第一章煤制甲醇技术概述.docx
《第一章煤制甲醇技术概述.docx》由会员分享,可在线阅读,更多相关《第一章煤制甲醇技术概述.docx(14页珍藏版)》请在冰豆网上搜索。
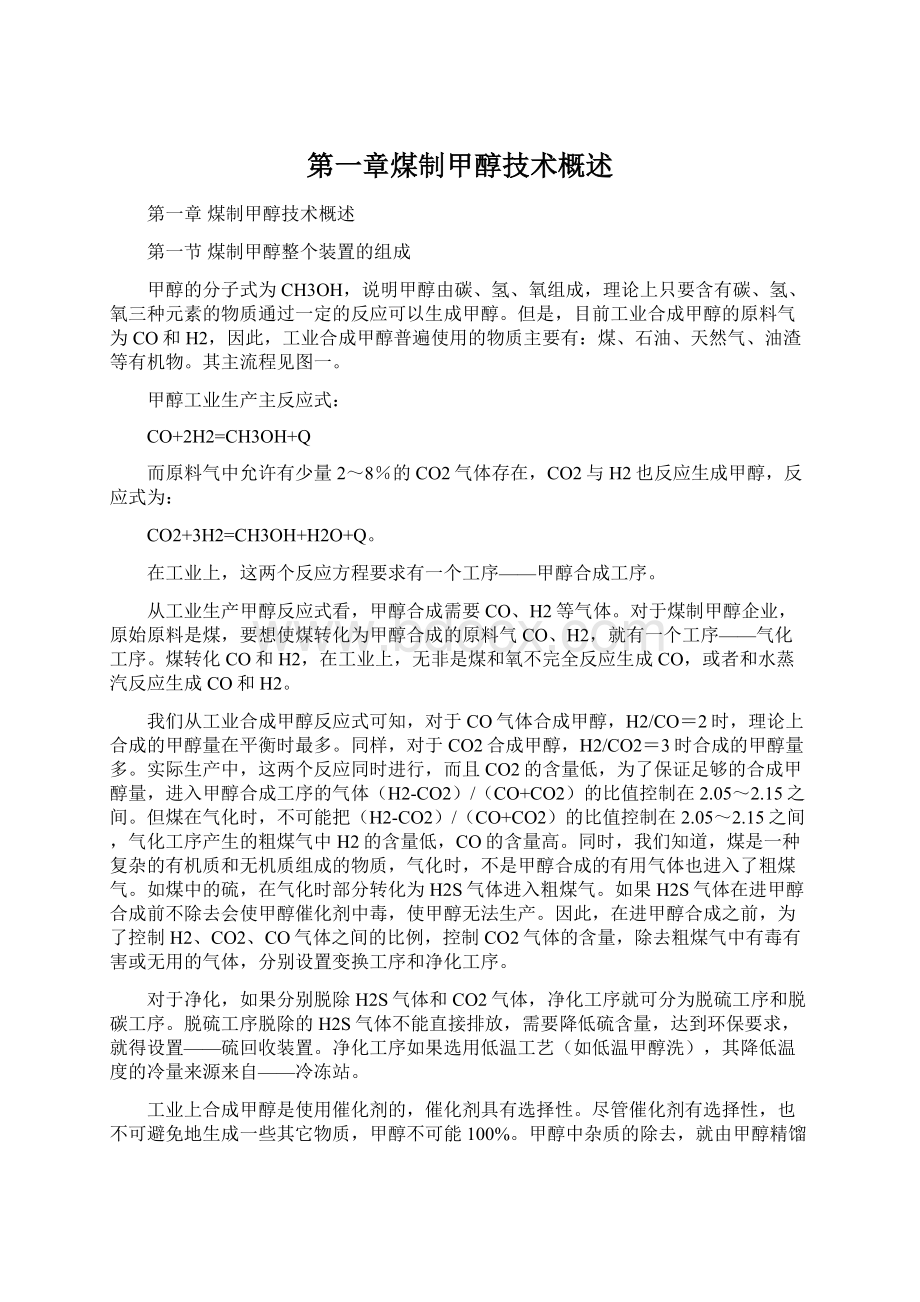
第一章煤制甲醇技术概述
第一章煤制甲醇技术概述
第一节煤制甲醇整个装置的组成
甲醇的分子式为CH3OH,说明甲醇由碳、氢、氧组成,理论上只要含有碳、氢、氧三种元素的物质通过一定的反应可以生成甲醇。
但是,目前工业合成甲醇的原料气为CO和H2,因此,工业合成甲醇普遍使用的物质主要有:
煤、石油、天然气、油渣等有机物。
其主流程见图一。
甲醇工业生产主反应式:
CO+2H2=CH3OH+Q
而原料气中允许有少量2~8%的CO2气体存在,CO2与H2也反应生成甲醇,反应式为:
CO2+3H2=CH3OH+H2O+Q。
在工业上,这两个反应方程要求有一个工序——甲醇合成工序。
从工业生产甲醇反应式看,甲醇合成需要CO、H2等气体。
对于煤制甲醇企业,原始原料是煤,要想使煤转化为甲醇合成的原料气CO、H2,就有一个工序——气化工序。
煤转化CO和H2,在工业上,无非是煤和氧不完全反应生成CO,或者和水蒸汽反应生成CO和H2。
我们从工业合成甲醇反应式可知,对于CO气体合成甲醇,H2/CO=2时,理论上合成的甲醇量在平衡时最多。
同样,对于CO2合成甲醇,H2/CO2=3时合成的甲醇量多。
实际生产中,这两个反应同时进行,而且CO2的含量低,为了保证足够的合成甲醇量,进入甲醇合成工序的气体(H2-CO2)/(CO+CO2)的比值控制在2.05~2.15之间。
但煤在气化时,不可能把(H2-CO2)/(CO+CO2)的比值控制在2.05~2.15之间,气化工序产生的粗煤气中H2的含量低,CO的含量高。
同时,我们知道,煤是一种复杂的有机质和无机质组成的物质,气化时,不是甲醇合成的有用气体也进入了粗煤气。
如煤中的硫,在气化时部分转化为H2S气体进入粗煤气。
如果H2S气体在进甲醇合成前不除去会使甲醇催化剂中毒,使甲醇无法生产。
因此,在进甲醇合成之前,为了控制H2、CO2、CO气体之间的比例,控制CO2气体的含量,除去粗煤气中有毒有害或无用的气体,分别设置变换工序和净化工序。
对于净化,如果分别脱除H2S气体和CO2气体,净化工序就可分为脱硫工序和脱碳工序。
脱硫工序脱除的H2S气体不能直接排放,需要降低硫含量,达到环保要求,就得设置——硫回收装置。
净化工序如果选用低温工艺(如低温甲醇洗),其降低温度的冷量来源来自——冷冻站。
工业上合成甲醇是使用催化剂的,催化剂具有选择性。
尽管催化剂有选择性,也不可避免地生成一些其它物质,甲醇不可能100%。
甲醇中杂质的除去,就由甲醇精馏工序来完成,合成工序的粗甲醇变为精甲醇产品。
同时,精甲醇的储存,需要——甲醇罐区。
