马铃薯淀粉生产精编版.docx
《马铃薯淀粉生产精编版.docx》由会员分享,可在线阅读,更多相关《马铃薯淀粉生产精编版.docx(12页珍藏版)》请在冰豆网上搜索。
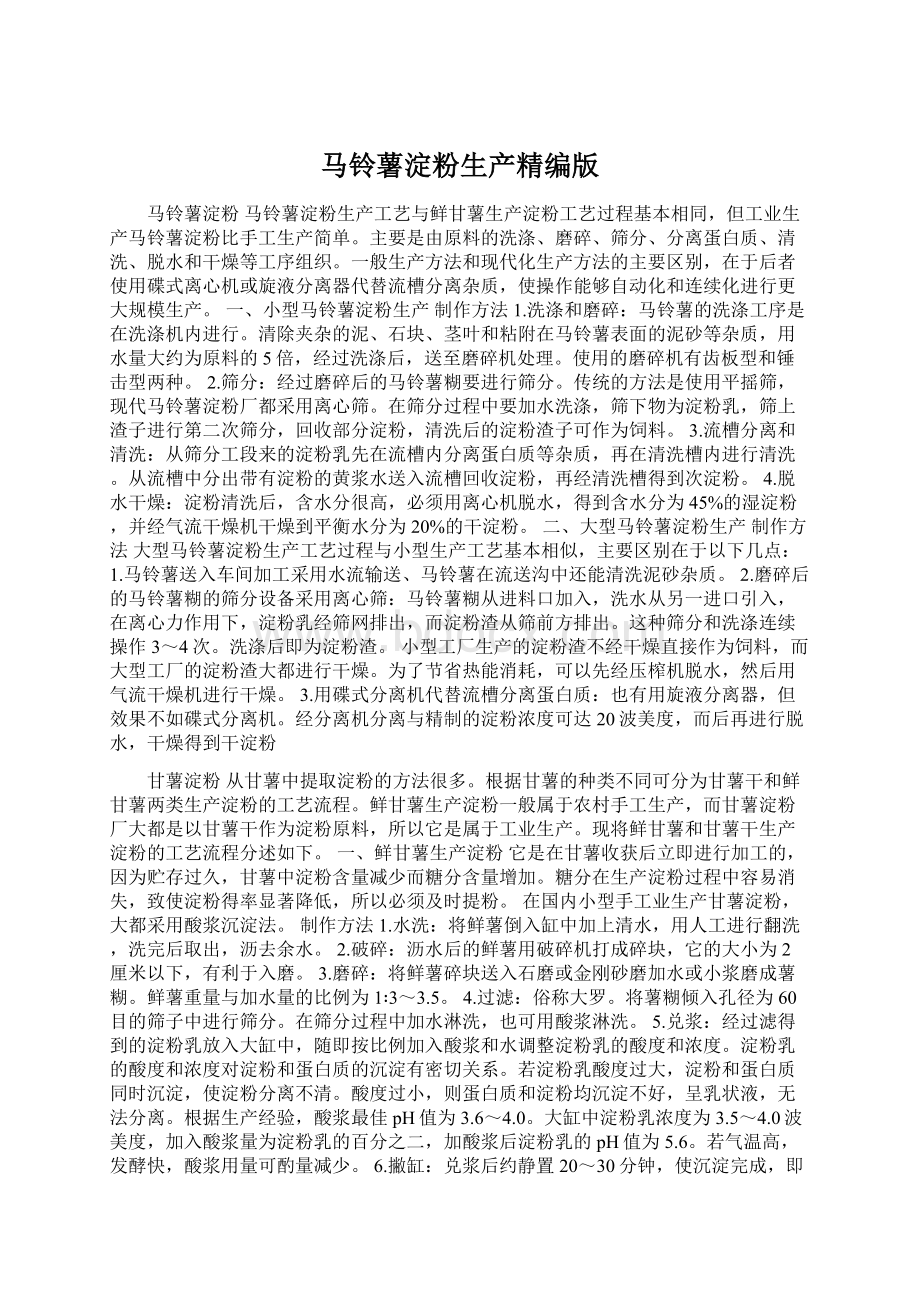
马铃薯淀粉生产精编版
马铃薯淀粉马铃薯淀粉生产工艺与鲜甘薯生产淀粉工艺过程基本相同,但工业生产马铃薯淀粉比手工生产简单。
主要是由原料的洗涤、磨碎、筛分、分离蛋白质、清洗、脱水和干燥等工序组织。
一般生产方法和现代化生产方法的主要区别,在于后者使用碟式离心机或旋液分离器代替流槽分离杂质,使操作能够自动化和连续化进行更大规模生产。
一、小型马铃薯淀粉生产制作方法1.洗涤和磨碎:
马铃薯的洗涤工序是在洗涤机内进行。
清除夹杂的泥、石块、茎叶和粘附在马铃薯表面的泥砂等杂质,用水量大约为原料的5倍,经过洗涤后,送至磨碎机处理。
使用的磨碎机有齿板型和锤击型两种。
2.筛分:
经过磨碎后的马铃薯糊要进行筛分。
传统的方法是使用平摇筛,现代马铃薯淀粉厂都采用离心筛。
在筛分过程中要加水洗涤,筛下物为淀粉乳,筛上渣子进行第二次筛分,回收部分淀粉,清洗后的淀粉渣子可作为饲料。
3.流槽分离和清洗:
从筛分工段来的淀粉乳先在流槽内分离蛋白质等杂质,再在清洗槽内进行清洗。
从流槽中分出带有淀粉的黄浆水送入流槽回收淀粉,再经清洗槽得到次淀粉。
4.脱水干燥:
淀粉清洗后,含水分很高,必须用离心机脱水,得到含水分为45%的湿淀粉,并经气流干燥机干燥到平衡水分为20%的干淀粉。
二、大型马铃薯淀粉生产制作方法大型马铃薯淀粉生产工艺过程与小型生产工艺基本相似,主要区别在于以下几点:
1.马铃薯送入车间加工采用水流输送、马铃薯在流送沟中还能清洗泥砂杂质。
2.磨碎后的马铃薯糊的筛分设备采用离心筛:
马铃薯糊从进料口加入,洗水从另一进口引入,在离心力作用下,淀粉乳经筛网排出,而淀粉渣从筛前方排出。
这种筛分和洗涤连续操作3~4次。
洗涤后即为淀粉渣。
小型工厂生产的淀粉渣不经干燥直接作为饲料,而大型工厂的淀粉渣大都进行干燥。
为了节省热能消耗,可以先经压榨机脱水,然后用气流干燥机进行干燥。
3.用碟式分离机代替流槽分离蛋白质:
也有用旋液分离器,但效果不如碟式分离机。
经分离机分离与精制的淀粉浓度可达20波美度,而后再进行脱水,干燥得到干淀粉
甘薯淀粉从甘薯中提取淀粉的方法很多。
根据甘薯的种类不同可分为甘薯干和鲜甘薯两类生产淀粉的工艺流程。
鲜甘薯生产淀粉一般属于农村手工生产,而甘薯淀粉厂大都是以甘薯干作为淀粉原料,所以它是属于工业生产。
现将鲜甘薯和甘薯干生产淀粉的工艺流程分述如下。
一、鲜甘薯生产淀粉它是在甘薯收获后立即进行加工的,因为贮存过久,甘薯中淀粉含量减少而糖分含量增加。
糖分在生产淀粉过程中容易消失,致使淀粉得率显著降低,所以必须及时提粉。
在国内小型手工业生产甘薯淀粉,大都采用酸浆沉淀法。
制作方法1.水洗:
将鲜薯倒入缸中加上清水,用人工进行翻洗,洗完后取出,沥去余水。
2.破碎:
