基与西门子802C的数控车床系统设计说明书.docx
《基与西门子802C的数控车床系统设计说明书.docx》由会员分享,可在线阅读,更多相关《基与西门子802C的数控车床系统设计说明书.docx(49页珍藏版)》请在冰豆网上搜索。
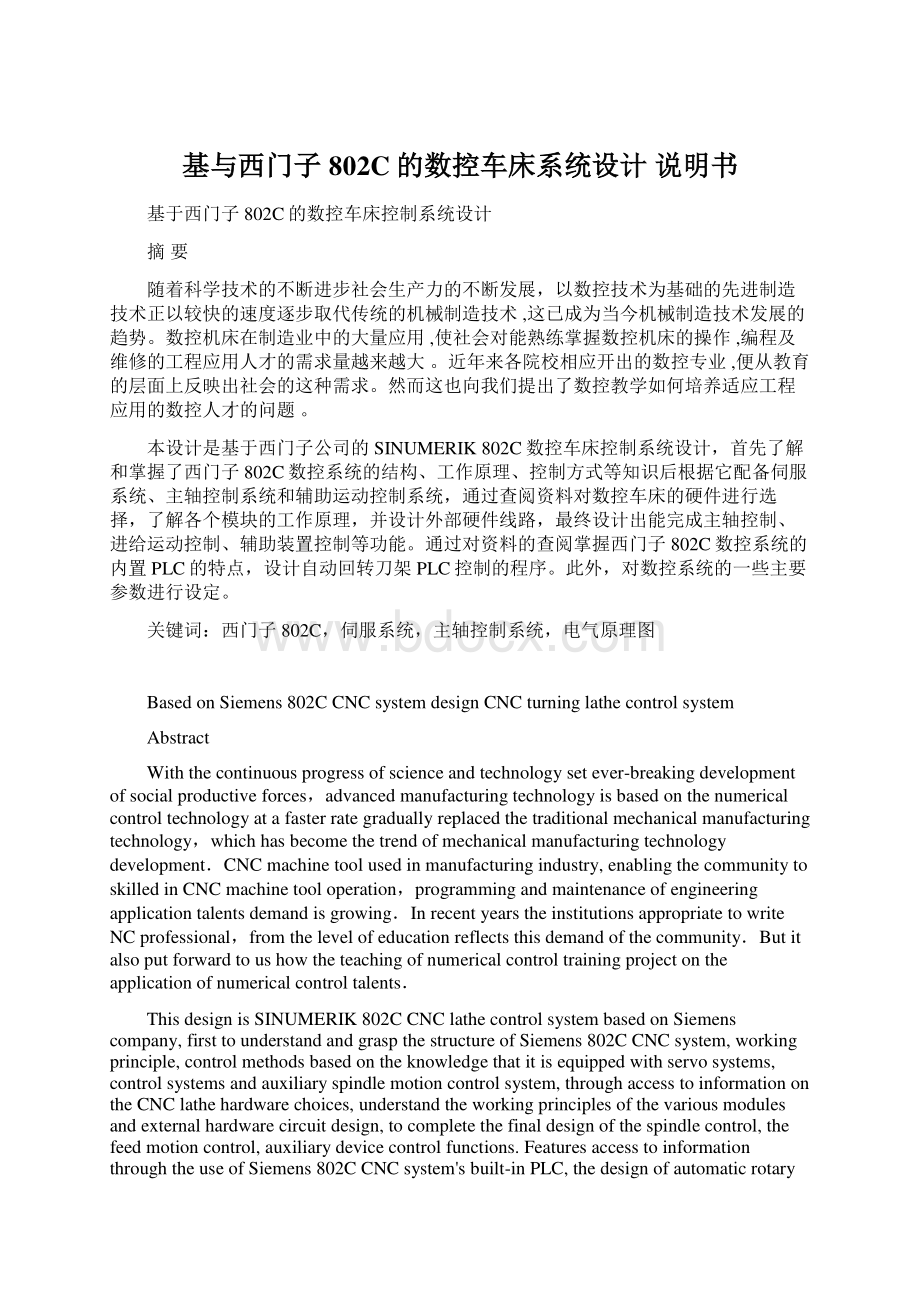
基与西门子基与西门子802C的数控车床系统设计的数控车床系统设计说明书说明书基于西门子802C的数控车床控制系统设计摘要随着科学技术的不断进步社会生产力的不断发展,以数控技术为基础的先进制造技术正以较快的速度逐步取代传统的机械制造技术,这已成为当今机械制造技术发展的趋势。
数控机床在制造业中的大量应用,使社会对能熟练掌握数控机床的操作,编程及维修的工程应用人才的需求量越来越大。
近年来各院校相应开出的数控专业,便从教育的层面上反映出社会的这种需求。
然而这也向我们提出了数控教学如何培养适应工程应用的数控人才的问题。
本设计是基于西门子公司的SINUMERIK802C数控车床控制系统设计,首先了解和掌握了西门子802C数控系统的结构、工作原理、控制方式等知识后根据它配备伺服系统、主轴控制系统和辅助运动控制系统,通过查阅资料对数控车床的硬件进行选择,了解各个模块的工作原理,并设计外部硬件线路,最终设计出能完成主轴控制、进给运动控制、辅助装置控制等功能。
通过对资料的查阅掌握西门子802C数控系统的内置PLC的特点,设计自动回转刀架PLC控制的程序。
此外,对数控系统的一些主要参数进行设定。
关键词:
西门子802C,伺服系统,主轴控制系统,电气原理图BasedonSiemens802CCNCsystemdesignCNCturninglathecontrolsystemAbstractWiththecontinuousprogressofscienceandtechnologysetever-breakingdevelopmentofsocialproductiveforces,advancedmanufacturingtechnologyisbasedonthenumericalcontroltechnologyatafasterrategraduallyreplacedthetraditionalmechanicalmanufacturingtechnology,whichhasbecomethetrendofmechanicalmanufacturingtechnologydevelopmentCNCmachinetoolusedinmanufacturingindustry,enablingthecommunitytoskilledinCNCmachinetooloperation,programmingandmaintenanceofengineeringapplicationtalentsdemandisgrowingInrecentyearstheinstitutionsappropriatetowriteNCprofessional,fromthelevelofeducationreflectsthisdemandofthecommunityButitalsoputforwardtoushowtheteachingofnumericalcontroltrainingprojectontheapplicationofnumericalcontroltalentsThisdesignisSINUMERIK802CCNClathecontrolsystembasedonSiemenscompany,firsttounderstandandgraspthestructureofSiemens802CCNCsystem,workingprinciple,controlmethodsbasedontheknowledgethatitisequippedwithservosystems,controlsystemsandauxiliaryspindlemotioncontrolsystem,throughaccesstoinformationontheCNClathehardwarechoices,understandtheworkingprinciplesofthevariousmodulesandexternalhardwarecircuitdesign,tocompletethefinaldesignofthespindlecontrol,thefeedmotioncontrol,auxiliarydevicecontrolfunctions.FeaturesaccesstoinformationthroughtheuseofSiemens802CCNCsystemsbuilt-inPLC,thedesignofautomaticrotaryturretPLCcontrolprocedures.Inaddition,someofthemainparametersofCNCsystemsetting.Keywords:
Siemens802C,Servosystem,Spindlecontrolsystem,Electricalcircuitdrawing摘要ABSTRACT1概述概述1.1数控机床的发展趋势数控机床的发展趋势1.1.1数控机床的产生于发展数控机床的产生于发展科学技术的不断发展,人们对机械产品的质量和生产率也提出了越来越高的要求。
机械加工工艺过程的自动化是实现上述要求的最主要的方法之一。
它不但能提高产品的质量、提高生产效率、降低生产成本、还可以很大程度上改善工人的劳动条件。
大批量的自动化生产广泛采用自动机床、组合机床和专用机床以及专用自动生产线,实行多刀、多工位多面同时加工,以达到高效率和高自动化。
但这些都属于刚性自动化,在面对小批量生产时这种方法并不是适用,因为小批量生产需要经常变化产品的种类,这就要求生产线具有柔性。
而从某种程度上说,数控机床的出现正是很地满足了这一要求。
1952年,美国麻省理工学院成功地研制出一套三坐标联动,利用脉冲乘法器原理的试验性数控系统,并把它装在一台立式铣床上。
当时用的电子元件是电子管,这就是第一代世界上的第一台数控机床。
我国是从1958年开始研究数控技术,一直到60年代中期处于研制、开发时期。
当时,一些高等院校、科研单位研制出试验样机,开发也是从电子管开始的。
1965年国内开始研制晶体管数控系统。
从70年代开始,数控技术在车、铣、钻、镗、磨、齿轮加工、点加工等领域全面展开,数控加工中心在上海、北京研制成功。
在这一时期,数控线切割机床由于结构简单,使用方便、价格低廉,在模具加工中得到了推广。
