反再部分培训教材.docx
《反再部分培训教材.docx》由会员分享,可在线阅读,更多相关《反再部分培训教材.docx(32页珍藏版)》请在冰豆网上搜索。
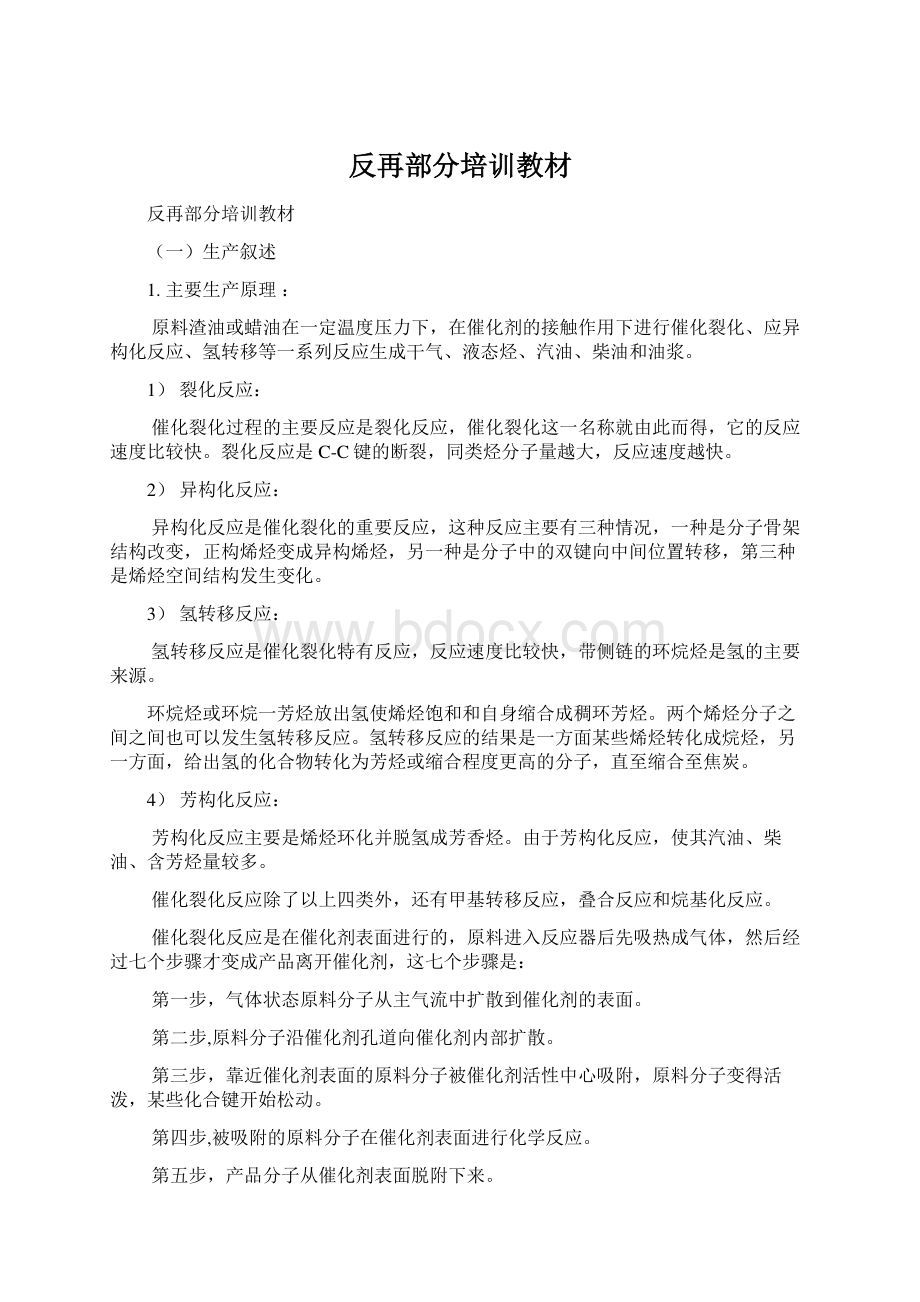
反再部分培训教材
反再部分培训教材
(一)生产叙述
1.主要生产原理:
原料渣油或蜡油在一定温度压力下,在催化剂的接触作用下进行催化裂化、应异构化反应、氢转移等一系列反应生成干气、液态烃、汽油、柴油和油浆。
1)裂化反应:
催化裂化过程的主要反应是裂化反应,催化裂化这一名称就由此而得,它的反应速度比较快。
裂化反应是C-C键的断裂,同类烃分子量越大,反应速度越快。
2)异构化反应:
异构化反应是催化裂化的重要反应,这种反应主要有三种情况,一种是分子骨架结构改变,正构烯烃变成异构烯烃,另一种是分子中的双键向中间位置转移,第三种是烯烃空间结构发生变化。
3)氢转移反应:
氢转移反应是催化裂化特有反应,反应速度比较快,带侧链的环烷烃是氢的主要来源。
环烷烃或环烷一芳烃放出氢使烯烃饱和和自身缩合成稠环芳烃。
两个烯烃分子之间之间也可以发生氢转移反应。
氢转移反应的结果是一方面某些烯烃转化成烷烃,另一方面,给出氢的化合物转化为芳烃或缩合程度更高的分子,直至缩合至焦炭。
4)芳构化反应:
芳构化反应主要是烯烃环化并脱氢成芳香烃。
由于芳构化反应,使其汽油、柴油、含芳烃量较多。
催化裂化反应除了以上四类外,还有甲基转移反应,叠合反应和烷基化反应。
催化裂化反应是在催化剂表面进行的,原料进入反应器后先吸热成气体,然后经过七个步骤才变成产品离开催化剂,这七个步骤是:
第一步,气体状态原料分子从主气流中扩散到催化剂的表面。
第二步,原料分子沿催化剂孔道向催化剂内部扩散。
第三步,靠近催化剂表面的原料分子被催化剂活性中心吸附,原料分子变得活泼,某些化合键开始松动。
第四步,被吸附的原料分子在催化剂表面进行化学反应。
第五步,产品分子从催化剂表面脱附下来。
第六步,产品分子沿催化剂孔道向外进行扩散。
第七步,产品分子扩散到主气流中去。
在工业生产中,常常用几种主要产物的产率来考察石油催化裂化馏分的反应,所以针对重质油馏分的催化裂化,可以用下列图1-1来做大致的描述。
由该图可见到:
原料同时向几个方向反应,同时随着反应深度的加深,中间产物又继续反应,这种反应叫顺序反应。
平行一顺序反应的特点是反应深度对产品产率的分配有重要影响。
2、工艺流程叙述
原料减压蜡油和重油分别用装置的冷蜡油泵(P-2201/1.2)抽入装置经静态混合器(D-2213)混合均匀后依次经原料——分馏一中回流换热器(E-2211/1,)原料——油浆换热器(E-2201/1-4)升温至140-223℃,然后进入提升管底部,原料与雾化蒸汽在进料喷嘴混合室混合后,原料油被雾化,经过六个进料喷嘴喷出的油料雾滴与从二再来的高温再生催化剂接触并立即气化,裂化成轻质产品(液化气、汽油、柴油)并生成油浆、干气及焦炭,专门设计的原料注入系统保证了原料油转化为轻质产品的最高转化率,最大限度的减少焦炭的生成,原料汽化热及反应热由高温再生催化剂来提供,即提升管出口温度由再生滑阀开度来控制,为使待生催化剂及再生催化剂上含碳量的差值控制在1.2%(重)以上,即维持剂油比在6-8的范围下操作,因此必须调整一再、二再烧焦分配,原料预热温度及提升管出口温度。
反应油气、水蒸汽、催化剂先经提升管出口的VQS旋流式快速分离器分出大部分催化剂,再经沉降器(C-2101)内四组单级旋风分离器分离出携带的催化剂。
反应生成物,惰性物质、蒸汽、连同微量的催化剂细粉至分馏塔底部,分馏塔底部油浆固含量一般低于0.9克/升。
分出的催化剂通过料腿将催化剂返回到汽提段,料腿装有翼阀,并没在汽提段床层中,保证具有正压密封,防止气体短路,汽提蒸汽分三路进入VQS封闭罩,经蒸汽分布环环通入蒸汽使床层保持流化状态,并置换掉催化剂夹带的烃蒸汽。
经汽提后的催化剂通过待生滑阀进入船形分布器,然后进入一级再生器密相床层顶部,待生催化剂滑阀可调节汽提段料位。
第一再生器在比较缓和的条件下进行操作,部分燃烧,操作压力0.23-0.29MPa(表),温度635-710℃,在床层中烧掉全部焦炭中的大部分氢及部分碳,烧碳的多少可视进料轻重不同而异,碳的燃烧量和再生器温度由进入一级再生器的风量来控制,以便获得灵活的操作条件,由有水蒸汽存在,第一再生器的温度要相对的控制低一些,以便将催化剂水热失活控制在最小程度,含有CO的烟道气与第二再生器出来的烟道气混合燃烧后,进入高温取热炉,然后进入能量回收系统及热能回收系统(余热锅炉)。
从第一再生器中出来半再生催化剂,经过半再生立管,半再生滑阀进入空气提升管,由增压机将主风升压后作为增压风,将催化剂提升到第二再生器,第二再生器在0.22-0.28MPa(表)压力,710-730温度下操作。
催化剂进入第二再生器空气分布环下部,并均匀地分布开,剩余的碳用过量空气在完全燃烧的情况下生成CO2,由于在第一再生器中烧掉了几乎全部的氢,从而降低第二再生器中水蒸汽分压,使二级再生器可以在更高的温度下操作,而不会造成催化剂水热失活。
第二再生器装有耐磨衬里的三组外部两级旋风分离器将烟气和催化剂分开,从而进一步降低了催化剂的消耗。
热的再生催化剂从第二再生器流出,进入脱气罐(C-2104),并顺次进入再生立管,为使再生立管获得平稳而均匀的流动效果,沿催化剂流动方向设置了多个松动点,使再生滑阀前的蓄压稳定并维持在需要的范围内,然后经再生滑阀进入提升管底部,实现催化剂连续循环。
为维持两器热平衡,增加操作灵活,在第一再生器旁设置可调节取热量的外取热器,由第一再生器床层引出高温催化剂流入外取热器(C-2105)后,经取热列管间自上而下流动,取热管没与流化床内,管内走水,取热器底部及中部通入空气,以维持良好流化。
经换热后的催化剂温度降100℃左右,通过立管及外取热器下滑阀流入空气提升管与部分半再生剂混合后由增压风提升至第二再生器。
取热器用的脱氧水经余热锅炉换热后,进入汽包(D-2118),与外取热器换热出来的汽-水混合物混合,传热并进行汽、液分离,分离后产生的饱和蒸汽进入余热锅炉过热,然后进入3.9MPa的蒸汽管网作动力蒸汽用。
汽包里的饱和水由循环热水泵(P-2103/1-3)抽出,形成强制循环,进入外取热器热管。
第一再生器和第二再生器烧焦用的主风由主风机供给,主风机出口分出一股主风经增压机(K-2101/1,2)升压后(压力0.45-0.56MPa,流量400-500Nm3/分),作为增压风大部分送入空气提升管,剩余部分作为外取热器流化风,及二再脱气罐分布环用风。
开工用新鲜及平衡催化剂由汽车从厂内仓库运送至装置内新鲜催化剂储罐和平衡催化剂储罐,用系统来的非净化风[压力0.7MPa(表)温度25℃]输送至第一再生器和第二再生器,正常补充催化剂用小型加料,用非净化风送到第一再生器。
为保持催化剂比表面积和重金属含量不超过允许值需从第二再生器定期卸出催化剂至废催化剂罐。
废催化剂储罐设有催化剂卸出装运设施。
桶装的钝化剂溶液用泵抽出至钝化剂储罐,然后由钝化剂注入泵(P-2101/1-3)压送至提升管进料总线与原料油混合进入提升管进料喷嘴。
在钝化剂注入泵出口用柴油稀释,轻柴油与钝化剂比例按10:
1考虑。
3、正常开车步骤
3.1做好开工前的准备检查工作
1)与主风机岗位配合,按自保试验方案进行自保系统的试验,认真记录各参数,测试结果填入自保系统联试记录中,各特阀响应时间应符合技术规范。
2)检查空气炉F—2101、F—2102火嘴畅通、好用,点火枪插入位置有明显标记,检查一、二次风电动阀及百叶窗灵活好用,调好一、二次风电动阀零位,试用电点火器好用,联系仪表工检查F—2101、F—2102上就地温度指示仪表好用。
3)检查大、小型加料系统良好,平衡剂,新鲜剂已按要求的数量加入催化剂罐中,罐底过滤网安装到位,锥体松动风过量正常,对催化剂罐检尺、计量。
4)联系仪表工给各特阀引吹扫风及冷却水。
5)检查一、二再燃烧油喷嘴、烟道补充空气喷嘴及各催化剂采样口畅通情况,引各喷嘴保护风及采样口反吹风,检查过量情况。
6)按反—再系统松动点要求将松动风引入各松动点,检查过量情况,发现孔板不通立即处理。
通知仪表工调整反再仪表引压点及量程。
7)反应—再生系统包括烟道上各用汽点器壁阀关闭、用汽总线上阀门关死。
8)检查F——2101、F—2102引瓦斯流程,准备好点明火用具,电点火用空气及瓦斯接好金属软管。
9)检查各膨胀节螺栓是否松开到合适位置,两器周围是否有易燃品,防止升温过程中着火或造成设备损坏。
10)打开沉降器顶、油气线上及外取热器顶放空阀,联系锅炉岗位及主风机岗位改好两器烘干流程。
11)烘干过程中检查各低点排凝畅通情况。
12)准备好气密试验用品。
13)全面检查结束,所有问题处理完毕后,联系仪表及计算机人员投用本岗位所有压力、温度、流量、压差、压降等仪表。
此时状态:
达到引主风条件
3.2反再升温
3.2.1、主风升温阶段:
1)、配合安装公司拆除油气线大盲板。
盲板拆除后,注意控制沉降器压力大于再生器。
2)备用主风机K—2101/2运行正常后,打开主风至一再上分布环、下分布环、二再分布环蝶阀,打开增压机旁路阀,打开增压风至外取热器,空气提升管、二再脱气罐流化风蝶阀、烟道上补充空气蝶阀升至10%左右,认真检查两器烘干流程无误后,联系主风机岗位,缓慢向系统引主风,控制各路主风量,按升温曲线进行两器升温。
3)联系仪表及计算机人员检查各点热偶测量值、压力测量值、流量测量值是否正确,有问题及时处理。
4)升温过程中,认真检查各松动点、流化介质过量情况,保证有适量风通过。
5)升温过程中,必须经常检查三器表面温度,检查全部吊架、弹簧膨胀节、法兰、催化剂管线等情况,做好各测量点温度记录,作出实际升温曲线。
6)一、二再流化正常后,准备F—2101、F—2102点火,联系分馏岗位建立封油循环。
7)联系锅炉岗位,给E—2401、E—2402汽包上水,汽包顶部放空打开。
4.F—2101、F—2102点火
1)点火前的准备工作
a进一步检查F—2101、F—2102一、二次风阀及百叶窗开关灵活,电打火器好用,启用F—2101、F—2102用就地温度指示。
b引蒸汽至炉前,脱水。
流程:
装置内蒸汽干线→F—2101、F—2102用汽专线→F—2101、F2102
c引非净化风至炉前,吹扫点火瓦斯嘴;
d联系71罐区,专人监护引瓦斯至F—2101、F—2102炉前,赶尽空气,脱水、做点明火准备。
引瓦斯流程:
71罐区98#、99#罐→气态烃专线→分液罐D—2204顶倒流程→F—2101、F—2102炉前。
e启用蒸汽套管加热器
f点瓦斯明火脱水脱液,控制瓦斯压力0.6~0.8MPa(G)。
g一次风阀关至20%左右,二次风阀开至60~65%百叶窗至1/3,联系主风机岗位撤风至15000~20000Nm3/hr,开大双阀将一再压力控制在0.03MPa左右。
2)点火:
按住电打火,打开点火瓦斯阀,按规程点F—2101,密切注意炉膛火嘴,一旦点着,适当调节瓦斯量,以免灭火或升温过快。
若一次给瓦斯没点着,应关闭瓦斯阀,打开瓦斯阀后放空,开大百叶窗,打开点火嘴非净化风阀吹扫10分钟以上,以赶尽炉膛内积存的瓦斯。
F—2101点着后按规程进行F—2102点火。
3)炉内火焰稳定后,切换至大瓦斯火嘴,小瓦斯火嘴熄火后抽到标记位置,防止烧坏。
4)燃烧油火嘴通入雾化蒸汽进行保护。
5)专人监护F—2101、F—2102的燃烧情况,调整一、二次风量及百叶窗开度,保证燃烧完全,控制炉膛温度≯960℃,出口温度≯650℃。
3.3提升管蒸汽置换
1.打开反—再部分用汽总线阀门,引蒸汽至各用汽点前,开低点排凝脱水,脱水完毕后,向各用汽点给汽,认真检查孔板过量情况,发现堵塞立即处理。
给汽正常后将各用汽点给汽量调整到下表要求的量:
表—4反再系统用汽点及用汽量
序号
给汽点名称
流量仪表
给汽量Kg/hr
1
提升管底部预提升蒸汽
FI—2123
3000
2
干气预提升口杯蒸汽
FI—2151
600
3
原料喷嘴雾化蒸汽
FI-2110~2113
1750×6
4
重化物喷嘴雾化蒸汽
孔板RO—44/1~2
94×2
5
急冷水雾化蒸汽
RO—45/1~2
170×2
6
油浆喷嘴雾化蒸汽
FI—2120
250×4
7
回炼油喷嘴雾化蒸汽
FI—2152/1~4
800×4
8
沉降器顶防焦蒸汽
FI—2139
1000
9
汽提段汽提蒸汽上环、中环
予汽提环蒸汽
FI-2104、FI-2114
FI—2140B
1000、3000
10
汽提段锥底松动蒸汽
FI—2122
1000
11
沉降器顶部放空吹扫蒸汽
孔板RO-37/1~2
26×2
12
MGD汽油喷嘴雾化汽
孔板RO-52/1~6
165×6
13
提升管Y型部分松动蒸汽
孔板RO-11/1~3
30×3
14
待生斜管、再生斜管松动蒸汽
孔板RO-11、13
30×12
30×326×3
2.各用汽点量调至正常位置,控制沉降器压力大于再生器压力0.01~0.02MPa再吹扫1小时。
3.联系分馏岗位打开E—2203入口,出口阀。
4.用分馏塔顶蝶阀控制沉降器压力0.12MPa,一、二再压力0.10MPa左右。
5.各事故蒸汽恢复正常流程,引至自保阀前疏水。
3.4加剂升温、转剂
喷燃烧油条件
1.催化剂升温后,当1#再生器温度高于370~380℃时可缓慢喷燃烧油,燃烧油喷入1分钟后如果床温度上升,则燃烧油已喷着。
否则应停喷燃烧油,需将再生器温度再提高10℃方可再喷燃烧油。
2.喷着后继续向1#再生器加剂,其加剂快慢应维持床层温度大于400℃,直至料位表LI-2105指示值为76%,可减缓加剂,使床温度提至550~600℃。
随着温度升高相应提高1#再生器压力,当温度为550~600℃,相应压力为0.15~0.16MPa
3.1#再生器向2#再生器转剂
(1)将2#再生器压力降到0.1MPa,提升风FIC-2118提至~18000NM3/分,由1#再生器向2#再生器转剂,1#再生器料位LI-2105指示不低于40%,使2#再生器尽快封住外旋料腿入口。
转剂过程中继续向1#再生器加剂,并注意床层温度。
(2)当2#再生器料位LI-2109约45%,LI-2108(上)为10%时,表明料位已封住外旋料腿入口,及二级料腿切线处,停止转剂(LI-2108为10%),当封住料腿后,提2#再生器压力比1#再生器压力低0.024MPa。
(3)继续向1#再生器加剂,使LI–2105达76%,一再床温达550~600℃,再向2#再生器转剂,转剂时必须缓慢,密切注意料位,使2#再生器LI-2108达到70~75,停止加剂,观察2#再生器催化剂跑损情况。
(4)当1#、2#再生器料位达到下列指标,可向沉降器转剂
1#再生器指示2#再生器量程指示
LI-210570%LI-210930KPa50~60%
LIC-210253%LI-210815KPa70~75%
并用燃烧油控制1#再生器床温600℃
炉-2101保持小火,炉-2102出口保持≤700℃。
反再系统催化剂循环正常,可慢慢降炉温。
(5)保证二再床温线速,此时观察二再密度上升,二再上料位指示LI—2108指示值下降。
(6)降低空气炉热负荷,F—2101、F—2102保持小火。
(7)密切观察一、二再催化剂跑损情况,发现问题及时处理。
一再压力0.15~0.16MPa,密相床温600~620℃,全料位:
LI—2105,70%二再压力0.14~0.16MPa,密相床温600~620℃,全料位:
LI—2109,70%上料位:
LI—2108,60%;脱气罐:
再生滑阀前蓄压PI—21190.23~0.238,料位LI—2110>80%。
4.向沉降器转剂:
a、一、二再压力、床温、料位达到上述状态。
(1)1#、2#再生器床温600-650℃
(2)1#再生器压力0.168MPa168KPa
(3)2#再生器压力缓慢升压至0.144MPa144KPa
(4)沉降器压力缓慢降至0.1MPa100KPa
b、提升管,沉降器用汽严格按下列用汽量控制。
根据VQS操作特点PDI-2108(封闭罩内外差压)控制在10~13MPa
各部蒸汽用量
1)进料雾化蒸汽FIC-(2110-2112)10.5t/h(3.5*3=10.5t/h)
2)回炼油雾化蒸汽FIC-21613.2t/h(0.8*4=10.5t/h)
3)油浆回炼雾化蒸汽FIC-21201.0t/h(0.25*4=1.0t/h)
4)急冷油、急冷水雾化蒸汽打开0.528t/h(限流孔板走量)
5)予提升蒸汽(杯口内)FT-21513.0t/h
(杯口外)FT-21230.6t/h
6)汽提蒸汽上环FIC-21401.0t/h中环FIC-21143.0t/h下环FIC-21141.0t/h
予汽提环FIC-2140B1.4t/h
7)防焦蒸汽FIC-21390.6t/h
(5)注意PDI-2107(封闭罩内外差压)应为10KPa左右
(6)仔细确认转剂条件均具备后,缓慢打开再生滑阀,密切注意提升管密度、温度、压降及沉降器温度变化情况。
(7)当反应温度达到480~500℃时,翼阀处密度PdI-2108指示抬头,说明料位已盍住封闭罩的溢流口,需视油浆中催化剂的浓度决定是否催化剂再加剂,当密度为600,指示28%,密度为760,指示36%,说明料面已淹住异阀。
沉降器料位LIC-2101达57-72。
同时注意观看TI-2190的温度,一般应比封闭罩内温度低30℃,将全部滑阀置于自动位置。
(8)各流化点流量应给定在最大流量上。
(9)向沉降器转剂,缓慢打开再生滑阀之后,注意下列仪表:
1)提升管喷嘴上温度突然变化(说明催化剂已到提升管)
2)提升管密度突然增加(说明催化剂已到提升管)
3)提升管压降突然增加(说明催化剂已到提升管)
4)提升管出口,沉降器温度增加(说明催化剂已到提升管)
5)从待生单动滑阀差压、沉降器藏量、密度表看出,当气提段密度DI-2102(D-5(+)、D-4(-)指示不变、沉降器料位LIC-2101(100KPa)显示12~15%,沉降器下料位LI-2104显示为26~33(量程120KPa),可活动待生单动滑阀,沉降器压力(PI-2108)提至0.12MPa(120KPa)、观看压力PI-2109应比PI-2108略低10KPa左右。
关闭再生单动滑阀,缓慢打开待生单动滑阀,将气提段中催化剂转入1#再生器,当待生滑阀差压降为0.01MPa,关闭待生滑阀,重复上述各步骤,直到沉降器温度达到500℃。
在向沉降器转剂过程中,向1#再生器补催化剂。
6)注意:
PDI—2108(封闭罩内外差压)应不小于0.012MPa。
7)根据二再料位下降情况控制半再生滑阀开度,使二再上料位LI—2108维持50%左右。
8)向沉降器转剂过程中,尽快向一再补新鲜催化剂,使一再全料位LI—2105不低于40%。
8)控制待生、再生滑阀开度,将沉降器全料位LI—2104升至65%,沉降器上料位LIC—2101升至40%,二再全料位LI—2109达到70%,二再上料位LI—2108达到40%时,调节控制小型加剂量,维持各床层料位。
9)密切观察沉降器封闭罩外密度PDI—2108(量程为20KPa),如指示超过5~6%则立即降低汽提蒸汽上环流量,防止催化剂大量跑损。
10)三器循环正常后,一、二再料位达到要求后,用燃烧油维持一、二再床温600~620℃,关小F—2101、F—2102火嘴直至关死,空气炉熄火。
熄火前联系49/2罐区关死气态烃罐上阀门,管线内瓦斯用明火烧完后,在气态烃进装置阀门后加盲板,盲板加好后,停用套管加热器及喷嘴雾化蒸汽。
11)拆原料喷嘴,油浆回炼喷嘴,重化物喷嘴上盲板。
认真检查有无漏点,有问题及时处理。
12)联系仪表工调校六路进料流量指示、控制仪表,确保准确好用。
5.向外取热器转装催化剂:
1)保持外取热器循环热水正常;2)外取热器上滑阀开度15~20%左右,向外取热器装催化剂;3)外取热器料位LI—2106达60~70%时,可停装催化剂。
3.5提升管进油
1.准备工作:
1)向系统加入500Kg助燃剂。
2)联系罐区及调度,准备好降温汽油,检查并改好重化物至喷嘴手阀前流程。
2.喷油条件:
(必需保证以下条件)
喷油前、为防止结焦措施反再操作做如下调整:
1)沉降器压力:
0.1~0.15MPa,提升管出口温度TI—2101、500-550℃。
全料位LI—2104:
60~70%,上料位为30~40%。
2)一再压力0.15~0.16MPa,密相温度600~620℃,全料位LI—2105:
60~70%,上料位L—2102,30~40%。
一再上分布环主风量:
38500~42000Nm3/h
二再上分布环主风量:
16500~18000Nm3/h
3)二再压力0.14~0.16MPa,密相温度600~620℃。
全料位LI—2109:
70%,上料位L—2108为40~50%。
二再主风量:
18000~20000Nm3/h。
空气提升管提升风量:
2000-22000Nm3/h。
4)脱气罐:
再生滑阀前蓄压:
0.23~0.238MPa(G)。
料位LI—2110:
60~80%。
再生立管密度≥350~450Kg/m3。
5)三器流化正常,催化剂循环能正常控制,三器料位均能用滑阀自如调节。
6)分馏塔内外循环正常、油浆外甩正常。
7)主风机、增压机运行正常,外取热器具备投用条件。
8)高压、低压放火炬阀灵活好用,分馏塔顶蝶阀灵活好用。
9)一再、二再烟气氧含量表、一再CO、CO2表,二再CO2表调试完毕,投用正常。
10)气压机具备升速条件。
11)指挥、通讯系统有可靠保障。
3.喷油
1)仔细确认各项喷油条件均具备后,准备喷油。
2)停油浆回炼线上吹扫蒸汽,启用油浆回炼控制阀,用控制阀控制油浆至喷嘴手阀前流量,先将两个相对的油浆喷嘴手阀各开1~2扣,然后逐渐开大手阀,使两喷嘴流量同步提高到8~10T/hr,密切注意沉降器压力变化,及时开大分馏塔顶蝶阀,用气压机入口放火炬控制沉降器压力,注意再生器床温及氧含量变化,若床温上升较快,适当降低燃烧油量。
3)沉降器压力平稳后,先开两个相对的原料喷嘴手阀,控制两路进料量分别为5~6T/hr,两喷嘴进料量应保持一致,观察沉降器压力、一再床温、氧含量变化情况,手动控制再生滑阀,按规程调节各参数正常后,再开二个进料喷嘴手阀,控制六个喷嘴流量均为5~6T/hr,观察并调整各参数,在打开进料喷嘴手阀的同时,将六路雾化蒸汽量均由4000Kg/hr降至3500Kg/hr。
4)进油过程中,密切注意一再氧含量变化随时采再生催化剂并观察颜色,并随进油量提高,再生床温上升,及时关燃烧油流量,防止一再超温。
5)在各参数正常后,逐步提高新鲜进料量,提量时相对的两个喷嘴同时提量,每次提4~5T/hr,待操作稳定后,再提另外两个喷嘴流量,提至六个喷嘴流量一致,在提量时,逐步关小直至关死事故旁通付线阀,使原料全部进入反应器,同时视回炼油罐液面下降情况降低回炼油量,在提进料流量的同时,逐步降低雾化蒸汽量,当新鲜进料总量为70~80吨/小时,雾化汽量控制为每路3200Kg/hr~4000Kg/h。
6)随进料量增大,反应油气量加大,联系气压机升速,逐步关小放火