轴类零件机械加工工艺设计.docx
《轴类零件机械加工工艺设计.docx》由会员分享,可在线阅读,更多相关《轴类零件机械加工工艺设计.docx(28页珍藏版)》请在冰豆网上搜索。
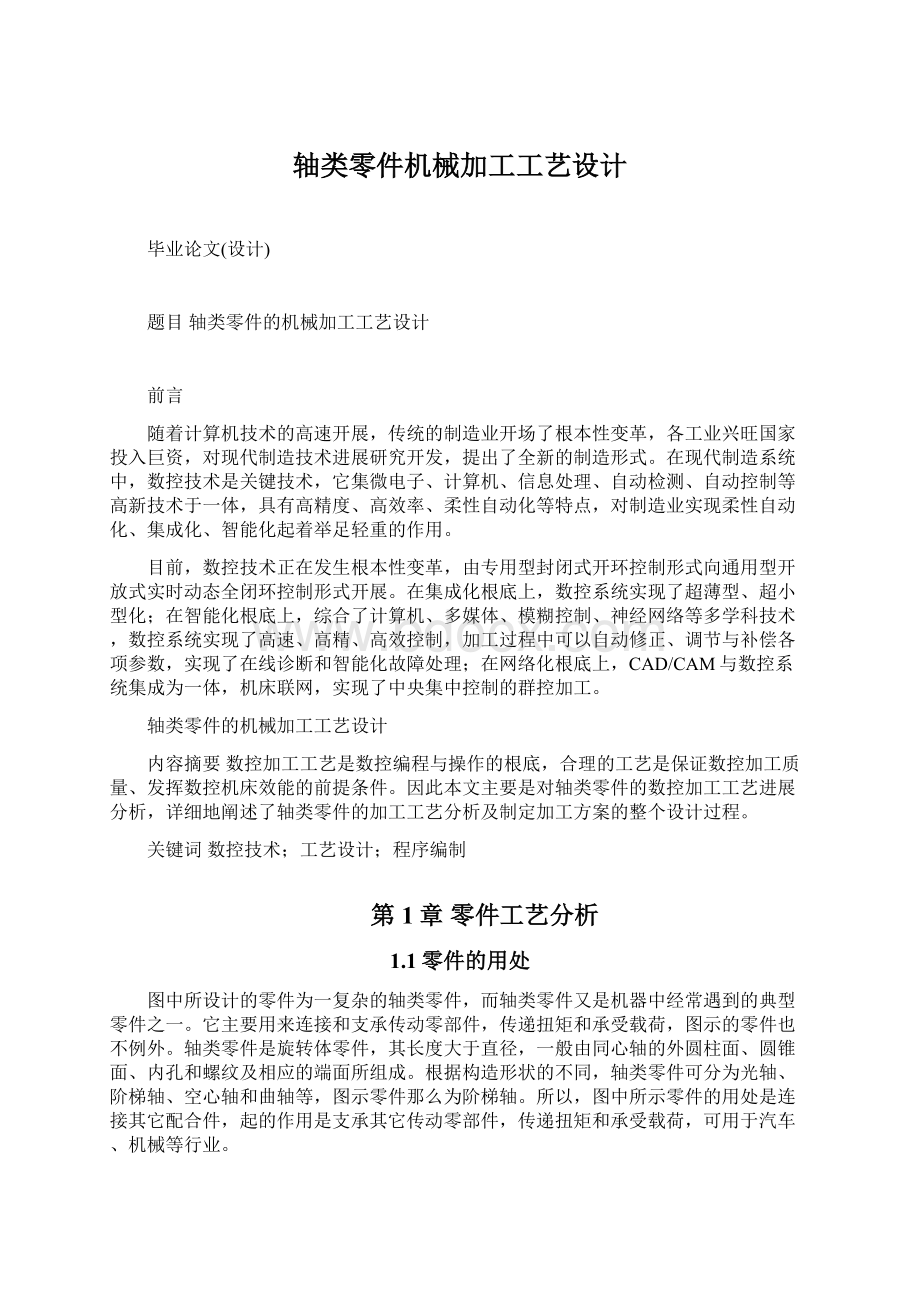
轴类零件机械加工工艺设计
毕业论文(设计)
题目轴类零件的机械加工工艺设计
前言
随着计算机技术的高速开展,传统的制造业开场了根本性变革,各工业兴旺国家投入巨资,对现代制造技术进展研究开发,提出了全新的制造形式。
在现代制造系统中,数控技术是关键技术,它集微电子、计算机、信息处理、自动检测、自动控制等高新技术于一体,具有高精度、高效率、柔性自动化等特点,对制造业实现柔性自动化、集成化、智能化起着举足轻重的作用。
目前,数控技术正在发生根本性变革,由专用型封闭式开环控制形式向通用型开放式实时动态全闭环控制形式开展。
在集成化根底上,数控系统实现了超薄型、超小型化;在智能化根底上,综合了计算机、多媒体、模糊控制、神经网络等多学科技术,数控系统实现了高速、高精、高效控制,加工过程中可以自动修正、调节与补偿各项参数,实现了在线诊断和智能化故障处理;在网络化根底上,CAD/CAM与数控系统集成为一体,机床联网,实现了中央集中控制的群控加工。
轴类零件的机械加工工艺设计
内容摘要数控加工工艺是数控编程与操作的根底,合理的工艺是保证数控加工质量、发挥数控机床效能的前提条件。
因此本文主要是对轴类零件的数控加工工艺进展分析,详细地阐述了轴类零件的加工工艺分析及制定加工方案的整个设计过程。
关键词数控技术;工艺设计;程序编制
第1章零件工艺分析
1.1零件的用处
图中所设计的零件为一复杂的轴类零件,而轴类零件又是机器中经常遇到的典型零件之一。
它主要用来连接和支承传动零部件,传递扭矩和承受载荷,图示的零件也不例外。
轴类零件是旋转体零件,其长度大于直径,一般由同心轴的外圆柱面、圆锥面、内孔和螺纹及相应的端面所组成。
根据构造形状的不同,轴类零件可分为光轴、阶梯轴、空心轴和曲轴等,图示零件那么为阶梯轴。
所以,图中所示零件的用处是连接其它配合件,起的作用是支承其它传动零部件,传递扭矩和承受载荷,可用于汽车、机械等行业。
零件图工艺分析
μμm。
经过以上分析,我可以采用以下几点工艺措施:
〔1〕椭圆轴外圆轮廓的尺寸精度都是要求公差在0~-0.05范围之内.因此编程时可以按整数编,粗加工过后,精加工之前统一进展磨耗调整,使得零件精度得到保证,即在磨耗调整中输入-0.025。
假设因加工误差导致零件加工出偏少那么在磨耗中加一个数值,假设零件加工出偏大那么减一个数值。
总之根据实际情况调整尽量使零件加工后尺寸处于公差范围中间值。
〔2〕在轮廓曲线上,有一处椭圆弧与阶梯轴相连,为了保证其椭圆起点与阶梯轴的端部相连的准确性,通过椭圆公式,及所给条件算出椭圆弧起点坐标为(22.98,12.144)。
〔3〕零件的右端是由外螺纹,圆柱、圆弧、槽等外表组成,且每段圆柱轴的长度很少,显然不好装夹,因此为了保证工件的定位准确、稳定、夹紧方便可靠、支撑面积大、便于装夹,所以应留在最后加工,先装夹毛坯加工左端内、外外表及圆柱φ38mm。
