国内外聚乙烯的生产技术.docx
《国内外聚乙烯的生产技术.docx》由会员分享,可在线阅读,更多相关《国内外聚乙烯的生产技术.docx(23页珍藏版)》请在冰豆网上搜索。
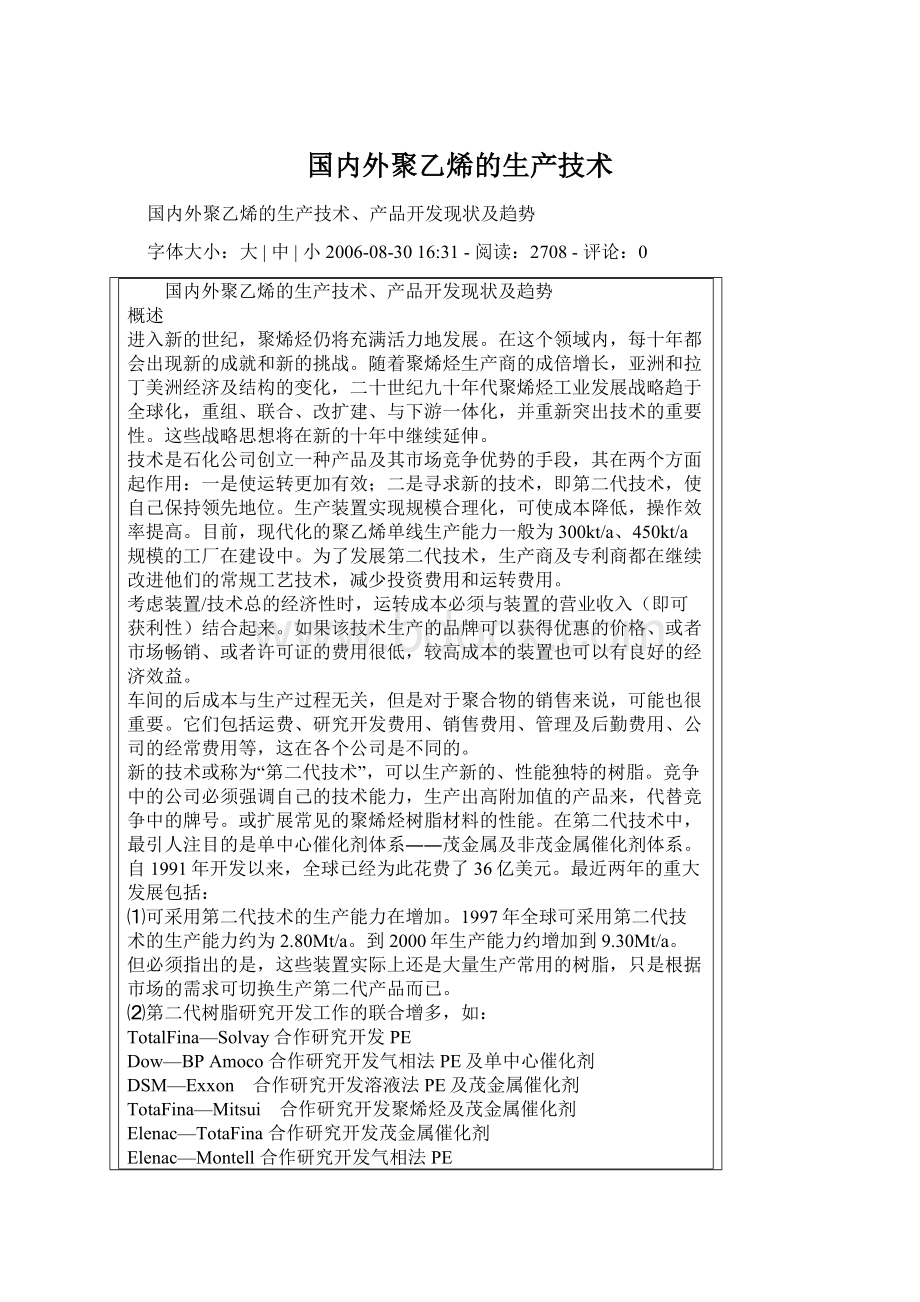
国内外聚乙烯的生产技术
国内外聚乙烯的生产技术、产品开发现状及趋势
字体大小:
大|中|小2006-08-3016:
31-阅读:
2708-评论:
0
国内外聚乙烯的生产技术、产品开发现状及趋势
概述
进入新的世纪,聚烯烃仍将充满活力地发展。
在这个领域内,每十年都会出现新的成就和新的挑战。
随着聚烯烃生产商的成倍增长,亚洲和拉丁美洲经济及结构的变化,二十世纪九十年代聚烯烃工业发展战略趋于全球化,重组、联合、改扩建、与下游一体化,并重新突出技术的重要性。
这些战略思想将在新的十年中继续延伸。
技术是石化公司创立一种产品及其市场竞争优势的手段,其在两个方面起作用:
一是使运转更加有效;二是寻求新的技术,即第二代技术,使自己保持领先地位。
生产装置实现规模合理化,可使成本降低,操作效率提高。
目前,现代化的聚乙烯单线生产能力一般为300kt/a、450kt/a规模的工厂在建设中。
为了发展第二代技术,生产商及专利商都在继续改进他们的常规工艺技术,减少投资费用和运转费用。
考虑装置/技术总的经济性时,运转成本必须与装置的营业收入(即可获利性)结合起来。
如果该技术生产的品牌可以获得优惠的价格、或者市场畅销、或者许可证的费用很低,较高成本的装置也可以有良好的经济效益。
车间的后成本与生产过程无关,但是对于聚合物的销售来说,可能也很重要。
它们包括运费、研究开发费用、销售费用、管理及后勤费用、公司的经常费用等,这在各个公司是不同的。
新的技术或称为“第二代技术”,可以生产新的、性能独特的树脂。
竞争中的公司必须强调自己的技术能力,生产出高附加值的产品来,代替竞争中的牌号。
或扩展常见的聚烯烃树脂材料的性能。
在第二代技术中,最引人注目的是单中心催化剂体系――茂金属及非茂金属催化剂体系。
自1991年开发以来,全球已经为此花费了36亿美元。
最近两年的重大发展包括:
⑴可采用第二代技术的生产能力在增加。
1997年全球可采用第二代技术的生产能力约为2.80Mt/a。
到2000年生产能力约增加到9.30Mt/a。
但必须指出的是,这些装置实际上还是大量生产常用的树脂,只是根据市场的需求可切换生产第二代产品而已。
⑵第二代树脂研究开发工作的联合增多,如:
TotalFina—Solvay合作研究开发PE
Dow—BPAmoco合作研究开发气相法PE及单中心催化剂
DSM—Exxon 合作研究开发溶液法PE及茂金属催化剂
TotaFina—Mitsui 合作研究开发聚烯烃及茂金属催化剂
Elenac—TotaFina合作研究开发茂金属催化剂
Elenac—Montell合作研究开发气相法PE
Mitsui—Dow 合作研究开发PE及单中心催化剂
⑶解决了一些专利的法律纠纷,消除了工业化的障碍。
第二代技术的另一个着重点是开发易加工的LLDPE,采用各种分子结构,使产品加工性接近于LDPE,这些树脂如能在现有的LDPE的加工设备(主要是吹膜设备)上加工,则在终端市场上就可以更多地代替常用的LDPE,包括高LDPE比例的LDPE/LLDPE共混料。
直至3年前重点还是用非茂金属催化剂,主要是改进常用的催化剂体系。
人们主要通过三个基本途径设计LLDPE聚合链:
创造双峰结构(双反应器)、宽分子量分布(MWD)结构(铬系催化剂)、Phillips技术(宽分子量分布)、引入第三单体,形成三元共聚物。
最引人注目的技术是UCC公司的Unipol-Ⅱ技术(双峰)、Phillips技术(宽分子量分布)、Montell公司的Spherilene技术(三元共聚物)以及最近NovaChemical公司的新Schairtech技术(双峰)等。
在过去两年中开发的重点又转移到用茂金属/单中心催化剂来生产易加工树脂的工业化。
这包括Dow公司的长支链(LCB)INSITE催化剂体系(用于Dow的溶液法工艺)、BP-Amoco公司开发的INNOVENE气相法技术、三井的EVOLUE(双峰)气相法工艺、Phillips公司的mPACT技术和Borealis公司的BORSTAR(双峰)淤浆法/气相法工艺技术等。
据美国化学系统公司预测到2005年全球LLDPE市场的21%将为第二代LLDPE所占有,届时LLDPE将占全球LDPE/LLDPE市场的53%。
在进入新世纪之际,对于一个公司的生存发展来说,竞争形势是严峻的,因此,在战略规划中应把技术置于重要的位置。
大的公司都十分重视开发新产品,以增加营业收入;重视出售许可证,增加效益;重视建设生产能力较大的装置,以获取较低的固定成本,提高边界效益及市场占有率;重视形成技术的联合和合作,以更有利地使新技术新产品实现工业化。
国外聚乙烯的生产技术
聚乙烯是通用合成树脂中产量仅次于聚丙烯的品种,主要包括低密度聚乙烯(LDPE)、线性低密度聚乙烯(LLDPE)、高密度聚乙烯(HDPE)及一些具有特殊性能的产品。
其特点是价格便宜、性能较好可广泛应用于工农业、包装及日常生活中,在塑料工业中占有举足轻重的地位。
2001年全球前十位聚乙烯生产商的生产能力分别为:
①陶氏(Dow)化学公司737万t/a;②埃克森美孚(Exxon-Mobil)公司611万t/a;③埃奎斯塔尔(Equistar)化学公司319公司万t/a;④Basell公司274万t/a;⑤雪佛龙-菲利浦斯(Chevron-Phillips)公司262万t/a;⑥萨比克公司243万t/a;⑦波力阿利斯公司(Borealis)202万t/a;⑧BP公司173万t/a;⑨诺瓦(Nova)化学公司170万t/a;⑩阿托-菲纳(Tota-Fina)公司160万t/a。
一 典型工艺技术的介绍
高压法生产LDPE是PE树脂生产中技术最成熟的方法,釜式法和管式法工艺己成熟,目前这两种生产工艺并存。
发达国家普遍采用管式法生产工艺。
国外各公司普遍采用低温高活性催化剂引发体系,降低反应温度和压力。
高压法生产LDPE将向大型化、管式化方向发展。
低压法生产HDPE和LLDPE主要采用钛系和铬系催化剂,欧洲和日本多采用齐格勒型催化剂,而美国多采用铬系催化剂。
典型的乙烯生产工艺有以下几种:
1 Basell公司气相法Spherilene工艺
该法生产的线性PE可以从很低密度PE(VLDPE)到LLDPE,也可生产HDPE。
采用齐格勒-纳塔(Z-N)钛基催化剂和Spherilene的气相法工艺,在惰性轻烃存在下,催化剂和进料预聚合。
浆液进入第一台气相反应器(GPR),采用循环气体回路冷却器取热,再进入第二台GPR。
产品密度从VLDPE(<900g/ml=到HDPE(>960g/ml),熔融指数(MI)0.01~100。
因采用两台GPR,故可生产双峰级和特种聚合物。
该Spherilene工艺1992年推向市场以来,己拥有生产能力180万t/a。
6套装置(美国1套、韩国2套、巴西2套、印度1度)己投入运转。
另有2套(1套在印度、1套在伊朗)在建设中,单线生产能力可从10万~30万t/a。
2 .北欧化工公司回路反应器的北星工艺
北星(BarVstar)PE工艺可生产双峰和单峰LLDPE、MDPE以及HDPE,采用串联的回路、气相低压法反应器。
PE密度为918~970kg/m3,熔融指数为0.1~100,现采用Z-N催化剂,也可采用单活性中心(SSC)催化剂。
催化剂与丙烷稀释剂混合进入紧凑的预聚合反应器,共聚催化剂、乙烯、共聚单体和氢气也进入反应器。
预聚合的浆液再进入第二较大的浆液回路反应器,在超临界条件:
75~100℃、5.5~6.5MPa下操作。
经闪蒸后的聚合物进一步送入流化床气相反应器,无需加入新鲜催化剂,可得到均聚物。
气相反应器操作条件为75~100℃、2.0MPa。
第一套工业化装置于1995年在芬兰投运。
在阿布扎比建设的两条生产线己于2001年下半年投运,产能45万t/a,第五套25万t/a装置也在上海石化公司建设,现己成为中国最大的PE装置。
该工艺单线最大的设计能力达30万t/a。
3 BP公司气相法Innovene工艺
该工艺采用Z-N,铬和茂金属催化剂生产LLDPE和HDPE。
铬催化剂可生产宽分子量产品,Z-N催化剂生产窄分子量分布的产品。
床层反应器操作条件约为2.0MPa和75~110℃,可用丁烯或己烯为共聚单体。
己有30套生产线投入运转、设计或建设中,能力范围为5万~35万t/a。
4 Exxon-Mobil公司管式和釜式反应工艺
高压自由基工艺可生产LDPE均聚物和乙烯-醋酸乙烯共聚物(EVA)。
有大规模管式反应器(能力范围13~35万t/a)和搅拌釜式反应器(能力为10万t/a)。
管式反应器操作压力高达300MPa,釜式反应器低于200MPa。
高压工艺的主要优点是短停留时间,生产中可以从均聚物切换到共聚物。
均聚物密度为0.912~0.935,熔融指数0.2~150。
醋酸乙烯产量高达30%。
生产每吨聚合物的物耗、能耗为:
乙烯1.008t,电力800kWh,蒸汽0.35t,氮气5Nm3。
己有23套高压法反应器投运,产能为170万t/a。
生产均聚物和各种共聚物。
5 三井化学公司低压浆液法CX工艺
低压浆液法CX工艺可生产HDPE和MDPE及双峰分子量分布的产品。
乙烯、氢气、共聚单体和超高活性催化剂进入反应器,在浆液状态下发生聚合反应。
聚合物性质自动控制系统可有效地控制产品质量。
超高活性催化剂无需处理就可直接循环到反应器。
可生产窄或宽分子量分布的产品,熔融指数0.01~>50,密度0.93~0.97。
每吨产品的公用工程消耗为:
乙烯和共聚单体1010kg,电力3~5kWh,蒸汽340kg,冷却水190t,氮气30Nm3。
己有35条生产线在运行或建设中,总能力为360万t/a。
6 Phillips-Chevren公司双回路反应器LPE工艺
菲利浦斯公司LPE工艺可生产密度0.920~0.970、窄和宽分子量分布的线性聚乙烯产品。
熔融指数和分子量分布可由催化剂、操作条件和氮气来调节控制。
共聚单体可为丁烯-1、己烯-1、辛烯-1等。
高活性催化剂无需从产品中脱除。
聚合时无石蜡烃或其他产物形成,大大减少了对环境的逸散性污染。
乙烯、异丁烷、共聚单体和催化剂连续赶进入回路反应器。
在低于100℃和约4.0MPa下发生反应,停留时间约1小时。
乙烯单程转化率超过97%。
每吨产品的原料和公用工程消耗为:
乙烯1.007t,催化剂和化学品(不同产品)为2~10美元,电力350kWh,蒸汽0.25t,冷却水185t,氮气30Nm3。
己有82条生产线运转和在建,占世界PE能力的34%。
7 Univation技术公司低压气相法Unipol工艺
采用低压气相法UnipolPE工艺生产LLDPE-HDPE。
使用浆液催化剂和气相流化床反应器。
产品无需脱除催化剂。
投资和操作费用较低,对环境污染较少。
乙烯、共聚单体和催化剂进入流化床反应器,操作条件为2.5MPa和约100℃。
聚合物密度为0.915~0.970。
根据催化剂类型,可调节窄或宽分子量分布。
产品熔融指数为<0.1~>200。
己有89条生产线投入运转或设计建设阶段。
8 斯塔米卡本公司COMPACTSolution工艺
该工艺采用先进的Z-N催化剂,生产密度为0.900~0.970的PE。
采用搅拌釜式反应器。
聚合温度200℃。
氢气用于控制聚合物分子量,无需脱除催化剂。
每吨产品的原料和公用工程消耗为:
乙烯和共聚单体1.016t,电力500kWh,冷却水230m3,低压蒸汽(产出)330kg。
己有5套装置投运,总能力65万t/a。
9 Basell聚烯烃公司Hostalen工艺
利用搅拌釜的Hostalen工艺生产HDPE。
采用并联或串联的两联的两台反应器进行浆液聚合。
生产每吨HDPE的物耗和能耗为:
乙烯和共聚单体1015kg,蒸汽400kg,电力350kWh,冷却水165m3。
己有23条生产线处于运转或设计中,生产能力近290万t/a。
10 埃尼化学公司高压法工艺
采用高压法釜式或管式工艺生产LDPE和EVA。
LDPE密度为0.918~0.935。
EVA中VAM(醋酸乙烯单体)含量3%~40%。
己有24条生产线投运转或建设中,单线能力可达20万t/a。
11 斯塔米卡高压法工艺
采用高压法管式反应器生产LDPE和EVA共聚体。
每吨产品的物耗和能耗为:
乙烯1.005t,电力800kWh,高压蒸汽230kg,冷却水120m3,低压蒸汽(产出)650kg。
DSM公司己有三条生产线投运,单线能力22万t/a。
己有多套单线能力15万30万t/a装置投入运转,总能力超过180万t/a。
二 新技术的进展
近几年来,一些新技术先后实现了工业化,其中包括茂金属、非茂金属单中心催化的工艺和基于Zigler-Nata催化剂的易加工LLDPE(如双峰树脂、宽分子量分布的三元共聚物和四元共聚物)。
在大多数情况下,掌握技术的公司为许可证领用者提供工艺和催化剂技术,提交运转,或建设大型的多功能装置。
新技术的发展提高了产品的性能,或降低了制造成本,成为聚烯烃工业中最重大的变化。
各种技术的发展已经实现了聚合物性能的改进,影响到了聚合物之间和聚合物内部的竞争。
这些变化主要包括:
l催化剂系统:
自由基型、常用的Zerggle-Nata型、改进的Zerggle-Nata型、茂金属单中心和非茂金属单中心
l共催化剂:
常用的烷基铝、甲基铝氧烷(MAO)、带非配位阴离子的弱路易士碱和羰基硼
l共聚单体:
丁烯-1、己烯-1、辛烯-1其它,混合型和极性型的
l硬件:
单反应器或多反应器
l聚合介质:
气相、本体、溶液、淤浆和杂化的
其中每一种都影响聚合物的分子结构。
这包括影响结晶度的支链度、共聚单体分布、密度、分子量、分子量分布,各自都确定聚合物的最终性能,包括机械强度、光学性能、纯度、流变行为(可加工性)、稳定性(对热、紫外线)热稳定性能和电性能等。
工艺和催化剂的优化组合使树脂的性能得到平衡,但需考虑聚合物最终的成本(投资和生产)。
一般来说,聚合物强度的提高会导致加工的困难,而过去易加工的双峰树脂又导致透明度的降低。
这些性能的协调平衡是聚合物生产商面对的主要挑战这一。
化学系统公司把在催化剂和工艺技术的革命进步称为“第二代”树脂。
其中最突出的就是采用茂金属或非茂金属单中心催化剂生产。
这种催化剂已经进行了大量的研究开发。
另一类第二代树脂是“更易加工”的LLDPE树脂。
也就是说,这些LLDPE聚合物挤出加工性能接近LDPE,同时具有优异的机械性能。
这意味着,如果该LLDPE可以以富LLDPE或100%的状况在现有的LDPE吹膜设备加工的话,这些LLDPE树脂可以代替高LDPE比的掺混物在一些最终市场中传统应用。
“设计”LLDPE聚合物链改进加工性能的方法有三种基本途径:
造就双峰结构;造就宽分子量分布结构;以及导入第三(或第四)种共聚单体,造就三元共聚物(或四元共聚物)。
直至目前,这些“设计”主要是通过使用非茂金属/单中心催化体系进行的。
最引人注目的聚乙烯工艺有:
Montell公司的Spherilene(三元共聚物)工艺;Phillips公司的LDLPE(宽分子量分布);Univation公司的Unipol-Ⅱ(双峰)工艺以及最近Boreakis公司的Borstar(双峰)工艺和Nova化学公司先进的Sclairtech(双峰)工艺。
对茂金属/单中心催化剂体系的大量开发,己工业化生产出更易加工的LLDPE。
这些新技术包括Dow公司的长支链(LCB)Insite工艺;三井的Evolue(双峰)工艺和Phillips的mPACT工艺。
开发易加工LLDPE由不同的技术路线组成(如双反应器用或不用单中心催化剂、单反应器用单中心催化剂.)。
其它有革命性发展的还有Dupont公司的镍-钯和BP/Amoco公司的铁-钴催化剂体系,这尚处于开发阶段。
为了让加工商接受这些新的树脂,必须使他们了解在价值-应用方面相对于现有平衡的改进。
不同创新开发均旨在增强企业的竞争地位,或降低成本,或用现有的技术市场生产新的树脂。
其包括:
l在气相法装置中采用“凝聚态”操作法,改进反应器的生产率(时空产率)。
l在气相法装置中生产辛烯-1基树脂。
l在聚乙烯聚合系统就地生产共聚单体,降低原料成本。
Phillips实践了有限数量的MDPE牌号的生产。
1 茂金属及单中心基聚乙烯
二十世纪七十年代以来,传统工艺的研究向新的一类催化剂体系延伸,这就是茂金属和单中心催化剂。
这些催化剂在结构上可以通过分子设计由α-烯烃制成无规的、等规的或间规的聚合物。
茂金属催化剂的成功,最终取决于与被加工的最终产品有关的树脂的价格性能比。
要提高性能,除了定制聚合物分子结构以外,生产商正在优化工艺和催化剂,以降低树脂生产的总成本。
溶液法LLDPE和气相法LLDPE,以及高压法LDPE釜式法、环管淤浆法HDPE等系统,均己开发出工业上可用的茂基产品。
随着茂/单中心催化剂的大规模生产(如Dow、Exxon/Mobil、Mitsui、Phillips等),这些体系比常用的Z-N催化剂竞争性更强。
