国家重点行业清洁生产技术导向.docx
《国家重点行业清洁生产技术导向.docx》由会员分享,可在线阅读,更多相关《国家重点行业清洁生产技术导向.docx(34页珍藏版)》请在冰豆网上搜索。
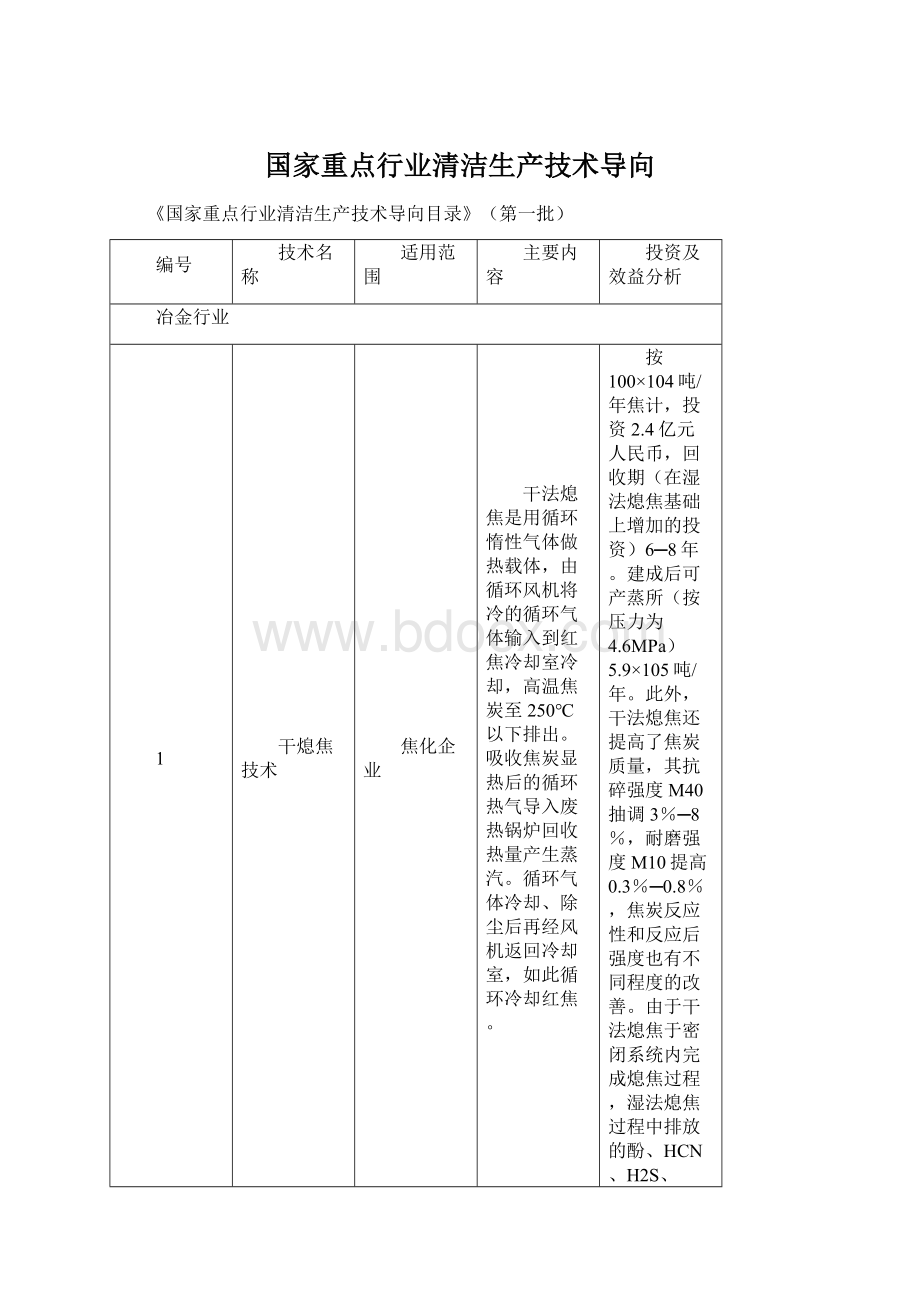
国家重点行业清洁生产技术导向
《国家重点行业清洁生产技术导向目录》(第一批)
编号
技术名称
适用范围
主要内容
投资及效益分析
冶金行业
1
干熄焦技术
焦化企业
干法熄焦是用循环惰性气体做热载体,由循环风机将冷的循环气体输入到红焦冷却室冷却,高温焦炭至250℃以下排出。
吸收焦炭显热后的循环热气导入废热锅炉回收热量产生蒸汽。
循环气体冷却、除尘后再经风机返回冷却室,如此循环冷却红焦。
按100×104吨/年焦计,投资2.4亿元人民币,回收期(在湿法熄焦基础上增加的投资)6─8年。
建成后可产蒸所(按压力为4.6MPa)5.9×105吨/年。
此外,干法熄焦还提高了焦炭质量,其抗碎强度M40抽调3%─8%,耐磨强度M10提高0.3%─0.8%,焦炭反应性和反应后强度也有不同程度的改善。
由于干法熄焦于密闭系统内完成熄焦过程,湿法熄焦过程中排放的酚、HCN、H2S、NH3基本消除,减少焦尘排放,节省熄焦用水。
2
高炉富氧喷煤工艺
炼铁高炉
高炉富氧喷煤工艺是通过在高炉冶炼过程中喷入大量的煤粉并结合适量的富氧,达到节能降焦、提高产量、降低生产成本和减少污染的目的。
目前,该工艺的正常喷煤量为200kg/t-Fe,最大能力可达250kg/t-Fe以上。
经济效益以日产量9500吨铁(年产量为346万吨铁)计算,喷煤比为120kg/t-Fe时,年经济效益为200kg/t-Fe时,年经济效益为6160万元。
3
小球团烧结技术
大、中、小型烧结厂的老厂改造和新厂新设
通过改变混合机工艺参数,延长混合料在混合机内的有效滚动距离,加雾化水,加布料刮刀等,使烧结混合料制成3mm以上的小球大于75%,通过蒸汽预热,燃料分加,偏析布料,提高料层厚度等方法,实现厚料层、低温、匀温、高氧化性的烧结矿,上下层烧结矿质量气氛烧结。
通过这种方法烧出的烧结矿,上下层烧结矿质量均匀。
烧结矿强度高、还原性好。
以1台90平方米烧结机的改造和配套计算,总投资约380万元,投资回收期0.5年,年直接经济效益895万元,年净效益798万元。
使用该技术还可减少燃料消耗、废气排放量及粉尘排入量;提高烧结质量和产量。
同时可较大幅度降低烧结工序能耗,提高炼铁产量和降低炼铁工序能耗,促进炼铁工艺技术进步。
4
烧结环冷机余热回收技术
大、中型烧结机
通过对现有的冶金企业烧结厂烧结冷却设备,如冷却机用台车罩子、落矿斗、冷却风机等进行技术改造,再配套除尘器、余热锅炉、循环风机等设备,可充分回收烧结矿冷却过程中释放的大理余热,将其转化为饱和蒸汽,供用户使用。
同时除尘器所捕集的烟尘,可返回烧结利用。