水煤浆气化,需要纯度很高的氧气,必须有——空分工序。
水煤浆的组成主要是水和煤,煤的储存和输送——就是煤输送系统;同时,水煤浆中的煤颗粒很小,需要把大颗粒的煤磨成很细的煤,并和水混合,形成一定浓度的煤浆,就是——磨煤装置。
对于一个化工装置,有许多动设备,如泵、风机、破碎机、磨煤机、压滤机、压缩机等等,要使用电,就得设置——总变电所和分变电所;
整个化工装置中有许多物料需要加热或降温。
如甲醇精馏工序需要蒸汽把粗甲醇加温到轻组分的沸点,大型空气压缩机需要蒸汽驱动等等,这些蒸汽来源于锅炉工序,而锅炉生产蒸汽,需要合乎规格的水,设置了——脱盐水装置;如甲醇合成工序需要把高温的甲醇和未反应气体分离,在进脱碳工序前把变换的高温气体降到常温等等,都需要冷却水,为了节约水资源和降低产品成本,设置了——循环水装置,使冷却水循环使用;
脱盐水和循环水装置的补充水,来自于新鲜水装置。
建化工装置的目的,就是安全、高效、稳定运行,出合格的化工产品,这需要控制许多工艺和质量指标,这些指标的控制由分析化验室和自控仪表系统(中控室)来完成;
化工生产中,要产生废气、废水、废渣,直接排放不符合环保要求。
可燃废气由火炬燃烧;废水有废水处理工序处理;废渣有废渣处理工序处理。
整个化工装置的开车和运行,需要辅助工序。
如柴油站供锅炉开车、液化气站供气化开车和火炬燃烧、地中衡称进出工厂的原料和产品、电仪修负责设备和仪器的检修和维护、后勤保障操作人员和管理人员的生活等等。
表一:
煤制甲醇整个装置工序组成
系统
工序名称
系统
工序名称
系统
工序名称
系统
工序名称
厂外工程
厂外供电
公用系统
总变电所
辅助系统
地中衡
辅助系统
储煤场
厂外给排水
分变电所
柴油站
全厂照明
厂外运输
原水站
液化气站
全厂电信
厂外渣场
仪表空压站
热交换站
全厂消防
主要装置
空分系统
脱盐水站
火炬
厂区道路
气化系统
循环水站
冷冻站
围墙及门卫
变换系统
输煤站
硫回收系统
仓库
净化系统
锅炉系统
泡沫站
综合办公
甲醇合成系统
中心化验
氢回收
机电仪维修
甲醇精馏系统
全厂控制室
装车站
食堂及宿舍
甲醇罐区系统
图一:
水煤浆制甲醇主流程简图
第二节煤制甲醇主流程概述
煤制甲醇,顾名思义就是原始原料为煤,最终产品为甲醇。
工业合成甲醇是用CO和H2气体,而CO和H2气体来源于煤的限制反应,即煤的气化。
煤气化得到的粗煤气中,含有大量的CO和H2气体,但合成甲醇是不合适的,一是CO和H2气体比例不合适,二是粗煤气中还含有对甲醇合成有害或无用的气体,因此,气化来的粗煤气要经过CO的转化、杂质气体的净化、CO和H2气体的合成、粗甲醇的精制等工序,最终制的精甲醇产品。
随着工业的发展,人类要求工业技术对环境越加友好,我们就以工程成熟的,对环境友好的低温精馏空气分离、德士古水煤浆气化、宽温耐硫变换、大连低温甲醇洗净化、鲁奇甲醇合成、三塔甲醇精馏、高浓度水煤浆湿法磨煤等技术来简要介绍煤制甲醇的主流程。
