10万吨年丁醇项目创新点概述.docx
《10万吨年丁醇项目创新点概述.docx》由会员分享,可在线阅读,更多相关《10万吨年丁醇项目创新点概述.docx(3页珍藏版)》请在冰豆网上搜索。
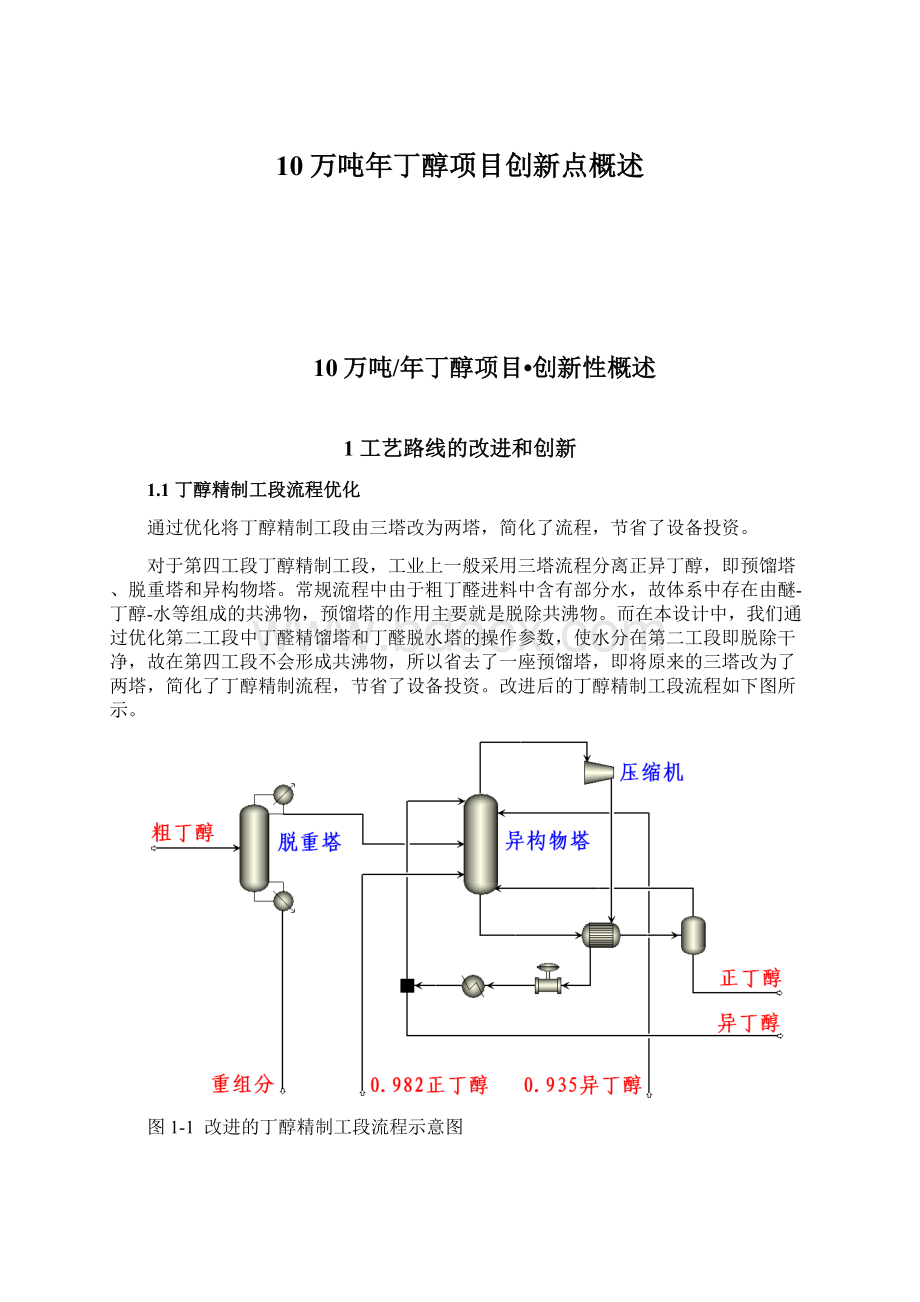
10万吨年丁醇项目创新点概述
10万吨/年丁醇项目•创新性概述
1工艺路线的改进和创新
1.1丁醇精制工段流程优化
通过优化将丁醇精制工段由三塔改为两塔,简化了流程,节省了设备投资。
对于第四工段丁醇精制工段,工业上一般采用三塔流程分离正异丁醇,即预馏塔、脱重塔和异构物塔。
常规流程中由于粗丁醛进料中含有部分水,故体系中存在由醚-丁醇-水等组成的共沸物,预馏塔的作用主要就是脱除共沸物。
而在本设计中,我们通过优化第二工段中丁醛精馏塔和丁醛脱水塔的操作参数,使水分在第二工段即脱除干净,故在第四工段不会形成共沸物,所以省去了一座预馏塔,即将原来的三塔改为了两塔,简化了丁醇精制流程,节省了设备投资。
改进后的丁醇精制工段流程如下图所示。
图1-1改进的丁醇精制工段流程示意图
1.2增设残液回收处理工段
增设了残液回收处理工段,有效回收了正异丁醇,增加了产品产量;同时预提纯了加氢尾气;另外采用了先进的隔壁精馏技术,节省设备投资和能耗。
一般的丁醇生产工艺并没有对尾气残液中的有用组分的回收处理工序,最简单的做法是将分离产生的重组分用做燃料油,尾气送火炬燃烧或送燃气总管作为燃料气,这样的做法既没有回收尾气残液中的有用组分,浪费了原料和产品,又会增加处理成本,尤其对成本较贵的组分,更加缺乏经济性。
因此本设计提出了一种新的尾气残液回收处理流程,如下图所示。
图1-2废气液回收处理流程图
用来自第三工段和第四工段的重组分残液吸收第三工段加氢尾气中的正异丁醇,塔顶气体送氢气膜分离单元提纯,吸收液送入隔壁精馏塔分离得到正异丁醇和辛烯醛,再将正异丁醇送第四工段异构物塔(T0402)侧线进料。
增加尾气残液回收处理工段能达到三个目的:
①回收了废气液中的有用组分,增加了产品产量;
②提高了第三工段加氢尾气中氢气的纯度,有利于后续的氢气膜分离操作,使膜分离得到高纯度加氢氢气变得更加容易;
③使用了先进的隔壁精馏技术分离三组分,节省设备投资和能量消耗。
1.3氢气膜分离单元回收氢气
采用先进的膜分离技术回收了70%加氢尾气中的氢气,纯度能达到99.9%,大大减少了新鲜氢气的补充量,每年可节省生产成本约3598万元。
一般工艺对加氢尾气的简单处理是送燃气总管做燃料气,然而氢气对于化工企业来说是一种重要的资源,所以对氢气的回收利用有很大的应用价值。
本设计采用先进的氢气膜分离单元回收大部分加氢尾气中的氢气,因为加氢尾气本身有一定的压力,且经过第五工段吸收丁醇后浓度得到提高,达到了86.1%(wt.),所以利用膜分离的方法回收氢气能收到很好的经济性。
由于Aspenplus没有膜分离单元模块,因此采用用户模型外接Fortran编程模拟氢气膜分离过程,模拟示意图如下。
经过第五工段吸收后的加氢尾气送入氢气膜分离装置,回收了70%纯度达99.9%的氢气循环回第三工段用于加氢反应,大大减少了新鲜氢气的补充量,且大大减少了能量消耗,每年可节省生产成本约3598万元人民币,具有十分显著的经济效益。
图1-3氢气膜分离单元示意图
2过程设备的创新
2.1热泵精馏节能技术
采用热泵精馏技术分离正异丁醇,可节省热耗22.3%,节省冷耗77.8%。
本工艺第四工段的异构物分离塔(T0402)是在常压下分离正异丁醇,此种情况下正异丁醇的沸点相近,相对挥发度很小,属难分离系统,普通精馏塔的计算结果显示分离正异丁醇需要60块理论塔板(包括塔顶冷凝器和塔底再沸器),能耗很大;另外,塔顶温度约110℃和塔底温度约127℃相差不大,故我们将普通精馏塔改造成采用塔顶蒸汽压缩式热泵精馏结构,示意图如下。