再调头装夹φ36mm的圆柱加工右端。
1-1椭圆球轴类零件图
1.3零件毛坯及材料的选择
轴类零件可根据使用要求、消费类型、设备条件及构造,选用棒料、锻件等毛坯形式及毛坯材料。
对于外圆直径之间相差不大的阶梯轴,一般以棒料为主;而对于外圆直径相差大的阶梯轴或重要的轴,常选用锻件,这样既节约材料又减少机械加工的工作量,还可改善机械性能。
由于该零件的进展机械要求不是很高且阶梯轴外圆直径相差不大,故毛坯选用棒料。
毛坯规格选择为φ40⨯120mm。
如下列图所示:
图1-2
45号钢是轴类零件的常用材料,它价格廉价经过调质〔或正火〕后,可得到较好的切削性能,而且能获得较高的强度和韧性等综合机械性能,淬火后外表硬度可达45~52HRC。
由于该零件无很高的机械性能要求,因此该零件材料选用45号钢。
第2章加工设备及辅助工具的选择
2.1机床的选择
根据该零件外形属于轴类零件,比拟合适在车床上加工,又经过对零件图尺寸及形状分析,尺寸精度较高且要加工椭圆弧及内腔,普通机床不能加工出该零件的形状,也很难保证其尺寸精度、外表粗糙度,为了保证零件的加工尺寸精度和外表质量,因此选用数控车床,由于我们学校如今使用的是FANUC数控系统,所以利用学校资源。
我选择在本校的数控机床FANUC-CK6140加工该零件。
数控机床FANUC-CK6140实物图见附录一。
2.2刀具的选择
刀具的选择是数控加工中重要的工艺内容之一,它不仅影响机床的加工效率,而且直接影响加工质量。
编程时,选择刀具通常要考虑机床的加工才能、工序内容、工件材料等因素。
与传统的加工方法相比,数控加工对刀具的要求更高。
不仅要求精度高、刚度高、红硬性好、耐用度高,而且要求尺寸稳定、安装调整方便,能适应高速和大切削用量切削。
选刀具时,要使刀具的尺寸与被加工工件的外表尺寸和形状相适应。
根据该零件分析选刀如下:
1、由于是钢件,平端面时我选用45°硬质合金端面车刀。
2、零件外圆粗车、精车在这里我选择一把硬质合金右端面93°外圆车刀。
零件内轮廓形状加工时我选用的是刀杆为20×20mm材料为硬质合金的镗孔刀。
3、切槽时由于零件中外形槽宽为8mm,一般都选刀宽4mm,刀杆20×20mm材料为硬质合金的切槽刀,切外形槽时选用4mm刀宽就可以了。
零件的内形槽槽宽也是8mm,因此我选用3mm的内切槽刀切内槽。
4、切螺纹时为了保证其螺纹刀的强度我选用的材料是硬质合金的60°外螺纹车刀和60°内螺纹车刀。
2.3量具的选择
数控加工一般采用通用量具,如游标卡尺、百分表、内径千分尺等,为了使零件加工后到达技术要求,我选择的量具规格是:
外端面长度用规格为0~150mm游标卡尺进展测量;内孔用规格25~50mm内径千分尺进展测量。
螺纹用0~150mm的游标卡尺进展测量,槽用高度尺测量。
量具的精度必须与加工精度相适应,以进步工件的测量精度。
2.4夹具的选择
数控机床加工零件中必须在机床上占有一个正确的位置,才能使工件加工后到达工序加工要求。
