图解丰田生产方式.docx
《图解丰田生产方式.docx》由会员分享,可在线阅读,更多相关《图解丰田生产方式.docx(45页珍藏版)》请在冰豆网上搜索。
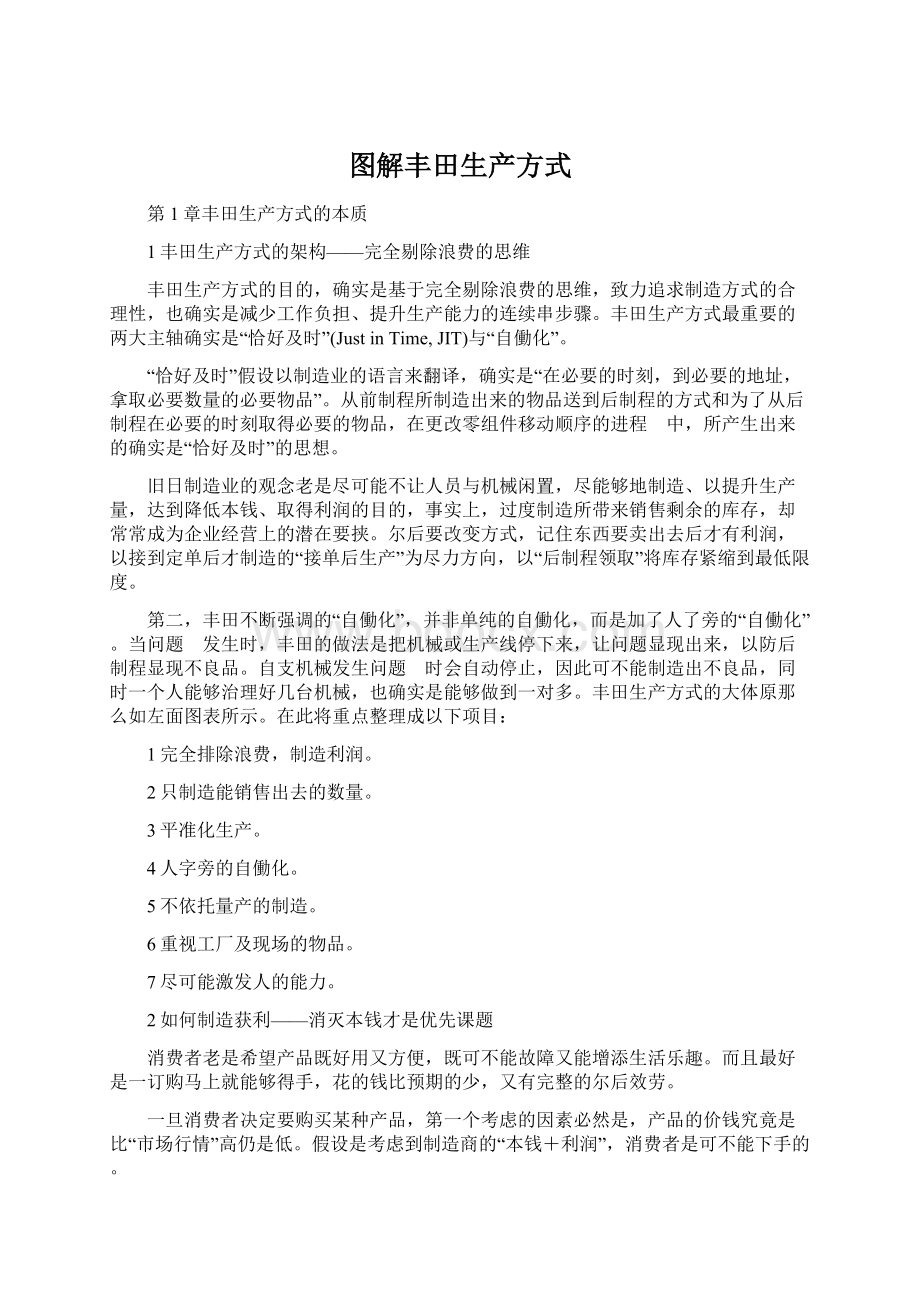
图解丰田生产方式
第1章丰田生产方式的本质
1丰田生产方式的架构——完全剔除浪费的思维
丰田生产方式的目的,确实是基于完全剔除浪费的思维,致力追求制造方式的合理性,也确实是减少工作负担、提升生产能力的连续串步骤。
丰田生产方式最重要的两大主轴确实是“恰好及时”(JustinTime,JIT)与“自働化”。
“恰好及时”假设以制造业的语言来翻译,确实是“在必要的时刻,到必要的地址,拿取必要数量的必要物品”。
从前制程所制造出来的物品送到后制程的方式和为了从后制程在必要的时刻取得必要的物品,在更改零组件移动顺序的进程 中,所产生出来的确实是“恰好及时”的思想。
旧日制造业的观念老是尽可能不让人员与机械闲置,尽能够地制造、以提升生产量,达到降低本钱、取得利润的目的,事实上,过度制造所带来销售剩余的库存,却常常成为企业经营上的潜在要挟。
尔后要改变方式,记住东西要卖出去后才有利润,以接到定单后才制造的“接单后生产”为尽力方向,以“后制程领取”将库存紧缩到最低限度。
第二,丰田不断强调的“自働化”,并非单纯的自働化,而是加了人了旁的“自働化”。
当问题 发生时,丰田的做法是把机械或生产线停下来,让问题显现出来,以防后制程显现不良品。
自支机械发生问题 时会自动停止,因此可不能制造出不良品,同时一个人能够治理好几台机械,也确实是能够做到一对多。
丰田生产方式的大体原那么如左面图表所示。
在此将重点整理成以下项目:
1完全排除浪费,制造利润。
2只制造能销售出去的数量。
3平准化生产。
4人字旁的自働化。
5不依托量产的制造。
6重视工厂及现场的物品。
7尽可能激发人的能力。
2如何制造获利——消灭本钱才是优先课题
消费者老是希望产品既好用又方便,既可不能故障又能增添生活乐趣。
而且最好是一订购马上就能够得手,花的钱比预期的少,又有完整的尔后效劳。
一旦消费者决定要购买某种产品,第一个考虑的因素必然是,产品的价钱究竟是比“市场行情”高仍是低。
假设是考虑到制造商的“本钱+利润”,消费者是可不能下手的。
毋需赘言,企业必需持续取得适当的利润,才能继续经营下去。
而公司有获利,才能照顾在企业工作的员工,让员工拥有健康丰硕的生活。
因此员工为公司工作,其所有行为应该都以追求利润为最终目的。
售价、本钱与利润的关系,可表示为以下三个公式:
1售价-本钱=利润 销售进程治理,提升售价以增加利润
2售价=本钱+利润 本钱主义(有可不能倒的国营企业当靠山)
3利润=售价-本钱 非本钱主义 降低本钱
几乎所有的企业推出新产品时都是依循公式②来决定售价,考虑的是本钱多少钱、我要赚多少钱,两个数字加起来就决定售价是多少。
会想到“市场行情”的企业有如凤毛麟角。
若是不能完全同意“售价由顾客决定”的观念,就会订出一个不上不下的售价,最后产品销售状况不佳,以怪罪国外廉价品倾销、市场景气不行等等,企图推卸责任。
丰田生产方式确实是采纳第三个公式:
利润是售价减去本钱。
因此,假设要确保利润,就只能尽力削减本钱。
如此一来,企业的生存之道,唯有完全排除浪费,别无其他方式。
3何谓“恰好及时”(JustinTime,JIT)——后制程只在必要的时刻,向前制程拿取必要数量的必要物品
