钢箱梁专项施工方案.docx
《钢箱梁专项施工方案.docx》由会员分享,可在线阅读,更多相关《钢箱梁专项施工方案.docx(41页珍藏版)》请在冰豆网上搜索。
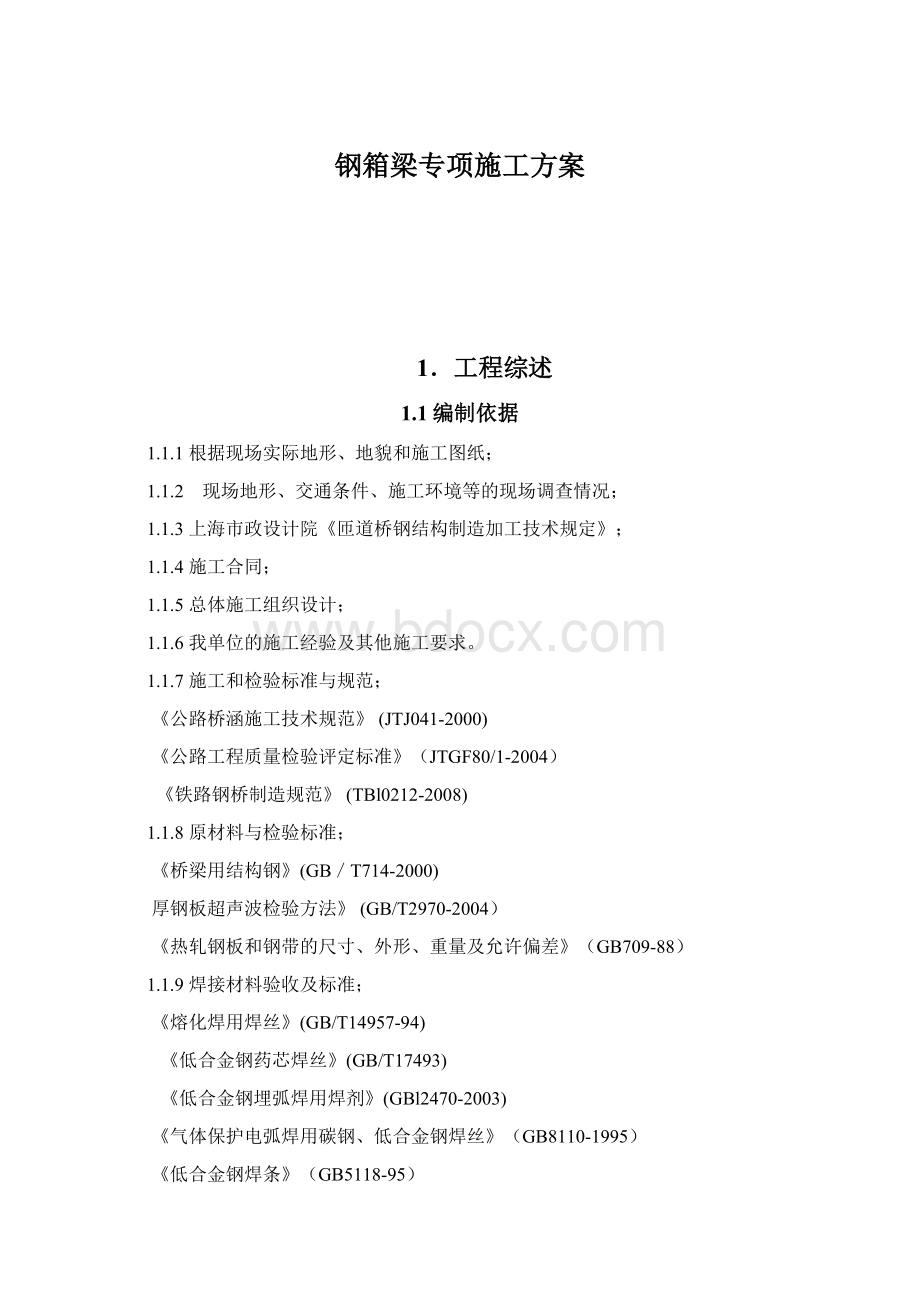
钢箱梁专项施工方案
1.工程综述
1.1编制依据
1.1.1根据现场实际地形、地貌和施工图纸;
1.1.2 现场地形、交通条件、施工环境等的现场调查情况;
1.1.3上海市政设计院《匝道桥钢结构制造加工技术规定》;
1.1.4施工合同;
1.1.5总体施工组织设计;
1.1.6我单位的施工经验及其他施工要求。
1.1.7施工和检验标准与规范;
《公路桥涵施工技术规范》(JTJ041-2000)
《公路工程质量检验评定标准》(JTGF80/1-2004)
《铁路钢桥制造规范》(TBl0212-2008)
1.1.8原材料与检验标准;
《桥梁用结构钢》(GB/T714-2000)
厚钢板超声波检验方法》(GB/T2970-2004)
《热轧钢板和钢带的尺寸、外形、重量及允许偏差》(GB709-88)
1.1.9焊接材料验收及标准;
《熔化焊用焊丝》(GB/T14957-94)
《低合金钢药芯焊丝》(GB/T17493)
《低合金钢埋弧焊用焊剂》(GBl2470-2003)
《气体保护电弧焊用碳钢、低合金钢焊丝》(GB8110-1995)
《低合金钢焊条》(GB5118-95)
1.1.10焊缝及焊接相关检验与规范
《手工电弧焊焊接接头的基本形式与尺寸》(GB985.1-2008)
《埋弧焊焊缝坡口的基本形式与尺寸》(GB985.2-2008)
《钢熔化焊对接接头射线照相和质量分级》(GB3323-2005)
《钢焊缝手工超声波探伤方法和探伤结果的分级》(GBll345-89)
《钢熔化焊脚接焊缝磁粉探伤》(JB/T6061-2007)
1.1.11箱梁涂装及相关检验与标准、规范:
《铁路钢桥保护涂装》(TB1527-99)
《涂装前钢材表面锈蚀等级和除锈等级》(JB8923-88)
《表面粗糙度参数及其数值》(GB1031-95)
《色漆和清漆漆膜厚度的测定》(GB/T13452.2-1992)
《色漆和清漆漆膜的划格试验》(GB/T13452.2-1992)
《金属及其它无机覆盖层厚度测量方法》(GB/T9286-1998)
《涂层附着力的测定方法拉开法》(GB/T52101985)
1.2工程概述
双龙街立交上部结构形式采用钢筋混凝土连续梁结构,跨径布置在18~20m之间,梁高1.5m,在跨越宁潥路主线时ES匝道采用多跨连续钢箱梁结构,梁高2.25m,WN匝道跨越宁潥路主线是采用跨径33~52m的钢箱梁结构,梁高统一为2m。
2、钢箱梁的总体施工方案
2.1总体施工方案
2.1.1、施工方案的确定
目前国内施工钢箱梁的施工方法,基于现场条件,基本都是在厂家分段加工,再运至现场拼装、安装及整体吊装。
实际方案的选择主要依据承包商施工能力、运输方式、安装方式、施工现场条件等因素来确定。
由于我标段钢箱梁不在河道上,不具备水运条件,因此只能采用陆路运输方式。
