风冷散热器相关技术浅析之散热片篇.docx
《风冷散热器相关技术浅析之散热片篇.docx》由会员分享,可在线阅读,更多相关《风冷散热器相关技术浅析之散热片篇.docx(41页珍藏版)》请在冰豆网上搜索。
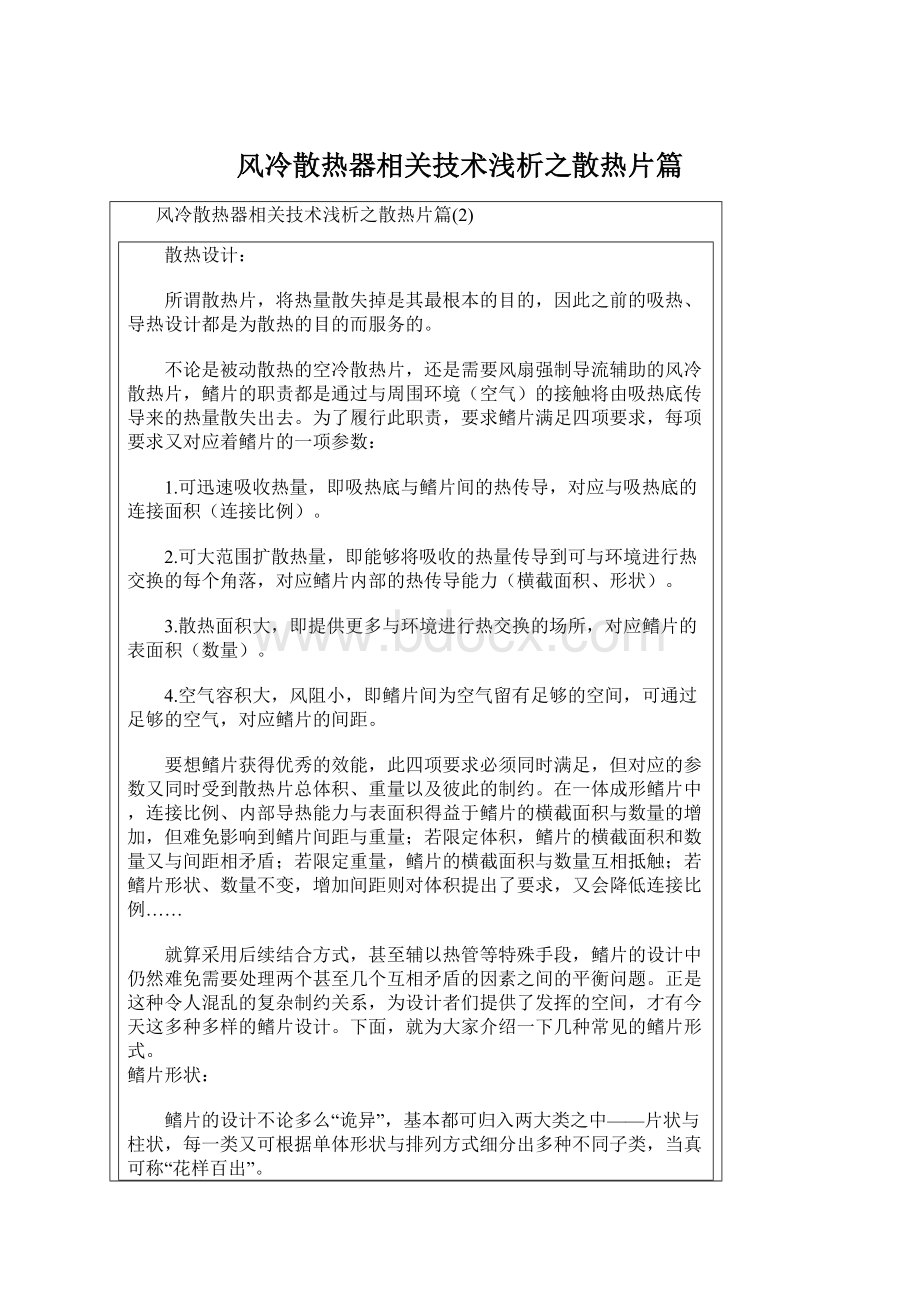
风冷散热器相关技术浅析之散热片篇
风冷散热器相关技术浅析之散热片篇
(2)
散热设计:
所谓散热片,将热量散失掉是其最根本的目的,因此之前的吸热、导热设计都是为散热的目的而服务的。
不论是被动散热的空冷散热片,还是需要风扇强制导流辅助的风冷散热片,鳍片的职责都是通过与周围环境(空气)的接触将由吸热底传导来的热量散失出去。
为了履行此职责,要求鳍片满足四项要求,每项要求又对应着鳍片的一项参数:
1.可迅速吸收热量,即吸热底与鳍片间的热传导,对应与吸热底的连接面积(连接比例)。
2.可大范围扩散热量,即能够将吸收的热量传导到可与环境进行热交换的每个角落,对应鳍片内部的热传导能力(横截面积、形状)。
3.散热面积大,即提供更多与环境进行热交换的场所,对应鳍片的表面积(数量)。
4.空气容积大,风阻小,即鳍片间为空气留有足够的空间,可通过足够的空气,对应鳍片的间距。
要想鳍片获得优秀的效能,此四项要求必须同时满足,但对应的参数又同时受到散热片总体积、重量以及彼此的制约。
在一体成形鳍片中,连接比例、内部导热能力与表面积得益于鳍片的横截面积与数量的增加,但难免影响到鳍片间距与重量;若限定体积,鳍片的横截面积和数量又与间距相矛盾;若限定重量,鳍片的横截面积与数量互相抵触;若鳍片形状、数量不变,增加间距则对体积提出了要求,又会降低连接比例……
就算采用后续结合方式,甚至辅以热管等特殊手段,鳍片的设计中仍然难免需要处理两个甚至几个互相矛盾的因素之间的平衡问题。
正是这种令人混乱的复杂制约关系,为设计者们提供了发挥的空间,才有今天这多种多样的鳍片设计。
下面,就为大家介绍一下几种常见的鳍片形式。
鳍片形状:
鳍片的设计不论多么“诡异”,基本都可归入两大类之中——片状与柱状,每一类又可根据单体形状与排列方式细分出多种不同子类,当真可称“花样百出”。
片状:
片状鳍片是非常典型的形状设计。
利用片状“宽广”的侧面与“单薄”的厚度,可以在相对狭小的空间内获得更大的表面积。
平行:
平行排列是片状鳍片非常典型的排列方式,是“经典中的经典”。
平行排列的鳍片,片间距离均匀,空间连贯,利于空气通过。
平行排列的片状鳍片最大的优势在于各鳍片形状相同或相似,排列整齐、规律,成形与结合工序相对简单,适合于工业化大规模生产。
风槽式:
鳍片与吸热底面垂直相连,空气由顶部进入,侧面流出(吹风),或由侧面流入,顶部抽出(吸风)。
空气由鳍片与吸热底形成的槽道中通过,且其间流动方向会发生变化,故而将之称为“风槽式”。
目前市场上绝大多数的散热片均系采用此种设计。
价格由高端到低端,材质由纯铜到铝合金,工艺由精密切削到铝挤压,都可见到风槽式鳍片设计的产品,可以说是“最经典”的设计。
风槽式鳍片设计的目标同样是增大散热面积,除了增大吸热底面积外,最重要的手段就是提高“瘦长比”——即鳍片高度与鳍片底部厚度的比值。
在不增大吸热底面积,不改变连接比例的情况下,瘦长比的提高可以增加鳍片的数量或高度,都可以加大鳍片总表面积。
当然,考虑到鳍片内部热量传导的要求,瘦长比也不应无限制的提高,当其超过一定限度时,鳍片的末端已经不能计入有效散热面积之内了。
这个限度的确定需要考虑到鳍片材质的热传导能力,例如铜质鳍片就可以比铝合金鳍片采用更高的瘦长比。
根据所采取的不同制造工艺,有的可以把鳍片间距做到很小,鳍片做到很薄而大幅增加鳍片数量,将散热片体积控制在较满意的范围内;有的则受到工艺限制,鳍片数量无法大幅增加,只能尽量增加鳍片高度,但散热片体积也随之增大。
如果考虑到对散热器工作噪音与风阻的影响,顾虑到风扇的性能,鳍片的数量与高度都不应过分增加,同样需要寻求一个性能最佳的平衡点。
此种风槽式经典设计已被沿用多年,而且目前及之后的一段时间内也是市场产品的绝对主流,但它却存在着一项设计者们一直寻求解决的弊端:
不论是吹风也好,吸风也好,在散热片的中心区域都会形成一个空气流动较少的高压区(吹风)或低压区(吸风),如果再加上轴流风扇轴心风力盲区的影响,此区域的范围有时可以达到散热片底面积的20%以上,倘若又遇到风扇性能不济,甚至可能整个鳍片底部区域的空气流动都非常微弱。
此处的空气受两侧气流的影响,运动非常混乱,虽然所形成的紊流可以与鳍片进行更多的热交换,但由于流动不畅,热量无法排出散热片外;而且,此处往往是发热设备(例如CPU核心)所处位置,是散热片热量最为集中的部分,如不加以处理,会对性能造成相当不利的影响。
虽然可以采用更大风压、更小甚至无盲区的风扇,尽量减小高压区(或低压区)的范围,但难免造成耗电的增加与噪音的增大,影响散热器整体的易用性。
针对这一问题,一些厂家采取了改进型的设计——增加吸热底中心位置的厚度,在空气沿鳍片流动的方向上形成坡道,既能够形成类似风道的导流作用,消除高压区(或低压区),又能够增加吸热底的热容量,并利用增大的连接面积将热量更加均匀的扩散到鳍片上。
ThermalRight的SLK系列就是此种设计的代表,其优秀的性能已经充分证明了设计的合理性。
此外也有利用热管将热量由吸热底中心直接传导到鳍片末端的设计:
同是出自ThermalRight的SP系列,曾经是一代风冷王者,当今热管散热器的盛行也不可否认有它的功劳在。
当然也可以在原本基础上进行简单改变而取得不错的效果,例如这种在平行鳍片的侧面开出几道风槽,令中心的高压(低压)区可以与外部空气连通,气流走向更接近于下文中采用柱状鳍片的情况,代价则是减少了表面积。
实际产品都是在表面积与空气流动间进行权衡后,才确定侧面风槽数量、宽度与排列位置的。
