乳液聚合法制备纳米聚合物微球毕业设计论文.docx
《乳液聚合法制备纳米聚合物微球毕业设计论文.docx》由会员分享,可在线阅读,更多相关《乳液聚合法制备纳米聚合物微球毕业设计论文.docx(29页珍藏版)》请在冰豆网上搜索。
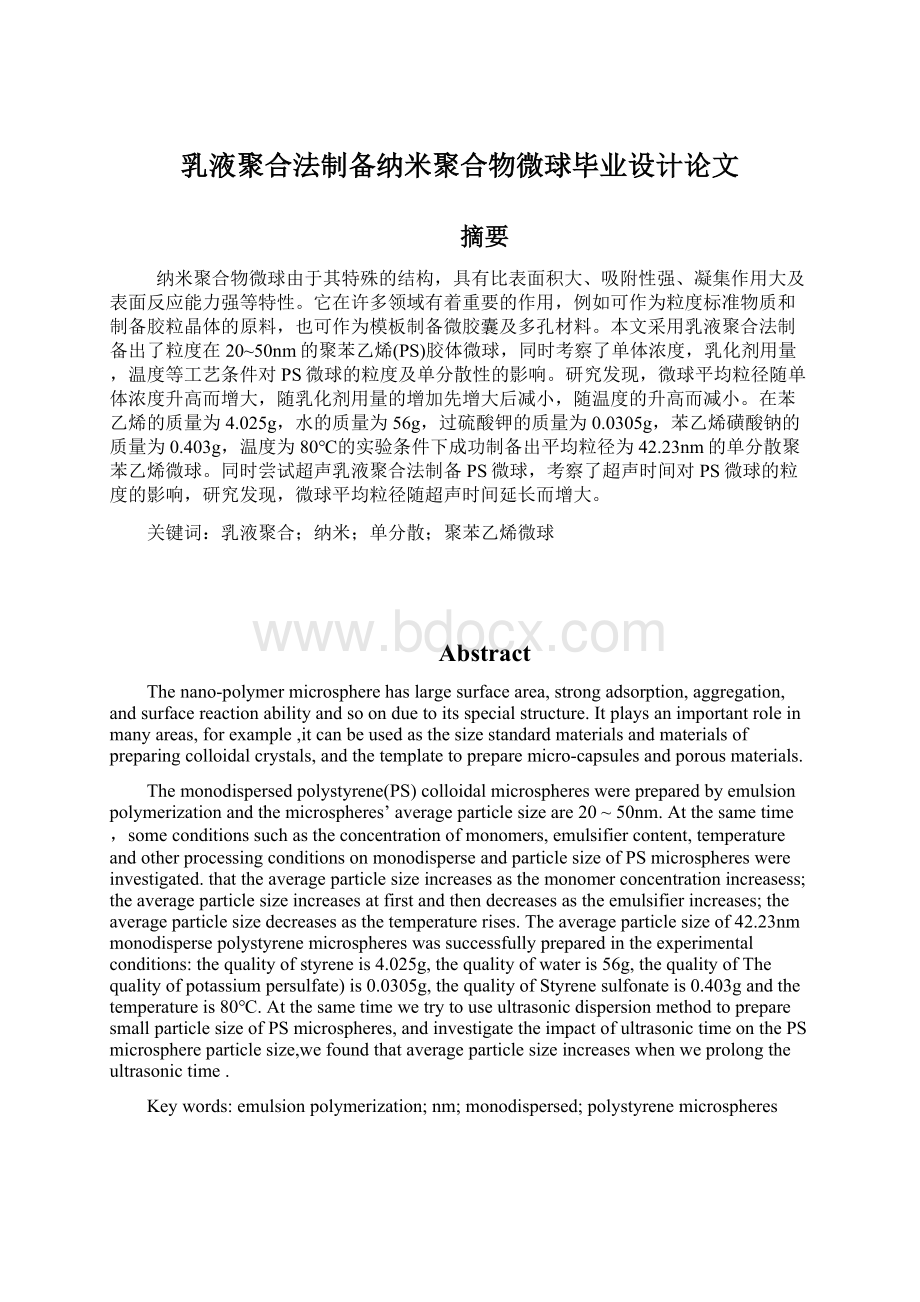
乳液聚合法制备纳米聚合物微球毕业设计论文
摘要
纳米聚合物微球由于其特殊的结构,具有比表面积大、吸附性强、凝集作用大及表面反应能力强等特性。
它在许多领域有着重要的作用,例如可作为粒度标准物质和制备胶粒晶体的原料,也可作为模板制备微胶囊及多孔材料。
本文采用乳液聚合法制备出了粒度在20~50nm的聚苯乙烯(PS)胶体微球,同时考察了单体浓度,乳化剂用量,温度等工艺条件对PS微球的粒度及单分散性的影响。
研究发现,微球平均粒径随单体浓度升高而增大,随乳化剂用量的增加先增大后减小,随温度的升高而减小。
在苯乙烯的质量为4.025g,水的质量为56g,过硫酸钾的质量为0.0305g,苯乙烯磺酸钠的质量为0.403g,温度为80℃的实验条件下成功制备出平均粒径为42.23nm的单分散聚苯乙烯微球。
同时尝试超声乳液聚合法制备PS微球,考察了超声时间对PS微球的粒度的影响,研究发现,微球平均粒径随超声时间延长而增大。
关键词:
乳液聚合;纳米;单分散;聚苯乙烯微球
Abstract
Thenano-polymermicrospherehaslargesurfacearea,strongadsorption,aggregation,andsurfacereactionabilityandsoonduetoitsspecialstructure.Itplaysanimportantroleinmanyareas,forexample,itcanbeusedasthesizestandardmaterialsandmaterialsofpreparingcolloidalcrystals,andthetemplatetopreparemicro-capsulesandporousmaterials.
Themonodispersedpolystyrene(PS)colloidalmicrosphereswerepreparedbyemulsionpolymerizationandthemicrospheres’averageparticlesizeare20~50nm.Atthesametime,someconditionssuchastheconcentrationofmonomers,emulsifiercontent,temperatureandotherprocessingconditionsonmonodisperseandparticlesizeofPSmicrosphereswereinvestigated.thattheaverageparticlesizeincreasesasthemonomerconcentrationincreasess;theaverageparticlesizeincreasesatfirstandthendecreasesastheemulsifierincreases;theaverageparticlesizedecreasesasthetemperaturerises.Theaverageparticlesizeof42.23nmmonodispersepolystyrenemicrosphereswassuccessfullypreparedintheexperimentalconditions:
thequalityofstyreneis4.025g,thequalityofwateris56g,thequalityofThequalityofpotassiumpersulfate)is0.0305g,thequalityofStyrenesulfonateis0.403gandthetemperatureis80℃.AtthesametimewetrytouseultrasonicdispersionmethodtopreparesmallparticlesizeofPSmicrospheres,andinvestigatetheimpactofultrasonictimeonthePSmicrosphereparticlesize,wefoundthataverageparticlesizeincreaseswhenweprolongtheultrasonictime.
Keywords:
emulsionpolymerization;nm;monodispersed;polystyrenemicrospheres
第1章绪论
聚合物微球即为高分子微球,指直径在纳米级至微米级,形状为球形或其他几何体的高分子材料或高分子复合材料,其形貌可以是多种多样的,包括实心、空心、多孔、哑铃形、洋葱形等。
高分子微球也包括微囊,微囊通常是指中间有一个或多个微腔,而且微腔内包埋了某种特殊物质的微球[1]。
纳米聚合物粒子由于其特殊的结构,具有比表面积大、吸附性强、凝集作用大及表面反应能力强等特性,在粒度标准物质、光子晶体的合成等方面有广泛用途[2],已成为聚合物科学领域的一个研究热点,因而其制备方法及其粒径的控制等研究近年来受到广泛的关注。
聚合物纳米微粒主要的制备方法有微乳液聚合和乳液聚合,已成为新兴的功能高分子材料,引起人们极大的兴趣。
80年代初期Stoffer等首次报道了微乳液聚合,用于制各尺寸小、均匀的聚合物乳胶粒。
但是微乳液聚合存在很多缺点,如:
乳化剂用量大、单体浓度小、产物粒子纯度差,对于一些易聚集而沉积的聚合物,乳胶粒形态仍然难以控制,另外在一些合成条件如强酸、强碱和离子强度较高的情况下,难以得到稳定的微乳液。
从而使微乳液聚合制备聚合物纳米材料方法难以实用。
此外,传统的乳液聚合可以制备粒径接近50nm的单分散聚合物粒子,而微乳液聚合方法可以直接制备小于50nm的聚合物粒子,但是过高的乳化剂含量及较差的单分散性限制了其应用。
因此用乳液聚合代替微乳液聚合来生产聚合物纳米粒子,尤其是50nm以下的纳米粒子,在理论和实践上都具有重要意义。
第2章国内外文献综述
2.1聚合物微球的制备方法
以单体为原料的高分子微球的制备方法有很多种主要分为乳液聚合、无皂乳液聚合、分散聚合、沉淀聚合、悬浮聚合、微乳聚合、细乳液聚合以及种子聚合。
不同方法可以制备不同尺寸的微球。
下表是对几种常见的聚合方法的比较[3]:
表2-1聚合物微球的制备方法
(table2-1themethodofpreparePolymermicrospheres)
比较项目
乳液聚合
无皂乳液聚合
悬浮聚合
分散聚合
无重力种子聚合
溶胀法
单体存在场所
单体珠滴,乳胶粒,
单体珠滴,乳胶粒,水相,介质
颗粒介质
介质颗粒
单体珠滴,颗粒,介质
颗粒,介质(少量)
存在场所
介质
介质
颗粒
介质颗粒
颗粒
颗粒
稳定剂
不需要
不需要
需要
需要
不需要
需要
乳化剂
需要
不需要
不需要
不需要
需要
需要
聚合反应前状态
多相
多相
二相
均相
多相
二相
粒径范围μm
0.04-0.5
0.5-1.0
100-1000
1-20
2-30
1-100
粒径分散性
分布较窄
分布窄
分布宽
单分散
单分散
单分散
2.1.1分散聚合
分散聚合是随涂科工业的发展而产生的,70年代初由ICI公司的研究者们最先指出分散聚合是一种特殊的沉淀聚合,它将稳定剂(或称分散剂)锚定于粒子表面使聚合物稳定地分散在介质中,形成分散体系易使微球(粒径在0.5~20μm)实现单分散性,且工艺简单,适合于多种单体。
2.1.1.1分散聚合特点
(1)聚合物颗粒球形好,粒径大(与乳液聚合相比),粒径分布窄。
(2)粘度低,无拉丝性,干燥快,不会使基材变形和生锈,可以在低温下使用,施工性能良好。
(3)可选用毒性低和危险性小的分散介质以减少对环境的污染,因此特别适合于制备各种类型的涂料,染料等[4]。
2.1.1.2分散聚合原理
分散聚合就其本质而言属于沉淀聚合,反应体系由单体、引发剂、稳定剂以及反应介质组成,反应前为均相体系。
随着反应的进行,生成的聚合物链变长,在反应介质中溶解度逐渐降低.当聚合物链达到临界链长后,从介质中析出,在稳定剂的作用下形成稳定的核心。
单体不断向核内扩散聚合,同时介质中的聚合物链不断被核表面所‘捕获’,逐渐增大,最终以微球形式分散在介质中。
影响微球性能主要有两方面因素:
反应体系的组成及反应条件。
反应体系的组成包括单体、引发剂、稳定剂、分散介质等的种类和浓度;反应条件有反应温度以及搅拌速度等。
分散聚合中常用的引发剂有偶氮二异丁腈,过氧化苯甲酰,过硫酸钾等引发剂,也可采用混合引发剂。
稳定剂是微球形成过程中成核的关键,常用的稳定剂有聚乙二醇、聚乙烯吡咯烷酮、纤维素及其衍生物等。
分散介质极性的大小决定了齐聚物在介质中的溶解度,进而影响聚合物微球的粒径和粒径分布。
为了获得合适的极性,常常选用混合溶剂作反应介质,通过调节其组成来控制极性大小。
反应温度和搅拌速度选择对于微球的合成也很重要。
2.1.1.3分散聚合过程
曹同玉等[5]利用膨胀计反应器研究了分散聚合动力学过程,指出分散聚合过程大致可分为三个阶段:
第一阶段为反应初期的成核期,这一阶段的反应行为类似于溶液聚合,引发剂在液相中分解,并在其中引发聚合,聚合物链增长到临界链长以后,从液相中沉析出来,形成初级粒子。
反应动力学曲线较为平坦,转化率和反应时间近似呈线性关系。
第二阶段为粒子的增长期,由于在该阶段刚开始时粒子尚小,捕捉自由基效率不高,粒子的增长主要靠吸收液相中终止的聚合物链,仅有极少数的自由基被粒子捕获并在其中进行增长反应,故在增长期前一阶段,其反应仍以溶液聚合为主。
随着粒子的长大,粒子对自由基捕捉能力逐渐增强,反应逐渐由液相转移到粒子相中进行,由于粒子中富集了较多的单体,即单体浓度较高,同时由于粒子对自由基的隔离作用降低了链终止速率,故分散聚合反应速率超过了溶液聚合。
随着单体转化率进一步提高,粒子己经具有足够大的表面积,能将几乎所有的自由基和引发剂吸收到粒子中来,此时反应中心由液相转移到粒子内部,其反应规律和乳液聚合反应类似,在该阶段聚合反应速率大幅度提高,动力学曲线变陡。
第三阶段,当单体转化率达90%以上时,由于玻璃化效应,分散聚合动力学曲线迅速趋于一条水平线。
随着粒子中单体逐渐转化成聚合物,粒子的玻璃化温度逐渐提高,当玻璃化温度提高到等于反应温度时,自由基链和单体均被固结,致使聚合反应速率骤降至零。
张凯[6]等人用分散聚合法制得微米级的PS微球,通过对影响分散聚合的原料组成(分散稳定剂、单体、引发剂)和反应条件(反应介质极性、反应体系温度、搅拌速度)的基础配方实验及交叉实验发现:
①随着分散稳定剂用量的增加,聚合物微球的粒径减小;随着单体和引发剂用量的增加,聚合物微球的粒径增大。
随着反应介质极性的增加,聚合物微球的粒径减小,粒径分布变化不大;随着反应体系温度的增加,聚合物微球的粒径增大,粒径分布变化不大。
分散稳定剂和单体用量是影响聚合物微球粒径分布的两个主要因素。
在满足粒径和粒径分布要求的前提下,搅拌速度以低速为宜。
②不同因素对分散聚合反应聚合速率的影响作用大小不同,以单体用量、引发剂用量、反应体系温度为主,反应介质极性、搅拌速度次之,分散稳定剂用量最弱。
胡杰[7]等人用乙醇/水作为分散介质,利用分散聚合制备得到了粒径在2~5μm,单分散性良好的聚苯乙烯微球。
发现当单体用量低于15%时,随单体量的增加聚合物颗粒粒径增大,同时能保持颗粒的单分散性,当单体用量再增加时颗粒趋于减小,即在单体用量为15%时出现一个粒径的最大值。
随着分散介质中含水量的提高,聚合物微球粒径逐渐减小,粒度分布均匀性随之降低。
随着引发剂用量提高,粒径逐渐增大,粒度分布系数增大。
张光华[8]等人采用分散聚合法制备了平均粒径D=6.60μm,ε=0.05的单分散交联聚苯乙烯微球。
他们发现增加单体浓度、引发剂用量,减少随单体浓度的增加,微球粒径和粒径分散系数增大。
随着引发剂AIBN用量的增加,微球的粒径增大,分散度逐渐增加。
随稳定剂PVP用量的增加,微球粒径减小,分散性变窄。
随交联剂DVB用量的增加,聚合反应速率逐渐增大,最终转化率也有所提高。
程艳玲[9]等人通过超声辐照分散聚合制得聚苯乙烯纳米微球,探讨了温度、引发剂和稳定剂浓度等对聚合反应的影响。
研究结果表明,与常规加热聚合相比,超声辐照分散聚合反应无诱导期,聚合反应速率快,转化率高。
反应速度快,制备的聚苯乙烯(PS)微球粒径小。
在超声辐照分散聚合下,反应1h的St转化率达到63%,所得PS纳米粒子的平均粒径为80nm。
随着引发剂浓度增大反应速率加快,St的转化率增大。
随着温度升高分散聚合反应速率增大,稳定剂浓度太大或太小均导致最终转化率稍低,不利于反应的稳定进行.
Tuncel等[10]系统地研究了由分散聚合制备PS单分散微球及粒子表面功能化的问题。
他们研究了引发剂和稳定剂浓度,醇的类型,醇/水比,单体/介质比等对PS微球粒径大小和分散性的影响,得到了如下的结论:
1)引发剂浓度越高,聚合物粒径越大,但分散性也越大。
2)稳定剂浓度越高,聚合物粒子越小,分散性也越小。
制备单分散性并有一定粒径的聚合物微粒,必须对稳定剂进行优化选择。
3)水是制备单分散性粒子的关键组分,分散介质中水的含量增加,分散介质的极性增加,导致生成的微球的平均粒径降低。
4)聚合介质的极性由醇的类型和用量,水和苯乙烯的含量来控制。
介质极性增加,单分散性提高,但粒径变小,降低极性,平均粒径增加,但分散性变宽。
5)分散介质的均匀性明显影响聚合物微球的大小和分布。
按照醇的类型,醇、水、单体/水的比例不同,也可以得到多项体系,但不能制得单一粒径微球。
6)按照介质的性质,为了防止两相体系的形成,单体浓度不能高于一定限度。
因为均相分散介质中,单体含量的增加,将引起介质的极性变化,会导致大的粒径生成,但粒径分布明显变宽。
2.1.2乳液聚合
乳液聚合法是最常用的微球制备方法,一般使用疏水性较强的单体制备。
用乳液聚合法制得的微球粒径一般在数十至数百纳米的范围之间。
乳液聚合技术发展至今已有80余年历史,其理论也较为完善。
乳液聚合在工业上应用广泛。
合成橡胶中产量最大的丁苯橡胶和丁睛橡胶采用连续乳液法生产,聚醋酸乙烯酯胶乳、丙烯酸酯类涂料和粘结剂、糊用聚氯乙烯树脂则用间歇乳液法生产。
图2-1乳液聚合体系三相示意图
Figure2-1Three-phasediagramofemulsionpolymerizationsystem
乳液聚合体系中主要由疏水性单体,水,乳化剂以及水溶性引发剂等组成。
乳化剂的作用:
降低表面张力,使单体分散成细小的液滴;在液滴或胶粒表面形成保护层,防止凝聚,使乳液稳定;形成胶束,使单体增溶。
制备时,通常先将乳化剂溶于水,再将单体用普通搅拌法分散于水中,通入氮气置换氧气,然后提高温度至引发剂分解温度以上,最后加入引发剂开始聚合。
乳液聚合体系的三相示意图如图2-1所示。
2.1.2.1乳液聚合优点:
(1)以水作分散介质,价廉安全。
乳液的粘度与聚合物分子量及聚合物含量无关,这有利于搅拌、传热和管道输送,便于连续操作。
(2)聚合速率快,同时产物分子量高。
可以在较低的温度下聚合。
(3)直接应用胶乳的场合,如水乳漆,粘结剂,纸张、皮革、织物处理剂等。
同时乳液聚合有若干缺点:
(1)需要固体聚合物时,乳液需经凝聚(破乳)、洗涤、脱水、干燥等工序、产品成本较悬浮法高。
(2)产品扣留有乳化剂等,难以完全除尽,有损电性能。
2.1.2.2乳液聚合原理
目前对乳液聚合的机理仍有争议,但基本上有两种理论得到认可和使用。
当乳化剂浓度高于临界胶束浓度(CMC)时,聚合机理用胶束成核理论。
该机理为:
在加入引发剂之前,聚合体系由在体系内加入水溶性引发剂后,引发剂在水相中分解成初级自由基。
初级自由基或立即被溶胀胶束捕捉,或在水相中与溶解于水的单体聚合成长为低聚物自由基后诶溶胀胶束捕捉。
然后,聚合反应将一直在溶胀胶束内进行,形成单体-聚合物微球。
虽然一开始单体大多以液滴形式才能在,但成核地点和聚合反应却不再油滴内。
这是因为单体油滴的数量和总表面积远远低于溶胀胶束,油滴从水相捕捉自由基的概率很小。
油滴的单体渐渐从油滴扩散至水相继而被单体-聚合物微球吸收。
即油滴其实为单体储存库。
同时未成核的胶束不断解体,乳化机被吸附在已成核的单体-聚合物表面当胶束状态的乳化剂消耗完后,不会再产生新的核,离子数维持一定,聚合只在单体-聚合物内进行,直至聚合结束单体转换率约为50%时油滴消失单体-聚合物内剩余单体继续聚合。
2.1.2.3乳液聚合过程
根据乳液聚合的动力学特征,整个聚合过程分为3个阶段。
第一阶段:
增速期,水相中自由基不断进入增溶胶束,引发其中的单体而成核,继续增长聚合,转变成单体-聚合物胶粒。
这一阶段,胶束不断减少,胶粒不断增多,速率增加,单体液滴数不变,只是体积不断缩小,一般以胶束的消失作为第一阶段结束的标志。
第二阶段:
恒速期,这一阶段从增溶胶束消失开始,只有胶粒和液滴两种粒子。
单体从液滴经水相不断扩散入胶粒内,保持胶粒内的单体浓度恒定,因此聚合速率恒定。
一般以单体液滴的消失或聚合速率开始下降为标志。
第三阶段:
降速期,这个阶段体系中已无单体液滴,只剩下胶粒一种粒子,胶粒数不变。
依靠胶粒内的残余单体继续聚合,聚合速率递降。
难溶于水的经典的乳液聚合以胶束成核为主,这是因为体系中胶束的表面积远远大于单体液滴的表面积,因此,初级自由基更容易被胶束捕捉到,引发成核。
但是,对于水溶性稍强的甲基丙烯酸甲酯来说,虽然胶束成核仍然存在,但是水相成核已不容忽视了。
近几十年来,乳液聚合技术研究继续向纵深方向发展,出现了许多新技术。
下面将对其进行简要的介绍:
王东波[11]等人通过乳液聚合的方法,成功地制备出了粒度在50nm左右,粒径分布均匀且具有良好球形度的单分散PS纳米微球。
并对其影响因素进行了研究,通过对反应温度、乳化剂浓度等反应条件的控制和合适的加料方式的选择,能够对PS纳米微球实现可控生长。
随着反应温度的升高,乳液的平均粒径逐渐变小,粒径分布变宽。
随着乳化剂用量的增加,粒子的粒径变小,分散性提高。
一锅法中反应单体一次加入反应体系时,得到的产物分散性较差,粒子互相连接在一起,要得到分散性良好的纳米微球需要加大乳化剂的用量。
当滴加单体时,粒子的分散性较好。
弭勇[12]等人用乳液法制备聚苯乙烯纳米微球,发现合成参数对苯乙烯转化率和聚苯乙烯分子量具有较大影响。
随乳化剂和引发剂用量的增加、乳化和反应时间的延长,苯乙烯的转化率和聚苯乙烯分子量相应提高,而随反应温度的升高转化率和聚苯乙烯的分子量出现了最大值。
2.1.3超声辐射乳液聚合
乳液聚合技术因具有反应散热快,并能在提高反应速率的同时提高聚合物分子量一直很受人们重视。
但是乳液聚合中乳化剂和引发剂的存在会降低聚合产物纯度,影响产品的性能。
超声波是一种频率为2×104~107的机械振动波。
机械振动波。
当超声波在液体媒介中传播时,声空化效应能产生局部高温高压,并伴随有强烈的冲击波和微射流。
因此超声空化能产生强烈的分散、搅拌、乳化、引发等作用,为发展乳液聚合提供了一种新的途径[13]。
超声辐照引发本体和溶液均相体系中聚合反应的研究报道较多,但是这些聚合反应的单体转化率都较低(<12%)。
更多聚合反应是在非均相体系中进行的,非均相体系中超声聚合反应的研究主要集中在乳液聚合方面。
2.1.3.1超声辐照乳液聚合的特点
与其他引发聚合方法相比,超声辐射引发乳液聚合方法有如下特点:
(1)不需使用引发剂。
这不仅可得到高纯度的产物,同时也排除了自由基对引发剂的链转移而导致分子量的降低。
(2)超声辐照具有强烈的分散、搅拌和乳化等作用,能促进单体在乳液体系中的分散,而且对生成的乳胶粒还有一定的稳定作用,从而能
显著降低乳化剂的含量。
有可能在很低的乳化剂的浓度下,或者甚至在没有乳化剂存在的情况下进行乳液聚合,从而有可能避免乳液聚合的主要不足即乳化剂的存在可能带来的弊病。
而且制得的聚合物乳胶粒子粒径较小。
范围可在纳米级。
(3)聚合反应可在低温下进行。
较低的温度有利于声致自由基的生成,这就使反应能在较低的温度下进行,从而大大避免了不必要的副反应(例如链转移反应)的产生,一方面增加了高聚物结构的规整性,同时也提高了分子量。
(4)与超声辐照本体聚合相比,反应速率快。
例如,BA的超声辐照乳液聚合10min转化率可达90%左右。
2.1.3.2超声辐照乳液聚合机理
超声辐照产生的自由基源于超声空化,超声空化产生的局部高温高压使物质分子裂解成自由基。
进一步引发单体反应;而常规乳液聚合中通常需要加入化学引发剂,这些化学引发剂加热分解或通过氧化-还原反应产生自由基引发单体反应。
由于两者产生自由基的途径不一样,故有一定的差异。
2.1.3.3超声辐照乳液聚合过程
已有的关于超声辐照乳液聚合动力学研究结果则表明:
超声辐照乳液聚合过程中无明显的恒速期,只有增速期和降速期。
与微乳液聚合相同。
这是因为超声空化作用不断产生大量的自由基,并且乳液不断受到超声波的强剪切作用,大的单体珠滴被分散成更小的液滴,所以成核过程在整个超声乳液聚合反应中将持续存在,反应中活性点数目不恒定,因而不存在反应恒速期。
在增速期内聚合物粒子数目不断增加,逐渐达到最高反应速率。
其后由于单体浓度的不断下降使得聚合速率开始降低。
2.1.4种子乳液聚合
种子聚合法可以分为乳液种子聚合法和分散溶胀聚合法。
一般乳液聚合得到的聚合物微粒直径在0.2以下,改变乳化剂种类和用量,或者改变工艺条件,虽然可使微粒直径有所增加,但是要使粒径不小于1μm,则很困难。
为了达到此目的,发展了乳液种子聚合法。
乳液种子聚合主要用于制备单分散且粒径小于2μm的乳液,而常规条件下,则很难获得几微米至几十微米的微粒
种子乳液聚合是将少量单体在有限的乳化剂条件下先乳液聚合成种子乳胶(50-100nm或更小),然后将少量种子乳胶(1%-3%)加入正式乳液聚合的配方中,种子胶粒被单体溶胀,继续聚合,使粒径增大。
经过多级溶胀聚合,粒径可达1-2微米或更大。
种子乳液聚合成功的关键是防止乳化剂过量,以免形成新的胶束,胶束仅供胶粒保护只需即可。
巫辉[14]人采用反应性乳化剂,在平均粒径为95.7nm、粒径分布为0.047种子乳液的基础上,由种子乳液聚合制备出平均粒径为261.6nm,粒径分布为0.021的单分散聚苯乙烯乳胶粒。
随着反应温度的升高,乳液的平均粒径逐渐变小,粒径分布变宽。
随着油水比的提高,乳胶粒的平均粒径增加。
粒径随乳化剂用量增加逐渐减小,当乳化剂用量大于0.47%时,粒径变化趋于平缓。
2.1.5核壳乳液聚合
核壳乳液聚合是种子乳液聚合的发展。
若种子聚合和后继聚合采用完全不同的单体则形成核壳结构的胶粒,在核与壳的界面上形成接枝成层,增加两者的相容性和粘结力,提高力学性能。
核壳乳液聚合成功的关键也是限量乳化剂。
2.1.6无皂乳液聚合
无皂乳液聚合是在传统乳液聚合的基础发展起来的一项聚合反应新技术。
它是指在反