斜齿轮轴机械工艺课程设计解析.docx
《斜齿轮轴机械工艺课程设计解析.docx》由会员分享,可在线阅读,更多相关《斜齿轮轴机械工艺课程设计解析.docx(26页珍藏版)》请在冰豆网上搜索。
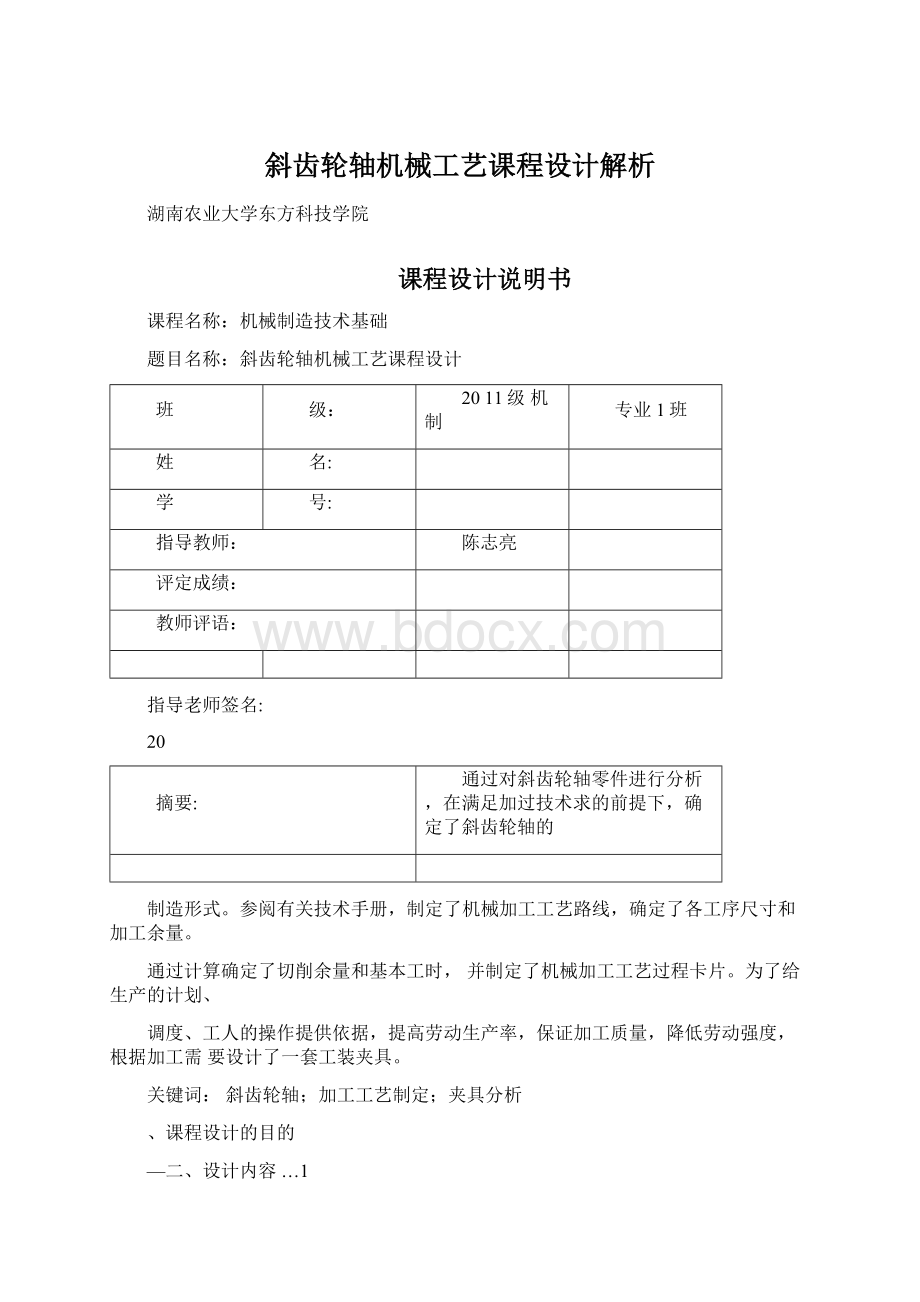
斜齿轮轴机械工艺课程设计解析
湖南农业大学东方科技学院
课程设计说明书
课程名称:
机械制造技术基础
题目名称:
斜齿轮轴机械工艺课程设计
班
级:
2011级机制
专业1班
姓
名:
学
号:
指导教师:
陈志亮
评定成绩:
教师评语:
指导老师签名:
20
摘要:
通过对斜齿轮轴零件进行分析,在满足加过技术求的前提下,确定了斜齿轮轴的
制造形式。
参阅有关技术手册,制定了机械加工工艺路线,确定了各工序尺寸和加工余量。
通过计算确定了切削余量和基本工时,并制定了机械加工工艺过程卡片。
为了给生产的计划、
调度、工人的操作提供依据,提高劳动生产率,保证加工质量,降低劳动强度,根据加工需要设计了一套工装夹具。
关键词:
斜齿轮轴;加工工艺制定;夹具分析
、课程设计的目的
—二、设计内容…1
二、零件分析・3
四、毛坯的确定.4
五、工艺规程的设计.5
六、拟定加工工艺路线方案.7
七、选择加工设备及工艺装备10
丿八、确定工序尺寸12
九、切削用量的选择13
十、夹具的设计15
十一一、总结26
十二、参考文献26
本课程设计是学生在学完机械制造技术基础课程的一个综合性和实践性很强的教学环节,通过课程设计,能综合运用所学基本理论以及在生产实习中学到的实践知识进行工艺及结构设计的基本训练,掌握机械制造过程中的加工方法、加工装备等基本知识,提高学生分析和
解决实际工程问题的能力,为后续课程的学习及今后从事科学研究、工程技术工作打下较坚
实的基础。
本次机械制造工艺学课程设计不仅仅能帮助我们利用已学的知识进行设计,还培养了我
们自己分析,独立思考的能力。
这次综合性的训练,我在以下几方面得到锻炼:
1、能熟练运用机械制造工艺学课程中的基本原理以及在生产实习中学到的实践知识,正
确地解决一个零件在加工中的定位,夹紧以及工艺路线安排,工艺尺寸确定等问题,保证
零件的加工质量。
2、提高结构设计能力。
通过设计零件的训练,获得根据被加工零件的加工要求,设计出高效,省力,经济合理而能保证加工质量的零件的能力。
3、学会使用手册以及图表资料。
掌握与本设计有关的各种资料的名称,出处,能够做到熟练的运用。
对我而言,我希望通过这次课程设计对自己未来将从事的工作进行一次适应性训练,从中
锻炼自己发现问题,分析问题和解决问题的能力,为今后参加工作打下良好的基础。
由于个人水平亟待提高,设计尚有许多不足之处,恳请老师给予指教。
斜齿轮轴机械工艺课程设计
一、课程设计的目的
机械制造技术是以机械制造中的工艺问题为研究对象,实践性较强的一门学
科,学生在学完了该课后并完成了生产实习的基础上,还应通过课程设计受到一次理论联系实际的综合训练,培养运用所学知识分析和解决机械制造工艺技术问题的能力。
通过课程设计,学生应在下述各方面得到锻炼:
1、能熟练运用机械制造技术课程中的基本理论以及在生产实习中学到的实
践知识,正确的解决一个零件在加工中的定位。
夹紧以及工艺路线安排、工艺尺寸确定等问题,保证零件的加工质量。
2、提高结构设计能力。
学生通过设计夹具的训练,应当获得根据被加工零件的加工要求,设计出高效、省力、既经济合理又能保证加工质量的夹具的能力。
3、学会使用手册及图表资料。
4、能具备一定创新能力的培养。
二、设计内容
(1)、分析零件图纸,进行工艺审查。
1、本零件为机械设备的斜齿轮轴轴,功用是传递动力和改变输出轴运动方向
要求编制一个典型的中等复杂程度的机器零件的机械加工工艺规程,按教师
指定设计其中一道工序的专用夹具,并撰写设计说明书。
具体内容如下:
1)、选择毛坯的制造方法,制定毛坯技术要求。
2)、拟定零件的机械加工工艺过程。
3)、合理选择各工序的定位基准。
4)、正确确定各工序的夹压位置和夹紧力的方向和作用点
5)、确定各工序所用的加工设备。
6)、确定刀具材料,类型及规定量具种类。
7)、确定一个加工表面的工序余量和总余量。
8)、选定一个工序的切削用量。
9)、确定工序尺寸,正确拟订工序技术要求。
10)、确定工序使用的冷却润滑液。
11)、计算一个工序的单件工时。
12)、设计指定工序的专用夹具(需计算切削力、夹紧力)绘制夹具装配图。
13)、测绘夹具中的指定零件
14)、填写工艺文件。
15)、编写设计说明书。
(以上内容的取舍根据具体情况由教师酌定)
三、零件分析
3.1零件的结构分析
3.1.1工艺特点
齿轮轴类件的工艺特点首先是它的形面特征多,在基于特征的零件信息描述中可以把它分为主特征:
内外圆柱面、圆锥面、齿轮表面等;辅助特征:
键槽、小平面、花键、螺纹等。
另外,齿轮轴类件加工所使用的机床多,材料及热处理种类也较多。
它的工艺特征如尺寸精度、形位公差、表面质量也要求较高。
在机械加工中,每一种零件都有几种加工工艺方法与之对应,根据生产规模、零件整
体形状和轮廓尺寸、制造资源等,针对每一特征的加工精度、表面粗糙度及不同材料选择不同加工方法。
且此零件为大批大量生产,工艺安排倾向于工序分散原则,选用通用设备+
通用公装,工艺手段采用常规工艺。
3.1.2基本工艺过程
1、铣端面——铣床
2、热处理----调质
3、钻中心孔----钻床
4、车右端外圆、倒角----车床
5、车左端外圆、齿顶圆及倒角----车床
6、钻孔----钻床
7、铣左端凹槽——铣床
8铣右端圆弧面----铣床
9、滚齿——滚齿机
10、去毛刺----钳工
11、成品检验
3.2零件的结构工艺分析
「20、门24.7、门16圆柱面及门28.75齿面。
其主要加工的面有车门20、
「24.7的外圆柱面及齿面,铣1个4的槽。
由于传动与装配的要求较高,对于
门20、门24.7、门16圆柱面有较高的同轴度要求,对于门20圆柱面及门28.75
齿面有径向圆跳动要求,对于:
J20圆柱面与4的槽有较高的对称度要求。
粗糙度方面表现在:
对于门20、叮•■28.75圆柱表面端面有较高的要求为Ra1.6卩m,
要求较高。
其余为Ra12.5卩m这些在安排加工工艺时也需给予注意。
工件上大
量的倒角为1X1,加工过程中应该主意。
四、毛坯的确定
4.1毛坯的选择
毛坯的选择和拟定毛坯图是制定工艺规程的最初阶段工作之一,也是一个比
较重要的阶段,毛坯的形状和特征(硬度,精度,金相组织等)对机械加工的难