│公斤/小时。
按照烧结厂烧结机90M2×2估算投资,约需4000─5000万元人民币。
烧结环冷机余热得到回收利用,实际平均蒸汽产量16.5吨/小时;由于余热气闭路循环,当废气经过配套除尘器时,可将其中的烟尘(主要是烧结矿粉)捕集回收,即减少烟尘排放,又回收了原料,烧结矿粉回收量336
5
烧结机头烟尘净化电除尘技术
24─450m2各种规格烧结机机头烟尘净化
电除尘器是用高压直流电在阴阳两极间造成一个足以使气体电离的电场,气体电离产生大量的阴阳离子,使通过电场的粉尘获得相同的电荷,然后沉积于与其极性相反的电极上,以达到除尘的目的。
以将原4台75米3烧结机的多管除尘器改为4台104m2三电场电除尘器计算,总投资1100万元,回收期15年,年直接经济效益255万元,年创净效益71万元。
同时烧结机头烟尘达标排放,年减少烟尘排放6273吨。
6
焦炉煤气H.P.F法脱硫净化技术
煤气的脱硫、脱氰净化
焦炉煤气脱硫脱氰有多种工艺,近年来国内自行开发了以氨为碱源的H.P.F法脱硫新工艺。
H.P.F法是在H.P.F(醌钴铁类)复合型催化剂作用下,H2S、HCN先在氨介质存在下溶解、吸收,然后在催化剂作用下铵硫化合物等被湿式氧化形成元素硫、硫氰酸盐等,催化剂则在空气氧化过程中再生。
最终,H2S以元素硫形式,HCN以硫氰酸盐形式被除去。
按处理30000米3/小时煤气量计算,总投资约2200万元,其中工程费约1770万元。
主要设备寿命约20年。
同时每年从煤气中(按含H2S6g/Nm3计)除去H2S约1570吨,减少SO2排放量约2965吨/年,并从H2S有害气体中回收硫磺,每年约740吨。
此外,由于采用了洗氨前煤气脱硫,此工艺与不脱硫的硫铵终冷工艺相比,可减少污水排放量,按相同规模可节省污水处理费用约200万元/年。
7
石灰窑废气回收液态二氧化碳
石灰窑废气回收利用
以石灰窑窑顶排放出来的含有约35%左右二氧化碳的窑气为原料,经除尘和洗涤后,采用“BV”法,将窑气中的二氧化碳分离出来,得到高纯度的食品级的二氧化碳气体,并压缩成液体装瓶。
以5000吨/年液态二氧化碳规模计,总投资约1960万元,投资回收期为7.5年,净效益160万元/年。
同时每年可减少外排粉尘600吨,减少外排二氧化碳5000吨,环境效益显著。
8
尾矿再生产铁精矿
磁选厂尾矿资源的回收利用
利用磁选厂排出的废弃尾矿为原料,通过磁力粗选得到粗精矿,经磨矿单体充分解离,再经磁选及磁力过滤得到合格的铁精矿,供高炉冶炼。
按照处理尾矿量160万吨/年、生产铁精矿4万吨/年(铁品位65%以上)的规模计算,总投资约630万元,投资回收期1年,年净经济效益680万元,减少尾矿排放量4万吨/年,具有显著的经济效益和环境效益,也有助于生态保护。
9
高炉煤气布袋除尘技术
中小型高炉煤气的净化
高炉煤气布袋除尘是利用玻璃纤维具有较高的耐温性能(最高300℃),以及玻璃纤维滤袋具有筛滤、拦截等效应,能将粉尘阻留在袋壁上,同时稳定形成的一次压层(膜这种滤袋得到高效净化,以提)也有滤尘作用,从而使高炉煤气通过供高质量煤气给用户使用。
以300m3级高炉为例,总投资约600万元,其中投资回收期2年,直接经济效益300万元/年,净效益270万元/年。
减少煤气洗涤污水排放量300万米3/年,主要污染物排放量200吨/年,节约循环水300─400万米3/年,节电80─100万千瓦时/年,节约冶金焦炭1500吨/年,高炉增产3000吨/年。
10
LT法转炉煤气净化与回收技术
大型氧气转炉炼钢厂
转炉吹炼时,产生含有高浓度CO和烟尘的转炉煤气(烟气)。
为了回收利用高热值的转炉煤气,须对其进行净化。
首先将转炉煤气经过废气冷却系统,然后进入蒸发冷却器,喷水蒸发使烟气得到冷却,并由于烟气在蒸发器中得到减速,使其颗粒的粉尘沉降下来,此后将烟气导入设有四个电场的静电除尘器,在电场作用下,使得粉尘和雾状颗粒吸附在收尘极板上,这样得到精净化。
当符合煤气回收条件时,回收侧的阀自动开启,高温净煤气进入煤气冷却器喷淋降温于约73℃而后进入煤气储柜。
经加压机加压后将高洁度的转炉煤气(含尘10mg/Nm3)提供给用户使用。
以年产300万吨炼钢为例:
LT废气冷却系统,如按回收蒸汽平均90kg/t-s计算,相当于10kg/t-s(标准煤),年回收标准煤约3万吨。
LT煤气净化回收系统,回收煤气量75─90Nm3/t-s,相当于23kg/t-s(标准煤),年回收煤气折算标准煤7万吨。
每年回收总二次能源(折算标准煤)10万吨。
11
LT法转炉粉尘热压块技术
与LT法转炉煤气净化回收技术配套
粉尘在充氮气保护下,经输送和储存,将收集的粉尘按粗、细粉尘以0.67:
1的配比混合,加入间接加热的回转窑内进行│×25mm)用于炼钢。
氮气保护加热。
当粉尘被加热至580℃时,即可输入辊式压块机,在高温、高压下压制成45×35×25mm成品块。
约500℃的成品块经冷却输送链在机力抽风冷却下,成品块温度降至 ̄80℃,装入成品仓内。
定期用汽车运往炼钢厂作为矿石重新入炉冶炼。
LT系统年回收含铁高的粉尘16kg/t-s×3,000,000t/a=48,000t/a,可以全部压制成块(45×35×25mm)用于炼钢。
12
轧钢氧化铁皮生产还原铁粉技术
适用大中型轧钢厂(低碳、低合金钢轧制过程)产生的氧化铁皮,也可用于高品位铁精矿、铁砂等含铁资源的综合利用
采用隧道窑固体碳还原法生产还原铁粉。
主要工序有:
还原、破碎、筛分、磁选。
铁皮中的氧化铁在高温下逐步被碳还原,而碳则气化成CO。
通过二次精还原提高铁粉的总铁含量,降低O、C、S含量,消除海绵铁粉碎时所产生的加工硬化,从而改善铁粉的工艺性能。
按年产12000吨还源铁粉计算,总投资约10600万元,投资回收期5年。
净效益2190万元/年。
按此规模每年可综合利用20000吨轧钢氧化铁皮。
13
锅炉全部燃烧高炉煤气技术
一切具有富裕高炉煤气的冶金企业
冶金高炉煤气含有一定量的CO,煤气热值约3100kj/m3。
除用于钢铁厂炉窑的燃料外,余下煤气可供锅炉燃烧。
由于锅炉一般是缓冲用户,煤气参数不稳定,长期以来仅为小比例掺烧,多余煤气排入大气,这样既浪费了能源又污染了大气环境。
当采用稳定煤气压力且对锅炉本体进行改造等措施后,可实现高炉煤气的全部利用,并可以确保锅炉安全运行。
与新建燃煤锅炉房相比,全烧高炉煤气锅炉房由于没有上煤、除灰设施,具有占地小、投资省、运行费用低等优点。
以一台75t/h全烧高炉煤气锅炉为例,年燃用高炉煤气583×106米3/年,仅此一项,年节约能源5.2万吨标准煤,减少向大气排放CO134×106米3/年,具有明显的经济效益和环境效益。
石油化工行业
14
含硫污水汽提氨精制
炼油行业含硫污水汽提装置
从汽提塔的侧线抽出的富氨气,经逐级降温、降压、高温分水,低温固硫三级分凝后,反应获得粗氨气,粗氨气进入冷却结晶器,获得含有少量H2S的精氨气,再使其进入脱硫剂罐,硫固定在脱硫隙内,氨气得到进一步脱硫,剂的空脱硫后的氨气经氨压机压缩,进入另一个脱硫剂罐,经两段脱硫和压缩的氨气,冷却成为产品液氨外销或内用。
以100吨/小时加工能力的含硫污水汽提装置计算,总投资为1506万元。
每年回收近千吨液氨,回收的液氨纯度高,可外销,也可内部使用,从而节约大量资金。
污水汽提净化水中的H2S、氨氮的含量大幅度降低,减少了对污水处理场的冲击,使污水处理场总排放口合格率保持100%。
污水汽提装置运行以后,厂区的大气环境得到了明显改善,不再被恶臭气味困扰。
15
淤浆法聚乙烯母液直接进蒸馏塔
淤浆法聚乙烯生产工艺
原来母液经离心机分离后通过泵将母液送至蒸馏塔中,再从蒸馏塔打进汽提塔,将母液中的低聚物与己烷分离。
现改为母液直接进塔,这样则可以使母液的温度不会下降,从而达到了节能的效果;同时也可以防止低聚物析出沉淀在蒸馏塔内,减轻大检修时的清理工作。
更主要的是母液直接进塔可增加汽提塔的处理能力,负荷可提高5吨以上,从而确保生产的正常运行。
技术改造属中小型,总投资仅4万元,全年运行总节省资金达142万元。
减少清理费2万元,同时减少因清理储罐和管线造成的环境污染,生产装置的安全也得到了保证。
16
含硫污水汽提装置的除氨技术
非加氢型含硫污水汽提装置
解决了汽提后净化水中残存NH3-N的形态分析研究,建立了相应分析方法,根据分析获得的固定铵含量,采用注入等当量的强碱性物质进行汽提,并经过精确的理论计算,以确定最佳注入塔盘的位置。
经工业应用,可有效地将NH2-N脱除至15-30ppm。
80t/h汽提装置需增加一次性投资约60万元。
注碱后,成本增加及设备折旧每年需54万元。
注碱后通过增加回收液水和节约软化水等,经济效益约氨、节约新鲜每年97万元。
由于废水的回用,每年污水处理场少处理废水36×104吨,节约108万元,同时由于NH3-N达标,可节省污水处理场技术改造一次性投资上千万元。
17
汽提净化水回用
石油炼制
含硫污水净化后可以代替新鲜水使用,通过原油的抽提作用可以减少污染物排放总量,其中酚去除率85%以上,COD去除率约60%。
二次加工装置的部分工艺注水也可以用净化水代替,这些工艺注水变成含硫污水回用到污水汽提装置,形成闭路循环。
以每小时回用30吨含硫污水为例,净化水回用管网系统投资70万元,投资回收期8个月,经济效益198.4万元,减少废水排放量36万吨/年,减少COD排放量54吨/年。
18
成品油罐三次自动切水
油品储罐
利用连通器原理和油水之间的密度差,有效地分离成品油中的水和切水中的油,并自动将回收的成品油送回成品库。
以10t/h储罐为例,总投资37万元,半年时间可回收投资,经济、环境、社会效益显著。
19
火炬气回收利用技术
石油炼制
在火炬顶部安装两种高空点火装置,利用电焊发弧装置,产生面状电弧火源,两种装置交替或同时工作,保证安全可靠。
利用PCC和微机全线自动监控,对点火过程、水封罐、各种气体流量自动调节,并自动记录系统动作。
全国石化生产企业现有火炬130支,年排放可燃气体约100-150万吨,全部回收利用,经济效益可达10-15亿元/年,目前经治理可回收利用80%的资源,投资回收期0.5-0.8年。
20
含硫污水汽提装置扩能改造
石油化工等含硫含氨污水预
对含硫污水汽提塔中LPC-1(100X)高效陶瓷规整填料及18处理│-8不锈钢阶梯环进行了通量、传质和压降性能的测试,其特点为:
在老塔塔体不变的情况下,更换填料可使处理量提高70%以上;传质效果好,分离效率高,提高了净化水的质量;压降低,可降低装置能耗;操作弹性大,处理量变化时,只需要相应调整蒸汽用量即可保证净化水合格。
以处理能力由28万吨/年提高到48万吨/年计算,总投资665万元(包括机泵、仪表、填料、除油器等)。
改造后处理能力扩大到60吨/小时以上,能耗下降,每年节约184万元,投资偿还期约3.6年。
改造后净化水质量提高,H2S在50mg/L以下,NH3-N为50-150mg/L,净化水回注率25-30%,降低了下游污水处理的费用。
21
延迟焦化冷焦处理炼油厂“三泥”
燃料型炼油厂污水处理产生的“三泥”与生产石油焦的延迟焦化装置
利用延迟焦化装置正常生产切换焦炭塔后,焦炭塔内焦炭的热量将“三泥”中的水份轻油汽化,大于350℃的重质油焦化,并利用焦炭塔泡沫层的吸附作用,将“三泥”中的固体部分吸附,蒸发出来的水份、油气至放空塔,经分离、冷却后,污水排向含硫污水汽提装置进行净化处理,油品进行回收利用。
以10.25吨/塔计算,总投资30万元左右,净利润80万元/年,投资偿还期0.37年。
使用该技术每年可回收油品816吨,节省用于“三泥”处理的设备投资和运行费用,防止由此而引起的二次污染,经济效益、环境效益和社会效益显著。
22
合建池螺旋鼓风曝气技术
大、中、小炼油(燃料油、润滑油、化工型)厂
空气从底部进入,气泡旋转上升径向混合、反向旋转,使气泡多次被切割,直径变小,气液激烈掺混,接触面增大,以利于氧的转移。
在曝气器中因气水混合液的密度小,形成较大的上升流速,使曝气器周围的水向曝气器入口处流动,形在水流大循环,有利于曝气器的提升、混合、充氧等。
以800-1000吨/小时污水处理能力计算,总投资80-120万元,主以800-1000吨/小时污水处理能要设备寿命15-20年。
具有操作人员少、节电、维修费用少、处理效果好、排水合格率高等优点,总计每年可节省费用约40-80万元。
23
PTA(精对苯二甲酸装置)母
PTA装置液冷却技术
利用空气鼓风机与特殊结构的喷嘴使物料喷雾,并与空气进行逆向接触冷却物料,利用新型塔板的不同排列实现了固体物料的防堵和良好的冷却效果,并成功地设计了在线清堵流程,实现了不停车即可清除物料。
35万吨/年PTA装置的母液冷却装置,总投资约355万元,经济效益87万元/年。
污水温度可降到45℃,保护了污水处理中分解分离菌,有利于污水的处理。
化工行业
24
合成氨原料气净化精制技术──双甲新工艺
大、中、小型合成氨厂
此工艺是合成氨生产中一项新的净化技术,是在合成氨生产工艺中,利用原料气中CO、CO2与H2合成,生成甲醇或甲基混合物。
流程中将甲醇化和甲烷化串接起来,把甲醇化、甲烷化作为原料气的净化精制手段,既减少了有效氢消耗,又副产甲醇,达到变废为宝。
以年产5万吨氨、醇计,总投资300─500万元,投副产1万吨甲资回收期2─3年。
因没有铜洗,吨氨节约物耗(铜、冰醋酸、氨)14元,节约蒸汽30元,节约氨耗6.5元等,每万吨合成氨可节约74万元;副产甲醇,按氨醇经5:
1计算,1万吨氨副产2000吨甲醇,利润40─100万元,年产5万吨的合成氨装置可获得经济效益570─870万元。
25
合成氨气体净化新工艺──NHD技术
各种工艺气体的净化,特别是以煤为原料的硫化氢、二氧化碳含量高的氨合成气、甲醇合成气和羰基合成气的净化
NHD溶剂是国内新开发的一种高效优质的气体净化剂,其有效成份为多聚乙二醇二甲醚的
混合物,是一种有机溶剂,对天然气、合成气等气体中的酸性气(硫化氢、有机硫、二氧化碳等)具有较强的选择吸收能力。
该溶剂脱除酸性气采用物理吸收、物理再生工艺,能使净化气中的酸性气达到生产合成氨、甲醇、制氢等的工艺要求。
以年产40000吨合成氨计,改造总投资(由碳丙工艺改造,含基建投资、设备投资等)约80万元,投资回收期0.31年。
新建总投资(基建投资、设备投资等)约400万元,投资回收期0.89年。
应用此项技术的企业年经济效益均在200万元以上。
26
天然气换热式转化造气新工世及换热式转化炉
以天然气、炼厂气、甲烷富气等为原料,生产合成氨及甲醇的生产装置。