机床夹具作为在金属切削机床上确保这个正确的位置的一种工艺装备,其设计及使用在金属切削加工、保证零件加工精度和质量中占有关键的地位。
因此选择适宜的夹具非常重要,根据该轴类零件的形状位置精度要求需保证同轴度,那么选用三爪自动定心卡盘。
第3章拟定工艺方案
3.1加工工序的划分
通常工序划分有三种方法:
①按零件的装夹定位方式划分;
②按粗、精加工划分;
③按所用的刀具划分工序;
由于零件需要调头加工,假如按粗、精加工划分工序。
在调头加工前有两次粗加工和精加工,调头后加工有一次粗加工和精加工,这样划分的话显得很繁琐且很难保证其同轴度,所以不可取。
假如按所用刀具划分工序,刀具至少有7把,比拟多,假设要调头加工前后至少要重复使用三把刀,而同一把刀的两次粗、精加工分别在调头加工前后,加工内容不连续,所以也不合理,不易划分工序;只有按零件的装夹定位方式划分工序比拟符合该零件的加工工序,且能保证两次装夹的位置精度,每一次装夹为一道工序。
该零件需调头一次完成三道加工工序即可以完成所有的加工外表,也可以保证各尺寸精度及外表粗糙度。
3.2加工顺序确实定
零件车削加工顺序确定需遵循以下几个原那么:
〔1〕基面先行原那么用作精基准的外表应优先加工出来,因为定位基准的外表越准确,装夹误差就越小。
所以我应先平左端面作为基准面。
〔2〕先主后次由于所加工外表都是重要外表,因此应按照顺序从右到左加工。
〔3〕先粗后精先车削去除大局部的金属余量,再进展成形加工以保证零件的尺寸要求和质量要求。
〔4〕先面后孔因此先加工左端外外表后再钻孔
〔5〕内外交加即对有内外表,又有外外表需加工的零件,安排加工顺序时,应先进展内外外表粗加工,后进展内外外表精加工。
因此我先对左端内外外表进展粗加工,再一次精加工。
3.3加工道路确实定
在数控加工中,刀具的刀位点相对于工件运动轨迹称为加工道路。
编程时,加工道路确实定原那么主要有以下几点:
(1)加工道路应保证被加工零件的尺寸精度和外表粗糙度,且效率高。
尽量使数值计算简单、以减少编程工作量。
(2)应使加工道路最短,这样即减少了程序段,又减少了空行程时间。
(3)确定加工道路时,还要考虑工件的加工余量和机床、刀具的刚度等情况
确定是一次进给,还是屡次进给来完成外表的加工。
综合上面加工道路的原那么及零件详细分析确定的加工道路有四步如下列图所示:
图3-1零件轮廓
第一步:
装夹右端,加工左端内轮廓形状,棒料伸出卡盘外75mm,找正后夹紧。
粗车左端面和外圆并钻φx40mm孔,用G71指令依次粗车左端外轮廓。
图3-2
第二步:
用用G71指令从右到左依次粗车左端内轮廓。
图3-3
第三步:
装夹右端,依次用G70指令精加工左端内轮廓,再进展左端用G01指令内轮廓切槽,G指令内螺纹加工,最后依次用G70指令进展左端外轮廓精加工。
图3-4
第四步:
装夹左端用G73指令对右端外轮廓进展粗加工,用G70指令对右端外轮廓进展精加工,用G75指令切槽,G指令螺纹加工。
图3-5
3.4零件定位基准确实定
零件定位基准的选择包括粗基准和精基准的选择。
〔1〕粗基准选择原那么
①为了保证不加工和加工外表之间的位置要求,应选不加工外表作粗基准。
②合理分配各加工外表的余量,应选择毛坯外圆作粗基准。
③粗基准应防止重复使用。
④选择粗基准外表应平整,没有浇口、冒口或飞边等缺陷。
以便定位可靠。
〔2〕精基准选择原那么
①基准重合原那么:
选择加工外表的设计基准为定位基准;
②基准统一原那么,自为基准原那么,互为基准原那么
综合上述基准选用原那么,由于是轴类零件,在车床上只需用三爪卡盘装夹定位,定位基准应选在零件的轴线上,以毛坯φ40mm的棒料的轴线和右端面作为定位基准。
3.5装夹方式确实定
数控机床与普通机床一样也要选择定位基准和夹紧应力求设计、工艺与编程计算的基准统一,减少装夹次数,尽可能在一次定位装夹后,加工出全部待加工外表,防止采用占机人工调整式加工方案,以充分发挥数控机床的效能。
装夹应尽可能一次装夹加工出全部或最多的加工外表。
由零件图可分析,我应先装夹mm直径毛坯的一端,夹紧其40mm的长度加工左端内外轮廓。
一直加工到零件右端的φmm然后将棒料卸下。
装夹mm的圆柱外表,加工另一端的外轮廓,槽,螺纹。
这样两次装夹即可完成零件的所有加工外表,且能保证其加工要求。
装夹方式如下:
图3-6加工左端装夹图
图3-7加工右端装夹图
3.6工作坐标原点与换刀点确实定
工件坐标系是编程人员在编程时使用的坐标系,编程人员为了编程方便,便于确定工件几何形状上各要素的位置。
选择工件上的某一点为原点,建立一个坐标系,称为工件坐标系。
工件坐标系原点的选择应注意以下三点:
(设计基准与工艺基准)重合,尽量选在精度较高的工件外表,以进步被加工零件的加工精度。
2.工件坐标系原点的选择应有利于编程和数值计算及精度测量。
3.便于对刀。
由于我们学校用的是FANUC系统CK6140VA数控车床,为了方便对刀,一般选工件端面为Z轴坐标原点。
车削时,工件坐标原点是编程时确定地址的根据。
通常把X轴的坐标原点设在主轴的回转中心,也就是工件直径为零的地方:
Z轴的坐标原点是根据零件详细分析确定的。
在这我把Z轴的坐标原点设在工件的端面上。
换刀点确实定,是数控加工工艺分析的重要内容之一。
假如换刀点没确定好那么可能会打到工件就会造成平安事故,因此我根据零件分析确定工件的换刀点和以工件的左端面为工件原点的工件坐标系如下列图所示。
图3-8工件原点和工件坐标系
第4章切削用量选择
合理的切削用量是指充分利用刀具切削性能和机床动力性能(功率、扭矩),在保证质量的前提下,获得高的消费率和低的加工本钱的切削用量。
数控编程时,编程人员必须确定每道工序的切削用量,并以指令的形式写人程序中。
切削用量包括背吃刀量、进给量(进给速度)、主轴转速〔切削速度〕。
对于不同的加工方法,需要选用不同的切削用量。
并编入程序单内。
合理选择切削用量的原那么是:
粗加工时,一般以进步消费率为主,但也应考虑经济性和加工本钱;半精加工和精加工时,应在保证加工质量的前提下,兼顾切削效率、经济性和加工本钱。
详细数值应根据机床说明书、刀具说明书、切削用量手册,并结合经历而定。
4.1背吃刀量确实定
背吃刀量:
ap一般指工件上已加工外表和待加工外表间的垂直间隔。
因此加工该零件背吃刀量选择如下:
零件外轮廓粗车循环时选ap=2mm,精加工时选ap=0.5mm,零件内轮廓粗车循环时选ap=mm,精加工时选ap=0.3mm,内、外螺纹粗车时首选ap=0.6mm,逐刀减少粗车5次后,精车时选ap=0.2mm。
4.2主轴转速确实定
主轴转速应根据零件上被加工部位的直径,并按零件和刀具的材料及加工性质等条件所允许的切削速度来确定。
切削速度除了计算和查表选取外,还可根据经历确定,需要注意的是交流变频调速数控车床低速输出力矩小,因此切削速度不能太低。
光车时,主轴的速度主要根据允许的切削速度Vc(m/min)选取,计算公式是:
N=
〔4-1〕
其中Vc-切削速度
D-工件或刀具的直径〔mm〕
而车螺纹时的主轴转速是:
n<
-k〔4-2〕
式中:
P—工件螺纹的螺距或导程〔mm〕;
k—保险系数,一般取80。
根据切削原理可知,切削速度的上下主要取决于被加工零件的精度、材料、刀具的材料和刀具耐用度等因素。
从理论上讲,Vc的值越大越好,因为这不仅可以进步消费率,而且可以防止生成积屑瘤的临界速度,获得较低的外表粗糙度值。
但实际上由于机床、刀具、工件材料等因素的限制。
参考机械设计手册及经历车轮廓时取:
粗车时Vc=140m/min,精车时Vc=220m/min
代入4-1式中:
=1000
60
=1000
60
得
=1100r/min
计算的主轴转速n要根据机床有的或接近的转速选取
取
=700r/min
=1100r/min
根据工件图样得知P=1.5,由公式n<
-k
计算得n<720,结合公式并根据加工经历确定主轴转速如下:
加工面
粗加工〔r/min〕
精加工〔r/min〕
外圆加工
500r/min
910r/min
内腔加工
450r/min
800r/min
外槽加工
400r/min
内槽加工
350r/min
外螺纹加工
500r/min
内螺纹加工
450r/min
4.3进给速度确实定
进给速度是数控机床切削用量中的重要参数,主要根据零件的加工进度和外表粗糙度要求以及刀具、工件的材料性质选取。
最大进给速度受机床刚度和进给系统的性能限制。
一般粗车选用较高的进给速度,以便较快去除毛坯余量,精车以考虑外表粗糙度和零件精度为原那么,应选择较低的进给速度。
进给速度νf可以按公式νf=f×n计算,式中f表示每转进给量。
在加工此零件时进给速度如下表所示:
加工面
粗车〔mm/r〕
精车〔mm/r〕
车外圆
mm/r
mm/r
镗内孔
mm/r
mm/r
切外槽
mm/r
切内槽
mm/r
车外螺纹
mm/r
车内螺纹
mm/r
第5章工艺文件的制定及程序编制
5.1数控加工工艺卡
产品名称
零件名称
零件图号
姓名
椭圆轴
班级
程序编号
夹具名称
使用设备
车间
机电1105班
O0001O0002
三爪卡盘
CK6140
数控车加工车间
工步号
工步内容
刀具号
刀具规格
主轴转速r/min
进给速度mm/r
背吃刀量