一般而言,对应发热设备的中心位置都会开出一条或对称的两条风槽,以达到中心“卸压”的目的。
作为最经典的一种鳍片设计,采用的产品也是目前市场上的绝对主流,涵盖各种档次与品牌,用户应改对判断其设计水平与特点的几大因素有所了解:
1.瘦长比——既然是设计中的诉求点,实际选购时自然也应关注,通常情况下越高越好,但不应超过一定限度。
2.连接比例——涉及到具体制造工艺间的差别,此处不便详细说明,但连接比例过小,即鳍片稀疏而单薄的产品无法提供较大的表面积,性能通常难以令人满意。
3.特殊设计——针对上文提到的弊端,如果实际产品能够采用一些特殊手段解决,在性能上必然能够取得较大的提升。
4.风扇搭配——根据鳍片的高度与密度,会对所搭配风扇提出一定要求:
鳍片高度高、密度大,则需要风扇具有较大的风压;鳍片数量多、厚度薄,则会产生较多的风噪,不利于满足静音需求。
风道式:
鳍片与吸热底可以采用多种方式连接,包括一体成形、直接连接,或者通过热管等手段间接连接;相对位置可以平行、垂直,或者置于与吸热底有相当距离的位置;共同点为,空气由一侧进入平行排列的鳍片所构成的风道,流过鳍片间的空隙,并与之进行热交换,再由另一侧排出。
鳍片的另外两侧闭合,或采用导流罩限制,空气流动过程中无法从其它途径流出,只能沿鳍片方向由一端流至另一端,故而将之称为“风道式”。
目前采用此种设计的产品主要是侧进风散热器、分离式热管散热器(即利用热管传热,鳍片与吸热底不直接结合)、及液冷、压缩机等的独立散热排。
相对而言,采用风道式设计的散热片定位较高。
采用大管径热管的AkustPipeTower,热管+风道式鳍片+侧吹风扇的典型产品。
风道式设计通常采用非常细薄的铜或铝合金片层叠焊接而成,片间距离可以非常小,因此可在小空间内安装大量的鳍片,获得巨大的表面积。
虽然鳍片数量众多,间距较小,但平行排列,且空气通过时无需改变方向,整体风阻很小,可轻松获得较大的风量。
此种设计由于鳍片细薄,内部导热能力不足,往往需要多个热量“输入点”才能发挥大表面积、大风量的优势,因此目前的产品中风道式鳍片设计主要配合热管或弯折的液体导管(液冷、压缩机等)使用。
能否有效利用巨大的表面积与风量正是风道式鳍片设计的重点所在,也是用户选购时应该注意的问题。
如果不能有效的将热量传导到鳍片的每个部分,那么众多大面积鳍片的末端部分就只是“摆设”,对散热效果起不到值得称道的帮助。
放射状:
鳍片与中心位置面积相对较小的吸热底连接,呈放射状向四周延伸,正是因此而得名。
空气由顶部流入,直接通过伸展而出的鳍片,或者在中心位置转为横向流动通过四周环绕的鳍片。
空气在流动过程中虽然可能发生方向改变,但转向角度并不大,且没有明显的阻碍,鳍片间的空隙也相对均匀、平顺,整体风阻较小。
采用放射状鳍片设计的散热片并不少见,从早年风行一时,PentiumIII玩家标配的“涡轮”,到现今正当红的Socket-T原配“太阳花”散热器,以及“花儿”一样的ZalmanCNPS7000系列,都当归为此类。
此外,还有一种将平行排列与放射状相结合的设计,被我们的一位编辑戏称为“鱼刺型”,细细看来,倒也确实贴切^_^。
放射状鳍片设计通常而言具有一个较为明显的特点——具有小而厚实的吸热底。
所有散热片都会汇聚至此,可以保证一定的储热能力,又可令热量均匀的传导到四周的鳍片上,有效利用鳍片的表面积。
根据空气流动则可分为纵向与横向两类——纵向气流方式的代表即“太阳花”与“鱼刺”-_-b,所采用轴流风扇的轴心部分正对吸热底位置,扇叶所带动气流直接通过四周的鳍片,直至遇到PCB板等阻碍才改变方向;横向气流方式的代表即早期的“涡轮”与ZalmanCNPS7000系列等,置于鳍片中间的轴流风扇将气流推向靠近吸热底相对密集的鳍片,一部分气流受到阻碍而转为横向流动,经过周围鳍片的直立部分。
放射状鳍片最大的优势在于对气流的干扰、限制很少,空气从各个角度沿鳍片的伸展方向流出,产生的风噪很小。
因此,放射状鳍片设计更加适合制造效能不俗的静音型散热器。
CoolerMaster的F71(“鱼刺型”的^_^)、Zalman的CNPS7000系列都是其中典范。
“太阳花”更是在驾驭Prescott的同时将噪音控制在不错的水平。
环形:
在内置风扇的放射状鳍片设计之上稍加变通,将鳍片改为套在风扇外侧的环形片状,并通过热管与吸热底相连,就得到了这种独特的环形片状鳍片设计。
目前采用此种设计的只有一线板卡大厂技嘉在“闲暇之余”推出的3D-Cooler一款。
3D-Cooler将风扇由传统的轴流风扇换为了出风更加平顺的涡轮扇叶。
没有导流罩的涡轮扇叶将顶部进入的空气依靠离心效应抛甩出去,经过环绕其周围的环形片状鳍片。
由于鳍片特殊的排列方式,无法与吸热底直接连接,为此,它采用了2根热管将热量由底部传导到鳍片的四角,令其均匀分布,有效利用众多鳍片的较大表面积进行热交换。
柱状:
柱状鳍片是与片状并驾齐驱的另外一种典型鳍片形状设计。
柱状鳍片与片状相比,在表面积上毫不示弱,而且可具有更大的截面积,内部导热能力更强,更有效的发挥大表面积的优势。
柱状鳍片相对片状最大的劣势在于鳍片单体成形复杂,造成加工成本过高,质量控制困难,不利于大量生产。
柱状鳍片设计较通常的片状鳍片可以获得更好的性能,这除了得益于更大的表面积与更好的内部导热能力外,更主要是来自柱状鳍片周围空气流动方式的优势。
在柱状鳍片周围,空气的流动不同于片状鳍片,受到鳍片的阻隔,只能在鳍片间沿一定方向流动,而是在密集的柱状鳍片间流动,会在每个鳍片周围形成一个小型的“旋风”,令鳍片的整个侧表面都成为有效散热表面积。
既然要利用柱状鳍片周围形成的小“旋风”增强散热效果,柱体的侧面就不应过于“粗糙”,产生过大风阻,阻碍“旋风”的形成。
那么是否需要采用圆形的柱状鳍片呢?