沥水后的鲜薯用破碎机打成碎块,它的大小为2厘米以下,有利于入磨。
3.磨碎:
将鲜薯碎块送入石磨或金刚砂磨加水或小浆磨成薯糊。
鲜薯重量与加水量的比例为1∶3~3.5。
4.过滤:
俗称大罗。
将薯糊倾入孔径为60目的筛子中进行筛分。
在筛分过程中加水淋洗,也可用酸浆淋洗。
5.兑浆:
经过滤得到的淀粉乳放入大缸中,随即按比例加入酸浆和水调整淀粉乳的酸度和浓度。
淀粉乳的酸度和浓度对淀粉和蛋白质的沉淀有密切关系。
若淀粉乳酸度过大,淀粉和蛋白质同时沉淀,使淀粉分离不清。
酸度过小,则蛋白质和淀粉均沉淀不好,呈乳状液,无法分离。
根据生产经验,酸浆最佳pH值为3.6~4.0。
大缸中淀粉乳浓度为3.5~4.0波美度,加入酸浆量为淀粉乳的百分之二,加酸浆后淀粉乳的pH值为5.6。
若气温高,发酵快,酸浆用量可酌量减少。
6.撇缸:
兑浆后约静置20~30分钟,使沉淀完成,即可进行撇缸。
将上层清泔水及蛋白质、纤维和少量淀粉的混合液(俗称毛粉)取出,留在底层的为淀粉。
毛粉必须舀出过滤,回收淀粉,并入大缸,滤渣可作为饲料。
7.坐缸:
在撇缸后的底层淀粉中加水混合,调成淀粉乳,使淀粉再沉淀。
在沉淀过程中,起酸浆发酵作用,故称坐缸。
坐缸时应控制温度和时间。
坐缸温度为20℃左右。
在天冷时必须保温或在加水混合时可用热水。
坐缸发酵必须发透,在发酵过程中适当地搅拌,促使发酵完成。
一般坐缸时间为24小时,天热可相应缩短一些时间。
发酵完毕,淀粉沉淀。
8.撇浆:
坐缸所生成的酸浆称为二和浆,即酸浆法中主要使用的酸浆。
发酵正常的酸浆有清香味。
浆色洁白如牛奶。
若发酵不足或发酵过头的酸浆,色泽和香味均差,供兑浆用时效果不好。
撇浆即是将上层酸浆撇出作为兑浆之用。
9.过滤:
撇浆后的淀粉用筛孔为120目的细筛进行筛分。
筛上物为细渣,可作饲料。
筛下物为淀粉,转入小缸。
10.小缸:
淀粉转入小缸后,加水漂洗淀粉,约需放置24小时,防止出现发酵现象。
11.起粉:
淀粉在小缸中沉淀后,上层液体为小浆,可与酸浆配合使用,或作为磨碎用水。
撇去小浆后,在淀粉表面留有一层灰白色的油粉,系含有蛋白质的不纯淀粉。
油粉可用水从淀粉表面洗去,洗出液可作为培养酸浆的营养物料,底层淀粉用铲子取出,淀粉底部可能有细砂粘附,应将其刷去。
12.吊包:
淀粉铲出放入方布中,方布四角用绳扎牢,挂起后,淀粉内的水分自行滴下沥干。
为了缩短吊包时间,可适当振动包布,加速漏水。
13.干燥:
从包布中取出的湿淀粉约含有40~45%的水分。
也可作成品。
为了便于贮藏和运输必须进行干净。
一般采用日光晒干或送入烘房烘干。
二、甘薯干生产淀粉鲜甘薯收获后,通常将它切成片状或丝状,经过日晒或火力干燥后,制成甘薯干。
这种甘薯干在加工和运输过程中不可避免混入各种杂质。
制作方法1.预处理:
送到甘薯淀粉车间加工的甘薯干夹带各种杂质,所以必须经过预处理。
预处理有干法和湿法两种。
干法是采用筛选设备和风选设备。
湿法处理是用洗涤机或洗涤桶。
在进行粉碎以前,最好经过磁选设备,清除金属杂质,保证安全生产。
2.浸泡:
为了提高淀粉出率可以采用碱水浸泡。
碱水浸泡的作用是:
(1)甘薯片的纤维膨胀增大,使甘薯片在破碎时纤维和淀粉容易分离,而淀粉颗粒破碎较少。
(2)使色素和胶体物质容易渗出。
过筛时,减少渣子粘附筛孔。
(3)保持碱性,抑制微生物活动。
(4)淀粉乳在流槽分离时,沉积淀粉的性能良好,粉质硬。
浸泡一般采用饱和石灰乳或1%稀碱液加入渍泡水,使pH值为10~11;浸泡时间约12小时;温度控制在35~40℃。
渍泡后,甘薯片含水量为60%。
3.破碎和磨碎:
浸泡后的甘薯片随水进入锤片式粉碎机进行破碎,达到一定的细度,穿过筛孔排出机外。
若粉碎机转速超过3,200转/分时,锤片易损,动平衡性能差,运转不稳定;薯干在粉碎过程中瞬时温度升高,部分淀粉易受热糊化,以致在过筛时,影响淀粉和薯渣的分离;在流槽分离时又不易沉淀,导致次数增加,影响好粉出率。
为了防止一次粉碎处理易使淀粉糊化,可以采用两道粉碎,分道过筛的工艺流程。
即薯干经第一道粉碎后,进行过筛,然后经第二道粉碎处理,再行过筛。
在粉碎过程中,为了降低瞬时温升,根据各道粉碎粒度不同,调整粉浆浓度,头道为3~3.5波美度,二道为2~2.5波美度。
同时采用匀料器控制甘薯干的进量,均衡粉浆,避免粉碎机的过载现象,也利于流槽分离。
为了提高渣子的粉碎效率,一般采用磨碎处理,对降低料液温升,减少渣子含粉量,提高淀粉出率和节省维修费用具有一定的效果。
4.过筛:
甘薯干经过粉碎后得到的甘薯糊又称料液,必须进行过筛,分离出渣子,即纤维。
通常采用平摇筛,料液进入筛面,要求均匀过筛,不断淋水,淀粉随水穿过筛孔进入存浆池,而渣子留存在筛面上从筛尾排出。
筛孔大小应根据料液内物料的粒度决定。
对于采用两道粉碎工艺的过筛设备的筛孔配备是:
一二道筛均采用80目尼龙布,二道筛得粉浆合并后用120目尼龙布精筛。
其目的是进一步分离细小渣子,提高纤维分离效率。
由于二次粉碎的粒度和过筛要求不同,二道筛理面积要注意适当地配备,合理分担。
在过筛过程中,由于料液中含有果胶等粘稠物质滞留在筛面上,影响筛子的分离效果。
因此,筛布应经常洗刷,保证筛孔畅通。
5.流槽分离:
经过精筛处理后的淀粉,目前一般采用流槽分离蛋白质。
它的优点是建造容易,少用钢材,节省动能,操作也较稳定。
缺点是占地大,间歇操作,分离效率低,淀粉损失大,劳动条件差。
6.碱、酸处理和清洗:
为了进一步提高淀粉纯度,在清洗淀粉过程中,还要经过碱、酸处理。
淀粉碱、酸处理和清洗都是在带有搅拌装置的水泥池内进行。
水泥池的大小根据生产能力确定,搅拌器转速为60转/分左右。
电流槽来的淀粉乳,先经碱处理,目的是清除淀粉中碱溶蛋白质和果胶等杂质。
碱处理的方法是将1波美度的稀碱液,缓慢地加入淀粉乳内,控制pH值为12,同时启动搅拌器,充分混合均匀,经半小时后,停止搅拌,待淀粉完全沉淀后,排出上层废液,并注入清水清洗二次,使它接近中性即可。
在碱处理过程中,还可加入浓度为35波美度的次氯酸钠溶液,用量不超过干基淀粉重量的0.4%。