详细流程在第二章叙述,本章是入门。
一、气化流程概述:
水煤浆气化是水煤浆与氧气在气化炉内进行高温反应产出甲醇原料气的过程。
水煤浆的主要组分为煤和水,添加剂的量很少。
因此,水煤浆的气化简单地可以看成两个阶段——煤与氧燃烧和燃烧产物与水、碳的反应。
第一阶段,煤与氧燃烧:
CmHnO(复杂有机物)+(m-1/2+n/4)O2=mCO2+n/2H2O+Q1
C+O2=CO2+Q2
第二阶段,上述产物与水蒸气、碳的反应:
CO2+C=2CO-Q3
C+H2O(g)=CO+H2-Q4
CO+H2O(g)=CO2+H2+Q5
CH4+H2O(g)=CO+3H2-Q6
CH4+CO2=2CO+2H2-Q7
还有许多副反应,在此不在写出。
从上面的反应式看,要使水煤浆气化反应得以顺利的进行,首要条件是在不计热损失和其它副反应的情况下,维持热平衡:
Q1+Q2+Q5=Q3+Q4+Q7+Q6。
德士古水煤浆气化技术,在实际生产中,水煤浆中的水分大于35%,气化温度在14000C左右,大量水需要变成相同温度的蒸汽,还有其它副反应的热量及各种热损失,这样,要求放出的热量必须远远大于吸收和损失的热量,气化才可以顺利进行。
气化在14000C左右的温度下反应,把煤中的无机质融化为流体,成为灰渣和飞灰,为了把高温灰渣顺利排出,把飞灰和煤气分离,大量热量需要移走。
同时产生的煤气温度也是14000C左右,而气化的下游变换工序要求的煤气温度低,也要求把多余的热量移走。
对于德士古水煤浆气化工艺中气化炉内的热量移走一般有两种:
a激冷法,即用大量水冷却。
b废热锅炉法,即副产蒸汽。
激冷过程:
14000C左右的粗煤气和熔渣(灰)经激冷环直接用水冷却后,沿下降管导入激冷室进行水浴,熔渣被固化分离,煤气中所带飞灰很少。
同时煤气中的水蒸气已经达到饱和,对变换工序是有利的。
废锅流程:
14000C左右的粗煤气和熔渣经过间接锅炉(辐射锅炉)回收一部分热量,生产一部分蒸汽,或经过对流锅炉回收一部分热量,产生一部分蒸汽,熔渣冷却被固化,粗煤气的温度也降低。
这样,粗煤气没有经过水冷却,其中水分含量少,达不到变换反应的要求。
上述两种工艺虽废锅流程具有很明显的热效率优势,但变换反应需要蒸汽。
如果水煤浆气化后面是变换工序,一般选用激冷流程。
气化炉内粗煤气,虽经过冷激水洗涤降温,出气化炉时,还夹带着许多细小的灰尘,灰尘不除,后工段无法生产,需采用文丘里和水洗塔继续进行除灰。
激冷室和水洗塔排出的黑水通过灰水处理,除去其中的细灰,循环使用。
根据上述原理,推导的气化主流程见图二:
图二:
水煤浆制甲醇水煤浆气化主流程
二、变换流程概述:
从气化来的粗煤气中,虽然含有CO2、CO和H2气体,但CO的含量远高于甲醇合成需要H2/CO=2的含量,CO加水蒸气转化成H2和CO2就是CO的变换。
