单面多轴钻孔机床液压系统.docx
《单面多轴钻孔机床液压系统.docx》由会员分享,可在线阅读,更多相关《单面多轴钻孔机床液压系统.docx(27页珍藏版)》请在冰豆网上搜索。
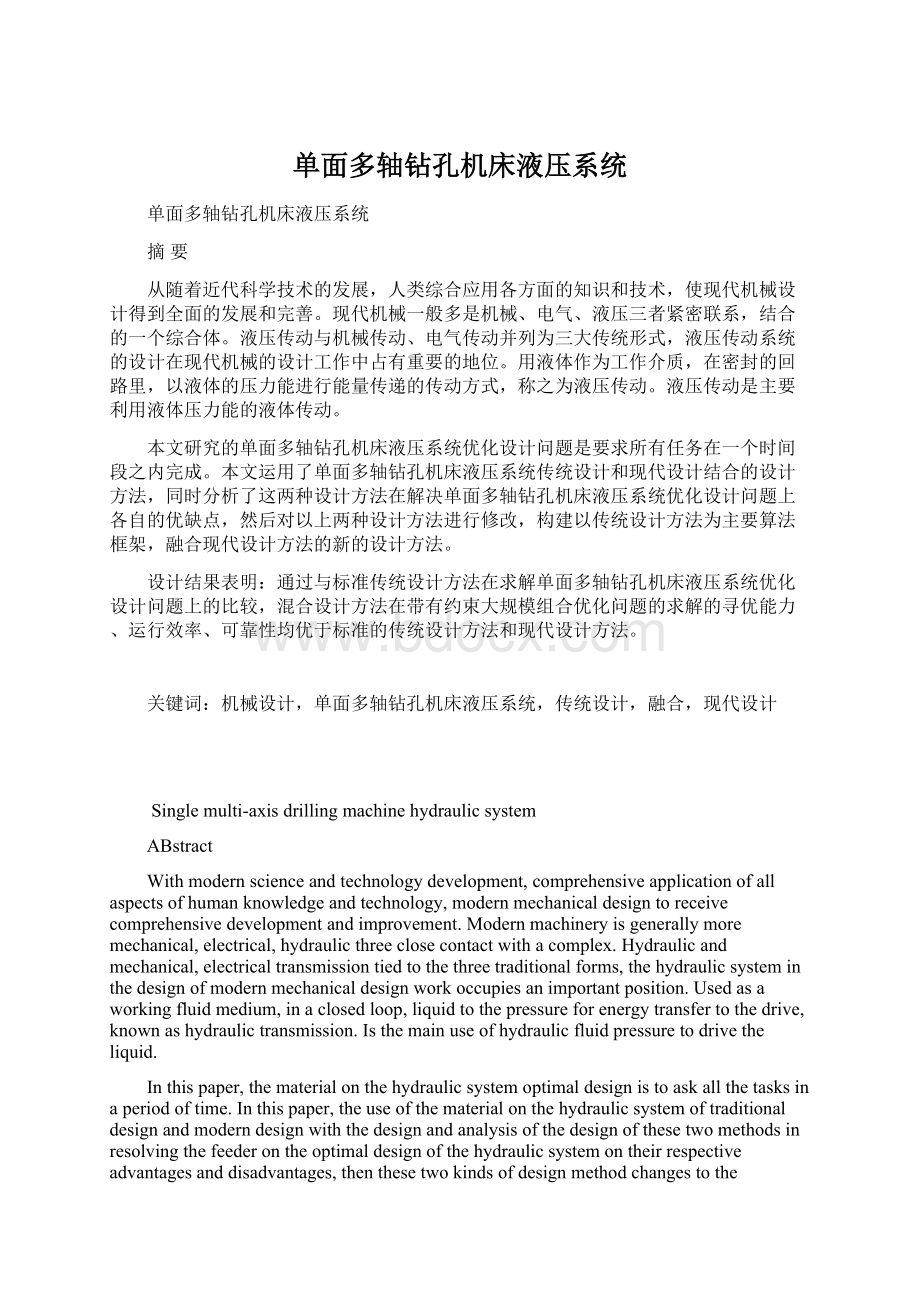
单面多轴钻孔机床液压系统
单面多轴钻孔机床液压系统
摘要
从随着近代科学技术的发展,人类综合应用各方面的知识和技术,使现代机械设计得到全面的发展和完善。
现代机械一般多是机械、电气、液压三者紧密联系,结合的一个综合体。
液压传动与机械传动、电气传动并列为三大传统形式,液压传动系统的设计在现代机械的设计工作中占有重要的地位。
用液体作为工作介质,在密封的回路里,以液体的压力能进行能量传递的传动方式,称之为液压传动。
液压传动是主要利用液体压力能的液体传动。
本文研究的单面多轴钻孔机床液压系统优化设计问题是要求所有任务在一个时间段之内完成。
本文运用了单面多轴钻孔机床液压系统传统设计和现代设计结合的设计方法,同时分析了这两种设计方法在解决单面多轴钻孔机床液压系统优化设计问题上各自的优缺点,然后对以上两种设计方法进行修改,构建以传统设计方法为主要算法框架,融合现代设计方法的新的设计方法。
设计结果表明:
通过与标准传统设计方法在求解单面多轴钻孔机床液压系统优化设计问题上的比较,混合设计方法在带有约束大规模组合优化问题的求解的寻优能力、运行效率、可靠性均优于标准的传统设计方法和现代设计方法。
关键词:
机械设计,单面多轴钻孔机床液压系统,传统设计,融合,现代设计
Singlemulti-axisdrillingmachinehydraulicsystem
ABstract
Withmodernscienceandtechnologydevelopment,comprehensiveapplicationofallaspectsofhumanknowledgeandtechnology,modernmechanicaldesigntoreceivecomprehensivedevelopmentandimprovement.Modernmachineryisgenerallymoremechanical,electrical,hydraulicthreeclosecontactwithacomplex.Hydraulicandmechanical,electricaltransmissiontiedtothethreetraditionalforms,thehydraulicsysteminthedesignofmodernmechanicaldesignworkoccupiesanimportantposition.Usedasaworkingfluidmedium,inaclosedloop,liquidtothepressureforenergytransfertothedrive,knownashydraulictransmission.Isthemainuseofhydraulicfluidpressuretodrivetheliquid.
Inthispaper,thematerialonthehydraulicsystemoptimaldesignistoaskallthetasksinaperiodoftime.Inthispaper,theuseofthematerialonthehydraulicsystemoftraditionaldesignandmoderndesignwiththedesignandanalysisofthedesignofthesetwomethodsinresolvingthefeederontheoptimaldesignofthehydraulicsystemontheirrespectiveadvantagesanddisadvantages,thenthesetwokindsofdesignmethodchangestothetraditionalbuildingdesignasthemainmethodframework,integrationofmoderndesignofthenewdesign.
Theresultsshowedthatthedesign:
thetraditionaldesignmethodsandstandardsforthematerialinthehydraulicsystemontheissueofoptimaldesign,hybriddesignmethodsincombinationwithlarge-scaleconstrainedoptimizationproblemfortheoptimizationofcapacity,efficiencyandreliabilityarestandardisbetterthanthetraditionaldesignmethodsandmoderndesign.
KEYWORDS:
mechanicaldesign,single-sidedmulti-axisdrillingmachinehydraulicsystem,traditionaldesign,integration,moderndesign
目 录
前 言1
第1章本论2
1.1任务分析2
1.1.1系统机构的主要构成2
1.1.2任务分析2
第2章方案选择3
2.1方案的拟定4
2.1.1供油方式4
2.1.2调速回路4
2.1.3速度换接回路4
2.1.4平衡及锁紧4
2.2方案的确定4
第3章总体设计6
3.1负载分析6
3.1.1工作负载6
3.1.2磨擦负载6
3.1.3惯性负载6
3.2负载图和速度图的绘制9
3.3液压缸主要参数的确定9
3.3.1初选液压缸的工作压力10
3.3.2计算液压缸的尺寸10
3.3.3液压缸的实际工作压强11
3.3.4活塞杆稳定性校核12
3.3.5求液压缸的最大流量12
3.3.6液压缸的功率12
3.3.7绘制工况图12
3.3.8液压缸其它参数的选择14
3.4液压系统图的拟定15
3.4.1供油方式15
3.4.2调速回路15
3.4.4平衡及锁紧16
3.4.5液压系统图17
3.4.6液压系统工作过程18
3.5液压元件的选择18
3.5.1确定液压泵的型号18
3.5.2确定电动机的型号19
3.5.3选择阀类元件及辅助元件21
3.5.4油箱的设计23
3.5.5联轴器25
3.6液压系统的性能验算25
3.6.1压力损失及调定压力的确定25
3.6.2系统的发热与温升27
结 论29
谢辞30
参考文献31
前 言
液压传动和气压传动称为流体传动,是根据17世纪帕斯卡提出的液
体静压力传动原理而发展起来的一门新兴技术,是工农业生产中广为应用的一门技术。
液压传动有许多突出的优点,因此它的应用非常广泛,如一般工业用的塑料加工机械、压力机械、机床等;行走机械中的工程机械、建筑机械、农业机械、汽车等;钢铁工业用的冶金机械、提升装置、轧辊调整装置等;土木水利工程用的防洪闸门及堤坝装置、河床升降装置、桥梁操纵机构等;发电厂涡轮机调速装置、核发电厂等等;船舶用的甲板起重机械(绞车)、船头门、舱壁阀、船尾推进器等;特殊技术用的巨型天线控制装置、测量浮标、升降旋转舞台等;军事工业用的火炮操纵装置、船舶减摇装置、飞行器仿真、飞机起落架的收放装置和方向舵控制装置等。
液压传动的基本原理是在密闭的容器内,利用有压力的油液作为工作介质来实现能量转换和传递动力的。
其中的液体称为工作介质,一般为矿物油,它的作用和机械传动中的皮带、链条和齿轮等传动元件相类似。
对设计液压系统进行分析,已知设计的是一卧式单面多轴钻孔组合机床的液压系统,要求液压系统完成的工作循环是:
快进→工进→快退→停止。
在设计过程中要注意液压设计的注意事项:
在滑台的速度变化较大,当滑台由工进转为快退时,以减少液压冲击,须使用背压阀等。
选用单杆活塞缸来实现工作循环所要求的快进、工进运动,借鉴经典的实现快进、快退的连接方式,差动连接来实现,而对于有大冲击,工作阻力不定对加工过程的影响,采用使用在回油路上接背压阀和在进油路上用调速阀和行程阀的组合来实现。
对于工况分段情况很大,借鉴同类机床多数采用双泵供油来节约能源。
为减少热变形对加工精度的影响,减少热源,选用远离机床床身的开式油箱。
在液压传动中,液压油缸就是一个最简单而又比较完整的液压传动系统,分析它的工作过程,可以清楚的了解液压传动的基本原理。
第1章本论
1.1任务分析
1.1.1系统机构的主要构成
机构不断地将材料从低的位置开始,通过快速上升,慢速上升运动到最高位置,停留,然后又回到起始位置重复上一次的运动。
滑台采用V形导轨,其导轨面的夹角为90度,滑台与导轨的最大间隙为2mm,工作台和活塞杆连在一起,在活塞杆的作用下反复做上下运动。
1.1.2任务分析
驱动它的液压传动系统完成快速上升——慢速上升——停留——快速下降的工作循环。
其垂直上升工件的重力为G物=5500N,滑台的重量为G台=1000N;
快速上升行程为S快=350mm,速度要求为
V快>=42m/min;
慢速上升的行程为S慢=100mm,速度要求为
V慢>=8m/min;
快速下降行程为S下=450mm,速度要求
V下>=65m/min;
滑台采用V型导轨,其导轨面的夹角为90度,已知垂直作用于导轨的载荷FN=120N,静摩擦因数:
Fs=0.2,动摩擦因数:
Fd=0.1。
启动加速和减速时间为T=0.5s;
液压缸的机械效率为η=0.91。
单位换算:
S快=0.35m;
V快>=7m/s;
S慢=0.1m;
V慢>=0.133m/s;
S下=0.45m;
V下>=1.1m/s.
系统总共承受的负载为:
F=G台+G物=5500+1000N=6500N,所以系统负载很小,应属于低压系统。
系统要求快上速度大于42m/min,慢上的速度大于8m/min,快下的速度大于65m/min,要完成的工作循环是:
快进上升、慢速上升、停留、快速下降。
但从系统的用途可以看出系统对速度的精度要求并不高,所以在选调速回路时应满足经济性要求。
第2章方案选择
2.1方案的拟定
2.1.1供油方式
由快速上升速度大于42m/min,而慢速上升的速度为大于8m/min,由此可知系统速度相差很大可知,因而该系统在快上和慢上时液压系统流量变化很大,综上所述可以选用变量泵或双泵供油。
2.1.2调速回路
由于速度变化大,所以液压传动系统功率变化也大,可以选容积调速回路或双泵供油回路。
2.1.3速度换接回路
由于系统各阶段对换接的位置要求不高,所以采用由行程开关发讯控制二位二通电磁阀来实现速度的换接。
2.1.4平衡及锁紧
为了克服滑台自重在快下过程中的影响和防止在上端停留时重物下落,必需设置平衡及锁紧回路。
根据上述分析,至少有两种方案可以满足系统要求。
(1)用变量泵供油和容积调速回路调速,速度换接用二位二通电磁阀来实现,平衡和锁紧用液控单向阀和单向背压阀。
系统的机械特性、调速特性很好,功率损失较小,但是系统价格较贵。
(2)用双泵供油,调速回路选节流调速回路,平衡及锁紧用液控单向阀和单向背压阀实现。
系统的机械特性、调速特性不及第一种方案,但其经济性很好,系统效率高。
2.2方案的确定
综上所述,考虑到系统的流量很大,变量泵不好选,第二种方案的经济性好,系统效率高,因此从提高系统的效率,节省能源的角度考虑,采用单个定量泵的、供油方式不太适,宜选用双联式定量叶片泵作为油源,所以选第二种方案。
第3章总体设计
3.1负载分析
3.1.1工作负载
其垂直上升工件的重力为5500N,滑台的重力为1000N,
所以,工作负载:
3.1.2磨擦负载
由于导轨角为90度,工件为垂直起升,所以垂直作用于导轨的载荷可由其间隙和结构尺寸可根据公式
计算出滑台垂直作用于导轨的压力约为120N,取
由公式:
Ff=fFn/sin(a/2)则有:
静摩擦负载
静摩擦负载的大小与两物体间的正压力Fn成正比:
动磨擦负载
动磨擦负载的大小有物体接触面的正压力成正比:
3.1.3惯性负载
惯性负载的方向与加速度a=△V/△t方向相反,即当物体受力改变起运动状态时候,由于摩擦的惯性,物体必将给施力物体一反作用力;这个反作用力称为惯性负载,物体的惯性负载力的大小等于质点的质量与加速度的乘积,方向与物体加速度的方向相反,作用在使其改变运动状态的施力物体上:
加速:
减速:
制动:
反向加速:
反向制动:
根据以上计算,考虑到液压缸垂直安放,其重量较大,为防止因自重而下滑,系统中应设置平衡回路。
因此在对快速向下运动的负载分析时,就不考虑滑台2的重量(
)。
液压系统启动时:
液压系统总负载:
F=FL+Ffs=6500+33.94=6533.94N
液压缸推力:
F=6533.94/0.91=7180.15N
液压系统加速时:
液压系统总负载
=6500+16.97+928.57=7445.54N
液压缸推力:
F=7445.54/0.91=8181.91N
液压系统总负载:
=6500+16.97=6516.97N
液压缸推力:
F=6516.97/0.91=7161.51N
液压系统减速时:
液压系统总负载:
=6500+16.97+752.14=5764.83N
液压缸推力:
F=5764.83/0.91=6334.98N
液压系统慢上时:
液压系统总负载:
=6500+16.97=6516.97N
液压缸推力:
F=6516.97/0.91=7161.51N
液压系统制动时:
液压系统总负载:
=6500+16.97-176.43=6340.54N
液压缸推力:
F=6340.54/0.91=6536.63N
液压系统反向加速时:
液压系统总负载:
F=Ffd=Fa4=16.97+1459.98=1476.15N
液压缸推力:
F=1476.15/0.91=1521.80N
液压系统快下时:
液压系统总负载:
F=Ffd=16.97N
液压缸推力:
F=16.97/0.91=18.65N
液压系统制动时:
液压系统总负载:
F=Ffd=Fa5=16.97-1459.18=-1442.21N
液压缸推力:
F=-1442.21/0.91=-1584.85N
则液压缸各阶段中的负载如表3-1表示
表3-1液压缸各阶段负载
工况
计算公式
总负载F/N
缸推力F/N
启动
7180.15
加速
7445.54
8181.91
快上
6516.97
7161.51
慢上
6516.97
7161.51
制动
6340.54
6536.63
反向加速
1476.15
1521.80
快下
16.97
18.65
制动
-1442.21
-1584.85
3.2负载图和速度图的绘制
图3-1液压缸各阶段负载和速度
按照前面的负载分析结果及已知的速度要求、行程限制等,绘制出负载图及速度图如上页图3-1所示:
3.3液压缸主要参数的确定
液压缸:
是液压系统中的执行元件,它的职能是将液压能转换成机械能。
液压缸的输入量是流体的流量和压力,输出的是直线运动速度和力。
液压缸的活塞能完成直线往复运动,输出的直线位移是有限的。
结构形式可分为:
缸体固定和活塞杆固定
缸体固定-工作台往复运动范围为活塞有效行程的三倍,(占地面积较大)。
常用于小型设备。
活塞杆固定-工作台往复运动的范围为活塞有效行程的两倍(活塞杆固定,缸筒与工作台相连,进出油口可以做在活塞杆的两端(油液从空心的活塞杆中进去)。
也可以做在缸筒的两端(需用软管连接)。
动力由缸筒传出。
常用于中、大型设备上。
单活塞杆式液压缸的特点:
往复运动速度不同-常用于实现机床的快速退回和慢速工作进给。
两端面积不同,输出推力不相等。
无杆腔吸油时-工作进给运动(克服较大的外负载)。
有杆腔进油时-驱动工作部件快速退回运动(只克服摩擦力的作用)。
工作台运动范围等于活塞杆有效行程的两倍。
缸体和底盖焊接成一体。
活塞靠支撑环导向用Y型密封圈密封,活塞与活塞杆用螺纹连接。
活塞杆靠导向套导向,用V型密封圈密封。
端盖和缸体用螺纹连接,螺母用来调整V型密封圈的松紧。
缸底端盖和活塞杆头部都有耳环,便于铰接。
因此这种液压缸在往复运动时,其轴线可随工作需要自由摆动。
综上所述,选择单活塞杆式液压缸
3.3.1初选液压缸的工作压力
根据分析此设备的负载不大,按类型属机床类,所以初选液压缸的工作压力为20MPa
3.3.2计算液压缸的尺寸
其所需面积由工作过程中液压缸的最大负载F=8181.91N与初选液压缸的工作压强P=20mpa的比值决定:
所以其直径为:
按标准取:
125mm。
所以其最大工作压力为:
P=F/A=8181.91/(3.14×(D/2)^2)=1.630mpa
根据快上和快下的速度比值来确定活塞杆的直径:
按标准取:
100mm。
所以液压缸的有效作用面积为:
无杆腔面积
有杆腔面积
3.3.3液压缸的实际工作压强
液压系统启动时:
P=F/A=7180.15/5024MPa=1.429MPa
液压系统加速时:
P=F/A=8181.91/5024MPa=1.630MPa
液压系统快上和慢上时:
P=F/A=7161.54/5024MPa=1.425MPa
液压系统减速时:
P=F/A=6334.98/5024MPa=1.26MPa
液压系统第一次制动时:
P=F/A=6536.63/5024MPa=1.301MPa
液压系统反向加速时:
P=F/A1521.80/5024MPa=0.443MPa
液压系统在快下时:
P=F/A=18.65/3436MPa=0.0054MPa
液压系统第二次制动时:
P=F/A=-1584.85/5024MPa=-0.461MPa
3.3.4活塞杆稳定性校核
因为活塞杆总行程为423mm,而且活塞杆直径100mm,
不需要进行稳定性校核。
3.3.5求液压缸的最大流量
3.3.6液压缸的功率
液压系统快上时:
P=FV=7161.51×42/60W=5013.06W
液压系统慢上时:
P=FV=7161.51×8/60W=952.48W
液压系统在快下时:
P=FV=18.65×65/60W=20.51W
其他过程中由于油处于停顿中,所以液压缸流量为0;此时功率也为0。
3.3.7绘制工况图
工作循环中各个工作阶段的液压缸压力、流量和功率如表3-2所示
表3-2工作循环中各个工作阶段的液压缸压力、流量和功率
工况
压力
流量
功率
P/W
启动
1.429
____
____
加速
1.630
____
____
快上
1.425
211.00
5013.06
减速
1.26
____
____
慢上
1.425
40.91
952.48
第一次制动
1.301
____
____
反向加速
0.443
____
____
快下
0.0054
226.78
20.51
第二次制动
-0.461
___
____
由此表绘出液压缸的压力,流量,功率的工况图,如下页图3-3所示。
钢筒壁及法兰的材料选45钢;
活塞杆材料选45钢。
液压缸的内径D和活塞杆直径d都已在前面的计算中算出:
,
D=125mm;d=100mm。
图3-3系统工况图
3.3.8液压缸其它参数的选择
(1)活塞的最大行程L已由要求给定为450mm。
(2)小导向长度当活塞杆全部外伸时,从活塞支承面中点到导向套滑动面中点的距离称为最小导向长度H。
如果导向长度过小,将使液压缸的初始挠度增大,影响液压缸的稳定性,因此设计时必须保留有一最小导向长度。
对于一般的液压缸,当液压缸的最大行程为L,缸筒直径为D时,最小导向长度为:
所以取;H=95mm。
(3)活塞的宽度的确定
活塞的宽度由液压缸筒的直径D来确定:
取其系数为0.7;
则B=0.7D=56mm
(4)活塞杆长度的确定
活塞杆的长度
活塞杆的长度应大于最大工作行程、导向长度、缸头、缸盖四者长度之和。
既L,=L+H+L头+L盖=450+95+66+82=655mm.
但是为了使其能够工作,必须和工作台连接,所以还应支出一部分。
考虑实际工作环境和连接的需要,取这部分长度为50mm.
液压缸筒长度的确定
L=活塞最大行程+活塞宽度+活塞杆导向长度+活塞杆密封长度。
L=450+56+95+10mm=611mm
液压缸总长度的确定
L=655+248mm=813mm
3.4液压系统图的拟定
液压系统图的拟定,主要是考虑以下几个方面的问题:
3.4.1供油方式
从工况图分析可知,该系统在快上和快下时所需流量较大,且比较接近。
在慢上时所需的流量较小,因此从提高系统的效率,节省能源的角度考虑,采用单个定量泵的供油是不合适的,宜选用双联式定量叶片泵作为油源。
3.4.2调速回路
由工况图可知,该系统在慢速时速度需要调节,考虑到系统功率小,滑台运动速度低,工作负载变化小,所以采用调速阀的回油节流调速回路。
3.4.3调速换接回路
由于快上和慢上之间速度需要换接,但对换接的位置要求不高,所以采用由行程开关发讯控制二位二通电磁阀来实现速度的换接。
3.4.4平衡及锁紧
为防止在上端停留时重物下落和在停留斯间内保持重物的位置,特在液压缸的下腔(无杆腔)进油路上设置了液控单向阀;
本液压系统的换向阀采用三位四通Y型中位机能的电磁换向阀。
3.4.5液压系统图
图3-4液压系统原理图
1—滤油器2—双联页片泵3—单向阀4—行程阀5—溢流阀6—三位四通电液换向阀7—液控单向阀8—单向背压阀9—电磁换向阀10—调速阀
3.4.6液压系统工作过程
快上时,电磁阀有电,两泵同时工作,液压油经过电换向阀6、液控单向阀7、背压阀8,流入无杆腔,再经过单向电磁阀9、换向阀6回油箱。
慢上时,活塞走到420mm处,压下行程开关,行程阀4换接,同时使电磁有电,大流量泵经过它卸荷,只有小流量泵供油,调速阀10调节回油。
工作速度下降。
快下时,行程阀复位,电磁阀有电,双泵同时供油,经过换向阀6(左位)、调速阀10、背压阀8、液控单向阀7、换向阀6回到油箱。
3.5液压元件的选择
3.5.1确定液压泵的型号
液压泵是液压系统的动力元件,其作用是将原动机的机械