易,工序数量的多少有直接影响,因此,合理选择毛坯在生产占相当重要的位置,
同样毛坯的加工余量的确定也是一个非常重要的问题。
毛坯种类的选择决定与零件的实际作用,材料、形状、生产性质以及在生产中
获得可能性,毛坯的制造方法主要有以下几种:
1、型材2、锻造3、铸造4、焊
接5、其他毛坯。
根据零件的材料,推荐用型材或锻件,但从经济方面着想,如用型材中的棒料,加工余量太大,这样不仅浪费材料,而且还增加机床,刀具及能源等消耗,本零件的主要功用是传递动力,其工作时需承受较大的冲击载荷,要求有较高的强度和韧性,以使金属纤维尽量不被切断。
因为直径差较大的阶梯轴,为了节约材料和减少机械加工的劳动量,锻造使零件粗略成型,改善纤维组织提高零件强度。
对于中等精度而转速较高的轴类零件多选用45号钢,这类钢经调质处理和高淬火后,具有较高的综合机械性能,能满足使用要求,毛坯的尺寸要求高。
又由于需要量产,且零件形状较简单,尺寸也不大,故应采用模锻棒。
坯料图
4.2外圆表面尺寸的确定
加工长度为107毫米,与其连接的最大外圆表面直径为①28.75,为简化模锻毛坯的外形,现直接取外圆表面直径为①30,①20表面粗糙度为Ra1.6,需要半精加工和精加工即可此时直径余量为7已能满足加工要求①20X12、①20X17、①20X30、①24.7X3、①16X3、①16X6。
4.3外圆表面沿轴线长度方向加工余量及公差的确定
查《机械制造工艺设计简明手册》锻件复杂形状复杂系数为S1锻件材质系数为M1,锻件轮廓尺寸(长度方向)大于0-95毫米,故长度方向偏差为+1.9—-0.9毫米。
长度方向余量查表2.2-25其余量规定值为8-12毫米,取10毫米①20处外圆加工余量为11mm①30处外圆加工余量为10mm①24处外圆加工余量为10mm①16处外圆加工余量为11mm因为锻造长轴时,有可能出现不在同一轴线上,故流余量稍大些,防止毛坯报废。
查《工艺手册》粗车外圆后半精车余量单边留1.2mm即可,半精车后外圆磨削余量0.5mm.由于毛坯及以后各道工序的加工都有加工公差,因此所规定的加工余量其实只上只是名义上的加工余量。
实际上,加工余量有最大最小之分。
由于本设计规定的零件为大批生产,应该采用调整法加工,因此在计算最大、最小加工余量时,应按调整法加工方式予以确定,但轴类零件一般以两中心孔定位,加工精度就可保证,所以不用调整法加工即可。
4.4毛坯图的设计
毛坯(锻件)图是根据产品零件设计的,经查《机械加工工艺手册》、《机
械零件工艺手册》,再考虑到其所要加工的次数,知磨削余量,精车----粗车各
余量,粗车余量可选用1mm精车余量可选用0.5mm,传动轴磨削余量可取
0.25mm。
毛坯精度等级为IT9级
五、工艺规程的设计
5.1基准的概念和分类
零件是由若干表面组成的,各表面之间都有一定的尺寸和相互位置要求。
用
以确定零件上点、线、面间的相互位置关系所依据的点、线、面称为基准。
基准按其作用不同,可分为设计基准和工艺基准。
5.1.1设计基准
设计图样上所采用的基准称为设计基准。
如零件图上的轴心线是各外圆和槽
的设计基准。
5.1.2工艺基准
在工艺中采用的基准称为工艺基准。
按用途可分为定位基准、测量基准和装配基准。
定位基准加工时使工件在机床或夹具中占据正确位置所使用的基准。
如零件在精车时,中心孔就是定位基准。
测量基准零件检验时,用于测量已加工表面尺寸及位置的基准。
装配基准装配时用已确定零件在部件或产品中位置的基准。
零件图中的
「24.7、门28.78即为装配基准。
5.1.3定位基准的选择
选择工件的定位基准,实际上是确定工件的定位基面。
根据选定的基面加工与否,又将定位基准分为粗基准和精基准。
在起始工序中,只能选择未经加工的毛坯表面作为定位基准,这种基准称为粗基准。
用加工过的表面作为定位基准,则称为精基准。
在选择定位基准时,是从保证精度要求出发的,因此分析定位基
准选择的顺序就应为精基准到粗基准
5.2齿轮轴的基准选择
521粗基准的选择
选择的原则是:
(1)非加工表面原则
(2)加工余量最小原则(3)重要表面原则(4)不重复使用原则(5)便于装夹原则。
根据以上选择的原则,在加工时:
(1)车左端时,以两端端面中心孔作为粗基准。
(2)车右端时,以两端端面中
心孔作为粗基准。
5.1.2精基准的选择
选择的原则是:
(1)基准重合原则
(2)基准统一原则
(3)自为基准原则
(4)互为基准原则
(5)便于装夹原则
根据以上选择的原则,我们就可以选择端面的中心孔作为精基准。
由于该传动轴的几个主要配合表面,轴肩面对基准轴线A-B均有径向圆跳动要求,它又是实心轴,所以应选择两端中心孔为基准,采用双顶尖装夹方法,以保证零件的技术要求。
根据零件的图纸和使用要求分析左右两个①20圆跳动要求为0.008mm基准选择是工艺规程设计中的重要工作之一。
基面选择的正确与合理,可以使加工质量得以保证,生产率得以提高,否则加工工艺过程中会问题百出,更有甚者,还会造成零件大批报废,使生产无法进行。
(1)粗基准的选择对于一般轴类零件而言以外圆作为粗基准是完全合理的。
(2)精基准的选择,以两顶尖孔作为轴类零件的定位基准既符合基准重合原则又能使基准统一。
所以以两顶尖为定位基准。
两顶尖孔质量的好坏对加工精度影响很大,应尽量做到两顶尖孔轴线重合,顶尖接触面积大,表面粗糙度底,否则,将会因工件与顶尖间的接触刚度变化而产生加工误差作为定位基准的中心孔经过多次使用可能磨埙或拉毛或因热处理和内应力发生位置变动或表面产生氧化皮。
因此,经常注意保持两顶尖孔的质量是轴类零件加工的关键问题之一。
5.3制定工艺路线
5.3.1加工阶段的划分
工件的加工质量要求较高时,都应划分加工阶段,一般可分为粗加工、半精加工和精加工三个阶段。
如果加工精度和表面质量要求特别高,则还可增设光整加工和超密加工阶段。
5.3.2各加工阶段的主要任务
(1)粗加工阶段的任务是切除毛坯大部分余量,使毛坯接近成品的形状和尺寸。
(2)半精加工阶段的任务是留下精加工余量后使主要表面达到一定的精度,为精加工做好准备并完成一些次要表面的加工。
(3)精加工阶段的任务是保证各主要表面达到规定的精度和表面粗糙度。
5.3.3加工顺序的安排
(1)切削加工的安排原则:
A.基准先行B.先粗后精C.先主后次D.先面后孔
(2)热处理工序的安排:
A.预备热处理的目的的改善工件的加工性能,消除残余内应力,改善金相组织,为最终热处理做好准备,如正火、退火和调质等。