CO的变换既生成有用的H2气体,又生成易除去的CO2气体(净化工序中除去),其反应式为:
CO+H2O(g)=CO2+H2+Q。
1、我们简单分析这个反应式的特点:
①CO和H2O(g)在4000C左右的情况下很难发生反应,即使在10000C,反应进行的很慢,为了使此反应在较低的温度下很快的发生反应,就借助催化剂。
②此反应式为可逆的反应,反应物和生成物间存在一个平衡问题,即为不完全反应。
CO反应的多少与变换反应的平衡常数有关。
变换的平衡常数为KP=PH2*PCO2/PCO*PH2O,与温度有关。
③变换反应为放热反应。
热量的放出可以提高反应温度,加快反应速度,以及平衡向左移动,CO的转换率下降。
因此在反应过程中要控制温度。
④变换反应为等体积反应。
压力对反应的影响不大,但高压下的气体体积小,反应速度快,设备小。
变换反应是一个有催化剂参与的反应,催化剂的参与,要求有起始活性温度,也就是说,气体和催化剂的温度达到一定的温度,催化剂才起作用,CO和水蒸气开始反应;同时由可逆和放热的特点决定了变换反应在催化剂床层有最适宜温度,最适宜温度与活化能有关。
降低活化能,反应容易进行,催化剂的本质就是降低变换反应的活化能,因此,变换催化剂的好坏和不同型号决定了变换反应的温度。
变换催化剂发展到目前,有中温变换和低温变换催化剂。
宽温耐硫催化剂为钴钼组分的。
2、相关工序对变换的影响:
①水煤浆气化来的粗煤气中,CO的含量远高于甲醇合成需要H2/CO=2的含量,通过计算,只要有47%左右的CO转化为氢气,就能满足H2/CO=2。
变换反应为不完全变换,即变换率很低,粗煤气一次通过催化剂床层,可满足甲醇合成的要求;不完全变换,使放出的热量比较少,不需要在催化剂中间置换热器———及时移走热量。
②水煤浆气化采用激冷流程,出气化工序的粗煤气中水蒸气已经饱和。
加之甲醇合成不要求CO全部转化为氢气(低变换率),粗煤气中的水蒸气能满足变换反应的要求;
③变换的下游工序是低温甲醇洗,低温甲醇洗的操作温度在零下60℃——零下40℃之间,这要求进净化前的变换气温度越低越好。
因此,在变换流程上要多次换热,一是回收反应热,二是降低变换气的温度。
由上述分析,推导的变换主流程见图三。
图三:
煤制甲醇变换主流程
三、低温甲醇洗流程概述:
粗煤气经过变换工序,已经把煤气成分中的CO、H2调整到甲醇合成的要求,但还有大量CO2气体和对甲醇合成有害的H2S、COS气体以及少量的CH4、N2等惰性气体。
变换气中CO2、H2S、COS等气体的脱除,需要用低温的甲醇吸收。
低温甲醇洗脱除CO2、H2S、COS气体是物理吸收法,即应用各种气体在甲醇中的溶解度存在很大差异以及同一种气体在甲醇中的溶解度随温度和压力的变化而变化进行的。