根据目前公路的路面条件和交通法规要求,货物运输宽度限制一般在3.5米内,长度限制在20米内,图纸要求最短长度为7米,所以根据设计要求,纵向只能分割成7~16.5米长,3.5米宽度以内的段落。
根据实际情况及钢箱梁结构特点,我们确定的钢箱梁总体施工方案是:
钢箱梁采用横向分四大块、纵向分段的方式在厂家加工制作,底漆涂装及箱内中间漆在厂内涂装,采用长车从公路运输,在现场建立与厂内基本一致的加工设施,如移动的封闭加工棚、组装胎架等,将四大组件组装拼接成一个整体段,采用大型起重设备对整体钢箱梁分段吊装到临时支架上,在支架上进行整体段对接焊接,然后拆除该施工分段的临时支架。
钢箱梁具体施工方案为:
1)、加工制作
钢箱梁构件的制作主要分为桥面板、桥底板、桥内侧腹板、桥中腹板、桥外侧腹板、隔舱板、U型肋、I型肋及其肋板等零部件的制作。
钢箱梁在拼装地面胎架流水线上进行组装、焊接。
钢箱梁通过胎架进行组立、焊接以及矫正。
零部件加工通过在数控及机械设备进行。
钢箱梁结构加工制作,以最大限度的使用机械操作并利用工装夹具,以减少手工操作的随机性和不稳定性,提高构件的准确率及生产效率。
焊接完成后按照设计要求进行涂装2层,并经验收合格后方可运输至工地。
2)、构件运输组织
构件在工厂加工完成后,可采用长车进行运输,对于超宽车辆应报请交通运输部门批准后方可起运。
长车应设置必要标志。
钢箱梁应采取牢固的包装,以防构件受损。
行驶路线为沪宁高速进入南京地区,然后转入绕城公路运至工地。
3)、现场拼装
箱梁组拼件在工厂加工后,运输到工地。
工地内拼接长度一般在7~16.5米。
钢箱梁现场组装焊接要求达到与工厂加工水平一致的质量标准。
这要求不能在露天进行加工,要在场地内拼装的临时加工棚内进行,临时加工棚要求隔风挡雨密闭,并安装保暖或降温设施,保持加工棚内良好的施工环境。
箱梁组装必须按图纸要求加工胎架,所使用设备要基本按照厂内设备配置,箱梁焊接尽量采用自动弧焊机或CO2保护焊,特殊情况可采用电弧焊接。
4)、钢箱梁安装
钢箱梁安装支架在节段钢箱梁两端设置临时支架,临时支架应有足够的刚度、强度和稳定性,以防支架变形。
临时支架主要采用钢管为支墩柱搭设而成,设置在钢箱梁节段接口处。
在跨越宁溧路、绕城公路时,应在每个方向留有最少2个车道,以确保交通车辆通行。
箱梁节段采用履带吊吊装,应对其吊装半径、吊装能力进行检算,确保安全。
钢箱梁拼接后应调整位置、标高至设计要求,再进行焊接。
在支架处设置操作平台及检测平台,便于操作,焊接质量应进行探伤检测。
2.2施工组织设计
2.2.1施工组织机构
钢箱梁制作具体管理及部分特殊工种人员见表1。
表1主要管理及技术人员一览表
序号
姓名
职务
职称
备注
1
朱道江
项目经理
高级工程师
2
李红金
项目总工
高级工程师
3
刘维川
质检负责人
工程师
4
田信景
质检员
工程师
5
毛明杰
测量控制
工程师
6
崔恩宁
试验
试验工程师
7
陈茂良
施工安全
安全工程师
5
严国龙
施工队长
工程师
6
丁国元
技术主管
工程师
7
严国弟
严国军
质量员
工程师
8
孙小平
现场安全员
安全员
9
陈建忠
施工员
工程师
10
唐根发
起重指挥
起重指挥
11
严冬青
资料员
资料员
2.2.2安装劳动力计划
制作及安装所需劳动力见表2。
表2劳动力投入计划表
序号
工种
数量
序号
工种
数量
1
管理人员
7
7
测量工
2
2
起重工
6
8
质检员
2
3
起重指挥员
2
9
数控及零部件制作
20
4
安装工
12
10
辅助工
10
5
施焊工
20
6
电工
2
合计
63
2.2.3主要机械设备
制作加工及安装主要机械设备见表3。
表3主要机械设备一览表
序号
设备名称
规格型号
数量
权属
1
门式切割机
F.P.9000D
1
自有
2
门式埋弧焊机
ZR1000
1
自有
3
数控等离子切割机cvt-160
PC5500
1
自有
4
端铣机
dx1500*2000
1
自有
5
液压剪板机
10*3000
2
自有
6
液压折弯机
10*4000
1
自有
7
型钢拼焊流水线
JNY-001
1
自有
8
数控平面钻床
PD16
1
自有
9
车床
CW6163C
2
自有
10
钻床
Z3080
2
自有
11
CO2焊机
CPXS-500
25
自有
12
交流电焊机
Bx1
(2)-500
10
自有
13
埋弧自动焊机
IPEALAREAC1200
3
自有
14
栓钉碰焊机
NELSON6000101
1
自有
15
碳刨机
ZX5-630
3
自有
16
除锈抛丸机
GYP
1
自有
17
铣边机
Xbj—12m
1
自有
18
履带吊
60T
1
自有
19
履带吊
100T
1
自有
20
汽车吊
25T
2
自有
注:
B表示零件宽度,L表示零件长度,H表示零件高度,D表示零件直径。
3工程材料及其管理
3.1工程主材料:
本工程中主体钢构件钢材采用(新余钢厂定轧的)Q345qD低合金高强度结构钢,其质量标准应分别符合我国现行国家标准《桥梁用结构钢》(GB/T714-2000)的要求。
钢材交货状态是:
t<20mm钢板按正火控轧状态交货,t≥20mm钢板按正火状态交货,并提供生产钢板的性能基础实验的证明材料。
所有材料均应专材专用,不得任意代用。
3.2工程焊接材料
所有的焊条、焊丝、焊剂均应与主体金属相适应,应符合《建筑钢结构焊接规程》(JGJ81-2002)。
Q345qd之间的焊接用焊条选用符合《GB5118》的E500系列焊条。
自动焊接或半自动焊接采用的焊丝和焊剂应与主体金属强度相适应,焊丝应符合现行国家标准《熔化焊用钢丝》或《气体保护焊用钢丝》(GB/T14957)的规定。
自动焊接或半自动焊接采用的焊丝和焊剂,其熔敷金属的抗拉强度不应小于相应手工焊焊条的抗拉强度。
3.3涂装材料
钢箱梁涂装材料分别为:
箱体外表面用:
无机富锌底漆,环氧封闭,漆环氧云铁漆,聚硅氧烷面漆;
箱体内表面用:
环氧富锌底漆环氧漆3道
3.4材料管理
3.4.1钢材进场后,应对其表面质量和表面缺陷进行检查,检查钢板尺寸、厚度、重量;检查钢板平整度,钢板2米范围不允许有S变形或折皱,每米波浪度和瓢曲度偏差在2~3mm以内,两端各2m范围内和顺平整,偏差2mm/m。
3.4.2钢厂对钢板按要求进行100%探伤,探伤等级为II级。
3.4.3供货钢板均必须有钢厂质量证明书,钢结构加工厂必须对钢板进行抽检和复检。