没有必要,同时也受工艺限制不易实现。
根据众所周知的几何常识——相同面积的多边形,圆形的周长是最短的,对应柱状鳍片的情况,即圆柱鳍片的侧面积最小。
而且为了获得圆形表面需要比多边形花费更多的工序与时间,圆形物体的固定难度又要比方形等平边多边形大得多,都是制约产能的不利因素。
柱状鳍片散热器的柱体形状关系到性能、工艺等多方面的因素,因此也正是设计中最为关注的。
此类散热片通常具有大量、密集的柱状鳍片,片间距离短,保留空间少,而且在各个鳍片周围都会形成一定的湍流,往往风阻很大。
不过得益于较大的表面积,以及充分的热交换,即便风量较小也可获得不错的散热效果。
实际使用中通过对风扇进行控制,可在性能与静音间自由选择,缺点则是往往重量较重,且价格不菲。
柱体形状:
与片状鳍片那相对单一的形状不同,虽说都是柱状鳍片,但既然不需要统一到圆柱形,不同的设计间就会存在着一些差异。
多边形:
鳍片的形状为多边形底面柱体,较常见的也只有方形与六边形。
方形柱状散热器多数为切削而成,即在具有片状鳍片的形材上进行切削,开出横向沟槽,将较厚的“片”分割为具有更大表面积的“柱”。
典型代表为曾名噪一时的“无酸素铜”散热片——KanieType-W。
切削而成的588根铜柱在当时造就了一代王者传说。
六边形底面的柱状鳍片则是Alpha的独门绝技,采用同样罕有采用的冷锻工艺(后文将详细介绍)而成,比方形底面柱体更加平滑。
Alpha8045/8942的名气有多大就不用笔者描述了,有许多人都是通过它才见识到柱状鳍片设计的性能优势。
圆形:
实际产品中极少有采用纯圆柱形鳍片的散热片,一般都会对其进行一定改进。
螺丝型鳍片(正式名称为“螺旋面插指”)就是Swiftech的独门绝技(专利哦~)了,应用于其品牌下MCX系列散热器上。
此种设计由螺旋面插指旋入铜质吸热底之中,替代传统的柱状鳍片。
相比纯圆柱与多边形底面柱体鳍片,螺旋面插指可以提供更大的表面积,而且螺旋状的侧面更加有利于“旋风”的产生。
从北桥芯片到CPU,从Socket-370到Socket-940,Swiftech的产品相当全面,甚至还有搭配制冷片的型号。
至于性能,就无需笔者在此多言,各种评测中的优异表现充分说明了其专利设计的效果。
另一种在圆柱形鳍片基础上进行的改良的产品为管形鳍片,典型产品为中光电器出品的空心管散热器CNA462U。
整体设计类似于Alpha8045,但采用了中空的铜管代替实心铝合金鳍片。
中空的铜管那表面虽然增加了相当多的表面积,但由于内部空间狭小,不便于空气流动,实际有效面积几可忽略,对性能影响甚微。
采用中空铜管的目的主要是保证与铝合金相当的内部导热能力同时,尽量控制散热片的重量。
此外,铜管较实心的圆柱鳍片还具有另一点优势——更加便于生产、固定与结合,大幅降低了制造难度。
排列方式:
柱状鳍片设计中,鳍片的排列方式相对种类较少,主要只有矩阵、三角与放射状三种。
矩阵排列即鳍片整齐的排列在横行与纵列之中。
典型的产品代表即KanieType-W与Swiftech的早期产品MCX-370等。
三角排列即鳍片列于3排互成120°的直线上,摆放位置与可铺满平面的六边形相同。
典型产品即Alpha的六边形鳍片系列以及后续产品。
柱状鳍片的放射状排列与片状鳍片有所不同,只是将环形紧密排列的鳍片向外围倾斜一定角度,角度向外逐层增大。
典型产品即Swiftech的后续MCX-V系列产品。
矩阵排列形式根据鳍片的高度与吸热底面积可以选择顶吹与侧吹。
三角排列形式通常采用顶置风扇,可根据风扇性能、导流罩设计与使用需求选择吹风或吸风方式。
放射状排列形式的产品则基本都采用顶吹式风扇,且需要风扇中心与鳍片排列中心重合,以保证风力分布更加均匀,有效利用所有鳍片的表面积。
另类:
原本这项只是随便列出,并没有想到什么确实的产品可称得上“另类”,但日前偶然间想起了这款真个可称另类的产品——KuthtecKTM2001。
KuthtecKTM2001采用回流焊结合的铝质鳍片,热缩嵌入的铜质柱状吸热底,顶吹风扇,单看任何一项都是较为常见的技术,单它的组合形式却非常怪异——鳍片与吸热底面平行,即铜柱垂直嵌入平行的鳍片中,类似上文的AkustPipeTower,但它又在外层增加“导流罩”,将风道的两端封闭。
那岂不就是一个封闭的盒子,失去了空气流动的通道么?