也适用于小氮肥装置的技术改造和技术革新
该工艺是将加压蒸汽转化的方箱式一段炉改为换热式转化炉,一段转化所需的反应热由二段转化出口高温气来提供,不再由烧原料气来提供。
由于二段高温转化气的可用热量是有限的,不能满足一段炉的需要,又受氢氮比所限,因此在二段炉必需加入富氧空气(或纯氧)。
按照装置设计能力为年产15000吨合成氨规模的组合成气计算,项目总投资1300万元,投资到利润率约9%,投资利税率约10%,投资收益率约20%。
本技术节能方面有较大的突破,这将大大增强小厂产品竞争能力。
27
水煤浆加压气化制合成气
以煤化工为原料的行业
德士古煤气化炉是高浓度水煤浆(煤浓度达70%)进料、液态排渣的加压纯氧气流床气化炉,可直接获得烃含量很低(含CH4低于0.1%)的原料气,适合于合成氨、合成甲醇等使用。
年产30万吨合成氨、52万吨尿素装置以及辅助装置约需30.5亿元投资回收期12年,主要设备使用寿命15─20年。
28
磷酸生产废水封闭循环技术
料浆法3万吨/年磷铵装置;二水法1.5万吨/年H3PO4(以P2O5计)装置
二水法磷酸生产中的含氟含磷污水,经多次串联利用后,进入盘式过滤机冲洗滤盘,产生冲盘磷石膏污水。
冲盘污水经过二级沉降,分离出大颗粒和细颗粒。
二级沉降的底流进入稠浆槽作为二洗液返回盘式过滤机,清液作为盘式过滤机冲洗水利用,实现冲盘污水的封闭循环。
1.5万吨/年H3PO4(以P2O5计)装置总投资为54万元,投资回收期1年。
回收污水中可溶性P2O5,污水回用后节水效益和节省排污费每年达63万元。
29
磷石膏制硫酸联产水泥
磷肥行业
磷石膏是磷铵生产过程中的废渣,用磷石膏、焦炭及辅助材料按照配比制成生料,在回转窑内发生分解反应。
生成的氧化钙与物料中的二氧化硅、三氧化二铝、三氧化二铁等发生矿化反应形成水泥熟料。
含7-8%二氧化硫的窑气经除尘、净化、干燥、转化、吸收等过程制得硫酸。
年产15万吨磷铵、20万吨硫酸、30万吨水泥的装置总投资95975万元,每年可实现销售收入84000万元,利税22216万元,投资回收期4.32年。
每年能吃掉60万废渣,13万吨含8%硫酸的废水,节约维存占地费300万元,节约水泥生产所用石灰石开采费10500万元和硫酸生产所需的硫铁矿开采费16000万元。
从根本上解决了石膏污染地表水和地下水的问题。
30
利用硫酸生产中产生的高、中温余热发电
适用于硫酸生产行业
利用硫铁矿沸腾炉炉气高温( ̄900℃)余热及SO2转化成SO3后放出的中温(-200℃)余热生产中压过热蒸汽,配套汽轮发电机发电。
蒸汽量达到0.9t/t酸,蒸汽消耗指标为5.94kg/kwh。
汽轮机采用凝结式汽机,冷凝水可回收利用。
新建300kw机组,总投资680万元。
年创利税190万元,投资回收期3.5年。
每年可节约6000吨标准煤;减排SO2192吨,CO8吨,NOx54吨,经济效益、环境效益显著。
31
气相催化法联产三氯乙烯、四氯乙烯
该技术应用于有机化工生产,适用于改造5000吨/年以上三氯乙烯装置
以1万吨/年(三氯乙烯5000吨,生成四氯乙烷或五氯乙烷,二者混合后(亦可用单一的四氯乙烷或五氯乙烷)经气化进入脱HCI反应器,生成三、四氯乙烯。
反应产物在解吸塔除去HCI后,导入分离系统,经多塔分离,分出精三氯乙烯和精四氯乙烯,未反应的物料返回脱HCI反应器,循环使用。
精三氯乙烯部分送氯化塔生成五氯乙烷,部分经后处理加入稳定剂作为产品。
精四氯乙烯经后处理加入稳定剂,即为成品。
四氯乙烯5000吨)计,总投资3000万元,投资回收期2─3年。
新工艺比皂化法工艺成本降低约10%,新增利税每年约800─1000万元。
同时彻底消除了皂化工艺造成的污染,改善了环境。
32
利用蒸氨废液生产氯化钙和
纯碱生产氯化钠
氨碱法生产纯碱后的蒸氨废液中含有大量的CaCl2和NaCI,其溶解度随温度而变化,经多次蒸发将CaCl2和NaCl分离,制成产品。
按照NaCl、CaCl2年产量分别为13000吨和28000吨计算,年经济效益为1551万元和3477万元,合计5028万元。
33
蒽醌法固定床钯触媒制过氧化氢
化肥、氯碱化工、石化等具有副产氢气的行业
该技术以2-乙基蒽醌为载体,与重芳烃等混合溶剂一起配制成工作液。
将工作液与氢气一起通入一装有钯触媒的氢化塔内,进行氢化反应,得到相应的2-乙基氢蒽醌。
2-乙基氢蒽醌再被空气中的氧氧化恢复成原来的2-乙基蒽醌,同时生成过氧化氢。
利用过氧化氢在水和工作液中溶解度的不同以及工作液和水的密度差,用水萃取含有过氧化氢的工作液得到过氧化氢的水溶液。
后者再经溶剂净化处理、浓缩等,得到不同浓度的过氧化氢产品。
年产10000吨27.5%的H2O2,总投资约3000万元;投资回收期3年左右。
该技术具有明显的经济效益,按上术生产规模计算,每年可获得税后利润500万元左右。
由于该技术中采用以污治污技术,环境效益明显。
轻工行业
34
碱法/硫酸盐法制浆黑液碱回收
适用于碱法/硫酸盐法蒸煮工艺,对所产生的黑液进行碱及热能回收,并大幅度降低污染
碱回收主要包括黑液的提取、蒸发、燃烧、苛化等工段。
提取:
要求提取率高,浓度高,温度高。
蒸发:
提取的稀黑液需进入蒸发工段浓缩,使黑液固形物含量达55─60%以上。
燃烧:
浓黑液送燃烧炉利用其热值燃烧。
燃烧后有机物转化为热能回收,无机物以熔融状流出燃烧炉进入水中形成滤液。
苛化:
澄清后的滤液进入苛化器与石灰反应,转化为NaOH及Na2S。
在稳定、正常运行条件下,碱回收的投资回收期约5─10年,木浆回收期较短,非木浆较长。
按年产34000吨浆(日产100吨浆)计算,碱回收的直接经济效益(商品碱价按1700元/吨,回收碱按800元/吨计)7344万元/年。
按吨浆COD产生量1400公斤,碱回收去除COD80%计,日产100吨