钢材按同一厂家、同一材质、同一板厚、同一出厂状态每10批炉号抽检一组试件。
3.4.4钢板要采用悬挂标志牌,标志所示内容还应包括序号/制造号、目的地、理论重量与规格。
3.4.5钢板不得露天存放,应存放在厂房内,并离地20cm以上。
3.4.6如钢板检测不合格,应再加强检测频率,直到对每块板进行检测,如发现仍有不合格的板材,不得再使用,应清除出场。
4、箱梁构件制作要求及工艺流程
主要制作流程见图4.1钢箱梁制作流程图。
图4.1钢箱梁厂内加工工艺流程图
4.1加工材料及技术准备
4.1.1施工单位应根据设图纸及总体方案编制钢结构制作施工工艺细则文件;同时根据设计图纸绘制详细加工图纸,并经建设单位、设计单位及监理单位批准后进行施工。
4.1.2工艺评定:
根据设计要求对一级对接焊缝、二级主要角焊缝进行试件工艺评定,工艺评定要分为现场和工厂加工两种情况。
根据焊缝设计要求等级及《铁路钢桥制造规范制》TB10212-2009制定试件板及焊接技术参数,按照焊接技术参数进行焊接,操作时焊接参数如有修正必须做好记录。
试件完工后,委托有资质的第三方检测机构进行无损检测、物理试验并出具其检测报告,根据检测报告结果,来最终确定焊接工艺。
4.1.3钢板使用前应进行矫平预处理,矫平只能使用冷矫平,使其钢板表面偏差在1mm/m范围内。
4.1.4对钢板进行规定项目的检查和试验,主要是表面质量、内部质量、力学性能、焊接材料进行试验。
4.2放样号料
4.2.1.放样
4.2.1.1.按照施工设计图纸和施工工艺的要求对形状复杂的零部件,采用计算机CAD进行放样,以确定各个零部件的精确尺寸;然后输入到数控加工设备加工。
4.2.1.2.对钢箱梁面板、底板宽度方向允许偏差正负1.0mm;在长度方向应加放2mm加工焊接收缩余量;
4.2.1.3.切割工艺根据评定试验结果编制,切割表面不应产生裂纹。
应优先采用精密(数控、自动、半自动)切割下料,剪切边缘应整齐、无毛刺、反口等缺陷,缺棱应不大于1.0mm,数控切割下料编程时除应考虑焊接收缩量之外,还应考虑切割热变形的影响。
手工气割仅用于工艺特定或切割后仍需机加工的零件,采用普通切割机或手工火焰切下料应根据施工图和工艺文件先作样(样板、样条、样杆),作样时应预留焊接收缩量、加工余量等。
4.2.2.排板
4.2.2.1排板时,钢板的长度方向一般应顺着结构的主要受力方向。
4.2.2.2平行焊缝之间的间距应大于200mm;
4.2.2.3严禁出现十字焊缝,焊缝错开最少20cm;该要求同样适用于现场整体拼装焊缝的要求。
(环型焊缝除外)
4.2.2.4当厚、薄板之间相对接,并且板厚差大于4.0mm时,则应按施工蓝图要求1:
8的斜度削斜。
(见下图4.2);
4.2.2.5钢箱梁的面板、底板、腹板的对接焊缝应错开~200mm,且成阶梯形(见下图4.3)。
图4.2图4.3
4.2.3号料与划线
4.2.3.1.零部件加工:
因桥箱梁为多块大小不一的钢板焊接成型的,所以各种规格的零部件很多,我们对其进行分类划分,分别为桥面板、桥底板、桥内侧腹板、桥外侧腹板、隔舱板、U型肋、I型肋、及其余肋板等,为了保证其零部件的尺寸,均采用1:
1放样式制作,对其形状较复杂的隔舱板进行数控号料,以保证尺寸精确。
U型肋的制作先有多头直条开料机切割成直条钢板,然后采用专用模具在折弯机折弯成型。
号料前应先确认材质和熟悉工艺要求,然后根据排版图、下料加工单和零件草图进行号料。
号料的母材必须平直、无损伤及其他缺陷,否则应先矫正或剔除
4.2.3.2焊缝坡口:
根据设计要求按《公路桥涵施工技术规范》(JTJ041-2000》)规范施工。
4.2.3.3根据零部件的位置实际情况,坡口形式如以下示意图(图4-4):
(除示意图及施工蓝图明注以外的焊缝均为贴角焊缝)。
图4-4
4.2.3.3划线公差要求:
项目
允许偏差
基准线,孔距位置
≤0.5mm
零件外形尺寸
≤1.0mm
4.2.3.4划线后应标明基准线、中心线和检验控制点。
作记号时使用凿子一类的工具,样冲标记其深度应不大于1.0mm,钢板上不应留下深度大于1.5mm的划痕。
4.2.4切割和刨削加工
4.2.4.1切割工具的选用:
设备及工具名称
切割形式
切割项目
门式多条切割机
氧乙炔气体火焰切割
板材
数控切割机
等离子、气体火焰切割
板材
铣边机
刀片
板材
4.2.4.2切割前应清除母材表面的油污、铁锈和潮气;切割后气割表面应光滑无裂纹,熔渣和飞溅物应除去,剪切边应打磨。
4.2.4.3气割的公差度要求:
项目
允许偏差
零件的长度
长度±1.0mm
零件的宽度
钢箱梁面板、底板、腹板:
宽度±1.0mm
零件板:
宽度±1.0mm
切割面不垂直度e
t≤20mm,e≤1mm;
t≥20,e≤t/20且≤2mm
割纹深度
0.5mm
局部缺口深度
对≤2mm打磨且圆滑过度。
对≥2mm电焊补后打磨且圆滑过度。
4.2.4.4切割后应去除切割熔渣;对于组装后无法精整的表面,应在组装前进行处理。
4.2.4.5火焰切割后须自检零件尺寸,然后标上零件号,再由质检员专检各项指标,合格后才能流入下一道工序。
4.2.4.6刨削加工的允许偏差
序号
项目
允许偏差(mm)
1
零件宽度、长度
±1.0
2
加工边直线度
L/3000且不大于2.0
3
相邻两边夹角角度
±6'
4
加工面垂直度
≤0.025t且≤0.5
4.2.4.7端部铣平和半自动气割的允许偏差
项目
半自动气割
铣削
序号
检查内容
允许偏差(mm)
允许偏差(mm)
1
加工后构件两端长度
根据附图公差
±2.0
2
加工平面平面度
±0.5
3
两端铣平时零件长度
2.0
±0.8
4
加工平面对轴线的垂直度
1.5H/1000
≤1/1500且≤0.50
4.3钢箱梁单元的组合拼装
4.3.1车间组装钢箱梁前必须车间内搭建零部件总组装地面胎架,搭建胎架材料采用焊接H型钢,为规格HB500*250*8*12,H型钢每根长度为11米,根据设计图纸的纵坡、横坡和起拱度尺寸有技术部细化出胎架所需的坐标和控制点尺寸。
每次组装前应对胎架进行检查,确认合格后方可组装。
梁段组装过程中应避开日照的影响,用经纬仪和测距仪监控主要定位尺寸。