备注
1
装夹右端
平左端面
T04
20X20mm
450r/min
自定
自定
手动
2
对刀及试车外圆
T01
20X20mm
450r/min
自定
自定
手动
3
左端打孔
T05
mm
380r/min
自定
自定
手动
4
对刀、试车内圆
T06
20X20mm
400r/min
自定
自定
手动
5
左端镗孔粗加工
T06
20X20mm
450r/min
自动
6
左端外圆粗加工
T01
20X20mm
500r/min
2mm
自动
7
左端镗孔精加工
T06
20X20mm
800r/min
自动
8
左端外圆精加工
T01
20X20mm
910r/min
自动
9
左端内槽加工
T07
20X20mm
350r/min
4mm
自动
10
左端内螺纹加工
T08
20X20mm
450r/min
自动
11
调头、切断控制尺寸
T02
20X20mm
400r/min
自定
自定
手动
12
右端外圆粗加工
T01
20X20mm
500r/min
2mm
自动
13
右端外圆精加工
T01
20X20mm
910r/min
自动
14
右端外圆槽加工
T02
20X20mm
400r/min
4mm
自动
15
右端外螺纹加工
T03
20X20mm
500r/min
自动
编制
审核
批准
共**页
第**页
5.2刀具卡
产品名称
零件名称
零件图号
程序号
序号
刀具号
刀具名称
刀具
规格
加工外表
补偿量〔mm〕
备注
1
T01
93°外圆车刀
20X20mm
加工外表
右偏刀
2
T02
外圆车槽刀
20X20mm
切削外圆槽及车断
3
T03
外螺纹刀
20X20mm
车削外螺纹
4
T04
45°端面车刀
20X20mm
车削端面
5
T05
麻花钻
mm
钻孔
6
T06
镗孔刀
20X20mm
加工内外表
7
T07
内切槽刀
20X20mm
切削内槽
8
T08
内螺纹刀
20X20mm
车削内螺纹
编制
审核
批准
共**页
第**页
5.3程序编制
加工程序1如下〔零件左端局部需要加工內腔,必须在钻孔后才能进展自动加工〕
GSK
1105班
数控加工程序清单
型别
×××
零件图号
零件名称
椭圆轴
A4
设备
名称
数控
车床
设备型号
CK6140
根本
材料
45钢
硬度
HBs180
工序
名称
外圆
工序号
30
数控
系统
FANCU-0i系统
程序号
O0001
程序清单
O0001(左端加工程序)
程序号
N1
T0101;
选择1号外圆刀1号刀补
N2
M03S500;
主轴正转,转速500r/min
N3
G00X42Z2;
绝对编程,快速毛坯定位轮廓循环起刀点
N4
G71U2R1;
外轮廓粗加工循环,给定加工参数。
N6~N12
N5
G71P6Q12U0.5W0.1F2;
为外轮廓加工循环程序段。
N6
G01X34F0.15;
从循环起刀点以2mm/r进给挪动到轮廓起始点
N7
Z0;
N8
X36Z-1;
倒角
N9
Z-40;
车削直径为36mm圆柱
N10
X38;
车削台阶
N11
Z-56;
车削直径为38mm圆柱
N12
X42;
退到毛坯之外(防止循环加工时刀具撞到工件〕
N13
G00X100;
快速退刀
N14
Z100;
N15
M05;
主轴停顿
N16
M00;
程序暂停
N17
M03S450;(内孔加工)
主轴正转,转速450r/min
N18
T0606;
选择6号镗刀,导入刀具补偿
N19
G00X20Z2;
快速挪动到孔外侧
N20
G71U1.3R1;
内轮廓粗加工循环,给定加工参数。
N22~N29
N21
G71P22Q29U0.3W0.1F2;
为内轮廓加工循环程序段。
N22
G01X32F0.15;
从循环起刀点以2mm/r进给挪动到轮廓起始点
N23
Z0;
N24
X30Z-1;
车削倒角
N25
Z-5
车削30mm的圆柱孔
N26
G02X24Z-8R3;
车削R3的圆弧
N27
G01X21.4;
车削台阶
N28
Z-32;
车削内螺纹圆柱孔
N29
X18;
车削台阶
N30
Z100;
沿轴向快速退出
N31
M05;
主轴停顿
N32
M00;
程序暂停
N33
M03S910;
主轴重新起动,转数为910r/min
N34
T0606;
重新调入6号刀补,引入刀具偏移量或磨损量
N35
G00X20Z2;
快速挪动到孔外侧侧
N36
从N22~N29对轮廓进展精加工
N37
G00Z100
沿轴向快速退出
N38
M05;
主轴停顿
N39
M00;
程序暂停
N40
M03S350;
主轴重新起动,转数为350r/min
N41
T0707;
选择7号内槽刀,导入刀具补偿
N42
G00X20Z2;
快速挪动到孔外侧
N43
G01Z-28F0.1;
直线插补到内槽轴向起点
N44
X26;
沿X方向加工槽底部
N45
X20
快速退刀
N46
Z-30;
沿Z方向前进
N47
X26;
沿X方向加工槽底部
N48
X20;
快速退刀
N49
Z-32;
沿Z方向前进
N50
X26;
沿X方向加工槽底部
N51
X20;
快速退刀
N52
G00Z100;
沿Z方向快速退刀
N53
M05;
主轴停顿
N54
M00;
程序暂停
N55
T0808;
选择8号内螺纹刀,导入刀具补偿
N56
M03S450;
主轴重新起动,转数为450r/min
N57
G00X21.4Z2;
快速挪动到孔外侧
N58
G01Z-4F0.1;
定位到螺纹孔起切点
N59
G92X21.4Z-8F2;
螺纹循环加工参数设置,螺纹精加工俩次
N60
X22.0;
N61
X22.6;
N62
X23.1;
N63
X23.5;
N64
X23.8;
N65
X24;
N66
X24;
N67
G01X10;
N68
G00Z100;
快速退到平安位置
N69
X100;
N70
T0101;
调换1号刀,调入刀补
N71
M05;
主轴停顿
N72
M00;
程序暂停
N73
M03S910;左端外圆粗加工
主轴重新起动,转数为910r/min
N74
G00X42Z2;
N75
G70P6Q1