制造的全然,确实是以更低廉的价钱,迅速提供更多的消费者品质更好的商品。
那个观念不论何时何地都可不能有所改变。
除此之外,“只制造能销售出去的东西”也是理要的。
过去有许多企业在廖定制造数量时,都只凭自己一厢甘心的预测,或是只看到市场表面的需求,因此尝到经营上的苦果。
泡沫经济崩解、IT(资讯技术)热潮冷却后,多余的设备和库存是何等让企业头痛,大伙儿应该都很清楚。
假设要以有效率、不浪费的方式制造能销售出去的商品,意即必需配合的商品销售出去的机会来制造。
如此的方式确实是“恰好及时”(JustinTime)的思维。
所谓“JustinTime”确实是“后制程只在必要的时刻,向前制程拿取必要数量的必要物品”。
完全执行如此的做法,前制程就可不能生产比后制程必要数量更多的物品,也就能够确信可不能生产卖不出去的东西,可不能产生多余的库存。
要达到零库存的目标,必需记住“太慢因然不行,太快却更糟糕”若是制造太多太快就会产生多余的库存,也就无法做到“JustinTime”。
作业员总感觉自己不该该闲着,万一真的没事做,闲得发慌之下可能会不警惕做出画蛇添足的动作,这也是人之常情。
只是,假设要避免过度制造,就必需以拍子时刻(Takttime)进行制造治理,确实依照定单来生产。
另外,还应该做到:
1流程生产:
将制造流程化,原那么上为单件流制造。
2订定拍子时刻:
确实把握具体的必要数量,和应该以何种速度制造哪些商品。
3后制程领取:
后制程指示资讯的一贯性,依照“看板”加以具体化。
4以缩短换模时刻达到小批生产。
4不依托量产的制造——不期待量产成效的制造方式
藉由较多的数量分摊总本钱中的固定费用,使每一个商品的单位本钱下降,这确实是所谓的量产成效。
在物资极度缺乏或经济高度成长的时期,量产的方式是没有问题的。
可是最近几年来,旧日那种强调量产成效的制造,已愈来愈来无法迅速灵活地因应上瞬息万变的需求,过度制造反而造成浪费,乃至使本钱增加。
现今的市场需求是少量而多样的,因此以后的制造除要配合产品的销售状况外还必需尽可能压低总费用才能从中挤出利润。
总费用与营收数字相同的那一点为损益平稳点,此刻的损益平稳点必需要再往下降才行。
总费用饮食变更费用及固定费用。
变更费用以物料、外包费等为主:
固定费用那么有人事费、折旧费和间接部门费等。
要降低损益平稳点,最有效的方式是消减固定费用,其中以减少人事费最能收到立竿见影之效。
要达到目的 ,必需推动员工的多能工化,将人员的能力发挥到极限,藉经减少人力;因剔除浪费而产生剩余人力也必需善加利用,藉此减少外包费用。
生产设备方面,那么必需进行完全的改善,以生产效率为优先,购买新设备时只买最低限度所需,将设备投资费降到最低,藉此紧缩机械折旧费用。
往后假设还需要其化功能,届时再依照需求另外追加购买就能够够了。
另外要提示的是,“制造过度的浪费”会侵蚀物料费、零组件费、电力能源费等等,致使多余费用产生。
关于削减固定费用,左页图表为降低设备费及人事费的方式。
另外,剔除浪费致使本钱降低、使固定费用成为变更费用等范例,也都列举在表中。
5前制程是神明,后制程是客户——对前制程与后制程的“体贴”
受托代为制造零组件或承接工程的企业,咱们称之为下包厂商。
协助自己公司,负责自己公司无力制造的前制程厂商,丰田视之有如神明,因为他们是帮忙自己公司中的制造、真正找起一部份生产责任的“合力公司”。