H型钢布置间距与钢箱梁的横隔板的间距相同,搭建时采取桥面板面向地面,使用水准仪将每一根H型钢所在位置的纵坡、横坡和起拱度尺寸标出和固定,然后将H型钢用20#槽钢连接整体刚性胎架。
胎架的坐标和纵坡、横坡和起拱度尺寸如图4.5、图4.6所示。
4.3.2组装前应熟悉图纸和工艺文件,按图纸核对零件编号、外形尺寸和坡口方向,确认无误后方可组装。
采用埋弧焊、CO2气体(混合气体)保护焊及低氢型焊条手工焊方法焊接的接头,组装前应彻底清除待焊区域的铁锈、氧化铁皮、油污、水分等有害物,使其表面显露出金属光泽。
组装时应在对接焊缝和主要角焊缝的端部连接引板,其材质、厚度、坡口应与所焊件相同。
U型板及顶板设在自动定位组装胎架上进行。
所有零件在组装前应进行尺寸检查,合格后方可组装。
4.3.3单元拼装采用倒装法拼装,拼装顺序为底板—横隔板---两侧腹板---悬挑梁----牛腿---肋板。
拼接后检查拼接尺寸、板缝宽度、板边弧线、拱度、高度,同时还要进行板的冲突检查。
对存在问题的零件要进行整修,不能整修的要重新进行加工。
4.3.4U型肋与顶板焊接前,内侧应完成涂装,所有切割处均打磨平肋与顶板之间采用单面坡口焊接。
.U型肋对接焊缝、在工厂坡口双面焊接,凸起高度不超过20%焊宽;现场采用单面坡口对焊,内衬永久性钢板垫片(4mm)。
4.3.5各类焊缝坡口型式应按本桥设计图纸、焊接工艺及相应规范要求进行加工。
4.3.6分段拼装应考虑必要的防止变形的措施,如设置假隔舱,以确保接头尺寸精度。
4.3.7应设置单向或双向弧形胎架拼装弧形分段,胎架要有足够的刚度,每段组装完成后需进行复测和调整。
4.3.8冷校的环境温不应低于5℃,矫正时应缓慢用力,总变形量不应大于变形部位原始长度的2%。
热校加热温度应控制在600~800℃,不允许过烧,不易在同一部位多次重复加热。
4.4厂内分段预拼装
4.4.1预拼装是构件的组件与组件、分段与分段进行试拼,每一试拼单元必须是相邻组件与分段,至少相连的3块,纵横均应进行试拼,试装不合格不能出厂,试拼合格后运走前面2块,留下1块前移用于下批试拼。
4.4.2试拼装在拼装胎架上进行,胎架根据钢箱梁线型设计,应对胎架进行总体测量。
要求各构件应保持自由状态,接缝符合规范要求。
4.4.3均应逐个检查,证明焊缝及构件各部尺寸、形状符合要求后,再进行预拼。
4.4.4预拼过程中,应检查拼接处有无互相抵触的情况。
4.4.5对拼装好的构件及零件进行编号、登记,绘制拼装编号图。
4.5焊缝探伤检测
4.5.1设计要求
本工程钢箱梁对接焊缝质量应符合《公路桥涵施工技术规范》(JTJ041-2000)规定的一、二级焊缝质量标准。
(JTJ041-2000)表17.2.27-2焊缝超声波探伤内部质量等级
项目
质量等级
适用范围
对接焊缝
Ⅰ
主要杆件受拉横向对接焊缝,工地主要纵向焊缝
Ⅱ
主要杆件受压横向对接焊缝、次要纵向对接焊缝
角焊缝
Ⅱ
主要角焊缝
(JTJ041-2000)表17.2.27-3焊缝超声波探伤范围和检验等级
焊缝质量等级
探伤比例
探伤部位
板厚
检验等级
ⅠⅡ级横向对接焊缝
100%
全长
10-45
B
>46-56
B(双面双侧)
Ⅱ级焊缝
100%
焊缝两端各1000
10-45
B
>46-56