预备热处理一般安排在粗加工前,但调质常安排在粗加工后进行。
B.消除残余应力处理的目的是消除毛坯制造和切削加工过程中产生的残余应力,如时效和退火。
C.最终热处理的目的是提高零件的力学性能(如强度、硬度、耐磨性等),如调质、淬火、回火以及各种表面处理,一般安排在精加工前。
本零件的主要功用是传递动力,其工作时需承受较大的冲击载荷,要求有较高的强度和韧性,故需要进行渗碳淬火回火热处理。
此零件为配合件,配合部位的精度要求比较高,为了达到图纸的精度要求,应该安排磨削工序,来达到精度要求和提高表面性能。
(3)辅助工序的安排:
辅助工序包括检验、去毛刺、清洗、防锈等检验。
除了工序中自检外,还需在下列场合单独安排检验工序:
a.重要工序前后;b.送往外车间加工之前;c.全部加工工序完成、去毛刺之后。
有些特殊去毛刺常安排在下列场合进行:
a.淬火工序之前;b.全部加工工序结束之后。
5.3.4粗加工阶段
(1)毛坯处理、毛坯备料、锻造和正火。
(2)粗加工,锯去多余部分、铣端面大中心孔和车外圆。
这个阶段的主要目的是:
用大的切削用量切除大部分余量,把毛坯加工至接近工件的形状和尺寸,只留下少量加工余量。
通过这个阶段还可及时发现锻件裂缝及缺陷,做处相应措施。
5.3.5半精加工阶段
(1)半精加工前热处理对于45号钢一般采用调质处理达到HB235
(2)半精加工外圆
这个阶段主要目的是:
为精加工做好准备,尤其为精加工做好基面准备。
一些要求不高的表面,在这个阶段达到图纸规定要求。
5.3.6齿轮加工阶段磨削加工阶段:
(1)粗磨削加工前热处理,低温时效。
(2)精加工前各种加工、铣槽、研中心孔、磨外圆、粗磨齿、二次时效。
(3)精磨齿,保证重要表面的精度。
六、拟定加工工艺路线方案
由于该零件是批量生产,可以采用机床配以专用夹具,工序以分散为主,某些工序可以适当集中应划分加工阶段,将粗加工和精加工分开,工艺路径的拟定,为保证达到零件的几何形状尺寸精度,位置精度及各项技术要求,必须制定合理的工艺路线。
在生产纲领已确定为中批生产的条件下,可以采用通用机床配一专用的工夹量具,并考虑工序集中,以提高生产率和减少机床数量使生产成本降低。
工序如下:
⑴备料:
45号钢①37X107
(2)锻造:
为了零件粗略成型,到节约原材料,减少切削用量,改善纤维组织要严格控制锻造温度,最好能一火锻成,外圆锻造余量8-10毫米,始锻温度1200
度,终锻温度800度,空冷。
⑶退火处理:
目的是降低硬度,改善切削加工性能。
消除锻造应力以及细化晶粒和消除组织不均匀,退火温度840-870C保温5小时,炉冷至550E空冷。
⑷钻中心孔B2GB145-2001,铣端面至尺寸。
⑸粗车:
夹①37粗车①30、①24、①16、①20均留余量3毫米,调头车①20留余量3毫米。
(6)调质热处理:
目的是为了提高零件的机械性能,获得均匀的回火奥氏体,为表面硬化作好纤维组织上的准备,是轴能获得高强度的心部和高硬度的表层。
同时有一个良好的硬度阶梯,避免应力集中。
调质淬火温度830-850C保时1-1.5
分/毫米回火温度600-640C2-4小时调质硬度HB220-25O
⑺钻中心孔。
(8)半精车:
半精车外圆各步,留余量0.5毫米,①30车至尺寸。
(9)滚齿:
齿数21模数1.25精度等级9。
(10)齿表面淬火:
不改变钢的表层成分,仅改变表层组织且心部组织不发生变
化。
目的是保持工件的心部韧性和使表面得到较好的耐磨性,提高其冲击韧性和
疲劳强度等力学性能。
感应加热表面淬火零件宜选用中碳非合金钢和低碳合合金结构钢。
经感应加热表面淬火的工件,表面不易氧化,脱碳变形小,淬硬层深度
易于控制,一般高频感应加热淬硬层深度为1-2毫米,表面硬度比普通淬火高
20-30HB。
此外,该热处理方便生产率高,易于实现机械化,多用于大批大量生产形状简单的零件,符合要求。
(11)铣槽:
保证尺寸。
(12)研磨中心孔。
(13)齿端面到角。
(14)磨外圆:
①24、①16两外圆虽无尺寸精度,由于进给箱齿轮轴在高速运转
中工作,进给箱齿轮轴所产生微小不平衡都全影响内磨质量,因此,两外圆需经
磨削加工。
(15)粗磨齿。
(16)二次时效:
加热到160C保温10小时空冷。
(17)精磨齿。
(18)终检。
(19)入库。
七、选择加工设备及工艺装备
7.1机床的选择
本零件在粗加工阶段所使用的是C616型普通车床,这是一种小型车床,床身最大工件回转半径为160mm最大加工长度为550mm适合批量较小,精度要求不高零件的加工。
在精加工阶段使用的是CJK6132型数控车床,床身上最大工件回转直径:
巾320mm最大加工长度:
600mm精加工阶段使用数控车床加工的优势在于:
数控车床的加工精度比普通车床的高,能满足零件设计的要求,而普通车床难以达到要求。
再者数控车床本身的精度高、刚性大,可选择有利的加工用量,生产率高,是普通车床的3〜5倍。
但数控车床的投资大,使用费用高,生产准备工作复杂。
由于整个加工过程采用程序控制,数控加工的前期准备工作较为复杂,包含工艺确定、程序编制等。
综合考虑这些因素,所以在粗加工阶段所使用的是C616型普通车床来加工,精加工阶段使用的是CJK6132型数控车床
来加工。
7.2刀具的选择
在车床上加工的工序,一般都选用高速钢W18Cr4加工钢质零件采用YT类硬质合金粗加工用YT5,精加工用YT15为提高生产率和经济性,可选用可转位车刀。
(GB5343.1-85,GB5343.2-85)滚齿根据《金属切削原理与刀具》采用A级单头滚刀能达到8级精度。
滚刀选模数为3mm的U型A级精度滚刀
(GB6083-85。
铣刀按直柄键槽铣刀(GB1112-85)零件要求铣切深度为4mm槽宽为8mm因此所选铣刀=铣刀直径d=8mm,L=50mm,l=14mm,d1=®硬质合金顶尖研磨中心孔,把硬质合金顶尖的60度圆锥体修磨成角锥的形状,使圆锥面留下4-6条均匀分布的刃带。
不带护锥的A型中心孔,d=4,D=8.5,L2=3.9,t=3.5。
外圆磨削:
200X20X75—AF60L5\—35m^s。
7.3量具的选择
本零件属成批生产,一般均采用通用量具。
选择量具的方法有两种:
一是按计算器具的不确定度选择;二是按计算器具的测量方法极限误差选择。
选择时,采用其中的一种方法即可。
以及齿厚游标卡尺。
7.3.1径向测量工具
选择各外圆加工面的量具
加工面尺寸
尺寸公差
量具
28.75
0.016