80年代,我国从日本发那科公司引进了5、7、3等系列的数控系统和交流伺服电机、交流主轴电机技术,以及从美国、德国引进一些新技术。
这使我国的数控机床在性能和质量上产生了一个质的飞跃。
1985年,我国数控机床品种有了新的发展。
90年代以及接下来主要是向高档数控机床发展。
目前,在数控技术领域中,我国和先进的工业国家之间还存在着很大的差距,但是这种差距正在飞速的缩小。
随着工厂、企业、技术改造的深入开展,各行各业对数控机床的需要将会有很大幅度的增长,这将有力地促进数控机床的发展。
1.1.2数控机床的发展趋势数控机床的发展趋势
(1)高精度化现代科学技术的发展、新材料及其新零件的出现,对精密加工技术不断的提出新的要求,提出高的加工精度,发展新型超精密加工机床,完善精密加工技术,适应现代科技的发展,已经成为数控机床的发展方向之一。
其精度已从微米级到亚微米级,甚至纳米级。
提高数控机床的加工精度,一般上可以通过减少数控系统的误差和采用机床误差补偿技术来实现。
在减少数控系统的误差方面,通常可以采用提高数控系统的分辨率、提高位置检测精度、在位置伺服系统中采用前馈控制与非线性控制等方法。
在机床误差补偿技术方面,除了采用齿隙补偿、丝杠螺距误差补偿和刀具补偿等技术外,还可以对设备热变形进行误差补偿。
(2)高速化提高生产率是数控机床追求的基本目标之一。
数控机床高速化可充分发挥现代刀具材料的性能,不但可以大幅度提升加工效率,降低加工成本,而且还可以提高零件的表面加工质量和精度,对制造业实现高效、优质、低成本生产具有广泛的适用性。
要实现数控设备的高速化,首先要求数控系统能对微小程序段构成的加工程序进行高速处理,以计算出伺服电动机的移动量,同时要求伺服电动机能高速度的作出反应,采用32为及64为的微处理器,是提高数控系统高速处理能力的有效手段。
实现数控设备高速化的关键是提高切削速度、进给速度和减少辅助时间(3)高柔性化采用柔性自动化设备或系统,是提高加工精度和效率缩短生产周期,适应市场变化需求和提高竞争能里的有效手段。
数控机床在提高单机柔性化的同时,朝着单元柔性化和系统柔性化方向发展。
(4)高自动化高自动化是指在全部加工过程中尽量减少人的介入二自动完成规定的任务,它包括物料流和信息流的自动化。
自20世纪80年代中期以来,以数控车床为主体的加工自动化已从“点”、“线”、“面”和“体”的方向发展。
尽管这种高自动化的技术还不够完备,投资过大,回收期较长,从而提出“有人介入”的自动化观点,但数控机床的高自动化并向着FMC、FMS集成方向发展的总趋势仍然是机械制造业发展的主流。
数控机床的自动化除进一步提高其自动编程、上下料、加工等自动化程度外,还在自动检索、监控、诊断等方面进一步发展。
(5)智能化随着人工智能在计算机领域的不断发展,为适应制造业生产柔性化、自动化发展需要,智能化正成为数控机床研究及其发展的热点,它不仅贯穿于生产加工的全过程,还贯穿于产品的售后服务和维修中,目前采取的主要技术措施包括以下几个方面:
a)自适应控制技术自适应控制可干根据切削条件的变化,自动的调节工作参数,使加工过程保持最佳宫坐状态,从而得到较高的加工精度和较小的表面粗超度,同时也能提高刀具的使用寿命和设备的生产效率,达到改进系统的运行状态的目的。