另一方面,负责自己制程以后作业的厂商,那么是丰田的“客户”。
从生产线的后制程,到成品的运输业者、零售商、消费者,都包括在内。
制造出来的产品必需百分之百都是良品,绝对不让不良品流到后制程。
在必要的时刻将必要数量的必要物品送到客户手上,这是理所固然的。
不良品和制造过度的浪费在本质上都是一样的,它们都是让本钱上升的凶手。
在以往,大量制造的产品就算临时卖不出去成为库存,总有一天仍是会卖得掉。
可是此刻已今非昔比,若是不配合销售的情形,只制造卖得出去的数量,绝对无法增加竞争力。
假设总自以为市场需求应该有多少,可不能随着市场需求的转变而改变,不把客户真正的需求放在心上,必然专门快就会感受到库存过量的压力。
另外还要记住一点,让客户等待也是无法真正照顾到客户的需求。
因此还需要多方尽力,减少让客户等待的时刻。
例如降低前置作业不时、快速换模等等。
即便在同一间工厂或公司内,也不可忘记“后制程是客户”。
例如同一间工厂内,自己的制程要供给零组件给组装作业,可是零组件的排列却乱七八糟,甚至沾染油污,致使组装作业无法立刻展开。
假设是组装作业能够马上开始,作业效率想必就会大幅提升。
尔后的制造,不但要提升自己制程的生产效率,更要注意到后制程的需求。
对制造能产生效率,更要注意到后制程的需求。
对制造能产生奉献的改善动作,列于左页图表中。
6库存是罪恶——库存不是资产,它什么都不是
似乎有很多人到此刻还活在过去那个东西做出来就卖得掉的时期。
大量制造物品,就算有库存仍是卖得掉,价钱也可不能太离谱,这都是以前的事了。
尤其是身处通货膨胀的年代,一个东西明天的售价说不定会比今天还高。
市场正在低成长乃至负成长,消费者的口味也慢慢多样化,生命周期短的商品愈来愈多。
就算做出产品来,销售情形也不见得就能够和自己预期的一样,更何况后面还不断有新产品冒出头。
只若是卖剩的价钱必然显著崩盘,这确实是目前市场的现况。
一次大量制造尽管能够压低产品单价,可是卖不出去的多余库存并非是资产,它们全然什么都不是,为了保管这些库存反而还要一笔花费。
只要纵容一次制造过度所产生费,浪费就会再产生浪费,陷入无止境的恶性循环。
因此丰田以为“库存是罪恶”,严格掌控必要数量。
那个地址所说的“必要数量”是依照市场动向,也确实是销售状况来决定的,因此制造的工厂並不能随自己快乐任意更改数字。
遵循“必要数量”,只在必要的时刻生产必要的物品,这确实是丰田生产方式 的大体思维。
不要以为让机械产生全开拼命制造,必然是比较有利的。
制造能销售出去的数量后就该把机械停止,获利並不是东西做出来就算数,而是卖出去才算数。
绝不制造多余的东西,应该是最全然的观念。
尤其是现今市需求走向多样化,少量多样的生产已是时期潮流,过去利用量产压低产品单价的做法已再也不通用。
假设不能将观念转变成:
制造必需配合销售状况,企业将难以在那个时期存活。
7完全激发人的潜能——以人为本、以人为主的制造
制造方式无时无刻不在改变,但“剔除浪费,以更好的方式、更低廉的价钱制造出更优良的产品”原那么,不论时期如何变迁,绝可不能有所动摇。
只要守住这项原那么,那么不管社会条件眧何转变,都能持续开辟客源。
这是企业的使命,也是企业的课题。
使改变成为可能,除依托“人的聪慧”之外,也必需奉行“以人为本的制造”,这些金科玉律绝对是永久的准那么。
因为有工厂作业人员的聪慧,丰田生产方式 才能成功实施,而且日新又新。
