机械加工工艺分析.docx
《机械加工工艺分析.docx》由会员分享,可在线阅读,更多相关《机械加工工艺分析.docx(17页珍藏版)》请在冰豆网上搜索。
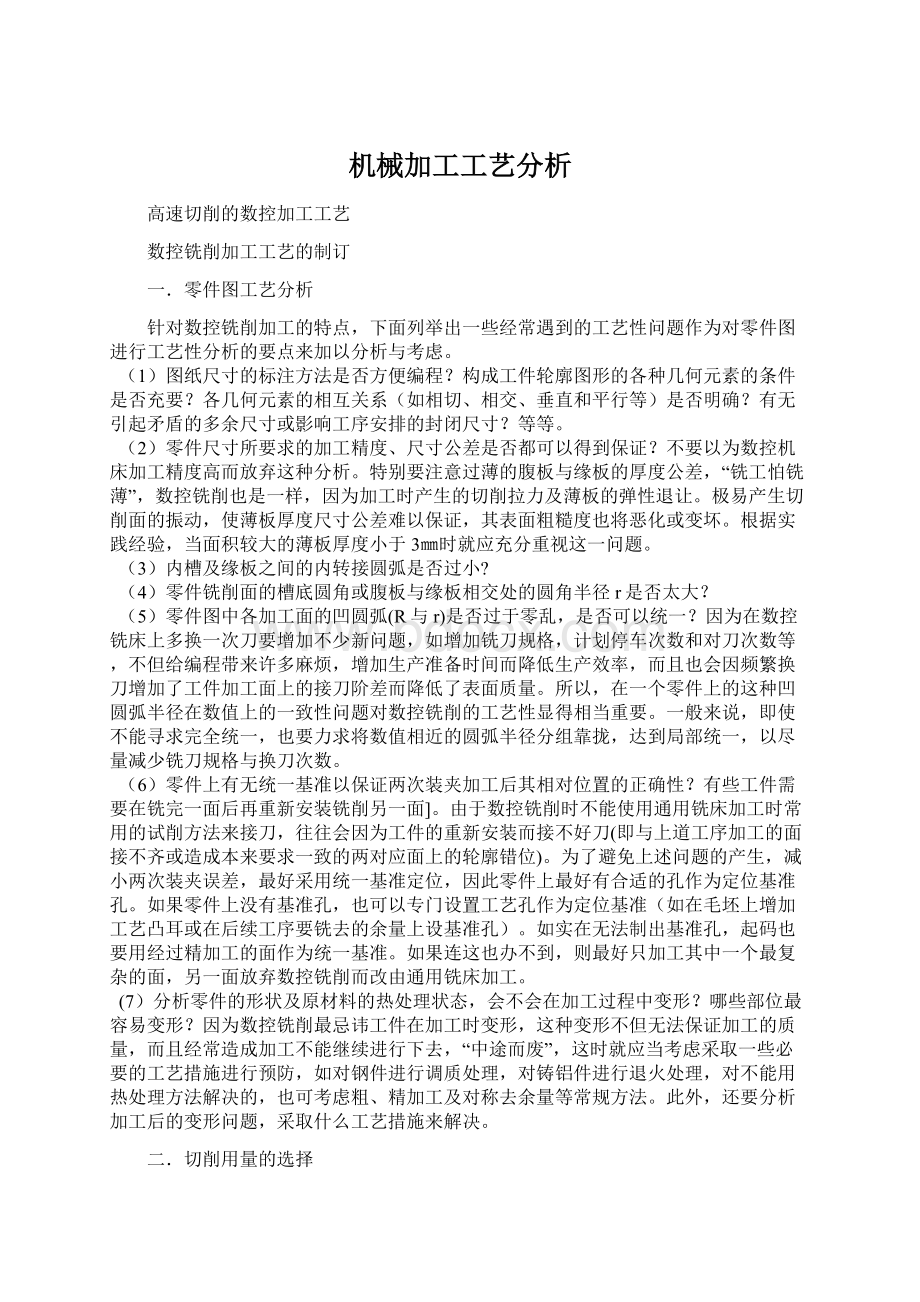
机械加工工艺分析
高速切削的数控加工工艺
数控铣削加工工艺的制订
一.零件图工艺分析
针对数控铣削加工的特点,下面列举出一些经常遇到的工艺性问题作为对零件图进行工艺性分析的要点来加以分析与考虑。
(1)图纸尺寸的标注方法是否方便编程?
构成工件轮廓图形的各种几何元素的条件是否充要?
各几何元素的相互关系(如相切、相交、垂直和平行等)是否明确?
有无引起矛盾的多余尺寸或影响工序安排的封闭尺寸?
等等。
(2)零件尺寸所要求的加工精度、尺寸公差是否都可以得到保证?
不要以为数控机床加工精度高而放弃这种分析。
特别要注意过薄的腹板与缘板的厚度公差,“铣工怕铣薄”,数控铣削也是一样,因为加工时产生的切削拉力及薄板的弹性退让。
极易产生切削面的振动,使薄板厚度尺寸公差难以保证,其表面粗糙度也将恶化或变坏。
根据实践经验,当面积较大的薄板厚度小于3㎜时就应充分重视这一问题。
(3)内槽及缘板之间的内转接圆弧是否过小?
(4)零件铣削面的槽底圆角或腹板与缘板相交处的圆角半径r是否太大?
(5)零件图中各加工面的凹圆弧(R与r)是否过于零乱,是否可以统一?
因为在数控铣床上多换一次刀要增加不少新问题,如增加铣刀规格,计划停车次数和对刀次数等,不但给编程带来许多麻烦,增加生产准备时间而降低生产效率,而且也会因频繁换刀增加了工件加工面上的接刀阶差而降低了表面质量。
所以,在一个零件上的这种凹圆弧半径在数值上的一致性问题对数控铣削的工艺性显得相当重要。
一般来说,即使不能寻求完全统一,也要力求将数值相近的圆弧半径分组靠拢,达到局部统一,以尽量减少铣刀规格与换刀次数。
(6)零件上有无统一基准以保证两次装夹加工后其相对位置的正确性?
有些工件需要在铣完一面后再重新安装铣削另一面]。
由于数控铣削时不能使用通用铣床加工时常用的试削方法来接刀,往往会因为工件的重新安装而接不好刀(即与上道工序加工的面接不齐或造成本来要求一致的两对应面上的轮廓错位)。
为了避免上述问题的产生,减小两次装夹误差,最好采用统一基准定位,因此零件上最好有合适的孔作为定位基准孔。
如果零件上没有基准孔,也可以专门设置工艺孔作为定位基准(如在毛坯上增加工艺凸耳或在后续工序要铣去的余量上设基准孔)。
如实在无法制出基准孔,起码也要用经过精加工的面作为统一基准。
如果连这也办不到,则最好只加工其中一个最复杂的面,另一面放弃数控铣削而改由通用铣床加工。
(7)分析零件的形状及原材料的热处理状态,会不会在加工过程中变形?
哪些部位最容易变形?
因为数控铣削最忌讳工件在加工时变形,这种变形不但无法保证加工的质量,而且经常造成加工不能继续进行下去,“中途而废”,这时就应当考虑采取一些必要的工艺措施进行预防,如对钢件进行调质处理,对铸铝件进行退火处理,对不能用热处理方法解决的,也可考虑粗、精加工及对称去余量等常规方法。
此外,还要分析加工后的变形问题,采取什么工艺措施来解决。
二.切削用量的选择
影响切削用量的因素有:
机床 切削用量的选择必须在机床主传动功率、进给传动功率以及主轴转速范围、进给速度范围之内。
机床—刀具—工件系统的刚性是限制切削用量的重要因素。
切削用量的选择应使机床—刀具—工件系统不发生较大的“振颤”。
如果机床的热稳定性好,热变形小,可适当加大切削用量。
表1-1常用刀具材料的性能比较
刀具材料
切削速度
耐磨性
硬度
硬度随温度变化
高速钢
最低
最差
最低
最大
硬质合金
低
差
低
大
陶瓷刀片
中
中
中
中
金刚石
高
好
高
小
刀具 刀具材料是影响切削用量的重要因素。
表1-1是常用刀具材料的性能比较。
数控机床所用的刀具多采用可转位刀片(机夹刀片)并具有一定的寿命。
机夹刀片的材料和形状尺寸必须与程序中的切削速度和进给量相适应并存入刀具参数中去。
工件不同的工件材料要采用与之适应的刀具材料、刀片类型,要注意到可切削性。
可切削性良好的标志是,在高速切削下有效地形成切屑,同时具有较小的刀具磨损和较好的表面加工质量。
较高的切削速度、较小的背吃刀量和进给量,可以获得较好的表面粗糙度。
合理的恒切削速度、较小的背吃刀量和进给量可以得到较高的加工精度。
冷却液冷却液同时具有冷却和润滑作用。
带走切削过程产生的切削热,降低工件、刀具、夹具和机床的温升,减少刀具与工件的摩擦和磨损,提高刀具寿命和工件表面加工质量。
使用冷却液后,通常可以提高切削用量。
冷却液必须定期更换,以防因其老化而腐蚀机床导轨或其他零件,特别是水溶性冷却液。
铣削加工的切削用量包括:
切削速度、进给速度、背吃刀量和侧吃刀量。
从刀具耐用度出发,切削用量的选择方法是:
先选择背吃刀量或侧吃刀量,其次选择进给速度,最后确定切削速度。
1.背吃刀量ap或侧吃刀量ae
背吃刀量ap为平行于铣刀轴线测量的切削层尺寸,单位为㎜。
端铣时,ap为切削层深度;而圆周铣削时,为被加工表面的宽度。
侧吃刀量ae为垂直于铣刀轴线测量的切削层尺寸,单位为㎜。
端铣时,ae为被加工表面宽度;而圆周铣削时,ae为切削层深度,见图1-1。
背吃刀量或侧吃刀量的选取主要由加工余量和对表面质量的要求决定:
∙当工件表面粗糙度值要求为Ra=12.5~25μm时,如果圆周铣削加工余量小于5㎜,端面铣削加工余量小于6㎜,粗铣一次进给就可以达到要求。
但是在余量较大,工艺系统刚性较差或机床动力不足时,可分为两次进给完成。
图1-1铣削加工的切削用量
∙当工件表面粗糙度值要求为Ra=3.2~12.5μm时,应分为粗铣和半精铣两步进行。
粗铣时背吃刀量或侧吃刀量选取同前。
粗铣后留0.5~1.0㎜余量,在半精铣时切除。
∙当工件表面粗糙度值要求为Ra=0.8~3.2μm时,应分为粗铣、半精铣、精铣三步进行。
半精铣时背吃刀量或侧吃刀量取1.5~2㎜;精铣时,圆周铣侧吃刀量取0.3~0.5㎜,面铣刀背吃刀量取0.5~1㎜。
2.进给量f与进给速度Vf的选择
削加工的进给量f(㎜/r)是指刀具转一周,工件与刀具沿进给运动方向的相对位移量;进给速度Vf(㎜/min)是单位时间内工件与铣刀沿进给方向的相对位移量。
进给速度与进给量的关系为Vf=nf(n为铣刀转速,单位r/min)。
进给量与进给速度是数控铣床加工切削用量中的重要参数,根据零件的表面粗糙度、加工精度要求、刀具及工件材料等因素,参考切削用量手册选取或通过选取每齿进给量fz,再根据公式f=Zfz(Z为铣刀齿数)计算。
每齿进给量fz的选取主要依据工件材料的力学性能、刀具材料、工件表面粗糙度等因素。
工件材料强度和硬度越高,fz越小;反之则越大。
硬质合金铣刀的每齿进给量高于同类高速钢铣刀。
工件表面粗糙度要求越高,fz就越小。
每齿进给量的确定可参考表1-2选取。
工件刚性差或刀具强度低时,应取较小值。
3.切削速度Vc
铣削的切削速度Vc与刀具的耐用度、每齿进给量、背吃刀量、侧吃刀量以及铣刀齿数成反比,而与铣刀直径成正比。
其原因是当fz、ap、ae和Z增大时,刀刃负荷增加,而且同时工作的齿数也增多,使切削热增加,刀具磨损加快,从而限制了切削速度的提高。
为提高刀具耐用度允许使用较低的切削速度。
但是加大铣刀直径则可改善散热条件,可以提高切削速度。
表1-2铣刀每齿进给量参考值
工件材料
fz/mm
粗铣
精铣
高速钢铣刀
硬质合金铣刀
高速钢铣刀
硬质合金铣刀
钢
0.10~0.15
0.11~0.25
0.02~0.05
0.10~0.15
铸铁
0.12~0.20
0.15~0.30
铣削加工的切削速度Vc可参考表1-3选取,也可参考有关切削用量手册中的经验公式通过计算选取。
表1-3铣削加工的切削速度参考值
工件材料
硬度
Vc/(m.min)
高速钢铣刀
硬质合金铣刀
钢
<225
18~42
66~150
225~325
12~36
54~120
325~425
6~21
36~75
铸铁
<190
21~36
66~150
190~260
9~18
45~150
260~320
4.5~10
21~30
典型工件的工艺分析
三.平面凸轮的数控铣削工艺分析
图1-2所示为槽形凸轮零件,在铣削加工前,该零件是一个经过加工的圆盘,圆盘直径为Ф280㎜,带有两个基准孔Ф35㎜及Ф12㎜。
Ф35㎜及Ф12㎜两个定位孔,X面已在前面加工完毕,本工序是在铣床上加工槽。
该零件的材料为HT200,试分析其数控铣削加工工艺。
1.零件图工艺分析
该零件凸轮轮廓由HA、BC、DE、FG和直线AB、HG以及过渡圆弧CD、EF所组成。
组成轮廓的各几何元素关系清楚,条件充分,所需要基点坐标容易求得。
凸轮内外轮廓面对X面有垂直度要求。
材料为铸铁,切削工艺性较好。
根据分析,采取以下工艺措施:
凸轮内外轮廓面对X面有垂直度要求,只要提高装夹精度,使X面与铣刀轴线垂直,即可保证。
2.选择设备
加工平面凸轮的数控铣削,一般采用两轴以上联动的数控铣床,因此首先要考虑的是零件的外形尺寸和重量,使其在机床的允许范围以内。
其次考虑数控机床的精度是否能满足凸轮的设计要求。
第三,看凸轮的最大圆弧半径是否在数控系统允许的范围之内。
根据以上三条即可确定所要使用的数控机床为两轴以上联动的数控铣床。
3.确定零件的定位基准和装夹方式
∙定位基准采用“一面两孔”定位,即用圆盘X面和两个基准孔作为定位基准。
∙根据工件特点,用一块320㎜×320㎜×40㎜的垫块,在垫块上分别精镗Ф35㎜及Ф12㎜两个定位孔(当然要配定位销),孔距离80±0.015㎜,垫板平面度为0.05㎜,该零件在加工前,先固定夹具的平面,使两定位销孔的中心连线与机床x轴平行,夹具平面要保证与工作台面平行,并用百分表检查,见图1-3。
4.确定加工顺序及走刀路线
整个零件的加工顺序的拟订按照基面先行、先粗后精的原则确定。
因此应先加工用作定位基准的Ф35㎜及Ф12㎜两个定位孔、X面,然后再加工凸轮槽内外轮廓表面。
由于该零件的Ф35㎜及Ф12㎜两个定位孔、X面已在前面工序加工完毕,在这里只分析加工槽的走刀路线,走刀路线包括平面内进给走刀和深度进给走刀两部分路线。
平面内的进给走刀,对外轮廓是从切线方向切入;对内轮廓是从过渡圆弧切入。
在数控铣床上加工时,对铣削平面槽形凸轮,深度进给有两种方法:
一种是在xz(或yz)平面内来回铣削逐渐进刀到既定深度;另一种是先打一个工艺孔,然后从工艺孔进刀到既定深度。
进刀点选在P(150,0)点,刀具来回铣削,逐渐加深到铣削深度,当达到既定深度后,刀具在xy平面内运动,铣削凸轮轮廓。
为了保证凸轮的轮廓表面有较高的表面质量,采用顺铣方式,即从P点开始,对外轮廓按顺时针方向铣削,对内轮廓按逆时针方向铣削。
图1-2槽形凸轮零件
图1-3凸轮加工装夹示意图
1—开口垫圈;2—带螺纹圆柱销;3—压紧螺母;4—带螺纹削边销;5—垫圈;6—工件;7—垫块
5.刀具的选择
根据零件结构特点,铣削凸轮槽内、外轮廓(即凸轮槽两侧面)时,铣刀直径受槽宽限制,同时考虑铸铁属于一般材料,加工性能较好,选用Ф18㎜硬质合金立铣刀,见表1-4。
表1-4数控加工刀具卡片
产品名称或代号
XXX
零件名称
槽形凸轮
零件图号
XXX
序号
刀具号
刀具规格名称(mm)
数量
加工表面
备注
1
T01
Ф18硬质合金立铣刀
1
粗铣凸轮槽内外轮廓
2
T02
Ф18硬质合金立铣刀
1
精铣凸轮槽内外轮廓
编制
XXX
审核
XXX
批准
XXX
共页
第页
6.切削用量的选择
凸轮槽内、外轮廓精加工时留0.2㎜铣削用量,确定主轴转速与进给速度时,先查切削用量手册,确定切削速度与每齿进给量,然后利用公式vc=πdn/1000计算主轴转速n,利用vf=nZfz计算进给速度。
7.填写数控加工工序卡片(见表1-5)
表1-5槽形凸轮的数控加工工艺卡片
单位名称
XXX
产品名称或代号
零件名称
零件图号
XXX
槽形凸轮
XXX
工序号
程序编号
夹具名称
使用设备
车间
XXX
XXX
螺旋压板
5025
数控中心
工步号
工步内容
刀具号
刀具规格(mm)
主轴转速(r/min)
进给速度(mm/min)
背吃刀量(mm)
备注
1
来回铣削,逐渐加深铣削深度
T01
Ф18
800
60
分两层削
2
粗铣凸轮槽内轮廓
T01
Ф18
700
60
3
粗铣凸轮槽外轮廓
T01
Ф18
700
60
4
精铣凸轮槽内轮廓
T02
Ф18
1000
100
5
精铣凸轮槽外轮廓
T02
Ф18
1000
100
编制
XXX
审核
XXX
批准
XXX
年月日
共日
第日
参考文献
1付永领,王岩,裴忠才.基于CAN总线液压喷漆机器人控制系统设计与实现.机床与液压.2003,(6):
90~92
2丁又青,朱新才.一种新型型钢翻面机液压系统设计.机床与液.2003,(5):
128~129
3刘剑雄,韩建华.物流自动化搬运机械手机电系统研究.机床与液压.2003,
(1):
126~128
4徐轶,杨征瑞,朱敏华,温齐全.PLC在电液比例与伺服控制系统中的应用.机床与液压.2003,(5):
143~144
5胡学林.可编程控制器(基础篇).北京:
电子工业出版社,2003.
6胡学林.可编程控制器(实训篇).北京:
电子工业出版社,2004.
7孙兵,赵斌,施永康.基于PLC的机械手混合驱动控制.液压与气动.2005,(3):
37~39
8孙兵,赵斌,施永康.物料搬运机械手的研制.机电一体化.2005,
(2):
43~45
9王田苗,丑武胜.机电控制基础理论及应用.北京:
清华大学出版社,2003.
10李建勇.机电一体化技术.北京:
科学出版社,2004.
11王孙安,杜海峰,任华.机械电子工程.北京:
科学出版社,2003.
12张启玲,何玉安.PLC在气动控制称量包装装置中的应用.液压与气动.2005,
(1):
31~33
13赵文.数字控制技术在龙门刨床电控系统中的应用.电气传动.2005.35卷(3):
55~57
14沈兴全,吴秀玲.液压传动与控制.北京:
国防工业出版社,2005.
15王宪军,赵存友.液压传动.哈尔滨:
哈尔滨工程大学出版社,2002.
16徐灏等.机械设计手册.第5卷.北京:
机械工业出版社,2000.
17陈铁鸣,王连明,王黎钦.机械设计(修订版).哈尔滨:
哈尔滨工业大学出版社,2003.
18邓星钟.机电传动控制(第三版).武汉:
华中科技大学出版社,2001.
19西门子自动化与驱动集团(SIEMENSAG).S7-200系统手册.2002.
20蔡行健.深入浅出西门子S7-200PLC.北京:
北京航空航天大学出版社,2003.
22张利平.现代液压技术应用220例.化学工业出版社,2004.
23高西林.锻床上料机械手.轻工机械.2001,
(2):
24李春波,王大明,李哲,王祖温.PLC控制的气动上下料机械手.液压气动与密封,1999.12.(6):
21~24
25尹自荣,熊晓红,骆际焕,王建坤.数控上下料机械手的研究及应用.锻压机械.1994,(6):
3~5
26张波,李卫民,尚锐.多功能上下料用机械手液压系统.2002,(8):
31~32
27侯沂,刘涛.装卸机械手设计研究.机械.2004,第31卷(6):
53~54
28叶爱芹,袁金强.PLC在机械手控制系统中的应用.安徽技术师范学院学报.2001,15卷(4):
64~65
29王会香,孙全颖.自动涂胶机械手的PLC控制.哈尔滨理工大学学报.2002,7卷(5):
16~18
30潘沛霖,杨宏,高波,吴伟光.四自由度折叠式机械手的结构设计与分析.哈尔滨工业大学学报.1994,26卷(4):
90~95
31刘新一.多工位自动冲床机械手控制器设计.广州大学学报(综合版).2000,第14卷(3):
19~20
32吉爱国,冯汝鹏,郭伟,张锦江.计算机在机械手控制中的应用.机械与电子.1996,(6):
8~9
附录1:
车床及其切削加工
车床主要是为了进行车外圆、车端面和镗孔等项工作而设计的机床。
车削很少在其他种类的机床上进行,而且任何一种其他机床都不能像车床那样方便地进行车削加工。
由于车床还可以用来钻孔和铰孔,车床的多功能性可以使工件在一次安装中完成几种加工。
因此,在生产中使用的各种车床比任何其他种类的机床都多。
车床的基本部件有:
床身、主轴箱组件、尾架组件、溜板组件、丝杠和光杠。
床身是车床的基础件。
它通常是由经过充分正火或时效处理的灰铸铁或者球墨铸铁制成。
它是一个坚固的刚性框架,所有其他基本部件都安装在床身上。
通常在床身上有内外两组平行的导轨。
有些制造厂对全部四条导轨都采用导轨尖顶朝上的三角形导轨(即山形导轨),而有的制造厂则在一组中或者两组中都采用一个三角形导轨和一个矩形导轨。
导轨要经过精密加工,以保证其直线度精度。
为了抵抗磨损和擦伤,大多数现代机床的导轨是经过表面淬硬的,但是在操作时还应该小心,以避免损伤导轨。
导轨上的任何误差,常常意味着整个机床的精度遭到破坏。
主轴箱安装在内侧导轨的固定位置上,一般在床身的左端。
它提供动力,并可使工件在各种速度下回转。
它基本上由一个安装在精密轴承中的空心主轴和一系列变速齿轮——类似于卡车变速箱一所组成。
通过变速齿轮,主轴可以在许多种转速下旋转。
大多数车床有8-18种转速,一般按等比级数排列。
而且在现代机床上只需扳动2-4个手柄,就能得到全部转速。
一种正在不断增长的趋势是通过电气的或者机械的装置进行无级变速。
由于机床的精度在很大程度上取决于主轴,因此,主轴的结构尺寸较大,通常安装在预紧后的重型圆锥滚子轴承或球轴承中。
主轴中有一个贯穿全长的通孔,长棒料可以通过该孔送料。
主轴孔的大小是车床的一个重要尺寸,因为当工件必须通过主轴孔供料时,它确定了能够加工的棒料毛坯的最大尺寸。
尾架组件主要由三部分组成。
底板与床身的内侧导轨配合,并可以在导轨上做纵向移动。
底板上有一个可以使整个尾架组件夹紧在任意位置上的装置。
尾架体安装在底板上,可以沿某种类型的键槽在底板上横向移动,使尾架能与主轴箱中的主轴对正。
尾架的第三个组成部分是尾架套筒。
它是一个直径通常大约在51—76mm(2-3英寸)之间的钢制空心圆柱体。
通过手轮和螺杆,尾架套筒可以在尾架体中纵向移人和移出几英寸。
车床的规格用两个尺寸表示。
第一个称为车床床面上最大加工直径。
这是在车床上能够旋转的工件的最大直径。
它大约是两顶尖连线与导轨上最近点之间距离的两倍。
第二个规格尺寸是两顶尖之间的最大距离。
车床床面上最大加工直径表示在车床上能够车削的最大工件直径,而两顶尖之间的最大距离则表示在两个顶尖之间能够安装的工件的最大长度。
普通车床是生产中最经常使用的车床种类。
它们是具有前面所叙述的所有那些部件的重载机床,并且除了小刀架之外,全部刀具的运动都有机动进给。
它们的规格通常是:
车床床面上最大加工直径为305-610mm(12-24英寸);两顶尖之间距离为610—1219mm(24-48英寸)。
但是,床面上最大加工直径达到1270mm(50英寸)和两顶尖之间距离达到3658mm(12英尺)的车床也并不少见。
这些车床大部分都有切屑盘和一个安装在内部的冷却液循环系统。
小型的普通车床——车床床面最大加工直径一般不超过330mm(13英寸)——被设计成台式车床,其床身安装在工作台或柜子上。
虽然普通车床有很多用途,是很有用的机床,但是更换和调整刀具以及测量工件花费很多时间,所以它们不适合在大量生产中应用。
通常,它们的实际加工时间少于其总加工时间的30%。
此外,需要技术熟练的工人来操作普通车床,这种工人的工资高而且很难雇到。
然而,操作工人的大部分时间却花费在简单的重复调整和观察切屑产生过程上。
因此,为了减少或者完全不雇用这类熟练工人,六角车床、螺纹加工车床和其他类型的半自动和自动车床已经很好地研制出来,并已经在生产中得到广泛应用。
普通车床作为最早的金属切削机床中的一种,目前仍然有许多有用的和为人们所需要的特性。
现在,这些机床主要用在规模较小的工厂中,进行小批量的生产,而不是进行大批量的生产。
在现代的生产车间中,普通车床已经被种类繁多的自动车床所取代,诸如自动仿形车床,六角车床和自动螺丝车床。
现在,设计人员已经熟知先利用单刃刀具去除大量的金属余量,然后利用成型刀具获得表面光洁度和精度这种加工方法的优点。
这种加工方法的生产速度与现在工厂中使用的最快的加工设备的速度相等。
普通车床的加工偏差主要依赖于操作者的技术熟练程度。
设计工程师应该认真地确定由熟练工人在普通车床上加工的实验零件的公差。
在把实验零件重新设计为生产零件时,应该选用经济的公差。
对生产加工设备来说,目前比过去更着重评价其是否具有精确的和快速的重复加工能力。
应用这个标准来评价具体的加工方法,六角车床可以获得较高的质量评定。
在为小批量的零件(100—200件)设计加工方法时,采用六角车床是最经济的。
为了在六角车床上获得尽可能小的公差值,设计人员应该尽量将加工工序的数目减至最少。
自动螺丝车床通常被分为以下几种类型:
单轴自动、多轴自动和自动夹紧车床。
自动螺丝车床最初是被用来对螺钉和类似的带有螺纹的零件进行自动化和快速加工的。
但是,这种车床的用途早就超过了这个狭窄的范围。
现在,它在许多种类的精密零件的大批量生产中起着重要的作用。
工件的数量对采用自动螺丝车床所加工的零件的经济性有较大的影响。
如果工件的数量少于1000件,在六角车床上进行加工比在自动螺丝车床上加工要经济得多。
如果计算出最小经济批量,并且针对工件批量正确地选择机床,就会降低零件的加工成本。
因为零件的表面粗糙度在很大程度上取决于工件材料、刀具、进给量和切削速度,采用自动仿形车床加工所得到的最小公差不一定是最经济的公差。
在某些情况下,在连续生产过程中,只进行一次切削加工时的公差可以达到±0.05mm。
对于某些零件,槽宽的公差可以达到±0.125mm。
镗孔和采用单刃刀具进行精加工时,公差可达到±0.0125mm。
在希望获得最大产量的大批量生产中,进行直径和长度的车削时的最小公差值为土0.125mm是经济的。
金属切削加工在制造业中得到了广泛的应用。
其特点是工件在加工前具有足够大的尺寸,可以将工件最终的几何形状尺寸包容在里面。
不需要的材料以切屑、颗粒等形式被去除掉。
去除切屑是获得所要求的工件几何形状,尺寸公差和表面质量的必要手段。
切屑量多少不一,可能占加工前工件体积的百分之几到70%—80%不等。
由于在金属切削加工中,材料的利用率相当低,加之预测到材料和能源的短缺以及成本的增加,最近十年来,金属成形加工的应用越来越多。
然而,