氨法脱硫规程烟气脱硫技术.docx
《氨法脱硫规程烟气脱硫技术.docx》由会员分享,可在线阅读,更多相关《氨法脱硫规程烟气脱硫技术.docx(18页珍藏版)》请在冰豆网上搜索。
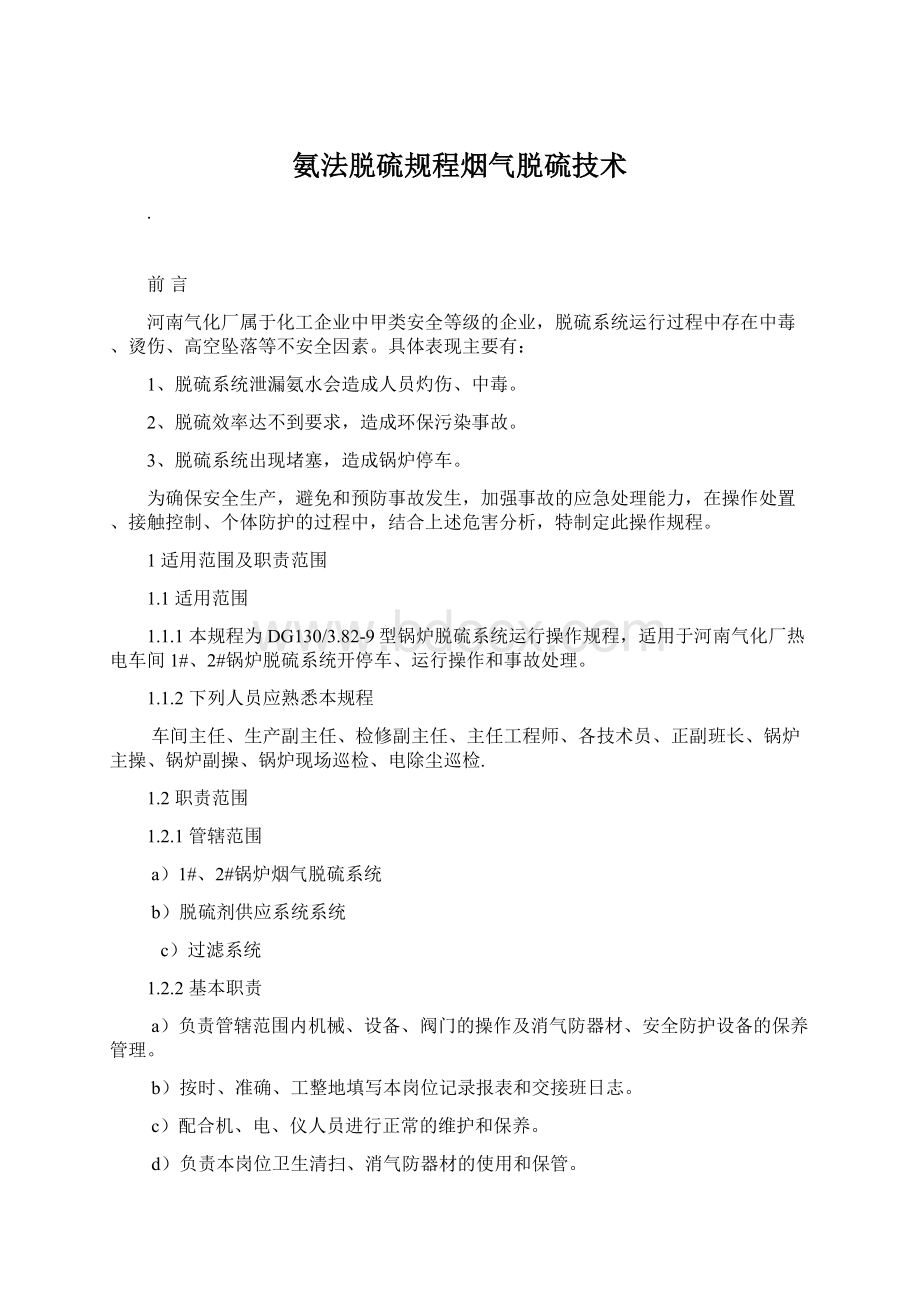
氨法脱硫规程烟气脱硫技术
.
