拉延模具设计.docx
《拉延模具设计.docx》由会员分享,可在线阅读,更多相关《拉延模具设计.docx(33页珍藏版)》请在冰豆网上搜索。
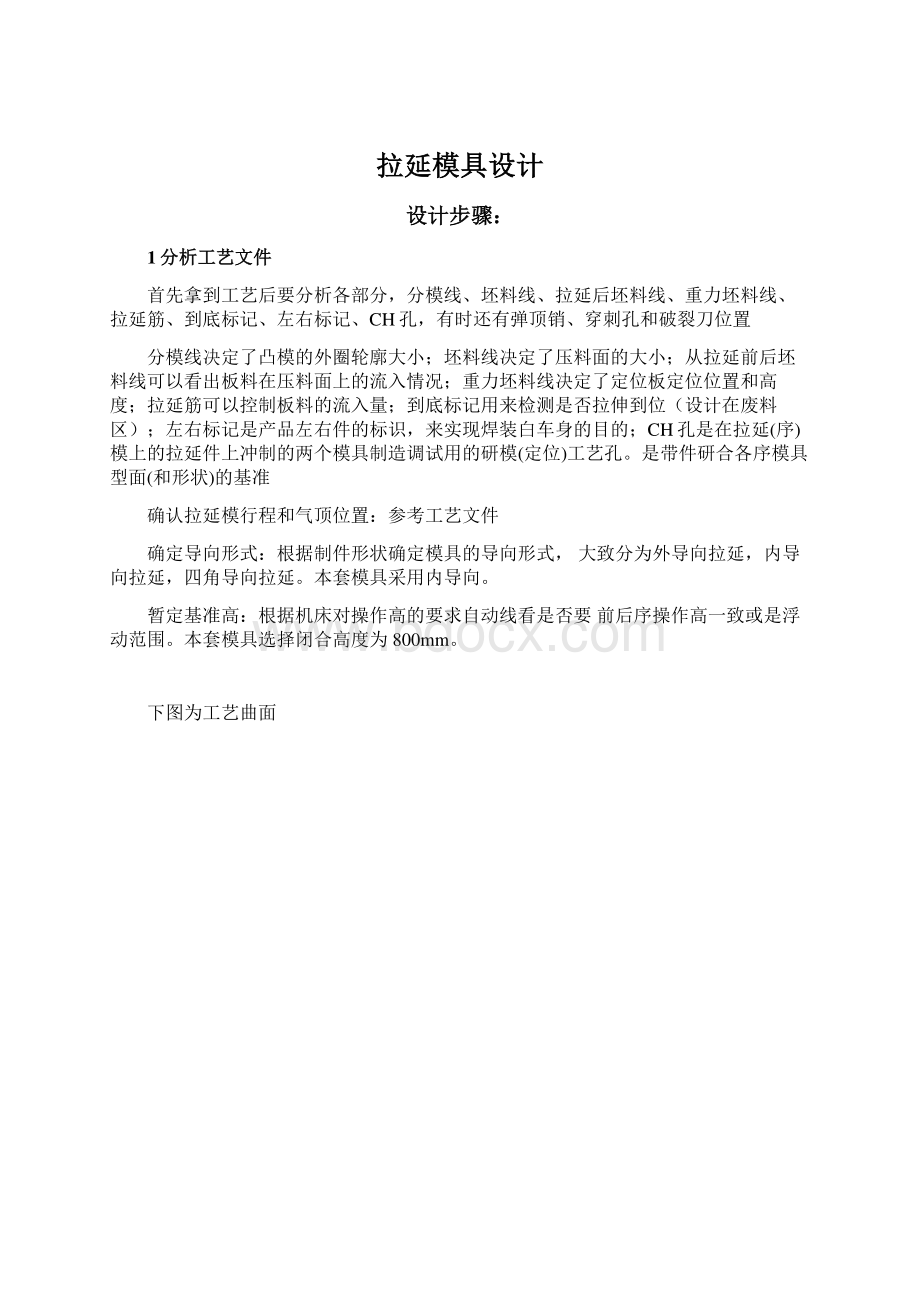
拉延模具设计
设计步骤:
1分析工艺文件
首先拿到工艺后要分析各部分,分模线、坯料线、拉延后坯料线、重力坯料线、拉延筋、到底标记、左右标记、CH孔,有时还有弹顶销、穿刺孔和破裂刀位置
分模线决定了凸模的外圈轮廓大小;坯料线决定了压料面的大小;从拉延前后坯料线可以看出板料在压料面上的流入情况;重力坯料线决定了定位板定位位置和高度;拉延筋可以控制板料的流入量;到底标记用来检测是否拉伸到位(设计在废料区);左右标记是产品左右件的标识,来实现焊装白车身的目的;CH孔是在拉延(序)模上的拉延件上冲制的两个模具制造调试用的研模(定位)工艺孔。
是带件研合各序模具型面(和形状)的基准
确认拉延模行程和气顶位置:
参考工艺文件
确定导向形式:
根据制件形状确定模具的导向形式,大致分为外导向拉延,内导向拉延,四角导向拉延。
本套模具采用内导向。
暂定基准高:
根据机床对操作高的要求自动线看是否要前后序操作高一致或是浮动范围。
本套模具选择闭合高度为800mm。
下图为工艺曲面
2图层的设置
用ug2.0打开工艺曲面进入建模模块。
把第1层的工艺面复制到11层把第2层的胚料线,分模线复制到12层。
3面的缝合
打开11层,其它层全部关闭。
用缝合命令缝合曲面缝合的时候注意不要直接点击确定,应该点击应用看他是否报错如果报错看是那些地方有错然后更改
更改好以后再缝补,检查报错,如果没报错,再拉伸一个通过曲面的体A。
用缝补好的曲面裁剪A,如果成功说明缝补成功。
下面是封面操作截图:
注意缝合公差
红点的地方表示有错
修改完成无报错
裁剪实体成功,删除实体保存一次图档,进入下一步
4偏置工艺面
用大致偏移命令
偏移Z向-60.-50和60的三个面。
下面是操作截图:
三个偏置的面如图所示
5凸模本体的制作
把12层设置为工作层,其它层关闭。
投影分模线到XY平面如图
用分模线拉伸实体上下各500mm如图:
把11层设置为可选用工艺面把刚拉伸的实体上部分裁减掉如图:
把得到的实体移动到62层。
然后用分模线拉伸一个上下各500mm,里外分别10mm的实体环如图:
用向Z方向偏置-50mm的面裁减掉这个体的上部分如图:
把所得到的实体移动到62层。
然后用分模线拉伸上下各500mm的实体,然后把实体往里收缩60如图:
用向Z方向偏置-60的面把实体上部分裁剪掉如图:
把所得到是实体移动到62层。
然后把62层设置为工作层其他层关闭。
把62层里面的三实体求差得到凸模本体如图:
6凹模本体的制作
把12层设置为工作层其他层关闭,拉伸胚料线,上下各500mm得到实体,再把所得到的实体前后左右四面往外生长20mm如图:
打开11层用工艺面把这个实体分割成上下两块,把下面的那块移动到52层做压片圈用。
把余下的部分用网上偏置60mm的面裁剪掉上半部分得到上模本体如图:
用分模线拉伸一个上下各200里外各25的实体用来做随形筋,然后用工艺面把所拉伸的实体下部分裁剪掉剩下的部分和上模本体求和得到上模,把上模移动到71层。
如图:
7压片圈本体的制作
把52层设置为工作层,打开12层,用分模线拉伸一个上下各500mm得到实体,再把得到的实体前后左右的轮廓往外长3mm,然后把这个实体和做上模剩下的实体求差如图:
打开11层用往下偏置60的面把这个实体的下部分裁剪掉,得到如图的实体:
用分模线拉伸上下各500mm往外13mm和63mm的环,如图:
用工艺面裁掉这个实体的上部分,余下部分和压边圈求和得到压边圈本体如图:
保存一次。
8气顶位置的确定
点击一下装配命令调出装配工具条如图:
把机床文件E4S600-MBC.prt装配到绝对坐标系上面装配好以后如图:
把里面的实体全部隐藏,把12层里面的分模线调出来,是界面里面只有白色的气顶位置圈和分模线。
计算气顶个数。
由工艺文件得知压边力是120T每个气顶承受4T,总共要30个气顶。
在分模线外侧附近均匀的选择30个气顶(使得每个象限的气顶数相等)选择好以后用装配工具条里面的WAVE几何连接器命令把气顶位置的线抽出来,然后消除参数把机床文件删除。
得到如图的气顶位置圆:
9导板的安装
装配导板标准件MWP.PRT文件到工作坐标如图:
导板的尺寸和布局:
导板高度应该要比压片圈行程高60mm,由工艺文件可知这套模具压片圈行程是110mm,考虑到后面要把导板滑配往下延长10mm,所以我们只要选择150mm的导板就可以了;导板的数量是每边两个。
模具左右长度大概是1540mm,前后长度大概是970mm。
共边的所有导板宽度和应该大于该边长的1/5,所以左右两边的导板宽度应该100mm,前后应该选择150mm,考虑到这八个导板的尺寸要相同所以我们选择一个折中的宽度-125mm。
操作方法把MWP设置为工作部件,然后点击工具里面的部件族,在弹出的对话框里面单选择最下面的编辑,在弹出的excel文件里面选择导板尺寸然后选择好以点击excel的第二行确定你选择的尺寸,然后点击最上面的部件族,在探出的对话宽里面选择应用值。
界面如图:
导板的定位:
把组件设置为工作部件。
调整导板到凸模的适当位置。
导板到相邻边的距离应介入所在边边长的1/6-1/4之间,导板应该在俩气顶中间位置;导板安装台加工面距离分模线的距离应该在3-5mm之间方便加工,导板安装台上表面距离凸模刃口下表面最低点的距离是25-30,再这套模具中我把导板底面距离原点的Z向的距离定为360mm。
调整好第一个,然后复制粘贴7个。
调整方法和第一个相同,保证八个导板在同一个高度。
全部调整好以后装配工具条里面的WAVE几何连接器命令抽出所有装配体,然后消除参数,把装配体删除掉。
如图:
把导板安装台和和凸模布尔加在一起(注意如果导板安装台底部和凸模有缝隙应该补齐)黄色的导板移动到64层绿色的滑配移动到71层把凸模底面和导板安装台底面平齐。
制作
10凸模螺钉台制作
在点击预设置,在弹出的菜单里面选择工作平面,然后把鼠标位置设为5的倍数如图:
凸模螺钉台的尺寸是50*50*10的一个平台。
它制作在凸模螺钉台躲孔里面,躲空的尺寸如图:
用画直线命令在凸模正中间画一条直线如图:
用这条直线往下拉伸一个高200,左右宽度各50的体如图:
设置这个体的下表面距离凸模下表面的距离为40,它的后表面距离凸模前表面的距离为100,它的上表面比凸模刃口底面稍微低一点点,把它的前面缩到稍微高出凸模前面的位置。
把凸模隐藏,把实体的左右面从实体的后面开始拔模30°把实体的上面绕着前上边线往下转30°;复制一个实体;把复制的实体的除前面的面以外的5个面往外长40mm;把凸模显示出来,把大实体的前面平齐到凸模前面;大实体和凸模求和,小实体再和求和结果求差得到如图的实体:
同样的方法在凸模后面中央,四个角上分别再做一个这样的躲孔。
做好以后结果如图:
在躲孔底面正中间做好凸模螺钉台并涂上加工色如图:
10布置筋
筋之间的距离尽量不超过250mm,距离在60-300可以容忍,筋的厚度40mm;深度和厚度比不要大于2.5,导板后面要有筋,避免十字筋;高度大于210,宽度大于160的筋必须要有减重孔,小于这范围的尽量开出气孔(直径60的孔),不管怎么样每个腔体的四壁至少开一个通气孔或者是流水孔。
筋布置好如图:
11凸模起吊布置
起吊有2种形式:
(1)起吊螺纹孔
(2)铸入式螺孔套
具体哪种形式看客户要求
1起吊位置
起吊和翻转的对角线交点要与凸模重心重合,保证在同一高度
2起吊螺纹孔的加工面不要凸出分模线(平齐分模线就可以了)
3铸入式螺孔套要保证周围壁厚40(标准间313里面有)前后套筒同轴,所有套筒同高
选择凸模起吊的尺寸:
先用公司开发小工具计算凸模重量,选择M30的凸模起吊。
起吊的标准件是CSN.prt。
如图:
凸模起吊的安装:
安上面的要求调好位置,安装好如图:
把加工台上多出的肉剪裁掉,然后把加工台和凸模求和,圆筒后面要补肉方便铸造清沙。
把补好的肉和凸模求和,再用白色的体和凸模就差凸模起吊就制作完成了。
得到的结果如图:
12凸模定位键
前后左右各一个。
进来布置在中间,键的外面与随形筋外边平齐,但是不能和凸模螺钉孔干涉;键的四周料厚要保证40mm。
应为本套模具比较大,件我们就选择标准库中最大规格的键,导入标准件,修改尺寸的方法和滑块的装配方法一样。
公司键的标准件名是LK.prt。
布置好如图:
13压片圈二层板
把52层设置为工作层其他层关闭;隐藏压片圈;把所有滑块底面往下伸长10mm;然后把压片圈显示出来;把压片圈的底面和滑块底面平齐,这就得到了压片圈的高度。
如图:
现在开始做压片圈二层板:
俩二层板厚度都是40,上面的距离压边圈上面最低点13-15,下面的底面和压边圈底面平齐,然后用平齐命令使他们和压边圈完美结合,再和压边圈求和完成。
注意:
长度画大一点后面再来确定,宽度使得前后面距离内壁的最小距离都是200
步骤:
在X轴上画一条(-2000,2000)的直线,用这条直线拉伸一个宽1600mm厚度40mm关于XZ平面对称的体如图:
往Z轴下方移动这个体直到它距离压边圈上面最低点13-15,再调整它到原点的Z向距离是5的倍数。
调整后如图:
用压边圈底面外边线拉伸一个实体把这个板的内部裁减掉,补齐他们的缝隙,平齐一下突出的地方
补好以后把板子与压片圈求和,得到如图的效果:
测量上板上表面到压片圈下表面的Z向距离是225拉伸一个如图所示参数的体
结果如图:
用压片圈底面里面的面把这块板的内部裁减掉;然后板和压片圈求和,二层板制作完成。
得到结果如图:
14调压垫的制作
调压垫标准件的尺寸,下面有俩圆柱外面圆柱直径是80mm,里面的是70mm,俩圆柱上面就是调压垫,他的直径是60mm高度20mm,调压垫上面是一个直径80的圆柱。
标准件名是DBH.prt。
标准键图:
调压垫的布局,里面那个直径是70的圆柱距离压料面外沿的距离是25,相邻调压垫的距离是300mm-400mm,Z向定位是使得压料面外圈刚好平分调压垫。
测得压料面左右时1720mm,前后是1140,所以前后应该分别放6个调压垫,左右分别放3个调压垫,布置好了如图所示:
抽体,消除参数,删除底下那个直径80的圆柱,
(注意:
左右的调压垫决定了模具的长度,调整的时候一定要正5调)
把底下的绿色体和压片圈求和,上面绿色体将来和上模求和的移动到91层,黄色的调压垫移动到54层,。
和压片圈求和部分凸台高于50mm的要做一个比凸台低10mm厚度是40的筋如同:
15气顶的布置
模具总高度是800mm上模取190mm,压片圈高度,由上图上,凸模高度是360mm,凸模底面和滑块坐板底面平齐,滑配比坐板高20mm但是滑配往下长了10mm所以滑配比凸模高出10mm,滑配底面和压片圈底面平齐,所以压片圈的高度是350mm,模具的行程是110,气顶的行程是200mm所以气顶杆的长度是(800-190-350-90)=170(mm);气顶杆的直径上面直径是80mm下面直径是70mm。
位置前面已经定好了。
做好以后的效果如图:
16压片圈导板滑配的制作
分两种情况,第一种是滑配标准件不在气顶杆正底下,如图:
第二种就是滑配在气顶杆正底下,如图:
制作的时候注意保重40mm厚的料厚。
第一种比较好做,做出来的结果如图:
第二种情况为了避免过度的挖掉气顶杆,所以要从滑配标准件的前面开始挖空所以上面要做一个5mm的台阶减少加工面积,被挖掉的气顶杆也和滑配也要有台阶,目的也是减少加工面积,如图:
17挡料板的安装
我们公司也也做了挡料板的标准件。
尺寸选择方法,每一类型的挡料板的宽度是一样的就是高度不同,挡料板高度应该高于胚料线15-20mm。
所以布置挡料板的时候先要把胚料线的高度调好。
胚料线应该和压片圈最高点平齐,调好的结果如图:
挡料板的定位:
挡料板决定了模具上模的宽度,所以调整的时候一定要确保和上模求差的体的外面距离原点的Y向距离为5的倍数。
我们公司做的工艺和,公司标准件库里面的文件时配合好的,安装时测量好挡料板挡料面和胚料线的距离然后直接移动过去平齐就可以保证到原点的三个坐标值都是5的倍数了。
挡料板有四种前面的是导轮挡料板标准件名是TS423.prt;右边的是右挡料板标准件名是TS422-R.prt;左边的是左挡料板标准件名是TS422-L.prt;后边的是挡料板标准件库名是TS421.prt。
安装好如图:
18压片圈二层板宽度的确定
保证前后面到压片圈内圈表面的距离都在200mm以上,且压片圈前后面到原点的距离是5的倍数。
所以我这里就取后面到原点的各向距离为:
增量XC=0.000000000X=0.000000000
YC=-735.000000000Y=-735.000000000
ZC=140.000000000Z=140.000000000
我这里就取后面到原点的各向距离为:
增量XC=0.000000000X=0.000000000
YC=685.000000000Y=685.000000000
ZC=140.000000000Z=140.000000000
他们到内壁的距离均大于200mm满足条件。
19墩死垫的制作
为了使模具合模时获得刚性力,防止模具起皱。
我们在鸦片圈和下模表面直径做一个墩死垫。
做法:
在调压垫正下方,拉伸一个和调压垫安装台直径一样的圆柱(直径是70mm);合模时压片圈和下模之间的距离是40mm,墩死垫,凸出压片圈下表面18mm,凸出下模上表面20mm,他们之间有2mm的间隙。
(他的分布和调压垫一样,另外在安全平台正下方也有墩死垫,这四个墩死垫做后安全平台在做)做好以后结果如图:
20凹模高度的确定
总高度是800mm,凸模底座底面到原点的Z向距离是610mm,那么凹模上表面到原点的Z向距离=800-610=190(mm)
用约束面命令。
约束凹模随形筋上表面到原点的距离是190.这就确定了凹模的高度。
21凹模二层板的制作
下二层板高度比凹模最高点高10-15mm。
宽度先不确定,长宽稍微做大一些。
做出来的结果如图:
调出11层的工艺面把如图二层板的内部干涉部分裁剪掉然后,把二层板和凹模本体求和,处理一些求和以后上面表面的面缺陷,得到如图的结果:
把调压垫上圆柱和凹模求和,把图中蓝色的那些体和凹模求差得到挡料板躲孔,做好以后如图:
测量二层板前表面和后表面距离与挡料板躲孔之间的料厚:
前表面和前挡料板躲孔之间的料厚,
后表面和后挡料板躲孔之间的料厚,
现在开始做前后的边框筋:
前边框筋的做法。
用二层板的前表面的一条棱线拉伸一个体使得他刚好与前挡料板躲孔平齐,其厚度为40mm,然后把筋的上表面和凹模上表面平齐,最后把它和凹模本体求和。
后边框筋的做法和前边框筋的做法一样,做好以后如图:
上二层板的制作方。
分别用前后边框筋的棱线往外拉伸一个厚度是40mm长度是100mm(这个100mm是客户的要求),体然后把他们和凹模求和就得到了上二层板,再把下二层板的面和下二层板的面平齐(这就确定了模具的宽度了,测量一下前后表面Y向坐标是否是5的倍数)做好结果如图:
22导腿的制作
导腿长度至少占整体宽度的1/3,最好能做到2/5左右;
导腿宽度根据模具宽度而定,一般遵循下表:
导腿导板保证上模触料时已导入30mm即可,通常使用125mm长导板即可满足要求,保证导腿上所有导板同一安装高度,同时刃入,稳定性好;
合上模时一般要求导腿距离导板底面的距离为30mm;
有些客户要求导腿应该和产品长度一样,本套模具就是这样要求的。
本套模具产品的宽度大概是1000mm,那么我们把压片圈上导腿长度定为900mm。
本套模具的宽度是1570mm所以导腿的宽度是180,那么压片圈上导腿的宽度=导腿宽度(180)+导板厚度(20)+导板滑块厚度(10)+导板安装台厚度(10)=220(mm)。
;压片圈导腿上表面超过压片圈上表面70mm。
导腿上安装导板的尺寸是宽度为125mm的导板,导腿高度=导板安装台的高度=导板安装台的高度(160)+导板滑块低于导板的高度(10)=170。
安装导板是注意不要上下不要反了;做导腿时为了防反把左边的导腿单边加长5mm。
导板的装配,如图:
抽体消除删除装配体求和得到如同的结果: