塑料水杯模具设计.docx
《塑料水杯模具设计.docx》由会员分享,可在线阅读,更多相关《塑料水杯模具设计.docx(31页珍藏版)》请在冰豆网上搜索。
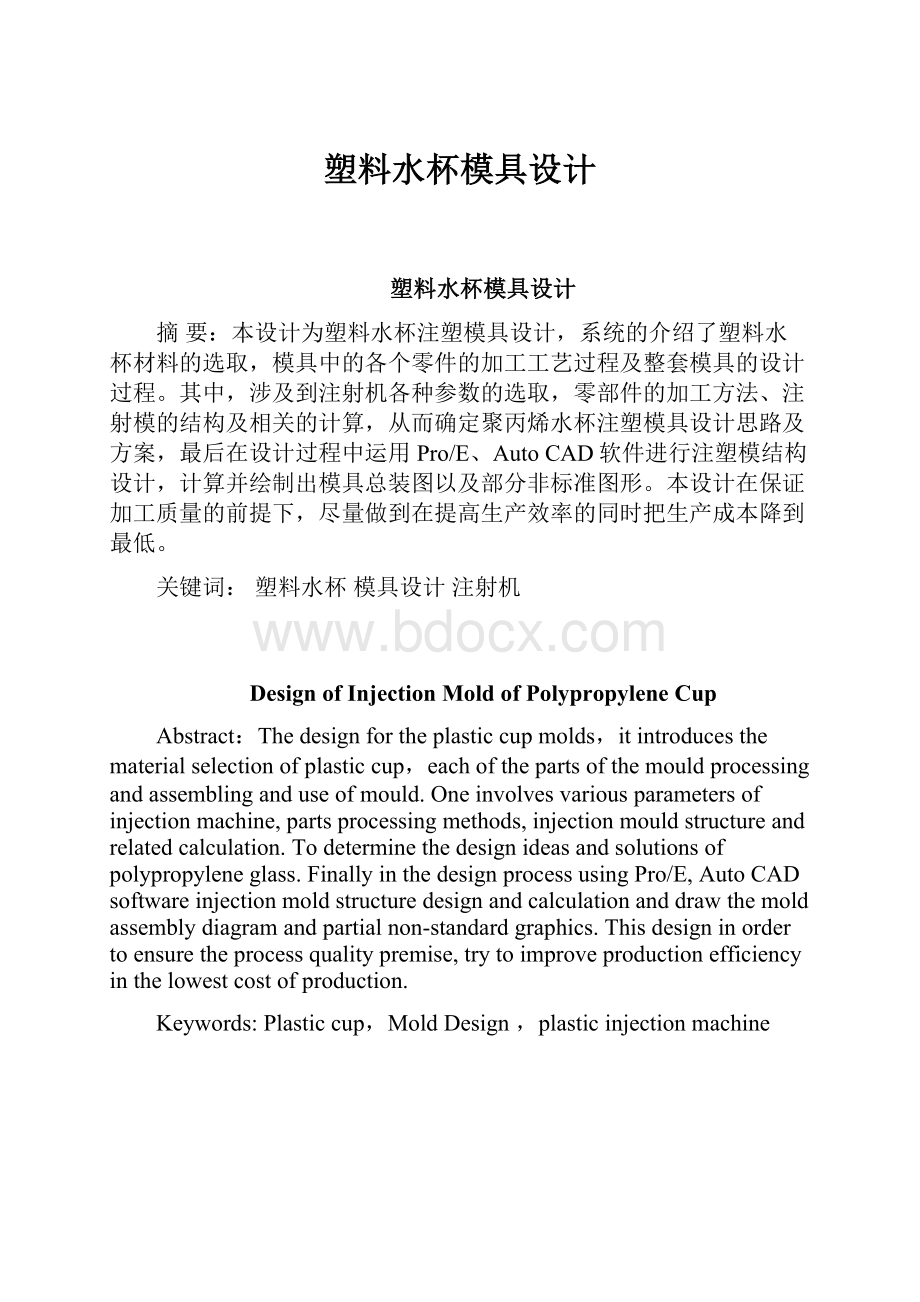
塑料水杯模具设计
塑料水杯模具设计
摘要:
本设计为塑料水杯注塑模具设计,系统的介绍了塑料水杯材料的选取,模具中的各个零件的加工工艺过程及整套模具的设计过程。
其中,涉及到注射机各种参数的选取,零部件的加工方法、注射模的结构及相关的计算,从而确定聚丙烯水杯注塑模具设计思路及方案,最后在设计过程中运用Pro/E、AutoCAD软件进行注塑模结构设计,计算并绘制出模具总装图以及部分非标准图形。
本设计在保证加工质量的前提下,尽量做到在提高生产效率的同时把生产成本降到最低。
关键词:
塑料水杯模具设计注射机
DesignofInjectionMoldofPolypropyleneCup
Abstract:
Thedesignfortheplasticcupmolds,itintroducesthematerialselectionofplasticcup,eachofthepartsofthemouldprocessingandassemblinganduseofmould.Oneinvolvesvariousparametersofinjectionmachine,partsprocessingmethods,injectionmouldstructureandrelatedcalculation.Todeterminethedesignideasandsolutionsofpolypropyleneglass.FinallyinthedesignprocessusingPro/E,AutoCADsoftwareinjectionmoldstructuredesignandcalculationanddrawthemoldassemblydiagramandpartialnon-standardgraphics.Thisdesigninordertoensuretheprocessqualitypremise,trytoimproveproductionefficiencyinthelowestcostofproduction.
Keywords:
Plasticcup,MoldDesign,plasticinjectionmachine
前言
随着社会生产力的发展,模具设计的发展进入了一个新的阶段。
过去在我国工业中,模具长期未受到重视,改革开放以来,塑料成型、家用电器、仪表等行业进入大批量生产,模具工业有一定发展,但高小多工位模压设备、以及供应高效冲压用的卷料设备仍然落后于需求,由于历史原因遗留下来的工厂大而全,专业化程度落后,这些不足的现象,需要我们有足够的认识,更需要我们从结构调整上下工夫。
在这次塑料模具设计的过程中,我们对塑料有了一个整体的认识与理解,并在设计过程中,对塑料模的性能,塑料的工艺性,以及注射模设计,塑料模制造工艺装配有了系统的了解。
此外,由于近一二十年来电子技术和计算机科学的迅猛发展,促使模具制造业发生着深刻的变化。
目前,数控机床已经成为模具加工的主要设备,继而,CAD/CAM技术在模具领域也得到应用。
在这次设计中,我们只是设计一个简单的塑料模具,也是对我们所学知识的巩固。
作为工业生产基础装备的模具,在我国民经济中占有重要地位,模具技术也成为衡量一个国家产品制造水平的重要标志之一。
我目前要解决的问题:
1.确定模具结构形式
2.模具设计的有关计算
3.绘制模具结构草图、装配图、零件图
4.撰写完备的设计说明书
设计过程是一个复杂的的过程,在查阅资料的基础上,结合所学知识,确定浇口形式,计算绘图尺寸。
在设计过程中我也遇到了很多困难,有专业性的也有非专业性的,解决这些问题让我更加深刻的掌握了模具设计的基础知识,也锻炼了自己的耐心与毅力。
在设计过程中,运用了大量的计算机辅助设计,提高了效率。
通过本次课程设计,使我加深了对模具方面的认识,培养了我独立思考、解决问题的能力
第一章制品成型工艺
1.1产品说明
本次设计的塑料制件为水杯,主要用于日常饮水之用,最重要的是无毒,其次要求水杯力学性能好,杯壁有一定的强度,质量要轻,而且要耐一定温度(120℃)。
1.2塑件材料的分析
根据上述产品说明,本次设计所选用塑件材料为聚丙烯(PP)。
以下是对该材料的具体分析。
聚丙烯,简称PP,是通用塑料中综合性能非常优异的一种材料。
近几年,PP工程塑料化的研究和开发取得很大进展,使PP在日常生活用品,汽车,家电等行业获得广泛的应用。
根据聚丙烯的立体构型,PP可分为等规PP和间规PP,目前工业上广泛应用的是等规PP,等规PP结晶度高,力学强度高;间规PP结晶度低,具有柔性,抗冲击性和透明性。
1.2.1性能与特点
聚丙烯的性质除了与分子量﹑分子量分布有关外,还与立体规整性有很大关系。
密度小,仅为0.89~0.91g∕c㎡,在热塑性塑料中,仅次于聚-4-甲基-1-戊烯。
制品的力学性能好,具有高的刚性和表面硬度,特别是有非常优异的奶弯曲疲劳性,能经受住几十万次的折叠弯曲而不破坏,很适合于铰链。
长期使用温度可达120℃,不受外力时最高可达150℃,是通用塑料中耐热性较高的一种材料。
低吸水性,突出的耐化学药品性,能耐80℃以下的酸﹑碱﹑盐及很多极性有机溶剂。
由于是非极性材料,因此有优良的电气绝缘性能。
1.2.2设计注意
耐日光性差,易发生热氧老化,用于室外需添加抗氧剂和光稳定剂。
低温耐冲击性差,抗蠕变性和耐磨性也不佳。
氧化性酸能促使PP降解,对脂肪烃﹑芳烃有不同程度的溶胀,而卤代烃对PP也有破坏作用。
避免与铜接触,铜盐溶液对有特殊的破坏作用,因此制品不宜有铜嵌件。
PP成型收缩率高,热膨胀系数也比较大,制品在热环境下受应力作用,要防止热应力脆化的发生。
与PE有相似之处,由于非极性的缘故,制品涂饰和粘结需要表面处理。
1.2.3材料收缩率
表1-1常用塑料的收缩率
塑料名称
聚乙烯
聚丙烯
聚氯乙烯
聚苯乙烯
聚碳酸酯
尼龙
ABS
聚甲醛
缩写
PE
PP
PVC
PS
PC
PA
ABS
POM
计算收缩率
1.5-3.6
1.0-2.5
0.6-1.5
0.6-0.8
0.5-0.8
0.8-2.5
0.3-0.8
1.2-3.0
对于聚丙烯水杯产品,材料为PP,理论收缩率为15/1000,而实际与理论是有区别的。
1.3塑件形状、尺寸大小的确定
塑料制件的形状在满足使用要求的前提下,应使其有利于成型,特别是应尽量不使用侧向抽芯机构,因此塑件设计时应尽量避免侧向凹凸形状或侧孔。
因为,侧向分型与抽芯机构的模具不但提高了模具设计与制造成本,而且还会在分型面上留下飞边,增加后加工的工作量。
某些制件只要适当改变其形状,即能避免使用侧向抽芯机构,使模具结构简化。
此设计中的塑料水杯,为圆柱形,高度为10.0mm.。
水杯外表面为平滑的曲面。
上底面与下底面有一定的脱模斜度,杯底有高度2.0mm的脚撑。
脚撑可以增加杯底的强度,使其放置时更平稳。
(1)壁厚的确定
壁厚是塑料制件结构设计的基本要素。
壁厚设计要考虑两方面的问题,一是壁厚尺寸的确定,二是遵循壁厚均一的设计原则。
壁厚均一的原则主要从工艺角度以及由工艺导致的质量方面的问题而提出来的,均匀的壁厚可使制件在成型过程中,熔体流动性均衡,冷却均衡。
厚薄部位在冷却收缩上的差异,会产生一定的收缩应力,内应力会导致制件在短期内或经过一个较长的时期之后发生翘曲变形。
壁厚不均时常采用的三种处置办法:
壁厚交接处的平稳过渡;
将尖角改为圆角处理;
厚壁部位减薄。
该产品图反映出,此塑料件壁厚为2.0mm,壁厚均匀,易于成型。
(2)水杯直径的确定
水杯的最小直径为58.0mm,最大直径为74.0mm,
1.4塑件尺寸精度和表面粗糙度
塑件的尺寸精度是指成型后所获得的塑件产品尺寸和图纸中尺寸的符合程度。
一般而言,塑件尺寸精度是取决于塑料因材质和工艺条件引起的塑料收缩率范围大小,模具制造精度、型腔型芯的磨损程度以及工艺控制因素。
而模具的某些结构特点又在相当大程度上影响塑件的尺寸精度。
故而,塑件的精度应尽量选择的低些。
对于本产品,图纸未注明尺寸精度,查表1-2,我们取IT7级精度。
表面质量一般要求较高,在Ra0.8
以上。
表面粗糙度是指加工表面具有的较小间距和微小峰谷不平度。
其两波峰或两波谷之间的距离(波距)很小(在1mm以下),用肉眼是难以区别的,因此它属于微观几何形状误差。
表面粗糙度越小,则表面越光滑。
表面粗糙度的大小,对机械零件的使用性能有很大的影响,主要表现在以下几个方面:
(1)表面粗糙度影响零件的耐磨性。
表面越粗糙,配合表面间的有效接触面积越小,压强越大,磨损就越快。
(2)表面粗糙度影响配合性质的稳定性。
对间隙配合来说,表面越粗糙,就越易磨损,使工作过程中间隙逐渐增大;对过盈配合来说,由于装配时将微观凸峰挤平,减小了实际有效过盈,降低了联结强度。
表1-2精度等级选用推荐值:
类别
`塑料品种
建议采用的等级
高精度一般精度低精度
1
PS
3
45
ABS
聚甲苯丙烯酸甲酯
PC
PSU聚砜
PF
氨基塑料
30%玻璃纤维增强塑料
2
聚酰胺
4
56
氯化聚乙醚
PVC硬
3
POM
`567
PP
PE低密度
4
PVC
`678
PE高密度
1.5脱模斜度
由于制品在冷却后产生收缩,会紧紧包住型芯或型腔突出的部分,为了使制件能够顺利从模具中取出或者脱模,必须对塑件的设计提出脱模斜度的要求,要求在塑件设计时或在模具设计时给予充分的考虑,设计出脱模斜度。
脱模斜度的设计与材料的性质、制品成型方法、制件的几何形状与尺寸、精度要求、模具的结构等因素有关。
一般脱模斜度的取值范围是30′~1°30′。
以下是确定脱模斜度的一些要点:
制品收缩率大,形状复杂且很不规则的,其脱模斜度宜取较大值;
材料性脆、刚性大、玻璃纤维增强的制品,脱模斜度要尽可能大;
尺寸较大或者尺寸精度要求高的制品,脱模斜度宜取小值;
塑件上带有表面花纹时,每蚀刻深度增加0.02mm,脱模斜度应大于1°;
制件内表面的脱模斜度应大于其外表面的脱模斜度。
下表为常用的脱模斜度如表1-1:
表1-1几种塑料的常用脱模斜度
制品斜度
聚酰胺
通用
聚酰胺
增强
聚乙烯
聚甲基丙烯酸甲脂
聚苯乙烯
聚碳酸酯
聚丙烯
脱模
斜度
型腔
20-40
20-50
20-45
20-
35-
35-40
25-45
型芯
25-40
20-40
20-45
30-40
30-40
30-50
20-45
本次设计的塑料水杯,内外表面均是光滑的,根据塑件材料的成型收缩率和塑件的高度综合考虑,选取的脱模斜度为:
型芯(
)型腔(
)
此结构本身就在常用的脱模斜度范围内,本身就有利于制品脱模,且此塑料制品的材料为PP,此产品能够脱模,故无需另行设计。
本次设计的水杯草图为
第二章注塑机的选用
2.1注射机分类及类型选定
注射机发展很快,类型不断增加,注射机的分类方法很多,根据注射装置和合模装置的排列方式不同,可分为卧式注射成型机、立式注射成型机、角式注射成型机和多模注射机等。
(1)卧式注射机卧式注射机是使用最广泛的注射成型设备,它的注射装置和合模装置的轴线呈一线并水平排列。
卧式注射机的优点是便于操纵和维修,机器重心低,比较稳定,成型后的塑件推出后可利用其重力自动落下,容易实现全自动化操作。
缺点是模具安装比较困难。
(2)立式注射机它的注射装置和合模装置的轴线呈一线并与水平方向垂直排列。
历史注射机的优点是占地面积小、模具拆装方便、安放嵌件便利。
缺点是塑件顶出后常需要用手或其他的方法取出,不易实现全自动化操作,机身重心较高。
机器的稳定性差。
(3)角式注射机它的注射装置和合模装置的轴线相互垂直排列,其优点介于卧、立两种注射机之间。
(4)多模注射机是一种多工位操作的特殊注射机。
注射机型号标准表示法主要有注射量、合模力、注射量与合模力同时表示等三种方法,本制品采用卧式注塑机。
注射量的确定:
塑料质量m最多为
凝料
按塑件质量的0.6倍计算
=8.019×0.6=4.811g
注射量;所需注射量小于或等于注射机最大注射量的80%
所需注射量为
注射机最大注射量为
=11.14
塑件和流道凝料在分型面上的投影面积及锁模力的计算。
流道凝料包括浇口在分型面上的投影面积
,
是每个塑料在分型面上的投影面积的0.2∽0.5倍,因此可用0.35
,所以
式中
=5803.191
式中型腔压力P约为注射压力的30%∽60%,注射压力是70—120MPa。
可查表而与保压压力相近,所以取pp的型腔压力为P=50MPa
选用注射机,根据每个生产周期的注射量和锁模力的计算值,可选用G54-S200/4200螺杆注射机。
注射机参数如下表所示。
表2-1G54-S200/4200注射机参数
额定注射量/cm3
200∽400
喷嘴孔直径/mm
4
螺杆直径/mm
55
拉杆空间/mm
290×368
注射压力/MPa
109
注射方式
螺杆式
锁模力/kN
2540
定位孔直径/mm
55
最大开模行程/mm
260
动定模固定板尺寸/mm
532×634
最大厚度/mm
406
最小厚度/mm
165
喷嘴圆弧半径/mm
18
2.2喷嘴尺寸确定
注塑机喷嘴头一般为球面,其球面半径R应与模具的主流道始端的球面半径吻合,以免高压熔体从隙缝处溢出,一般模具的主流道始端的球面半径应比喷嘴球半径大2~5mm,否则主流道内的塑料凝料无法脱出,其相应尺寸关系如图3-1。
图2-1喷嘴与浇口套的尺寸关系图
其中,R=r+(2~5)mm
D=d+(0.5~1)mm
2.3定位环尺寸
注塑机定模固定板上有一规定尺寸的定位孔,注塑模定模板上相应设计有定位环。
为了使模具的主流道的中心线与注塑机喷嘴的中心线相重合,模具定模固定板上的定位环或主流道衬套与定位环的整体式结构的外径尺寸d应与注塑机固定模板上的定位孔呈间隙配合,便于模具安装。
定位环的高度小型模具为7~10mm,大型模具为10~15mm,定位孔深度应大于定位环的高度。
2.4模具厚度
在模具设计时应使模具的总厚度位于注塑机可安装模具的最大模厚和最小模厚之间。
同时应校核模具的外形尺寸,使得模具能从注塑机拉杆之间装入。
模具闭合后的厚度(闭合厚度)Hm应在注塑机允许的最大模具厚度
和最小模具厚度
之间,即
式中:
2.5模具的长度与宽度
模具外形尺寸要与注塑机拉杆间距相适应,校核其安装时能否穿过拉杆空间在动、定模固定板上固定。
模具在注塑机动、定模固定板上安装的方式有两种:
用螺钉直接固定(大型注塑模多用此法)和用螺钉、压板固定(中、小型模具多用此法)。
采用第一种方法时,动、定模座板上的螺钉孔尺寸及间距应与注塑机对应模板上所开设的螺孔相适应(注塑机动、定模安装板上开着许多不同间距的螺钉孔,只要保证与其中一组相适应即可);若采用后一种方法,灵活性大,只需在模具动、定模固定板附近有螺孔就行。
第三章注射模设计步骤
3.1塑件成型方案的确定
通常,塑料按照性能分为热塑性塑料和热固性塑料两种,两种塑料的成型方式有所不同,对于热塑性塑料大多数都是注射成型,本产品聚丙烯,要求材料为PP,PP为热塑性塑料,且多为注射成型,根据实际,我们采用注射成型。
3.2型腔数目的确定
对于一个塑件的模具设计的第一步骤就是型腔数目的确定。
单型腔模具的优点是:
塑件精度高;工艺参数易于控制;模具结构简单;模具制造成本低,周期短。
缺点是:
塑件成型的生产率低、成本高。
单型腔模具适用于塑件较大,精度要求较高或者小批量及试生产。
多型腔模具的优点是:
塑件成型的生产率高,成本低。
缺点是:
塑件精度低;工艺参数难以控制。
模具结构复杂;模具制造成本高,周期长。
多型腔模具适用于大批量、长期生产的小塑件。
根据塑件的精度:
根据经验,在模具中每增加一个型腔,塑件的尺寸精度就要降低4%。
确定型腔数目的方法:
考虑到塑件的技术要求,本设计采用根据注射量方法确定型腔数目。
即:
式中,G—注塑机的最大注射量(200g)
—单个塑件的重量(25g)
—浇注系统的重量(14.9g)
由于该塑件尺寸形状很大,只能为一模1腔。
根据需要和后续加工的要求我们确定为平行于塑件的最大尺寸方向,中心分布。
3.3成型零部件的设计计算
3.3.1影响塑件尺寸精度的因素的分析
成型零部件的设计计算主要指成型部分,与塑件接触部分的尺寸计算。
而对于塑件尺寸精度的影响因素主要有以下方面:
塑件收缩率的波动塑件成型后的收缩变化与塑料的品种,塑件的形状、尺寸、壁厚、成型工艺条件,模具的结构等因素有关。
塑料收缩率波动误差为
PP的平均收缩率:
×100﹪=1.75﹪(
)
模具成型零件的制造误差一般成型零件工作尺寸制造公差值取塑件公差值的1/3-1/4,本次设计中取
还有模具成型零件的磨损和模具安装配合误差等,综上所述,塑件在成型过程所产生的尺寸误
差应该是上述各种误差的综合,即
式中
——塑件的成型误差;
——模具成型零件制造误差;
——塑料收缩率波动引起的误差;
——模具成型零件配合间隙变化的误差;
——模具装配引起的误差。
由此可见,塑件的误差为累积误差,由于影响因素多,因此塑件的尺寸精度往往较低,设计塑件时,其尺寸精度的选择不仅要考虑塑件的使用和装配要求,而且要考虑塑件在成型过程中可
能产生的误差,使塑件规定的公差值
大于或等于以上各种因素引起的累积误差
,即
由国家标准GB/T14486-1933可知,取
=1.40mm,故
mm
3.3.2各类成型零件的尺寸设计
凹模(型腔)
杯子四周就一个整体,且无螺纹和其它外部特征,可用整体式,而且加简单,
成本低。
=
(2)凸模(型芯)
(3)型腔深度尺寸的计算
(4)中心距尺寸的计算
二、成型零件强度及支撑板厚度
按刚度条件,侧壁和型腔底配合处间隙
已知u=0.25E=2.06
R=37mmr=30mmP=50Mpa,代入公式计算,得
(2)按刚度条件计算,型腔底板厚
3.4浇注系统设计
流道设计包括主流道、浇口的设计。
3.4.1主流道的设计
主流道通常位于模具中心塑料熔体入口处,它将注塑机喷嘴注出的塑料熔体导入分流道或是型腔。
由于主流道要与高温塑料熔体反复接触,所以在注塑模中主流道部分常设计成可以拆卸更换的主流道衬套。
在卧式或立式注塑机上使用的注塑模中,主流道垂直于模具分型面。
为了使塑料熔体平稳的向前流动,开模时塑料凝料能从主流道中顺利的拔
出,需将主流道设计成圆锥形,具有2°~4°的锥角,内壁有Ra0.8
以下的表面粗糙度,抛光时应沿轴向进行。
若沿圆周进行抛光,产生侧向凹凸面,使主流道凝料难以拔出。
同时浇口套与注塑机喷嘴接触频繁,为防止撞伤,应采取淬火处理使其具有较高的硬度(48HRC~52HRC)。
主流道的基本尺寸通常取决于两个双方面:
第一个方面是所使用的塑料种类,所成型的制品质量和壁厚大小。
其表如3-1:
表3-1制品厚度与壁厚的关系
制品质量/g
D1/mm
R/mm
0~20
3
0.5
20~40
4
1
40~150
5
1
150~300
6
2
300~500
8
2
500~1500
10
2
第二个方面,注塑机喷嘴的几何参数与主浇道尺寸的关系,如图3-1。
热塑性塑料的主流道衬套与注塑机喷嘴的尺寸:
主流道始端直径φB=φA+(0.5~1)mm,球面凹坑半径
mm,半锥角a为
,尽可能缩短长度L(小于60mm为佳)。
如图3-1:
(1)主流道尺寸设计
根据所选注射机,则流道小端尺寸为
d=注射剂喷嘴尺寸+(0.5~01)=4+1=5mm
主流道球面半径为
SR=喷嘴球面半径+(1~2)=18+2=20mm
(2)主流道村套形式
主流道长度取40mm,约等于定模板的厚度。
材料用T10A钢,热处理淬后表面硬度为53HRC-57HRC
图3-1主流道形状及其与注射机喷嘴的关系
(3)流道凝料体积
式中
(4)主流道剪切速率校核
有经验公式:
3.4.2浇口的设计
浇口是连接流道与型腔之间的一段细短通道,它是浇注系统的关键组成部分。
浇口的形状、位置和尺寸对制品的质量影响很大。
浇口的作用主要有以下几点:
1.熔体充模后,首先在浇口处凝固,当注塑机螺杆抽回时可防止熔体向流道回流。
2.熔体在流经狭窄的浇口时产生的摩擦热,使熔体升温,有助于充模。
3.易于切除浇口尾料,二次加工方便。
4.对于多型腔模具,用以平衡进料;对于多浇口单型腔模具,用于控制熔接痕的位置。
浇口的截面积通常为分流道的截面面积的0.03%~0.09%。
浇口截面积通常有矩形和圆形两种。
浇口长度约为0.5~2mm左右。
浇口具体尺寸一般根据经验
确定,取其下限值,然后在试模时逐步修正。
在注塑模具中常用的浇口形式有如下几种:
直接浇口、点浇口、潜伏式浇口、侧浇口、重叠式浇口、扇形浇口、平缝式浇口、盘形浇口、圆环形浇口、轮辐式浇口与爪形浇口、护耳浇口。
浇口开设的位置对制品的质量影响很大,在确定浇口的位置时应注意以下几点:
1.浇口应设在能使型腔各个角落都可以同时填满的位置。
2.浇口应设置在制品壁厚较厚的部位,使熔体从厚断面流向薄断面,以利于补料。
3.浇口的部位应选在易于排除型腔内空气的位置。
4.浇口的位置应选在能避免制品表面产生熔合纹的部位。
当无法避免产生熔合纹的产生时,浇口位置的选择应考虑到熔合纹产生的部位是否合适。
5.浇口的设置应避免引起熔体断裂的现象。
6.浇口应设置在不影响制品外观的部位。
7.不要在制品中承受弯曲载荷或冲击载荷的部位设置浇口,一般制品浇口附近的强度较差。
由于本次设计中选用的是推板推出,故选择直浇口为佳。
3.5冷却系统的计算
塑料模具的温度直接影响塑件的成型质量和生产效率。
由于各种塑料的性能和成型工艺不同,模具温度也要求不同。
因此在设计注塑模具时必须考虑用加热或冷却装置来调节模具的温度。
对于一般的热塑性塑料注射成型时只需考虑冷却装置。
3.5.1温度调节对塑件质量的影响
温度调节对塑件质量的影响主要有以下几个方面:
a.尺寸精度
利用温度调节系统来保持模具温度的恒定或采取较低的模温,可减少塑件成型收缩率的波动,提高塑件精度。
b.形状精度
模具型芯与型腔各部分温差过大,会使塑件收缩不均匀而导致翘曲变形,影
响塑件的美观和使用。
特别对于壁厚不一致和形状复杂的塑件,经常会出现因收缩不均匀而变形的情况,必须采用合适的冷却回路,使模具型腔各个部位的