这绝非一朝一夕之功,而是基于对“人性”的尊重,重视所有人的试探能力,同时必需配合“看板”与“灯号”(Andon)等“目视化治理”架构,才能得以实现。
丰田生产方式不只是制造的方式,而是一个经营系统,告知你如何培育制造产品和提供效劳的人材,和如何激发出他们的潜能。
丰田生产方式透过将人的潜能发挥到极限的方式,达到迅速因应多样少量的顾客需求的目标。
“发挥人的潜能”这名知其实隐含以下几个涵义。
①人的潜能是深不可测的
只要环境条件配合,潜能发挥的度会令人感到十分惊讶,而且完全无法预测能发挥到什么境界,因为这和机械能力不一样,不是固定不变的。
②无法善用人的潜能,是经营上的一大浪费
关于“人”这项经营资源,应该让其充分发挥本来的能力才是。
③试探能力与提供聪慧的能力,最应该受到尊重
人会真正充满干劲,不是因为取得金钱上的报酬或精神上的确信,而是有机遇奉献、展现他的聪慧。
左页的图表举出一部份例子,示范如何开发並善用工厂作业人员的能力,使之成为制造架构的一部份。
下方的表格那么是丰田生产方式中善用人力的范例。
8生产、流通、消费的同时,也与地球和平共存——环保是企业经营的大前提
温室效应恶化,臭氧层破洞扩大等环保问题断发生,如何减少汽车废气中的氮氧化物(NOx)等有害物质,和降低引发温度效应的二氧化碳排放量,一直是环保人士关切的两大议题。
要减少氧化碳,就必需提高汽车的燃料利用效率,藉此降低汽车利用的燃料量。
所有汽车制造商都在尽力研发相关技术,只是有人指出以前的引擎反而会使氮氧化物增加,能做到的超级有限。
因此油电混合车最近受到广大注视,因其能时兼提升燃料利用效率及减少有害物质的两在目标。
油电混合车的动力是由引擎与马达一起提供的。
另外,拥有“终极低公害车”之称的燃料电池车也已经问世。
其原理是以氢所作为燃料,利用空气中的氧与之反映而发电,因此排出的物质只有水,可不能排入有害物质,丰田和本田两大汽车制造商已经达到有效化。
为了减少汽车报废时对环境的损害,回收利用过的汽车也是超级重要的。
将可再利用的零件或材料回收后,经粉碎剩下的残渣(Shreder,Dust),目前几乎都以掩埋方式处置。
日本2004年度实施的汽车回收法,标准制造商负有回收的义务。
此刻的回收率约75%,日本政府目标是95%。
要提升回收率,就必需残渣也加以回收利用。
环保机械制造商已经开发出几种 装置,有的能利用不同溶剂别离回收材料,有的能够利用气化溶解烟技术来发电,这些装置将销售给产业废弃物上处置业者。
汽车业都也从企划、开发时期开始即采纳可回收的材料,以模组化、减少零组件数量、整合树脂材料,以模组化、减少零组件数量、整合树脂材料等方式提升解体容易度,並减少分类的麻烦。
汽车内装也采纳能吸收较多二氧化碳的材料,此刻也已经显现可分解微生物的树脂。
9与结盟企业携手合作——成立结盟企业合作新关系
“结盟企业”指的是汽车制造商和零组件制造商两边间具有经济效益且合情合理的关系,涵盖“资本与人的关系”、“长期持续的交易”,和“紧密的资讯共享”等层面。
站在长期观点,汽车制造商和零组件制造商一起尽力强化设备投资与技术研究开发,让本来体质贫弱的零组件制造商成长为具有产品设计能力的专业厂商,帮忙汽车制造商达到降低本钱与提升产品品质的目标。
一部汽车是由三万个左右的零组件所组成,其中70~80%购自零组件制造商。
