塑料模课程设计机电.docx
《塑料模课程设计机电.docx》由会员分享,可在线阅读,更多相关《塑料模课程设计机电.docx(15页珍藏版)》请在冰豆网上搜索。
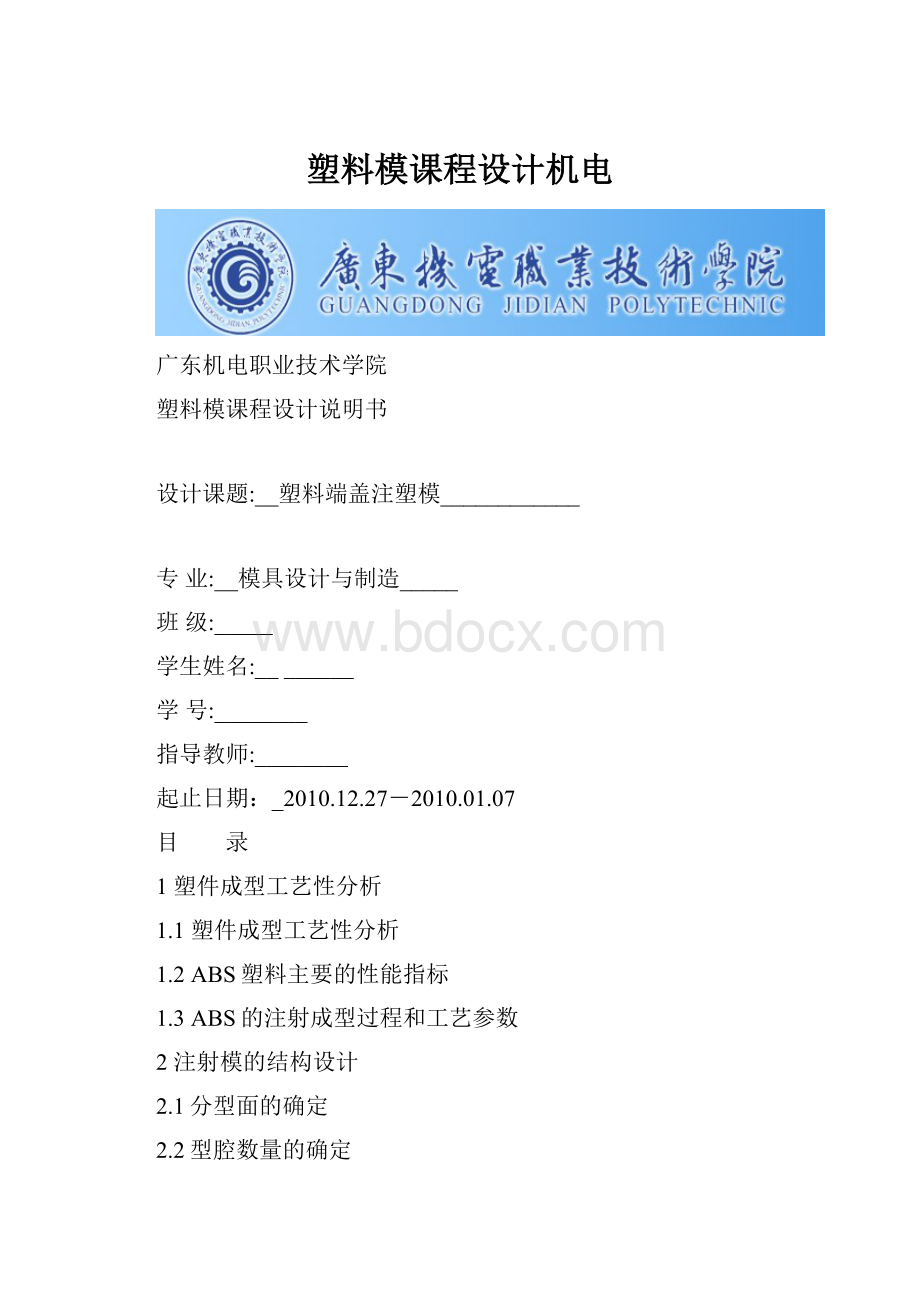
塑料模课程设计机电
广东机电职业技术学院
塑料模课程设计说明书
设计课题:
__塑料端盖注塑模____________
专业:
__模具设计与制造_____
班级:
_____
学生姓名:
________
学号:
________
指导教师:
________
起止日期:
_2010.12.27-2010.01.07
目 录
1塑件成型工艺性分析
1.1塑件成型工艺性分析
1.2ABS塑料主要的性能指标
1.3ABS的注射成型过程和工艺参数
2注射模的结构设计
2.1分型面的确定
2.2型腔数量的确定
2.3型腔、型芯工作部位尺寸的确定
3选标准模架
4浇注系统的设计
4.1主流道的设计
4.2分流道的设计
5排气槽的设计
6型腔的设计
6.1型腔壁厚的确定
7冷却系统的设计
8导向机构的设计
9推出机构的设计
10设计总结及体会
塑件成型工艺性分析
1.1塑件成型工艺性分析
1.塑件的分析⑴从图纸上分析,该塑件的外形为回转体,壁厚均匀,塑件外形尺寸不大,塑件熔体流程不长,且符合最小壁厚要求。
⑵塑件型腔较大,有尺寸不等的孔,
(3)塑件材料为热塑性材料,流动性较好,适合注射成型。
2.塑件的尺寸精度分析
塑件外形尺寸:
¢66、¢25、28、22;
内形尺寸:
¢19、¢60;
孔尺寸:
¢5+0.16﹑¢10+0.15;
孔心距尺寸:
¢42±0.32;
塑件每个尺寸的公差不一样,任务书中已给定部分尺寸公差,未注公差的尺寸取公差为MT4-A。
3.脱模斜度 ABS的成型性能良好,成型收缩率较小,选择脱模斜1°。
由于塑料冷却后产生收缩,会紧紧地包在凸模上,或由于粘附作用,塑件紧贴在型腔内,为了便于脱模,在设计时应考虑塑件表面具有合理的脱模斜度。
1.2ABS塑料主要的性能指标
