第七部分加工精度及表面质量.docx
《第七部分加工精度及表面质量.docx》由会员分享,可在线阅读,更多相关《第七部分加工精度及表面质量.docx(17页珍藏版)》请在冰豆网上搜索。
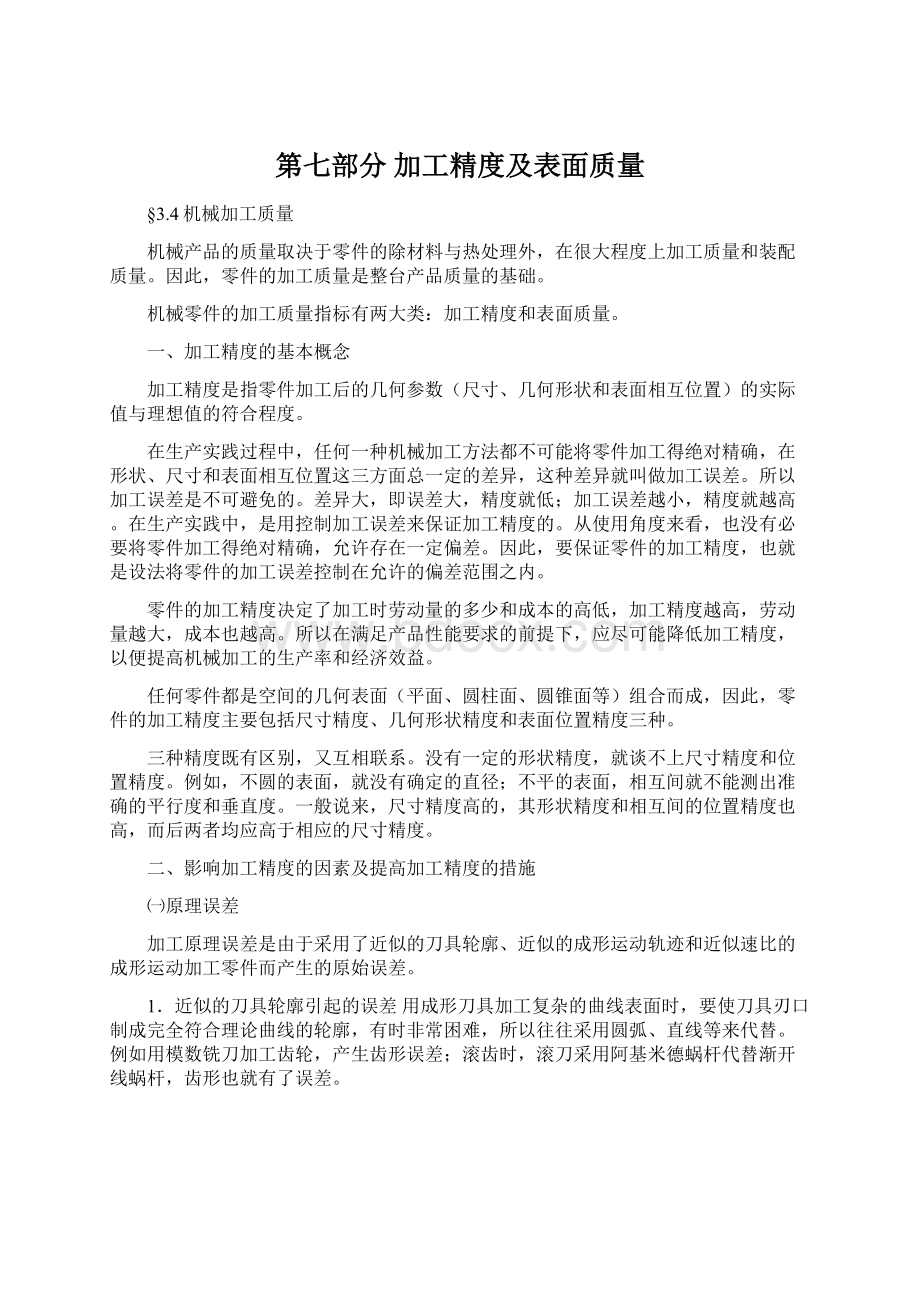
第七部分加工精度及表面质量
§3.4机械加工质量
机械产品的质量取决于零件的除材料与热处理外,在很大程度上加工质量和装配质量。
因此,零件的加工质量是整台产品质量的基础。
机械零件的加工质量指标有两大类:
加工精度和表面质量。
一、加工精度的基本概念
加工精度是指零件加工后的几何参数(尺寸、几何形状和表面相互位置)的实际值与理想值的符合程度。
在生产实践过程中,任何一种机械加工方法都不可能将零件加工得绝对精确,在形状、尺寸和表面相互位置这三方面总一定的差异,这种差异就叫做加工误差。
所以加工误差是不可避免的。
差异大,即误差大,精度就低;加工误差越小,精度就越高。
在生产实践中,是用控制加工误差来保证加工精度的。
从使用角度来看,也没有必要将零件加工得绝对精确,允许存在一定偏差。
因此,要保证零件的加工精度,也就是设法将零件的加工误差控制在允许的偏差范围之内。
零件的加工精度决定了加工时劳动量的多少和成本的高低,加工精度越高,劳动量越大,成本也越高。
所以在满足产品性能要求的前提下,应尽可能降低加工精度,以便提高机械加工的生产率和经济效益。
任何零件都是空间的几何表面(平面、圆柱面、圆锥面等)组合而成,因此,零件的加工精度主要包括尺寸精度、几何形状精度和表面位置精度三种。
三种精度既有区别,又互相联系。
没有一定的形状精度,就谈不上尺寸精度和位置精度。
例如,不圆的表面,就没有确定的直径;不平的表面,相互间就不能测出准确的平行度和垂直度。
一般说来,尺寸精度高的,其形状精度和相互间的位置精度也高,而后两者均应高于相应的尺寸精度。
二、影响加工精度的因素及提高加工精度的措施
㈠原理误差
加工原理误差是由于采用了近似的刀具轮廓、近似的成形运动轨迹和近似速比的成形运动加工零件而产生的原始误差。
1.近似的刀具轮廓引起的误差用成形刀具加工复杂的曲线表面时,要使刀具刃口制成完全符合理论曲线的轮廓,有时非常困难,所以往往采用圆弧、直线等来代替。
例如用模数铣刀加工齿轮,产生齿形误差;滚齿时,滚刀采用阿基米德蜗杆代替渐开线蜗杆,齿形也就有了误差。
2.近似的成形运动轨迹引起的误差例如用数控线切割机床加工曲线成形面,只能使工作台作纵向或横向进给的直线运动,当用直线去逼近所加工的曲线时,就产生了插补误差。
3.近似速比的成形运动引起的误差例如在车床上车蜗杆时,或在米制丝杠的车床上车英制螺纹时,由于工件的导程(t=πm)都含有无理数π,只能配换出近似的传动比,因而使工件的导程产生误差。
理论上完全正确的加工方法(或因加工效率低,或因机床(或工装)结构太复杂,或因刀具很难制造),有时很难实现,所以只要它的误差不超过允许的公差范围,往往比准确的加工方法能获得更好的经济效果。
∴采用近似的加工方法,是保证质量,提高生产率和经济效益的有效措施,特别适合于形状复杂的表面。
㈡工艺系统的几何误差及改善措施
在机械加工时,机床、夹具、刀具和工件构成一个完整的系统,称为工艺系统。
由于工艺系统受多方面因素的影响,会产生各种各样的误差,即是工艺系统本身的误差。
不同的加工条件,会以不同程度反映到工件上形成加工误差。
工艺系统的几何误差包括:
机床、刀具和夹具的制造、安装、磨损所引起的误差、调整误差及工件的定位误差等。
1.机床的误差机床误差包括机床本身的制造误差、安装误差和磨损所引起的几何误差等。
对加工精度影响较大的有:
主轴回转误差、导轨误差和传动链误差。
⑴主轴回转误差主轴的回转误差可以分为纯径向跳动、纯角度摆动和纯轴向窜动三种基本形式。
主轴回转精度对加工的影响①径向跳动使镗出的孔呈椭圆;磨削引起棱圆度、波度及表面粗糙度。
②轴向窜动使加工出的端面却与内外圆不垂直。
总之主轴的回转精度对加工精度的影响十分显著。
影响主轴回转精度的主要因素①主轴与轴承本身的精度、刚性较差(圆度、前后轴颈的同轴度、滚动体的尺寸和圆度误差引起主轴径向和轴向跳动;轴承滚道的端面跳动和推力轴承的端面跳动都会使主轴轴线产生轴向窜动。
);②主轴箱箱体的前后轴承孔和有关部分(压紧螺母、轴承内外隔圈和垫圈等)的精度(使主轴产生径向和轴向跳动)。
③装配质量(轴承的间隙)。
⑵导轨误差机床直线运动的导轨误差有:
在水平面内的直线度误差、在垂直面内的直线度误差和两导轨的平行度。
①导轨在水平面内导轨直线度误差使产生工件的圆柱度误差。
②导轨在垂直平面内的直线误差造成工件的形状误差。
③两导轨的平行度误差主要造成形状误差。
水平面内的误差
垂直面内的误差
数控车床导轨在水平面内的弯曲或与主轴轴线的平行度对加工精度影响最大,而导轨在垂直平面内的直线误差对加工精度的影响则小到可以忽略的程度。
减小导轨误差对加工精度的影响可通过提高导轨的制造、安装和调整精度来实现。
⑶传动链误差当加工螺纹、齿轮、蜗杆、蜗轮等零件时,要求刀具和工件间具有精确的传动比,这种传动比是由机床的传动链来保证的。
若传动链存在误差,将会直接影响到工件的加工精度。
传动链误差是由于传动链中传动元件的制造误差和装配误差引起的,使用过程中的磨损,也会引起传动链误差等。
传动机构越多、传动路线越长,传动链误差就越大。
减少传动链误差的措施有①尽可能减少传动元件,缩短传动链;②提高各传动元件,特别是未端件的制造和装配精度;③传动元件间的间隙,同样会产生传动链误差,因此要消除传动间隙。
2.刀具和夹具的误差
⑴刀具误差刀具误差对加工精度的影响,随刀具的种类不同而异。
①单刀刀具(如车刀、刨刀、单刃镗刀等)对加工精度没有直接影响。
②定尺寸刀具(如钻头、铰刀、拉刀和键槽铣刀等)的尺寸精度、成形刀具(如成形车刀、成形铣刀等)的形状精度,加工时,会直接影响工件的加工精度。
刀具的磨损会影响刀具与工件被加工表面的相对位置,直接造成工件的尺寸误差和形状误差。
⑵夹具误差夹具误差主要指定位元件、导向元件和夹具体等零件的加工和装配误差对工件的加工精度影响较大。
定位元件和导向元件的磨损也会增大加工误差。
为了减少夹具误差所造成的加工误差,夹具的制造误差必须小于工件的公差,一般常取工件公差的1/3~1/5。
对于容易磨损的定位元件和导向元件,除应采用耐磨性好的材料制造外,还应采用可拆卸结构,以便磨损到一定程度时可以及时更换。
㈢工艺系统受力变形引起的加工误差
工艺系统在切削力、夹紧力、惯性力、重力等外力的作用下,会产生相应的变形,这种变形通常都是弹性变形。
1.切削力引起的变形切削力大小的变化和作用位置的变化造成加工误差。
⑴切削力大小的变化造成的加工误差
切削力因毛坯几何形状和硬度不均匀而有大小的变化,从而造成加工误差。
如下图,车削一有椭圆误差的毛坯。
车前先将车刀调到图中虚线位置,车削时在工件每一转过程中,切削深度在ap1与ap2之间变化。
因此,切削力F也随切削深度ap的变化,由最大变到最小。
工艺系统将产生相应的变化,即由y1变到y2,这样就使毛坯的椭圆度误差仍保留在加工后的工件表面。
这种现象称为“误差复映”。
);
注意:
加工前后的误差大小是不同的,误差在逐步减小。
当工艺系统刚度越高,毛坯误差越小时,复映到工件上的误差也越小。
由此可以理解,零件的加工为什么需要经过多次走刀和经过粗、精加工阶段才能取得较高的精度。
当毛坯误差较大,一次走刀不能满足加工精度要求时,需多次走刀来消除复映的误差。
⑵由切削力作用位置的变化引起的加工误差切削力作用在不同的部位时,工艺系统的刚度也随之而异,由此会使工件产生形状误差。
①顶车粗而短的光轴(∵工件的刚度大;刀架的变形又很小,忽略)
工艺系统的变形量主要为尾座和刀架;当车刀靠近主轴箱车削时,变形量主要为主轴箱;当车刀切削至中间位置时,工艺系统的变形量小于在两端时。
因此加工出来的工件呈鞍形件。
由于主轴箱的刚度总是大于尾座,所以靠近尾座一端的直径稍大于主轴箱处的直径。
②顶车细长轴工件的刚度很小,工艺系统的变形主要是工件的变形,当车刀切削至中间位置时,工件的挠度最大,被切去的金属要比两端少,所以加工出来的工件呈腰鼓形。
2.夹紧力、惯性力、重力等引起的加工误差
⑴夹紧力引起的变形刚性较差的工件,若夹紧方法不当,常引起工件的形状误差。
例如,薄壁套筒夹在三爪卡盘中车孔,夹持点处套筒向内变形,相邻处则向外变形,内孔车圆后松开卡盘,套筒弹性变形恢复,又使孔变为三角棱圆形。
为了减少夹紧力造成的变形,可在工件外加装一个开槽的过渡环,增大夹持面积以减少夹紧变形。
⑵惯性力引起的变形象曲轴这类旋转零部件(包括夹具、工件和刀具)的不平衡将产生离心力,使工艺系统的受力变形发生变化,引起工件的加工误差。
为了减少这种误差,在车削和磨削不平衡工件时必须加上配重,消除旋转时不平衡现象。
⑶重力引起的变形
大型机床部件和工件本身的重量以及它们在移动中位置的变化,也会引起加工误差。
例如立车、龙门刨、龙门铣的横梁和刀架,其自重会引起导轨变形,从而影响刀具进给运动的直线性。
在制造和修理这些大型机床时,可先测出导轨的变形量,有意识地将导轨制成中凸,以抵消其变形。
减少工艺系统受力变形的主要措施有:
①通过提高联接表面的几何形状精度、减细表面粗糙度(刮研导轨副、研磨中心孔等)和提高装配质量(减少配合间隙)来提高联接表面的接触刚度;②改进机床部件的某些结构提高机床部件的刚度;③设置辅助支承提高工件或刀具刚度(例如,车削细长轴时,工件容易变形,采用中心架或跟刀架,缩短了切削力作用点与支承点之间的距离,从而提高了工件的刚度。
镗孔时,若镗杆伸出过长,可采用导向套来提高镗杆的刚度。
)④合理安装工件减少夹紧变形等。
㈣工件内应力引起的加工误差及改善措施
当工件承受的外部载荷去除后,仍残留在工件内部的应力称为内应力(内应力是由于热加工和冷加工使金属内部组织发生了不均匀的体积变化而产生的)。
具有内应力的工件,其内部组织处于一种不稳定状态,即使在常温下其内部组织也在不断地发生变化,直到内应力完全消失为止。
在此过程中,零件会发生变形,从而丧失其原有的加工精度。
1.内应力产生的原因及引起的加工误差
⑴热加工产生的内应力在铸、锻、焊和热处理等热加工中,由于各部分金属热胀和冷缩的不均匀及内部金相组织转变的体积变化,导致毛坯内部产生很大的内应力。
右图a表示一个内外壁厚相差较大的铸件,浇注后冷却时产生内应力的情况。
因此铸件在加工前一般都应进行消除内应力退火。
2.减少或消除内应力的方法①设计零件时,尽量减少零件各部分厚度差(应均匀),以减少热加工产生的内应力。
②毛坯制造出来后,应根据工件的精度要求,采取(自然、人工、振动)时效工艺措施来消除内应力。
③加工中粗精加工分阶段进行;④冷校直后安排回火工序。
㈤工艺系统热变形所引起的加工误差及改善措施
在精密件和大件加工中,据统计,热变形引起的加工误差占40~70%。
工艺系统的热源:
①内部热源有切削热、传动系统(轴承、齿轮、离合器、工作台与导轨、丝杠与螺母等)的摩擦热。
②外部热源(气温变化、阳光、供暖设备等)
1.工件热变形所引起的加工误差加工中产生的热变形,主要是切削热(加工方式不同,切削热传给工件的多少也不等。
如车削时传给工件的热量一般为30%,高速切削时只有10%。
对于铣削、刨削,传给工件的热量在30%以上。
钻削、镗削时,因大量切屑留在孔内,因而传给工件的热量在50%以上。
磨削时约有84%的热量传给工件,其加工表面温度可达800~1000℃,)影响工件的加工精度,而且还影响到表面质量。
另:
工件受热均匀与否,热变形影响也很大。
若工件单面受热,会产生弯曲变形。
2.机床热变形所引起的加工误差机床热变形对加工精度的影响,最主要的是主轴部件和床身导轨。
3.刀具热变形所引起的加工误差刀具热变形的热源是切削热。
切削热传给刀具的百分比虽很小,但由于刀具的体积小,故仍有相当大的温升和热伸长。
例如用高速钢车刀车削时,切削刃的温度可达刀700~800℃,刀具热伸长可达0.03~0.05㎜。
刀具热变形对加工精度的影响,常需要与其它的误差因素(如刀具磨损、工艺系统受力变形等)综合起来考虑。
例如车长轴或在立车上加工大直径平面时,由于刀具的热伸长,会造成几何形状误差,前者造成锥度;后者造成平面度误差。
但由于刀具的磨损能相对补偿一些,所以对加工精度的影响,有时就不太明显。
4.减少工艺系统热变形的方法
⑴减少发热和隔热(分开热源)
①减少发热减少切削热(或磨削热)。
切削热主要对精加工时影响较大,因此,在精加工时可通过合理选择(较小的)切削用量和正确选择刀具的几何角度(较大的前角和后角,使刀具锋利,减少与工件表面的摩擦)的方法,来减少切削热。
采用涂层硬质含金(如涂TiC、TiN)等,能有效地降低摩擦力和切削温度,并且因涂层硬度高、耐磨性好,能经常保持锋利,也有利于降低切削力和切削热。
改善轴承的润滑条件,减少摩擦热。
轴承发热是机床发热的主要原因,因此新设计或技术改造时应从结构和润滑等方面对轴承、摩擦片及各传动副采取措施,减少发热。
②分开热源凡是可能从主机分离出去的热源,如电动机、变速箱、液压装置和油箱等置于床身外部,以减少它们对主机的影响。
⑵冷却与散热正如不能避免发热一样,完全隔热也不可能,但可采取使用冷却液或风冷散热装置进行强制冷却。
强制冷却可带走大量热量,减少和控制机床的热变形。
⑶控制温度变化精密零件的加工与测量、精密机床时装配与调试,都必须在恒温环境下进行。
恒温室的标准温度为20℃,一般控制在±1℃以内,随季节的变化,温度一般控制在[(18~23)±1]℃的范围内。
§6.7机械加工的表面质量
一、表面质量的概念
表面质量是指零件加工后的表面层的状态。
机械加工后的零件表面并非是完全理想的表面,而是存在着不同程度的❶微观不平度、❷残余应力、❸冷作硬化及❹金相组织变化等。
虽然只是极薄的一层,但对机械零件的使用性能,如耐磨性、疲劳强度、配合性质、耐腐蚀性等都有很大影响。
表面质量的主要包括:
1.表面的微观几何形状
(1)表面粗糙度指表面微观的几何形状误差。
即已加工表面峰谷h和间距所组成的微观几何形状特征。
波距<1mm。
(2)波度也是微观的几何形状,其特征是波距L在1~10mm之间,它介于宏观的几何形状误差(L>10mm)与微观几何形状误差(表面粗糙度)之间的周期性的几何形状误差(波度是周期性的几何形状误差)。
它主要是由加工过程中工艺系统的振动所引起的。
2.加工表面层的物理机械性能
(l)表面层的冷作硬化(加工硬化)指零件加工表面层产生强烈的塑性变形后,其强度、硬度有提高的现象。
(2)表面层的残余应力σ加工中∵切屑变形和切削热的影响,材料表层内产生的附加应力(残余应力)。
(3)表面层金相组织的变化切削(特别是磨削)的高温使工件表层金相组织发生变化,改变了金属的物理机械性能,降低了零件的使用寿命。
二、表面质量对零件的使用性能的影响
1.对零件耐磨性的影响零件的耐磨性主要决定于零件的材料和润滑条件,当材料和润滑条件确定后,零件的表面质量对耐磨性起着决定性作用。
⑴零件的表面粗糙度对磨擦影响很大。
较粗时,凸峰先接触,压强大,磨损严重。
但是粗糙度过细,不利于贮存润滑油,从而产生分子亲和力,磨损反而加剧。
通常,一对运动副表面有一最佳粗糙度(右图),处于和Ra处磨损量最小,最佳点约在Ra0.8~0.4μm处。
高精度导轨面刮好后,为了改善润滑条件,常用珩磨产生交叉网纹或“刮花”使之具有均匀细浅的凹坑来改善贮油条件,减轻零件的磨损。
⑵冷作硬化可提高耐磨性,但过度冷硬反而会使组织疏松而降低耐磨性。
2.对接触刚度的影响接触表面越粗糙,其实际有效接触面积越小。
尽管零件间承受的载荷不变,但压强增大,表面接触应力增大,引起表层变形增大,从而表面接触刚度变小,影响零件的工作精度和抗振性。
3.对配合性质的影响表面粗糙度会影响配合性质的稳定性。
对于间隙配合,因接触表面的峰顶在初期工作中很快磨损,使间隙增大;对于过盈配合,因装配表面被压平,使有效过盈减小,降低联接强度;对于过渡配合,也会使配合变松。
4.对疲劳强度的影响
①表面粗糙、有划痕及微裂纹,则易引起应力集中,使零件疲劳损坏。
为了提高零件的疲劳强度,对零件的轴肩、沟槽或拐角处等应力集中区,用精磨、抛光、滚压等减细表面粗糙度。
②表面层适度的冷作硬化,使表面硬度和耐磨性有所提高,且能阻止表面已有裂纹的扩展和防止疲劳裂纹的产生。
所以,适度的冷作硬化能提高零件的疲劳强度。
但是,硬化程度与硬化深度过大,易产生微裂纹甚至剥落。
③表面层的残余应力如果是压应力,能抵消部分工作载荷引起的拉应力,延缓疲劳裂纹的产生和扩展;若为残余拉应力,会降低疲劳强度。
5.对耐腐蚀性的影响金属腐蚀是化学过程和电化学过程引起的。
钢、铁生锈,铜表面变绿都是腐蚀的结果。
表面越粗糙,微小裂纹越多,腐蚀性气体或液体越容易积存在谷部,腐蚀越强烈。
所以,精磨、研磨、抛光后的零件表面,不易被腐蚀。
表面的残余压应力,使零件表面紧密,腐蚀性物质不易进入;残余拉应力则降低了零件的耐腐蚀性。
三、影响表面质量的因素
(一)影响表面粗糙度的因素及改进措施
1.切削用量⑴V:
在一定范围内易产生积屑瘤或鳞刺,积屑瘤是不稳定的,自生自灭,反复生成与消失,留在已加工表面的一部分形成鳞片状毛刺,造成切削力的不稳定引起振动,进一步使表面粗糙度变粗。
鳞刺(用较低的切削速度切削塑性材料时,在已加工表面上往往会出现鳞片状毛刺叫鳞刺)的出现将使表面粗糙度增大2~4级,工件材料变形程度愈大,与刀具间磨擦愈大,愈易引起鳞刺。
∴↑γ,↓a,↑V,↑HB及合理选择切削液,可抑制鳞刺的产生,降低表面粗糙度。
⑵f:
↓f,可↓残余面积高度H,(H≈)∴可↓表面粗糙度。
2.刀具⑴刀具材料与工件材料分子间亲和力大时,易产生积削瘤;∴硬质合金刀具比高速钢刀具加工的表面粗糙度细。
⑵几何参数(刀尖圆弧半径)r、Kr和均影响残留面积的大小,∴↓r、Kr、可↓表面粗糙度。
⑶表面光洁度表面光洁,可减少摩擦和磨损,∴前后刀面的表面粗糙度应不小于工件表面粗糙度1~2级,且Ra≤1.6μm。
3.工艺系统的振动加工时振动使工件与刀具间的距离发生周期性变化,形成振纹,使表面粗糙度的Ra值↑,因此应设法减少振动,隔开振源。
4.切削液其冷却和润滑作用可↓切削温度,减小刀具与工件的摩擦,减少切屑的塑性变形,抑制积削瘤和鳞刺的生长,有利于↓表面粗糙度。
(二)影响加工表面物理机械性能的因素
1.加工表面的冷作硬化由于机械加工时工件表层金属受到切削力的作用,产生强烈的塑性变形,使金属的晶格间剪切滑移,晶格严重扭曲、拉长,甚至被破坏,引起金属表面层硬度提高,塑性降低,物理力学性能发生变化。
这种现象叫冷作硬化。
切削力大,塑性变形大,硬化程度加强;塑性变形速度快,变形不充分,硬化程度弱。
另外,机械加工中的切削热,提高了表面层的温度,使已强化的金属产生回复现象,使金属失去加工硬化中所得到的物理力学性能,这种现象称软化。
切削温度高,持续时间长,回复作用也大。
因此,机械加工时表面层的冷硬就是硬化和回复作用的综合结果。
影响加工表面冷作硬化的因素有:
⑴刀具前角越大,切削层金属的塑性变形越小,硬化层深度越小;刀尖圆弧半径越大,已加工表面在形成过程中受挤压越大,加工硬化也越大;随着刀具后刀面磨损量的增加,后刀面与已加工表面的摩擦也随之增加,硬化层深度也增大。
⑵工件材料工件材料的塑性越大,硬度越低,加工表面层的硬化越严重。
例如,磨削低碳钢与磨削淬火钢相比,硬化层深度h由30~60μm降至20~40μm,硬化程度N由160%降低至125%。
∴工件材料需调质、正火。
⑶切削用量①V:
V↑,刀具与工件接触时间少,变形不充分,冷硬程度↓;同时切削温度↑,回复作用大,∴冷硬程度↓。
若V很高,回复来不及进行,冷硬层深度↑;因此宜选用较高的切削速度。
②f:
f增大时,F增大,表层金属塑性变形加剧,冷硬程度增加;但f太小时,刀口圆弧工件的挤压增加;冷硬程度不仅不会减小,反而会增大。
2.加工表面的残余应力残余应力主要由金属表层的塑性变形和金相组织的变化引起。
残余应力会引起工件变形,失去原有精度。
残余应力为拉应力时,使疲劳裂纹增加,耐蚀性下降;是压应力时,则使疲劳强度及耐磨性提高。
⑴冷塑性变形切削力→挤压→压缩变形→在表层产生残余压应力,↑耐磨性和疲劳强度;
⑵热塑性变形切削热→表面局部温度高→膨胀变形比里层大→冷却快收缩比里层大→(受里层金属的阻碍,)产生了残余拉应力→(切削温度越高,残余拉应力也越大,甚至出现微观裂纹)→↓耐磨性和疲劳强度。
∴在切削温度不高(车削)时,以冷变形为主,主要产生残余压应力;切削温度高(磨削)时,以热变形为主,主要产生残余拉应力;
⑶金相组织变化不同的金相组织有不同的密度,金相组织的变化引起体积变化而产生的残余应力。
磨削时产生的高温可能使工件表面层的金相组织发生变化。
以淬火钢磨削为例,淬火钢原来是马氏体组织,磨削后,表面层可能产生回火而变为屈氏体或索氏体,密度增大,体积减小,因受里层金属阻碍,故工件表面产生残余拉应力。
3.表面层金相组织变化与磨削烧伤车削加工中,切削热大部分被切屑带走,表面温度升高不大,不可能达到相变温度。
因而金相组织发生变化主要由磨削(尤其在冷却液不充分或冷却液不能到达磨削区时)高温(1000℃)引起,金相组织变化后,硬度下降,出现细微裂纹,甚至彩色氧化膜,称之为烧伤。
磨削烧伤要尽量避免。
如轴承内外环经精磨后,检验员用肉眼检查不出烧伤在何处,必须用专用检验液逐只检查发现其烧伤部位,以免存在隐患。
磨削烧伤的原因及预防措施如下:
①控制磨削用量∵a↑,T↑,∴a不宜太大(尤其粗磨削时);f↑,T↓,∴↑f(为了弥补增大粗糙度值的缺陷,可采用宽的砂轮磨削);V↑,虽然发热量增大,但热作用时间减少,金相组织来不及变化,从而能减少烧伤。
因此,用较宽砂轮磨削或提高砂轮线速度可以降低烧伤程度并可减细粗糙度。
②工件材料材料硬度越高,磨削热量越多,材料过软,易堵塞砂轮,使磨削温度上升;工件强度越高,磨削消耗功率越大,发热也越多;工件韧性越大,磨削力越大,发热越多,故材料强度、硬度越大,导热性越差的材料越容易产生磨削烧伤。
③合理选择砂轮砂轮、硬度高、自砺性差、磨削温度高。
砂轮组织太紧密,砂轮易堵塞容易引起烧伤。
砂轮钝化时,在工件表面打滑,仅起挤压和摩擦作用,使磨削温度增高,容易引起烧伤。
一般,精磨时,选用中等粒度(细粒度自锐性差,粗粒度又影响表面粗糙度)、硬度适中的氧化铝砂轮。
④冷却方法冷却液可以带走磨削区的热量,避免烧伤。
常见的冷却方法效果欠佳,(因为高速旋转的砂轮会造成圆周表面的强气流,使切削液不易进入磨削区达到有效冷却,只是大量倾注在已离开磨削区的加工表面上,这时,早已产生烧伤。
)所以可改用开槽砂轮和内冷却砂轮磨削。
为改善冷却方法,目前,有人研究试验一种内冷却方法(赵元吉P198),但因一些具体问题(空间大量水雾、操作者劳动条件差、不便操作、试切……),有待改进。
复习课
1.顶车光轴产生鼓形度的可能原因:
①工件刚性不足(让刀);
②中心架压力不足,没接触工件;
③车床导轨中部磨损;
④工件受热伸长弯曲。
消除或减少措施
①改变装夹(用中心架或跟刀架)或反向走刀;
②调整压块,使之接触工件;
③修刮导轨;
④用弹性顶尖或后缩顶尖。
2.顶车光轴产生鞍形度的可能原因:
①机床刚性太差,而工件刚性较好;
②导轨在水平面内的直线误差(磨损或扭曲);
③中心架支块压力过大,将工件压向车刀;
④(因尾座底版磨损等原因,)前后顶尖在垂直面内不同轴。
消除或减少措施
4.顶车光轴产生喇叭形的可能原因:
①车床尾顶尖刚性不足;
②前后顶尖在水平面内