前言
河南气化厂属于化工企业中甲类安全等级的企业,脱硫系统运行过程中存在中毒、烫伤、高空坠落等不安全因素。
具体表现主要有:
1、脱硫系统泄漏氨水会造成人员灼伤、中毒。
2、脱硫效率达不到要求,造成环保污染事故。
3、脱硫系统出现堵塞,造成锅炉停车。
为确保安全生产,避免和预防事故发生,加强事故的应急处理能力,在操作处置、接触控制、个体防护的过程中,结合上述危害分析,特制定此操作规程。
1适用范围及职责范围
1.1适用范围
1.1.1本规程为DG130/3.82-9型锅炉脱硫系统运行操作规程,适用于河南气化厂热电车间1#、2#锅炉脱硫系统开停车、运行操作和事故处理。
1.1.2下列人员应熟悉本规程
车间主任、生产副主任、检修副主任、主任工程师、各技术员、正副班长、锅炉主操、锅炉副操、锅炉现场巡检、电除尘巡检.
1.2职责范围
1.2.1管辖范围
a)1#、2#锅炉烟气脱硫系统
b)脱硫剂供应系统系统
c)过滤系统
1.2.2基本职责
a)负责管辖范围内机械、设备、阀门的操作及消气防器材、安全防护设备的保养管理。
b)按时、准确、工整地填写本岗位记录报表和交接班日志。
c)配合机、电、仪人员进行正常的维护和保养。
d)负责本岗位卫生清扫、消气防器材的使用和保管。
e)服从班长的领导和指挥,遇有异常现象立即向分管管理人员汇报,遇到对人身和设备有严重危害的故障,有权先停车后汇报,对违章指挥有权拒绝执行并向有关领导汇报。
f)有权制止他人接近或操作本岗位设备。
2.工艺原理
2.1烟气吸收工艺原理
氨水通过喷淋与烟气接触,吸收烟气中的二氧化硫,最终生成亚硫酸铵,反应式如下:
SO2+NH3+H2O=NH4HSO3
(1)
SO2+2NH3+H2O=(NH4)2SO3
(2)
SO2+(NH4)2SO3+H2O=2NH4HSO3(3)
NH3+NH4HSO3=(NH4)2SO3(4)
上述反应中,在送入氨量较少时,则发生
(1)式反应;在送入氨量较多时,则发生
(2)式反应;而式(3)表示的是氨法脱硫吸收反应的主反应式;因吸收过程中所生成的酸式盐NH4HSO3对SO2不具有吸收能力,吸收液中NH4HSO3数量增多时对SO2吸收能力下降,操作中需向吸收液中补充氨,使部分NH4HSO3转变为(NH4)2SO3,这就发生(4)式反应,以保持吸收液对SO2的吸收能力。
2.2.工艺流程
本装置采用的工艺为湿式氨法脱硫工艺,采用一定浓度的氨水为脱硫剂来脱除烟气中的二氧化硫,回收的副产品硫酸铵可作为商品出售。
本装置总流程为:
热烟气自引风机引出后,首先在脱硫塔进风管和浓缩段与喷淋的硫酸铵溶液进行热交换降温增湿,同时浓缩硫酸铵溶液;然后进入脱硫段,与喷淋的亚硫酸铵液接触进行SO2吸收,完成脱硫;进入洗涤段后再与喷淋的循环水接触,进一步脱除逃逸的SO2和NH3;最后经除雾器除雾后进入烟囱,排入大气。
脱硫后生成的亚硫酸铵液经氧化生成硫酸铵,再经预浓缩、过滤、蒸发浓缩、甩干、干燥、包装等,得到副产品硫酸铵。
本装置分为脱硫系统与产品回收系统,这两个系统中又各有子系统,现分项说明如下:
2.2.1脱硫系统