变换气中有CO2、H2S、COS、CO、H2、CH4、N2等气体,而CO2、H2S、COS在甲醇中溶解度是CO、H2、CH4、N2等气体在甲醇中溶解度的几千倍、几万倍。
而CO2、COS、H2S在甲醇中的溶解度又有差异,如-400C时COS和H2S在甲醇中溶解度和CO2相比,H2S/CO2=5.9,COS/CO2=3.6这决定了甲醇在同一条件下更易吸收COS和H2S。
如果甲醇温度从200C降到-400C,CO2的溶解度增加6倍左右。
气体的溶解度随压力的升高而增大。
根据实验和生产实践,低温甲醇脱除硫和二氧化碳气体的温度在-400C左右时,脱掉硫和二氧化碳的净化气组分可以达到甲醇合成的要求,又比较经济。
可是在-400C左右,变换气中所含的水蒸气被冷凝成固体,会堵塞管道和设备,同时,如果水进入甲醇,,CO2气体在甲醇中的溶解度要下降,因此,低温甲醇脱除硫和二氧化碳气体之气要除去变换气中的水分。
我们知道甲醇和水可以互溶。
变换气中COS、H2S气体含量很小,CO2气体含量很大。
-400C时COS在甲醇中的溶解度是CO2气近6倍。
这就决定了在低温甲醇洗中CO2的吸收是控制因素,即CO2吸收流程比H2S吸收流程长。
脱硫脱碳如果在一个塔内进行,脱硫在下部进行,脱碳在中上部进行。
气体在溶解于甲醇时,要放出热量。
如CO2气体在甲醇中的熔解热为16.945KJ/mol,H2S为19.264KJ/mol。
变换气中,CO2气体占到总量的30%以上,溶解于甲醇时放出大量的热量,溶液温度升高,可能造成净化气组分不达标。
这要求吸收塔中部引出甲醇,降温后再继续脱硫脱碳。
甲醇吸收H2S、CO2后,再循环到吸收塔,净化气组分一定不达标,因此,吸收H2S和CO2后的甲醇要把H2S和CO2气体从甲醇中解析出来,即甲醇溶液的再生。
甲醇溶液的再生,有闪蒸法(减压降低气体在甲醇中的溶解度,把溶解的气体释放出来)、气提法(用惰性气体降低溶解在甲醇中气体的分压,把溶解的气体释放出来)、加热再生法(提高温度降低气体在甲醇中的溶解度,把溶解的气体释放出来)。
由上述分析,推导的低温甲醇洗主流程见图四。
图四:
煤制甲醇低温甲醇洗主流程
四、甲醇合成流程概述:
水煤浆气化出来的粗煤气,经过变换和净化工序,(H2-CO2)/(CO+CO2)的比值控制在了2.05~2.15,同时煤气中有效组分H2、CO2、CO含量大于98%,符合工业合成甲醇要求。
工业合成甲醇的主反应式:
CO+2H2=CH3OH(g)+100.4KJ/mol
工业合成甲醇的次反应式:
CO2+3H2=CH3OH(g)+H2O(g)+58.6KJ/mol
实际上反应热与温度和压力都有关系。
1、我们简单分析主反应式的特点:
A此反应式为可逆的反应,反应物和生成物间存在一个平衡问题,即为不完全反应。
即使KP=PCH3OH/PCO*P2H2达到平衡时,甲醇的生成量也很低,在3%——6%之间,说明未反应的原料气CO和H2的量很大。
