3万吨合成氨变换毕业设计副本.docx
《3万吨合成氨变换毕业设计副本.docx》由会员分享,可在线阅读,更多相关《3万吨合成氨变换毕业设计副本.docx(39页珍藏版)》请在冰豆网上搜索。
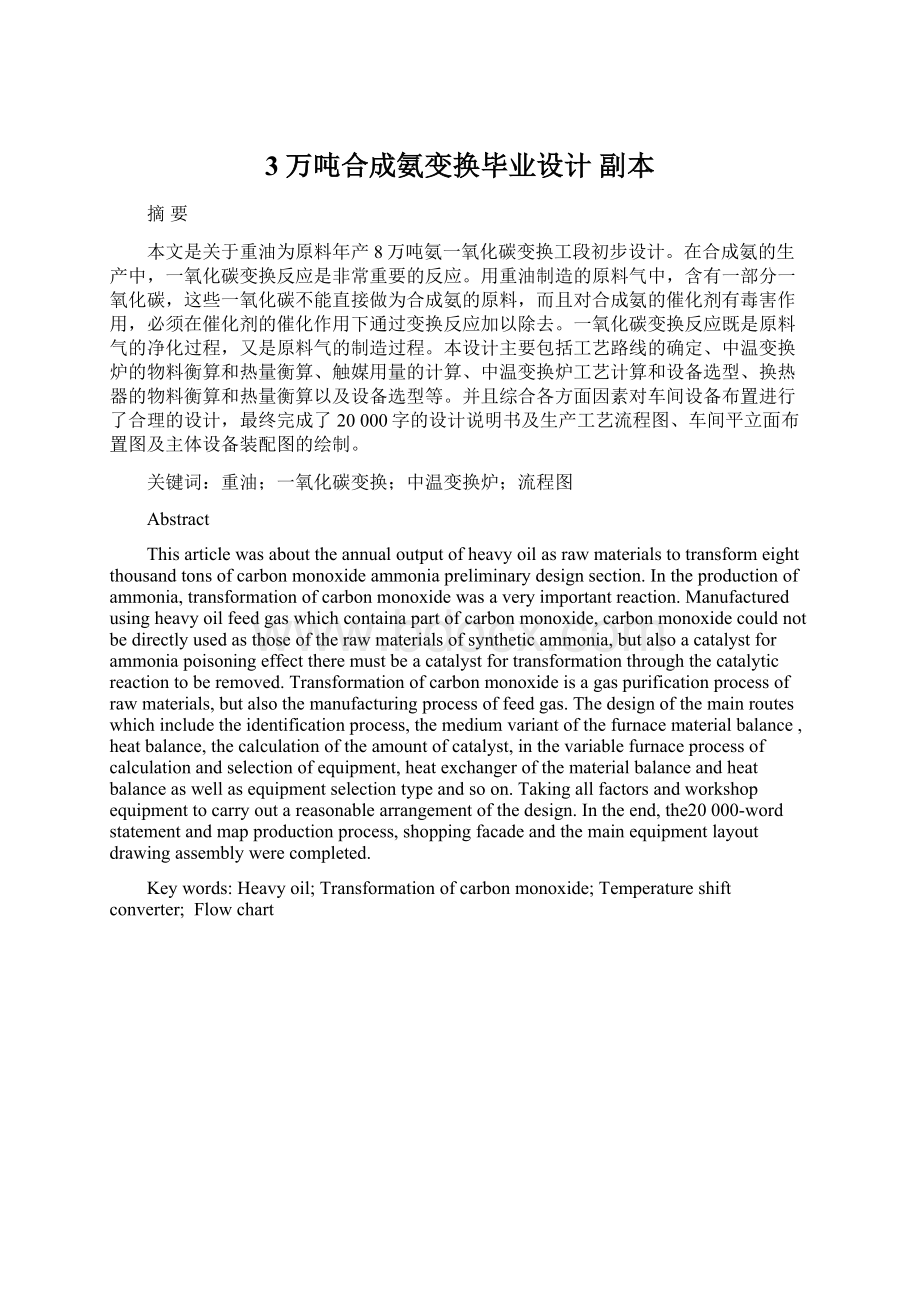
3万吨合成氨变换毕业设计副本
摘要
本文是关于重油为原料年产8万吨氨一氧化碳变换工段初步设计。
在合成氨的生产中,一氧化碳变换反应是非常重要的反应。
用重油制造的原料气中,含有一部分一氧化碳,这些一氧化碳不能直接做为合成氨的原料,而且对合成氨的催化剂有毒害作用,必须在催化剂的催化作用下通过变换反应加以除去。
一氧化碳变换反应既是原料气的净化过程,又是原料气的制造过程。
本设计主要包括工艺路线的确定、中温变换炉的物料衡算和热量衡算、触媒用量的计算、中温变换炉工艺计算和设备选型、换热器的物料衡算和热量衡算以及设备选型等。
并且综合各方面因素对车间设备布置进行了合理的设计,最终完成了20000字的设计说明书及生产工艺流程图、车间平立面布置图及主体设备装配图的绘制。
关键词:
重油;一氧化碳变换;中温变换炉;流程图
Abstract
Thisarticlewasabouttheannualoutputofheavyoilasrawmaterialstotransformeightthousandtonsofcarbonmonoxideammoniapreliminarydesignsection.Intheproductionofammonia,transformationofcarbonmonoxidewasaveryimportantreaction.Manufacturedusingheavyoilfeedgaswhichcontainapartofcarbonmonoxide,carbonmonoxidecouldnotbedirectlyusedasthoseoftherawmaterialsofsyntheticammonia,butalsoacatalystforammoniapoisoningeffecttheremustbeacatalystfortransformationthroughthecatalyticreactiontoberemoved.Transformationofcarbonmonoxideisagaspurificationprocessofrawmaterials,butalsothemanufacturingprocessoffeedgas.Thedesignofthemainrouteswhichincludetheidentificationprocess,themediumvariantofthefurnacematerialbalance,heatbalance,thecalculationoftheamountofcatalyst,inthevariablefurnaceprocessofcalculationandselectionofequipment,heatexchangerofthematerialbalanceandheatbalanceaswellasequipmentselectiontypeandsoon.Takingallfactorsandworkshopequipmenttocarryoutareasonablearrangementofthedesign.Intheend,the20000-wordstatementandmapproductionprocess,shoppingfacadeandthemainequipmentlayoutdrawingassemblywerecompleted.
Keywords:
Heavyoil;Transformationofcarbonmonoxide;Temperatureshiftconverter;Flowchart
第1章总论
1.1概述
1.1.1一氧化碳变换反应的意义与作用
在合成氨的生产中,一氧化碳变换反应是非常重要的反应。
用重油制造的原料气中,含有一部分的一氧化碳,这些一氧化碳不仅不能直接做为合成氨的原料,而且对氨合成中的催化剂有毒害作用,因此必须在催化剂的作用下通过变换反应加以除去。
在一定的条件下,利用一氧化碳和水蒸汽等摩尔反应生成二氧化碳和氢气,除去大部分一氧化碳,使一氧化碳含量净化到3%左右,然后进入铜洗进一步的清除。
所以通过一氧化碳变换反应既能把一氧化碳转化为易在下游除去的二氧化碳同时又生产有效组分氢气或生产具有较高H2/CO2比的合成气。
变换反应既是原料气的净化过程,又是原料气制造的继续过程。
一氧化碳加压变换,可以提高生产能力,降低能源消耗,节约触媒,提高经济效益[1]。
1.1.2国内外研究现状
许多氮肥厂都对一氧化碳变换系统采取了一些相应的改进措施,力争降低能量的消耗和成本。
常用的有采用中温变换串联低温变换工艺,使用新型高活性的低温催化剂,常压变换变为加压变换等。
从我国目前的情况看,新建工厂或是改建的工厂基本都采用加压变换。
随着新型耐硫催化剂的开发成功,八十年代中期开发了中变串低变工艺;为了利用低变的低温高活性,九十年代初期开发了全低变工艺;为了克服全低变工艺不能长期稳定运行的缺点,九十年代中期又开发了中-低-低工艺。
其后的十年间是全低变工艺和中-低-低工艺推广和完善的过程。
国外大部分使用宽温区的催化剂,变换催化剂从传统类型Fe-Cr系变换为Co-Mo系。
国外合成氨的规模一般都比较大,不管是原料还是操作压力的选择都与我国的中小型氮肥厂大不相同[2]。
1.2设计依据
本次设计是按照学校下发的《齐齐哈尔大学本科生毕业设计(论文)工作手册》和齐齐哈尔大学化学工程与工艺专业下达的《化学工程与工艺专业毕业教学环节文件编》。
并依据以下国标进行详细的设计:
ZBY47-87、GB457-4460-84、GB100-93、GB50160-92、HGJ211-85。
1.3厂址的选择
1.3.1厂址选择
厂址选择是工业基本建设中的一个重要环节,是一项政策性,技术性很强,牵涉面很广,影响面很深的工作。
正确的选择厂址是保障化工生产的重要前提。
化工厂的选择应根据城市规划和工业区的要求,按经批准的设计计划任务书指定的地理位置选择厂址。
选择厂址应综合分析与权衡厂址的地形条件以及有关的自然和经济资料,进行多方案的技术经济、安全可行性的比较,合理选择,作到安全可靠。
从全局出发,正确处理工业与农业、城市与乡村、远期与近期以及协作配套等各种关系,并因地制宜、节约用地、不占或少占耕地及林地。
同时,还要做到有利生产、方便生活、便于施工,并提供有多个可供选择的方案进行比较和评价。
厂址的安全可靠要涉及工程地质条件的优劣、厂区范围能否适应平面布置和安全距离的要求、自然灾害的威胁程度及抗衡的可能性、能否避免由于邻近企业发生事故时而引起此生灾害、能否便于治理三废以及同外部的联系与协调等因素。
选择厂址的基本安全要求是:
土地面积与外形,能满足根据生产工艺流程特点合理布置建筑物、构筑物的需要,即厂区总图的要求;地形应力求平坦而略有坡度(一般以不超过千分之五至十为宜),以减少土地平整的土方工程量,有利于厂区排水和运输;有良好的工程地质条件,厂址不应设在有滑坡、断层、泥石流、岩溶、地下水位过高,有强烈地震以及地基上承载力低于0.1MPa的地区;应尽可能接近水源地,并便于污水的排放和处理;应靠近主要原料燃料的供应源,靠近动力供应中心,并有利于和有关联企业的协作;应注意与附近交通的联系,尽量接近铁路、水路、公路,以缩短货运距离;对排放有毒废水、废气、废渣和噪声严重的工厂,不要设在城镇居民区的上风向、水源上游。
和人口密集之处;重要项目应远离机场,避开国际航线,且不宜选在水库、水力枢纽、大桥、大工厂等明显目标附近;厂区和居住区应保持一定的间隔距离,设置必要的卫生防护地带;要满足当地航空站,通讯发射台等对间隔距离和技术上的要求。
1.3.2方案比较
根据以上原则和依据,本设计厂址初步设在在齐齐哈尔市南郊区的下风向处。
齐齐哈尔铁路比较发达,又靠近大庆油田,故生产用的原料重油可以方便快捷的得到。
另外,黑龙江又是产粮大省,因此化肥的需求量较大,故有较好的市场。
水也是合成氨的重要原料,齐齐哈尔靠近嫩江,水源丰富[3]。
1.4设计规模与生产制度
1.4.1设计规模
重油为原料年产8万吨氨车间一氧化碳变换反应工段初步设计,年生产时间为7200小时。
1.4.2生产制度
本工厂实行倒班制度,初步拟定为五班三倒。
在生产过程中,一定要加强安全防范意识,严格按照化工行业安全生产规范来操作。
注意防火、防爆、防泄漏等一系列危险情况的发生。
要做到时时注意安全,事事想着安全,做到早预报,做处理,尽量避免重大事故的发生。
1.5原料与产品规格
1.5.1原料规格
原料由上一工段重油氧化所制得,氮气来自空气,其余气体均为在氧化过程中所产生。
原料气组分如表1-1所示。
表1-1原料气组分
组分
CO2
CO
H2
N2
CH4
O2
合计
%
8.090
29.444
39.261
21.533
1.282
0.390
100
1.5.2产品规格
经过变换反应后,气体中CO含量应低于3%。
第2章工艺设计与计算
2.1工艺原理
半水煤气中CO是在一定温度和有催化剂存在的条件下与水蒸气发生变换反应,生成CO2和H2,同时产生大量的反应热,这是一个等体积可逆的放热反应:
CO+H2O
CO2+H2+Q
在变换触媒中CO变换反应的原理一般认为是水分子首先被催化剂的活性表面所吸附,然后分解成氢和吸附态的氧,氢脱附后进入气相,当气相中的CO撞击到氧原子的吸附层后,即被氧化为CO2,离开催化剂表面,催化剂则复原,然后其表面与水分子作用重新生成氧原子的吸附层,如此反应反复进行,催化剂用[K]表示,则化学反应过程表示如下:
[K]+H2O
[K]·H2O
[K]+H2O
[K]·O+H2O
[K]·O+CO
[K]+CO2
从反应式看出,催化剂本身不发生氧化还原作用,而只是提供吸附反应物和活性吸附中心[4]。
2.2工艺路线的选择
目前的变化工艺主要有:
多段中温变换,中温串连低温变换,全低变这3种工艺。
本设计参考齐齐哈尔市黑龙江化工集团的生产工艺,选用多段中温变换工艺[5]。
2.3工艺流程简述
中温变换工艺大都采用加压变换,本流程的气压是1.75MPa。
采用低温高活性中变催化剂B113型,降低了工艺上对过量蒸汽的要求。
由造气来的半水煤气给原料气压缩后,进入半水煤气分离器分离掉油后进入饱和塔接触传热,然后进入第一、第二换热器进行换热,达到工艺要求后进入中变炉一段进行反应,再依次进入二、三段进行反应。
反应结束,经过第一、第二交换器使气体达到工艺要求,进入下一工段。
在各段之间配有冷凝水作为冷激线,调节汽气比和温度。
系统中的热水在饱和塔、热水塔以及水加热器中循环,定期排污,保持循环水的质量和水的平衡。
图2-1变换工段流程图
2.4工艺参数
2.4.1原料气体组分
表2-1原料气组分
组分
CO2
CO
H2
N2
CH4
O2
合计
%
8.090
29.444
39.261
21.533
1.282
0.390
100
2.4.2工作压力
进料气压力:
1.5-2.0MPa
进料汽压力:
2.5MPa
2.4.3工作温度
进中变炉一段催化剂的气体温度:
320℃
出中变炉一段催化剂的气体温度:
450℃
进中变炉二段催化剂的气体温度:
350℃
出中变炉二段催化剂的气体温度:
400℃
进中变炉三段催化剂的气体温度:
350℃
出中变炉三段催化剂的气体温度:
380℃
出系统变换气(干基)中CO含量:
低于3%[6]
2.4.4计算基准
以1t/h氨为计算基准,则
V变=
=3059.6Nm3/h
假设生产过程中的物料损失10%,则
V变=3059.6
(1+10%)=3373.8Nm3/h=150.62kmol/h
2.5物料衡算
原料气组分如表2-2。
表2-2原料气组分
组分
CO2
CO
H2
N2
CH4
O2
合计
%
8.090
29.444
39.261
21.533
1.282
0.390
100
Nm3/h
272.82
993.394
1324.568
726.480
43.298
13.240
3373.8
Kmol/h
12.179
44.348
59.133
32.432
1.933
.591
150.616
2.5.1变换气量及变换率计算
设氢与氧在变换炉一段催化剂作用下完全燃烧生成水,由O2+2H2→2H2O可知,实际参加CO变换反应的半水煤气量为:
3373.8-3V氧=3373.8-13.24
=3334.1Nm3/h
则干变换气量为:
V变=V+V·YCO·X(2-1)
V—参加反应的班水煤气体积,Nm3/h
YCO—参加反应的半水煤气中CO含量,%
CO变换率为:
(2-2)
其中:
YCO=
X=
则:
V变=3334.1
(1+87.31%
29.79%)=4201.288Nm3/h=187.56kmol/h
CO变换总量为:
3334.1
29.7%
87.31%=867.188Nm3/h=38.714kmol/h
变换气中CO的量为:
3334.1
29.79%-8671.88=126.040Nm3/h=5.627kmol/h
2.5.2总蒸汽量计算
中温变换炉出口变换气温度为38℃,平衡温距去24℃,则t=404℃
CO变换反应式为:
CO+H2O=CO2+H2
设起始浓度为:
abcd
则a=29.444,b=8.090,d=39.261
CO反应量为:
CO=29.444
87.310%=25.708Nm3/h(每100Nm3干半水煤气)[7]
查表,得404
时,Kp=11.441
=11.441
将a,c,d的值代入上式,得b=75.683,即汽/气=0.75683上式中,O2为半水煤气中氧的浓度,为0.390需要总蒸汽量(包括喷的冷凝水量)为:
158.616×75.683%=113.991kmol/h[8]
2.5.3中变炉物料衡算
(1)一段物料衡算
入炉蒸汽比计算
设CO在一段催化剂层转化率为60.073%,且O2在一段催化剂与氢气完全燃烧生成水,则CO反应量为:
CO反应=29.444×60.073%=17.685Nm3/h(每100Nm3干半水煤气)
CO总反应量=3373.8×17.688%=596.758Nm3/h=26.64kmol/h
气体出一段催化剂层温度为450℃,平衡温距取18℃,出口气平衡温度为428℃。
查表得,468℃的Kp=6.405,则
(2-3)
将a,c,d即O2代入上式,得b=36.137.即汽/气=0.36137
入炉蒸汽量为3373.8×0.36137=1219.190Nm3/h=54.43kmol/h
入炉湿气组分如表2-3。
表2-3入炉湿气组分
组分
CO2
CO
H2
N2
CH4
O2
H2O
合计
%
5.940
21.629
28.839
15.817
0.943
0.288
26.654
100
Nm3/h
272.82
993.394
1324.57
726.480
43.298
13.240
1219.19
4592.93
Kmol/h
12.129
44.348
59.133
32.432
1.933
0.591
54.428
205.044
此时,a=21.629,b=26.645,c=5.940,d=28.839,O2=0.288
变换率计算
设450℃CO变换为Xp,查表得450℃时,Kp=7.455则:
(2-4)
将入炉气有关组分代入上式得,Xp=62.698%
实际变换率为平衡变换率的百分数:
×100%=95.813%
则,出一段催化剂层干气体量为:
3373.8+596.758-13.204×3=3930.838Nm3/h=175.484kmol/h
其中,剩余CO=993.394(1-0.60073)=396.636Nm3/h=17.707kmol/h
CO2=272.82+993.394×0.60073=869.578Nm3/h=38.820kmol/h
H2=1324.568+993.394×0.60073=1894.846Nm3/h=84.59kmol/h
出一段干气如表2-4。
表2-4出一段催化剂层干气组分
组分
CO2
CO
H2
N2
CH4
合计
%
22.13
10.09
48.20
18.48
1.10
100
Nm3/h
869.578
396.636
1894.546
726.480
43.298
3930.838
kmol/h
38.820
17.707
84.591
32.432
9.933
175.484
出一段催化剂层剩余蒸汽量为:
1219.190-596.758+13.240×2=648.912Nm3/h=28.969kmol/h
出一段湿气如表2-5。
表2-5出一段催化剂层湿气组分
组分
CO2
CO
H2
N2
CH4
H2O
合计
%
18.989
8.661
41.374
15.863
0.943
14.169
100
Nm3/h
869.578
396.846
726.480
43.298
43.298
648.912
457.750
kmol/h
38.826
17.707
84.591
32.432
1.933
28.969
204.453
(2)二段物料衡算
二段入炉蒸汽比计算
表2-6二段入炉干气组成
组分
CO2
CO
H2
N2
CH4
合计
%
22.13
10.09
48.20
18.48
1.10
100
Nm3/h
869.578
396.636
1894.546
726.480
43.298
3930.838
kmol/h
38.820
17.707
84.591
32.432
9.933
175.484
设CO在二段催化剂层转化为50%,则二段催化剂层中CO反应量为:
CO反应量=10.09×0.5=5.045Nm3/h(每100Nm3干半水煤气)
CO总反应量=3930.838×0.05045=198.311Nm3/h=8.853kmol/h
气体出二段催化剂层温度为400℃,平衡温距取18℃,出口气平衡温度为418℃,查表得418℃时的Kp=9.977
此时:
(2-5)
a=10.09,c=22.13,d=48.20
Kp=
解得,b=33.792,即入二段催化剂层汽/气=0.33792
二段入炉蒸汽量为:
3930.838×0.00792=1328.309Nm3/h=59.3kmol/h
表2-7二段入炉湿气组分
组分
CO2
CO
H2
N2
CH4
H2O
合计
%
16.534
7.542
36.029
13.814
0.823
25.257
100
Nm3/h
869.518
396.636
1894.846
726.898
43.298
1328.309
5259.147
kmol/h
38.820
17.707
84.591
32.432
1.933
59.300
234.783
平衡变换率计算以及出二段催化剂层气体的计算
设400℃时,CO平衡变换率为Xp,400℃时,Kp=11.911
(2-6)
a=7.542,b=25.257,c=16.534,d=36.029
将a,b,c,d代入(1-6)
=11.911
解得Xp=55.843%
实际变换率为平衡变换率的百分数:
出二段催化剂层干气体量为:
3930.838+198.34=4129.174Nm3/h=184.338kmol/h
其中:
CO2=869.578+396.636×0.5=1067.898Nm3/h=47.67kmol/h
CO=396.636(1-0.5)=198.33Nm3/h=8.854kmol/h
H2=1894.846+396.636×0.5=2093.168Nm3/h=93.445kmol/h
出二段催化剂层干气组分如表2-8。
表2-8出二段催化剂层干气组分
组分
CO2
CO
H2
N2
CH4
合计
%
25.862
4.803
50.692
17.594
1.049
100
Nm3/h
1067.898
198.330
2093.168
726.880
43.298
4129.174
kmol/h
47.674
8.854
93.445
32.432
1.933
184.338
出二段催化剂层剩余蒸汽量为:
1328.309-198.311=1129.998Nm3/h
出二段催化剂层湿气组分如表2-9。
表2-9出二段催化剂层湿气组分
组分
CO2
CO
H2
N2
CH4
H2O
合计
%
23.305
3.770
39.800
13.814
0.823
21.486
100
Nm3/h
1067.898
198.320
2093.168
726.480
43.298
1129.998
5259.172
kmol/h
47.674
8.854
93.445
32.432
1.933
50.446
234.784
(3)三段物料衡算
三段入炉蒸汽比计算
表2-10三段入炉干气组分
组分
CO2
CO
H2
N2
CH4
合计
%
25.862
4.803
50.692
17.594
1.049
100
Nm3/h
1067.898
198.330
2093.168
726.880
43.298
4129.174
kmol/h
47.674
8.854
93.445
32.432
1.933
184.338
设CO在三段催化剂层转化率为36.5%,则三段催化剂层中CO反应量为:
CO=4.803×0.365=1.753Nm3/h(每100N