PSA制氮技术与氮气纯化技术.docx
《PSA制氮技术与氮气纯化技术.docx》由会员分享,可在线阅读,更多相关《PSA制氮技术与氮气纯化技术.docx(17页珍藏版)》请在冰豆网上搜索。
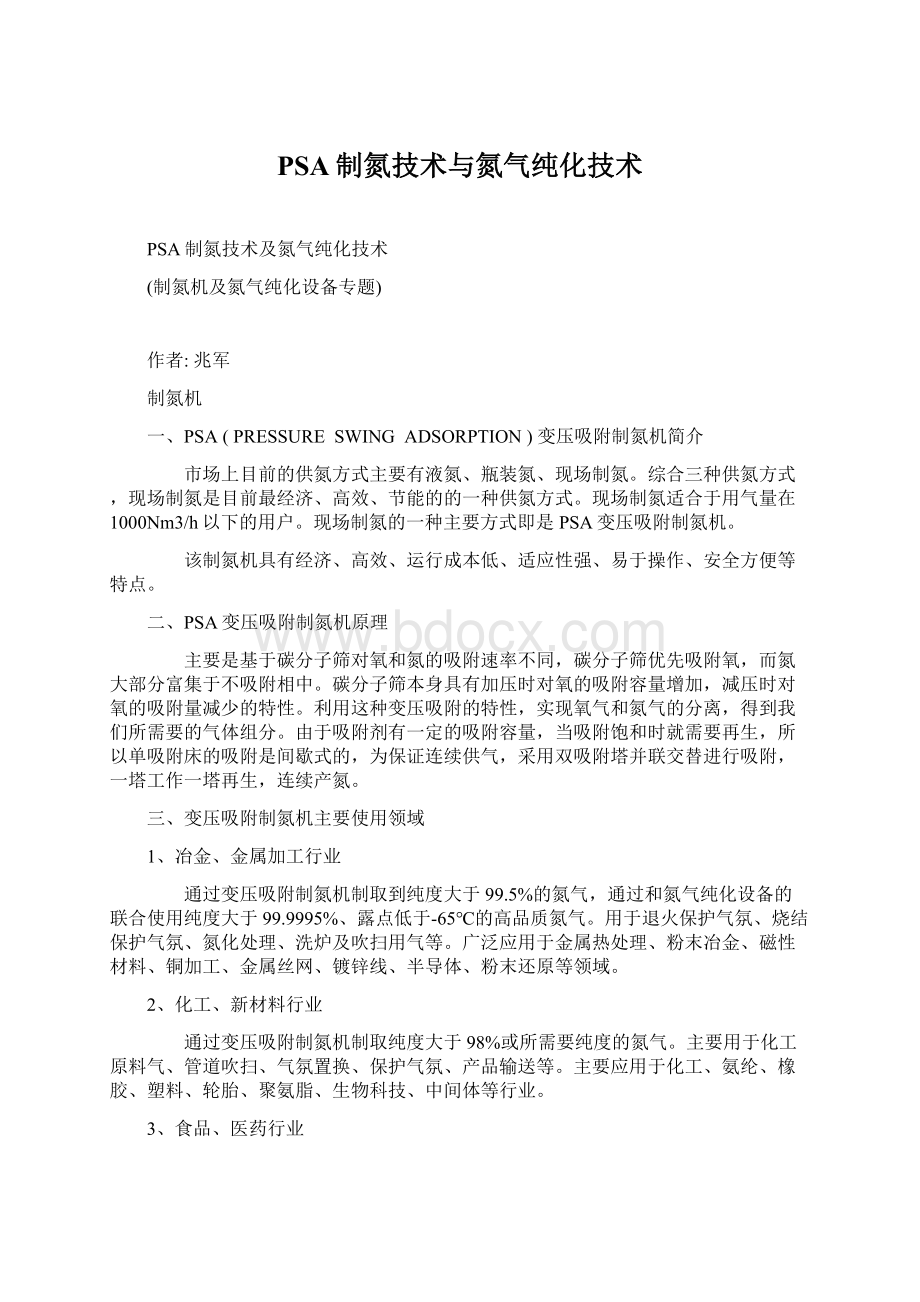
PSA制氮技术与氮气纯化技术
PSA制氮技术及氮气纯化技术
(制氮机及氮气纯化设备专题)
作者:
兆军
制氮机
一、PSA(PRESSURESWINGADSORPTION)变压吸附制氮机简介
市场上目前的供氮方式主要有液氮、瓶装氮、现场制氮。
综合三种供氮方式,现场制氮是目前最经济、高效、节能的的一种供氮方式。
现场制氮适合于用气量在1000Nm3/h以下的用户。
现场制氮的一种主要方式即是PSA变压吸附制氮机。
该制氮机具有经济、高效、运行成本低、适应性强、易于操作、安全方便等特点。
二、PSA变压吸附制氮机原理
主要是基于碳分子筛对氧和氮的吸附速率不同,碳分子筛优先吸附氧,而氮大部分富集于不吸附相中。
碳分子筛本身具有加压时对氧的吸附容量增加,减压时对氧的吸附量减少的特性。
利用这种变压吸附的特性,实现氧气和氮气的分离,得到我们所需要的气体组分。
由于吸附剂有一定的吸附容量,当吸附饱和时就需要再生,所以单吸附床的吸附是间歇式的,为保证连续供气,采用双吸附塔并联交替进行吸附,一塔工作一塔再生,连续产氮。
三、变压吸附制氮机主要使用领域
1、冶金、金属加工行业
通过变压吸附制氮机制取到纯度大于99.5%的氮气,通过和氮气纯化设备的联合使用纯度大于99.9995%、露点低于-65℃的高品质氮气。
用于退火保护气氛、烧结保护气氛、氮化处理、洗炉及吹扫用气等。
广泛应用于金属热处理、粉末冶金、磁性材料、铜加工、金属丝网、镀锌线、半导体、粉末还原等领域。
2、化工、新材料行业
通过变压吸附制氮机制取纯度大于98%或所需要纯度的氮气。
主要用于化工原料气、管道吹扫、气氛置换、保护气氛、产品输送等。
主要应用于化工、氨纶、橡胶、塑料、轮胎、聚氨脂、生物科技、中间体等行业。
3、食品、医药行业
通过变压吸附制氮机制取纯度大于98%或纯度为99.9%的氮气。
通过除菌、除尘、除水等处理,得到高品质的氮气,满足该行业的特殊要求。
主要应用于食品包装、食品保鲜、医药包装、医药置换气、医药输送气氛。
4、电子行业
通过变压吸附制氮机制取纯度大于99.9%或99.99%以上的氮气,或经过氮气纯化设备得到纯度大于99.9995%、露点低于-65℃的高品质氮气。
用于电子产品的封装、烧结、退火、还原、储存等。
主要应用于波峰焊、回流焊、水晶、压电、电子陶瓷、电子铜带、电池、电子合金材料等行业。
5、其他使用领域
制氮机除了使用在以上行业以外,在煤炭、石油、油品运输等众多领域也得到广泛使用。
随着科技的进步和社会的发展,氮气的使用领域也越来越广泛,现场制气(制氮机)以其投资省、使用成本低、使用方便等优点已经逐渐取代液氮蒸发、瓶装氮气等传统供氮方式。
PSA制氮设备在高性能MnZn铁氧体生产中的应用
1 引言
众所周知,气氛烧结是现代高性能MnZn铁氧体生产中的关键工序,而品质良好、价格便宜的氮气又是实施气氛烧结的基本条件之一。
我国是世界上铁氧体生产大国,软磁铁氧体的产量已跃居世界第二位,生产企业很多,因生产规模及设备不同,故采用的供气方式也各异。
以真空气氛烧结炉作为主要烧结设备者,因规模相对较小,其氮气总量需求不多,一般均使用外购的瓶装高纯氮气。
瓶装氮气规格通常是6Nm3/瓶,价格在30~40元/瓶,故氮气单价在5~7元/m3。
生产规模较大(年产量一般在300吨以上)的工厂则是以氮气隧道窑作为磁芯的主要烧结设备,它们的供气方式有两种。
一是购买液氮(液氮贮罐及气化器)来提供生产所需的氮气。
1m3液氮可气化为标准状态下的气氮643m3,氮气的综合单价在2~2.5元/m3。
另一种方式是工厂购置制氮设备现场制氮,因制氮设备的种类、规格不同,其氮气成本在0.4~0.6元/m3。
近年来也有尝试租赁制氮设备供气的,其氮气成本在1.5元/m3左右。
由上可知,采用不同的供气方式其生产成本差别是较大的。
表1以年产量1200吨MnZn铁氧体磁芯生产线(每小时需供气100m3,年供气量864000m3)为例将不同供气方式的单价及年用气成本作一粗略比较,就可见一斑。
表1 不同供气方式下的氮气成本
供气方式
单价/元.m-3
成本/万元.年-1
外购液氮
2.5
216
自购设备制氮
0.6
51.8
租赁设备制氮
1.5
129.6
2 三种制氮方法及其特点
现代工业用氮的制取方法都是以空气为原料,将其中的氧和氮分离而获得。
目前主要有三种,即深冷空分法、分子筛空分法(PSA)和膜空分法。
1) 深冷空分制氮
深冷空分制氮是一种传统的制氮方法,已有近九十年的历史。
它是以空气为原料,经过压缩、净化,再利用热交换使空气液化成为液空。
液空主要是液氧和液氮的混合物,利用液氧和液氮的沸点不同(在1大气压下,前者的沸点为-183℃,后者的为-196℃),通过液空的精馏,使它们分离来获得氮气。
深冷空分制氮设备复杂、占地面积大,基建费用较高,设备一次性投资较多,运行成本较高,产气慢(12~24h),安装要求高、周期较长。
综合设备、安装及基建诸因素,3500Nm3/h以下的设备,相同规格的PSA装置的投资规模要比深冷空分装置低20%~50%。
深冷空分制氮装置宜于大规模工业制氮,而中、小规模制氮就显得不经济。
2) 分子筛空分制氮
分子筛空分制氮是以空气为原料,以碳分子筛作为吸附剂,运用变压吸附原理,利用碳分子筛对氧和氮的选择性吸附而使氮和氧分离的方法,通称PSA(PressureSwingAdsorption)制氮。
此法是七十年代迅速发展起来的一种新的制氮技术。
