E型电击垫片冲压模毕业设计.docx
《E型电击垫片冲压模毕业设计.docx》由会员分享,可在线阅读,更多相关《E型电击垫片冲压模毕业设计.docx(16页珍藏版)》请在冰豆网上搜索。
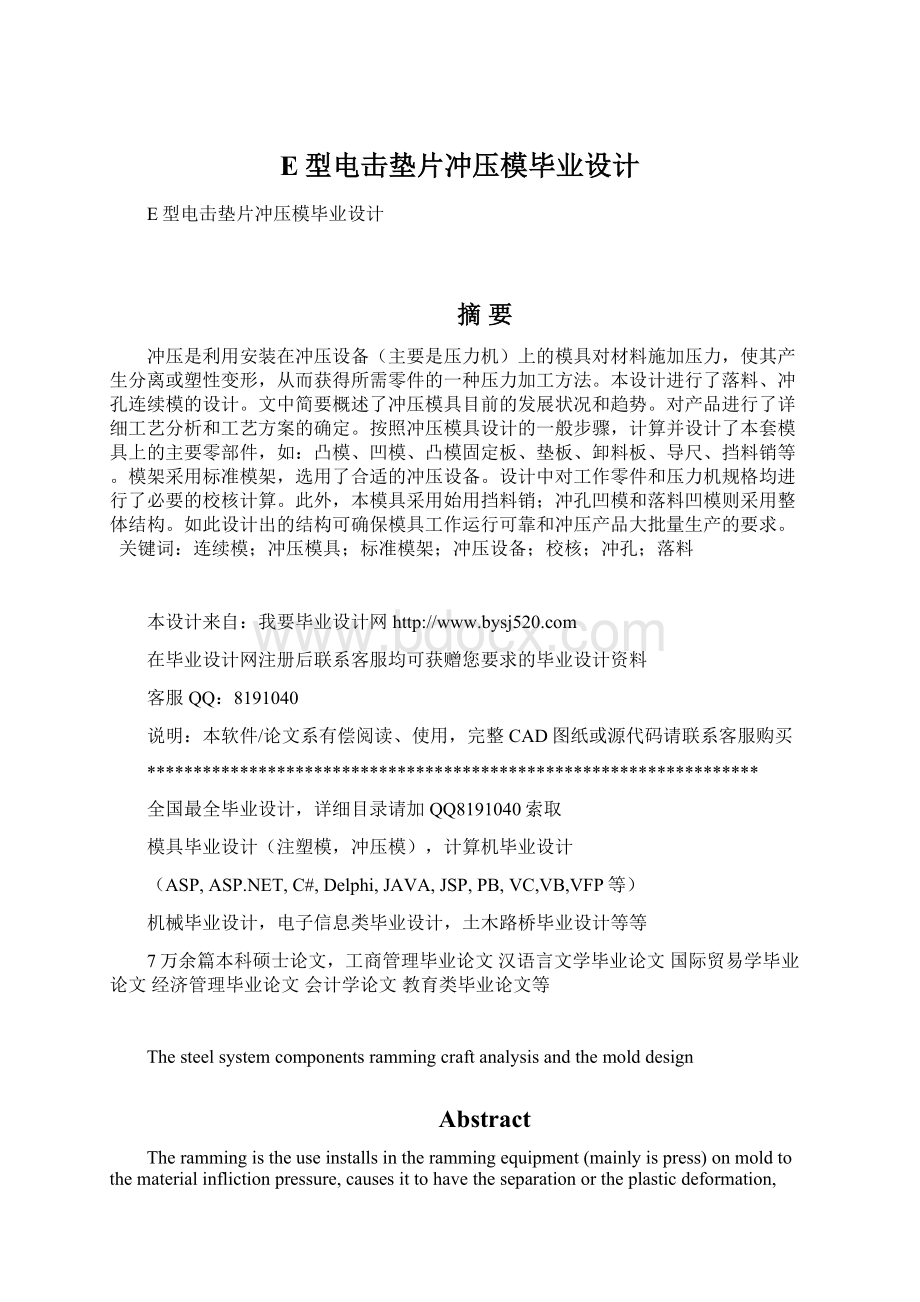
E型电击垫片冲压模毕业设计
E型电击垫片冲压模毕业设计
摘要
冲压是利用安装在冲压设备(主要是压力机)上的模具对材料施加压力,使其产生分离或塑性变形,从而获得所需零件的一种压力加工方法。
本设计进行了落料、冲孔连续模的设计。
文中简要概述了冲压模具目前的发展状况和趋势。
对产品进行了详细工艺分析和工艺方案的确定。
按照冲压模具设计的一般步骤,计算并设计了本套模具上的主要零部件,如:
凸模、凹模、凸模固定板、垫板、卸料板、导尺、挡料销等。
模架采用标准模架,选用了合适的冲压设备。
设计中对工作零件和压力机规格均进行了必要的校核计算。
此外,本模具采用始用挡料销;冲孔凹模和落料凹模则采用整体结构。
如此设计出的结构可确保模具工作运行可靠和冲压产品大批量生产的要求。
关键词:
连续模;冲压模具;标准模架;冲压设备;校核;冲孔;落料
本设计来自:
我要毕业设计网
在毕业设计网注册后联系客服均可获赠您要求的毕业设计资料
客服QQ:
8191040
说明:
本软件/论文系有偿阅读、使用,完整CAD图纸或源代码请联系客服购买
******************************************************************
全国最全毕业设计,详细目录请加QQ8191040索取
模具毕业设计(注塑模,冲压模),计算机毕业设计
(ASP,ASP.NET,C#,Delphi,JAVA,JSP,PB,VC,VB,VFP等)
机械毕业设计,电子信息类毕业设计,土木路桥毕业设计等等
7万余篇本科硕士论文,工商管理毕业论文汉语言文学毕业论文国际贸易学毕业论文经济管理毕业论文会计学论文教育类毕业论文等
Thesteelsystemcomponentsrammingcraftanalysisandthemolddesign
Abstract
Therammingistheuseinstallsintherammingequipment(mainlyispress)onmoldtothematerialinflictionpressure,causesittohavetheseparationortheplasticdeformation,thusobtainsneedsthecomponentsoneshapingmethod.Thisdesigncarriedonfellthematerial,thepunchholescontinualmolddesign.Inthearticlehasbrieflyoutlinedtherammingmoldatpresentdevelopmentconditionandthetendency.Hascarriedonthedetailedcraftanalysisandthecraftplandeterminationtotheproduct.Accordingtogeneralstepwhichtherammingmolddesigns,calculatedandhasdesignedonthissetofmoldmainsparepart,forexample:
Theraisedmold,theconcavemold,theraisedmolddeadplate,thebackingstrip,unloadtheyardlumber,leadtheruler,keepoffthematerialtosellandsoon.Thepouldframeusesthestandardpouldframe,hasselectedtheappropriaterammingequipment.Inthedesignhascarriedontheessentialexaminationcomputationtotheworkcomponentsandthepressspecification.Inaddition,thismoldusesthebeginningwithtokeepoffthematerialtosell.;Thepunchholesconcavemoldandfallsthematerialconcavemoldtousetheoverallconstruction.Sodesignsthestructuremayguaranteethemoldworkmovementreliableandtherammingproductmassproductionrequest.
Keyword:
Continualmold;Rammingmold;Standardpouldframe;Rammingequipment;Examination;Punchholes;Fallsthematerial
目录
摘要I
AbstractII
第1章绪论1
1.1技术上1
1.2经济上1
1.3连续模的分类:
3
第2章分析零件工艺性5
2.1分析零件的工艺性5
2.2排样方案设计6
2.2.1步距与定距精度的确定10
第3章压力和压力中心11
3.1压力和压力中心的计算11
3.1.1冲裁力的计算:
11
3.1.2卸料力的计算:
12
3.2压力机的选择13
第4章模具工作部分尺寸的计算15
4.1冲裁工艺尺寸的计算15
4.1.1冲裁间隙的确定:
15
第5章模具结构的设计17
5.1模具总体结构形式17
5.2工艺零件的设计17
5.2.1凸、凹模的设计:
18
5.2.2定位零件的设计:
20
5.3导向与卸料装置的设计22
5.3.1导板结构形式22
5.4凸凹模固定板的设计24
5.4.1固定板24
5.5模架的选择25
5.5.1模架25
5.5.2模架的技术要求26
5.5.3导柱与导套的选用27
5.6导向零件的设计28
5.6.1导料板的设计28
5.7辅助零件的设计29
5.7.1垫板29
5.7.2模柄29
5.7.3紧固与安装要求30
5.7.4限位销31
5.8模具零件的技术要求31
第6章模具装配32
第7章结论33
第8章附录A模具设计时须考虑的安全措施33
第9章附录B防止冲压事故的安全装置35
9.1分析35
9.2防止冲压事故的安全装备36
参考文献38
致谢39
第1章绪论
冲压加工是利`用安装在冲压设备上的冲模对材料施加压力,使其产生分离或塑性变形,从而获得一定尺寸、形状和性能的零件加工方法。
材料、模具和冲压设备是冲压加工的三要素。
由于冲压加工通常是在室温下进行的,所以也被称为冷冲压。
冲压加工与其他加工方法相比,具有如下优点:
1.1技术上
1)在材料消耗不大的前提下,制造出的零件质量轻、刚度好、精度高。
由于在冲压过程中材料的表面不受破坏,使得制件的表面质量较好,外观光滑美观。
并且经过塑性变形后,金属内部的组织得到改善,机械强度有所提高。
2)在压力机的简单冲击作用下,一次工序即可完成由其他加工方法所不能或难以制造完成的较复杂形状零件的加工。
3)制件的精度较高,且能保证零件尺寸的均一性和互换性。
不需进一步的机械加工即可以满足一般的装配和使用要求。
1.2经济上
1)原材料是冶金厂大量生产的廉价的轧制板材或带材。
2)采用适当的冲压工艺后,可大量节约金属材料,可以实现少切屑和无切屑的加工方法。
材料利用率一般可达75%~85%,因而制件的成本相应地比较低。
3)节省能源。
冲压时可不需加热,也不像切削加工那样将金属切成碎屑而需要消耗很大的能源。
4)生产率高。
每分钟一台冲压设备可生产零件从几件到几十件。
目前的高速冲床生产率则每分钟高达数百件甚至一千件以上。
5)操作简单,便于组织。
在大批量的生产中,易于实现机械化和自动化,进一步提高劳动生产率。
6)对操作人员的技术要求不高。
当生产发展需要时,用短期培训的方法即可解决操作人员不足的矛盾。
冲压加工也有其不足之处,主要缺点为:
1)需要有专用的模具,其制造周期长、费用高。
因此,在生产批量小时,经济上不合适。
2)需要有制作精度较高、相适应于冲压工艺要求(满足相应的应力状态、符合一定的变形要求)的模具。
因此,有时不能制造出精度要求极高的制件。
冲裁模的结构形式很多,按工序的组合方式分,有单工序模、级进模和复合模。
级进模,又称为多工位级进模、连续模、跳步模,级进模是在单工序模基础上发展起来的一种多工序、高效率冲模,是技术密集型模具的重要代表,是冲模发展方向之一。
在压力机的一次行程中,级进模在依次分布于条料送进方向的几个工序上分别完成一系列冲裁工序,条料从第一工位到最后工位相继成形,因此压力机每动作一次即可获得一个完整的工件或工序件。
一般来说,无论冲压零件形状怎样复杂,冲压工序怎样多,均可用一副级进模冲制完成。
连续模有如下特点:
1)连续模是连续冲压的多工序冲模。
在一副模具内可以包括冲裁、弯曲、拉深、成形等多道工序。
生产过程相当于每次行程中冲制一个工件或工序件,因此具有比复合模更高的劳动生产率,适用于大批量生产。
2)连续模冲压可以减少设备数量和模具数量,减少车间的占地面积,省去半制品运输及存储仓库。
3)连续模利用卷料或带料,可以实现自动送料、自动出料、自动叠片等功能,便于实现冲压生产的自动化。
4)连续模工序可以分散,不必集中在一个工位,因此可以解决复合模“最小壁厚”的问题。
且模具强度较高,寿命也较长。
5)连续模属自动化冲模,在加工中不需要手工操作,因此人的身体部位不必进入危险区域,具有操作安全的特点。
6)连续模生产的工件和产生废料多数往下漏,因此可以采用高速压力机生产。
7)连续模结构复杂,制造精度高,周期长,成本高,维护困难。
8)由于各工序是在不同的工位上完成的,因此定位产生的累计误差会影响工件的精度,所以连续模生产的工件精度不高。
9)连续模多用于生产批量大,精度要求不高,需要多工序冲裁的小工件加工。
1.3连续模的分类:
连续模按模具的设计方法可以分为以下两种:
(1)封闭形孔连续式级进模
这种级进模的各个工作形孔(除定距形孔外)与被冲零件的各个形孔以及零件的外形(对于弯曲件即是零件展开外形)的形状完全一样,并把它们分别设置在一定的工位上,材料沿各工位连续冲压,最后得到一个个冲压零件或半成品。
用这样方法设计的级进模称为封闭形孔连续式级进模。
封闭形孔连续式级进模精度偏低,而且产生累积误差,所以只适合冲制一些形状简单、精度在IT12~IT14的零件。
采取一些措施后,可以冲制IT10级精度的零件。
如果零件的形状复杂,凸模和凹模的加工就困难。
形状特别复杂的零件,其封闭形孔的凸、凹模往往无法加工。
所以这种模具的局限性较大。
(2)分断切除多段式级进模
这种级进模是对冲压零件较为复杂的异形孔和整个零件外形是采取分断开切除多余废料的方式进行的。
也就是说,在前一工位先切除一部分余料,在以后的工位再切除一部分余料;而对于零件的一些简单形孔,模具上的相应形孔可与零件上的形孔做成一样。
经过逐工位的连续冲制,最后就能获得一个个完整的零件或半成品。
分断切除多段式级进模的工位数较封闭形孔连续式级进模要增加很多。
但是在分断切除余料的过程中,就可以伴随着对零件进行弯曲、拉深、成形等冲压加工,所以对于形状非常复杂,甚至包含多种冲压工序的冲压零件,在设计级进模时,都是按分断切除多段式级进模的设计思路进行设计的。
连续模按模具中所包含冲压工序的性质及其加工工步的排列顺序主要分为以下几钟:
(1)单纯冲裁连续模按条料排样形状又可分为落料连续模、冲裁连续模、剪断连续模等三种;
(2)冲裁弯曲连续模;
(3)冲裁拉深连续模;
(4)冲裁成形连续模;
在一副连续模中,一般弯曲、拉深和成形并不单独存在,因此对于冲裁、弯曲、拉深和成形混合存在的情况,又可详细分为冲裁弯曲拉深连续模、冲裁弯曲成形连续模、冲裁拉深成形连续模和冲裁弯曲拉深成形连续模等几类。
连续模的应用:
连续模在生产上虽然效率高,但其冲制工件时材料的利用率不高,模具制造、维护困难以及成本较高等特点也限制了它的应用。
一般应用连续模生产时必须具备冲压件本身的适用性、机床设备性能以及技术力量等条件。
对于冲压件本身来说,一是被加工的工件产量和批量要足够大,以便以较低的单件成本维持稳定而持久的生产;二是工件形状复杂,凸模或凹模型腔难以加工或其结构尺寸难以满足强度要求而需要将工序分解。
对于机床设备来说,必须具有能承受模具连续作业的足够刚性、功率和精度,具有较大的工作台面、良好可靠的制动系统。
因此连续模多用于生产批量大,精度要求不高,需要多工序冲裁的小工件加工。
由上可知,多工位级进模的结构比较复杂,模具设计和制造技术要求较高,同时对冲压设备、原材料也有相应的要求,模具的成本高。
因此,在模具设计前必须对工件进行全面的分析,然后合理确定该工件的冲压成形工艺方案,正确设计模具结构和模具零件的加工工艺规程,以获得最佳的技术经济效益。
第2章分析零件工艺性
2.1分析零件的工艺性
如图2.1所示,该零件为垫片,其材料为T62(黄铜),抗剪强度为275~392(
)抗拉强度为260~300﹝
﹞.根据零件形状和材料性质判断该零件为冲压零件,其结构简单,精度要求较低,可用一般精度冲模冲出。
图2.1
材料厚度为0.5(
),大批量生产。
冲压该零件的所需的基本工序为冲孔和落料。
由此冲压该零件的工艺方案有以下两种。
方案一:
可以用连续模,先冲孔再落料。
方案二:
可以用复合模,一次成型。
考虑到生产量较大,选用连续模更为方便快捷。
由于零件形状较小。
所以采用多行排列,最终将工艺方案确定为:
1冲两个长为17
,宽为3
的长方形孔,侧刃用于定位,
2空位,
3落料
零件的整个加工过程共分三个工位
其示意图如下
3落料2空位1侧刃,冲孔
图2-2
2.2排样方案设计
多工位级进模的设计,首先要设计条料排样图,这是设计多工位级进模的重要依据.设计排样图时,必须全面地考虑以下因素:
1)生产能力与生产批量:
设计多工位级进模时,要力求使企业的生产能力与生产批量相平衡.当企业的生产能力(冲床数量、冲床吨位、自动化程度、工人技术水平高低等)与生产批量相矛盾时,要力求采用双排或多排排样,在模具上提高效率.如果上产能力与生产批量相一致时,则以单排排样为最好.但要在排样图设计中考虑提高材料利用律,模具制造力求简化,提高模具刚性,延长模具使用寿命.
2)送料方式:
自动送料一般适合于高速冲床冲制,也可用一般冲床冲制,而手工送料只适合一般冲床冲制.高速冲压的多工位级进模,用自动送料机构送料,用导正钉精确定距;手工送料则多用侧刃粗定距,用导正钉精确定距.
3)冲压力的平衡:
在设计条料排样图时,应考虑整个冲压加工的压力中心力求与模具中心一致,不应有过大的差异,一般地说模具中心与冲压中心偏移最大不得超过L/6(或B/6),如下图所示:
图2.3
多工位级进模在生产过程中产生侧向力是不可避免的.在设计条料排样图时,必须充分考虑在整个冲制过程中产生侧向力的部位、方向、大小和影响,力求采取抵消侧向力的措施.
4)模具的具体结构和加工工艺性:
在设计条料排样图时,必须考虑模具的具体结构,要把每一个环节,每一个具体部分的装配关系、装配顺序,以至对每部分的加工方案等都要考虑全面.这样设计出来的条料排样图才能够指导模具设计.
5)被加工材料:
①材料的供料状态:
多工位级进模最适宜以成卷的带料供料.这样可以进行连续、自动、高速冲压.当不能实现带料供料时,采用板料剪裁成的料条供料,则自动送料就有困难;
②被加工材料的力学性能:
选用材料的牌号必须能够充分满足冲压工艺的要求;
③材料的辗压纹向:
冲压件的弯曲线与材料的纹向有密切关系.弯曲线与材料纹向垂直,压出的零件质量稳定光滑.当两者平行,对某些材料或弯曲半径很小时,零件弯曲部分会出现裂纹,甚至发生断裂;
④材料利用率:
材料利用率的高低是直接影响成本的主要因素之一.一般来说多工位级进模的材料利用率是偏低的。
在设计多工位级进模时,很重要的是尽最大的努力使废料达到最小限度.
6)冲件的毛刺方向:
在设计多工位级进模条料排样图时,对冲件毛刺方向掌握的原则是:
①当冲件图纸提出毛刺方向要求时,无论条料排样是双排还是多排,应保证各排冲出的零件毛刺方向一致;
②对于带有弯曲加工的冲压零件,在设计条料排样图时,应使毛刺面保留在弯曲件的内侧,这样不仅零件外形压制美观,而且弯曲部位不会出现边口裂纹.
③在考虑分断切除余料时,会出现在一个冲压件的周边毛刺方向不一致的现象,这是不允许的现象.如果在排样图设计时确实解决不了周边毛刺方向不一致的问题,要在设计模具时考虑在某部位进行倒冲等措施来满足这一要求.
7)正确安排侧刃孔和导正钉孔:
侧刃孔是用来控制步距的工艺性用孔,以便用它来保证每一工步送进的距离;导正钉孔与导正钉的位置的安排对多工位级进模的精确定位是很关键的.
8)凹模应有足够的强度
多工位级进模凹模的工作形孔以及其它各种安装孔很多,在设计条料排样图时,必须全面考虑凹模强度,尤其在高速冲压的场合下
9)弯曲、成形部位邻近孔冲压加工应考虑的问题:
靠近弯曲部分的孔,应先加工孔后压弯,这样能简化模具设计.如果孔的位置精度要求很高,孔的形状要求较严,先冲孔就很难保证孔位精度(压弯时必然引起孔的变形).为了保证孔位与孔形的正确,就应先压弯后冲孔.孔在弯曲时避免变形的条件:
h≥1.5t+r
10)分断切除过程零件形状连接方式的选择:
多工位级进模在冲制过程中,分断切除余料后,各段之间连接成一个完整的冲压零件。
因此,一个很重要的问题就是如何做到各段间的连接得十分平直或圆滑,是保证冲件质量的一个重要环节。
由于多工位级进模工位比较多,模具制造误差,步距间的误差累计,都有可能导致在逐工位冲切余料后,形孔各段的连接处不平直、不圆滑、错乐出现尖角和塌角等质量问题。
这些疵病是由于设计条料排样图时在选择连接方式时,考虑不周而造成的,只要能够合理地选择连接方式,再加上必要的措施,是完全能够克服的。
多工位级进模的分段切除的排样图,其连接方式基本上可以分为三种:
即搭接、平接和切接。
搭接最有利于保证冲件的连接质量。
平接和切接容易出现上述疵病。
11)载体:
载体是条料在送进过程中,经过不断地冲切余料,条料内连接冲压零件运载前进的这部分材料。
条料载体分为:
双侧载体,单侧载体和中间载体三个基本形式。
双侧载体送进平稳,但材料利用率较低,中间载体一般适用于对称性零件,单侧载体一般应用于条料厚度为0.5mm以上的冲压件。
特别对于零件一端或几个方向带有弯曲的场合。
12)条料在送进过程中应避免阻碍现象产生。
综合上述因素,为了简化级进模结构,降低制造成本,保证条料送进刚性和稳定性,减小级进模工作面积,减少级进模发生故障及返修,提高材料利用率,拟采用单排少废料排样。
若采用双排排列或斜排排列会使弯曲凸模发生结构干涉问题,同时人为地增加了设计和制造成本。
排样的选择要根据零件的形状尺寸和冲裁的形式,直排样为最佳的选择,其利用率较高。
由于零件的形状较为复杂,所以在确定搭边值时按r>2t的圆角,查表确定工件间搭边值α=6
侧面α1=6
其图示如下:
图2-4
条料宽度的确定要保证冲裁时工件周边有足够的搭边值,最大条料宽度要能在冲裁时顺利地在导板之间送进,并与导板之间有一定的间隙
式中:
B——条料宽度的基本尺寸(
);
D——条料宽度方向零件轮廓的最大尺寸(
);
a——侧面搭边(
);
△——条料宽度方向的单向(负向)偏差(
);
b——条料与导料板之间的间隙
△——查《冲压工艺与模具设计》表3-20得,△=0.5
b-----查表《冲压工艺与模具设计》表3-11得,b=0.5
条料宽度:
B=(3D+4α1+6△+2b)0-△=220-0.5(
)
2.2.1步距与定距精度的确定
级进模的步距是确定条料在模具中每送进一次,所需要向前移动的固定距离。
1.步距基本尺寸的确定:
对于单排排列的排样步距,基本尺寸为:
S=A+
=22+1=23
(2-1)
2.步距精度的确定:
由邱永成-《多工位级进模设计》一书,得多工位级进模步距精度的经验公式为:
δ=±
×k(2-2)
式中:
δ——多工位级进模步距对称偏差值(
);
β——冲件沿条料送进方向最大轮廓基本尺寸精度提高三级后的实际公差值,β取0.13
;
n——模具设计的工位数,n=3
k——修正系数,查表3-1得,k=1.10
.
所以,δ=±
×k==±0.034
(2-3)
板料规格选用:
0.5
×800
×1800
材料利用率的计算:
η=
=
=
(2-4)
S2——冲裁件的面积(
)
B——条料宽度(
)
n——一个步距内冲裁件的数目
L——步距(
)
送料方式:
由于对零件精度要求不高,模具结构采用侧刃粗定位,导正销精确定位,使用手工送料。
第3章压力和压力中心
3.1压力和压力中心的计算
3.1.1冲裁力的计算:
模具共有五个冲裁区,冲裁力由下式计算:
F=K×L×t×τ=1.3×【23×2+4+8.5×8+6+18×2】×260×0.5=27.04(KN)
(3-1)
式中:
L——冲裁件周边长度(
)
t——材料厚度(
)
τ——材料抗剪强度(Mpa)
K——系数。
考虑到模具刃口的磨损,模具间隙的波动,材料力学性能的变化及材料厚度偏差等因素,取K=1.3
各冲裁区只是冲裁线长度不同,材料剪切强度极限τ=260Mpa,板料厚度t=0.5
3.1.2卸料力的计算:
=208(N)(3-2)
式中:
——卸料力系数,查《冲压工艺与模具设计》表3-9得,K
=0.05
由于模具采用弹性卸料装置和下出料方式,所以总冲裁力:
=27.212(KN)(3-3)
模具压力中心的计算:
冲模的压力中心由图的对称性可知压力中心必在x轴上
图3-1
B图左右对称,压力中心再b处。
A图左右不对称左边受力边长:
12
.右边受力边长:
18
有杠杆原理
解之得:
A图压力值
;
B图压力值
由杠杆原理(x-3.4)
代值得:
X=38.86
压力中心为:
(38.86,0)
传统算法:
(3-4)
与前一种算法结果相同。