因为次氯酸钠是一种强氧化剂,具有较强的漂白和杀菌作用,以致能达到增白和防腐的目的。
经过碱、次氯酸钠处理和清洗后的淀粉再经酸处理。
其目的是溶解酸溶蛋白,中和碱处理时残留的碱性,还可抑制微生物的活动和繁殖。
酸处理可用工业盐酸,操作时也必须缓缓地加入,充分搅拌,控制淀粉乳的pH值为3左右。
防止局部过酸,造成淀粉损失。
加酸后的淀粉乳用碱处理的同样操作方法使淀粉沉淀,除去上层废液,加水清洗,最后使淀粉呈微酸性,即pH6左右。
以利于淀粉的贮存和运输。
7.离心分离和干燥:
清洗后得到的淀粉含水分很高,必须先经离心分离机脱水处理,使淀粉水分含量下降到45%以下。
有些工厂直接作为湿淀粉出厂或使用。
为了有利于贮藏和运输,脱水后的湿淀粉最好进行干燥,达到需要的淀粉含水量。
通常甘薯淀粉的水分为12~13%。
淀粉干燥可采用气流干燥。
因为它具有干燥速度快、效率高、设备生产能力大和设备造价较低等优点。
甘薯淀粉质量指标项目产品精淀粉粗淀粉色泽pH12的碱性溶液中水清透正常纯粉含量97%90%杂质无黄斑、夹花及不该有的杂质同左pH66蛋白质0.2%以下——灰分0.4%以下——水分符合使用要求同左
马铃薯制试剂用淀粉利用马铃薯,可制得试剂用淀粉,成本低,经济效益高。
制作方法1.洗涤及制薯浆:
用水将马铃薯洗2~3遍,除尽全部泥砂,并将有锄伤、烂洞的薯块削除。
开动粉碎机,投入洗净的薯块,立即流出薯浆。
因鲜马铃薯本身约含75%的水分,故打浆时不须外加水。
2.滤粉及淀粉漂洗:
用机器或人工将薯浆过滤,淀粉乳(含淀粉的水)贮于池内澄清。
待池内淀粉沉底后,放去上层水,取出粉块,放在陶土缸中,加清水搅拌。
淀粉澄清后,倾去上层液体,刮除黄粉,再加清水搅拌,用100~140目的筛除去杂质。
反复加清水漂洗,至上层水清亮为止。
3.淀粉水解:
水解之前,将清水放入水解池,接通电源,将水加热到40~50℃,再放入洗净的陶土缸中,按配料表将酸、水、湿淀粉计量投入缸内进行水解。
水解过程随时搅拌,经化验合格后出缸。
4.洗酸:
将水解合格的淀粉乳用塑料盆取出,倒入预先加有半缸清水的陶土缸中,再将缸加满清水,使料液温度迅速降低,防止转化为糊精。
淀粉澄底后,倾去上层酸液,加清水反复漂洗至中性(用pH试纸控制)。
过100~140目筛除去杂质。
用蒸馏水洗至氯化物含量合格(约2~3遍)。
5.烘干磨细:
漂洗合格后,倾去上层清液,取出粉块捣碎,放在铺有白布的板上,进烘干室干燥。
烘烤初期,温度控制在40~50℃,待大部分水烘除后,可逐步升高温度。
烘干过程中随时翻动捣碎,约20小时后取出。
用磨粉机磨碎,筛除杂质,再烘烤数小时,至装入干燥玻璃瓶中抖动时无粘结感,取出冷却,取样化验。
6.包装:
磨细复烘的产品,用预先洗净的650~750毫升棕色螺口玻璃瓶分装,每瓶装500克。
盖上塑料内外盖,瓶口套封口。
化验合格后贴上相应等级的瓶签,装入特制纸箱,每箱10瓶
木薯淀粉木薯淀粉生产过程与甘薯淀粉生产过程基本相同。