分度值为0.01mm测量范围为25--50mm外径百分尺
(GB1216-85
20
0.016
16
0.125
22
0.125
分度值为0.01mm测量范围为20--50mm外径百分尺
(GB1216-85
7.3.2工具轴向测量
尺寸及公差
量具
30
分度值为0.02,测量范围为0—150游标卡尺。
(GB1214-85
12
17
3
6
22
分度值为0.02,测量范围为0—150游标卡尺。
(GB1214-85
107
分度值为0.02,测量范围为0—500游标深度尺。
(GB1215-87
7.3.3选择加工槽所用量具
槽经粗铣、半精铣两次加工。
槽宽及槽深的尺寸公差等级为:
粗细是均为
IT14;半精铣时,槽宽为IT9级、槽深为IT12均可选用分度值为0.01测量范围0—10百分表(GB1219-85.
D选择滚齿工序所用量具
滚齿工序在加工时测量公法线长度即可。
根据《公差配合与测量技术》,选
分度值为0.01,测量范围0—25的公法线百分尺(GB1217-86
八、确定工序尺寸
确定工序尺寸的一般方法是,由加工表面的最后工序往前推算,最后工序的工序尺寸按需零件图样的要求标注。
8.1确定圆柱面的工序尺寸
圆柱面即轴表面的工序尺寸只与加工余量有关。
前面根据有关资料已查处零件各表面的总加工余量(毛坯余量),应将总加工余量分为各工序加工余量,然后再由后往前计算工序尺寸。
查表修正法是以生产实践和实验研究积累的有关加工余量资料数据为基础,并按具件生产条件加以修正来确定加工余量的方法,该
方法应用比较广泛。
加工余量数值可在各种机械加工工艺手册中查找,其步骤如
下:
1.根据各工序的加工性质,查表得它们的工序余量。
2.确定各工序的尺寸公差及表面粗糙度。
由各工序的加工性质查有关经济加工精度和经济表面粗糙度。
3.根据查的余量计算各工序尺寸。
4.确定各工序的上下偏差。
按“单向入体”原则,对于孔基本尺寸值为公差带的下偏差,上偏差取正值;对于毛坯尺寸偏差应取双向对称偏差。
8.2确定轴向工序尺寸
确定各加工表面的工序加工余量,本零件各端面台阶的工序加工余量。
因为用顶尖顶紧工件进行加工,径向又没有标注公差尺寸,只选用两端面为测量基准,故不用确定工序尺寸,每次工序加工中只选测量出要求尺寸即可。
所以轴向工序
尺寸可略。
8.3确定铣槽的工序尺寸
半精铣可达到零件图样的要求,则该工序尺寸:
槽宽为4mm槽深7mm粗铣时,为半精铣留有加工余量:
槽宽双边余量为2mm槽深余量为2mm则粗铣的工序尺寸:
槽宽为3mm槽深2mm
8.4磨外圆至工序尺寸
磨齿到表面粗糙度。
九、切削用量的选择
粗车工序:
已知加工材料为45号钢,Eb600Mpa锻件,有外皮,坯件D=30mm车削后d=29mm加工长度为107mm机床为c616,工件两端支承在顶尖上。
由于工件是锻造毛坯,加工余量达5mm而加工要求较高,故分两次走刀完成,粗车加工余量为4mm半精车加工余量为0.75mm
粗铣槽工序:
所选刀具为高速钢直柄槽铣刀,铣刀直径=6,立铣刀可直接加工到图纸要求,不用确定切削用量
⑴确定铣削宽度立铣刀=4mm
确定每齿进给量,根据X52型铣床说明书,其功率为75KVy中等系统刚度,根
据说明书v=0.12-0.20
(2)选择铣