茂金属催化剂目前主要通过装置改造实现工业化,特别是气相法和淤浆法。
这些单中心/茂基装置将是交替生产的,也就是说,装置仍然可以生产传统的产品牌号。
用茂金属催化剂运转进,必须考虑的关键工艺领域是:
单体的净化;催化剂进料系统;聚合系统等等。
在气相法工艺中,茂金属催化剂允许加入不同量的共聚单体和氢。
因此,一些操作情况会发生改变,包括:
循环气组成(有更大的自由度)、生产速率的差别、树脂洗提的要求、牌号转换、树脂的粘着性以及添加剂用量。
用强化和超冷凝态操作可以获得高聚合速率,其中部分液体返回反应器。
事实上,停留时间可以从3~5h降低到1~2h。
加之,用茂金属催化剂体系,气相反应器可以在较高的温度下操作,进一步提高产量。
在溶液工艺中,使用高级α-烯烃共聚单体和单中心催化剂与使用Z-N催化剂之间的不同,主要是反应器的温度和聚合物在溶剂中的浓度不同。
用于后反应器温度控制的附加热交换器和脱挥发物步骤,是茂金属催化剂体系所要求的,其在较低的温度下操作。
在淤浆法工艺中,由Z-N系转为茂金属催化剂系,实际上不要求工艺的改进。
2 易加工的LLDPE工艺
在低压工艺中生产双峰和宽分子量分布的LLDPE共聚物和三聚物,可以得到加工性能类似于传统高压LDPE的树脂。
一般来说,LDPE有较强的支链结构,其中长支链占优势,而LLDPE只有短支链,它们的数目决定聚合物的结晶度和密度。
改进加工性能将有利于LLDPE向LDPE应用渗透的能力,进入那些由于性能差别(如透明度、熔体强度等)先前未涉及的领域。
这也影响到LLDPE/LDPE挤出掺混的比例。
具有高分子量树脂性能特征(韧性、强度等),又具有LDPE的可加工性能,这就是LLDPE树脂的最终目标。
有多峰MWD的聚乙烯,通过挤出、模塑、热成型、旋转成型等方法制成的产品,性能优于缺乏多峰MWD的一般聚乙烯。
有多峰MWD的聚乙烯比较容易加工,同时因其熔体流动指数显著降低,改善了产品如高强度膜的性能。
各家公司通过不同的途径改进了LLDPE的加工性能,包括茂基和常用的Z-N基树脂。
它们包括:
采用长支链聚合物;插入第三单体形成三元共聚物;控制分子量分布以形成双峰和宽分子量分布的聚合物;加入加工助剂以提高熔体的润滑性,等等。
几乎所有研究聚乙烯的公司都有生产双峰聚合物的。
不同的公司采用不同的方法,如用两台串联的反应器,分别生产高分子量和低分子量的聚乙烯;或在一个反应器中用两种不同的茂金属催化剂、混合的茂金属-Z-N催化剂、或用混合的铬-过渡金属(如钛)催化剂;或用负载型茂金属催化剂,得到宽的分子量分布。
虽然单反应器系统从投资和操作成本考虑是较理想的,但目前两个串联反应器的应用,能最佳地控制分子量和分子量分布,并提供最大的加工易性。
a)Borealis工艺(BORSTAR)
BORSTAR工艺第一套工业装置1995年在芬兰的Pouvoo开始运转,生产能力为265kt/a。
1999年末脱除瓶颈达到353kt/a。
Borealis公司指出如果没有原料、挤出机和固体物料处理系统的限制,Pouvoo装置的生产能力可达440kt/a。
该工艺的目的是在一种工艺中能够生产全密度的聚乙烯树脂(LLDPE、MDPE及HDPE),得到的树脂具有良好的加工性能和机械性能(刚性和耐撕裂强度)。
Borealis公司采用BOSRSTAR工艺,改造其在瑞典Stenungsund 的UNIPOL气相法装置,包括增加一环管前端。
该装置于2000年9月开车,生产能力为225kt/a。
此外,Borealis公司与阿联酋的阿布扎比国家石油公司合资的Borouge公司建有一套22kt/a的生产装置,于2001年11月开车。
Borealis最近的许可证领有者是上海石化公司在上海金山的250kt/a装置,该装置也于2002年初开始运转。
BORSTAR工艺基于两个串联的反应器,生产出双峰树脂。
伴随着双峰技术的开发,进一步强化了丙烷超临界状态的应用。
b)BPAmoco/Dow(INNOVENE/INSITE)工艺
1996年BP公司和Dow公司宣布合作,将BP的气相法INNOVENE工艺和Dow公司的INSITE催化剂技术结合起来。
两家公司通过一项联合开发合同,以产品和技术进行开发,并提供其许可证。
主要产品一为高性能的线型低密度(HPLL)吹塑和流延膜,目标瞄准具有优异的机械性能和光学性能的HAO-LLDPE和茂基树脂;另一为“貌似”LDPE的膜料树脂。
后者加工性能好,膜泡稳定,其机械性能和热封性能与LDPE相似。
c)三井化学工艺(EVILUE)
三井化学公司开发了用茂金属催化剂生产LLDPE的气相法工艺。
三井开发EVOLUE工艺的目的是生产具有良好加工性能、优异机械性能(冲击性能及撕裂性能)以及良好光学性能的LLDPE。
该公司也采用两个气相流化床反应器。
除了可生产双峰树脂外,也可生产通用树脂、低熔体流动指数(较高分子量)树脂和高流动性(低熔本流动指数)树脂。
采用己烯-1作共聚单体,生产的树脂密度为0.900~0.935g/cm3、熔体流动指数在0.7~4.0g/10min、EVOLUE工艺可以生产单峰的LLDPE,用在加工性要求不严格的场合。
EVOLUE工艺也可以用来生产非茂基牌号(用Z-N催化剂),但不出售技术,其产品开发集中在自己的聚乙烯装置中。
d)Montell工艺(SPHERILENE)
1999年,Montell与Elenac(Shell和BASF的合资公司)合资合作开展研究、开发,转让两家公司聚乙烯技术的许可证(Montell的SPHERILENE工艺和Elenac的LUPOTECH G工艺)。
Montell主要用它的SPHERILPOL(PP)和CATALLOY技术开发SPHERILENE工艺,基于Montell在聚烯烃工艺的理论和经验,SPHERILENE工艺仅用了五年就实现了工业化。
第一套100kt/a规模的装置于1994年在韩国的大林公司开车。
巴西的OPP公司于1999年建成的260kt/a装置是目前能力最大的生产线。
Montell公司可提供最大的单线能力是350kt/a。
SPHERILENE工艺采用单催化剂家族生产全范围的LLDPE/HDPE(窄MWD和中MWD)产品;采用预聚合技术以控制粒子的形态;用反应器造粒技术,与多元的的共聚单体结合,生产高度一致的产品;以高STY运转而不使用冷凝方式。
e)NOVA化学工艺(先进的SCLALRTECH)
近年来,NOVA化学公司先进的SCLALRTECH(AST)聚乙烯溶液法工艺实现了工业化,向全世界颁发了这项技术的许可证。
AST基于新的高强度的混合、低停留时间(2min)、多反应器系统及先进的、高活性的Z-N催化剂简化工艺流程。
AST工艺可以生产ULDPE到HDPE(0.950~0.965g/cm3)全密度范围的产品。
熔体流动指数在0.2~150