制作方法1.木薯制造淀粉,第一道工序是洗涤,清除块根上附着的泥沙杂质,然后剥去块根的外皮,最好能脱掉内皮。
木薯块根内皮厚约2~3毫米,木薯含有的氰化物量绝大部分存在于皮层。
所以去皮能除去氰化物,防止淀粉着色,保证淀粉质量。
2.木薯去皮后,可送入锯齿式圆辊磨碎机或锤碎机进行磨碎。
为了使木薯块根得到充分磨碎,可以经过二道磨碎处理。
在磨碎过程中,不断加水,引入离心筛或平摇筛分离渣子,并用流槽分离蛋白质和水溶性杂质,得到粗制淀粉。
3.为了更好地清除各种杂质,提高淀粉纯度,经过流槽处理后的淀粉乳加入0.3%氢氧化钙溶液处理,并洗净,或在粗制淀粉中加入各种酸和盐类等化学药品,以便得到精制淀粉。
常用的化学药品1.硫酸:
每升2%的淀粉乳中,加入比重1.84的浓硫酸0.001毫升,可促进淀粉沉淀,但使淀粉粘度略有降低,应当加以注意。
2.硫酸铝:
每升2%的淀粉乳中加0.1克,能改善淀粉的沉降性,淀粉粘度约可增加5%。
3.亚硫酸:
淀粉乳中亚硫酸浓度达0.3%,使蛋白质易于分离,并且可以防止发酵,兼有漂白作用。
长期作用的情况下,亦可使淀粉粘度降低,所以待淀粉沉淀后,必须及时进行清洗。
4.氯:
单独的氯或它的钙盐以及亚氯酸盐均可使用。
每升淀粉乳中加氯1毫克,能改善淀粉的沉降性,防止发酵,也兼有漂白效果。
但氯的添加量不宜太多,否则会使淀粉沉淀变软,而且粘度下降。
淀粉乳经过碱或酸处理后,均需进行清洗,然后与上述甘薯淀粉操作方法相同处理,脱水制成湿淀粉,或干燥作成干淀粉。
玉米淀粉制作方法1.清理玉米中含有各种尘芥、有机和无机杂质。
为了保证安全生产和产品质量,对玉米中存在的杂质必须进行清理。
清理玉米的方法,主要采用筛选、风选等。
清理设备有振动筛、比重去石机、永磁滚筒和洗麦机等。
振动筛是用来清除玉米中的大、中、小杂物。
筛孔配备,第一层筛面用直径17~20毫米圆孔,第二层筛面直径12~15毫米圆孔,除去大、中杂,第三层筛面选用直径2毫米圆孔除去小杂。
比重去石机是用来除去玉米中的并肩石。
由于玉米粒度较大,粒型扁平,比重也较大等特点,在操作时应将风量适当增大,风速适当提高,穿过鱼鳞孔的风速为14米/秒左右。
鱼鳞孔的凸起高度也应适当增至2毫米,操作时应注意鱼鳞筛面上物料的运动状态,调节风量,并定时检查排石口的排石情况。
永磁滚筒是用来清除玉米中的磁性金属杂质,应安置在玉米地入破碎机前面,防止金属杂质进入破碎机内。
洗麦机可以清理玉米中的泥土、灰尘。
经过清理后玉米的灰分可降低0.02~0.6%。
2.浸泡:
玉米浸泡方法目前普遍采用金属罐几只或几十只用管道连接组合起来,用水泵使浸泡水在各罐之间循环流动,逆流浸泡。
在浸泡水中溶加浸泡剂经试用的结果表明,石灰水、氢氧化钠和亚硫酸氢钠都不及二氧化硫效果好,二氧化硫的含量不宜太高。
因为含二氧化硫的浸泡水对蛋白质网的分散作用是随着二氧化硫含量增加而增强。
当二氧化硫浓度为0.2%时,蛋白质网分散作用适当,淀粉较易分离;而浓度在0.1%时,不能发生足够的分散作用,淀粉分离困难。
一般最高不超过0.4%,因为二氧化硫的浓度过高,酸性过大,对玉米浸泡并没有多大好处,相反地会抑制乳酸发酵和降低淀粉粘度。
浸泡温度对二氧化硫的浸泡作用具有重要的影响,提高浸泡水温度,能够促进二氧化硫的浸泡作用。
但温度过高,会使淀粉糊化,造成不良后果。
一般以50~55℃为宜,不致于使淀粉颗粒产生糊化现象。
浸泡时间对浸泡作用亦有密切的关系。
在浸泡过程中,浸泡水不是从玉米颗粒的表皮各部分渗透到内部组织,而是从颗粒底部根幅处的疏松组织进入颗粒,通过麸皮底层的多孔性组织渗透到颗粒内部,所以必须保证足够的浸泡时间。
玉米在50℃浸泡4小时后,胚芽部分吸收水分达到最高值,8小时后,胚体部分也吸收水分达最高值。
这个时候玉米颗粒变软,经过粗碎,胚芽和麸皮可以分离开。
但蛋白质网尚未被分散和破坏,淀粉颗粒还不能游离出来。
若继续浸泡,能使蛋白质网分散。
浸泡约24小时后,软胚体的蛋白质网基本上分散,约36小时后,硬胚体的蛋白质网也分散。
因为蛋白质网的分散过程是先膨胀,后转变成细小的球形蛋白质颗粒,最后网状组织破坏。
所以要使蛋白质网完全分散,需要48小时以上的浸泡时间。
各地工厂的玉米浸泡条件不完全相同。
一般操作条件如下:
浸泡水的二氧化硫浓度为0.15~0.2%,pH值为3.5。
在浸泡过程中,二氧化硫被玉米吸收,浓度逐渐降低,最的放出的浸泡水内含二氧化硫的浓度约为0.01~0.02%,pH值为3.9~4.1;浸泡水温度为50~55℃;浸泡时间为40~60小时。
浸泡条件应根据玉米的品质决定。
通常是贮存较久的老玉米含水分低和硬质玉米都需要较强的浸泡条件,即要求较高的二氧化硫浓度、温度和较长的浸泡时间。
玉米经过浸泡以后,含水分应达40%以上。
3.玉米粗碎:
粗碎的目的主要是将浸泡后的玉米破成10块以上的小块,以便分离胚芽。
玉米粗碎大都采用盘式破碎机。
粗碎可分两次进行。
第一次把玉米破碎到4~6块,进行胚芽分离;第二次再破碎到10块以上,使胚芽全部脱落,进行第二次胚芽分离。
4.胚芽分离:
目前国内胚芽分离主要是使用胚芽分离槽。
优点是操作比较稳定,缺点是占地面积大,耗用钢材多,分离效率低,一般不超过85%。
国内外还有采用旋液分离器的玉米淀粉厂。
这种分离器由尼龙制成,用12只分离器集中放在一个架子上,总长度不超过1米,占地面积小,生产能力大,分离效率高,可达95%以上。
5.玉米磨碎:
经过分离胚芽后的玉米碎块和部分淀粉的混合物,为了提取淀粉,必须进行磨碎,破坏玉米细胞细胞,游离淀粉颗粒,使纤维和麸皮分开。
磨碎作业的好坏,对淀粉的提取影响很大。
磨得太粗,淀粉不能充分游离出来,因被粗细渣带走,影响淀粉出度。
太细,纤维分离不好,影响淀粉质量。
为了有效地进行玉米磨碎,通常采用二次磨碎。
第一次用锤碎机进行磨碎,经筛分淀粉乳后;第二次用砂盘淀粉磨进行磨碎。
有的用万能磨碎机作第一次磨碎,经筛分淀粉乳后,再用石磨进行第二次磨碎。
根据各地生产实践证明:
金刚砂磨较石磨好,硬度高,磨纹不易磨损,磨面不需经常维修,磨碎效率也高。
现已逐步以金刚砂磨代替石磨。
6.淀粉筛分:
玉米碎块经过磨碎后,得到玉米糊,可以采用筛分的方法将淀粉和粗细渣分开。
常用的筛分设备有六角筛、平摇筛、曲筛和离心筛等。
筛分淀粉的筛孔应根据筛分设备的种类和淀粉质量要求决定。
六角筛清洗粗渣筛孔直径为0.6毫米,细渣筛孔直径为0.12毫米,平摇筛筛分粗渣筛孔用7××号双料尼龙,筛分细渣筛孔用12××号双料尼龙,曲筛清洗粗、细渣使用六级的120°曲筛,筛长1.6米,第一级曲筛的筛缝宽0.05毫米,其余各级筛缝宽0.075毫米;离心筛的转子筛板筛孔为2×0.24毫米。
一般是用四级连续操作。
筛分粗、细渣需要清水量,按100公斤干物质计算,筛分粗渣需230~250升,细渣需10~130升,水温为45~55℃,含有0.05%二氧化硫,pH约为4.3~4.5为宜。
7.蛋白质分离和淀粉清洗:
分离粗、细渣后的淀粉乳浓度为6~8波美度,含干物质约11~14%。
这里的淀粉化学组成分析如下表:
成分含量(%)成分含量(%)淀粉88~92水溶性物质2.5~4.5蛋白质6~10二氧化硫0.035~0.045脂肪0.5~10细渣0.05~0.1克/升灰分0.2~0.4 从上表可以看出,淀粉乳中干物质除了淀粉以外,主要是蛋白质和水溶性物质,所以必须进行蛋白质分离和淀粉清洗。
分离蛋白质一般采用流槽分离,因占地大,分离效率低,现在逐步改用离心机分离。
但要求淀粉乳中含渣子要少,防止碟片内喷嘴堵塞,造成机械振动。
分离蛋白质后的粗制淀粉乳必需进行清洗。
淀粉清洗大都在清洗池内进行,但清洗时间长,淀粉损失大。
现代玉米淀粉厂淀粉清洗采用旋液分离器进行清洗,一般用9~14级旋液分离器处理。
根据测定,从离心机出来的淀粉乳蛋白质含量不超过2.5%,经过9级旋液分离器处理,成品淀粉中蛋白质含量可降至0.35%。
8.离心分离和干燥:
从旋液分离器出来的淀粉乳含水分78%,如果淀粉车间与淀粉糖车间结合在一起,就可直接送至淀粉糖车间使用。
不必进行淀粉乳脱水和干燥处理。
但是从清洗桶得到的淀粉乳含水分离,必须进行脱水处理。
把淀粉乳送入离心分离机进行脱水,可得含水分为45%的湿淀粉,这种湿淀粉也可以作为成品出厂。
为了便于运输和贮藏,最好进行干燥处理,将淀粉含水分降低至12%的平衡水分。
然后作为成品干淀粉出厂。
为了保证成品细度均匀,有时还要进行成品整理。
先经筛分处理,筛出规定细度的淀粉,筛上物送入粉碎机进行粉碎,然后再行筛分,使产品全部达到规定的细度。
9.副产品加工:
在生产玉米淀粉过程中,可以得到玉米浆、胚芽、渣子和蛋白质水等中间产品,如果进行加工,均能作为副产品利用。
玉米主要副产品加工方法如下:
(1)玉米浆:
用二氧化硫溶液逆流浸泡玉米,最后泵出浸泡水含干物质6~7%,可以采用三效真空蒸发,将它浓缩到含干物质50%的浓液,称为玉米浆。
根据玉米浆化学成分测定结果如下:
水分48~50%还原糖5.5%以上含氨量3.6%以上无机物10%以上氨氮0.9%以上乳酸9~12%以上玉米浆除了可作为培养酵母和抗菌素营养料和制造菲门和肌醇的原料外,与回收的玉米蛋白质和粗、细渣混合后,也是很好的动物饲料。
(2)玉米胚芽:
从筛分工段清洗过的胚芽含水分约50~60%,可用滚筒干燥机或沸腾机将它干燥至水分含量达4%。
通常采用三级干燥,第一级干燥到胚芽含水分约35%;第二级为10%;第三级达到胚芽规定的水分含量。
干燥后的胚芽含有45~50%的油分。
它比大豆的含油量高(大豆含油量约为20%),所以它是很好的油料。
经榨油机榨得的粗玉米油呈黄色,含游离脂肪酸,再经精炼处理,得精炼玉米油可以食用,油饼可作饲料。
(3)蛋白质水:
从流槽、碟式分离机或旋液分离器得到的蛋白质水,又称为麸质水或黄浆水。
蛋白质水的浓度低,但干物质中蛋白质含量高。
过滤性差,所以不能直接用过滤方法回收其中悬浮的蛋白质类物质。
通常采用在沉淀池内间歇沉淀或用浓缩离心机分离。
浓缩后的蛋白质与细渣混合,进行过滤、干燥、粉碎和筛分,得到含水分10~12%的蛋白质粉,也称为谷朊粉,含蛋白质在40%以上,可供配制饲料的原料。
(4)渣子和玉米浆的干燥:
从筛分设备筛上物得到的粗细渣子含水分约在85%以上,先经压榨机脱水,使水分含量降低到55~70%,再与玉米浆混合。
由于玉米浆的酸度较高,所以在与渣子混合前先用石灰中和玉米浆的酸度,然后混合、干燥到含水量为12%以下。
它的化学成分如下:
水分11~13%粗脂肪2%以下粗蛋白质18%以下粗纤维9%以下灰分8%以下可溶性蛋白50%以上从上列数据可以看出,蛋白质含量较高,可以作为良好的动物饲料。
小麦淀粉从小麦中提取淀粉,过去是采用发酵法,即将小麦加水浸软、磨碎后,进行加酸发酵,使包围在淀粉颗粒周围的细胞被溶解而淀粉易于分离。
但该法面筋的损失较多,而且淀粉中蛋白质不易去尽,影响淀粉质量,目前已被马廷法所代替。
马廷法它是以小麦面粉为原料,在搅合机中加水50~80%,以40转/分的转速使面粉捏合成面团。
搅合时间约30分钟,放置30分钟,使面筋膨润而互相粘结,使淀粉易于分离。
若添加适量食盐,可改良面筋的品质,而促进其粘结。
如遇面粉的游离酸多时,可加入适量的氢氧化钙调节其pH值。
面团暂时静置后,加5~8倍的水进行揉洗,分3~4次揉洗。
洗出的乳状液为淀粉乳,需进行精制提纯,剩下物为面筋,含水分为65~70%,经干燥后,蛋白质含量约为75~85%,可以食用或作为制造油面筋的原料。
上述小麦淀粉的提取方法是属于分段处理,不能连续操作。
国外曾报道过连续式制法,工序基本上相同,只是需采用连续设备组合起来进行生产。
阿耳塞廷法近年来,还有以小麦为原料生产淀粉的阿耳塞廷法。
该法生产原理与玉米淀粉生产工艺相同。
制作方法将含水分为14%、粗蛋白质含量约10%的软质小麦,用含0.2%二氧化硫的浸泡水在39℃温度下,浸泡12小时,吸水增加到55%。
其它操作方法与玉米加工相同。
得到成品淀粉中粗蛋白质含量在0.4%以下,回收率最高达83%。
藕粉藕粉一般含蛋白质0.8%、脂肪0.5%、