第二节 齿轮的降噪设计汇总.docx
《第二节 齿轮的降噪设计汇总.docx》由会员分享,可在线阅读,更多相关《第二节 齿轮的降噪设计汇总.docx(31页珍藏版)》请在冰豆网上搜索。
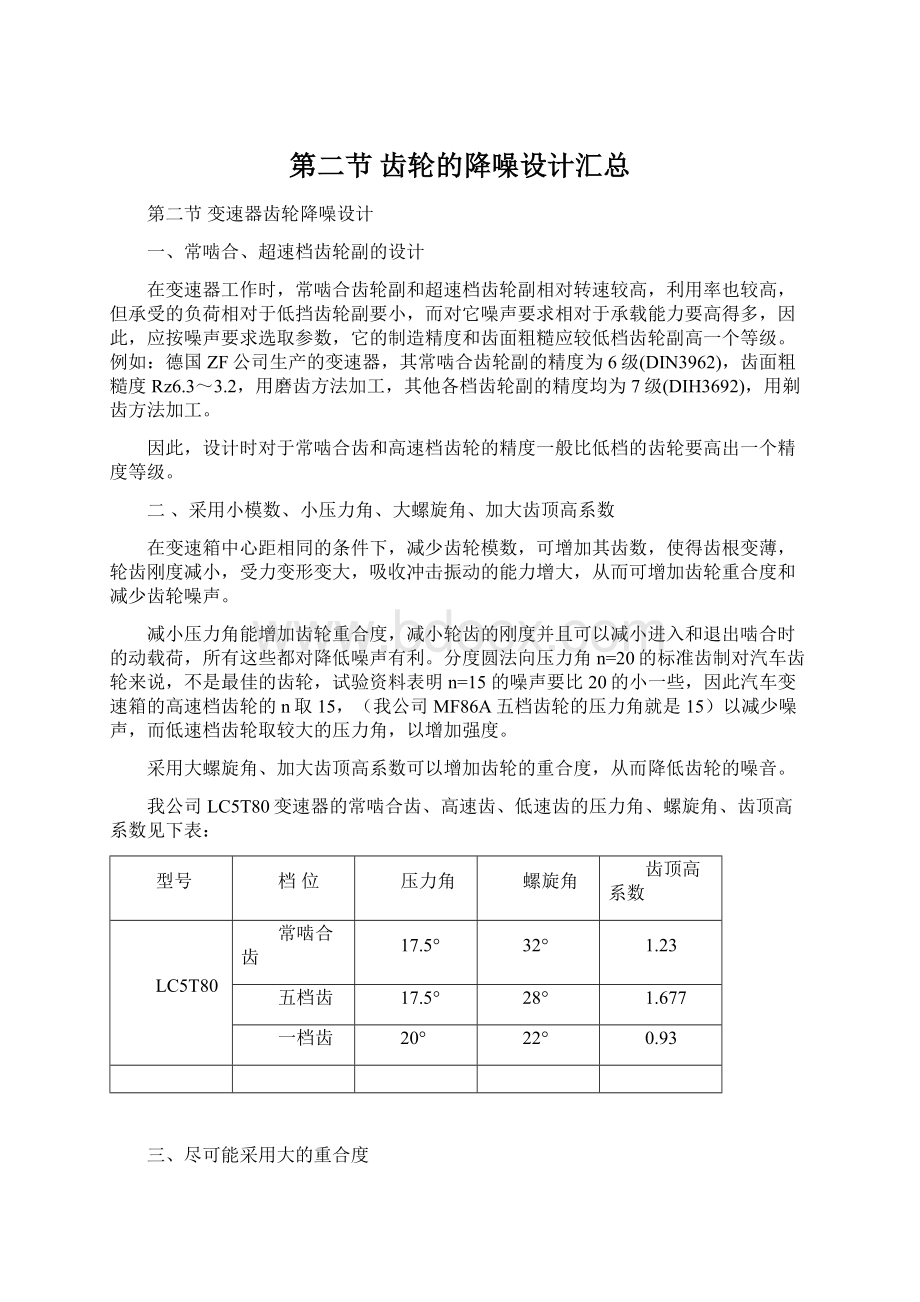
第二节齿轮的降噪设计汇总
第二节变速器齿轮降噪设计
一、常啮合、超速档齿轮副的设计
在变速器工作时,常啮合齿轮副和超速档齿轮副相对转速较高,利用率也较高,但承受的负荷相对于低挡齿轮副要小,而对它噪声要求相对于承载能力要高得多,因此,应按噪声要求选取参数,它的制造精度和齿面粗糙应较低档齿轮副高一个等级。
例如:
德国ZF公司生产的变速器,其常啮合齿轮副的精度为6级(DIN3962),齿面粗糙度Rz6.3~3.2,用磨齿方法加工,其他各档齿轮副的精度均为7级(DIH3692),用剃齿方法加工。
因此,设计时对于常啮合齿和高速档齿轮的精度一般比低档的齿轮要高出一个精度等级。
二、采用小模数、小压力角、大螺旋角、加大齿顶高系数
在变速箱中心距相同的条件下,减少齿轮模数,可增加其齿数,使得齿根变薄,轮齿刚度减小,受力变形变大,吸收冲击振动的能力增大,从而可增加齿轮重合度和减少齿轮噪声。
减小压力角能增加齿轮重合度,减小轮齿的刚度并且可以减小进入和退出啮合时的动载荷,所有这些都对降低噪声有利。
分度圆法向压力角n=20的标准齿制对汽车齿轮来说,不是最佳的齿轮,试验资料表明n=15的噪声要比20的小一些,因此汽车变速箱的高速档齿轮的n取15,(我公司MF86A五档齿轮的压力角就是15)以减少噪声,而低速档齿轮取较大的压力角,以增加强度。
采用大螺旋角、加大齿顶高系数可以增加齿轮的重合度,从而降低齿轮的噪音。
我公司LC5T80变速器的常啮合齿、高速齿、低速齿的压力角、螺旋角、齿顶高系数见下表:
型号
档位
压力角
螺旋角
齿顶高系数
LC5T80
常啮合齿
17.5°
32°
1.23
五档齿
17.5°
28°
1.677
一档齿
20°
22°
0.93
三、尽可能采用大的重合度
齿轮副的重合度越大,则动载荷越小、啮合噪声越低、强度也越高,特别是端面重合度等于2.0时,啮合噪声最低,噪声级数将急剧地减小。
由于齿轮传动时的总载荷是沿齿面接触线均匀地分布,所以在啮合过程中,随着接触线的变化,齿面受力情况也不断地发生变化,当接触线最长时齿面接触线单位长度载荷最小,当接触线最短时接触线单位长度载荷最大。
显然单位载荷变化大而快时容易产生振动,引发噪声,特别是齿面接触线最长的那一对轮齿尤甚。
对于齿轮重合度的分析有以下定义:
定义:
斜齿轮端面重合度
=K1+KP;
斜齿轮轴向重合度
=K2+KF;
斜齿轮总重合度=
+
;
式中:
K1
的整数值;Kα
的小数值;
K2
的整数值;Kβ
的小数值;
在设计斜齿轮的重合度时,应满足以下几条设计准则:
1、尽可能地使
或
接近于整数,以获得最小的噪声,只要Kα0或Kβ0一项成立即可。
2、避免采用Kα=Kβ=0.5的重合度系数,因为这时齿面载荷变化太快,齿轮啮合噪声最大。
3、当Kα=Kβ时,齿轮副的噪声也比较大。
4、总重合度系数为整数的齿轮噪声不一定小,特别是Kα或Kβ在0.3至0.7的范围内噪声较大,越接近0.5噪声越大。
5、尽可能采用大的端面重合度
,因为
对噪声的影响要比
大得多,对于汽车变速箱的高速档齿轮来说,要采用
>1.8,以获得较小的噪声,而对低速档齿轮来说,也要尽可能地采用大的
值,以降低噪声。
6、应该采用大的总重合度系数以减小接触线长度变化时引起齿面载荷变化的幅度,最好使变速箱低档齿轮的>2,高档齿轮的>3。
由研究证明,增大齿数和、减小模数、加大齿顶高系数、采用小压力角、增大螺旋角和齿面宽度等,均可达到增大重叠系数的目的。
四、采用噪声指标cg和RB来选定变位系数
(1)控制滑动比的噪声指标cg:
由于在基圆附近的渐开线齿形的敏感性非常高,曲率变化很大,齿面间的接触滑动比非常大,因此在基圆附近轮齿传递力时的变化较激烈,引起轮齿的振动而产生较大的噪声,而且齿面容易磨损,所以在齿轮设计时应使啮合起始圆尽可能远离基圆,在此推荐啮合起始圆与基圆的距离应大于0.2的法向齿距,控制滑动比的噪声指标cg的公式如下:
式中:
db基圆直径;db’相配齿轮的基圆直径;dfa啮合起始圆直径;
tn法向齿距;A齿轮中心距;D’相配齿轮的外径;t端面压力角;
在现代变速箱的设计中,为了达到良好的低噪声性能,各档齿轮的控制滑动比的噪声指标一般都要小于1.0,而采用细高齿制来降低噪声的设计方案,这时的噪声指标cg就有可能大于1.0,所以对于这种齿制的齿轮可采用cg<1.10的设计要求。
对于高速档齿轮来说,降低噪声是首选目标,所以其cg必须设计的小一些。
例:
LC5T80变速器二轴五档齿轮的噪声指标cg的验算,已知:
mn=2.06,Z1=24,Z2=43,αn=20°,β=28°,αt=22.4°,da1=φ62.9,da2=φ105.49,d1=φ55.99,d2=φ100.32。
由式5.2-1:
2控制摩擦力的噪声指标RF
从主动齿轮的节圆到其啮合起始圆的这段齿形弧段称为进弧区,从节圆到其齿顶这段齿形称为退弧区,齿轮在啮合过程中齿面有摩擦力,当齿面接触由进弧区移到退弧区时,摩擦力方向在节圆处发生突变,从而导致轮齿发生振动而产生噪声。
如果进弧区越大,齿面压力的增加幅度也越大,那么噪声就越大,而在退弧区情况正好相反,因此工作比较平稳,噪声较小。
齿面啮合从进弧区到退弧区的瞬间,摩擦力的突变量是它本身的两倍,所以产生的噪声较大。
因此在汽车变速箱的齿轮设计中,采用退弧区大于进弧区的设计方法可以获得较小的啮合噪声,由此得到了控制摩擦力的噪声指标RF,其公式如下:
(5.2-2)
式中:
max齿顶的齿形曲率半径;
在现代变速箱的设计中,为了达到良好的低噪声性能,各档齿轮的控制摩擦力的噪声指标一般都要小于1.0,尤其当RF小于0.9时,降低噪声的效果比较明显。
因此在设计过程中可以通过改变齿顶高系数和变位系数,来减小从动齿轮的外径和增大主动齿轮的外径,以使RF减小。
在降噪设计过程中必须同时控制cg和RF两个噪声指标,使它们同时小于1.0,这样才能从总体上获得较小的噪声性能。
例如:
LC5T80变速器二轴五档齿轮的噪声指标RF的验算,已知:
mn=2.06,Z1=43,Z2=24,αn=20°,β=28°,αt=22.4°,da1=φ105.4,da2=φ62.9,d1=φ100.32,d2=φ55.99。
由式5.2-2:
五、合理设计齿轮副侧隙和确定齿厚偏差;
按国家齿轮标准的规定来先取侧隙,从控制噪声的角度出发,按下列公式确定最小侧隙Jnmin。
式中:
fpt1、fpt2——主、从动齿轮齿距误差
△Fr1、△Fr2——主、从动齿轮径向跳动偏差
αn——法向压力角
K——考虑热变形热膨胀和尘屑等因素的系数,一般取0.7~0.85
在确定各档齿轮副侧隙时,应使其步调一致,以消除系统侧隙对噪声的不利影响。
齿轮侧隙与许多因素有关,例如齿轮体热膨胀系数、齿轮受载后轮齿变形、制造误差、安装误差及润滑油膜厚度等。
根据一般推荐的数值,考虑表中的最小侧隙要求,再按上述Jnmin的近似计算公式,再参照齿轮国际规定来分配齿厚上、下极限偏差。
我公司的部分变速器齿轮的侧隙见下表:
型号
一档副
二档副
三档副
四档副
五挡副
六档副
倒档副
LC5T80
0.035~0.147
0.035~0.146
0.035~0.147
0.035~0.145
0.04~0.15
0.04~0.163
0.04~0.153
LC6T70
0.116~0.205
0.082~
0.183
0.069~0.154
0.07~0.16
0.105~0.175
0.091~0.185
0.111~
0.207
0.129~
0.222
六、正确进行轮齿的修形(设计齿形和设计齿向
轮齿修形设计齿形和设计齿向是降低齿轮噪声最合理最有效的途径。
它一直是国内外齿轮界研究的热门课题。
当前,国内外的一些汽车变速器齿轮图纸上均标有对设计齿形和设计齿向的要求。
修形原理已为众多的齿轮方面的专家和学者阐明,但修形的计算和方法是各不相同的。
正是因为每种齿轮的工作条件(载荷变化大小、转速和油温等)、轮齿几何特征和综合刚度等不尽相同的,所以各个汽车变速箱生产厂家的修形计算都有它的局限性,不可能适用于所有齿轮的修形。
确定自己产品的修形要求时,最有效的途径是要进行大量的试验,经获得适合本齿轮的齿形和齿向要求,以便在生产中予以执行。
一般齿轮修形有以下几种情况:
a.齿轮齿顶倒棱:
仅对齿顶部分进行修正(见图1)。
△=△1+△2
式中△1——考虑加工误差的倒棱量,对于固定工艺和精度等级,其值为常数。
△2——克服啮合过程中由双对齿啮合向单对齿啮合过渡时引起载荷突变的倒棱量,其值与载荷成正比。
关于△值,虽有不少计算方法,但过于繁杂和理论化。
根据汽车变速箱齿轮设计制造的经验,推荐△=0.08~0.12mm。
模数小时取大值,反之取小值。
另外,倒棱部分齿形角取2αn。
如齿轮齿形角αn=20°,则取αn=20°*2=40°为宜。
b.齿形修正(设计齿形):
除齿顶和齿根部分较理论渐开线稍短一些外,一般希望沿整个齿高方向为呈正压力角误差的齿形为宜。
具体齿形形状仍需通过大量试验确定。
c.齿向修正(设计齿向):
为避免轮齿的端接触或偏接触的出现,一般要求按齿的长度方向做成中间凸出即鼓形齿,中凸量一般为0.005—0.012mm。
d.也可用专用软件进行齿形、齿向的优化修形,如MASTA软件。
七、齿轮体结构形状的设计
从限制噪声传播的角度考虑,为降低噪声,应减小齿轮表面的辐射面积,而达到这一目的的方法:
一是尽可能减小齿轮直径,其次是在齿轮体上打孔。
如LC5T80中间轴主动齿设计出均布的8个孔。
另外,增加齿轮体厚度和布上环状筋等也可降低噪声,但这些措施受到变速器轴向尺寸的限制。
八、齿轮精度的设计
变速器齿轮的传动不平稳会引起振动和冲击,从而引起噪音加大,保证传动平稳性的齿轮精度项目有:
一齿切向综合公差
一齿径向综合公差
齿廓总公差Fα
齿距极限偏差
螺旋线形状偏差
国家标准(GB/T10095.1-2001)对齿轮及齿轮副规定了13个精度等级,第0级的精度最高,第12级的精度最低。
齿轮副中两个齿轮的精度等级一般取成相同,也可取成不同。
若两齿轮的精度等级不同,则按较低的精度确定齿轮副的精度等级。
在12个精度等级中,第0、1、2两级是目前一般加工和测量条件难以达到的,所以较少采用。
第3~12级大致可以划分为三挡:
高精度等级:
3、4、5级;
中精度等级:
6、7、8级;
低精度等级:
9、10、11、12级。
汽车变速器齿轮一般选用中精度等级。
它们可以用滚齿、插齿、剃齿和磨齿等常用加工和通用的齿轮测量仪器进行加工和测量。
齿轮精度等级的选用,通常用下列方法来选择齿轮的精度等级:
a、计算法根据机械动力学和机械振动学计算并考虑震动、噪声、强度计算、寿命计算的基础上来考虑精度等级。
b、类比法按现有已证实可靠的同类产品或机构的齿轮,按精度要求、工作条件、生产条件等加以必要的修正,选择相应的精度等级。
我公司在变速器齿轮的设计时主要采用类比法确定齿轮的精度。
商用车变速器齿轮的精度取8级,乘用车变速器取齿轮的精度7级。
齿轮的精度设计时一般控制以下几个项目:
齿距累积总偏差
单个齿距偏差
齿廓总偏差
螺旋线总偏差
齿圈径向跳动
第四章齿轮的材料及热处理
第一节变速器齿轮材料的选择
汽车变速器齿轮材料的选择不仅要考虑齿轮材料要满足齿轮的工作条件,使齿轮有较高的疲劳强度;而且要求齿轮材料有较好的加工工艺性。
以便提高产品的生产效率,降低生产成本,减少消耗。
如果材料选择的不当,则会出现零件的过早损伤,甚至实效。
一、材料的机械性能的选择
材料的机械性能包括强度、硬度、塑性及韧性等,反映材料在使用过程中所表现出来的特性。
齿轮在啮合时齿面接触处有接触应力,齿根部有最大弯曲应力,可能产生齿面或齿体强度失效。
齿面各点都有相对滑动,会产生磨损。
齿轮主要的失效形式有齿面点蚀、齿面胶合、齿面塑性变形和轮齿折断等。
因此要求齿轮材料有高的弯曲疲劳强度和接触疲劳强度,齿面要有足够的硬度和耐磨性,芯部要有一定的强度和韧性。
二、满足材料的工艺性能
材料的工艺性能是指材料本身能够适应各种加工工艺要求的能力。
齿轮的制造要经过锻造、切削加工和热处理等几种加工,因此选材时要对材料的工艺性能加以注意。
一般来说,碳钢的锻造、切削加工等工艺性能较好,其机械性能可以满足一般工作条件的要求。
但强度不够高,淬透性较差。
而合金钢淬透性好、强度高,但锻造、切削加工性能较差。
我们可以通过改变工艺规程、热处理方法等途经来改善材料的工艺性能。
三、材料的经济性要求
所谓经济性是指最小的耗费取得最大的经济效益。
在满足使用性能的前提下,选用齿轮材料还应注意尽量降低零件的总成本。
四、渗碳齿轮钢的质量要求
汽车变速器齿轮一般承受的载荷比较大,工作条件也比较恶劣。
要求有较高的齿轮表面硬度、耐磨性和低的芯部韧性,所以用的多为渗碳齿轮钢。
例如:
汽车变速箱中的齿轮选择20CrMnTi钢,该钢具有较高的机械性能,在渗碳淬火低温回火后,表面硬度为HRC58-63,芯部硬度为HRC30-45。
20CrMnTi的工艺性能较好,锻造后以正火来改善其切削加工性。
此外,20CrMnTi还具有较好的淬透性,由于合金元素钛的影响,对过热不敏感,故在渗碳后可直接降温淬火。
且渗碳速度较快,过渡层较均匀,渗碳淬火后变形小。
适合于制造承受高速中载及冲击、摩擦的重要零件,因此根据齿轮的工作条件选用20CrMnTi钢是比较合适的。
影响渗碳齿轮钢失效的主要因素除了渗碳、淬火、回火工艺和质量之外,还与制造齿轮所用的钢材的化学成分和冶金质量有关。
后者即对齿轮芯部性能产生直接影响,又对渗层的性能产生直接(杂质、夹杂物的含量及分布)和间接(渗层碳浓度、内氧化、淬火后显微组织形态)影响,而且往往影响齿轮的力学性能、工艺性能和尺寸稳定性。
渗碳齿轮钢的质量要求主要表现在淬透性带宽、钢材的纯净度及原始组织。
1、钢材的淬透性
渗碳齿轮钢表面的淬硬性是保证齿轮表面具有高强硬度、高耐磨性的基础。
渗碳齿轮钢的淬透性是保证不同大小齿轮芯部的硬度足以满足接触疲劳强度和弯曲疲劳强度的要求,另外,要有尽可能小的淬透性带宽的波动,有利于齿轮热处理变形的控制。
特别象我公司这样批量生产的汽车变速器齿轮显得格外重要。
国标GB5216标准规定的齿轮钢的淬透性带宽为12HRC,但目前国内钢厂对渗碳齿轮钢的淬透性带宽提出了较严格的要求,可达到6~8HRC。
2、钢材的纯净度
钢材的纯净度主要指钢材含氧量,含氧量对齿轮疲劳强度和工艺性能都有明显的影响。
我国目前对齿轮钢的含氧量ωo的要求是小于20×10-6,国外一般要求小于20×10-6。
研究表明,在相同载荷下SCM420H钢的含氧量从25×10-6降至11×10-6,接触疲劳寿命可提高47%。
3、其他
A、奥氏体晶粒度
奥氏体晶粒度是渗碳齿轮钢质量要求的又一项重要指标,细小均匀的奥氏体晶粒可以稳定淬透性,减少热处理变形,提高渗碳钢的脆断抗力。
国标规定齿轮钢的奥氏体晶粒度级别小于或等于5级。
B、成分偏析
钢中的成分偏析(主要是合金元素分布不均)在随后的热处理时并不能消除,从而会影响渗碳层碳浓度和硬度的均匀性,这将降低齿轮的力学性能,尤其是降低疲劳抗力。
因此,对齿轮钢的偏析程度应作出合理的要求并要求严格控制。
我公司常用的齿轮钢的牌号有:
20CrMnTiH、SCM420H(20CrMoH)、SCM822H、19CN5。
第二节变速器齿轮的热处理
汽车变速器齿轮不仅要具备优良的耐磨性,又要具备高的抗接触疲劳和抗弯曲疲劳性能。
齿轮质量的优劣直接到整个车辆的使用寿命,而材料和热处理是保证齿轮使用性能和可靠性的基础。
变速器齿轮采用主要是渗碳齿轮钢,采用渗碳后淬火、低温回火的热处理方式。
一、渗碳淬火的技术要求
把齿轮置于渗碳介质中,在一定温度下加热保温,以提高表面碳浓度,然后进行淬火、回火处理称为渗碳。
渗碳淬火的技术要求有:
1、渗碳硬化层深度
硬化层深度t是确定渗碳齿轮承载能力的重要参数。
德国DIN6336标准规定t=0.25m(m为模数)。
渗碳齿轮有效硬化层深度指齿轮或试样经渗碳淬火、回火后,于齿宽中部轮齿法截面上,在半齿高处沿垂直于齿面方向自表面测至维氏硬度值为550HV1(或515HV5)处的深度。
由于有效硬化层深度体现了力学性能的本质,所以国际上各种标准都采用了这一概念及相应的检测方法。
我国在渗碳工艺实践中普遍采用金相法或定碳法来确定硬化层深度,这是比较简便易行的方法。
通常金相法是以渗层表面到心部过渡区的一半处为界限;定碳法则是从表面到
=0.35%处为界限;即认为这两种方法确定的界限处淬火后的硬度基本上为550HV1。
2.表面碳浓度
渗碳表面碳浓度指距表面0.05mm处(即0.10mm厚表面剥层分析)的碳含量。
对齿轮的强度性能有较大影响,所以各种规范中提出了一个含碳量范围。
有的推荐为
=0.70%~0.90%,有的规定为
=0.8%~1.0%,也还有认为
=1.0%~1.2%为佳。
不过从国内外一些著名齿轮加工企业研究及实践经验来看,应控制在
=0.75%~0.95%的观点是可取的。
即表面
高于0.9%的齿轮具有较高的表面点蚀疲劳抗力,而
低于0.9%时齿轮的弯曲疲劳强度和冲击抗力得到改善。
表面层碳量控制应较低一些,这对碳化物形态和数量、残余奥氏体量及马氏体亚结构孪晶性控制都有好处,从而使渗碳表面层具有较好的性能。
3.心部强度
适宜的心部强度和韧性,既可保证齿的整体强度和渗层的抗剥落能力,又可以具有足够的抗冲击能力,防止齿的脆断。
在相同的淬火条件下,心部强度的高低还会影响齿轮表面残余应力的性质(拉应力或是压应力)和大小。
心部强度低时,有利于形成表面残余压应力和使其数值增大,从而有利于疲劳抗力的提高。
渗碳齿轮钢的心部强度和韧性,在淬透的情况下,主要取决于钢的含碳量,而合金元素的影响相当微小。
国内企业研究试验结果也表明,心部强度存在一个最佳值范围1150~1350MPa关于心部硬度的测定部位,过去是在距齿顶2/3的齿高处,现在国际标准和我国的相关标准规定为在齿宽处齿根
切线的法向截面上,深度为5倍硬化层深的硬度,最小深度不得小于1倍模数的位置。
这从齿轮的受力分析显然是合理的,同时还可以反映出钢材的淬透性及热处理的质量。
4.渗碳层的显微组织
国家有关标准仅对汽车齿轮有要求。
根据生产实践证明,所有的车辆用渗碳齿轮渗碳淬火后都可按此执行。
影响齿轮强度性能的渗碳层组织主要有碳化物、残余奥氏体及马氏体。
碳化物是硬而脆的相,它的形态和数量及其分布对齿轮强度性能有很大影响。
综合国内外各种试验数据可以得到结论:
粗大的块状、尖角状、网状分布的碳化物对齿轮性能有显著的不利影响,对磨齿的齿轮碳化物1~5级合格,非磨齿的齿轮应控制在4级以下,显微镜下放大100倍时应看不见碳化物。
4级呈细网状碳化物作为合格极限。
残余奥氏体是渗碳淬火组织中的重要组成相,然而也是迄今为止尚未形成统一观点来评判的显微组织,但是过多的残余奥氏体含量对很多齿轮的性能和寿命有不良影响,这点现在已没有多大分歧。
我国汽车渗碳齿轮的残余奥氏体含量通常要求不大于5级。
直接淬火齿轮以2~5级(10%~30%残余奥氏体)为合格,重新加热淬火齿轮以1~4级(小于5%~23%残余奥氏体)为合格。
马氏体是渗碳层的基本组织。
对马氏体组织的控制主要是马氏体针的大小,马氏体针的大小与奥氏体晶粒大小密切相关。
而奥氏体晶粒大小从材料角度来说与原始晶粒度有关,从热处理工艺角度来说与渗碳温度有关。
因而控制马氏体针的大小要从以上两方面严格把关。
按照国家有关标准,在3/4齿高处评定马氏体1~5级为合格。
当发现马氏体针较长,对晶粒度有怀疑时应进行检验,晶粒度不合格者判为不合格。
当用晶粒度不合格的材料制造的齿轮,要求渗碳后重新加热淬火以细化晶粒,这就控制了马氏体针的长短,故齿轮产品渗碳淬火后可不检验马氏体,但在显微组织观察中,马氏体针与残余奥氏体密切相关,粗大的马氏体针总是伴随大量的残余奥氏体存在。
二、减小渗碳齿轮热处理变形的措施
1.影响渗碳齿轮热处理变形的因素
渗碳齿轮热处理变形是齿轮在热处理过程中因齿轮各部位组织结构不同或结构组织转变次序不同及各部位热应力不同而产生的尺寸和形状上的变化。
影响渗碳齿轮热处理畸变的主要因素如表所示。
影响渗碳齿轮热处理变形的主要因素
影响因素
造成齿轮畸变的因素
设计
形状对称性及截面均匀性差,轮辐结构差
材料
晶粒度不均匀带状组织严重,淬透性带宽
锻造
锻造流线不对称,锻后冷却不均匀
预先热处理
加热温度过高或过低,冷却不均匀
切削加工
切削量过大,工艺孔位置不当
渗碳淬火
加热不均匀,渗碳夹具设计不合理,冷却
剂及冷却规范选择不当,渗层质量不均匀
2.减小渗碳齿轮热处理变形的措施
从表可知,对于某一确定形状的齿轮,设计和材料是不易改变的,用锻后余热等温退火代替二次加热正火,避免了锻后冷却不均匀和正火后冷却不均匀现象。
通过调整余热等温退火的温度等,预先热处理后可获得均匀的组织和适当的晶粒度。
试验表明,通过改善材料(改变钢材牌号)锻造、预先热处理等因素,可有效减小热处理变形。
但是,渗碳齿轮淬火后的心部硬度与齿轮主导应力方向的变形程度之间有一定关系。
当心部硬度在HRC27~32范围时,多数齿轮淬火后不产生明显的收缩或胀大变形。
随着淬火后心部硬度提高,胀大变形率增大。
渗碳齿轮淬火后回火时,都会出现尺寸收缩,回火温度越高,收缩变形量越大。
结合生产实际试验,采用相应的工艺措施防止和减小齿轮渗碳淬火畸变,对提高产品质量、降低生产成本都至关重要。
第五章齿轮的润滑及齿轮油
润滑对变速箱齿轮传动的工作能力有很大的影响,许多类型的齿面损伤如点蚀、胶合、磨损、塑性变形等都可通过合理的润滑来防止或减轻。
随着变速箱齿轮传动速度的提高,单位重量的功率的增大,工作条件的苛刻性增加,对齿轮润滑提出了更高的要求。
正确的润滑,可以提高齿轮的承载能力,减少齿轮的失效,延长齿轮的寿命,提高齿轮的传动效率。
为此,设计制造部门需要掌握摩擦学知识,根据齿轮的使用条件正确的选择润滑剂和润滑方法。
使用部门需要严格按产品说明书的规定使用润滑剂。
第一节齿轮的润滑原理及润滑方式
一、齿轮的啮合特性
7.1-1
如图7.1-1所示的渐开线齿轮啮合过程可知,齿面间的接触应力很大,啮合时间非常短,同时存在着滑动和滚动,它们只有在一定的条件下才可能形成液体动压油膜。
变速箱齿轮一般是渐开线直齿圆柱齿轮和渐开线斜齿圆柱齿轮。
由于滑动方向不同,滑动速度的比值不同,各种传动的摩擦损耗亦即效率不同,损耗形式亦不同。
渐开线直齿圆柱齿轮沿齿高方向有滑动,滑动方向与接触线垂直,因此容易形成动压油膜。
渐开线斜齿圆柱齿轮的滑动方向与接触线也接近垂直,同时沿齿宽方向有滚动,滚动速度比较大,因此也比较容易形成动压油膜。
二、齿轮的润滑状态
齿面的润滑状态可分为边界润滑、混合润滑与弹性流体动力润滑三类。
它们取决于速度、应力、啮合精度、齿面光洁度、润滑剂及润滑方式。
图7.1-2所