与传统制氮法相比,它具有工艺流程简单、自动化程度高、产气快(15~30分钟)、能耗低,产品纯度可在较大围根据用户需要进行调节,操作维护方便、运行成本较低、装置适应性较强等特点,故在1000Nm3/h以下制氮设备中颇具竞争力,越来越得到中、小型氮气用户的欢迎,PSA制氮已成为中、小型氮气用户的首选方法。
3) 膜空分制氮
膜空分制氮是八十年代国外迅速发展的又一种新型制氮技术,在国推广应用是最近三四年的事。
膜空分制氮的基本原理是以空气为原料,在一定压力条件下,利用氧和氮等不同性质的气体在膜中具有不同的渗透速率来使氧和氮分离。
和其它制氮设备相比它具有结构更为简单、体积更小、无切换阀门、维护量更少、产气更快(≤3分钟)、增容方便等优点,它特别适宜于氮气纯度≤98%的中、小型氮气用户,有最佳功能价格比。
而氮气纯度在98%以上时,它与相同规格的PSA制氮机相比价格要高出15%以上。
由上可知,MnZn铁氧体生产企业,采用什么供气方式和何种供气技术,必须根据企业情况进行技术经济论证,选择最佳供气方案。
3 PSA制氮法的应用
众所周知,氮窑烧结时有三条重要曲线即温度、压力和气氛曲线,这三条曲线对产品的质量影响极大,生产中一旦调整到位最好保持稳定。
而所提供的氮气压力、流量和纯度的变化将影响窑气氛的稳定。
因此高性能锰锌铁氧体磁芯使用氮气保护烧结时对所供氮气有如下特定的要求。
(1)氮气纯度
①氧含量必须控制在一定量以下,否则不能满足高性能磁芯的烧结气氛要求。
②残氢量应尽可能少,否则磁芯在烧结时会开裂、变形,磁芯性能会恶化。
③氮气尽可能干燥,通常是以露点来表示其含水量。
(2)氮气的流量
氮气流量是气氛烧结的基本要素之一,不同规格的氮窑和烧结制度,其单位台时的耗氮量是不同的。
如28米单推板氮窑年生产磁芯的能力约为300吨,非致密化烧结时耗氮量约为20m3/h,而采用致密化烧结时耗氮量在30m3/h左右,平均耗氮量约为25m3/h。
36米双推板氮窑年生产磁芯的能力约为800吨,非致密化烧结时耗氮量约为40m3/h,而采用致密化烧结时耗氮量约为60m3/h,平均耗氮量约为50m3/h。
目前国新制氮窑大多是这两种规格。
按此测算年产1000吨磁芯耗氮量为80~120m3/h。
(3)氮气压力适宜,因为氮气输送需要一定的压力。
(4)氮气压力、流量、纯度要稳定。
因为氮窑的烧结特点是连续进行,一年365天每天24小时要不间断供气,为保证已调好的烧结气氛稳定,要求氮气的压力、流量和纯度保持稳定。
瑞气空分设备有限公司自1979年开始,研制了PSA制氮设备,至今为止,已为国各大型磁材生产商提供了适应于各种工艺的现场制氮设备,其中包括东磁集团、恒磁、升华强磁、通力、永久、金鸡、江门粉末等国知名企业。
瑞气空分设备有限公司愿以多年的现场制氮经验,与磁材生产商共同为中国从磁材生产大国向磁材生产强国转变而努力。
PSA设备与深冷技术比较
一、设备组成
PSA设备主要由空压机、压缩空气净化装置、氧氮分离系统组成,稳定性高;操作极为方便,主要运行部件为管道式气动阀,其密封件寿命可达150万次以上;
而深冷设备组成为:
空压机、预冷机、纯化器、膨胀机、精馏塔、液空过滤器、换热器……设备组成相对复杂、故障点多,纯化器中的电加热器、固态继电器需经常更换,其中的13X分子筛也需三年左右更换一次,膨胀机也容易发生烧瓦事故,因而稳定性不高;
PSA设备开机时间极短,只需20分钟,并且可以随开随停。
而深冷设备开机时间为16-48小时,甚至更长,一旦设备出现停机,重新开机相当麻烦。
二、占地
PSA设备组成简单,因而占地极少,无须任何基础,安装调试极为方便,现场费用低;而深冷设备占地极较多,现场基建工作量大,费用高,现场及基建费用约占设备投资的20%,安装调试时间长。
三、电耗(设备运行年时间以8000小时计,电费以0.5元/KW.h计)
PSA设备耗气量为420Nm3/min,与深冷相差较大,而深冷设备耗气量为625Nm3/minPSA空压机配置与深冷至少相差1000KW,每年电耗相差400万元。
PSA的冷干机125KW,深冷设备预冷机190KW,纯化器电加热1000KW,两者相差1065KW,年电耗相差426万元。
四、其它运行成本
PSA设备只需要定时过滤器滤心及管道式气动阀密封件,平均年费用不足10万元,分之筛十年不用更换。
深冷设备纯化器中的电加热器、固态继电器需经常更换,其中的13X分子筛也需三年左右更换一次,膨胀机也容易发生烧瓦事故,平均年费用至少16万元;10年相差160万元.而PSA设备没有此项费用。
还有每年的设备大修至少在50万以上。
人力成本,PSA设备只须两人,而深冷设备至少要求配备8人以上,并且深冷设备的操作、维护人员要求取得国家颁发的上岗证书。
每人每年按20000元工资计算,相差12万元。
几种空分方法的比较如下:
几种空分方法的比较
项目
深冷空分法
膜分离空分法
变压吸附空分法
分离原理
将空气液化,根据氧和氮沸点不同达到分离。
根据不同气体分子在膜中的溶解扩散性能的差异来完成分离。
加压吸附,降压解吸,利用氧氮吸附能力不同达到分离。
装置特点
工艺流程复杂,设备较多,投资大。
工艺流程简单,设备少,自控阀门少,投资较大。
工艺流程简单,设备少,自控门较多,投资省。
工艺特点
-160~-190℃低温下操作
常温操作
常温操作
操作特点
启动时间长,一般在15~40小时,必须连续运转,不能间断运行,短暂停机,恢复工况时间长。
启动时间短,一般在一般≤20min,可连续运行,也可间断运行。
启动时间短,一般≤30min,可连续运行,也可间断运行。
维护特点
设备结构复杂,加工精度高,维修保养技术难度大,维护保养费用高。
设备结构简单,维护保养技术难度低,维护保养费用较高。
设备结构简单,维护保养技术难度低,维护保养费用低。
土建及安装特点
占地面积大,厂房和基础要求高,工程造价高。
安装周期长,技术难度大,安装费用高。
占地面积小,厂房无特殊要求,造价低。
安装周期短,安装费用低。
占地面积小,厂房无特殊要求,造价低。
安装周期短,安装费用低。
产气成本
0.5~1.0KW.H/Nm3
以RICH膜分离制氮设备单位产气量能耗为例:
单位产98%纯度氮气的电耗为0.29KW.H/Nm3。
以RICH常温变压吸附制氮设备单位产气量能耗为例:
单位产98%纯度氮气的电耗为0.25KW.H/Nm3。
安全性
在超低温、高压环境运行可造成碳氢化合物局部聚集,存在爆炸的可能性。
常温较高压力下操作,不会造成碳氢化合物的局部聚集。
常温常压下操作,不会造成碳氢化合物的局部聚集。
可调性
气体产品产量、纯度不可调,灵活性差
气体产品产量、纯度可调,灵活性较好。
气体产品产量、纯度可调,灵活性好。
经济适用性
气体产品种类多,气体纯度高,适用于大规模制气、用气场合。
投资小、能耗低,适用于氮气纯度79%~99.99的中小规模应用场合。
膜分离制氮能耗在氮气纯度99%以下和变压吸附制氮能耗相差不大,氮气纯度99.5%以上经济性比变压吸附差。
膜分离制氧工艺尚不成熟,一般产氧纯度21%~45%,基本未得到工业应用。
投资小、能耗低,适用于氧气纯度21%~95%、氮气纯度79%~99.9995的中小规模应用场合。
RICH牌节能型变压吸附系列制氮装置经济性优异,特别是氮气纯度99.9%以上的设备更体现了变压吸附空分法的无与伦比的优势。
注:
其他供气方式是基于上述空分制气产业基础上的产业延伸,供气过程产生了中间环节的费用,增加了用气成本,可操作性差,其中运输式和钢瓶式供气存在较大安全隐患。
氮气在各行业中的应用
作者:
兆军
通用变压吸附制氮设备
氮气是空气的主要成分,在室温和大气压力下是无色、无味、无毒和不可燃的气体,沸点为-195.8℃,其化学性质不活泼。
除合成氨外,氮气通常被作为保护气广泛用于冶金、化工、煤炭、食品、医药、电子、磁材、运输、热处理、轮胎、热电、航空等行业。
石油石化行业专用变压吸附氮气设备
化工乃氮气设备应用最大最多的行业,目前运用较多的为:
聚氯乙烯(PVC),纯度99.5%,流量较大。
聚丙烯(PE),纯度99.9%,流量较大,该产品氮气应用分为两部分,一是活化剂、催化剂在装填和排空时需要99.9%的氮气(量小),反应釜用氮气99.5%量大,习惯性取纯度99.9%。
聚乙烯、苯胺,纯度99.95%,石化产品苯胺在催化剂再生时用氮气是平常的4倍左右,但使用周期短。
顺酐及乙醇,一般纯度为99.9%,石化产品聚甲醛(目前国厂家不多,需求强劲),纯度99.9%。
石油:
可应用于系统中管道容器等的氮气吹扫,储罐充氮、置换、检漏,可燃性气体保护,也应用于柴油加氢和催化重整,纯度一般为99.9%。
苯酐:
纯度为99%。
聚酯:
上游原料PTA(精对苯二甲醇),实际使用纯度为95%,一般取99%。
PTA生产工艺中利用高纯氮气吹泡,测量高温和低温反应釜中乙二醇原料的液位,测取高压端和低压端的压差后输送4~20mA标准信号,然后转化为液位高度。
并利用高纯氮气来测量真空系统的压力,以及在PTA生产工艺中利用高纯氮气对过滤器进行反吹冲洗。
聚酯切片一般根据实际工艺不同为99%~99.999%,切片下游产品长丝、短丝,99.9~99.999%。
浮法玻璃:
纯度为99.9995%,无氢。
热处理:
镀锌板分为退火及镀锌工艺,对氮气纯度要求为99.9995%,要求配H25~20%,设备组成相当复杂。
铝材:
一般为99.9995%,要求无氢,否则会有“氢胞”现象。
汽车空调:
基本采用液氮,根据实际情况,采用99.999%,结合碳燃烧法完全可以满足要求。
轮胎充氮变压吸附氮气设备
21世纪轮胎竞争的关键在于技术和价格,而轮胎的价格又与制造工艺和技术息息相关,瑞气PSA制氮设备可以协助您在竞争中赢得先机,并已在上海双钱载重轮胎公司实现了有效的价值提升。
国传统的工艺,钢丝子午线轮胎均使用过热水对轮胎进行定型和硫化没。
所谓过热水硫化,指轮胎的定型使用低压蒸汽,轮胎的正硫化过程中,胶囊(类似模具的作用)充介质为170℃以上高压热水,外温采用低压蒸汽来进行硫化;而充氮硫化是指轮胎的定型使用低压氮气(0.4-0.5MPa),轮胎的正硫化过程中,胶囊充介质为高压蒸汽与高压氮气(2.5MPa)的混合气体,外温采用低压蒸汽来进行硫化,两种方式均是利用高温,将天然橡胶链状的分子结构改变成网状结构,同时将一层层带束层紧密结合起来,并在胎面形成花纹。
氮气硫化,轮胎的性能指标如里程数、耐久性、均匀性、压穿能力试验中,都高于传统过热水硫化的性能指标。
制氮设备购置费用基本一年多时间即可收回全部的投资。
目前国部分轿车用子午线轮胎已经如国外一样广泛采用氮气硫化,如佳通轮胎、玲珑轮胎等,载重子午线轮胎方面,上海双钱轮胎公司是第一家使用,以上厂家均使用瑞气公司生产的氮气设备。
轿车轮胎每条用氮量约:
1.25m3
载重轮胎每条用氮量约:
12m3
一般工厂采用氮气回收节约用氮成本,通常考虑40-50%的氮气回收量。
煤矿专用防灭火氮气设备
注氮防灭火的实质是向采空区氧化带或火区注入一定流量的氮气,使其氧含量降到7%或3%以下,达到防灭火的目的,其作用有消除瓦斯爆炸危险;防止煤的自然发热和自燃;降低燃烧强度,防止密闭漏风。
其作用原理如图示:
针对矿井情况、产煤量、通风、输送距离、瓦斯含量、自燃发火期的不同,瑞气为客户提供KGZD系列地面固定式和JXZD系列井下移动式两种氮气设备。
该系列设备是瑞气空分设备有限公司与煤炭科学研究总院分院联合制造,已取得国家煤矿矿用产品安全标志准用证。
药用变压吸附制氮机
通常易于氧化的水针(青霉素等)和大输液(如氨基酸等)都需要冲氮保护,否则药液在保存期里很容易氧化,亦即变质。
一般是在封装之前,采用前冲氮后冲氮的方式(或单一冲氮),使得安瓿瓶或输液瓶里的氧气浓度降到0.5%以下,药液可长时间保质。
就目前来讲,一般厂家购买的设备大约是5-20m3/h,纯度为99.99%。
药用制氮机与其他氮气设备不同的是因医药行业国际标准GMP标准规定,与药品或药液接触的部分均采用不锈钢材质及除菌方面的要求,设备需要采用不锈钢材质,设备氮气出口部位加装除菌过滤器装置。
也因为药厂对设备的总体要求高,通常会有高端配置。
其他还有原料药制造厂,也需要氮气保护,其用氮工艺更象精细化工厂的用氮方式。
通常纯度为99-99.9%,但视工厂规模不同而用量有区别,但相对药用制氮机的用量要大很多。
象医药股份公司及永宁制药厂用量均为300立方/小时。
食品行业制氮设备
主要应用于食品保鲜、冷藏等方面,瑞气空分设备有限公司专利设计的后净化系统,保证产品气无菌、无尘、无异味,减除了食品厂家使用氮气的后顾之优。
电子磁材行业制氮机
包括分支门类很多,主要有压电晶体、半导体及无铅焊接等。
国变压吸附制氮技术概述
作者:
兆军
1前言
采用变压吸附技术从空气中提取氮气,在中小规模用户已经广泛普及。
在2000Nm3/H能力围,比深冷更具吸引力,已经成为氮气市场的主流,它不但生产过程简单维护操作方便,产品纯度在一定围可以任意调节,而且规模从几十到上千方规模可以任意选用。
2工艺介绍
以空气为原料,变压吸附制氮技术是在常温下利用O2和N2在吸附剂上的吸附速率的差异或吸附容量不同,采用在高压下吸附,低压下解吸原理来制备的。
根据不同性能的吸附剂,制氮的机理也不相同。
目前变压吸附制氮采用碳分子筛(CMS)和沸石分子筛(MS)两种技术。
1)碳分子筛制氮(CMS)是利用碳分子筛对O2和N2吸附速率不同的原理来分离N2的。
碳分子筛是一种非极性速度分离型吸附剂,通常以煤为原料,以纸或焦油为粘结剂加工而成。
它之所以能对氧氮分离主要是基于氧气和氮气在碳分子筛上的扩散速率不同(35℃时扩散速率,O2为6.2×10-5,N2为2.0×10-6),氧气在碳分子筛上的扩散速度大于氮气的扩散速度,使得碳分子筛优先吸附氧气,而氮气富集于不吸附相中,从而在吸附塔流出得到产品氮气。
碳分子筛制氮一般采用2个吸附塔,原料压缩空气经过冷干机除去气体中的水分和微量油进入床层,O2等杂质迅速吸附在床层上,N2得以分离在吸附塔出口得到,吸附结束后经过均压和真空解吸或者常压解吸,使吸附剂的杂质组分脱除再生,2个塔循环交替吸附再生。
真空解吸或者常压解吸再生的目的是为了往复利用吸附剂。
真空法较常压法能耗高,但产品气纯度高。
实际中这两种解吸方法都在应用,不过为了降低能耗,真空解吸方式逐渐减少。
碳分子筛技术能得到普氮,纯度小于99.99%时相对经济。
2)沸石分子筛制氮(MS)是利用沸石分子筛对O2和N2吸附容量不同的原理来分离N2的。
沸石分子筛是人工合成的硅铝酸盐晶体,加热到一定程度失去结晶水得到的,它由离子孔穴和带负电荷的硅铝骨格所结构。
它之所以能对氧氮分离主要是基于非极性的O2和N2受到极性分子的影响产生偶极,而O2和N2分子的诱导偶极与吸附剂固有的极性偶极具有吸附作用,在等温条件下分子筛吸附N2量大于O2,从而在吸附相解吸得到N2产品气,产品气压力低,使用时需要在加压故能耗较高。
MS制氮,原料压缩空气经过干燥器严格脱除水分和CO2,然后再进入MS分子筛床层,N2迅速吸附在床层上,O2等杂质作为吸附废气排空,吸附结束后经过真空解吸,得到产品N2。
沸石分子筛制氮对原料要求严格,需要流程较为复杂投资和操作费用增加。
制氮方法
能耗KWh/Nm3
碳分子筛
0.35
沸石分子筛
0.5-0.6
低温法
0.25
3装置评价技术分析
评价一套变压吸附装置的优劣,一般从产品纯度、生产能力、回收率能耗等指标衡定。
产品纯度和生产能力是装置设计目的,在一般情况下均可达到,而回收率和能耗往往被忽视。
回收率也是能耗的一部分,收率低消耗的原料气也就越多,能耗也就增加。
能耗一般指用于原料气或产品气生压和真空解吸所消耗的电能。
从运行装置来看,一般氮气回收率在45-60%之间,单位能耗0.35KWh/Nm3左右。
一般真空解吸流程能耗高于常压解吸流程。
流程合理吸附剂性能高的装置,回收率高能耗低。
以99.5%纯度氮气装置为例。
N2纯度
消耗
流程及投资
装置能力
碳分子筛
98.5-99.9%
低
少
大
沸石分子筛
99.9-99.99%
高
大
小
加氢脱氧技术
99.99%以上
较高
大
小
影响装置性能的因素有吸附压力和吸附时间。
经验表明,提高吸附压力可以增大碳分子筛的吸附容量,提高氮气纯度,但压力达到0.6Mpa时床层死空间等因素反而导致纯度降低能耗增高。
吸附时间越长,产品纯度越低,但回收率高,气流切换次数少碳分子筛粉化程度轻。
氮气的产量和纯度是一对对立的因素,氮气出气量越高,纯度越低回收率越低,反之亦然。
4技术发展和展望
变压吸附制氮技术的发展主要是吸附剂技术的发展。
1977年德国埃森矿业研究有限公司BergauForschung(B.F公司)研制开发了碳分子筛制氮技术以来,日本美国等都迅速发展起来。
1981年化公设计研究院研制的碳分子筛通过了省级鉴定,随后中国船舶工业总公司也研制开发了碳分子筛。
1986年长兴化工厂采用上海化工研究院技术生产的碳分子筛成为国主要碳分子筛生产力量。
国外大批量生产碳分子筛的有德国BF公司、美国Calgon碳公司、日本Takeda化学工业公司和Kuraray化学品公司。
国上海化工设计院、天一科技、瑞气空分设备有限公司等企业生产氮气装置规模和技术水平发展速度很快,接近世界先进水平。
通过对不同的分子筛比较,国碳分子筛的产氮率还远低于国外产品,主要原因是国产碳分子筛比表面积仅是BF公司的55%,微孔不够发达。
造成此状况的原因是没有完全掌握制作工艺条件和原料配比,检测设备落后无法及时监控生产,原料煤杂质高等。
近年来国碳分子筛也有了长足进步,以长兴化工厂的碳分子筛