在靠近烟道的一侧。
散装料的各个高位料仓沿炉子跨纵向布置,在其顶部有分配皮带机通过,高位料仓布置在紧靠烟道的后面,这样烟道倾角较大,不易积灰。
转炉烟气净化系统采用湿法文氏洗涤器,布置在炉子跨内。
转炉修炉方法采用上修法,烟罩下部可侧向移动。
.精炼跨的布置
精炼采用两个LF精炼炉,沿精炼跨纵向布置,LF炉支持于支架上,真空室旋转有两个工作位置:
钢水处理位置,真空室下降进行处理;准备工位,修砌、喷补真空室内衬、更换上升、下降管,预热、氧气供应。
氧气转炉炼钢要消耗大量的工业纯氧,为了适应氧气转炉炼钢工艺的要求,炼钢厂的供应系统一般是由制氧机、加压机、中压储氧罐、输氧管、控制闸阀、测量仪表和喷枪等主要设备组成。
氧枪升降装置布置于转炉上方,这样其结构简单,运行可靠,换枪迅速。
当氧枪烧坏时须及时更换,设置横移装置及换枪装置。
在横移装置上并排设有两套氧枪升降小车。
其中一套工作,一套备用。
氧枪和副枪平行插入炉内。
3物料平衡与热平衡计算
3.1物料平衡
.需原始数据
基本数据有冶炼钢种及其成分,金属料――铁水和废钢的成分。
终点钢水成分(表3-1),造渣用溶剂及炉衬等原材料的成分(表3-2),脱氧和合金化用铁合金的成分及其回收率(表3-3),其他工艺参数(表3-4)。
根据《毕业设计任务书》要求,本设计冶炼普碳钢、低碳钢,据此选定转炉冶炼钢种的牌号为Q235A。
表3-1钢种、铁水、废钢和终点钢水的成分设定值
成分含量/%
类别CSiMnPS钢种Q235设定值0.20.20.5≤0.045≤0.050铁水设定值4.180.820.620.2200.033废钢设定值0.160.270.530.0280.032终点钢水设定值0.08痕迹0.1860.0220.020CaOSiO2MgOAl2O3Fe2O3CaF2P2O5SCO2H2OC灰分挥发分石灰86.002.402.401.700.300.120.044.660.08石0.285.480.621.581.5287.800.880.121.48生白云石36.380.8225.580.9636.18炉衬1.182.9078.701.381.6214.10焦炭0.6081.5212.405.50
表3-3铁合金成分及其回收率
成分含量回收率
类别CSiMnAlPSFe硅铁―73.00,780.4,802.50,00.04,1000.05,10024,100锰铁6.58,900.4,7868,80―0.2,1000.1,10025,10010%C与氧生成CO2
表3-4其他工艺参数设定值
名称参数名称参数终渣碱度WCaO/WSiO23.5渣中铁损(铁珠)为渣量的6%萤石加入量为铁水量的0.4%氧气纯度99%,余者为N2生白云石的加入量为铁水量的2.7%炉气中自由氧含量0.6%(体积比)炉衬蚀损量为铁水量的0.4%气化去硫量占总去硫量的1/3终渣∑WFeO含量(按W(Fe2O3)1.35W(FeO)折算)15%,而WFe2O3/∑WFeO1/3。
即WFe2O35%,WFeO8.25
%金属中[C]的氧化物90%C氧化成CO,10%C氧化成CO2烟尘量为铁水的1.5%(其中WFeO为75%,WFe2O3为20%)废钢量由热平衡计算确定。
本计算结果为铁水量的12.76%,废钢比为11.32%喷溅铁损为铁水的1%C[C]→CO4.1090%3.6904.9208.610[C]→CO24.1010%0.4101.0901.500Si[Si]→SiO20.8200.9371.757入渣Mn[Mn]→MnO0.4600.1340.594入渣P[P]→P2O50.1980.2550.453入渣S[S]→SO20.0131/30.0040.0040.008[s]+CaO→CaS+O0.0132/30.009-0.0050.020CaS入渣Fe[Fe]→FeO1.10956/720.8630.1881.109入渣(见表3-8)[Fe]→Fe2O30.626112/1600.4380.2460.626入渣(见表3-8)合计6.8927.769成渣量4.559入渣组分之和由CaO还原出的氧量;消耗的CaO的量0.00956/320.016kg
表3-6炉衬蚀损的成渣量
炉衬蚀损量成渣组成/kg气态产物/kg耗氧量/kgCaOSiO2MgOAl2O3Fe2O3C→COC→CO2C→CO,CO20.4据表3-40.0040.0090.2360.0040.0050.414%90%28/12
0.1180.414%10%44/12
0.0210.414%90%16/12+10%32/12
0.082合计0.2560.1380.082表3-7加入溶剂的成渣量
类别加入量/kg成渣组分/kg气态产物/kgCaOMgOSiO2Al2O3Fe2O3P2O5CaSCaF2H2OCO2O2萤石0.40.0020.0030.0280.0080.0080.0050.0010.4400.005生白云石2.70.9100.6400.0200.0250.905石灰6.8766.044②0.1730.1670.1000.0330.0070.0090.0070.3090.002③合计6.9560.8160.2150.1330.0410.0120.0100.4400.0121.2140.002成渣量8.623注:
石灰加入量计算如下:
有表3-5――表3-7知,渣中已含CaO-0.016+0.004+0.002+0.9100.900kg。
渣中已含SiO21.757+0.009+0.028+0.0201.814kg。
因设定的终渣碱度R3.5;故石灰加入量为
设A石灰加入量,由
得上式
②为石灰中CaO含量-石灰中S生成CaS自耗的CaO量
③为CaO还原出的氧量,计算同表3-5的注
表3-8总渣量及其成分未注明单位/kg
炉渣成分SiO2MgOAl2O3MnOFeOFe2O3CaF2P2O5CaS合计元素氧化成渣量/kg1.7570.5941.109②0.626③0.4530.020石灰