B(双面双侧)
Ⅱ级熔透角焊缝
100%
两端螺栓孔部位并延长500,板梁主梁及纵、横梁跨中加探1000
10-46
B
>46-56
B(双面单侧)
钢箱梁的焊缝等级:
钢箱梁的桥面板、桥底板、纵向腹板的横向对接焊缝为全熔透一级,桥面板、桥底板、腹板纵向主角焊缝、U型肋、I型肋现场对接为全熔透二级,U型肋与桥面板焊接为坡口焊及其余焊缝为二级。
焊缝具体位置,一级焊缝:
面板对接、腹板对接、底板对接、现场焊接主要纵向对接焊缝。
二级焊缝:
腹板与底板、顶板的焊接、I型肋、U型肋对接。
4.5.2检测方法:
本工程将选用有无损检测资质的检测单位对本工程钢结构I、II级焊接焊缝质量进行射线及超声波探伤检查。
I级焊缝采用100%超声波检测并抽检10%射线检验,II级焊缝按规范规定进行超声波检测,裂缝采用磁粉检测。
由于U型肋采用超声波不易检测,一般要带随梁试件进行焊缝检测。
4.5.3检测标准
全熔透焊的一、二级焊缝采用超声波探伤进行内部缺陷的检查,检验标准为现行国家标准《钢焊缝手工超声波探伤方法和探伤结果分级法》GB11345-89B类Ⅱ级合格。
抽查10%的全熔透焊的一级焊缝射线检验标准为现行国家标准《钢熔化焊对接接头射线照相和质量分级》(GB3323-2005)B类Ⅱ级。
裂缝检测采用磁粉探伤,检验标准为现行国家标准《钢熔化焊脚接焊缝磁粉探伤》(JB/T6061-2007),对焊缝表面裂纹的检查,由于制作周期因素只能对钢箱梁分批进行探伤,对每批已超声波探伤合格的钢箱梁先开具超声波、磁粉探伤合格临时报告,便于进入下一工序施工,待每一个施工段的钢箱梁最后一批超声波、磁粉探伤完成,开具正式探伤报告。
4.6.焊接工艺评定及焊接工艺
4.6.1焊接工艺评定的一般要求
4.6.1.1焊接工艺评定(以下简称“评定”)是编制焊接工艺的依据。
4.6.1.2评定条件应与产品条件相对应,评定必须使用与产品相同的钢材及焊接材料。
4.6.1.3根据钢材类型、结构特点、接头形式、焊接方法、焊接位置等制定评定方案,
4.6.1.4首次采用的钢材和焊接材料必须进行评定,已评定并批准的工艺,可不再进行评定;遇有下列情况之一者,应重新进行评定:
——钢种改变;
——焊接材料改变;
——焊接方法或焊接位置改变;
——衬垫材质改变;
——焊接电流、焊接电压或焊接速度改变±10%以上;
——坡口形状和尺寸改变(坡口角度减少10°以上,钝边增大2mm以上,根部间隙变化2mm以上,有衬垫的根部间隙变化在-2~+6mm);
——预热温度低于规定值下限温度20℃;
——增加或取消焊后热处理时;
——电流种类及极性改变;
——加入或取消填充金属;
——母材焊接部位涂车间防锈漆而焊接时又进行不打磨的;
4.6.1.5“评定”包括进行对接接头试验、熔角接透试验和T型接头试验。
4.6.2.试板
4.6.2.1对接接头代表板厚范围按下表执行。
C2.1对接接头试板厚度(mm)
序号
试板板厚
产品板厚
备注
1
t≤16
0.5t<δ≤1.5t
δ—产品板厚
t—试板板厚
2
16<t≤25
0.75t<δ≤1.5t
3
25<t≤50
0.75t<δ≤1.3t
4
50<t≤80
0