对汽车制造商而言,零组件的本钱与技术 改善能力超级重要,因此近来有些制造商开始舍弃“结盟企业”方式,导入欧美的供给系统(竞标、每一年签约等)。
只是,与汽车大体性能息息相关的特制组件並不等同一样零组件,一旦连特制零组件都必需倚赖零组件制造商,汽车制造商极可能会丧失独家技术的优秀。
特制零组件的设计需要具有产品设计能力的专业厂商,且必需拥有紧急变更设计时能迅速因应的能力。
另外,生产据点遍及全世界的结果,汽车制造商也必需都是如何维持全世界生产据点的供给畅通,並培育数量变更时的因能力,因此汽车制造商目前也正在试探和零组件供给商之间的“结盟企业”新合作关系。
以前汽车制造商的组装作业全都是在自己工厂内进行的,此刻有些业都已经将部份作业交给零组件制造商。
欧美厂商带动的模组化确实是典型的一例,目前这股风潮也慢慢透进日本业界。
模组化持续进展下去,零组件制造商的规模会愈来愈大,其和汽车制造商的关系,和汽车的制造方式,都将显现重大转变。
只是,模组化会使交货的物品体积增加,产生较多的输送费用。
因此,最近日本开始显现“卫星工厂”。
“卫星工厂”指的是,零组件制造商借用汽车制造商组装工厂的场地,将零组件组装起来,並直接送到生产线。
这可说是新的制造业合作模式。
10监督者的任务——监督者是生产线的灵魂人物
监督者必需熟知丰田生产方式,並且能够完全剔除切中要害的浪费。
换句话说,监督者确实是推动“持续改善”的实际负责人。
另外,在生产治理方面,监督者还有两项重要任务,确实是:
①数量确保与品质保证;②推动改善,以减少所需要人力。
可是这两项任务却包括着相斥的要素。
要让两项任务都能圆满达到,监督者必需确实把握工厂状况,紧密注意工厂运作情形。
监督者要具有作业分派、作业方式的训练、QCD打算的达到、设备维修、物料预备、换模等工作上的治理技术,还要能将异样状况“标准化”,让作业人员能觉察到异常状况的发生。
另外,治理异样状况、使这些状况能让“任何一眼就能够判定且得知”,更是治理中的重点。
生产线停止或制造出不良品时,很容易明白必然有异样状况发生了。
但是,让制造本钱增加的“异样”却不易发觉,因此更需要专门注意。
监督者要明白,停止下来的生产线会让问题凸显出来,因此在发觉异样状况时,应该要主动停止生产线,尽力从全然解决问题。
解决问题的顺序,应该是从改善作业开始,接下来才是改善设备。
依照顺序确实执行,是超级重要的一件事。
削减人力不可勉强推行,要落实改善方案更非一蹴而就的事。
生产线上事,监督者既不可事事都要插足,也不能完全放牛吃草。
要找出改善的地址,监督者必需亲自动用,同时也是给作业人员一个良好示范。
监督者要牢记以下三件情形:
1常常巡视现场(养成判定异样的能力)。
2确实治理並指挥下属(让下属照自己方式做事)。
具有远大的目光,能凝视全部状况並加以判定(永久明白该怎么做最好)。
11透过自主研究会,改善企业的体质——丰田生产方式的自主研究会
“自主研”是“丰田生产方式自主研究会”的简称,这是一个为了将丰田生产方式的观点、做法导入自己公司或制程内所发起的研究会。
有些研究会只限于自己公司内部,由母公司专门指导,只是一样的研究会都是在母公司的支援下,结合了数家公司的力量,大伙儿合作合作,以集团研究会的方式进行,现在称为“合同自主研”。
“合同自主研”的活动以一年为单位,年初时订定整体活动打算,先决定进行主题、参与的公司(会员)、担任会场的公司等。