Kuthtec也真算别出心裁,竟然打出了贯穿众多层叠平行鳍片的小洞,以此作为空气流动通道。
想到它,笔者不免茫然……这应算作平行片状鳍片,还是利用内表面散热的柱状鳍片?
且不论其性能如何,这种独树一帜的想象力就足以令我们耳目一新了!
设计部分小结:
看过关于散热片设计的介绍,相信很多读者都会感到混乱,这部分由始至终都在说明几种互相矛盾、冲突的参数或特性的作用,其中的每一项都希望有更好的表现,但偏偏都是“牵一发而动全身”的互相影响着,很难令所有表现全面提高,即便做到了,也一定会面临着加工、成本等方面的制约,只能尽量在混乱中寻求一种平衡。
这就是目前的散热片设计者们所面临的处境。
当然,这些可敬的技术人员并不会像前文叙述的那样,在混乱的参数间挣扎,他们拥有一件利器——专业的流体模拟软件STAR-CD,由CD-adapco集团公司开发,并与全球许多著名的高等院校、科研机构、大型跨国公司合作,不断的丰富、完善。
STAR-CD在散热器设计中得到了广泛的应用,它可以根据设计者设定的材料、部件参数,模拟散热器使用过程中热量的分布,为设计者对产品规格或设计进行调整提供了参考。
上图即利用STAR-CD对目前Socket-T平台原配的“太阳花”散热器原型产品散热状态的模拟,两图分别对应3000rpm与4000rpm风扇的表现。
目前而言,普通用户对于散热片的设计仍然是无能为力,只能根据一些较易获取的特征信息对其性能进行大致判断。
但由于散热片各种参数间这种混乱的关系,只通过散热片的外形与材质准确判断其性能是不可能的,我们前述的建议也只是由经验与一些浅显理论而来,仅供参考。
更何况,有了优秀的设计,散热片能否获得强悍的性能,还要取决于实际的制造工艺。
工艺:
散热器的材料是性能的基础,设计是产品精髓所在,而最终能否将优秀的设计思想实现,或者实现成果如何,用户最终可获得怎样的产品,都完全取决于所采用的制造工艺。
成形与结合工艺:
散热片的成形与结合工艺间有着密切的联系,而且其中一些技术在两道工序中均可使用,因此在本节内一齐介绍。
切削:
工艺介绍:
应用最广的散热片成形技术是什么?
铝挤压?
是切削!
所有的散热片在成形过程中都会或多或少的使用到切削——这种金属加工中最常用的工艺。
切削工艺的具体种类很多,从无润滑切削到润滑切削,从高速切削到激光切割,从车、钻到铣、磨,在散热片的成形过程中,为了获得一些较特殊、精细的形状,都需要使用切削工艺。
具体用途主要有板材(吸热底、鳍片等)成形、散热片开槽、底面修整、特殊雕刻等。
切削而来的浮雕效果
优势:
根据不同方式、刀具,可适用于各种用途。
劣势:
设备,主要是刀具磨损快,多数需要人工参与或自动化控制,成本较高。
典型产品:
所有散热片!
铝挤压:
工艺介绍:
著名的铝挤压工艺,为绝大多数的铝合金散热片所采用,是市场上真正的主流。
铝挤压是加工铝合金形材最常用的工艺,在各个领域中均有采用。
在散热片加工方面,铝挤压工艺主要用来制造片状鳍片或柱状鳍片的初坯。
上图即铝挤压的模具。
铝挤压工艺所采用的材料通常为AA6061或AA6063,加工过程中,将铝合金原锭加热至约520~540℃,利用机械加压,令铝液流经模具钢制成的挤型模具,在模具出口处对铝液进行冷却,使之迅速凝固,成为具有连续平行结构的散热片初胚。
上图左部即铝合金原锭,中间则是铝挤压而成的条状形材,已可看出散热片的初形,再经由二次加工,进行冷铡切割、边角裁剪与剖沟后,即可获得成形的散热片单品。
实际上挤压成形工艺也可用于铜质散热片的加工,但由于铜的熔点过高,加工难度大,成品性能又并非特别出众,市场上几乎没有实际产品出现。
优势:
投资少、技术门槛低、开发周期短,易于投产;模具费用、生产成本低,产量大;适用范围广,既可制造单独散热片,也可制造结合型散热片的鳍片部分。
劣势:
鳍片形状相对简单,无法获得很大(大于20)的瘦长比。
典型产品:
几乎所有一体成形铝合金片状鳍片散热片。
精密切削:
工艺介绍:
一种独到的金属成形工艺,是最有望大范围应用的铜质散热片一体成形工艺。
“精密切削”的说法已经不知出自何处了,单从这名字上很难想象实际的加工工艺,但结合英文名称Skiving,就容易理解了。
Skiving,skive的动名词,为切片之意。
加工方法为:
将一整块金属型材根据需要。
利用精确控制的特殊刨床切割出指定厚度的薄片,再向上弯折为直立状态,成为散热鳍片。
早年间,Foxconn曾尝试应用这一工艺而推出了著名的PK085与PK130,但由于当时工艺尚不成熟,成品率较低,及铝合金应力不足而无法使鳍片处于直立状态,且性能较铝挤压工艺的产品没有明显优势,并未得到广泛的接受。
近两年,通过对精密切削工艺的改进,良品率已经大幅提高,且随着散热能力需求的增长,铜质材料使用的增多,自然解决了早期因铝材应力不足所导致的鳍片形状与排列问题。
精密切削工艺可望大展拳脚。
优势:
精密切削工艺最大的优势在于吸热底与鳍片一体成形,连接面积(连接比例)大,不存在介面阻抗,鳍片较厚,能够更有效利用散热表面积;此外,切割而成的鳍片排列密集,能在单位体积内获得更大的散热面积。
劣势:
受到原材料等的影响,良品率低;为了保证一定的应力,切割过程中无法将鳍片切得很薄、很长,即瘦长比不足;提供更大表面积的同时,片间距离短,过风空间较小,风阻较大。
此外,相对铝挤压等适于大规模生产的成型工艺,精密切削的设备、人工成本高,大规模生产资金投入过大。
典型产品:
热布斯系列散热器。
金属粉末喷射成形:
工艺介绍:
金属粉末喷射成形散热片主要采用高熔点、高热传导的材料(如铜),其加工方式为:
金属粉末高速喷射,直接做成散热片初胚,再利用高温烧结,制成具有相当强度与密度的成品。
主要应用于具有较高发热量又明显受空间限制的特殊需求电子产品上,制造成本与价格均极高。
优势:
金属粉末烧结一体成型,热传导率高;可加工具有复杂形状的散热片,设计者受限制较少。
劣势:
原料、设备、模具成本高,工艺复杂,良品率较低,不易量产。
典型产品:
无——目前市场上未见实际产品,只是“传说中的”技术。
铝压铸:
工艺介绍:
一种广泛应用的单体铝合金制品加工工艺。
制造过程为:
将铝合金原锭熔解成液态后,充填入模型内,利用压铸机一次性压铸成型,再经过冷却与后续处理,制成单体散热片。
压铸工艺通常用来加工一些形状非常复杂的元件,使用在散热片加工中虽有些大材小用的意味,但的确可制造出一些具有特殊结构设计的产品。
例如,可配合