MINITAB技术.docx
《MINITAB技术.docx》由会员分享,可在线阅读,更多相关《MINITAB技术.docx(20页珍藏版)》请在冰豆网上搜索。
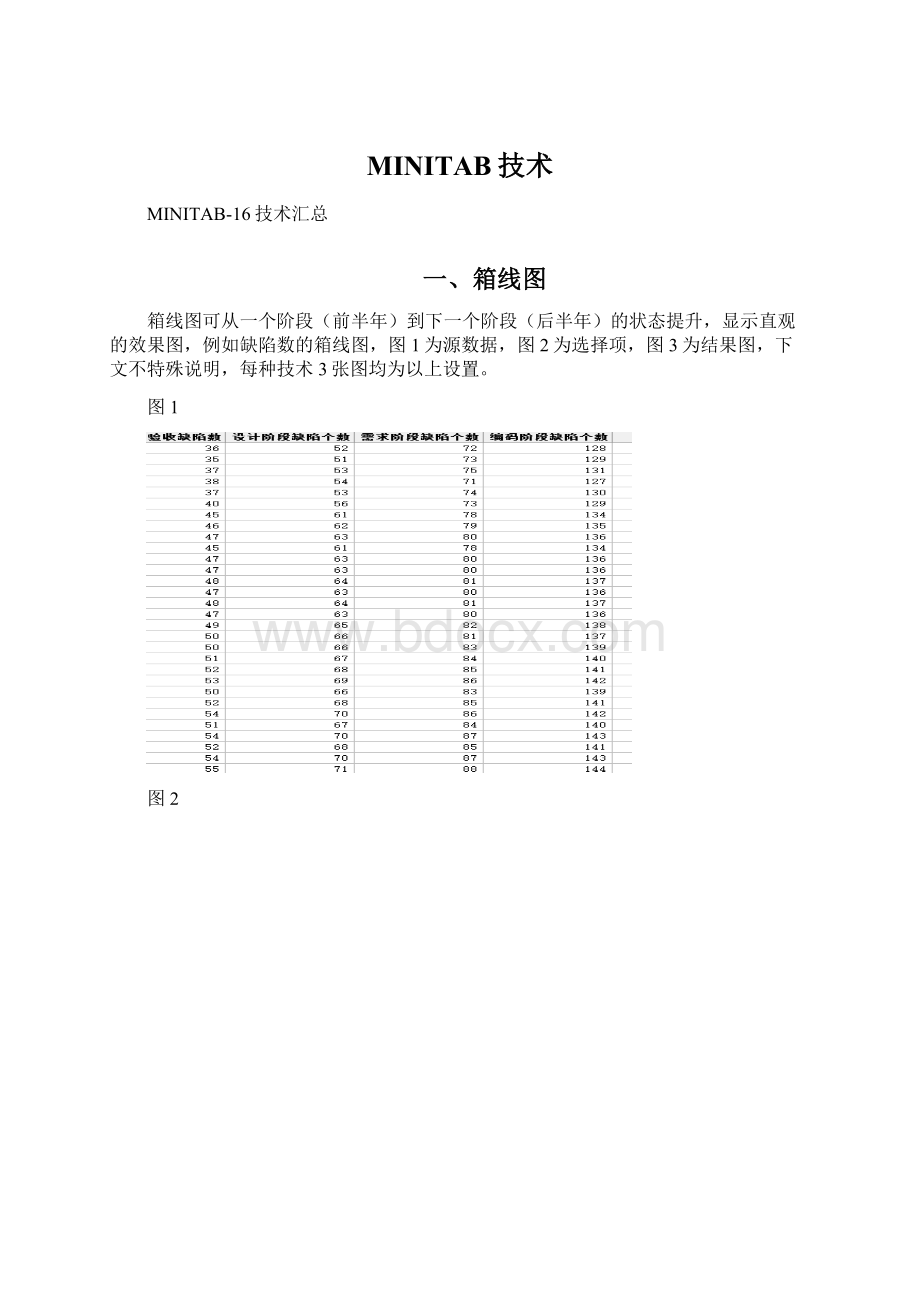
MINITAB技术
MINITAB-16技术汇总
一、箱线图
箱线图可从一个阶段(前半年)到下一个阶段(后半年)的状态提升,显示直观的效果图,例如缺陷数的箱线图,图1为源数据,图2为选择项,图3为结果图,下文不特殊说明,每种技术3张图均为以上设置。
图1
图2
图3
鼠标悬停在箱体内,可以显示中位数、四分卫数和均值箱体框,这里以不同阶段的缺陷数为例,从上图可以清晰看见缺陷数的改进提升效果。
二、控制图
2.1标准控制图
控制图的使用方法非常简单,均值、上限(均值+3倍标准差),下限(均值-3倍标准差),下限因为是单纯的减法,所以可能导致某些数据为负(此种情况通常出现在标准差较大),可以通过控制图中的设置将下限设置为0,即下限不会出现负数的情况。
这里以需求阶段生产率为例,见下图:
图1
图2
图3
控制图的判异原则一般有,1)点子出界、2)6点都呈现往上或下、3)9点都在同一侧,4)14点交替上升下降。
2.2分阶段控制图
本章具体介绍控制图和分阶段的控制图,以下为分阶段的控制图介绍:
分阶段的控制图,具体好处是直观的显示稳定的生产率之前和之后的比较,数据的律动情况和上下限都能一目了然。
图1
图2
图3
从以上图形,可以明显看出之前和之后的标准差、均值对比,对两阶段的不同图形也能直观反映在同一张控制图上,对于过程改进的之前和之后效果图,尤为直观。
三、正态分布图
正态分布,作为检验一组数据是否呈正态分布,一般是SPC(统计过程控制)的先导步骤。
图1
源数据省略
图2
图3
从上图可见,P值=0.172>0.05,所以总生产率是呈正态分布的。
四、单因子方差分析
单因子方差分析,通常是为了找出Y值到底是受哪种因子影响,这些因子是否可以分组,如果他们是纠缠在一起的一组数据(比如各因子没有呈现单独的关系),那么可能需要继续往下探究各个因子的子因子是否能够分组,如果到了最低层的因子依然没有呈现显著的不同,那么这组数据就需要舍弃掉,因为他们是同一类的数据。
MINITAB中X值通常以数字代表进行分析,比如下例中我们需要洞察生产率是否受行业、模型和编程语言的分组影响,那么我们就将客户行业设置为1,模型设置为2,编程语言设置为3。
图1
Y值=生产率
X值分别=客户行业、生命周期模型、不同的编程语言
图2
图3
总生产率与客户行业
来源自由度SSMSFP
客户行业26863430.270.763
误差54680641260
合计5668750
S=35.50R-Sq=1.00%R-Sq(调整)=0.00%
均值(基于合并标准差)的单组95%置信区间
水平N均值标准差---+---------+---------+---------+------
119190.6728.35(----------------*---------------)
222182.4739.12(--------------*---------------)
316185.9837.82(-----------------*-----------------)
---+---------+---------+---------+------
170180190200
合并标准差=35.50
通过上图可知:
P值=0.763>0.05,所以总生产率和客户行业无关。
五、图形化汇总
图形化汇总,可以从图中清楚的观察到,均值、标准差和百分比的可能性值,对于单值的分析非常适用。
图1
图2
图3
从图形化汇总可见:
最小值和最大值,均值,标准差,正态性检验P值。
六、帕累托分析
帕累托分析,即20/80原则,一般适用于从所有影响因素中找出最关键的几项,通常是百分之二十的因素导致了百分之八十的问题。
图1
源数据省略,一般为单列统计出现的问题次数
图2
图3
七、双样本T检验
双样本T检验,适用于两个过程之间的显著变化统计,用值的形式显示于计算图表中。
图1
源数据省略,一般是不同的两组数据,在过程之前和之后的统计
图2
图3
双样本T检验和置信区间:
2014年前三月验收缺陷率,部署后验收缺陷率
2014年前三月验收缺陷率与部署后验收缺陷率的双样本T
N均值标准差均值标准误
2014年前三月验收缺陷率120.81750.03570.010
部署后验收缺陷率200.56040.04130.0092
差值=mu(2014年前三月验收缺陷率)-mu(部署后验收缺陷率)
差值估计值:
0.2500
差值的95%置信区间:
(0.2216,0.2784)
差值=0(与≠)的T检验:
T值=18.07P值=0.000自由度=26
从上述结果可见P值=0<0.05,所以验收缺陷率在部署前后有显著的变化。
八、卡方检验
卡方检验,当需要比较的两组数据都为离散数时,通常采用卡方检验判断数据组之间是否存在强弱的关系。
图1
源数据省略,当两组数据都为离散型数据时
图2
图3
将Y值和X值分别赋值,例如:
Y=复用率
X=注释问题、代码规范性问题、提交版本问题。
列表统计量:
复用率,提交版本问题
行:
复用率列:
提交版本问题
提交不提交
正确正确全部
低224
高224
中033
全部4711
单元格内容:
计数
Pearson卡方=1.238,DF=2,P值=0.308
似然比卡方=2.310,DF=2,P值=0.189
从以上卡方分析可见,P值=0.308>0.05,所以提交版本问题和复用率没有关系。
列表统计量:
复用率,代码规范性问题
行:
复用率列:
代码规范性问题
不规范规范全部
低224
高224
中033
全部4711
单元格内容:
计数
Pearson卡方=1.362,DF=2,P值=0.035
似然比卡方=2.260,DF=2,P值=0.089
从以上卡方分析可见,P值=0.035<0.05,所以代码规范性问题和复用率有关系。
列表统计量:
复用率,代码注释问题
行:
复用率列:
代码注释问题
注释注释不
正确正确全部
低224
高224
中033
全部4711
单元格内容:
计数
Pearson卡方=1.857,DF=2,P值=0.162
似然比卡方=1.312,DF=2,P值=0.145
从以上卡方分析可见,P值=0.162>0.05,所以代码注释问题和复用率没有关系。
九、过程能力指数CPK
过程能力指数CPK,一般为判断实际的过程能力是否达到了组织的目标,或者客户声音的一种判断图形。
图1
源数据省略,将实际的过程绩效带入工具,将客户或组织的目标要求设定为CPK的上下限。
图2
图3
通过对项目编码阶段生产率和公司编码能力范围进行CPK分析,可见该项目编码阶段生产率的能力指数CPK=1.27。
说明该项目的编码生产率过程能力指数为强。
CPK判断准则为下图:
这里再对CPK和PPK进行一个差别说明:
关于Cpk与Ppk的关系,这里引用QS9000中PPAP手册中的一句话:
“当可能得到历史的数据或有足够的初始数据来绘制控制图时(至少100个个体样本),可以在过程稳定时计算Cpk。
对于输出满足规格要求且呈可预测图形的长期不稳定过程,应该使用Ppk。
”
所谓PPK,是进入大批量生产前,对小批生产的能力评价,一般要求≥1.67;而CPK,是进入大批量生产后,为保证批量生产下的产品的品质状况不至于下降,且为保证与小批生产具有同样的控制能力,所进行的生产能力的评价,一般要求≥1.33;一般来说,CPK需要借助PPK的控制界限来作控制。
十、拟合回归
拟合回归,一般为制作PPM模型计算不同变量联系的一种技术,该技术提供了变量之间的计算公式。
图1
源数据省略,这里以需求阶段的缺陷数和项目总规模(代码行数)进行拟合回归分析。
图2
响应Y:
项目总规模,预测变量X:
需求阶段缺陷数。
图3
使用Minitab回归拟合分析后,从上图可见,需求阶段质量的回归方程式为:
38.56+0.000475*项目总规模。
标准差预判为:
(75-66)/6=1.5。
十一、相关性分析(Pearson检验)
相关性分析,主要目的是查看两组因子之间是否有联系,通常以Pearson指数来判定他们之间联系的强弱关系,从这点来看,Pearson指数和CPK指数有异曲同工之妙,只是前者是查看相关性强弱的指数,后者是查看过程能力的指数。
图一
图二
图三
相关:
合同额,总工时
合同额和总工时的Pearson相关系数=0.631
P值=0.001
从以下的判断说明可以看出,0.631在0.6-0.8之间,为强相关关系。
(判断说明:
相关系数的绝对值越大,相关性越强,相关系数越接近于1或-1,相关度越强,相关系数越接近于0,相关度越弱。
通常情况下通过以下取值范围判断变量的相关强度:
相关系数0.8-1.0极强相关
0.6-0.8强相关
0.4-0.6中等程度相关
0.2-0.4弱相关
0.0-0.2极弱相关或无相关。
)