接着会员同意基础讲习,並对自己公司估量实施丰田生产方式的工厂,调查过实际状况以后,合同自主研即正式展开。
基础讲习确实是丰田生产方式的念书会,由负责支援的企业讲师,以丰硕且浅显懂的改善范例实施导入教育。
合同自主研的实施依照既定打算,分成数次,由会员公司一路到担任会场的公司去,参加该公司活动主题的改善,透过实践活动亲躯体验並了解改善方式。
如此一来,不但担任会场的公司能享受改善功效,会员公司也可学习到指导能力,能够应用在自己公司上。
“公司内部推动”那么是在各公司高层人士的主导下,依照记录主题实施的活动,与合同自主研同时进行。
会员一方面在自己公司内部推动从合同自主研学习到的改善方式,一方面利用做出来的功效让改善活动加倍深切,这确实是最要紧的目标。
合同自主研的功效,是依照每一年的打算表来确认,必需同意支援者的查验,并在一起发表会发布。
在自己公司内部推动的“公司内部推动”也是一样,活动功效必需由高层人士确认事后,在公司内的发表会上发布。
“最后查验”的实施方式,那么是与研究会开始前的调查结果相互对照,由会员全部参加一起发表会,并到各公司的工厂去举行。
12确保平安为首要之务——平安的行为与机械高的本质平安化
平安和环保都是与企业基础相关的重要事项。
基于丰田生产方式的理念“对人的尊重”与“平安确实是治理,从上对虾上每人都平安第一的使命”的大体方针,最近丰田打出以下口号:
1挑战“零重要灾害、零重要疾病”,强化防患于未然的机制与体制。
2打造身心健全的工作环境。
另外,由于平安与“人”和“物”息息相关,关于那个问题,丰田正在各工作单位推行以下活动:
1培育行为平安的人,成立活动平安的职场。
2设备的“本质平安化”
灾害的发生,大部份都是起因于“人”的不平安行为,或机械的不平安状况。
因此企业持续推动机械设备的本质平安化(企业所提供的机械设备,在作业人员采取不平安的行为时,仍然能够保证作业人员的平安卫生)。
最近的机械设备,由于朝向自働化、软体操纵化进展,危险因子加倍不易查觉,故障平安处置(FailSate)、防呆[(Fool-Proof)、连锁装置(Interlock)]等解决方式因此纷纷出笼。
发生灾害多半是因为“人”随意接近或启动机械设备,而且反映太慢。
因此 ,要应付短暂停止、修复完毕后、产生不良品、作业中断等标准作业范围外的状况,强化作业人员不让灾害发生的意识,是超级重要的。
除实施日常作业开始时的平安确认和非日常作业时的4R-KYK(4回合的危险预测),同时要教育、训练作业人员,使之即便一个人工作,也能独立执行KYK。
幸免劳动灾害也是极为重要,尤其是重物作业,作业姿势、次数及时刻应该加以量化,做成评量表,以增进作业环境(排除或转换化学物质、粉尘等)改善。
13致力成为“零废料”工厂——推动工厂内废弃物减量,先选择示范工厂
一样制造工厂在产品制造的进程 中,总免不了会产生一些排出物或废弃物。
废弃物可分成焚化处置垃圾和掩埋处置垃圾两种:
排出物那么有污水、废气等,都会对环境造成不良阻碍,因此近来要求废弃物减量乃至工厂零废料的呼声愈来愈高。
其中废弃物的掩埋地和焚化场的问题,也广受各界关注。
隔热材料、耐火材料、化学处置进程中产生的沉淀物(如涂装前打底处置的残屑)、从地板或沟槽中扫出来的尘埃纸屑等,这些不容易回收的不可燃物就属于掩埋处置的垃圾。
零件的爱惜套、脱模剂、涂装用的遮蔽胶带、包装材料等不容易再利用的可燃物,确实是焚化处置垃圾。