如通过监控切削过程中的刀具磨损、破损、切屑形状、切削力机零件的加工质量等,向制造系统反馈信息,通过将过程控制、过程监控、过程优化结合在一起,实现自适应调节。
b)专家系统技术将专家的经验和切削加工一般规律与特殊规律存入计算机中,以加工工艺参数数据库为支持,建立具有人工智能的专家系统,提供经过优化的切削参数,使加工系统达到最佳的工作状态,从而提高编程效率和降低对操作员的技术要求,缩短生产准备时间。
c)故障自诊断、自修复技术在整个工作状态中,系统随时对CNC系统本身以及与其相连的各种设备进行自诊断、检查。
一旦出现故障,立即采用停机等措施,进行故障报警,提示发生故障的部位、原因等,并利用相关的技术,自动进行相关的反应。
d)智能化交流伺服驱动技术目前已开始研究能自动识别负载并自动调整参数的智能化伺服系统,包括智能主轴交流驱动装置和智能化进给伺服装置,使驱动系统获得最佳的运行状态。
e)模式识别技术应用图像识别和声控技术,使机器自己识别图样,按照自然语音命令进行加工。
1.2数控机床的组成和工作原理数控机床的组成和工作原理1.2.1数控机床的促成数控机床的促成数控机床一般由控制介质、数控装置、伺服机构和机床本体组成,如图11所示,其中实线部分表示开环系统。
为了提高加工精度精度,再加入测量装置构成反馈,形成闭环系统。
图11数控机床的组成a)控制介质控制介质又称为信息载体。
数控机床加工时,所需的各种控制信息要靠某种中间载体携带和传输,这种载体称为“控制介质”。
控制介质是存储数控加工所需要的全部动作和刀具相对于工件信息的媒介物,它记载这零件的加工程序。
控制介质有多种,如穿孔带、穿孔卡、磁带以及磁盘等,业可以通过通信接口直接输入所需各种信息,采用何种控制介质则取决于数控装置的类型。
b)数控装置数控装置可以分为普通数控系统(NC)和计算机数控系统(CNC)两大类。
前者利用控制计算机,又称为硬件数控;后者利用通用的小型计算机或微型的计算机佳软件,又称为软件数控。
数控装置是数控机床的核心,一般由输入装置、控制器、运算器、和输出装置等组成。
它根据输入的程序和数据,经过数控装置的系统软件或逻辑电路进行编译、运算和逻辑处理后,输出各种信号和指令控制机床的各个部分,进行规定的、有序的动作。
这些控制信号最基本的信号时:
经插补运算决定的各坐标轴的进给速度、进给方向和位移量指令,送伺服驱动系统驱动执行部件坐进给运动;主运动部件的变速、换向、和启停信号;选择和交换刀具指令信号;控制冷却、润滑的启停,工作和机床部件松开、夹紧,分度工作台转位等辅助指令信号等。
c)伺服系统伺服系统由伺服驱动电路和伺服驱动装置组成,并与机床上的执行部件和机械部件组成数控机床的进给系统。
它根据数控装置发来的速度和位移指令控制执行部件的进给速度、方向和位移。
每个做进给运动的执行部件,都配有一套伺服系统。
伺服系统有开环、半闭环和闭环之分。
在半闭环和闭环伺服系统中,使用了位置检测装置,间接或直接测量执行部件的实际进给位移,与指令位移进行比较,按闭环原理,将其误差转换放大后控制执行部件的进给运动。
1.2.2数控机床的工作原理数控机床的工作原理用数控机床加工零件时,首先应将加工的零件的几何信息和工艺信息编制成加工程序,由输入部分送入数控装置,经过数控装置的处理、运算,按照各坐标轴的分量送到各轴的驱动电路,经过转换、放大进行伺服电动机的驱动,带动各轴运动,并进行反馈控制,是刀具与工件及其他辅助装置严格的按照加工程序规定的顺序、轨迹和参数顺利的进行,从而加工出零件的全部轮廓。
数控机床的加工,是吧刀具与工件的运动坐标分割成一些最小的单位量,即最小位移量,由数控系统按照零件程序的要求,是坐标移动若干各最小的位移量,从而实现刀具与工件的相对运动,完成对零件的加工。
当走刀轨迹为直线或圆弧时,数控装置则在线段的起点和终点坐标之间进行“数据点的密化”,求出一系列中间点的坐标值,然后按中间的坐标值,向各个坐标输出脉冲数,保证加工出需要的直线或圆弧轮廓。
数控装置进行的这种“数据点的密化”称为插补,一般数控装置都具有对基本函数进行插补的功能。
对任意曲面零件的加工,必须使刀具的运动的轨迹与该曲面完全吻合,才能加工出所需要的零件。
数控机床具有很好的柔性,当加工对象变换时,只需要重新编写加工程序即可,原来的程序可以储存备用,不必像组合机床那样需要针对新的加工零件重新设计机床,致使生产的准备时间过于太长。
1.3数控车床的特点数控车床的特点1.3.1数控机床的结构特点数控机床的结构特点a)传动链短。
沿纵、横两个坐标轴方向的运动是通过用伺服电动机直接与滚珠丝杠联结带动刀架运动,伺服电动机与丝杆间也可以用同步皮带或齿轮副联结。
b)刚度大、转速较高,可实现无级变速。
数控车床的总体结构刚性好、抗震性好,能够使主轴的转速更高,实现高速、强力切削。
它多采用直流或交流主轴控制单元来驱动主轴,按控制指令做无级变速。
c)轻拖动、润滑好、排屑方便,机床寿命较长。
刀架移动多采用安装在专用滚动轴承上的滚珠丝杠副;润滑大部分采用油雾自动润滑;一般都配有自动排屑装置。
d)加工冷却充分、防护较严密。
一般都使用安全防护门实现全封闭或半封闭的加工状态,因此,可以将原来的单向冲淋冷却方式改变成多方位强力喷淋,从而改善了刀具和工件的冷却效果。
e)自动换刀。
数控车床都配有自动换刀刀架实现自动换刀,以提高生产效率和自动化程度。
f)模块化设计。
数控车床的制造多采用模块化设计。
1.3.2数控机床的优点数控机床的优点a)加工对象改型的适应性强利用数控机床加工改型零件,只需要重新编制程序就能实现对零件的加工,它不同于传统的机床,不需要制造、更换许多工具、夹具和检具,更不要重新调整机床。
因此,数控机床可以快速地从加工一种零件到另一种零件,这就为单件、小批以及试制新产品提供了极大的方便。
它不仅缩短了生产准备周期,而且节省了大量工艺装备费用。
b)加工精度高数控机床是以数字形式给出的指令进行加工的,由于目前数控装置的脉冲当量一般达到了0.001mm,而且进给传动链的反向间隙与丝杠螺距误差等均可由数控装置进行补偿,因此,数控机床能达到比较高的加工精度和质量稳定性。
这是由数控机床结构设计采用的了必要的措施以及机电结合的特点决定的。
首先是在结构上采用了滚珠丝杠螺母机构、各种消除间隙的结构等,使机械传动误差尽可能的减少;其次采用了软件精度补偿技术,是机械误差进一步减少;第三是用程序控制加工,减少了人为因素对加工精度的影响。
这些措施不仅可以保证了较高的加工精度,同时还保持了较高的质量稳定性。
c)生产效率高零件加工所需要的时间包括机动时间与辅助时间两部分。
数控机床能够有效地减少这两部分时间,因而加工生产率比一般机床高。
数控机床主轴转速和进给来那个的范围比普通机床的范围大,每一道工序都能选用最有利的切削用量,良好的结构刚性允许数控机床进行大切削用量的强力切削,有效地节省了机动时间。
数控机床一定部件的快速移动和定位均采用了加速与减速措施,因而选用了很高的空行程运动度,消耗在进给、快退和定位的时间要比一般机床少。
数控机床在更换被加工零件时几乎不要重新调整机床,而零件有都安装在简单的定位夹紧装置中,可以节省用于停机进行零件安装调整的时间。
数控机床的加工精度比较稳定,一般只做首件检验或工序间关键尺寸的抽样检验,因而可以介绍停机检验的时间。
在使用带有刀库和自动换刀装置的数控加工中心机床时,在一台机床上实现了多道工序的连续加工,减少了半成品的周转时间,生产效率的提高就更为明显d)自动化程度高数控机床对零件的加工是按照事先编好的程序自动完成的,操作者除了操作面板、装卸零件、进行关键工序的中间测量以及观察机床的运行之外,其他的机床动作直至加工完毕,都是自动化完成的,不需要进行繁复的重复性手工操作,劳动强度与紧张程度均可大为减轻,劳动条件也得到相应的改善。
e)良好的经济效益使用数控机床加工零件时,分摊在每个零件上的设备费用是比较昂贵的。
但在单件、小批生产情况下,可以节省工艺装备费用、辅助生产时间、生产管理费用以及降低废品率等,因此能够获得良好的经济效益。
2西门子西门子802C数控系统的介绍数控系统的介绍2.1西门子西门子802C数控系统概述数控系统概述SINUMERIK802Cbaseline是在SINUMERIK802C基础上新开发的全功能说控系统,它可以控制2到3个伺服电机进给轴和一个伺服主轴或变频主轴,连接SIMODRIVE611U或SIMODRIVEbaseline.当系统匹配SIMODRIVE611U或SIMODRIVEbaseline时连接1FK7系统伺服电机。
它主要由:
CNC控制器、驱动器和电机、电缆这三大部分组成。
它具有结构紧凑,高度集成于一体的数控单元,操作面板,机床操作面板和输入输出单元机床调试配置数据少,系统与机床匹配更快速、更容易简单而友好的编程界面,保证了生产的快速进行,优化了机床的使用西门子802Cbaseline集成了所有的CNC、PLC、HMI、IO于一身可独立于其他部件进行安装等优点。
正如下图21所示,西门子802C数控系统在西门子公司数控系统产品中拥有高性能、低价位的特性,一直以来备受人们的青睐。
图21西门子公司数控系统产品结构2.2西门子西门子802C数控系统的操作面板数控系统的操作面板2.2.1面板的划分面板的划分西门子802C数控系统的操作面板可以划分为三大区:
LCD显示区、NC键盘区和机床控制区域,如图2-2所示。
图2-2面板划分面板定义LCD显示区:
8液晶黑白显示,640x320象素点,VGA显示,CCFL背光。
NC键盘区:
34个数字字符键,5个软键,7个功能键和4个特殊键。
MCP机床控制区域:
27个功能键,12个用户定义键键,16个LED显示。
2.2.2NC键盘区键盘区图2-3NC键盘各功能键说明:
1)加工显示键:
按此键后,屏幕立即回到加工显示的画面,在此可以看到当前各轴的工作状态。
2)返回键:
返回到上一级菜单。
3)软键:
在不同的屏幕状态下,操作对应的软键,可以执行相应的操作。
4)删除/退格键:
在程序编辑画面时,按此键删除(退格)清除前一字符。
5)报警应答键:
报警出现时,按此键可以消除报警(取决于报警级别)。
6)光标向上键/向上翻页(上档)键。
7)菜单扩展键:
进入同一级的其他菜单画面。
8)区域转换键:
按此键后立即回到主界面。
9)垂直菜单键:
在某些特殊画面,按此键可垂直显示选项。
10)光标向右键。
11)光标向下键/向下翻页(上档)键。
12)回车/输入键:
按此键确认所输入的参数或换行。
13)选择/切换键:
在设定参数时,按此键可以选择或转换参数。
14)空格键:
在编辑程序时,按此键插入空格。
15)光标向左键。
16)字符键:
用于字符输入,上档键可转换对应字符。
17)上档键:
按数字键或字符键时,同时按此键可使数字/字符的左上角字符生效。
18)数字键:
用于数字输入。
2.2.3MCP机床控制面板区域各按键功能说明:
基本功能区:
1)POK(绿灯):
电源上电,灯亮表示电源正常供电。
2)ERR(红灯):
系统故障,此灯亮表示CNC出现故障。
3)DIA(黄灯):
诊断。
该灯显示不同的诊断状态,正常状态时闪烁频率为1:
14)急停开关5)K1K12用户自定义键(带LED):
用户可以编写PLC程序进行键的定义。
运行方式键:
6)增量选择键:
在JOG方式(手动运行方式)下,按此键可以进行增量方式的选择,范围为:
1,10,100,1000。
7)点动方式键:
按此键切换到手动方式。
8)回参考点键:
在此方式下运行回参考点。
9)自动方式键:
按此键切换到自动加工方式,按照加工程序自动运行。
10)单段运行键:
按此键设定单段方式,程序按单段运行。
11)手动数据键:
在此方式下手动编写程序,然后自动执行。
主轴键:
12)主轴正转键:
按此键,主轴正方向旋转。
13)主轴停止键:
按此键,主轴停止转动。
14)主轴反转键:
按此键,主轴反方向旋转。
倍率键:
15)进给轴倍率增加键(带LED):
按动此键,进给轴倍率增大。
当进给轴倍率大于100%时LED亮,达到120%时(最大)LED闪烁。
16)主轴倍率增加键(带LED):
按动此键,主轴倍率增大。
当主轴倍率大于100%时LED亮,达到120%时(最大)LED闪烁。
17)进给轴倍率100%键:
按此键大于系统所设定的时间值(缺省值为1.5秒)时,进给轴倍率直接变为100%。
18)主轴倍率100%键:
按此键大于系统所设定的时间值(缺省值为1.5秒)时,主轴倍率直接变为100%。
19)进给轴倍率减少键(带LED):
按动此键,进给轴倍率减少。
按此键大于系统所设定的时间值(缺省值为1.5秒)时,进给轴倍率直接变为0%。
进给轴倍率在0%-100%时LED灯亮,降为0%时(最小)LED闪烁。
20)主轴倍率减少键(带LED):
按动此键,主轴倍率减少。
按此键大于系统所设定的时间值(缺省值为1.5秒)时,进给轴倍率直接变为50%。
进给轴倍率在50%-100%时LED灯亮,降为50%时(最小)LED闪烁。
点动键:
21)X轴正向点动键:
在手动方式下按动此键,X轴向正方向点动。
22)Z轴正向点动键:
在手动方式下按动此键,Z轴向正方向点动。
23)快速运行叠加键:
在手动方式下,同时按此键和一个坐标轴点动键,坐标轴按快速进给速度点动。
24)Z轴负向点动键:
在手动方式下按动此键,Z轴向负方向点动。
25)X轴负向点动键:
在手动方式下按动此键,X轴向负方向点动。
启动/停止键:
26)复位键: