加热炉工艺技术操作作规程.docx
《加热炉工艺技术操作作规程.docx》由会员分享,可在线阅读,更多相关《加热炉工艺技术操作作规程.docx(20页珍藏版)》请在冰豆网上搜索。
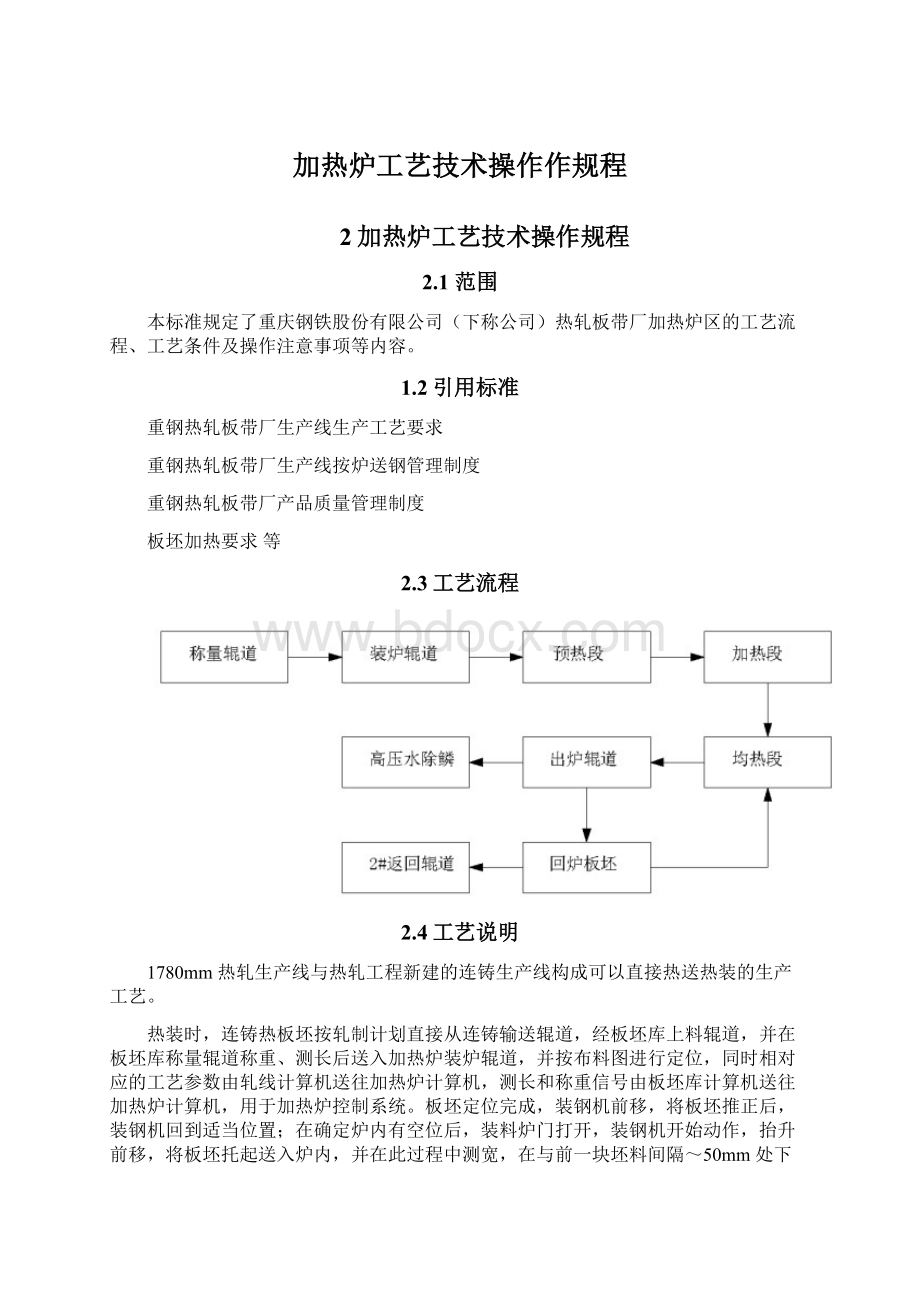
加热炉工艺技术操作作规程
2加热炉工艺技术操作规程
2.1范围
本标准规定了重庆钢铁股份有限公司(下称公司)热轧板带厂加热炉区的工艺流程、工艺条件及操作注意事项等内容。
1.2引用标准
重钢热轧板带厂生产线生产工艺要求
重钢热轧板带厂生产线按炉送钢管理制度
重钢热轧板带厂产品质量管理制度
板坯加热要求等
2.3工艺流程
2.4工艺说明
1780mm热轧生产线与热轧工程新建的连铸生产线构成可以直接热送热装的生产工艺。
热装时,连铸热板坯按轧制计划直接从连铸输送辊道,经板坯库上料辊道,并在板坯库称量辊道称重、测长后送入加热炉装炉辊道,并按布料图进行定位,同时相对应的工艺参数由轧线计算机送往加热炉计算机,测长和称重信号由板坯库计算机送往加热炉计算机,用于加热炉控制系统。
板坯定位完成,装钢机前移,将板坯推正后,装钢机回到适当位置;在确定炉内有空位后,装料炉门打开,装钢机开始动作,抬升前移,将板坯托起送入炉内,并在此过程中测宽,在与前一块坯料间隔~50mm处下降放钢,板坯停稳后,装钢机快速退回原位,准备重复送钢动作;同时装料炉门关闭。
冷/热装料时,连铸冷/热板坯按轧制计划被吊到板坯上料辊道上,在板坯库上料辊道称重、测长后送入加热炉装炉辊道,并按布料图进行定位,同时其对应的工艺参数由轧线计算机送往加热炉计算机,测长和称重信号由板坯库计算机送往加热炉计算机,用于加热炉控制系统。
板坯定位完成,装钢机前移,将板坯推正后,装钢机回位;再按上述步骤将板坯装入炉内。
装入炉内的板坯通过步进梁的运动从入炉端运送到出炉端。
步进梁的运动周期是一个矩形运动轨迹。
步进梁运动由水平运动和垂直运动组成。
水平运动和垂直运动过程中的速度是变化的,其目的在于保证运动的开始和结束时动作缓和,防止步进机构产生冲击和震动。
步进机构的水平运动是:
通过平移液压缸驱动平移框架,使其在提升框架的滚轮上作平移运动。
此时,提升缸处于静止状态。
步进机构的升降运动是:
提升缸驱动提升框架,使其滚轮沿斜台面滚动,完成升降运动。
此时,平移缸处于静止状态。
当板坯较长时间停在炉内时,要求步进梁停在中位或进行踏步以避免板坯变形弯曲和黑印加重。
正常生产时步进梁停在低位,为减少板坯加热过程中变形步进梁可停在中位。
板坯到达出料端时,被出料激光检测装置检测到后,步进梁继续向前走完最后一个步距后停止,此时板坯被加热到轧制要求温度,在接到轧线要钢信号后,出料炉门打开,出钢机开始动作,从板坯下位运行进入炉内,根据板坯位置定位,托起板坯出炉,将板坯托放在出料辊道上,出料炉门关闭。
板坯由出料辊道送至高压水除鳞装置去除板坯上下表面的氧化铁皮,然后进入轧机进行轧制。
对回炉板坯有以下两种处理方式:
(1)直接由炉前出料辊道送往返回坯辊道上,由车间吊车吊到板坯库等待处理。
(2)由出钢机送回炉内继续均热,等待轧机要钢指令。
2.4.1加热技术要求
2.4.1.1加热过程中严格执行“三勤”操作,即勤观察、勤调整、勤联系。
2.4.1.2严格执行加热温度制度、停轧降温制度。
根据轧制节奏需要,合理控制各段炉温,保证开轧温度和断面温差,避免过热、过烧。
2.4.1.3合理控制炉内气氛,空气过剩系数控制在1.05~1.1之间,采用微正压加热,炉内控制在10~40Pa之间。
2.4.1.4合理调节各冷却部件的冷却水量,确保各冷却回路循环正常。
步进梁出口水温低于50℃,其它冷却部件出口水温低于55℃。
2.4.1.5考虑煤气预热器寿命和安全要求,当煤气预热器前烟气温度超过600℃时发出报警信号,同时稀释风机自动向烟道内掺入冷风,以保护煤气预热器。
2.4.1.6正常燃烧和安全要求,煤气压力为4000~8000Pa。
当煤气压力低于4000Pa时,关闭部分烧嘴,减少煤气用量;当煤气压力低于3000Pa时,关闭烧嘴熄火停炉。
2.4.1.7突发停水、停电、停助燃空气、煤气低压等有可能危机设备、人身安全时,紧急停炉。
2.4.2加热温度制度
2.4.2.1板坯加热温度制度见表3.。
正常节奏生产(参考节奏120s)时,板坯加热温度按中限控制。
表3板坯加热温度制度
钢种
代表钢种
板坯温度,℃
板坯温差,℃
碳素结构钢
Q215~235
1190~1250
≦20
优质碳素结构钢
08F、08~25
1190~1250
≦20
低合金高强度结构钢
Q345B
1170~1250
≦20
管线钢
X42~70(80)
1170~1240
≦20
注:
1.板坯出炉温度与目标温度偏差:
±10℃
2.板坯水印温差小于20℃。
沿板坯各向温差:
≤20℃
2.4.2.2炉温控制要求见表4。
出钢节奏小于120s,炉温按中限控制;出钢节奏大于120s,加热段炉温按下限控制;停轧后或出现保温开轧时,均热段炉温按下限控制。
表4炉温控制要求
钢种
代表钢种
均热段炉温℃
加热段炉温℃
预热段炉温℃
轧制节奏S
碳素结构钢
Q215~235
1220~1280
1250~1300
1100~1220
120
优质碳素结构钢
08F、08~25
1220~1280
1250~1300
1100~1220
120
低合金高强度结构钢
Q345B
1200~1270
1230~1290
1000~1180
120
管线钢
X42~70(80)
1200~1260
1230~1280
1000~1170
120
注:
表中炉温允许瞬间时(≦5min)超上限波动20℃。
2.4.3停轧降温制度
2.4.3.1因故停轧15min以上按表5降低炉温。
表5加热炉停轧降温制度
停轧时间,min
均热段炉温,℃
加热段炉温,℃
15~30
—20~50
—50~80
>30~60
—50~80
—50~80
>60~120
—100~120
—80~100
>120~180
900℃以下保温
900℃以下保温
>180
800℃以下保温
800℃以下保温
注:
1.停轧时间以调度室通知为准,调度室要准确确定停轧时间。
2.降温时以表5中的下限为起点。
2.4.3.2重新开轧前15~20min启动步进梁踏步功能,以消除水梁黑印。
2.4.3.3当炉温降到950℃以下,重新开轧时,炉温升到规定的炉温,在此温度下保温5~15min。
2.4.4烘炉制度
2.4.4.1因故停炉,炉温降到600℃以下(含大中修),重新开炉时必须烘炉。
2.4.4.2烘炉严格按照以下烘炉曲线进行。
图2加热炉烘炉曲线
2.4.5出钢技术要求
2.4.5.1按规定加热到工艺要求温度的板坯方可出炉。
2.4.5.2在精轧操作台要求送钢的情况下方可出钢,且出钢机一次只取一支钢坯。
2.4.5.3合理控制出钢节奏,保持均衡生产。
不得出现轧件头尾相接和出炉待轧的现象。
2.4.5.4不得向轧线送低温钢、黑印钢等不合加热要求的板坯。
2.4.5.5出现过热、过烧的板坯,不得送往轧线,一律进行技术处理或报废。
2.4.5.6出钢机与炉门要协调好,不得出钢后不关炉门或敞开炉门连续出钢。
2.4.5.7回炉钢做好炉号记录和堆放位置确认,交接班时未跟队的回炉坯,逐支标识炉号和钢号,下班次及时跟队生产。
(由谭欧补充)
2.5主要设备及性能参数
2.4.6.1步进梁及运动机构
运动机构形式:
采用液压传动和滚轮斜台面机构,两层框架(升降框架和水平框架)。
平移行程:
550mm
升降高度:
200mm
步进周期:
50s
提升框架:
1段
提升滚轮:
16-800
平移滚轮:
16-800
斜台面倾角:
11.5°
平移导向轮:
6-400mm
提升导向轮:
6-450mm
平移液压缸:
1-250/160×650mm
提升液压缸:
4-250/160×1150mm
2.4.6.2加热炉
炉型:
端进端出步进梁式连续加热炉,节能型,6段自动控制
额定生产能力:
270(额定);300(碳钢、最大)
加热钢种:
低碳结构钢、结构用钢、汽车结构钢、船用钢、锅炉及压力容器
用钢、集装箱及车厢用钢、焊接气瓶钢、高耐候结构钢、管线钢
(X80)、冷轧深冲钢等
坯料尺寸:
44×11.7m
坯料尺寸:
厚230(70%)、190(30%)
宽850~1650
长9000~11000(单)、4500~5300(双)
加热温度:
1150~1250℃
燃料及热值:
混合煤气7524kJ/m3
额定燃耗:
混合煤气55000Nm3/h
空气预热形式及预热温度:
蓄热式,预热温度1050~1150℃
2.4.6.3助燃风机
型式:
每座加热炉配置2台离心通风机,考虑2座炉共4台助燃风机并联在一起
每台风机的性能、规格如下:
风量:
73500Nm3/h
风机出口静压:
11000Pa
转数:
1450r/min
电机:
10KV,50Hz,410kW,1450r/min
风机数量:
2台/炉
消声器:
2台/炉,安装在风机进风口
2.4.6.4稀释风机
每炉设2台稀释风机,当煤气预热器前烟气温度超过600℃时发出报警信号,同时稀释风机自动向烟道内掺入冷风,以保护煤气预热器。
稀释风机入口带百页窗调节阀,通过该调节阀来调节稀释风的风量,稀释风机的技术参数如下:
数量:
2台/炉
风量:
29344m3/h
全压:
1800Pa
电机:
380V
功率:
18.5KW
2.4.6.5燃烧器
烧嘴型式及供热能力见表6。
表6加热炉烧嘴型式及能力配置
供热段
供热方式
烧嘴数量
烧嘴实际
能力(Nm3/h)
段最大供热
能力(Nm3/h)
上均热段
侧向低NOx蓄热烧嘴
2×5
10
1300
6500
下均热段
侧向低NOx蓄热烧嘴
2×5
10
1300
6500
上加热段
侧向低NOx蓄热烧嘴
2×6
12
2150
12900
下加热段
侧向低NOx蓄热烧嘴
2×6
12
2150
12900
上预热段
侧向低NOx蓄热烧嘴
2×4
8
2150
8600
下预热段
侧向低NOx蓄热烧嘴
2×4
8
2150
8600
2.4.6.6装料炉门提升装置
提升型式:
液压传动
提升能力:
10.5t×2
升降行程:
1900mm
升降速度:
0.2m/s
液压缸:
Φ140/Φ100×1900mm2只/炉
工作压力:
17MPa
链条型式:
重载传动滚子链
2.4.6.7出料炉门提升装置
提升型式:
液压传动
提升能力:
12.5t×2
升降行程:
1900mm
升降速度:
0.2m/s
液压缸:
Φ140/Φ100×1900mm2只/炉
工作压力:
17MPa
链条型式:
重载传动滚子链
(由谭欧补充)
2.6操作规程
2.6.1点火前准备操作规程
1.1.1操作前确认
1)启车前必须打铃警示确认设备所属区域无人和障碍物
2)确认急停打开,设备运转正常;
3)确认工业电视、对讲机、电话正常;
4)确认具备出钢条件:
步进梁、炉门、出钢机在原点;
5)确认设备的停车位置正常;
1.1.2操作前准备
1)将操作台上各操作手柄打至“零”位;
2)检查各液压系统正常;
3)检查相应的指示灯显示正确;
4)检查机械设备处于待运转状态。
1.1.3装出料炉门试运转操作步骤
装出料炉门模式选为手动,确认上升、下降正常,极限位置正确;
1.1.4烟道闸板调整操作步骤
1)L1画面上分别选择烟道闸板单动、联动、手动及自动控制;
2)现场确认挡板转动方向及开度与监控画面显示一致。
1.1.5入口百叶窗、出口蝶阀操作步骤
a)L1画面选择助燃风机、稀释风机入口百叶窗、出口蝶阀自动、手动方式,调整其开度;
b)现场确认入口百叶窗开度、出口蝶阀状态与监控画面显示一致。
1.1.6燃烧自动调节装置的调整操作步骤
a)画面选择快速切断阀、压力调节阀、各段流量调节阀、热风放散阀、脉冲阀等进行调节;
b)现场确认各调节阀动作灵活,开度或状态与监控画面显示一致。
1.1.7步进梁投用操作步骤
a)L1画面上对步进梁模式进行选择;
b)确认步进梁运行轨迹及周期与设计相符:
运行周期50秒;
前进、后退行程550mm;
上升、下降行程200mm。
1.1.8空气、氮气压力检查操作步骤
检查仪表用压缩空气、吹扫用氮气压力显示:
:
仪表空气压力0.5Mpa;
氮气压力无报警0.2至0.3MPa。
1.1.9冷却装置检查
1)检查冷却水压力是否正常,其中净环水压力0.35MPa,浊环水压力0.2至0.25MPa;
2)检查步进梁、水封槽、装出料炉门、装出钢机等冷却件是否已通水,确认排水温度不大于48℃;
3)检查阀门是否开闭灵活,有无漏水现象;
4)检查汽化冷却系统是否正常投入。
7.2.1.10杂物清理操作步骤
5)检查炉内、水封槽内、烟道内杂物已清理完毕;
6)确认炉内镁砂铺设完毕;
7)确认检修人孔、小炉门均已关严。
2.6.2加热炉送煤气操作规程
1.2.1操作前确认
1)启车前必须打铃警示确认设备所属区域无人和障碍物
2)确认急停打开,设备运转正常;
3)确认工业电视、对讲机、电话正常;
4)确认各调节阀门、炉门处于规定状态;
5)确认具备出钢条件:
步进梁、炉门、出钢机在原点。
6)确认送煤气前风机已正常运转2至4小时以上
1.2.2操作前准备
1)联系主作业长、煤气调度及煤气防护站,准备送煤气。
2)CO检测仪、劳保防护用品等佩戴齐全。
1.2.3操作步骤
1)关闭两道φxxxmm煤气手动蝶阀、紧急切断阀、电动盲板、压力调节阀。
开闭盲板前,应对煤气主管进行放水作业;操作盲板开闭时,必须用手动模式,先点动再连动,同时注意站位;
2)确认各段煤气流量调节阀手动全开、1,2号炉1至6段烧嘴前煤气手动蝶阀全关;
3)全开1至6段烧嘴前煤气手动蝶阀;
4)关闭点火烧嘴前球阀;
5)全开装出料炉门及烟道挡板。
1.2.4电动盲板间氮气吹扫操作步骤
1)打开第二道φxxxmm煤气手动蝶阀与电动盲板之间的放散阀及第二道φxxxmm煤气手动蝶阀、紧急切断阀;
2)打开φxxxmm氮气总阀和φxxxmm氮气吹入阀,吹扫10分钟;
3)关闭φxxxmm氮气吹入阀及第二道φxxxxmm煤气手动蝶阀与电动盲板之间的放散阀;
4)打开电动盲板。
1.2.5烧嘴前氮气吹扫操作步骤
1)打开压力调节阀、各段烧嘴前放散阀;
2)打开1,2号炉1---6段点火烧嘴段总放散;
3)打开φxxmm氮气吹入阀,吹扫20分钟;
4)关闭φxxmm氮气吹入阀和φxxxmm氮气总阀。
1.2.6送煤气操作步骤
1)打开第一道φxxxmm煤气手动蝶阀,送煤气到烧嘴前;
2)各取样阀处取样做爆发试验,合格后关闭所有放散阀.
1.2.7检查确认操作步骤
用CO检测仪检查确认各阀门、盲板、管道等无煤气泄漏。
2.6.3烧嘴点火操作规程
1.3.1操作前确认
1)启车前必须打铃警示确认设备所属区域无人和障碍物
2)确认急停打开,设备运转正常;
3)确认工业电视、对讲机、电话正常;
4)确认具备出钢条件:
步进梁、炉门、出钢机在原点;
5)确认设备的停车位置正常;
1.3.2操作前准备
1)将操作台上各操作手柄打至“零”位;
1)确认煤气压力、燃烧用空气压力、仪表用空气压力正常;
3)确认冷却水投入正常,汽化冷却系统正常;
4)检查各液压系统正常;
5)检查相应的指示灯显示正确;
6)检查机械设备处于待运转状态。
1.3.4操作步骤
1)步进梁试运转完毕;
2)确认送煤气及送风作业完成;
3)装、出料炉门及烟道挡板全开;
4)1至6段烧嘴处于手动状态。
1.3.5二、四、六段烧嘴点火操作步骤
(以六段为例)
1)在画面上手动将六段空、煤气流量调节阀开至30%;
2)全关准备点火的烧嘴前空气手动蝶阀;
3)点着煤气点火枪插入点火孔;
4)缓缓打开烧嘴前煤气手动蝶阀,并确认烧嘴点火成功;
5)缓缓打开烧嘴前空气手动蝶阀至合适位置;
6)调整烟道挡板;
7)待火焰稳定后进行空、煤气流量的控制调节;
8)全关装、出料炉门。
1.3.6一、三、五段烧嘴点火操作步骤
(以五段为例)
1)在画面上手动将空、煤气流量调节阀打开至30%;
2)全开该段烧嘴前空气手动蝶阀;
3)全开该段烧嘴前煤气手动蝶阀;
4)调整煤气流量。
1.3.7确认各段烧嘴点火成功;炉温在800℃以上,可以直接点火不需点火烧嘴。
2.6.4降温、熄火、停煤气操作规程
1.4.1操作前确认
1)启车前必须打铃警示确认设备所属区域无人和障碍物
2)确认急停打开,设备运转正常;
3)确认工业电视、对讲机、电话正常;
4)确认具备出钢条件:
步进梁、炉门、出钢机在原点;
1.4.2操作前准备
1)停止装钢作业完成;
2)最后一块板坯离开预热段,预热段。
1.4.3降温熄火操作步骤
1)依次逐步减少预热段、加热段各烧嘴负荷输入值,从而减少煤气流量和烧嘴个数直至全段熄火;
1)严格按照主烧嘴熄火顺序进行熄火(1段-2段-3段-4段-5段-6段);
2)降温熄火只剩下6段烧嘴且炉温降至450℃以下时才能全炉熄火;
3)脉冲烧嘴熄火后,现场将烧嘴前空、煤气手动蝶阀关闭,并确认;
4)逐步减少均热段5段煤气流量和烧嘴个数,直至全段熄火;
5)等待炉温降至450℃以下时,逐步减少均热段6段煤气流量和烧嘴个数,直至全段熄火;
6)注意降温熄火过程中煤气和空气流量的变化。
1.4.4氮气吹扫放散操作步骤
1)快速切断阀,各段煤气流量调节阀转现场手动全开
2)关闭第一道和第二道Ф1000煤气手动蝶阀;
3):
压力调节阀、烧嘴前放散阀全开、1,2炉1---6段烧嘴前煤气手动蝶阀、点火段总放散全开,其余段煤气手动蝶阀全关,电动盲板前放散阀全开,软管连接要牢固,防止崩开伤人;
4)打开Ф150氮气总阀和Ф50氮气阀,吹扫10分钟;
5)开闭盲板前,先对加热炉煤气主管进行放水,然后点动关闭电动盲板,、打开第二道Ф1000煤气手动蝶阀;
6)打开Ф32氮气阀分两段进行吹扫作业直至煤气防护站采样化验合格;
7)煤气采样化验合格后关闭Ф32氮气阀和Ф150氮气总阀;
8)吹扫完毕后脱开软管
1.4.5停助燃风机操作步骤
1)全炉熄火后,炉温降至400℃以下,停助燃风机;
2)在L1画面上将风机百叶窗关闭;
3)在L1画面上或现场将风机出口蝶阀全关到位;
4)在L1画面上或现场将风机关闭;
5)现场观察风机运转状况。
1.4.6开装出料炉门操作步骤
炉温降至200℃以下时,全开装、出料炉门
1.4.7进炉检查操作步骤
确认炉温降至100℃以下,方可进炉检查作业
2.6.5风机启动操作规程
1.5.1操作前确认
1)启车前必须打铃警示确认设备所属区域无人和障碍物
2)确认急停打开,设备运转正常;
3)确认工业电视、对讲机、电话正常;
4)确认具备出钢条件:
步进梁、炉门、出钢机在原点
1.5.2操作前准备
1)将操作台上各操作手柄打至“零”位;
2)与燃烧有关的仪表投入;
3)联络电气、机动及自动化等相关人员到现场确认相关项目;
4)检查各液压系统正常;
5)检查相应的指示灯显示正确;
6)检查机械设备处于待运转状态。
1.5.3操作步骤
1)全开装、出料炉门及烟道挡板;
2)手动全开热风放散阀;
3)关闭风机入口百叶窗及出口气动阀门;
4)现场确认人员通知抽钢台操作人员启动风机,启动前通知有关人员撤离风机周围;
5)在风机监控画面上点击风机示意图,在弹出的对话框中点击“启动”按钮;
6)在L1画面上将风机百叶窗开至50%以上;
7)将风机出口蝶阀全开到位;
8)现场观察风机运转状况;
9)相关人员确认风机电流及定子、轴承温度在要求范围之内
2.6.6启车操作规程
1.6.1操作前确认
1)启车前必须打铃警示确认设备所属区域无人和障碍物
2)确认急停打开,设备运转正常;
3)确认工业电视、对讲机、电话正常;
4)确认具备出钢条件:
步进梁、炉门、出钢机在原点
7.2.6.2操作前准备
1)将操作台上各操作手柄打至“零”位;
2)将出钢机、出料炉门操作模式设为“手动”;
3)检查各液压系统正常;
4)检查相应的指示灯显示正确;
5)检查机械设备处于待运转状态;
6)严格按停送电制度通知电气对相关设备送电;
7)检查辊道各CMD投入正常;
8)检查热装时辊道冷却水投入正常。
1.6.2出料炉门启车操作步骤
1)配合机电人员现场确认,启车前打铃警示;
2)依次进行出料炉门半开、全开、全关操作;
3)现场确认设备同步到位,如不同步联系相关人员处理,处理时严禁动作设备
4)出料炉门退回至原点位置。
1.6.3步进梁启车操作步骤
1)配合机电人员现场确认,启车前打铃警示;
2)操作步进梁操作手柄,依次完成步进梁上升、前进、下降、后退;
3)现场确认设备同步到位,如不同步联系相关人员处理,处理时严禁动作设备;
4)步进梁退回至原点位置。
1.6.4出钢机启车操作步骤
1)配合机电人员现场确认,启车前打铃警示;
2)确认出钢机在原点位置、装料炉门开至全开位置;
3)出钢机分别以一档、二档速度进行平移和升降操作(先点点动,再连动);
4)现场确认设备同步到位,如不同步联系相关人员处理,处理时严禁动作设备;
5)出钢机退回至原点位置、全关出料炉门。
1.6.5辊道启车操作步骤
1)配合机电人员现场确认,启车前打铃警示;
2)辊道装分别以一档、二档速度进行正转和反转(先点动,再连动);
3)现场确认设备是否运行到位,如有异常联系相关人员处理,处理时严禁动作设备
4)停止辊道运转,运行方式切换为自动。
2.6.7半自动出钢操作规程
1.7.1操作前确认
1)长时间(30分钟以上)停车,启车前必须打铃警示;
2)确认急停打开,设备运转正常;
3)确认工业电视、对讲机、电话正常;
4)确认激光检测器接通,板坯定位符合要求;
5)确认L2具备出钢条件后将板坯信息传至L1;
6)确认L1画面显示正确的出钢机行程设定值;
7)确认具备出钢条件:
步进梁、炉门、出钢机在原点。
1.7.2操作前准备
1)将操作台上各操作手柄打至“零”位;
2)将出钢机操作模式设为“半自动”;
3)检查各液压系统正常;
4)检查相应的指示灯显示正确;
5)检查机械设备处于待运转状态。
1.7.3操作步骤
1)L1画面单击出钢机,输入正确的板坯宽度;
2)单击“半自动启动”启动抽钢,出现异常拍下快停,防止引发设备事故;
3)确认L1、L2画面数据出炉;
4)确认设备动作完成:
出钢机及出料炉门恢复到原点。
2.6.8手动出钢操作规程
1.8.1操作前确认
1)确认急停打开,设备运转正常;
2)确认工业电视、对讲机、电话正常;
3)确认激光检测器接通,板坯定位符合要求;
4)确认L2具备出钢条件