要推动制造工厂的废弃物减量,与其发动全公司一路进行,不如先订立公司目标,再选择一个示范工厂,成立打算小组来负责企划、实施、评估等,更易产生成效。
具体的推展行动包括制作垃圾分类公约(治理表)、详细分类垃圾种类,并调查垃圾产生的进程 ,明确提出再利用、代替、回收,以有作为其他商品的资源等改善方案。
某个汽车制造商打出“混在一路是垃圾,分门别类成资源”的口号将示范工厂的功效推展到全公司和全事业单位,成功达到工厂垃圾零掩埋的目标,目前正在挑战更高的“垃圾零焚化”的目标。
这家公司达到垃圾零掩埋的主法,第一 将零件爱惜套回收后给进货商再利用、废弃的塑胶材料用来制作燃料、停止使 用涂装的遮蔽胶囊(无胶带化),和成立可不能产生废弃物的生产线等等。
另外,工厂也应该致力减少能源消耗,尽可能做到省能源、提升物料良率、推动零不良品,最好能设法取得ISO14001的认证,这也是回应社会需求的方式之一。
小论坛——什么是TPS?
丰田汽车现在已是全世界知名的大企业,其成长的基础是在1950年奠定的。
那时丰田面临破产危机,在公司高层绞尽脑汁之下,才产生以“JustinTime”及“加入了人字旁的自働化”为两大支柱的生产系统,亦即简称为“TPS”的TOYOTAProductionSystem。
丰田生产方式的灵感来自超市的销售模式。
消费都上超市只会采购他们需要的物品,而超市也只会补上卖掉的货物。
催生了TPS的大野耐一先生,确实是将此原理应用到汽车制造商,并加以落实,在1954年把“看板”那个工具导入了TPS。
TPS不是一成不变的生产方式,而是具有哲理、天天都在进步的生产方式。
持续试探该如何才能迅速提供消费者加倍物美价廉的商品,改变制造、物流等方式、因应时期的需求不断革新。
第2章品质保障
14在间接部门推动科学SQC——丰田SQC后兴运动
从丰田推展开来的统计品质治理(StatisticalQualityControl,SQC),开始时其目的主若是将过去应用在制造或技术部门的问题解决方式,用来帮忙治理、销售、客服部门等间接部门,解决他们的问题。
从过去以数量、测量数字为基础的“货物品质问题”解决方案,进展到以语言资讯为基础的“工作品质问题”解决方案,这确实是“SQC振兴运动”。
所谓心知肚明的“默契”常是间接业务流程中的阻碍,而科学SQC确实是有系统的将“默契”开诚布公的方式。
从经营的观点来看,科学SQC是由四个核心原理所组成的。
第一是科学的研究态度。
不偏重分析,从问题设定到目标达到,都采纳科学的归纳式SQC的方式,发挥优秀的观看力。
第二是慢慢攀峰解决问题。
运用积存下来的技术能力,和七手法(Q7)、新品管七手法(N7)、基础的SQC方式、多变量分析法、实验打算法等方式,分析问题的实质结构。
第三是综合性网路。
为使重要的技术问题确实解决,普协助将原先自以为共有的默契“化暗为明”,而把登录、搜寻、SQC方式范例集、实践指南、问题 解决流程图等加以组合,使之得以应用。
第四是治理SQC。
为解决根深蒂固的技术问题 ,除要将默契开诚布公,还必需提升技术水准,使之有利于新技术、新制法、新物料等的研发。
要善用科学SQC,了解并应用的SQC方式是超级重要的。
此刻已经有完整的训练课程,且修习课程的人可取得SQC专业顾问或专业建议师的资格。
取得证书的人有的正在率领各事业单位、各公司推动科学SQC,有的由是指导实践方式,希望让更多的公司采纳这些方式。
15IT时期的TQM——技术