本系统由SO2吸收系统(包含几个子系统)、亚硫酸铵氧化循环、硫酸铵预浓缩循环、除杂系统组成
2..2.2烟风系统
(1)热风自进风管引出后,以在风管内首先与喷淋的硫酸铵溶液接触,在蒸发其水分的同时进行降温,然后进入脱硫塔浓缩段,在塔内以3.5米/秒左右流速逐步上升,上升过程中首先与喷淋的硫酸铵溶液接触,对其进行浓缩,同时完成进一步降温。
(2)气流上升穿过浓缩段升气帽后,开始与脱硫段喷淋的亚硫酸铵溶液接触,烟气中的SO2被亚铵液中的NH3和(NH4)2SO3吸收,完成脱硫过程。
在此过程中亚铵液中的水分会部分蒸发,在亚铵液喷淋的上部设置循环水喷淋,以补充蒸发的水分。
(3)气流上升穿过脱硫段升气帽后,开始与喷淋的循环水接触,以洗去烟气中未脱除干净的SO2和逃逸的NH3,同时也除去脱硫段中形成的微小液滴。
循环水补充至脱硫段部分的水分,由其上喷淋的工艺水补充,以维持系统中水的平衡。
(4)气流继续上升穿过除沫器,以除去在脱硫过程中形成的液沫,减少烟气中夹带的水分并尽可能多地回收产品。
除沫后的湿烟气经塔顶烟囱排入大气。
烟气经上述操作后完成脱硫操作。
2.2.3液体物料循环吸收系统
(1)工艺水流程
工艺水去循环水洗涤段最上层喷淋,目的是洗涤吸收从下部逃逸的NH3和SO2,并补充因水循环段补充脱硫段用水而缺损的水量,本路工艺水喷淋后在升气帽上汇集流入循环水罐,在管路上设置电动调节阀与循环水罐的液位计联控,以保持循环水罐液位的稳定。
(2)水循环流程
由循环水泵将循环水自循环水罐中打出,打出后分为三路:
第一路去循环水喷淋层喷淋,为主管路;此喷淋与上层喷淋的工艺水一起下落,捕捉随气流逃逸的SO2和NH3,并在升气帽上形成水膜继续捕捉SO2和NH3,以保证脱硫效果和产品回收率,此喷淋液除少量挥发外,绝大部分在升气帽上积液后回流入循环水罐。
第二路在脱硫段的最上层喷淋,以补充脱硫段和浓缩段为控制各塔段温降而喷淋蒸发的水分,本路循环水喷淋后与亚硫酸铵溶液一起在升气帽上汇集后流入亚硫酸铵循环罐,本路循环水设置电动调节阀与亚硫酸铵循环罐的液位计联控,以保持亚硫酸铵循环罐液位的稳定。
第三路去塔的最上层清洗除雾器(分为四层),为间歇式喷淋,以冲洗除雾器上的结晶,防止除雾器堵塞引起的压降增大,此层喷淋水喷淋后回流到循环水罐。
此路喷淋使用时第一路水需关小或关闭,控制方式由电控阀与第一路水联控。
2.2.4亚硫酸铵循环脱硫流程
本路循环由脱硫循环泵将亚硫酸铵溶液自亚铵罐中打出,打出后在脱硫段循环水喷淋下方分两层进行喷淋,以保持喷淋覆盖率在200%以上,保证脱硫效率。
此喷淋与上层喷淋的循环水一起下落,以吸收随气流上升的SO2,吸收SO2的是亚铵液中的NH3和(NH4)2SO3,吸收后形成NH4HSO3,吸收SO2后的溶液在升气帽上汇集并溢流入亚铵罐,完成脱硫循环,在亚铵罐中部分NH4HSO3与补充氨水中的NH3反应生成(NH4)2SO3,恢复脱硫能力。
周而复始。
本循环因烟气温度较高,会挥发出较多水分,加之从亚铵罐向氧化罐的出料,水分需不断补充,水分的补充有两个来源:
一是循环水喷淋补水,二是所补充氨水所带水分,补氨时自动带入。
补氨流量由设在亚铵罐上的PH计与补氨管路上的电动调节阀联控实现。
控制亚铵罐PH是保证亚铵液中含合适浓度的自由氨和亚硫酸铵,以保证脱硫效果,同时也为了向氧化罐提供合格待氧化液。
亚铵罐向氧化罐的出料通过亚铵循环泵出口管路上的抽出管来实现,管路上设置电动调节阀与塔底液位计联控,以保持塔底液位的稳定,保证浓缩循环流程中的液量。
向氧化罐出料后亚铵罐中的液位会必然下降,所缺损的液量由循环喷淋水补充。
2.2.5亚硫酸铵氧化循环
自亚铵罐来的亚铵液首先通过自吸空气氧化泵进入氧化罐第一级,所吸入空气会自动将亚硫酸根氧化为硫酸根,从而使亚硫酸铵变为硫酸铵。
因自动吸入的空气被高速液流剪切为极其细小的颗粒,并均匀分散于液流之中,空气中氧气的氧化效率较高。
亚铵液在氧化罐中的循环氧化共分为三级:
由氧化循环泵自罐底抽出,进入自吸空气氧化泵内高速喷射并吸入空气氧化后再进入罐内,上一级氧化液自动溢流到下一级继续氧化,到第三级后已基本氧化完全。
在第三级继续氧化的同时分为两种方式出料:
一是自第三级的溢流口自动溢流入脱硫塔浓缩段底部进行浓缩循环,二是自第三级氧化泵的出口抽出管进入脱硫塔烟气进口管对烟气进行降温,实际操作中设置第二种出料方式比进料量稍低,剩余亚铵自溢流口流入塔底,氧化罐液位始终保持恒定。
2.2.6硫酸铵稀溶液预浓缩循环
进入浓缩段的稀硫酸铵溶液需在脱硫塔浓缩段蒸发浓缩至40%含量;目的一是为刚进入系统的热烟气降温,以保护塔体及改善脱硫段脱硫效果;二是充分利用热烟气的热量,以高含量的硫酸铵溶液进入蒸发系统,以节约蒸发系统的蒸汽。
流程为:
硫铵液由浓缩循环泵自塔底抽出,分别进入热烟气进口喷淋管和脱硫塔浓缩段喷淋管,溶液喷淋后在热烟气的加热下蒸发出大量水分,一方面降低了烟气温度,一方面浓缩了溶液。
两路喷淋的溶液均落入塔底,不断循环,直至浓度合格为止。
浓度合格后由出料泵打入过滤机过滤。
出料流量的控制由设在出料管路上的电动调节阀与流量计联控实现,控制目的是向过滤机输送符合浓度要求的硫酸铵溶液,并以相对稳定的流量向过滤机输送。
2.2.7除杂系统
用的除杂方式为过滤,由出料泵向厢式压滤机供料,含粉煤灰杂质的溶液经过滤除去粉尘,清液进入滤液池后待进一步处理回收。
3.技术指标和工艺设备参数
Ø处理气体:
锅炉烟气
Ø进入脱硫除尘系统烟气量:
2×195000Nm3/h
Ø进入脱硫除尘系统烟气温度:
160℃
Ø脱硫塔出口烟气温度:
50-60℃。
Ø进系统烟气温度:
≤140℃~160℃。
Ø脱硫系统压降:
≤1000Pa
Ø除雾器压降:
≤150Pa
Ø进入系统的SO2量:
713.90kg/h
Ø进入系统的SO2浓度:
1830.5mg/Nm3
Ø脱硫后净烟气中的SO2含量不超过100mg/Nm3。
Ø氨水9.007t/h
Ø水9.80t/h
Ø电158kw·h/h
Ø亚铵罐V03:
PH值6.0至6.2;正常液位:
+2000mm,波动区间:
+600~+2500mm
Ø氨水罐液位波动区间:
+600~+3500mm
Ø循环水罐液位:
正常液位:
+1500mm,波动区间:
+600~+2000
Ø滤液罐液位波动区间:
+600~+3500mm
系统主要工艺设备
序号
位号
设备名称
技术规格
生产厂家
材料或性能等级
单位
数量
重量(㎏)
备注
单重
总重
1
T01
脱硫塔
Φ7500×25500mm
碳钢Q235B
座
1
内衬玻璃鳞片防腐
2
V01
氨水罐
Φ4550(罐底)×4070mm
碳钢Q235B
座
1
内衬玻璃鳞片防腐
3
V02
清水罐(塔底)
Φ7500×2300mm
碳钢Q235B
座
1
内衬玻璃鳞片防腐;布置于塔内,底层
4
V03
亚铵罐
Φ6000×4000mm
碳钢Q235B
座
1
内衬玻璃鳞片防腐
5
V04
滤液罐
Φ3000×4000mm
碳钢Q235B
座
1
内衬玻璃鳞片防腐
6
P01AB
氨水泵
Q=15m3/hH=10mP=1.1KW
烟台龙港
304
台
2
7
P02AB
循环水泵
Q=140m3/hH=48mP=37KW
烟台龙港
2205
台
2
8
P03AB
脱硫循环泵
Q=280m3/hH=35mP=55KW
烟台龙港
2205
台
2
9
P04AB
出料泵
Q=15m3/hH=70mP=15KW
烟台龙港
2205
台
2
10
P05AB
滤液泵
Q=12m3/hH=25mP=3KW
烟台龙港
2205
台
2
11
B01
密封风机
37KW
台
1
12
M01
箱式压滤机
8KW
长葛盛威
Q235B+PP
台
1
4.1#、2#锅炉脱硫系统投运及操作
4.1脱硫系统投运前的检查
4.1.1确认检修工作全部结束,各检修施工设施已完成拆除,工作票回收至车间核实各项目均已完成;
4.1.2脱硫系统塔、罐、池类静态设备进行清理和清洗,不得有异物,完毕后封闭人孔、手孔、观察孔等,防止异物二次进入;
4.1.3所有液位计投入正常,报警系统投入正常;
4.1.4所有热工仪表、电源开关、调节装置及报警信号、保护装置齐全、指示正确;
4.1.6检查完毕后,工艺人员办理送电票,电气人员负责隔离开关投至“工作”位置送上电源。
4.2泵类设备开车
a)启动前的准备
1)拔转电机风叶,水泵应转动灵活,无卡磨现象。
2)打开进水阀门及电机座上的放气塞,使泵腔充满水,放气塞排出水后拧紧放气塞。
3)点动电机确定转子的转向应符合旋转标志。
b)启动与运行
1)全开进口阀门,关闭出口阀门。
2)接通电源,当泵正常运转后,逐渐打开水管路上的阀门,并调节至所需工况。
3)注意观察仪表读数,检查机械密封情况,应无泄漏。
4)检查泵的振动,有无不正常噪音,如发现异常,及时停车处理。
5)检查电机的负载电流,应在铭牌额定值以内,如负荷电流太高,应调节流量,降低电机负载电流。
c)运行中的维护
1)进口管道必须充满液体,禁止泵在汽蚀状态下长期运行。
2)定期检查电动机的电流值,不得超过额定电流。
3)经长期运行,如泄漏量增大、压力显著下降,或噪音、振动增大,应停泵检查,必要时更换易损件,如机械密封、轴承、叶轮等。
4.3厢式压滤机开车
4.3.1操作前的检查
(1)油泵油位正常,油管路畅通。
(2)检查滤布状况,滤布不得折叠和破损。
(3)检查各接口连接完好,法兰螺栓、垫片无泄漏。
4.3.2压滤机启动与运行
(2)启动与运行程序
a.合上电源开关,电源指示灯亮。
b.按“启动”按钮,启动油泵。
c.将所有滤板移至止推板端,并使其位于两横梁中央。
d.按“压紧”按钮,活塞推动压紧板,将所有滤板压紧,达到液压工作压力值后(16~20MPa),旋转锁紧螺母锁紧保压,按“关闭”按钮,油泵停止工作。
e.打开压滤机出料阀
1、全开滤液泵进口阀门,关闭出口阀门。
2、打开冷却水阀门,调节水压为0.02~0.04Mpa
3、启动滤液泵,当泵运转且压力达到所需指标时,打开泵出口阀门。
4.注意观察仪表读数(出口压力表),检查机械密封情况,应无泄漏。
5.检查泵的振动,有无不正常噪音,如发现异常,及时停车处理。
6.检查电机的负载电流,应在铭牌额定值以内,如负荷电流太高,应调节流量,降低电机的负载电流。
7.严禁缺水运行,当泵出口压力显示大幅晃动或压力大幅减小时,表示水已用完,应及时停泵。
4.3.3压滤机停车
a.逐渐关闭出口阀门,切断电源,关闭进口阀。
b.如环境温度低于0℃,停泵后应将泵内液体放净,以免冻裂。
c.如长期停用,应放空液体,必要时将泵拆卸、清洗、涂油封装。
5、脱硫系统开车
5.1脱硫开车前的准备工作
(1)开车用氨水已经备足,且含量等质量指标符合要求;
(2)确认锅炉工作状态正常:
记录锅炉的工作负荷、引风机工作参数(电机工作电流、工作压力、烟气温度等有关参数)、确认锅炉燃煤含硫率等;
(3)从配电室向脱硫系统供电。
(4)打开仪表控制系统。
使系统所有仪表投入运行,巡检室内外所有仪表显示状态工艺管道设备完好。
(5)脱硫设施各系统检查已经结束,确认具备开车条件。
5.2脱硫系统开车及运行调整
1)打开工艺水管路上的进水阀(开度到最大),V02循环水罐开始进工艺水;打开调节阀LV103,V03亚铵罐开始进工艺水。
2)循环水罐V02内液位达+2000mm时,启动一台循环水泵(P02),脱硫塔(T01)内循环水喷淋层开始喷淋。
记录开泵时间。
3)打开亚铵补水阀LV103,向V03亚铵罐注工艺水。
液位达到+1000时,启动一台脱硫循环泵(P03),脱硫塔(T01)吸收喷淋层开始喷淋。
4)设置V03液位与V03进水调节阀连锁自动。
5)开车过程中应注意调节系统仪表,使液位、流量始终处于正常范围。
6)开车过程中应特别注意液位调节的准确与否,如果失准,应及时调节。
若调节无效,应及时关闭工艺水进料管上的阀门,排查原因,调节正常后重新开车。
7)开车中若发现泵类设备故障,应紧急停车,启动备用泵。
8)打开氨水罐出液阀,启动一台氨水泵,氨水流量手动调节,控制流量在正常流量的2/3,此时要巡视供氨系统运行情况,运行10分钟后,要调整流量,要基本和进烟量成比例,待进烟量稳定正常后将调解阀组和液氨的调节阀组设置为自动。
9)启动氨水泵10分钟后,全部打开烟气进出脱硫塔的电动阀,将锅炉引风机原出口烟道的风阀关小至原开度的2/3,运行15分钟。
观察并记录脱硫塔、风管、锅炉、引风机运行参数、亚铵罐V03的PH及氨水流量等情况,必要时做出调整。
全部正常后稳定运行60分钟。
开车过程中,每动一次风门,都要巡视,并密切联系锅炉主控室,无异常后,才进行下一步。
10)将锅炉引风机原出口烟道的风阀关小至原开度的1/2,运行15分钟,将锅炉引风机原出口烟道的风阀关小至原开度的2/3,运行15分钟。
观察并记录脱硫塔、风管、锅炉、引风机运行参数、亚铵罐的PH及氨水流量等情况,必要时做出调整。
全部正常后稳定运行30分钟。
11)将锅炉引风机原出口烟道的风阀关小至原开度的1/4,运行5分钟。
观察并记录脱硫塔、风管、锅炉、引风机运行参数、亚铵罐的PH及氨水流量等情况,必要时做出调整。
正常后稳定运行120分钟。
如有对锅炉运行不利的异常情况时,将锅炉引风机原出口烟气入烟道的风阀开度开回到1/2开度,分析找出原因,调整锅炉或引风机运行参数,然后再行调试。
12)全关闭锅炉引风机原出口烟气入烟道风阀,此时锅炉烟气全部经过脱硫系统到烟囱排放。
巡视无异常持续运行。
13)系统运行正常后,及时启动连锁保护装置。
启动后,一定要让仪表人员检查,确认自动连锁保护装置已投入正常运行。
5.3脱硫系统运行中的调节
系统启动及投入运行后,应通过调节各工艺管路上的阀门,使脱硫率、脱硫塔内各段温降、各项操作工艺条件等均处于设计范围内。
(1)系统需维持的正常参数如下:
1进系统烟气温度:
≤140℃~160℃。
2脱硫塔出口烟气温度:
50-60℃。
3脱硫系统压降:
≤1000Pa。
4除雾器压降:
≤150Pa。
5亚铵罐V03:
PH值6.0至6.2;正常液位:
+2000mm,波动区间:
+600~+2500mm
6氨水罐液位波动区间:
+600~+3500mm
7循环水罐液位:
正常液位:
+1500mm,波动区间:
+600~+2000
8滤液罐液位波动区间:
+600~+3500mm
(2)满负荷运行时各泵参数控制如下:
设备或管道位号和名称
出口压力(MPa)
流量(m3/h)
温度(℃)
备注
FI101
10
P01氨水泵及FI102
0.4-0.5
15
10~30
P03脱硫循环泵
0.4~0.6
~280
40~50
FI103
——
80-100
——
FI104
——
10
——
P02循环水泵
0.4~0.6
~140
40~50
P04出料泵
0.35~0.5
~15
40~50
P05滤液泵
0.3~0.5
~10
40~50
根据运行情况,控制参数随时调整,也可决定系统的手动与自动,确保系统运行平稳。
运行中可能出现局部故障,只要对锅炉及引风机运行不造成不利情况,无需系统停车,局部检修即可。
5.3.1运行中除雾器的冲洗操作
除雾器是脱硫塔内重要部件,是烟气出塔前最后一道处理程序,为保证除雾效率及减小压降,运行中必须对除雾器进行必要的清洗,以防止除雾器堵塞,冲洗步骤如下:
(1)检查冲洗水管路上的手动阀门是否开启,自控调节阀是否设置好,并完好侍命;
(2)电动阀按设定的冲洗程序定期或定压差依次启动下、中、上层冲
(3)冲洗效果不佳时,可手动启动冲洗程序,强制冲洗.
(4)自动冲洗效果不佳或无法达到要求时,可打开冲洗层手孔,进行手工清洗;
(1)注:
定时冲洗一般为每4小时各轮流冲洗一次;定压差冲洗一般为当压差达到约200Pa时,分层轮流冲洗一次,冲洗时间视压降变化情况而定。
5.4脱硫系统正常运行中的注意事项
(1)时刻注意工艺参数变化情况,进行必要的调节,使系统处于正常运行状态;
(2)每二小时进行一次现场巡检,要按规定时间、线路和内容进行检查,并按规定格式填写巡回检查记录;
(3)巡检中发现流程泵异常时,应及时启动备用泵,并报修故障泵;
(4)巡检时发现跑冒滴漏现象应及时做出处置并上报,以便及时采取应对措施;
(5)对发现的其它系统或设备故障,应及时做出判断,采取应对措施,方法详见(系统及设备故障处理)。
6、脱硫系统停车
6.1正常停车
(1)正常停车,应首先打开热烟气入烟囱风阀,关闭热烟气入脱硫系统风阀,稍等再关闭湿烟气出脱硫系统风阀。
(2)关闭工艺水进料管上的阀门,停止系统进水。
(3)关闭补氨水阀,停止补氨水。
(4)关循环泵出口阀,手动停循环泵
(5)关氨水泵出口阀,手动停氨水泵
(6)停压滤机
6.2紧急停车
(1)紧急停车,应首先打开热烟气入烟囱风阀,关闭热烟气入脱硫系统风阀,稍等再关闭湿烟气出脱硫系统风阀。
(2)关闭工艺水进料管上的阀门,停止系统进水。
(3)关闭补氨水阀,停止补氨水
(4)停氨水泵、循环泵、压滤机。
7、脱硫系统联锁保护
(1)当脱硫系统热烟气进风温度大于170℃、增浓循环泵突然停泵、脱硫塔塔底液位低,低报警时,系统将自动进入解列程序,解列时将首先打开热烟气入烟囱风阀,然后关闭热烟气入脱硫系统及湿烟气出脱硫系统风阀;
(2)当系统供电中断或停电时,应及时手工干预解列系统,解列程序与自动解列程序相同。
(3)系统解列后操作人员应及时上报,根据领导指示或根据实际情况决定是否紧急停车。
系统及设备的常见故障分析与调整维修
现象
原因
措施
液位调节失准
液位计失灵
检查、校验液位计
检查液位计接管是否堵塞,罐体内是否淤积
电动调节阀阀芯失灵
检查电动调节阀,如有故障,更换新的电动调节阀
管路或喷嘴堵塞
供液不足时检查进液管路,出液不足时检查出口管路,查出故障点后冲洗管路或更换喷嘴
除雾器冲洗水量太大
合理设置,减少冲洗水量
烟风系统压降太大
风管堵塞
清理风管
除雾器内有结晶
若除雾器压差太大,则为该处堵塞,及时冲洗
升气帽内有结晶
停车冲洗
脱硫率达不到要求
亚铵液PH太低
合理提高PH
进脱硫段烟气温度太高
提高浓缩段喷淋蒸发效果,降低烟温
喷嘴堵塞,烟气短路
检修或更换喷嘴
泵流量不足,喷淋量小,雾化不好致吸收差
检查原因并排除
除雾效果差,液沫夹带多
降低循环水喷淋量,使之喷淋变粗
亚铵浓度太高,形成气溶胶
提高浓缩段喷淋蒸发效果,以增加浓缩段蒸发量,降低亚铵出料浓度
氨逃逸量超标
亚铵液PH太高
合理调低PH
喷嘴堵塞,烟气短路
检修或更换喷嘴
泵流量不足,喷淋量小,雾化不好致吸收差
检查原因并排除
亚铵浓度太高,形成气溶胶
提高浓缩段喷淋蒸发效果,以增加浓缩段蒸发量,降低亚铵出料浓度
亚铵罐PH调节失准
PH计失准
检查并校验仪表
电动阀调节失灵
修理或更换
亚铵与氨水混合不匀
在管路或罐内采取措施促其混匀
故障
可能的原因
解决办法
泵不出水
1、水泵反转
2、吸程过高
3、泵腔内蓄水太少
4、吸入管路漏气
1、调整电机接线
2、降低水泵安装位置
3、加注水,打开排气螺塞排气
4、