烟气脱硫技术.docx
《烟气脱硫技术.docx》由会员分享,可在线阅读,更多相关《烟气脱硫技术.docx(12页珍藏版)》请在冰豆网上搜索。
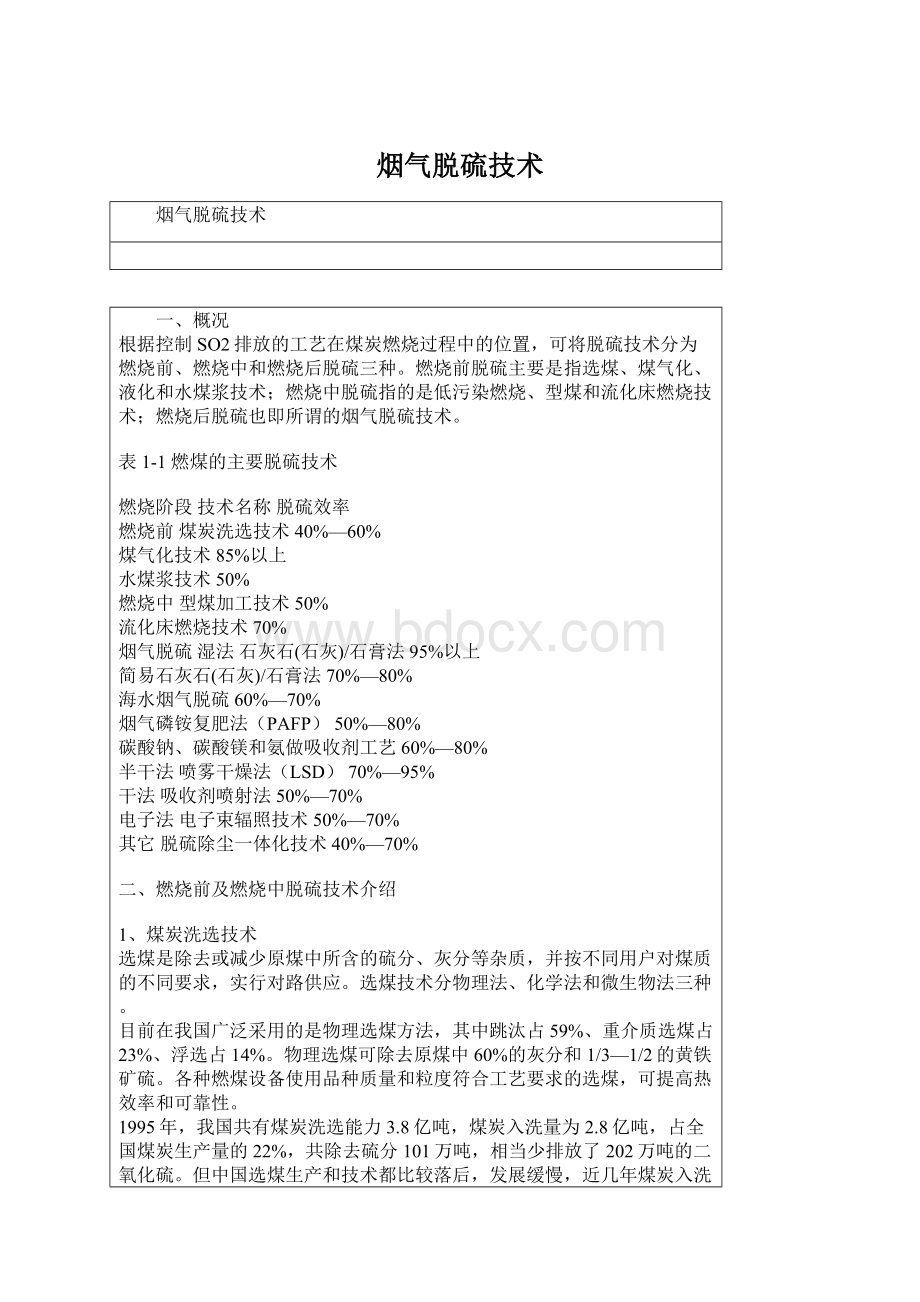
烟气脱硫技术
烟气脱硫技术
一、概况
根据控制SO2排放的工艺在煤炭燃烧过程中的位置,可将脱硫技术分为燃烧前、燃烧中和燃烧后脱硫三种。
燃烧前脱硫主要是指选煤、煤气化、液化和水煤浆技术;燃烧中脱硫指的是低污染燃烧、型煤和流化床燃烧技术;燃烧后脱硫也即所谓的烟气脱硫技术。
表1-1燃煤的主要脱硫技术
燃烧阶段技术名称脱硫效率
燃烧前煤炭洗选技术40%—60%
煤气化技术85%以上
水煤浆技术50%
燃烧中型煤加工技术50%
流化床燃烧技术70%
烟气脱硫湿法石灰石(石灰)/石膏法95%以上
简易石灰石(石灰)/石膏法70%—80%
海水烟气脱硫60%—70%
烟气磷铵复肥法(PAFP)50%—80%
碳酸钠、碳酸镁和氨做吸收剂工艺60%—80%
半干法喷雾干燥法(LSD)70%—95%
干法吸收剂喷射法50%—70%
电子法电子束辐照技术50%—70%
其它脱硫除尘一体化技术40%—70%
二、燃烧前及燃烧中脱硫技术介绍
1、煤炭洗选技术
选煤是除去或减少原煤中所含的硫分、灰分等杂质,并按不同用户对煤质的不同要求,实行对路供应。
选煤技术分物理法、化学法和微生物法三种。
目前在我国广泛采用的是物理选煤方法,其中跳汰占59%、重介质选煤占23%、浮选占14%。
物理选煤可除去原煤中60%的灰分和1/3—1/2的黄铁矿硫。
各种燃煤设备使用品种质量和粒度符合工艺要求的选煤,可提高热效率和可靠性。
1995年,我国共有煤炭洗选能力3.8亿吨,煤炭入洗量为2.8亿吨,占全国煤炭生产量的22%,共除去硫分101万吨,相当少排放了202万吨的二氧化硫。
但中国选煤生产和技术都比较落后,发展缓慢,近几年煤炭入洗率一直在20%左右。
2、煤气化技术
煤气化是把经过适当处理的煤送入反应器,在一定的温度和压力下,通过气化剂(空气或氧和蒸汽)以一定的流动方式(移动床、流化床或携带床)转化成气体。
中国的煤气化用途主要分为工业和民用二大类,其中工业用途主要是生产化工合成原料气、燃料气。
中国已成功地掌握了年产8万吨合成氨的德士古炉设计、制造及运行技术;燃料气主要用于冶金、建材工业,采用的气化技术有固定床和二段空气气化炉。
城市居民用气主要依赖于炼焦副产煤气和煤的气化来实现,我国引进鲁奇气化炉技术成功地完成了产气量160万m3/hr的依兰煤气工程和产气量54万m3/hr的兰州煤气工程。
3、水煤浆技术
水煤浆是70年代发展起来的一种以煤代油的新型燃料。
它是把灰分很低而挥发分高的煤,研磨成微细煤粉,按煤水合理的比例,加入分散剂和稳定剂配制而成,可以象燃料油一样运输贮存和燃烧。
生产水煤浆的原料煤,灰分一般小于8%,硫分小于5%,并且燃烧效率高,烟尘和SO2排放远低于烧原煤;另外,水煤浆燃烧时火焰中心温度比烧煤和烧油低,故氮氧化物的生成量低。
目前我国共有六个制浆厂,制浆能力已超过了年产60万吨。
至今已成功地完成了20t/hr、35t/hr工业锅炉、轧钢加热窑炉的应用工作,230t/hr电站锅炉应用水煤浆工程也已进行调试和试生产。
4、型煤加工技术
型煤加工是用粉煤或低品位煤制成具有一定强度和形状的煤制品,可分为民用型煤和工业型煤两类。
前者有煤球和蜂窝煤,后者包括用于工业锅炉、窑炉和蒸汽车的型煤。
型煤加工一般需加粘结剂和固硫剂,以提高成型率和在燃烧中固硫。
型煤的固硫率一般在50%左右,并可节煤和减少烟尘排放。
我国近十几年来对工业型煤固硫技术开展了大规模的研究工作,相继在重庆、洛阳、贵阳、北京、太原等地建设了工业型煤厂;集中成型基础上开发的集中配煤、炉前成型技术已在兰州、北京、天津等地部分推广。
目前工业型煤的生产总能力达550万吨,较多的是用于中小锅炉上。
5、流化床燃烧技术
流化床燃烧是把煤和吸附剂(石灰石)加入燃烧室的床层中,从炉底鼓风使床层悬浮,进行流化燃烧。
循环流化床锅炉由于湍流混合充分,燃烧效率可达85%—90%,而层燃炉只有70%;在加入石灰石的钙硫比达2.0时脱硫率可达70%。
较低的燃烧温度使NOx生成量大大减少,其排放比层燃炉少70%以上。
近年来,电厂循环流化床锅炉有很大发展,目前国外已有240台在运行,总容量约10GW,最大单机容量达250MW。
我国自六十年代初开始研究和开发循环流化床燃烧锅炉,已经历了四个阶段:
第一阶段,研究开发中小型流化床工业锅炉,目前全国在用量达3000多台;第二阶段,研究开发电站用循环流化床锅炉,目前我国已有大约68MW机组在正常运行;第三阶段,研制煤气与蒸汽联产的锅炉,1994年我国投入运行了一台35t/hr的示范锅炉;第四阶段,研制以流化床气化和燃烧为基础的燃气—蒸汽联合循环发电技术,目前已在徐州贾旺电厂进行示范。
我国CFB锅炉在使用时绝大多数还未加脱硫剂。
三、烟气脱硫技术(FGD)
表1-2脱硫技术应用情况
类别脱硫率(%)主要特点缺点适用范围
湿法钠吸收法废弃法≥95是所有烟气脱硫方法最经济者未能回收硫资源,且造成二次污染日、美等国用于火力发电厂
直接利用法≥95吸收SO2后的吸收液NaSO3得以利用多用于造纸、纺织、食品工业等
回收亚硫酸钠、硫酸钠法90~95流程简单,操作方便,副产品得以利用投资高于废弃法多用于燃油锅炉、硫酸厂尾气
韦尔曼-洛德法90~95流程简单,投资费用较低,回收SO2纯度高目前产品亚硫酸钠需求量有限硫酸尾气及有色冶炼烟气脱硫
双碱法90~95可得纯度高的石膏、设备不易堵塞、结垢碱耗量大,脱硫费用高多用于大中型燃煤锅炉
碱性硫酸钠-石膏法98~99流程简单,操作方便,原料价廉可得优质石膏吸收液再生困难该工艺在日本应用较多
氨吸收法氨-酸法90~95流程简单、技术最成熟、投资省耗氨、耗酸量大我国最早应用于冶炼烟气脱硫
二段氨-酸法95~98流程简单、技术成熟、硫回收率高我国多用于中小型硫酸厂、冶炼厂
亚胺法90~98不耗酸、气、压缩空气、流程简单,投资省产生白色烟雾,溶液对设备有腐蚀作用用于硫酸厂、有色冶炼厂烟气脱硫
氨-石膏法90~95可得结晶良好的石膏产品耗氨量大、产生白色烟雾多用于钢厂,可用于一般锅炉烟气脱硫
石灰石或石灰乳吸收法生成物废弃法70~90流程简单、投资省、见效快未能回收硫资源,易造成二次污染国内外应用于一般锅炉烟气脱硫
石灰、石灰石-石膏法70~90原料便宜来源方便,可得石膏产品石膏结晶堵塞设备,操作费用高日本等多用于火力发电厂
稀硫酸催化氧化法90~98流程简单、无堵塞磨损问题、运转费用低可得副产品石膏和稀硫酸多用于有稀硫酸或石膏用户者或无适当吸收剂的工厂
氧化镁法≥90吸收剂便宜、吸收效率比石灰、石灰石-石膏法高,堵塞结垢问题小,可回收资源多用于大中型火力发电厂及集中供热锅炉烟气脱硫
干法活性氧化锰吸收法≥90吸收剂不易失去活性、再生温度低,无需加温可得副产品硫铵
活性炭吸附法≥90操作简单,运行可靠、可得副产品稀硫酸设备装置庞大,占地面积大投资费用高、动力消耗大适用于对单转化制酸流程的硫酸厂尾气脱硫
1、石灰石(石灰)/石膏法
在现有的电厂烟气脱硫工艺中,湿式石灰石(石灰)洗涤工艺技术最为成熟,运行也最可靠,吸收剂利用率高,一般Ca/S等于1.2时,脱硫效率可达90%以上,该工艺采用廉价的石灰石或石灰作吸收剂,脱硫产物为亚硫酸钙或硫酸钙,如采用强制氧化,产物基本为硫酸钙石膏。
1.1化学原理
石灰石吸收湿法洗涤工艺是按下列化学过程进行的。
在水中,气相SO2被吸收并经下列反应离解。
由于H+被OH-中和生成H2O使得这一平衡向右进行。
OH-离子是由水中溶解的石灰石产生的,且鼓入的空气可将生成的CO2带走。
鼓入的空气也可用来氧化在上述有关反应中得到的和离子,最后生成石膏沉淀物。
1.2石灰石(石灰)法烟气脱硫系统的构成
石灰石(石灰)法烟气脱硫装置原则上可以划分为下列结构单元:
·由石灰石粉料仓、石灰石磨机及测量站构成的石灰石制备系统。
·由洗涤循环、除雾器和氧化工序组成的吸收塔。
·由回转式烟气/烟气换热器或蒸汽/烟气预热器、清洁烟气冷却塔排放或湿烟囱排烟构成的烟气再热系统。
·由水力旋流分离和过滤皮带组成的石膏脱水装置。
·石膏贮存装置。
·废水处理系统。
典型的工艺流程见图1-1。
由石灰石粉与再循环洗涤水混合而成的重量浓度20%左右的石灰石浆用泵打入洗涤塔底槽,与槽中浆液混合后再泵至不同高度处由喷嘴喷射到洗涤塔中。
洗涤液与烟气中结合生成亚硫酸钙和石膏,为了实现将反应产物完全转化成石膏,需将氧化用的空气通到洗涤塔的石灰石浆槽中。
通过水力旋流分离器将粗石膏晶体从洗涤液中分离出来,然后用真空皮带过滤机将石膏脱水到水份含量低于10%。
图1-1常规型FGD系统
1.3石灰石/石膏法的应用情况
湿式石灰石洗涤工艺应用范围较广,无论燃用低、中硫煤还是高硫煤,均可使用;在美国火电厂FGD系统中,脱硫产物抛弃的湿式石灰石洗涤工艺占48.0%,而对脱硫产物加以利用的石灰石/石膏法只占1.3%,我国在重庆珞璜电厂引进了两套该种烟气脱硫设备,分别匹配两台容量同为36万KW的凝汽式汽轮发电机组,其中1号机组于1992年11月开始商业运转,2号机组于1993年5月开始运转,均为100%烟气处理。
该系统脱硫效率95%;系统有效利用率达锅炉运行时间的99%以上;石膏纯度高于90%;工艺年副产石膏约40万吨。
2.海水烟气脱硫
天然海水含有大量的可溶性盐,其中主要成分是氯化钠和硫酸盐,及一定量的可溶性碳酸盐。
海水通常呈碱性,自然碱度约为1.2~2.5mmol/l,这使得海水具有天然的酸碱缓冲能力及吸收SO2的能力。
海水脱硫系统主要有烟气系统、供排海水系统、海水恢复系统等组成。
锅炉排出的烟气经除尘器除尘后,有FGD系统增压风机送入气-气换热器的热侧降温,然后送入吸收塔,在吸收塔中用来自电厂循环冷却系统的冷却水洗涤烟气,洗涤过的海水经曝气处理后排入大海。
国外一些脱硫公司利用海水的这种特性,成功地开发出海水脱硫工艺。
海水脱硫系统主要由烟气系统、再热系统、供排海水系统、海水恢复系统等组成。
1988年以前,海水脱硫工艺多应用于冶金行业的炼铝厂及炼油厂等。
近年来在火电厂的应用有较快的发展。
挪威ABB公司的海水脱硫工艺已在挪威和国外建成20多套装置,挪威的烟气脱硫全部采用这种工艺。
深圳西部电力有限公司2号300MW机组引进海水脱硫技术,预计1998年7月工程建成投产。
该系统在设计工况条件下的脱硫率³90%,在校核工况下,脱硫率³70%,曝气池出口处排放海水的pH³6.5,FGD系统出口烟气温度³70℃。
福建漳州后石电厂一期2台600MW机组利用海水脱硫的可行性研究也在进行之中。
3.干法喷钙类脱硫
喷吸着剂工艺属干法工艺。
按所用吸收剂不同可分为钙基和钠基工艺,吸着剂可以干态,湿润态或浆液喷入。
喷入部位可以为炉膛、省煤器和烟道。
当钙硫比为2.0时,干法工艺的脱硫效率可达50-70%,钙利用率达50%。
这种方法较适合老电厂改造,因为在电厂排烟流程中不需增加什么设备,就能达到脱硫目的。
喷吸收剂工艺目前占总装机容量的3.2%,其中89%用于燃煤含硫量<2%的机组。
3.1化学原理
喷钙脱硫技术由两步固硫反应组成,首先作为固硫剂的石灰石粉料喷入炉膛热烟气中,热解后生成的CaO随烟气流动,与其中反应脱除一部分;然后,烟气进入锅炉尾部的活化反应器(或烟道),通过有组织的喷水增湿,一部分尚未反应的CaO转变成具有较高吸硫活性的,继续与烟气中的反应,从而完成脱硫的全过程。
整个工艺流程的化学过程如下:
在第一阶段