丙烯腈-丁二烯-苯乙烯共聚物ABS树脂微黄色或白色不透明,是丙烯腈-丁二烯-苯乙烯共聚物。
丙烯腈使聚合物耐油,耐热,耐化学腐蚀,丁二烯使聚合物具有优越的柔性,韧性;苯乙烯赋予聚合物良好的刚性和加工流动性。
因此ABS树脂具有突出的力学性能和良好的综合性能。
同时具有吸湿性强,但原料要干燥,它的塑件尺寸稳定性好,塑件尽可能偏大的脱模斜度。
拉伸强度MPa35~49
拉伸弹性模量GPa1.8
弯曲弹性模量Gpa1.4密度(Kg.dm-3)1.13——1.14
收缩率%0.3~0.8
熔点℃130~160
热变形温度45N/cm65~98
弯曲强度Mpa80
压缩强度Mpa18~39
缺口冲击强度kJ/㎡11~20
硬度HRR62~86
体积电阻系数Ωcm1013
击穿电压Kv.mm-115
介电常数60Hz3.7
1.3ABS的注射成型过程和工艺参数
(1)成型前的准备。
对ABS的色泽,粒度均匀度等进行校验,ABS成型前必须进行干燥,处理温度50~70°C,干燥2h。
(2)注射过程。
塑料在注射机料筒内经过加热、塑化达到流动状态后,有模具的浇注系统进入模具的型腔成型,其过程可分为充模、压实、保压、倒流和冷却五个阶段。
(3)塑件的后处理(退火)。
注射模的结构设计
2.1分型面的确定
a)、Ⅰ、在开模时尽量使塑件留在动模内
Ⅱ、应有利于侧面分型和抽芯
Ⅲ、应合理安排塑件在型腔中的方位;
b)、考虑和保证塑件的外观不遭损坏
c)、尽力保证塑件尺寸的精度要求(如同心度等)
d)、有利于排气
e)、尽量使模具加工方便
通过对塑件结构形式的分析,分型面应该选择在端面截面积最大且利于开模取出塑件的底平面。
2.2型腔数量的确定
由于该塑件的精度要求不是很高,塑件尺寸较小,且为大批量生产,可采用一模多腔的结构形式。
同时考虑到塑件的尺寸,磨具的结构尺寸的关系,以及自造费用等因数,初步定为一模四腔的结构形式。
2.3型腔、型芯工作部位尺寸的确定
该塑件尺寸精度无特殊要求,所有尺寸均为自由尺寸,可按MT5查取公差.
ABS塑料的收缩率是0.3%~0.8%.
平均收缩率S=(0.3%+0.8%)/2=0.55%
型腔工作部位尺寸;
型腔径向尺寸Lm=(1+S)Ls
型腔深度尺寸Hm=(1+S)Hs
型芯径向尺寸Lm=(1+s)Ls
型芯深度尺寸hs=(1+s)Ls
中心距尺寸
式中
-----塑件外型径向基本尺寸的最大尺寸(mm);
----塑件内型径向-向基本尺寸的最小尺寸(mm);
-----塑件外型高度基本尺寸的最大尺寸(mm);
-----塑件内型深度基本尺寸的最小尺寸(mm);
-----塑件中心距基本尺寸的平均尺寸(mm);
X------修正系数,取0.5~0.75;
-----塑件工差(mm);
-----模具制造公差,取(1/3~1/4)
;
塑件外形尺寸:
66、25、28、22;
塑件内形尺寸:
60、10、5、19;
型腔径向尺寸:
Lm=(1+S)Ls=66.33
型腔深度尺寸:
Hm=(1+S)Hs=28.14
型芯径向尺寸:
Lm=(1+s)Ls=60.3
型芯深度尺寸:
hs=(1+s)Ls=25.13
选标准模架:
定模板厚度:
A=60mm动模板厚度:
B=35mm
垫块厚度:
C=70mm模具厚度:
H=270mm
浇注系统的设计
4.1主流道的设计
主流道通常位于模具中心塑料溶体的入口处,它将注射机喷嘴注射出的溶体导入分流道或型腔中,主流到的形状为圆锥型,以便溶体的流动和开模时主流道凝料的拔出,主流道的尺寸直接影响到溶体的流动速度和从模时间。
、
主流道浇口套的形式
主流道衬套为标准件课选购,主流道小端入口处与注射机喷嘴反复接触,易磨损。
,对材料的要求较严格,因而尽管小型注射模可以将主流道衬套与定位圈设计成一个整体,但考虑上述因素通常仍然将其分开来设计,以便拆卸更换,同时也便于选用优质刚才进行大都加工和热处理。
本设计中浇口套采用碳素工具钢,热处理淬火表面硬度为50HRC~55HRC,如图5-1所示,定位圈的结构由中装图来确定。
1.主流道的长度一般由模具结构确定
2.主流道小端直径d=注射机尺寸+(0.5~1)=5mm
3.主流道大端直径D=d+2Ltan(a/2)=8mm,a=4°
4.主流道球面半径17mm。
5.球面的配合高度3mm。
4.2分流道的设计
分流道的布置形式为了尽量减少在流道内的压力损失和尽可能避免熔体温度降低,同时还要考虑减少分流道的容积和压力平衡,因此采用平衡式分流道
。
分流道的形状及尺寸,应根据塑件的体积、壁厚、形状的复杂程度、注塑速率、分流道长度等因素来确定。
本塑件的形状简单,熔料填充型腔比较容易。
根据型腔的排列的方式可知分流道的长度较短,为了便于加工起见,选用截面形状为梯形截面分流道,且熔体的热量散发和流动阻力都不大。
浇口直径可以根据经验公式计算
式中d----浇口直径(mm);
----塑件在浇口处的壁厚(mm);
A-----型腔表面积(
).(用UG软件可以计算表面积A=7.8*
)
*7.8*
mm=3mm
进料位置的确定
根据塑件外观质量的要求以及型腔的安放方式,进料位置设计在塑件底部。
排气槽的设计
该塑件由于采用侧浇口进料溶体竞塑件下方的台阶向上从面型腔,每个芯上有俩个或四个推杆,其配合间隙可作为气体排出方式,不会在顶部产生憋气的现象。
同时,底面的气体会沿着分型面,型芯,和推件板之间的间隙向外排出。
型腔的设计
6.1型腔壁厚的确定
成型零部件的壁厚计算一般常用计算法和查表法,但计算法比较复杂且繁琐,而计算结果却与经验数据比较接近,因此在进行模具设计时,一般采用经验数据或查有关表格。
冷却系统的设计
1、冷却系统设计
塑料在成型过程中,模具温度会直接影响到塑料的充模、定型、成型周期和塑件质量。
所以,我们在模具上需要设置温度调节系统以到达理想的温度要求。
一般注射模内的塑料熔体温度为200℃左右,而塑件从模具型腔中取出时其温度在60℃以下。
所以热塑性塑料在注射成型后,必须对模具进行有效的冷却,以便使塑件可靠冷却定型并迅速脱模,提高塑件定型质量和生产效率。
对于熔融黏度低、流动性比较好的塑料,如聚丙烯、有机玻璃等等,当塑件是小型薄壁时,如我们的塑件,则模具可简单进行冷却或者可利用自然冷却不设冷却系统;当塑件是大型的制品时,则需要对模具进行人工冷却。
2、冷却系统设计原则
①、尽量保证塑件收缩均匀,维持模具的热平衡
②、冷却水孔的数量越多,孔径越大,则对塑件的冷却效果越均匀。
③、尽可能使冷却水孔至型腔表面的距离相等。
④、浇口处加强冷却。
⑤、应降低进水与出水的温差。
⑥、合理选择冷却水道的形式。
⑦、合理确定冷却水管接头位置。
⑧、冷却系统的水道尽量避免与模具上其他机构发生干涉现象。
⑨、冷却水管进出接头应埋入模板内,以免模具在搬运过程中造成损坏。
ABS是流动性较好的材料,其成型温度及模具温度分别为200°C和50~70°C,热变形温度为60°C~90°C。
所以模具温度初步取40°C,常用温水对模具进行冷却。
3、冷却系统的结构形式
根据塑料制品形状及其所需的冷却效果,冷却回路可分为直通式、圆周式、隔板式等,同时还可以互相配合,构成各种冷却回路。
其基本形式有几种,我们这里选用的是简单流道式。
简单流道式即通过在模具上直接打孔,并通过以冷却水而进行冷却,是生产中最常用的一种形式,如下图所示
导向机构的设计
注射机的导向机构用于动、定模之间的开合模导向和脱模机构的运动导向。
按作用分为模外定位和模内定位。
模外定位是通过定位圈与注射机相配合,使模具的浇口套能与注射机喷嘴精确定位;而模内定位机构则通过导柱导套进行合模定位。
锥面定位则用于动、定模之间的精密定位。
本模具定位精度不高,因此可采用模架本身自带的定位机构。
推出机构的设计
1.推出机构的选用原则。
①尽量使塑件留在动模一侧。
②保证塑件不变形、不损坏脱模力作用位置靠近型芯。
脱模力应作用于塑件刚度及强度最大的部位作用力面积尽可能大③保证塑件外观良好。
推出位置尽量选在塑件内侧。
④结构简单、可靠,合模时可正确复位
二、对于薄壁容器、壳体以及表面不允许有推出的痕迹的制品,需要采用推板推出机构。
在分型面处从壳体塑件的周边推出,推出力大且均匀。
对侧壁脱模阻力较大的薄壁箱体或圆筒制品,推出后外观上几乎不留痕迹,这对透明塑件尤为重要。
推板脱模机构不需要回程杆复位。
推板应由模具的导柱导向机构导向定位,以防止推板孔与型芯间的过度磨损和偏移。
为防止推杆与推板分离推板滑出导柱,推杆与推板用螺纹连接。
应注意,该种结构在合模时,推板与模具底脚之间应留2~3mm的间隙。
推板与型芯之间要有高精度的间隙、均匀的动配合。
要使推板灵活脱模和回复,又不能有塑料熔体溢料。
为防止过度磨损和咬合发生,推板孔与型芯应作淬火处理。
推板脱模的分型面应尽可能为简单无曲折的平面。
设计总结及体会
两周的课程设计结束了,在这次的课程设计中不仅检验了我所学习的知识,也培养了我如何去把握一件事情,如何去做一件事情,又如何完成一件事情。
在设计过程中,与同学分工设计,和同学们相互探讨,相互学习,。
学会了合作,学会了宽容,学会了理解,也学会了做人与处世。
课程设计是我们专业课程知识综合应用的实践训练,是我们迈向社会,从事职业工作前一个必不少的过程.”千里之行始于足下”,通过这次课程设计,我深深体会到这句千古名言的真正含义.我今天认真的进行课程设计,学会脚踏实地迈开这一步,就是为明天能稳健地在社会大潮中奔跑打下坚实的基础.
通过这次模具设计,本人在多方面都有所提高。
通过这次模具设计,综合运用本专业所学课程的理论和生产实际知识进行一次冷冲压模具设计工作的实际训练从而培养和提高学生独立工作能力,巩固塑料模具设计等课程所学的内容,掌握塑料模具设计的方法和步骤,掌握塑料模具设计的基本的模具技能懂得了怎样分析零件的工艺性,怎样确定工艺方案,了解了模具的基本结构,提高了计算能力,绘图能力,熟悉了规范和标准,同时各科相关的课程都有了全面的复习,独立思考的能力也有了提高。
在这次设计过程中,体现出自己单独设计模具的能力以及综合运用知识的能力,体会了学以致用、突出自己劳动成果的喜悦心情,从中发现自己平时学习的不足和薄弱环节,从而加以弥补。
在此感谢我们的林老师.,老师严谨细致、一丝不苟的作风一直是我工作、学习中的榜样;老师循循善诱的教导和不拘一格的思路给予我无尽的启迪;这次模具设计的每个实验细节和每个数据,都离不开老师您的细心指导。
而您开朗的个性和宽容的态度,帮助我能够很顺利的完成了这次课程设计。
同时感谢对我帮助过的同学们,谢谢你们对我的帮助和支持,让我感受到同学的友谊。
由于本人的设计能力有限,在设计过程中难免出现错误,恳请老师们多多指教,我十分乐意接受你们的批评与指正,本人将万分感谢。