B此反应为放热反应,热量的放出可以提高反应温度,加快反应速度,以及平衡向左移动,甲醇的合成率下降。
因此在反应过程中要控制温度,尽可能生成多的甲醇。
C此反应为体积缩小的反应,压力升高,平衡向右移动生成的甲醇量就多。
DH2、CO2、CO气体反应时,如果没有催化剂,可以生成好多种有机物,甲醇是我们的目标产品,利用催化剂的选择性尽可能地生成甲醇。
因此,甲醇合成是有催化剂参与的反应,一是加快反应,二是利用其选择性。
甲醇合成反应式和变换反应式的特点有相似之处,因此,气体反应要达到催化剂的起始活性温度和尽可能维持最适宜温度。
鲁奇合成塔的温度控制,是用水循环冷却,同时副产蒸气。
甲醇合成工艺,即使反应达到平衡时,甲醇的生成量在3%——6%之间,未反应的原料气CO和H2的量很大。
一种方案是冷却分离甲醇后进入下一个甲醇合成塔,直接到CO和H2基本反应完,这种方法能耗太高,已淘汰。
另一种方法是冷却分离甲醇后的气体再返回甲醇合成塔循环使用。
2、其它影响因素:
A甲醇合成塔内反应温度在240℃——280℃,生成的甲醇为气态(气体),要想使甲醇从体中分离出来,就要利用甲醇的沸点64.8℃,在加压下甲醇的沸点更高,更易液化。
用水冷却就可以把甲醇从气体中分离出来。
B原料气中除有大量的CO、H2外,还有少量的CH4、N2等杂物,这部分杂质会随反应的进行而积累即含量增加(未反应的氢气和一氧化碳气体循环反应,不断消耗,惰气含量就增加)。
当这部分杂物超过一定含量后,甲醇的合成就不经济了,因此,甲醇的合成气中要维持一定含量的惰气,即放空一部分气体。
而放空气中含有大量的H2,放空不回收,白白浪费,因此要有H2回收装置。
C从合成塔出来的反应气通过降温,气体甲醇变为液体甲醇。
未反应的H2、CO2、CO等气体在低温高压下,有少量溶解于液体甲醇中,溶解的气体通过降低压力而解析出来。
由上述分析,推导的甲醇合成主流程见图五。
图五:
煤制甲醇鲁奇甲醇合成主流程
五、甲醇精馏流程概述:
甲醇合成来的粗甲醇中含有少量的H2、CO、CH4等气体,含有比甲醇的沸点低的二甲醚、甲酸、甲醋等杂质,含有比甲醇的沸点高的水、丁醇等杂质。
这些杂质不除去,是不能成为甲醇产品出售或加工下游产品的。
这些杂质的除去就是采用粗甲醇中的各组分的沸点不同,控制适当的温度把气体、低沸点杂质、高沸点杂质和甲醇分开。
因此,甲醇精馏分为两步,一步是在较低温度下除去低沸点杂质和气体,一步是在较高温度下把甲醇从高沸点杂质中分离出来。
由上述分析,推导的甲醇精馏主流程见图六。
图六:
煤制甲醇甲醇精馏主流程
六、硫回收流程概述:
低温甲醇洗再生释放出来的气体中H2S含量大于15%,直接放入大气,环保不达标,这要求选用合适的方法把气体中的硫回收,达到排放标准。
含高浓度H2S气体的处理有很多种,但传统的方法是克劳斯硫回收法.
克劳斯硫回收的反应式:
H2S+1/2O2=S+H2O+Q
最初克劳斯硫回收,直接用氧化剂氧化H2S生成单质硫,由于反应速度太快,短时间放出大量的热量,反应温度难以控制,为了改变这种局面,技术工程人员作了重大改进,把硫回收的反应式分成二步来进行,先把1/3的H2S先转化为SO2,然后和2/3的H2S反应生成单质硫。
这是克劳斯法硫回收的技术关键之一。
第一步反应式:
H2S+3/2O2=SO2+H2O+Q1
第二步反应式:
2H2S+SO2=3S+2H2O+Q2
从反应式知道,生成的单质硫要和反应完的气体分离,硫有许多种晶体,熔点也不一样,最低的熔点为119℃。
因此通过降温来分离单质硫和反应完的气体。
由上述分析,推导的克劳斯硫回收主流程见图七。
图七:
煤制甲醇克劳斯硫回收主流程
七、水煤浆制备流程概述:
水煤浆是煤清洁利用的发展方向之一。
水煤浆的组成主要是煤、水、添加剂,是一种流体,这要求水煤浆具有如下的特点:
1、良好的流变特性,适应不同运输和燃烧情况的要求:
①储存时,能形成一定的结构,表现为高粘度防止沾淀;②流动输送时粘度迅速降低,有良好的流动性;③燃烧时,粘度迅速降低,易雾化,提高效率。
2、良好的稳定性和触变性:
①稳定性好,水煤浆中固体煤炭颗粒保持均匀分散悬浮状态的性质;②触变性好,水煤浆储存时有良好的结构化特性,但给予外力时,粘度迅速降低有良好流动性。
3、具有合理粒度分布特性,以保持水煤浆中煤炭不同颗粒径比例与分布以达到较高的堆积效率和浓度。
水煤浆气化用到的水煤浆浓度大于58%,属高浓度水煤浆,目前只能用湿法磨矿工艺,其主流程见图八。
图八:
水煤浆制甲醇水煤浆制备主流程
八、空分流程概述:
水煤浆气化要求氧气纯度大于99.6%,而空气中,氧气含量不到21%,这就需要把氧气从空气中分离出来。
气化时需要的氧气量大,纯度高,目前空气分离采用较多的是低温精馏法。
气液相进行物质和热量的交换是精馏的条件之一,气液相接触时,沸点高的物质变为液体,沸点低的物质变为气体,从而达到分离的目的,即低温精馏空气分离的原理就是利用空气中各种成分的沸点不同,通过精馏把氧气从空气中分离出来。
空气在常温常压下是气体,不具备精馏的条件。
在一个大气压下,氧气的沸点为-182.980C,其临界状态下其沸点为-118.90C,压力为5.053MPa;氮气的沸点-195.80C,其临界状态下其沸点为-146.80C,压力为3.400MPa;空气的沸点-193.00C,其临界状态下其沸点为-140.50C,压力为3.0766MPa。
要想使空气变为液体,或把空气降到很低的温度,或加压后再降到较低温度,这么低得温度可以通过空气加压后突然减压获得。
通过实验,空气从3.104MPa的压力突然降到0.1MPa,减压前后的温差约1000C。
空气精馏塔的操作温度很低,相应从精馏塔出来的气氮和液氧的温度就很低,需要加温后送出界外。
我们知道,空气是一种混合物,其组分除N2、O2主要成分外,还有少量的或微量的组分,如尘埃、惰性气体、水蒸气、二氧化碳、碳氢化合物等多种物质。
空气中少量或微量的物质,有些是对空气分离有害的,必须清除。
尘埃可能损坏压缩机,用空气过滤器清除。
水蒸气和二氧化碳在低温下会成为固体,堵塞管道和设备;碳氢化合物在高纯度的液氧中会发生爆炸。
少量的水蒸气、二氧化碳、碳氢化合物如丙烯,用分子筛吸附。
把空气看成简单的氧氮二组分气体,由上述分析,推导的空气分离主流程见图九。
主要包括:
①空气的过虑和压缩②空气的冷却和纯化③空气的精馏。
图九:
低温精馏空气分离主流程